Fertilizer International 509 Jul-Aug 2022
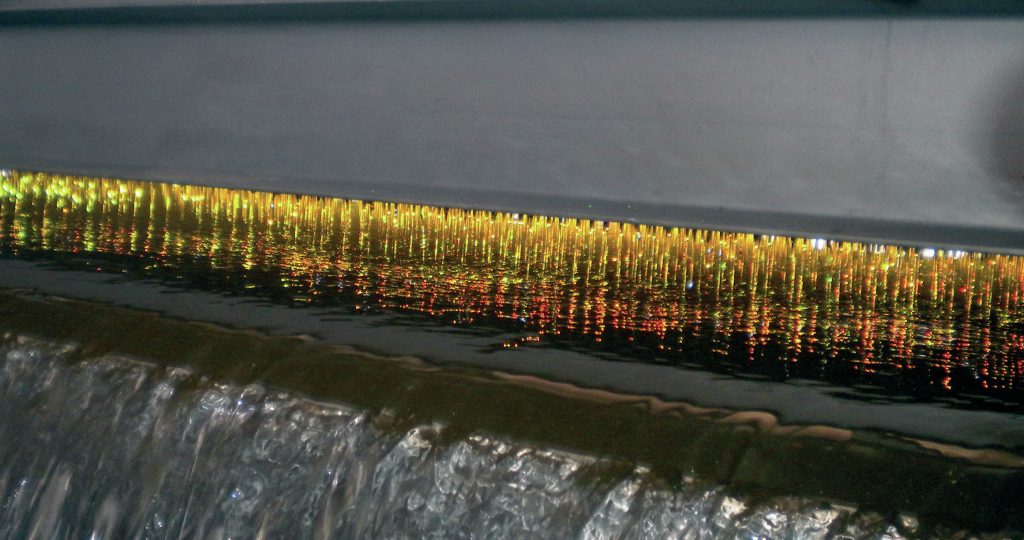
31 July 2022
Sulphur forming technologies
GRANULATION, PASTILLATION & PRILLING
Sulphur forming technologies
It is generally necessary to solidify sulphur into a robust form suitable for handling and long-distance transport. Granulation, pastillation and prilling are some of the technologies used to produce solid sulphur from molten material. Similar technologies are also used to manufacture sulphur fertilizers.
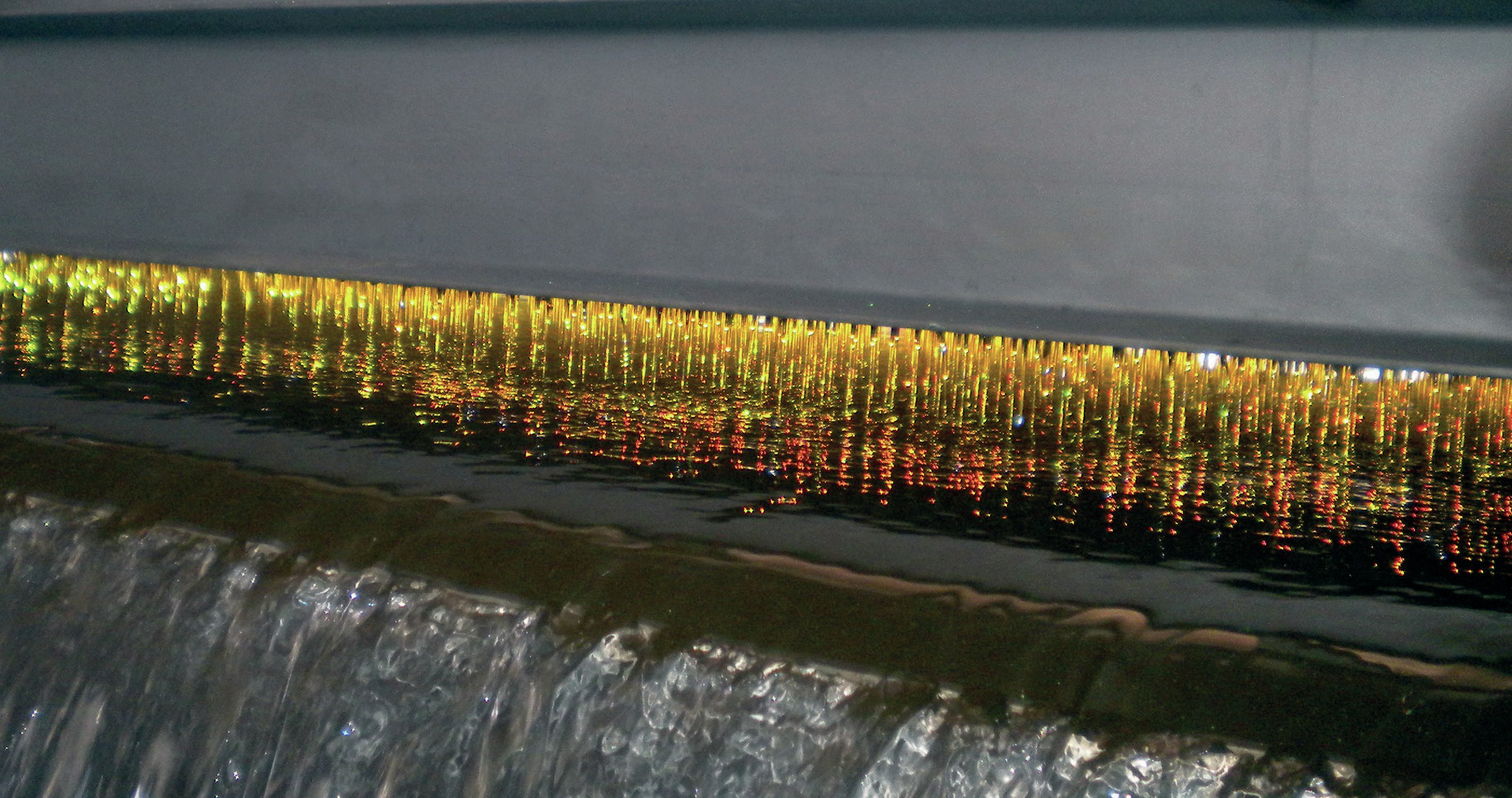
KREBER
Developments in sulphur prilling
Family-owned and Rotterdam-based prilling company Kreber was founded in 1902. The company offers prilling equipment and technology for sulphur and fertilizers such as urea ammonium nitrate and calcium ammonium nitrate.
Kreber has a strong focus on innovation and operates both a prilling laboratory and pilot plant facilities. The company’s in-house R&D team also collaborates with Delft University of Technology and other research institutions. These collaborative efforts resulted in the development of Vibro prilling. This major breakthrough – by adding a vibration to the melt – produces more uniform prills with a narrow size distribution.
Kreber has been monitoring new developments in sulphur prilling and has highlighted the challenges that remain (Sulphur 389, p30), as summarised on the next page.

Prilling and other sulphur-forming technologies
Sulphur forming – the transformation of large volumes of molten sulphur into solid particles suitable for transport – has always been a challenge. Forming was originally achieved by crushing solid sulphur blocks into smaller pieces. But the industry soon started looking for new technologies to form sulphur due to the dust formation and handling problems associated with this approach.
One of these technologies was air prilling, a method already successfully employed by the fertilizer industry. Prilling generates large quantities of small yet perfectly spherical pellets as a finished product. Advantageously, these sulphur prills are free-flowing with a polished surface and a relatively narrow particle-size distribution. Prilling went on to become the dominant method of producing solid sulphur. This led to the widespread introduction of the SUDIC (Sulphur Development Institute of Canada) specification as a market standard for all sulphur finishing technologies.
A range of other sulphur solidification processes, including granulation, (steel belt) pastillation and wet prilling, have become more prevalent over time. This shift to new sulphur forming methods resulted from two main concerns.
Firstly, prilling towers operated in the 1960s were based on an open-air design. These immediately ejected all the cooling air used for solidifying prills into the atmosphere. This air was laden with dust from the prilling process and vapours from the sulphur melt – causing environmental problems downwind of the prilling plant.
Secondly, it was concluded that dry prilling should be classed as a high-risk technology following a major fire at a prilling tower in the Middle East. This disastrous incident demonstrated how two factors – low ignition energy and the potential build-up of static charge in solidifying prills – can cause dangerous sparks, especially in the hot, dry climate of the Middle East.
Safer and more sustainable prilling
In the last few years, prilling has been developed to handle a wide variety of products. Air treatment sections were also widely incorporated into designs from the late 1980s onwards. These use either a dry filter or wet scrubber to drastically reduce prilling tower dust emissions.
Nevertheless, more stringent regulations have been applied to prilling towers as the environmental impacts on their surroundings have become more apparent. This has resulted in a surge of new research – with the development of the closed loop prilling process being one of the main outcomes.
Closed loop prilling
In a closed loop process, the cooling medium (air) is reused after firstly being cleaned in a treatment section and then cooled down in a heat exchanger. One of the main benefits from closing the loop is that emissions are reduced to zero. Additionally, the heat removed from the cooling medium can be reused elsewhere in the plant, leading to better overall heat integration and efficiency.
Prilling is widely applied in other industries where similar fire and dust explosion hazards exist – these usually being associated with the air treatment section. One advantage of the closed loop prilling process is that the complete recycling of the cooling medium eliminates the need to use ambient air. As wastage is very limited, practically any gas can be chosen as a cooling medium. Consequently, prilling towers which use inert nitrogen gas as a cooling medium have started to emerge. They offer an intrinsically safe method of prilling with no emissions and a low fire hazard.
Looking ahead, closed loop prilling towers are showing promise for sulphur forming, due to their growing reputation as a safe and high-capacity production process for converting melts into finished solid products. The main challenge now, suggests Kreber, is to adapt the closed loop processes used in plastics and fertilizer prilling into systems that can safely handle sulphur.
Latest innovations
Prilling has gone through many developments since its emergence in the 18th century. The latest innovations are mainly in the off-gas section and improved process control. These have led to a safer and more reliable production of sulphur prills from melt.
Prilling – by providing desirable product qualities such as a narrow particle-size distribution and free flowing behaviour – has distinct advantages over the other main sulphur finishing technologies, according to Kreber. Looking ahead, closed loop prilling using an inert cooling medium shows great promise as a method for prilling sulphur in the safest and most economical way (Sulphur 389, p30).
Wet prilling
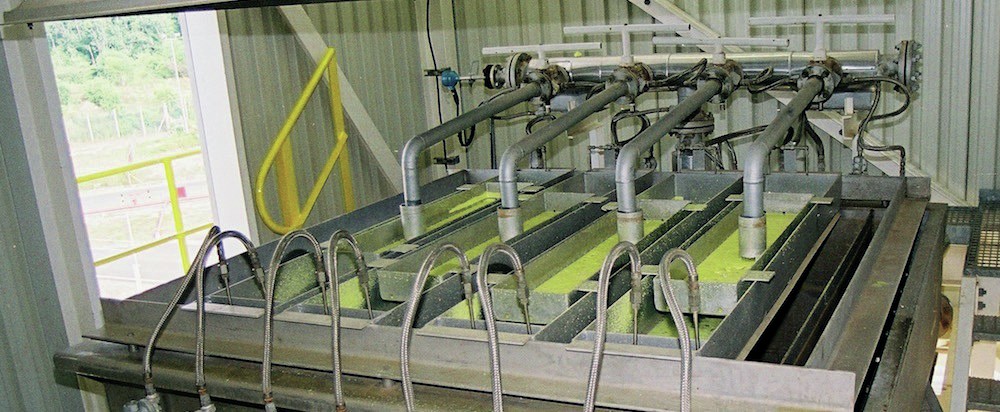
The Canadian sulphur technology company Enersul offers the WetPrill forming method as an alternative to its well known the GX granulation process. Wet prilling allows sulphur forming to take place at a higher temperature and, according to Enersul, is associated with lower operational costs and a smaller plant footprint. The process generates low friability, low moisture content and high bulk density prills. These high-quality end products are small, round and uniform with few entrained fines and are easy to handle and transport.
In the WetPrill process, molten sulphur is pumped into perforated streams at the top of a forming tower. This generates small droplets of liquid sulphur in a controlled manner which then fall into the top of a tank of cooling water to instantly solidify into uniform pellets.
The process has been continuously refined and improved by Enersul over the past three decades through in-plant operational development and pilot plant research. WetPrill units are individually designed to meet customer requirements and available in capacities of up to 2,500 t/d.
IPCO
Advances in drum granulation
IPCO is a world leading manufacturer of sulphur processing and handling equipment. The company has successfully delivered hundreds of complete end-to-end systems around the globe since 1951. In addition to granulation drums, more than 700 IPCO Rotoform sulphur processing systems have been installed worldwide to date.
Rotoform is an environmentally-friendly sulphur pastillation system designed to meet small to medium capacity requirements. It produces premium quality pastilles of uniform shape and size.
New showcase drum granulator
IPCO recently commissioned a groundbreaking new SG20 drum granulator in Italy (Sulphur 395, p28). This fully automated, once-through sulphur granulation system is based on rotating drum technology. The unit has been delivered to a long-standing Italian customer operating multiple sulphur solidification lines. IPCO has an agreement in place that enables prospective customers to visit the site and observe a fully functioning unit working under operational conditions.
The SG20 is a scaled-down version of the company’s 2,000 t/d capacity SG30 model. This medium-size unit offers a solidification capacity of up to 800 t/d and is noted for being easy to monitor, its quiet operation and good maintenance access.
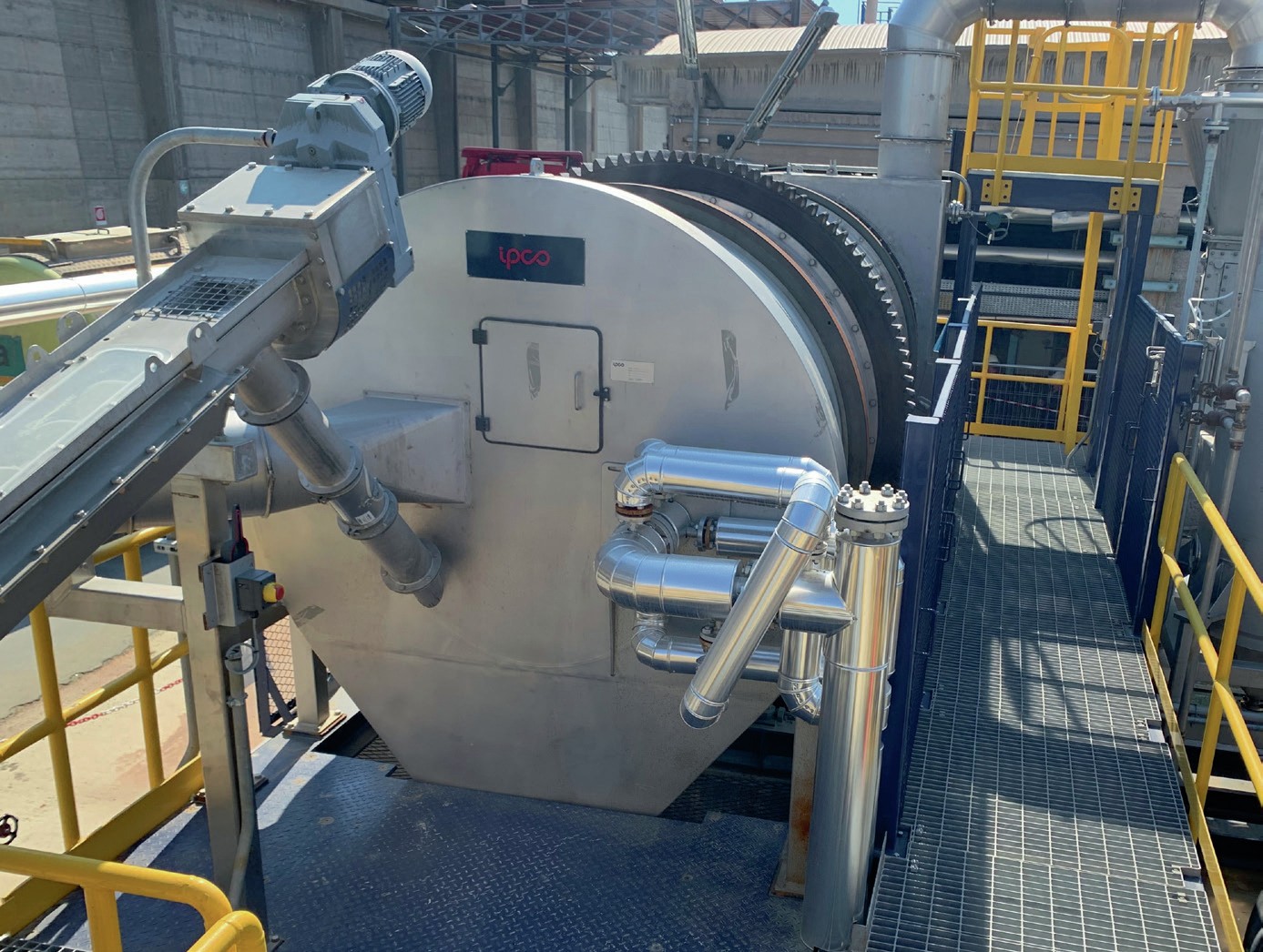
The SG20 and SG30 models use the same design and operating principles. Both are based on single-pass granulation process that eliminates the need for screens or recycle conveyors. They also incorporate an innovative approach to sulphur nucleation. Sulphur seed particles are created outside the granulation drum by freezing a liquid sulphur spray in a water bath. Generating these particles externally, while also consuming sulphur recycled from the downstream wet scrubbing system, simplifies the process. It also allows more flexibility over the temperature of liquid sulphur entering the granulator.
SG series units deliver high-quality sulphur granules that satisfy the shape criteria and friability requirements (Stress Level I and II) of the SUDIC product specification. This ensures that formed sulphur can be stored handled and transported efficiently, cleanly, and safely. The SUDIC specification also limits moisture content. This is important as excess moisture, by adding weight, creates avoidable extra transportation and melting costs. The presence of moisture also raises acidity and therefore increases the corrosion risk for storage, handling and transportation equipment.
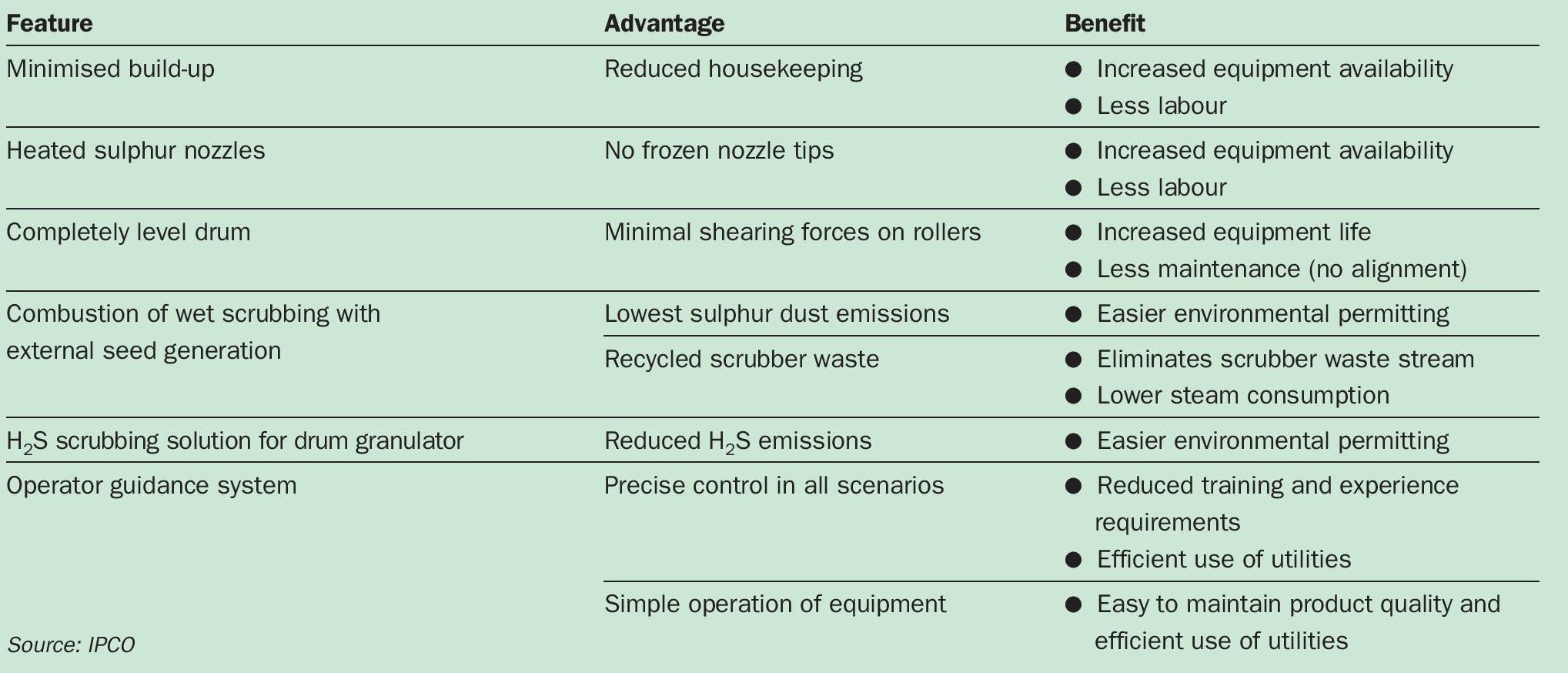
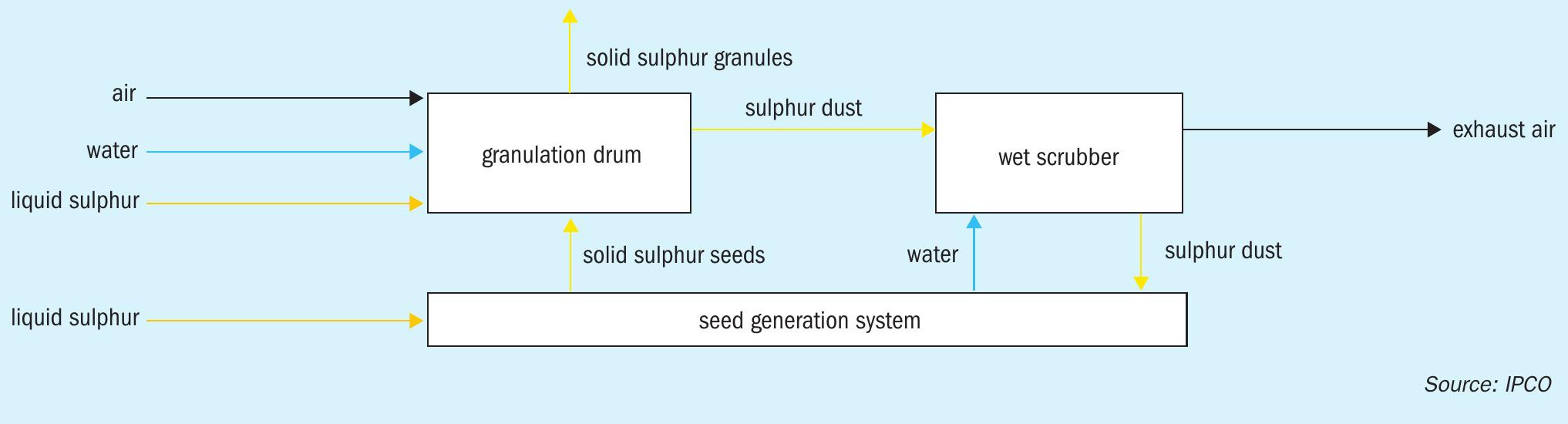
Enhanced capabilities
In designing the SG series, IPCO has taken the inherent advantages of drum granulation – i.e., its combination of large capacity and high product quality – and added to these by overcoming the challenges previously associated with this sulphur forming method (Table 1). For example:
- Equipment availability has been increased by significantly reducing cleaning and maintenance requirements.
- Reductions in sulphur dust and H2 S emissions ensures these are kept well within the limits set by prevailing environmental legislation, while noise levels are far below standard limits.
- A new drum design increases equipment life by cutting roller stress and wear.
- Operations have also been simplified – allowing the units to be stopped and started at the touch of a button.
- Finally, a game-changing operator guidance system enables high-quality products to be generated at all times, regardless of operator experience and process conditions.
Key innovations and operational advantages
A simplified drum granulation process is shown schematically in Figure 1. The IPCO patented SG system has been designed to overcome the drawbacks often associated with traditional drum granulation, especially cleaning, maintenance and process control. The main operational advantages are listed below.
Substantial reduction in sulphur build-up. The SG20 can run continuously for a full week before a shutdown is required. Even then, cleaning requirements are minimal compared with traditional drum granulation systems.
Heated sulphur nozzles. Liquid sulphur has to be maintained at a specific temperature range (around 120 to 160°C). Any liquid sulphur remaining in the nozzle when the system is shut down will freeze and block flow at the next start-up. IPCO has overcome this potentially time-consuming maintenance issue by incorporating the industry’s first heated sulphur spray nozzles in the SG series drum granulators. This completely eliminates the need to send maintenance crews into the drum to fix freeze up problems.
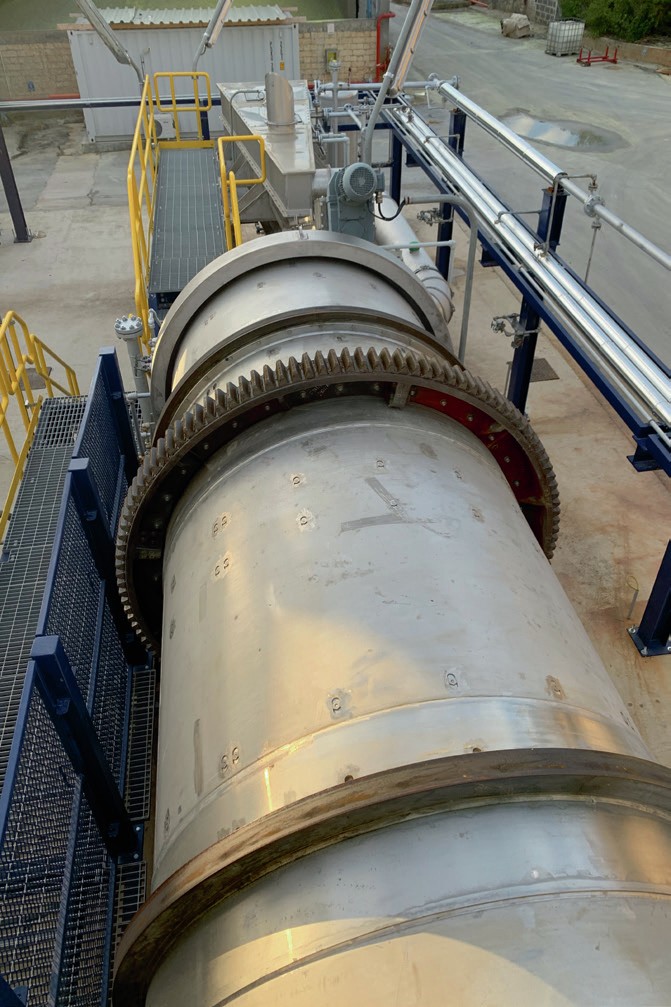
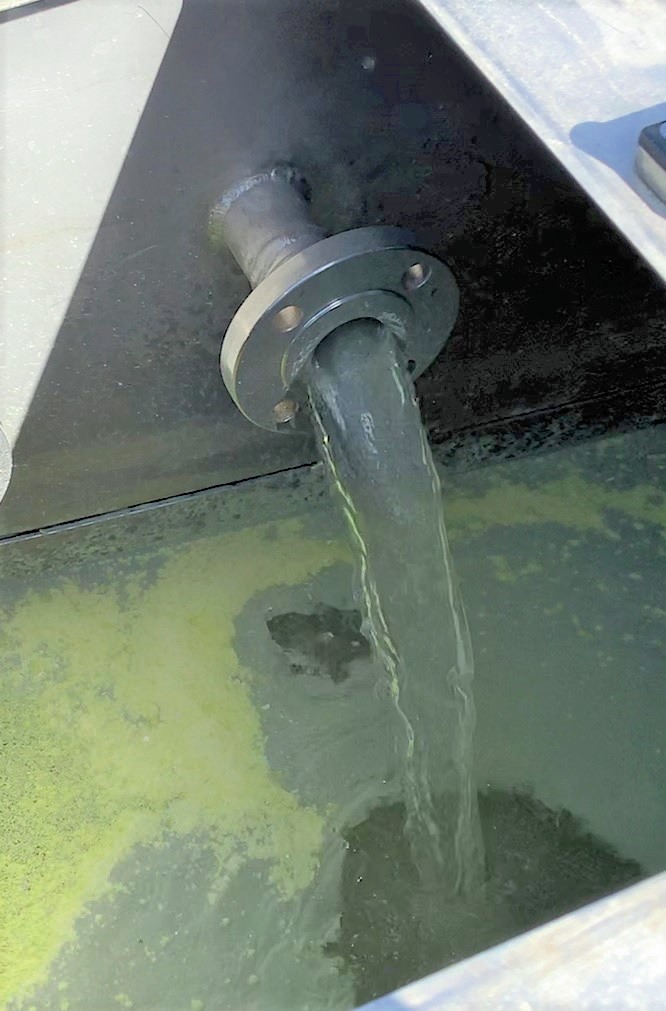
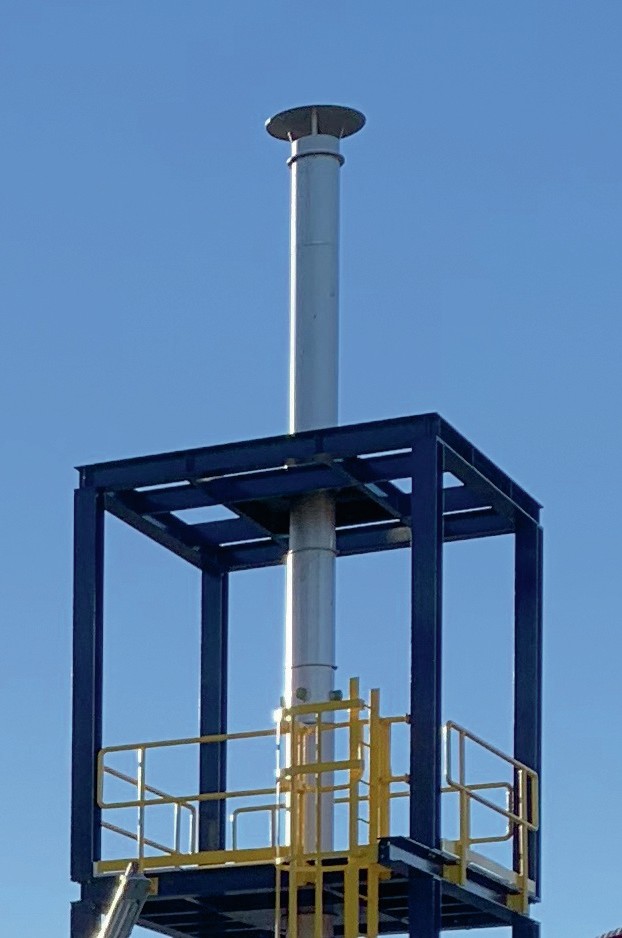
Redesigning the drum to minimise roller wear. IPCO’s SG series granulators (see overhead photo), instead of rotating at an angle, operate on a completely level base and use angled internal flights to advance the product instead of gravity. This prevents unnecessary wear and tear on the rollers, and avoids the regular maintenance needed to keep the unit properly aligned.
Dust emissions and scrubber waste. IPCO chose a wet scrubbing system for the SG series due to its ability to deliver the lowest sulphur dust emissions and therefore have the lowest environmental impact. The waste stream from the scrubber is also recycled directly into the external seed generation system (see photo).
Managing H2 S emissions. The spraying of liquid sulphur through nozzles as part of the drum granulation process releases H2 S. Therefore, to comply with strict European regulatory limits, preventative measures need to be taken to prevent H2 S from entering the atmosphere. This can be achieved by the addition of an H2 S scrubbing system to reduce stack emission levels and ensure compliance with the most stringent regulations globally (see photo).
Consistent operation. Operating conditions, such as throughput, liquid sulphur feed temperature, ambient temperature and humidity, all need to be taken into account during the solidification process. While a drum granulator can be set to operate at fixed parameters, this is likely to result in sub-optimal performance when these conditions change. SG series units therefore incorporate an operator guidance system – an industry-first for sulphur drum granulation. The system uses process simulation to ensure that the granulator is working at its full potential under different operating conditions. An accurate simulation was developed by analysing real operational data generated by both the SG20 and SG30 units.
Rotoform pastillation for sulphur fertilizers
Sulphur-bentonite pastilles
Sulphur-bentonite pastilles combine elemental sulphur with 10 percent bentonite. This special clay swells in wet soil, breaking apart the pastilles and releasing dust-size particles of elemental sulphur. These can then be easily oxidised into plant-available sulphate by soil microbes.
Rotoform pastillation
IPCO’s Rotoform process is ideally suited to the small/medium capacity pastillation of sulphur fertilizer products. It is simple and versatile, with low investment and operating costs, and minimal environmental impacts.
Multi-nutrient fertilizers can be created by combining sulphur with macronutrients (such as nitrogen from urea) or micronutrients, opening up new opportunities for producers in the speciality fertilizer market. The range of suitable speciality products includes:
- Sulphur-bentonite + micronutrients, e.g. zinc, iron, boron
- Urea + sulphur
- Urea + ammonium sulphate.
The Rotoform process has been used to successfully mix sulphur with urea to produce Special S and Urea-ES products.
The Rotoform process, when linked to an upstream dosing and mixing plant, can be delivered as an automated continuous process for fertilizer production. An example of an IPCO plant for blending and mixing urea with sulphur is shown in Figure 2.
Additional benefits provided by the IPCO Rotoform process include:
- High-quality uniform and free-flowing pastilles with high crushing strength
- Very low dust, vapour and gas emissions
- Low power consumption.
The superior performance and operational flexibility offered by IPCO’s Rotoform process allows fertilizer producers to develop and launch innovative new sulphur-enhanced fertilizers. These can boost profit margins by adding value to existing commodity products, while at the same time helping farmers to achieve the higher crop yields they need.
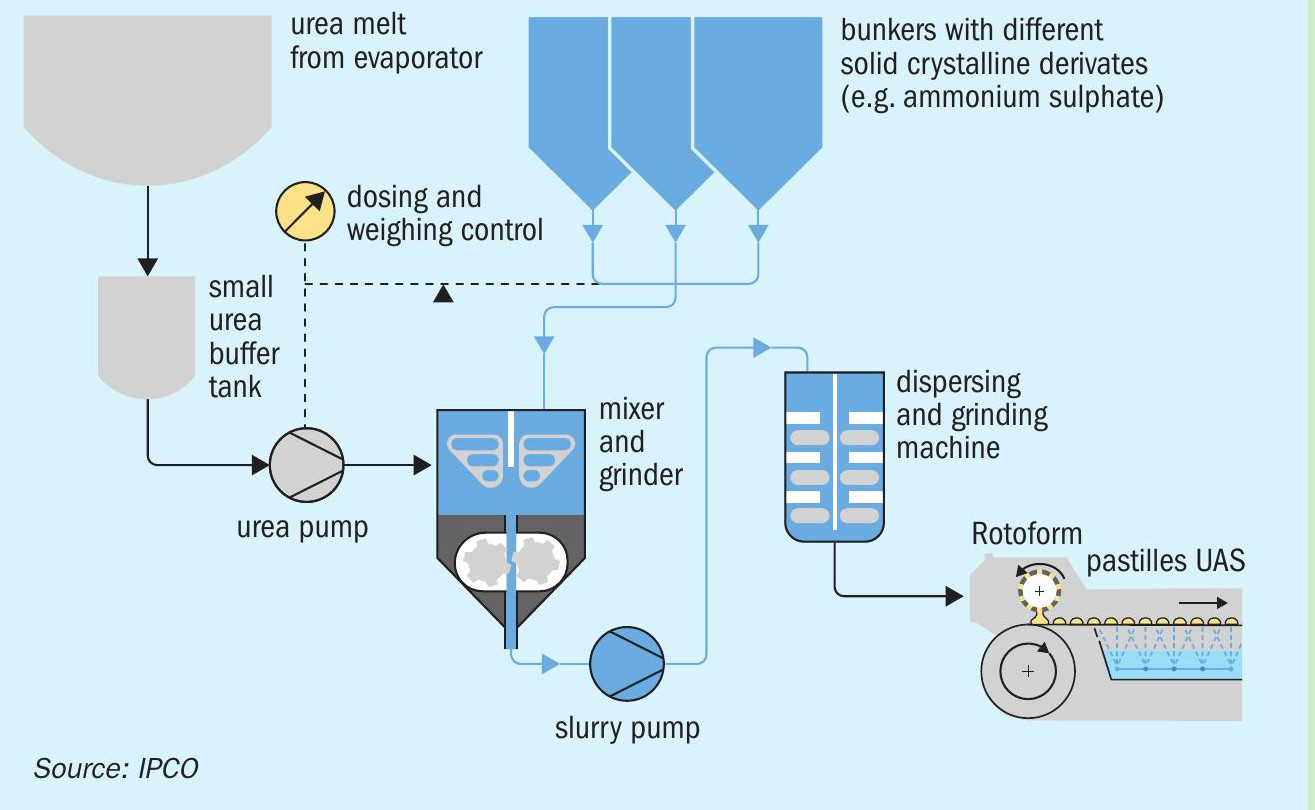
MATRIX PDM ENGINEERING
Sulphur forming for a global market
As world markets continue to reel from supply chain issues first triggered by Covid-19, the impacts on both producers and consumers of sulphur – a vital raw material used in the creation of sulphuric acid and the subsequent production of fertilizers – have been no exception.
For fertilizer manufacturers, the price of molten sulphur is up more than 400 percent compared to a year ago, while transportation and other operating costs are also on the rise as diesel and other utility prices increase. Now, geopolitical events also threaten further supply chain disruption and increases in material costs. These includes the worldwide sanctions placed on Russia (the largest global exporter of fertilizer) in response to its invasion of Ukraine, and China’s recent lockdowns in Shanghai and Beijing.
In this environment, producers and consumers are looking for ways to:
- Lower capital outlay and operating costs
- Ensure sufficient product moisture to minimize the dangers associated with dust formation
- Minimise logistical issues associated with long-distance shipment
- Maximise longer-term storage.
The method chosen for sulphur forming, a process used to solidify molten sulphur, is critical when it comes to achieving these objectives.
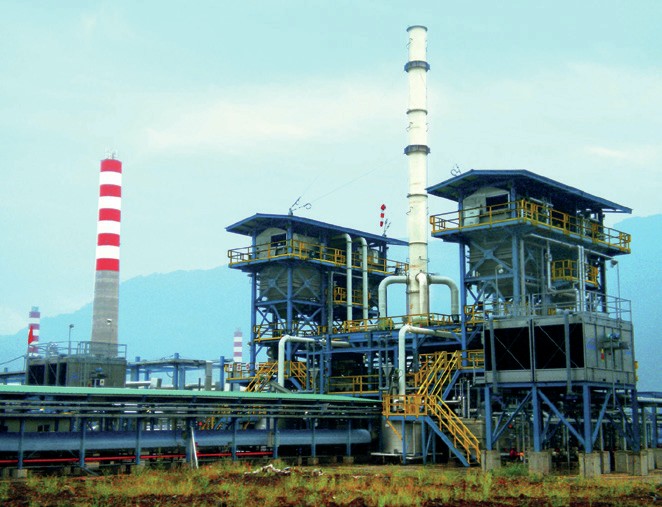
Exploring the options.
Technologies available for sulphur forming include granulation, pastillation, and wet prilling.
- Granulation is a process where molten sulphur is sprayed onto a seed curtain within a rotating drum and water is then sprayed into the drum to cool the sulphur, forming sulphur granules.
- Pastillation occurs when water is sprayed under a steel belt onto which liquid sulphur drops have been deposited, producing pastilles or small lozenge-shaped sulphur pills. During pastillation, water and sulphur do not come into direct contact during the forming process.
- Wet prilling is the other option. It is provided through modern technology like the Devco II system, a proprietary prilling technology offered by Matrix PDM Engineering. In wet prilling, molten sulphur travels through a counter-current forming tank where it is exchanged with water to produce uniformly sized prills. These are withdrawn from the bottom of the forming tank after which the correct amount of water is removed on dewatering screens.
As forming methods, granulation and pastillation both require the addition of proper dust control during handling and transportation due to their similar environmental and safety risks. Both methods often require sulphur preconditioning too. This is to ensure that sulphur is maintained at an optimal temperature and any H2 S generated – a highly toxic gas found in molten sulphur – is kept to safe, minimal levels.
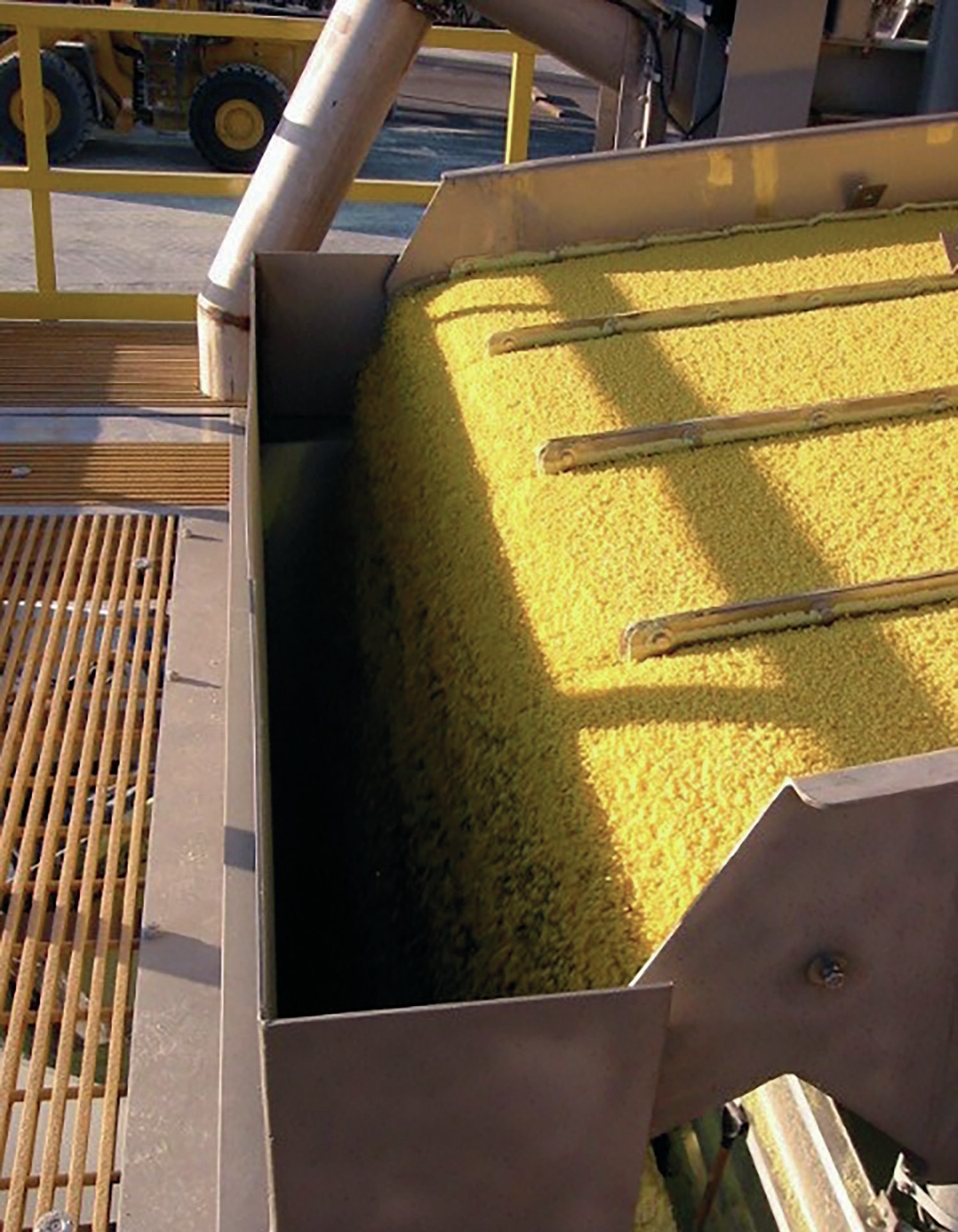
Wet prilling offers maximum flexibility in moisture control. In our view, it is the only forming technology that properly maintains sulphur moisture content for global market transportation by meeting or exceeding international requirements set by global sulphur importers. The ability to optimise moisture content has also been proven for long-term storage under extreme environmental conditions (hot arid, hot humid, extremely cold) without the need for additional dust control or specialised loading equipment.
Advantageously, the technology used for wet prilling:
- Is modular in design and construction, resulting in lower capital outlay. Among its major components are the forming tray(s), forming tank, dewatering screen(s), fume hood, process water cooling system and atmospheric fume scrubber (when required). No intermediate molten storage, pumping or pre-conditioning is required between the sulphur recovery unit (SRU) and prilling system.
- Has lower operating costs – critically important in the current environment, especially in energy-intensive industries such as fertilizer production. These reduced operating costs are achieved through minimal power consumption, a gravity-driven process flow, minimal moving parts, elimination of the need for dust suppressants, and fast startup/shut down.
- Offers flexibility in processing capacity while also offering a substantially higher maximum single-unit capacity with a significantly smaller footprint. For example, a single Matrix system has a capacity of 2,000-2,250 tons per day (t/d) compared to a single granulation unit which has a capacity of approximately 500-1,000 t/d and a typical pastillation unit with a capacity of 120275 t/d. The Matrix system’s footprint is just 10 metres by 8.5 metres, small compared to similar capacity systems for granulation (38 m x 22 m) or pastillation (28 m x 26.5 m).
The Devco II wet prilling system
The Devco II system, the modern proprietary wet prilling technology offered by Matrix PDM Engineering, is notable for combining high production capacity with low capital outlay and operating costs. This system is currently installed in more than 18 countries and on nearly every continent, with proven operational success under extreme weather conditions and in highly scrutinised environmentally sensitive areas. Matrix PDM Engineering prides itself on its flexibility in providing custom-based solutions to meet any client need.
Matrix PDM Engineering, the engineering division of Matrix Service Company, provides lifecycle engineering, procurement, and construction (EPC) services across the energy and industrial markets. Matrix PDM possesses more than 40 years of industry-leading expertise across the entire sulphur spectrum, including capabilities for:
- Molten sulphur storage, handling, and loading
- Sulphur forming
- Solid sulphur handling and loading
- Sulphur block pouring
- Sulphur remelting.