Fertilizer International 510 Sept-Oct 2022
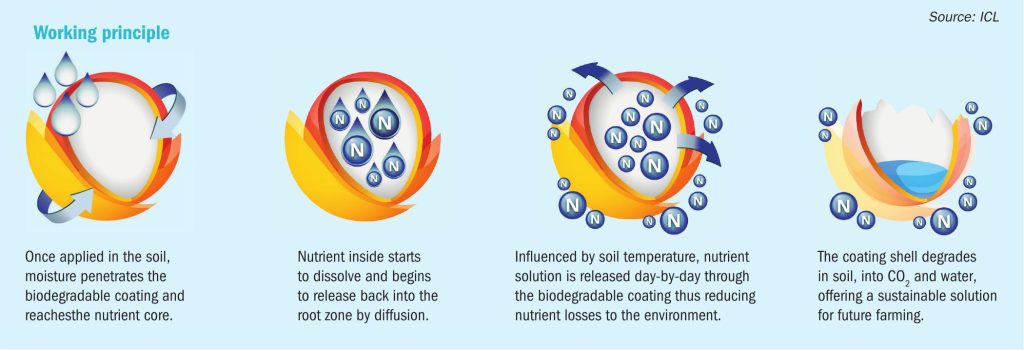
30 September 2022
New biodegradable CRF coating technology
SMART FERTILIZERS
New biodegradable CRF coating technology
ICL has developed a new generation of rapid biodegradable coatings for its controlled-release fertilizer (CRF) portfolio. The new coating technology reduces the environmental footprint of CRFs and will help farmers meet the requirements of Europe’s Green Deal. This patented innovation, named eqo.x, coats nitrogen fertilizers for field grown crops. Eqo.x has already been fully tested in the field – and shows excellent results in terms of production, nutrient use efficiency, volatilisation and leaching reduction. Ronald Clemens, ICL Global Marketing & Portfolio Manager CRF, explains the benefits.
CRFs rise to the sustainability challenge
One of the main challenges facing today’s farmers is the changing regulations governing fertilizer inputs. For example, Europe’s Green Deal, which includes the Farm-to-Fork strategy, aims to minimise the environmental footprint of agriculture. The reduction of fertilizer losses by at least 50 percent by 2030 is an important pillar of this strategy.
Controlled-release fertilizers (CRFs) can play a key role in meeting these Green Deal requirements. They increase nutrient use efficiency (NUE) – by maintaining or increasing yields while lowering the fertilizer input – reduce nutrient losses, and often only require one application for the entire season.
ICL has been testing CRFs in the field for decades, proving how they can reduce fertilizer inputs, while maintaining yields, and at the same time reduce nitrogen losses, ammonia volatilisation, and nitrous oxide (N2O) emissions.
Biodegradable technology for sustainable farming
To meet the future requirements of the new EU Fertilising Products Regulation (2019/1009), ICL has been (and still is) developing sustainable innovations for its CRFs. The company has just launched its new generation of rapid biodegradable coatings: eqo.x. This biodegradable release technology has been thoroughly field tested – showing the same or better production results with consistent and fully predictable release patterns.
Ronald Clemens says: “Sustainability and high nutrient use efficiency are ICL’s focal points in respect of its specialty fertilizers to the agriculture markets. With this innovation we create a sustainable solution from various angles, delivering a solution towards the Farm-to-Fork strategy in Europe, and making it possible for farmers to reduce fertilizer rates without losses in yield. In that respect, this innovation is ahead of the present regulations and ready for future standards coming.”
ICL’s R&D department in the Netherlands is renowned for its coating expertise. The department’s expert team of coating specialists, drawn from various industries, have managed to ‘crack the code’ by creating the first of a new generation of rapid biodegradable coatings. These will help create more sustainable farming systems, as Ronald Clemens explains: “We have been working on the topic of faster biodegrading coatings, combined with maximum field performance, for the last 15 years. For controlled-release nitrogen fertilizers for soil grown crops, we are ready now. The eqo.x release technology is protected by patent and ICL is investing in a new production line in the Netherlands.”
Coating technologies over the years
ICL’s Osmocote pioneered the CRF market, having been introduced more than 50 years ago as the first polymer coated fertilizers on the US market. These NPK granules, encapsulated with an organic resin coating, ensured that one nutrient application to crops was enough for a prolonged period of time.
Osmocote’s market introduction marked the start of a whole new principle in fertilizer application. In the decades that followed, new generations of fertilizer coatings were developed. These helped match nutrient release much more closely to plant demands, without any peaks or dips in the nutrient supply to crops. E-Max release technology is the current polymer coating that ICL incorporates in its CRF products for the agricultural market.
ICL’s newest biodegradable coating, eqo.x, is set to be one of the most important innovations and technological launches since the first CRFs were introduced on the market. It is expected, once again, to shape the future of fertilization.
“We see this as a huge step forward in the use of enhanced efficiency fertilizers for the agricultural market,” comments Ronald Clemens. “The biodegradable release technology will be able to reduce all kinds of nutrient losses, and combines this with all the known advantages of CRFs, like the possibility to reduce application frequency and rates.”
Consistent and predictable nutrient release
One of the key characteristics of high quality CRFs is that farmers can always rely on their performance. A consistent and predictable nutrient release pattern is essential to match the plant’s demands – and the performance of each bag of fertilizer product should always meet these expectations.
Eqo.x technology shows the same high performance and reliability as currently used technologies (Figure 1). Ronald Clemens explains how the new biodegradable coating functions:
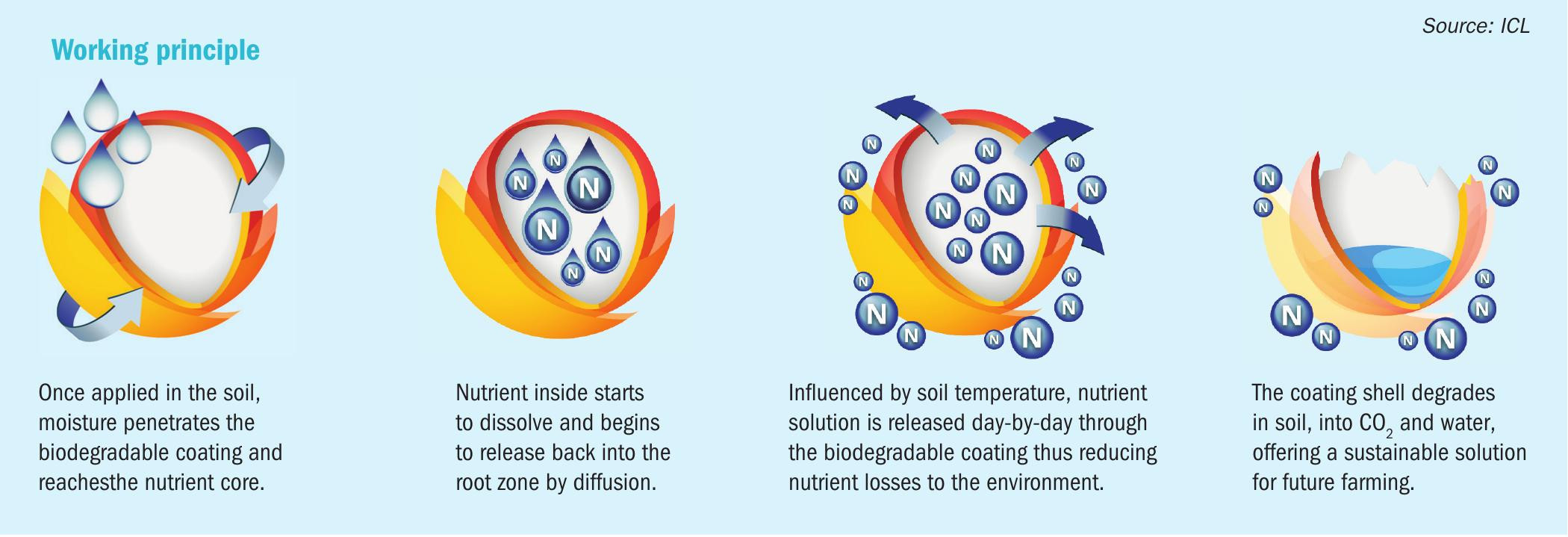
“The coating works similar to our existing coatings. The soil temperature is affecting the speed of release in a similar way as the E-Max coating is doing. That makes it easy for the farmer to use the products, as both the application as well as the performance will not change. The new technology includes an improvement in release patterns, making the CRFs with eqo.x technology even more reliable and predictable than before. And after the longevity ends, the coating shells will degrade even faster to CO2 and water, leaving no trace behind.”
Reducing nutrient losses to the environment
The amount of nutrient loss and how it occurs (volatilisation, leaching or denitrification) depends on the type of fertilizer, the soil to which the fertilizer is added and the weather conditions. The challenge is to maximise the nitrogen (N) efficiency of fertilizers and minimise the risk of environmentally-problematic N losses (Figure 2). The use of enhanced efficiency fertilizers (EEFs) such as CRFs offers one successful route to minimise the risk of losses.
Based on the latest trial results, nitrogen losses from conventional urea can be as high as 40-50 percent of total applied N. CRFs, in contrast, limit these losses substantially, being able to reduce both nitrogen losses and improve NUE, in comparison to conventional urea.
Results of the NMI lab trial
The environmental impacts of CRFs with eqo.x technology were evaluated by NMI (Nutrient Management Institute B.V.) in a recent lab trial. The institute measured nitrogen losses by leaching, volatilisation and denitrification, and compared these results to conventional fertilizers.
In the NMI experiment with red beet, a CRF with eqo.x technology was compared to conventional urea applied at the same time and the same rate. Results are shown graphically in Figures 3-9.
In the NMI trial, the CRF reduced N leaching by 54-61 percent (Figure 3) and reduced NH3 volatilization by up to 54 percent (Figure 4), versus conventional urea. The N2O losses were also significantly higher for conventional urea in the first 30-40 days, whereas the CRF reduced N2 O emissions by 11 percent overall (Figure 5).
Some 40-50 percent of N applied was lost to the environment using conventional urea (Figure 6). The CRF, in comparison, limited these losses to only 16 percent (Figure 7). Encouragingly, N uptake also increased and, in general, the experiment demonstrated an 83 percent NUE increase (Figure 8).
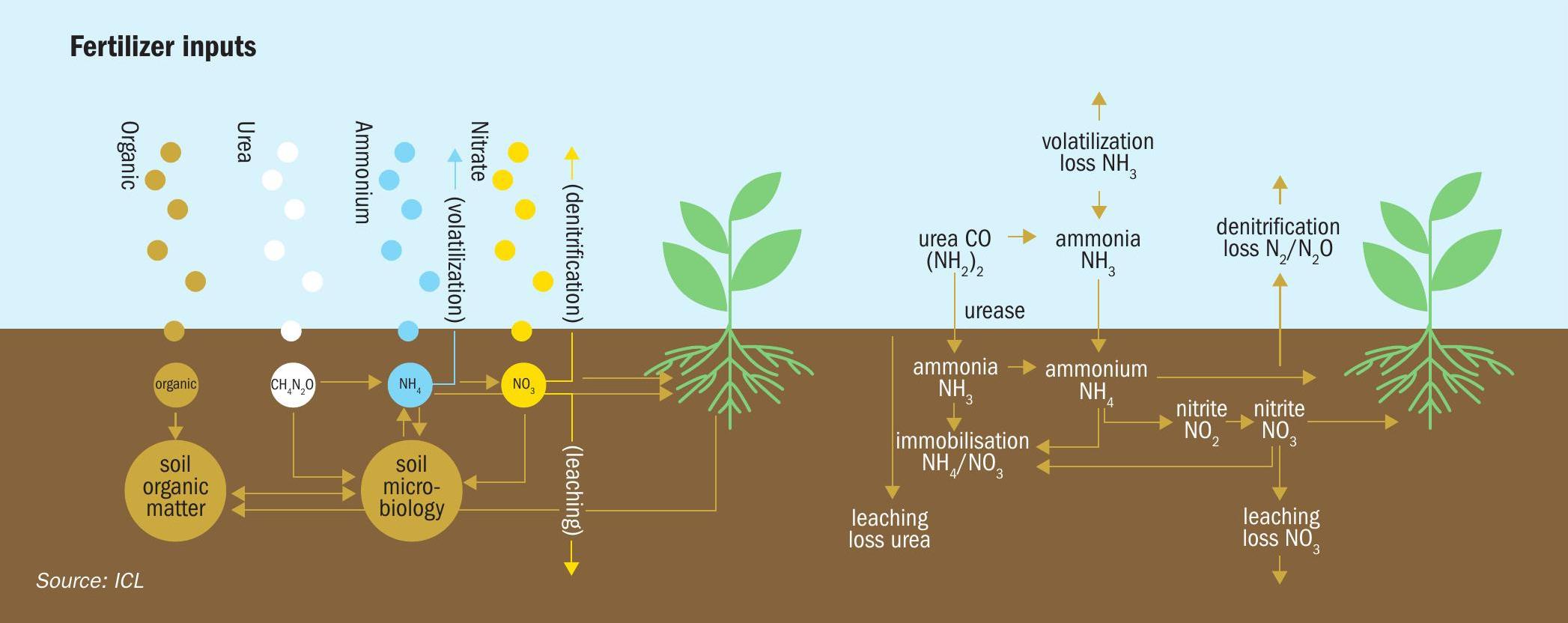
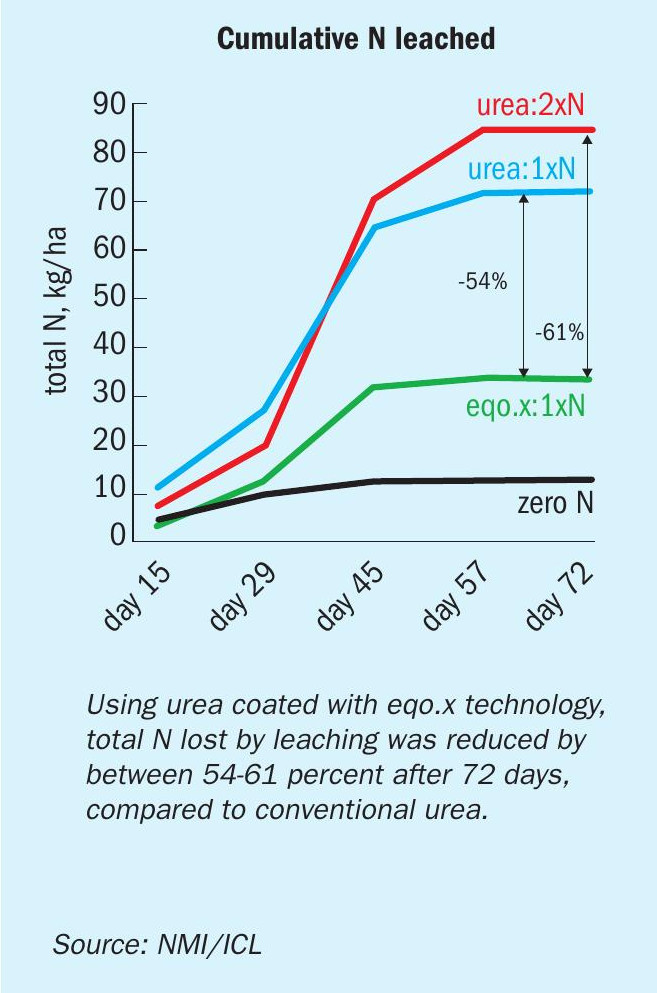
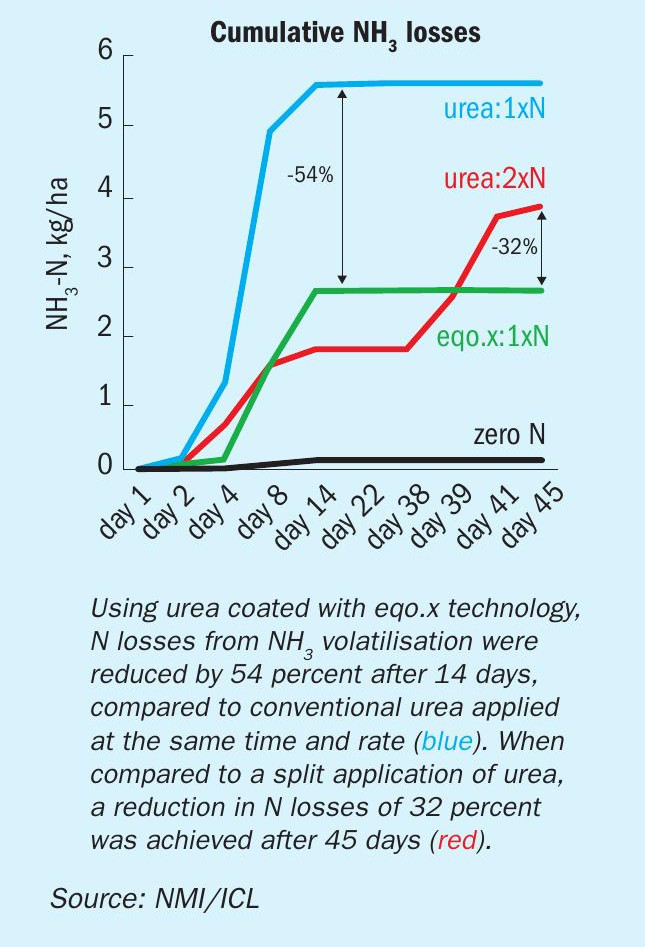
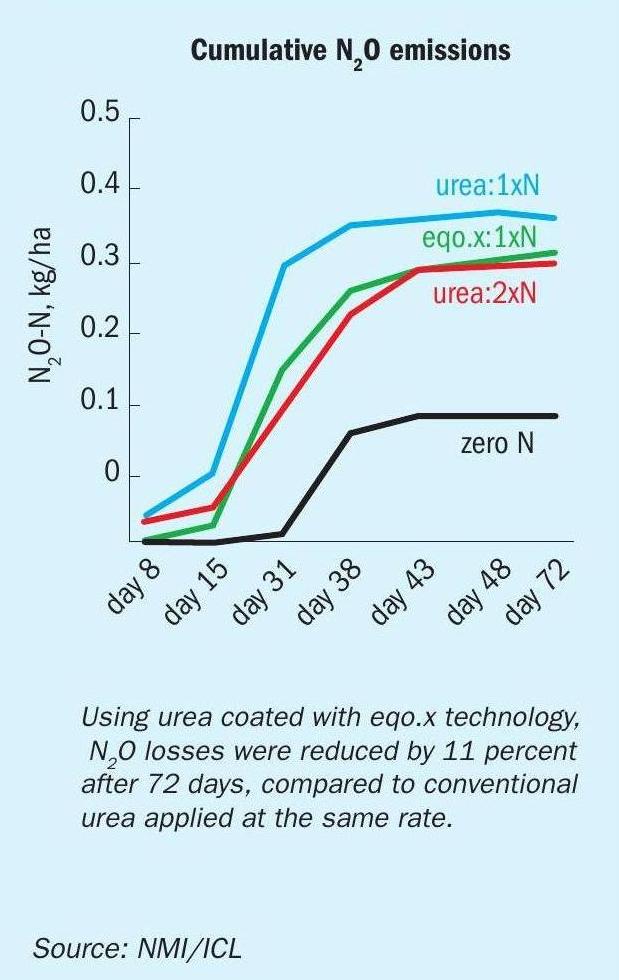
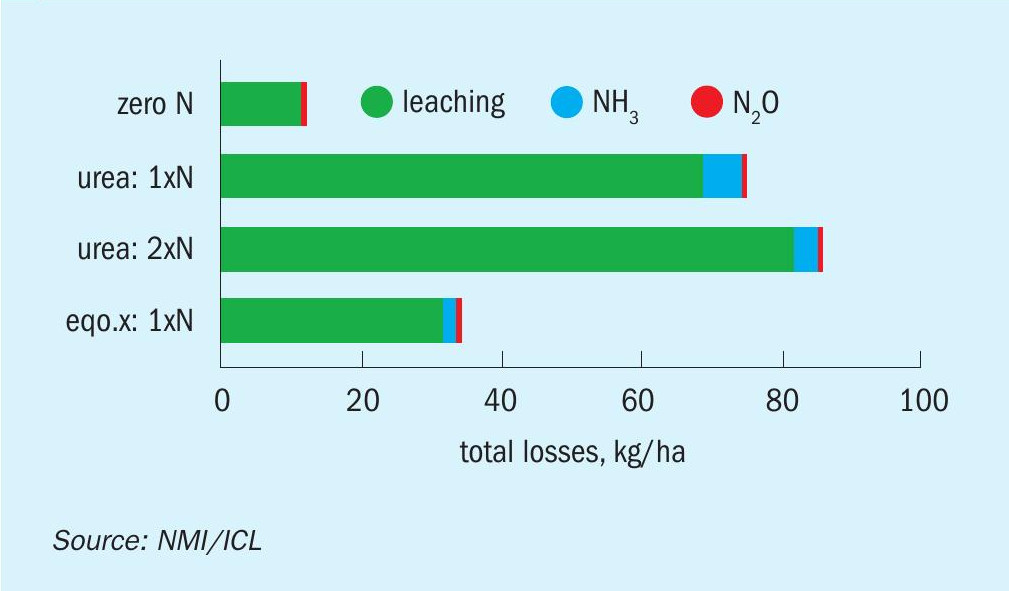
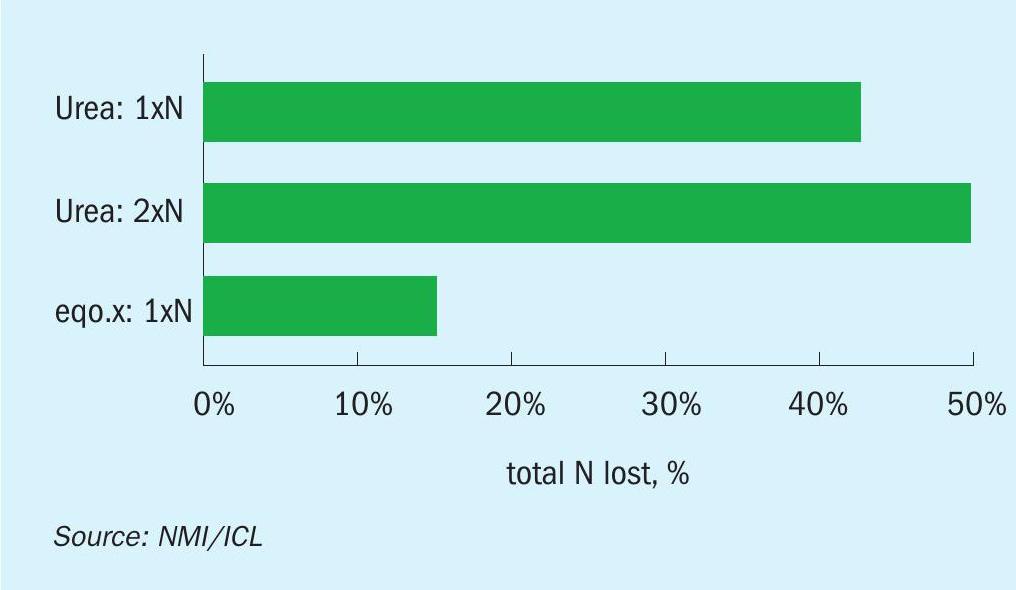
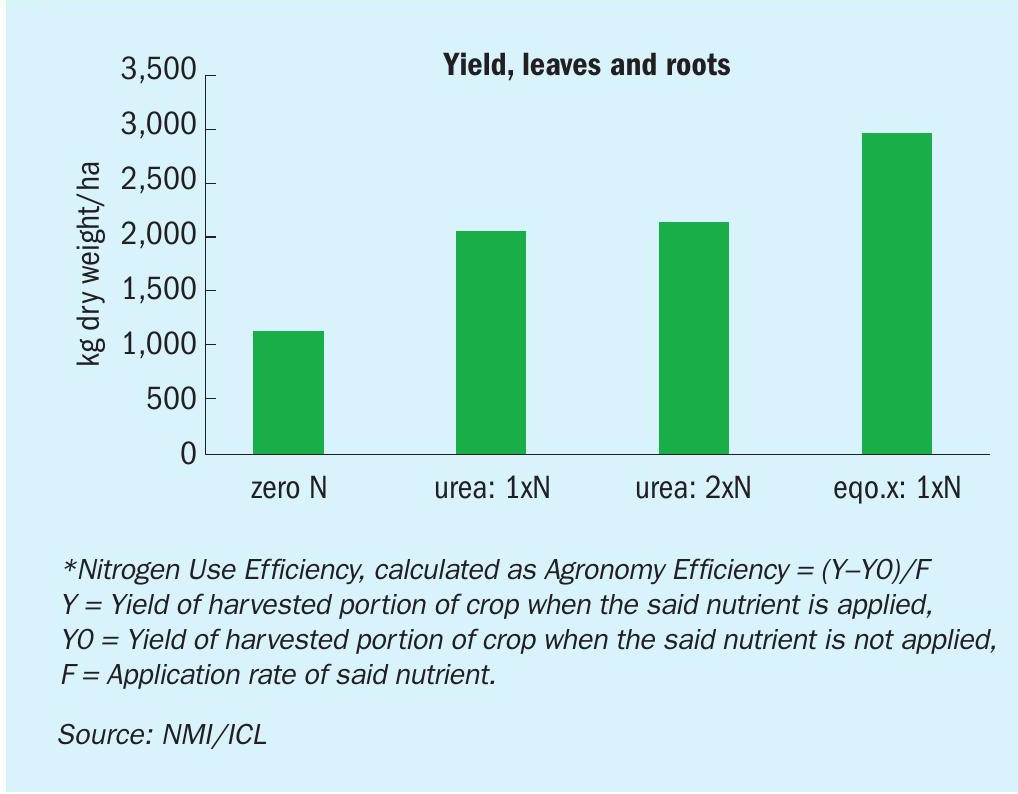
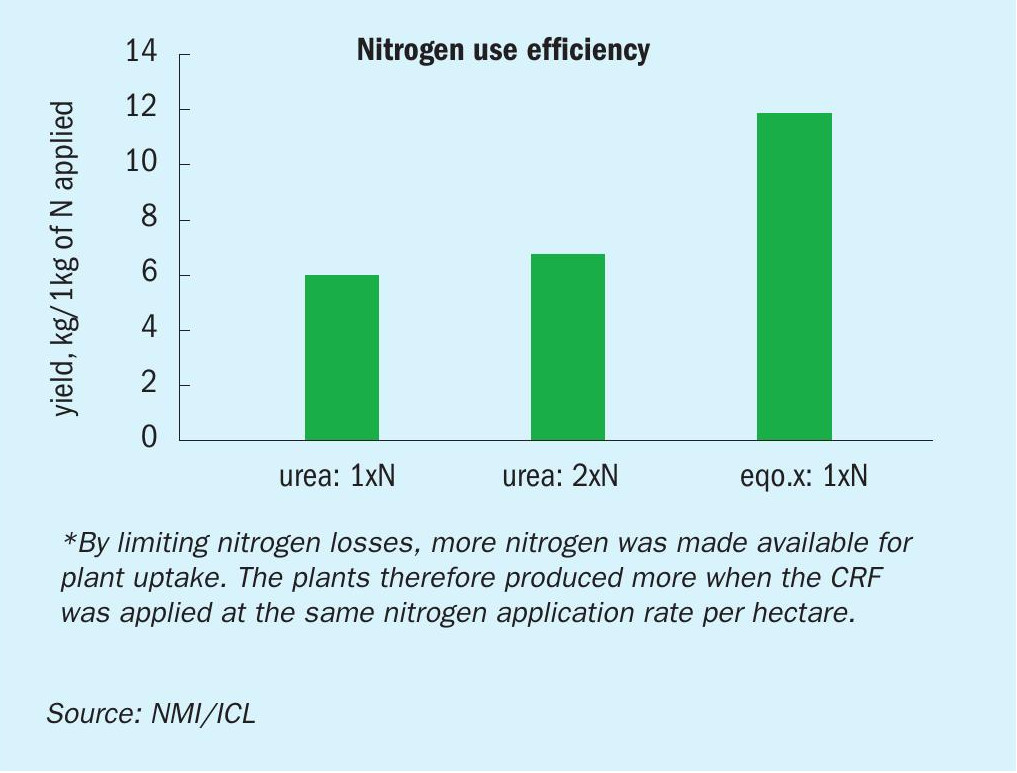
Importantly, the CRF with eqo.x technology is capable of achieving higher or similar crop yields with less fertilizer. Trial results with the CRF showed a significant yield increase of 37 percent, versus conventional urea, at the same N application rate per hectare (Figure 9).
“These results confirm our thoughts that with CRFs we are able to improve nutrient use efficiency by reducing fertilizer rates, and at the same time lower nutrient losses, without farmers losing their yields,” comments Ronald Clemens.
Increased nutrient use efficiency with eqo.x
Wide ranging trials with eqo.x technology have all shown an increase in NUE (e.g., Figure 8). This is to be expected with a CRF, says Ronald Clemens: “The technology contributes to reducing nutrient losses and improved nutrient use efficiency. It will help farmers to maximise their yields. Official trials were done with trial institutes and universities from North to South Europe, in various conditions. We have tested in crops like potatoes, but also in very hot conditions in rice cultures where the product is fully under water. We have tested the release specifications in the lab under various temperature regimes, in water and in soil as well as under practical circumstances. In all those conditions the nutrient use efficiency was significantly increased, giving better results than growers practices in terms of yield, number of applications or application rates.”
What’s next
From 2023 onwards, ICL will start to gradually deliver eqo.x technology to the market in its Agrocote and Agromaster formulations. In the meantime, the company’s R&D team is continuously working on new solutions.
“We are extremely happy with this innovation, being available already now so that we are prepared towards the future,” sums up Ronald Clemens. “The next step is that more of our coating technologies will move to a faster degradability.”
The benefits of CRFs
- Controlled-release fertilizers (CRFs) are a precision nutrition technology that release nutrients over a longer period of time through a special coating. This resulting nutrient release pattern closely matches the needs of crops throughout the growing season.
- CRFs play a key role in modern agriculture by improving yields, reducing nutrient losses, and minimising fertilizer application rates.
- CRFs have environmental benefits in comparison to conventional fertilizers, as their use allows growers to cultivate high-quality plants efficiently with a significant reduction in nutrient leaching to both soil and groundwater.
- As such, CRFs are part of the solution in helping meet the future target to reduce nutrient losses in EU agriculture by 50 percent, as set out in the Farm-to-Fork Strategy, the Zero Pollution Action Plan, and EU Soil Strategy for 2030.