Nitrogen+Syngas 379 Sept-Oct 2022
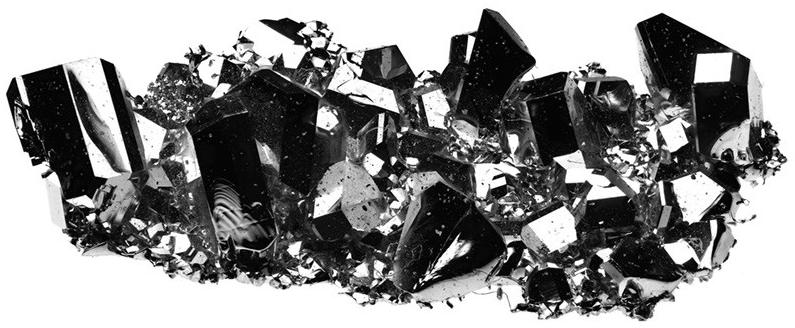
30 September 2022
Syngas News Roundup
Syngas News
ITALY
Contract awarded for waste to methanol plant
Maire Tecnimont subsidiary MyRechemical has been awarded a basic engineering contract for a waste to methanol and hydrogen plant to be located in Empoli, Tuscany. The scope of work includes the basic engineering design of the plant and the provision of necessary documentation to start the plant’s public authorisation process with the Tuscany region. The basic engineering phase is expected to be completed by the end of 2022. Once completed, the plant will process 256,000 t/a of non-recyclable waste and will produce 125,000 t/a of methanol and 1,400 t/a of hydrogen. The plant will use MyRechemical’s chemical conversion technology which allows the recovery of waste that cannot be mechanically recycled, or other types of unsortable dry waste. The carbon and hydrogen in the waste are converted via gasification into synthesis gas, which is used to produce low-carbon methanol and hydrogen.
Alessandro Bernini, Chief Executive Officer of Maire Tecnimont Group and NextChem, commented: “This is one of the more interesting waste-to-chemicals initiatives that Maire Tecnimont is developing in Italy. This is the first application worldwide of an integrated technological scheme that allows to produce methanol from waste for sustainable mobility and hydrogen that will substitute methane in glass production processes, enabling both recycling and industrial symbiosis. It responds to the core need of the circular economy and creates the bases of a new era of waste as a resource”.
UNITED STATES
JM to partner ClimeCo to develop low carbon solutions
Johnson Matthey (JM) has signed a memorandum of understanding with climate solutions company ClimeCo to accelerate the deployment of enhanced carbon capture solutions for industry. The two companies will help syngas producers, initially in hydrogen and methanol, to build the business case for reducing CO2 emissions from existing processes by up to 95%. The partnership combines JM’s experience in technology development and deployment with ClimeCo’s expertise in ESG strategy and regulatory analysis, empowering customers to make informed decisions on allocating capital for the deployment of JM’s CLEANPACE™ solutions, accelerate emissions reductions, and future-proof plants against the rising costs of carbon.
Syngas producers are responsible for approximately 70% of CO2 emissions in the chemicals sector. JM believes that the deployment of existing technology to over 150 grey hydrogen plants in Europe and North America alone could reduce CO2 emissions by over 100 million tons per year by 2030, equivalent to the annual emissions from approximately 40 million cars.
“Companies around the world are under pressure to reduce carbon emissions and meet net zero targets,” says Jane Too-good, Catalyst Technologies Chief Executive at JM. “Creating strategic partnerships allows us to offer our customers rounded and complete solutions. By working with ClimeCo, we will enable industries such as chemicals and refining, which rely on syngas, to quickly understand the regulatory frameworks, accelerate capital decisions for decarbonisation programmes and easily deploy proven technology solutions that can have an impact today, to create a cleaner world.”
BRAZIL
Unigel to build industrial-scale green hydrogen production
Unigel, one of the largest chemical companies in Latin America and the largest manufacturer of nitrogen fertilizers in Brazil, is investing $120 million in the development of a production site for green hydrogen. In the first phase of the project, Unigel will instal three 20 MW standard electrolysers from thyssenkrupp nucera, for a total of 60 MW. The plant will feed one of the largest green ammonia plants by capacity when it starts its production, at the Camacari Industrial Complex, with a capacity of 10,000 t/a of green hydrogen and 60,000 t/a of green ammonia. In future phases the company says that it plans to quadruple its production of green hydrogen by expanding the electrolyser plant to a multi-hundred MW facility, which will produce approximately 40,000 t/a of green hydrogen. The products will be offered to customers who aim to decarbonize their production chains, e.g. the steel industry, oil refining, and e-fuels. Green ammonia will also be used as a raw material in the manufacturing of fertilizers and acrylics.
“This project is the first of its kind in Brazil and reinforces the pioneering spirit of Unigel to produce green molecules on an industrial scale,” said Werner Ponikwar, CEO of thyssenkrupp nucera. “As Brazil is one of the world-leading countries in terms of installed renewable energy, we are pleased to enter this partnership to make green hydrogen an affordable energy vector already today. Only through large-scale production with robust, reliable and cost-effective technologies at competitive renewable power prices green hydrogen will become market-ready with widespread use.”
“Given the potential of Brazil in the generation of wind and solar energy, we believe that the country has a great opportunity to be a reference for the world in green hydrogen, a solution that brings versatility to transform renewable energy into raw materials and zero carbon fuels”, said Roberto Noronha Santos, CEO of Uni-gel. Brazil’s energy mix already has a very high share of renewables. Around three quarters of the energy used in electrolysis of the project comes from renewable sources. This makes Unigel and thyssenkrupp nucera first movers on an industrial scale in one of the most important markets in South America.
PORTUGAL
Partnership for sustainable aviation fuel
The Navigator Company and German-based developer P2X-Europe have agreed to create a joint venture, P2X-Portugal, to develop a facility for the industrial-scale production of sustainable aviation fuels based on green hydrogen and biogenic CO2 . The project will leverage Portugal’s competitive renewable energy sources and biogenic CO2 generated by Navigator’s biorefineries using sustainable forests, to produce net-zero synthetic feedstocks for the chemical industry and jet fuels on an industrial scale, fostering the decarbonisation of the aviation industry. P2X-Europe is a global pioneer in power-to-liquids project development and technology based on its parent companies’ H&R Group and Mabanaft’s market expertise in waxes and liquid fuels.
The facility will be located at Navigator’s Figueira da Foz site and will eventually capture up to 280,000 t/a of biogenic CO2 , combining this with green hydrogen from several hundred megawatts of renewable energy capacity, for a zero carbon production capacity of 80,000 t/a of kerosene and waxes using a Fischer-Tropsch polymerisation. Capex is estimated at e550-600 million for the first two development phases, with a production capacity of 40,000 t/a of synthetic products. Subject to a final investment decision by mid-2023, the project is scheduled to start commercial operations in 1H 2026.
FRANCE
Feasibility study on waste wood gasification
NextChem has been awarded a contract by Storengy to carry out an advanced basic engineering study for a waste wood and solid recovered fuel conversion plant to produce biomethane. Once the project has reached the final investment decision, targeted for the end of 2022, and has secured the required permits, NextChem will act as an EPC contractor for the methanation package of the project, which is to be implemented at Le Havre. Storengy, an ENGIE subsidiary, is a world leader in underground natural gas storage, and aims to become a leader in hydrogen storage and production of renewable gases.
NextChem will be responsible for the engineering and cost estimating for the syngas purification, methanation unit and methane upgrading of the plant, which will produce 11,000 t/a of renewable and low carbon natural gas (biomethane). French company COMESSA will be responsible for the design and supply of the chemical reactor. The technology to be used in the plant has already been successfully applied to the Gaya pilot plant near Lyon, owned by ENGIE, which validated the feasibility to produce biomethane. This will be the first commercial project in the world of its kind to inject in the grid methane produced through gasification of waste wood.
GERMANY
Joint venture for production of large-scale electrolysers
Siemens Energy and Air Liquide have formed a joint venture for the production of industrial scale renewable hydrogen electrolysers in Europe. The partnership aims to foster a European ‘ecosystem’ for electrolysis and hydrogen technology. Production is expected to begin in the second half of 2023 and ramp-up to an annual production capacity of 3 GW per year by 2025.
Air Liquide will a 25.% stake in the joint venture, and Siemens Energy the other 74.9%. The joint venture will be headquartered in Berlin, as will the factory that produces electrolysis modules (stacks) based on proton exchange membrane (PEM) electrolysis technology. In addition, Air Liquide and Siemens Energy have agreed to dedicate R&D capacities to the co-development of the next generation of electrolyser technologies within the framework of the partnership.
The strategic partnership will benefit from a portfolio of hydrogen projects combining both Air Liquide and Siemens Energy’s pipelines, targeting large industrial-scale hydrogen projects in collaboration with customers. This will create a solid basis for the required rapid ramp-up of electrolysis capacities and thus is expected to make competitive renewable hydrogen available sooner. One of the first projects is the Air Liquide Normand’Hy electrolyser project, with a capacity of 200 MW in the first phase, in Normandy, France.
“We want to be a driving force in hydrogen technology,” said Christian Bruch, CEO, and President of Siemens Energy AG. “To make green hydrogen competitive, we need serially produced, low-cost, scalable electrolyzers. We also need strong partnerships. Together with Air Liquide as a pioneer in hydrogen for over 50 years, we look forward to implementing innovative solutions and collaborating to shape this new hydrogen market.”
Demonstration plant for electrically heated steam cracker furnaces
BASF, SABIC and Linde have started construction of the world’s first demonstration plant for large-scale electrically heated steam cracker furnaces. By using electricity from renewable sources instead of natural gas, the new technology has the potential to reduce CO2 emissions of one of the most energy-intensive production processes in the chemical industry by at least 90% compared to technologies commonly used today. The demonstration plant will be fully integrated into one of the existing steam crackers at BASF’s Verbund site in Ludwigshafen, Germany. It will test two different heating concepts, processing around 4 t/h of hydrocarbon feedstock and consuming 6 MW of renewable energy. The start-up of the demonstration plant is targeted for 2023.
BASF and SABIC are both investing in the project, and the demonstration plant will be operated by BASF. Linde is the engineering, procurement and construction partner for the project and in the future will commercialise the technology. To support the development of the novel furnace technology, the project has also been granted e14.8 million by the German Federal Ministry for Economic Affairs and Climate Action under its “Decarbonisation in Industry” funding program. The program is supporting energy-intensive industries in Germany in their efforts to achieve carbon neutrality.
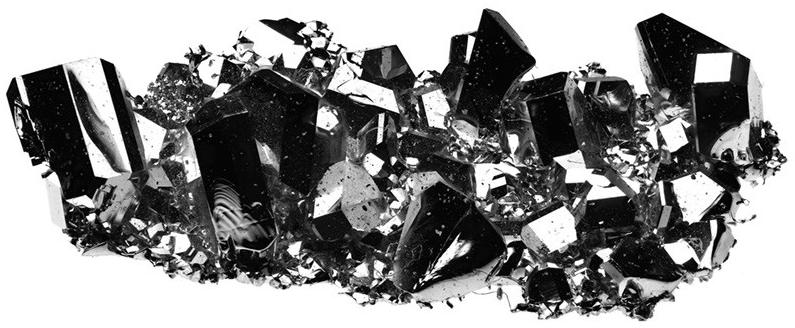
Yousef Al-Benyan, Vice-Chairman and CEO of SABIC said: “Our vision is to transform our business and to help address urgent global challenges through efficient carbon management. This project holds huge potential for all of the petrochemical industry around the world in our drive for low carbon emitting processes. With the milestone we are jointly announcing today on the start of construction, we hope that our three-party collaboration can inspire many more collaborations that ultimately bring the world to net-zero greenhouse-gas emissions through a circular carbon economy.”
The demonstration plant aims to show that continuous olefin production is possible using electricity as a heat source. The plant is designed in such a way that two heating concepts can be tested in parallel: direct heating applies an electric current directly to the process tubes inside the reactor; indirect heating uses the radiative heat of heating elements placed around the tubes. Testing these two concepts will make it possible to react flexibly to different customer and site requirements.
Partnership for new hydrogen electrolysis catalysts
South Africa’s Sibanye-Stillwater and Heraeus Precious Metals have agreed to jointly collaborate on research and development of novel platinum group metals containing catalysts with high activity and stability for proton exchange membrane (PEM) electrolysers for the production of green hydrogen. The project will be equally funded by both parties over a three-year period and the results mutually commercialised.
Platinum and iridium are currently essential components of catalysts for the generation of green hydrogen via PEM electrolysis. Iridium, however, is one of the scarcest platinum group metals, and its limited availability is a potential constraint on the future widespread adoption of PEM electrolysers. Reducing iridium loadings in catalysts is key to ensuring a sustainable hydrogen ecosystem, enabling PEM technology to be cost competitive to make triple digit GW scale electrolysis plants a reality within the next decade. Technologies that reduce or replace iridium with, for example, ruthenium, offer significant potential. The partners aim to develop a new, robust solution based on looking at the substitution of iridium with other metals, as well as developing more sophisticated metal oxide structures.
Heraeus brings significant technical expertise in the design of catalysts for PEM electrolysis and innovative solutions for the sustainable and cost-effective use of precious metals catalysts. “With our mutual know-how and resources, we are confident to develop novel solutions that will further strengthen the role of PEM electrolysis in the hydrogen economy”, said Dr. Philipp Walter, Executive Vice President New Business Development at Heraeus Precious Metals. “Without cost effective PEM electrolysis the targets for the ramp-up of the hydrogen economy cannot be achieved. We are ready to invest into a sustainable raw material strategy to make it happen.”
SWEDEN
Green methanol plant secures EU funding
The European Union Innovation Fund has selected Project Air, a production facility for sustainable methanol in Stenungsund, Sweden, as one of 17 large-scale green tech projects to be granted more than e1.8 billion in EU funding. Project Air is a collaboration between Perstorp, Fortum and Uniper, and has applied for e97 million funding as part of a total investment estimated at e230 million.
Project Air is based on using CO2 and other residue streams recovered from Perstorp’s ongoing operations, biogas from new dedicated plants, and hydrogen from a new large electrolysis plant to begin large-scale green methanol production by 2026. It will produce 200,000 t/a of methanol, replacing all fossil fuel methanol used by Perstorp in its existing downstream production processes.
DENMARK
Topsoe joins Circular Industrial Plastics initiative
Topsoe has joined a newly formed partnership, Circular Industrial Plastics, which consists of large Danish companies, which have committed themselves to increase the recycling of industrial plastics by at least 20% before 2025. Circular Industrial Plastics has a budget of 41 million Danish krone ($5.6 million), of which 18 million ($2.5 million) were granted by the Danish Eco-Innovation Program (MUDP) under the Danish Environmental Protection Agency. The ambition is to make knowledge and technology within circular plastic available for Danish companies. Besides Topsoe, the project partners comprise Coloplast, Novo Nordisk, Danfoss, BASF, Grundfos, and COOP.
The first step in the project will be to survey and investigate the plastic materials that are currently used in the companies and then create an infrastructure for further treatment and recovery. At the completion of the project, the objective will be to demonstrate full-scale solutions for selected products within the categories of medical, technical, and consumer plastics, and to demonstrate the interaction of new recovery technologies in the circular flow.
Supply agreement for methanol plant
Anaergia Inc. has signed an agreement to supply European Energy with up to 60,000 t/a of liquid biogenic carbon dioxide over the next 10 years. Biogenic carbon dioxide is released during the decomposition of organic matter such as food waste. All Anaergia plants use organic waste material to produce biogas, which is composed of methane and carbon dioxide. European Energy, a renewable wind and solar energy producer, will produce green methanol from this biogenic CO2 . Under the terms of an agreement European Energy had previously entered into with A.P. Moller-Maersk, the green methanol will be used to power a container vessel that Maersk is having built to operate on the carbon neutral fuel. Anaergia will provide the liquified CO2 from the anaerobic digesters that will operate at its plant being built in Tønder, Denmark.
“The benefit for us is the ability to sell the biogenic CO2 from our plants that is produced when we convert organic materials to methane and CO2 . By selling this CO2 instead of returning it to the atmosphere, our plants contribute to de-carbonising hard-to-abate sectors, such as shipping, while becoming more profitable, as we turn this waste gas from our plants into a useful fuel,” said Andrew Benedek, Chairman and CEO of Anaergia. “This is a great example of carbon capture and utilisation, a critical step on the path towards net zero. We are looking forward to working with European Energy on this innovative endeavour, and to potentially working with them on other projects in the future as the need for green methanol rises globally”.