Fertilizer International 510 Sept-Oct 2022
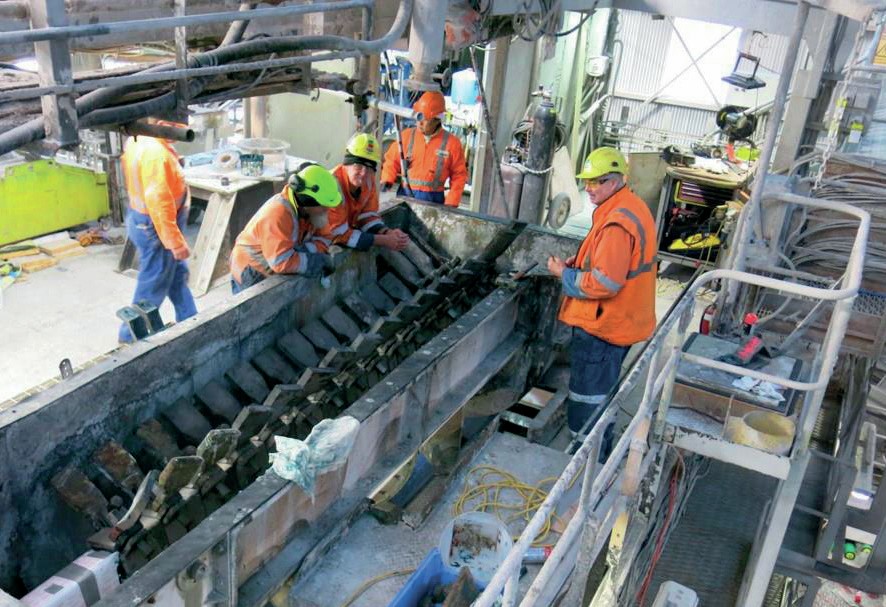
30 September 2022
The Bradley Broadfield superphosphate process
PHOSPHATE TECHNOLOGY
The Bradley Broadfield superphosphate process
The Broadfield process has remained a mainstay of the global phosphate industry since its introduction in the 1930s. Ian Hancock, vice president sales & operations, Bradley Pulverizer, explains it continuing success in superphosphate production worldwide
The Bradley Broadfield process is the global standard for single superphosphate (SSP) manufacturing. Its flexible and reliable design is based on more than 100 years of SSP manufacturing experience and can produce SSP economically from all known phosphate rock sources.
The process is also used to make:
- Triple superphosphate (TSP)
- Monoammonium phosphate (MAP)
- Diammonium phosphate (DAP)
- Monocalcium phosphate (MCP)
- Dicalcium phosphate (DCP)
- Partially acidulated phosphate
- Synthetic gypsum
- Iron sulphate
- Other acidic salts.
Bradley’s Broadfield process has been the workhorse of the phosphate fertilizer industry since 1936 and is offered in two designs:
- The Broadfield Den – typically used in applications of more than 30 t/h capacity
- The Broadfield Belt Den – its smaller ‘cousin’ for applications of less than 30 t/h capacity.
These two process options have been successfully employed worldwide to produce SSP, TSP, MAP and other finished phosphates. Its latest application is the production of partially acidulated superphosphate, a slow-release fertilizer used in end markets such as forestry.
Bradley’s long experience with the process has allowed the basic concept to be modified to suit individual products and the requirements of each manufacturer. The capacities and types of Broadfield Den design have also been expanded, with current models being able to offer maximum flexibility at the most economic cost. These intrinsic strengths make the Broadfield process ready to cater for industry changes over the next 85 years.
Origins of superphosphate manufacturing
It is well known that crops require a supply of nitrogen, phosphorus and potassium for their sustenance – and that using fertilizers to correctly control the soil’s NPK balance is therefore essential for the longterm sustainability and commercial viability of agriculture.
“Bradley’s Broadfield process has been the workhorse of the phosphate fertilizer industry since 1936.”
While phosphorus is abundant in nature, the majority is locked away in insoluble form within crystalline phosphate rock. Indeed, phosphorus in its natural form offers little nutritional benefit to plants, as these can only absorb nutrients from the soil solution. That means there is a need to convert insoluble phosphate rock into plant-available soluble phosphates to support the productivity of global agriculture.
Shortly after Justus von Liebig set out his theories for the acidulation of phosphate for fertilizer manufacturing, John Lawes patented a landmark superphosphate process in 1842 for converting insoluble phosphate rock into calcium phosphate (which is both water and citric soluble). Judged by later standards, the equipment initially developed for Lawes’ acidulation-based method was incredibly crude and far from ideal. To quote Lawes from the original patent, “with 4 common farm labourers and 2 cast iron pans I have mixed 2 tonnes in a day” in an open pile.
The process did improve subsequently, with ground phosphate being thrown into a stream of acid running into a brick lined pit. This was agitated by men standing around with rakes – which, understandably, was a thoroughly miserable job. Early mechanical manufacturing was also limited to batch production performed by a variety of different machines.
William Bradley became the first US manufacturer of single superphosphate in 1873 when he started production at the Bradley Fertilizer works in North Weymouth, Massachusetts. In 1886, his son, Peter Bradley, established the Bradley Pulverizer Company, to provide grinding and acidulating equipment for the fertilizer industry and general sale.
Then, in 1936, Bradley applied its 50+ years of experience in manufacturing equipment to the fertilizer industry by developing the Broadfield process, the first turnkey continuous superphosphate processing machine known as the Broadfield Den. Bradley’s long association with the fertilizer industry continues to this day.
In this article, we focus on single superphosphate (SSP) and triple superphosphate (TSP) production by the Broadfield process. We also highlight the innate flexibility of the process, particularly its ability to provide multiple revenue streams and accept variations in phosphate rock composition.
Making SSP and TSP
SSP is made by reacting non-soluble fluorapatite (the mineral present within phosphate rock) with sulphuric acid to produce soluble monocalcium phosphate and calcium sulphate. Gaseous by-products from the reaction include SiF4 and CO2 (released from associated calcium carbonate in the rock). The overall chemical reaction is summarised in equation 1 below.
TSP is made by reacting the phosphate rock with phosphoric acid. The reaction is faster than for SSP as deposition of calcium phosphate on the rock surfaces, which slows diffusion, is avoided. The TSP obtained is also a better grade product with a higher concentration of monocalcium phosphate. The overall chemical reaction is summarised in equation 2 below.
Superphosphate acidulation in the Broadfield Den
The Broadfield Den is a turnkey system specifically designed to continuously acidulate inert phosphate rock into water soluble superphosphate (Figure 1). In detail, it is actually comprised of a series of individual and interlocking equipment systems. Ultimately, proper calibration and maintenance of this entire system is required to ensure continuous production and profitable operation.
The information provided in this article assumes ‘typical working conditions’ based on general operational experience. In practice, however, each Broadfield Den is individually engineered for optimal output. Units are designed to meet the conditions specified by the end user, as well as the results of laboratory trials and testing, with confirmation of raw material composition being of primary importance.

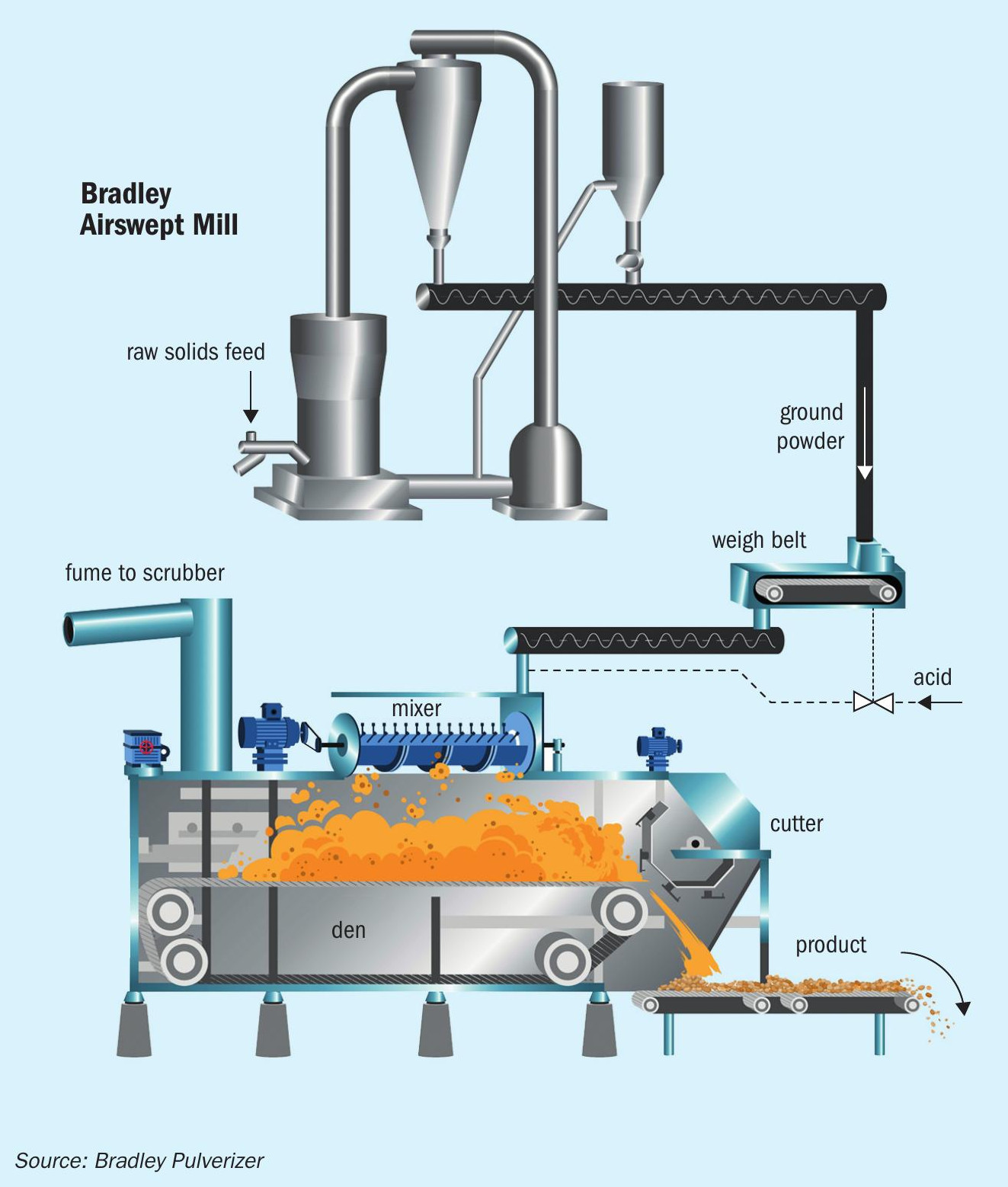
Superphosphate production begins with the grinding of insoluble phosphate rock (mainly fluorapatite, Ca3 (PO4 )2 CaF2 ) to a fine powder. This upstream process is carried out by a milling system, such as the Bradley BM20 Airswept Roller Mill, to generate phosphate rock particles of specified fineness (Figure 2). Typically, for sedimentary rock, the specified size is 75-90 percent passing 75µm (200 Tyler mesh), whereas igneous rock, due to its lower reactivity, is typically ground finer to 90+ percent passing 53µm.
Grinding significantly increases the particle surface area available for decomposition by acid. The finer the phosphate rock is ground, the faster the rate of reaction will be. The mill allows particle fineness to be adjusted to allow for differences in rock reactivity, so ensuring that adequate surface area is available for proper acidulation.
Mills which include properly specified and integrated classification systems enable more precise control of particle fineness – which requires adjustment for different rock types. Typically speaking, a properly maintained mill system will generate consistent particle size and yield rates, unless or until changes are introduced, such as differences in rock type.
The phosphate rock powder obtained is decomposed in two steps:
1. Firstly, dilute sulphuric acid reacts with part of phosphate rock to produce phosphoric acid. This reaction step takes place mainly in the Broadfield Mixer.
2. The free phosphoric acid produced then reacts with the remaining phosphate rock to produce monocalcium phosphate. This step takes place mainly in the Broadfield Den.
The first SSP reaction step occurs as soon as the diluted sulphuric acid (produced on-site) comes into contact with rock particles within the Broadfield Mixer (Figure 3), and takes just 1-2 minutes at typical rock fineness. The reaction is exothermic and releases steam, CO2 and SiF4 into the vapour space above the paddles. The paddles use shear forces to constantly create new reaction surfaces. This helps to minimise any reaction slowdown due to calcium sulphate deposition on unreacted rock particles.
The reaction slurry solidifies at the exit to the mixer and is discharged into the Broadfield Den. Mixer settings ensure
that the slurry spreads evenly across the den to give a level cake. Variations in the chemical analysis and temperature of the reactants, and in rock size analysis, must be minimised to allow good operation. The operator has tools at his disposal – such as the variable speed mixer drive and paddle design – to use in response to any change in mixer conditions.
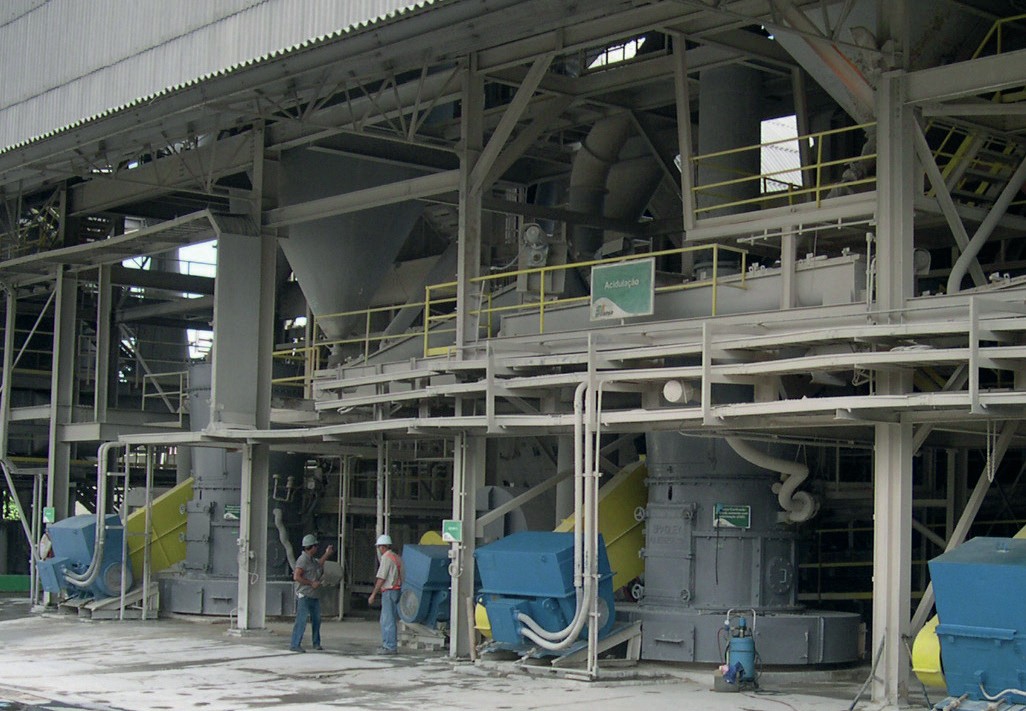
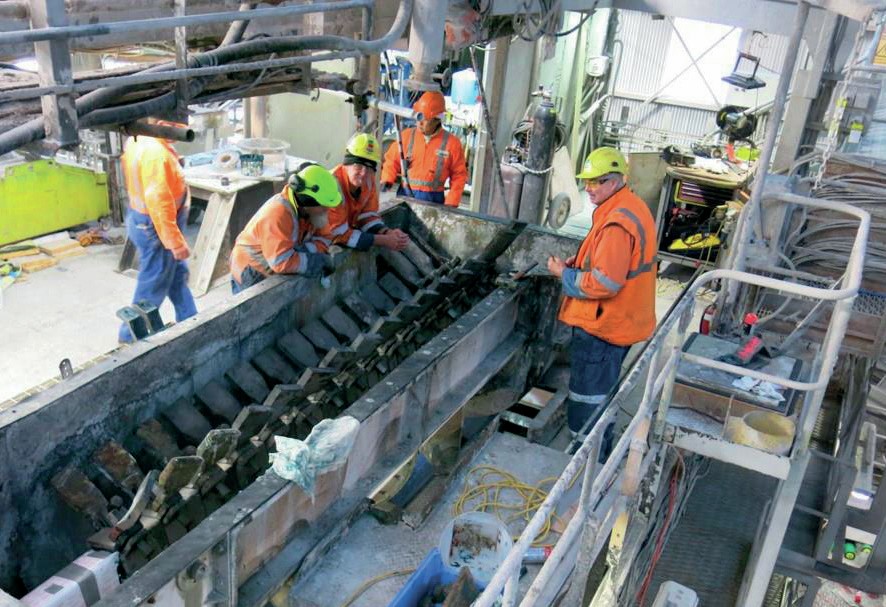
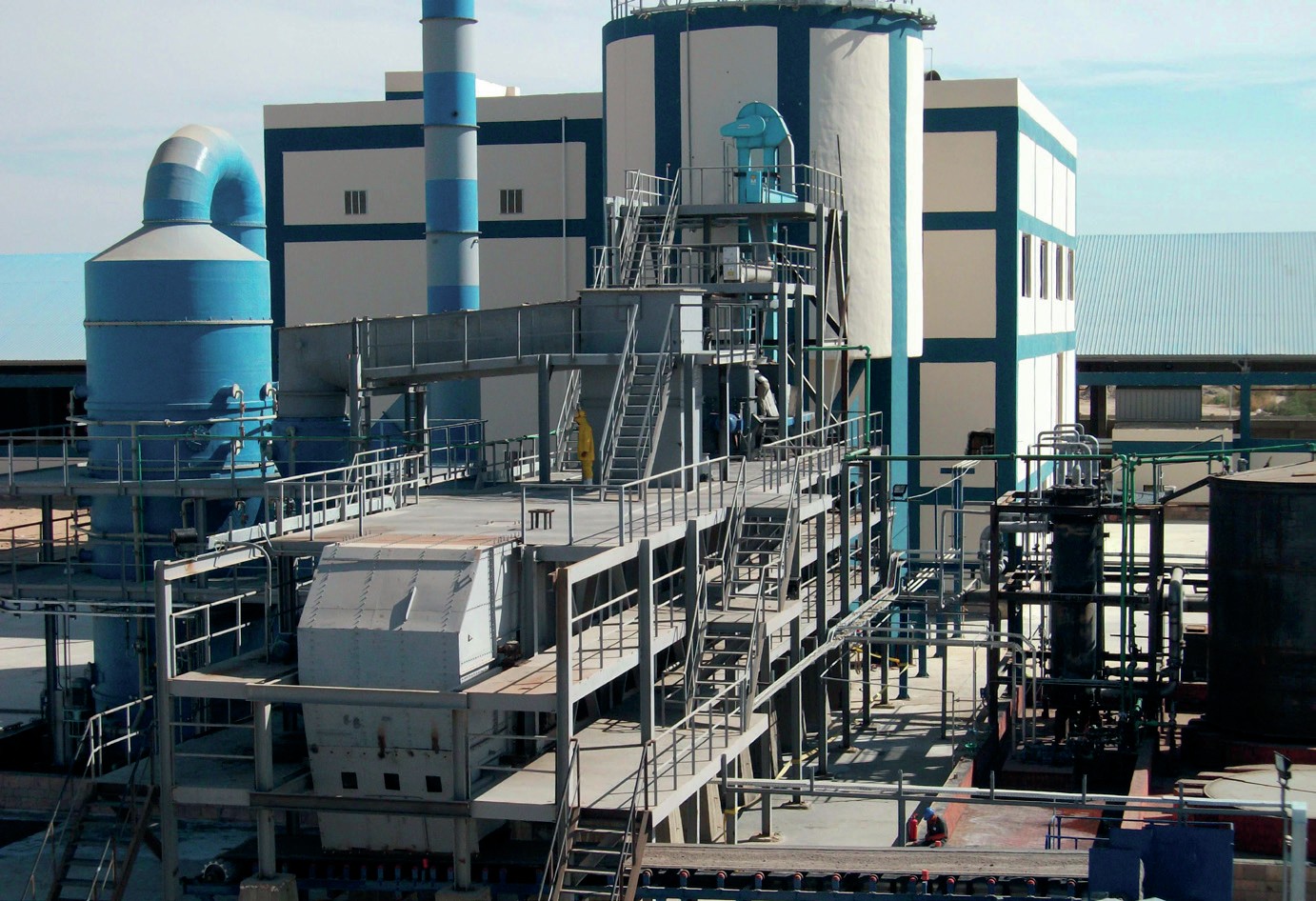
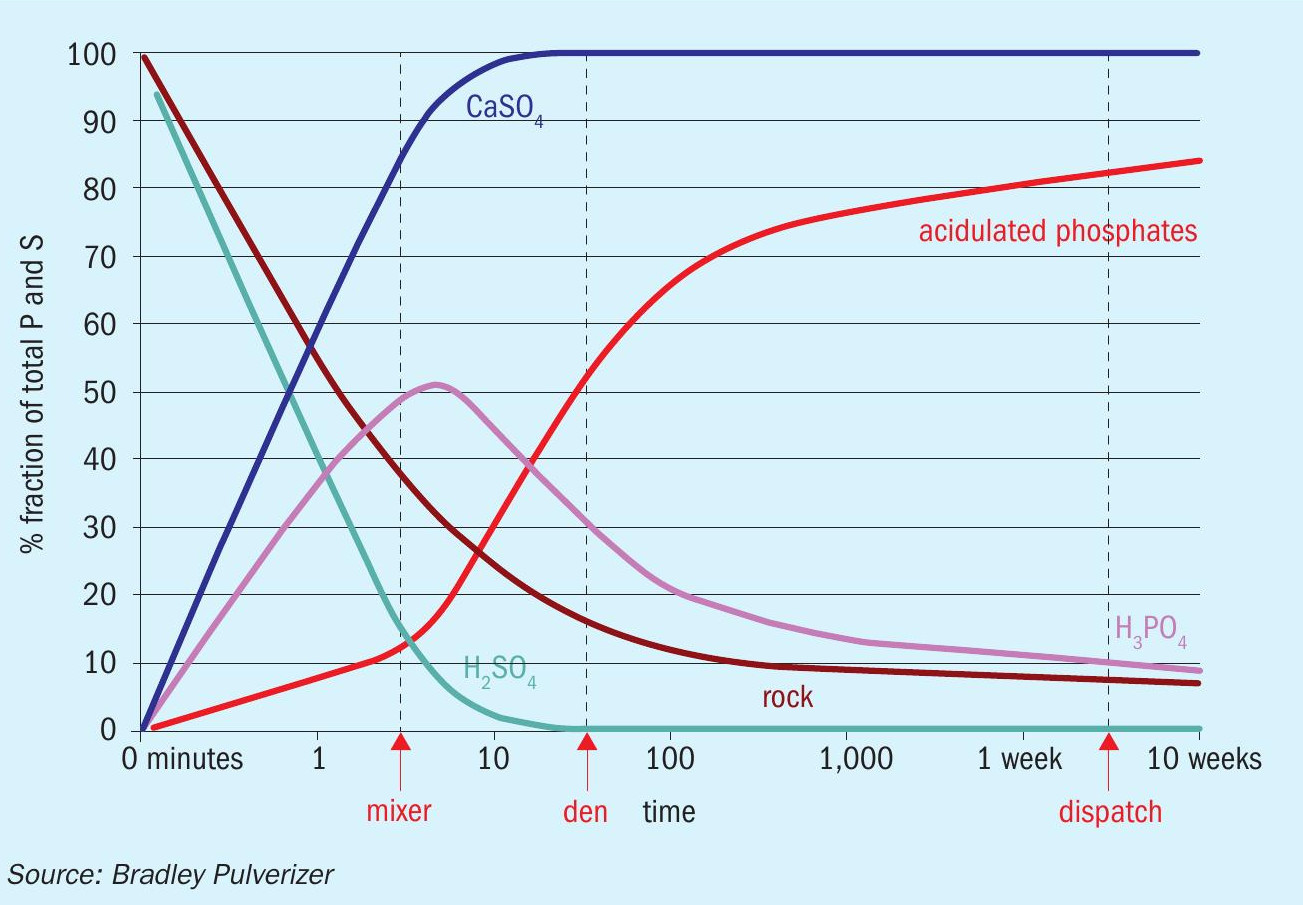
The second part of the reaction takes place in the Broadfield Den (or Broadfield Belt Den). This is where the slurry solidifies into a cake and can take from 10-60 minutes (average 40 minutes), depending on the rock type and grinding fineness.
The Broadfield Den unit is a rugged, gas-sealed, continuous, metal slat conveyor which moves slowly in a horizontal plane. It prevents the slurry from sticking to the sides by incorporating reciprocating sides at the inlet. Inside the unit, the reaction mass is kept in one block to minimise heat loss and maximise reaction rate. (Maintaining temperature is important as reaction rate typically doubles with every 10°C.) The conveyor of the Broadfield Belt Den differs from that of the original Broadfield Den, with a rugged polyurethane belt replacing the metal slats. Both units have similar reaction times. However, while relatively easy to maintain and clean, the Belt Den runs into capacity limitations above 30 t/h.
At the end of the den, a continuous rotary cutter is used to disintegrate the reaction mass and shave off SSP powder. This falls onto a wide, slow moving cutter belt which then passes through a gas-sealed transfer point for storage and final reaction outside of the Den. The floor of the Den is inverter driven. This avoids overloads during emergency shutdowns by allowing the hardened reaction mass to be fed slowly to the cutter.
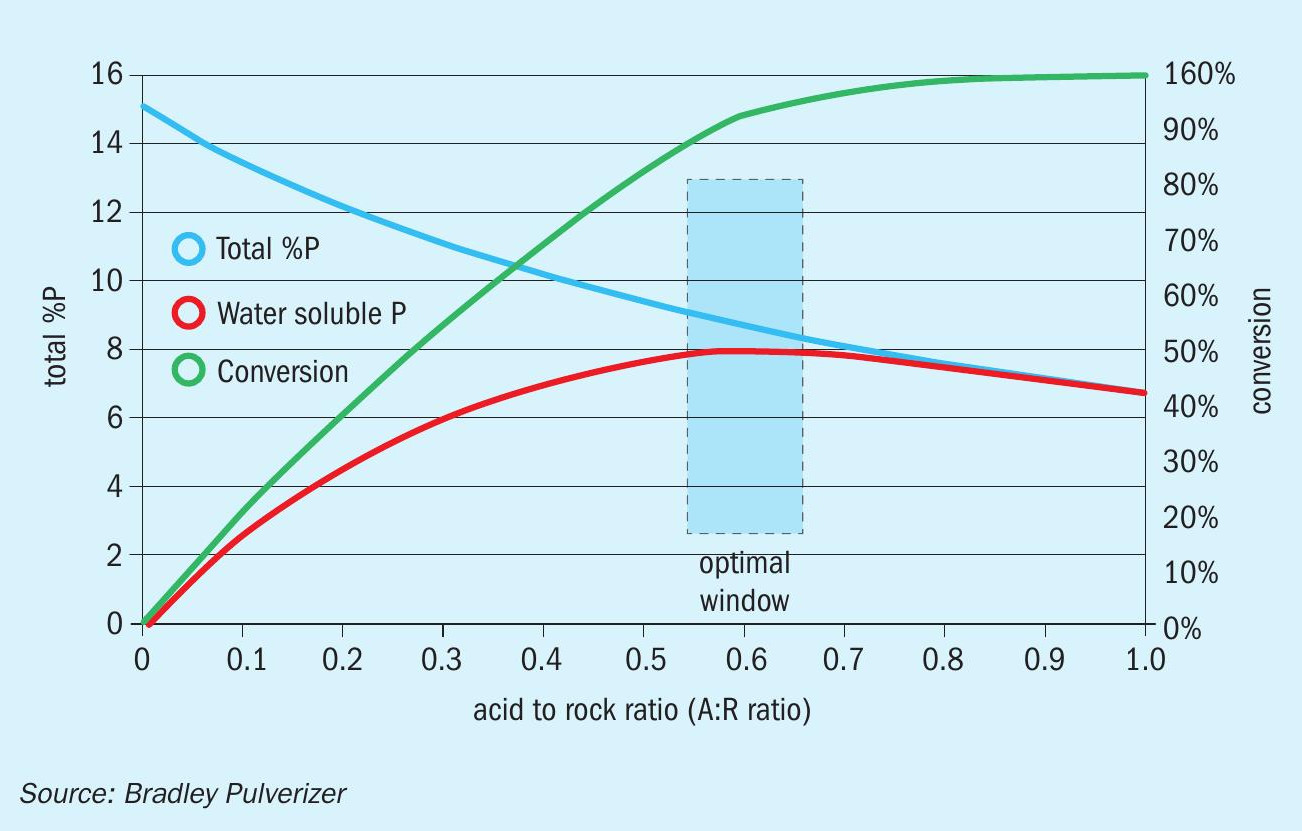
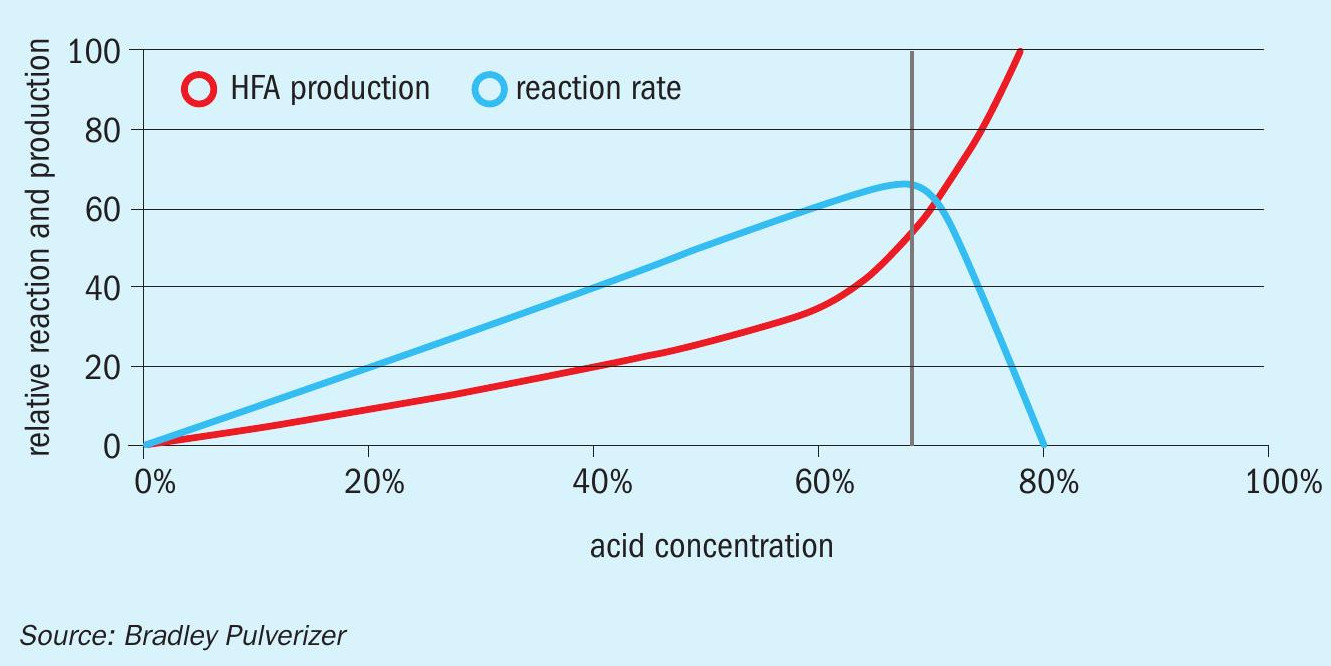
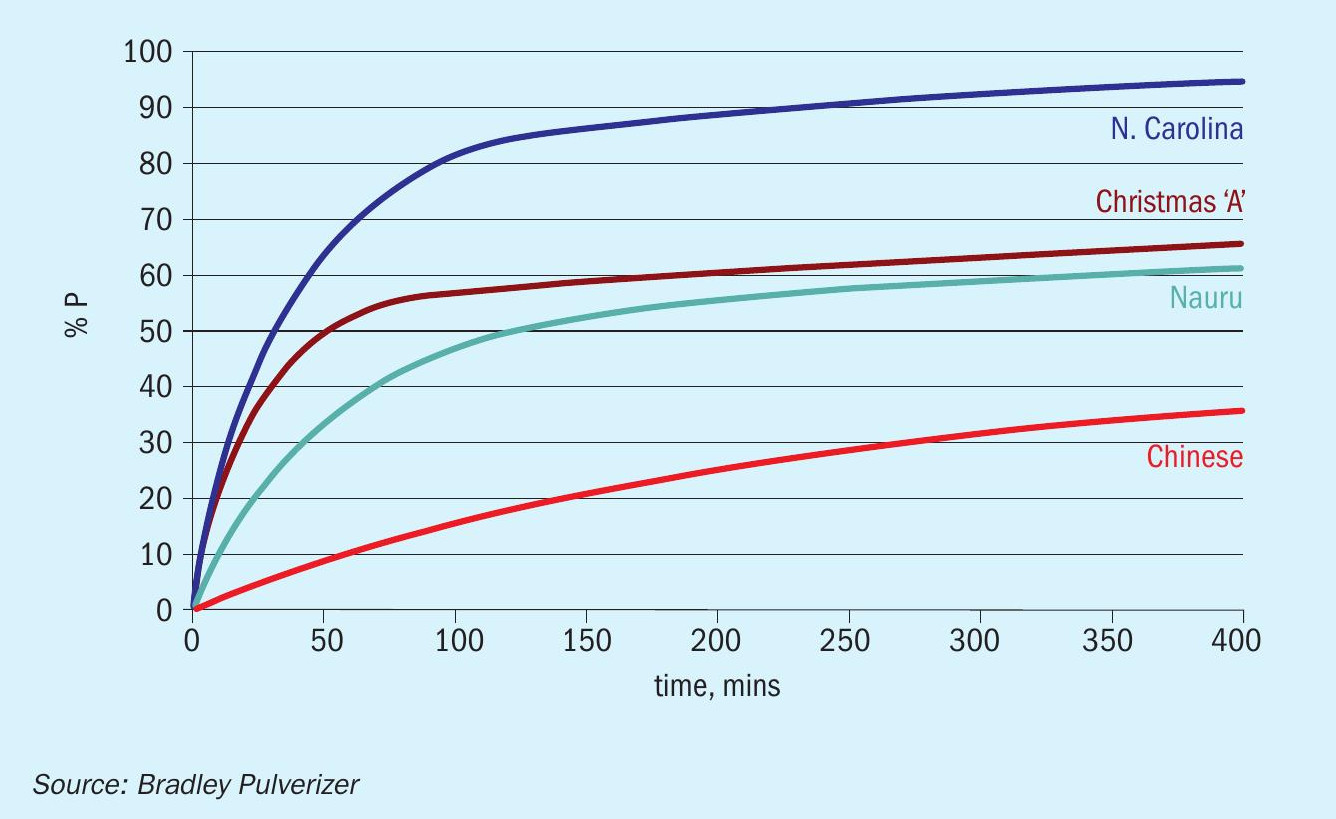
Disintegrated SSP generated by the rotary cutter is transported to storage for the final curing stage. Curing allows the reaction to reach its end point and reduces residual free phosphoric acid (Figure 5). Sufficient storage capacity is required to ensure that the bagging machines (or granulation plant) have enough SSP powder to handle after an average curing period of 15 days, or at least 10 days minimum.
An exhaust fan extracts fluoride-containing gases from the mixer and the den and sends these to a gas scrubbing system where a series of water sprays remove fluoride from the air stream. This generates HFA (hydrofluosilicic acid – H2 SiF6 ) solution which is recycled back to the SSP/TSP mixer to provide fluorine for acidulation. This closed loop system is unique to the Bradley Broadfield Den.
The overall process for TSP manufacture is essentially the same. In fact, the Broadfield process uses the same den for both SSP and TSP production, although smaller turbine or cone mixers are used for TSP as the reaction is much faster. TSP powder takes 1-2 weeks to cure and can then be granulated as a straight or blended fertilizer with standard equipment.
Operational considerations
Acidulation in the Broadfield Den is a continuous process that requires good coordination between the various feed streams and equipment so they operate together in equilibrium. However, as ideal process conditions are almost never met in practice, Bradley’s Broadfield Dens and Belt Dens are designed to operate effectively at between 60-110 percent of their rated output. This provides operators with the necessary flexibility to adjust for changes in feed composition and/or plant conditions while ensuring that consistent end-product quality is maintained. Some of the key operational considerations are highlighted below.
Rock blend. Individual phosphate rock sources and shipments will have different parameters for total phosphorus content, reactivity rates, impurity levels (i.e., cadmium), fluorine volatilisation, and odorous compounds. To adjust for these differences, rocks from different sources are blended to establish the desired chemical composition and achieve the necessary ‘operational window’. This is important as the chemistry of the rock blend will directly influence the equilibrium of the entire system, including milling fineness, acid concentrations, mixer speeds, den residence time, and granulation conditions etc.
Acid-to-rock ratio (A:R ratio). The phosphoric acid that is produced in the acidulation process initially increases the A:R ratio, even though it reacts subsequently to form calcium phosphate. This bump in acid generation must be properly accounted for when accurately determining the ideal A:R ratio. Additionally, high iron, aluminium, and magnesium levels must also be considered, as these will also reduce the achievable A:R ratio. These elements slow down the reaction rate by increasing the viscosity of the liquid phase and making the ex-den product sticky. These effects can be offset by increasing the fineness of the rock, increasing the residence time in the den, and increasing the reaction temperature.
Acid strength. Optimal acid strength is around 68-70 percent (Figure 7), depending on the phosphate rock blend. Acid strength is an important parameter as it can negatively affect the reaction rate, as follows:
- If it is too weak, acid strength slows reaction rate by reducing reaction temperature and/or reducing reaction ‘chances’.
- If it is too strong, acid strength slows reaction rate by reducing liquid diffusion and particle-liquid contact, and/ or blinding rock reaction surface with insoluble calcium sulphate. Strong acid also increases gaseous emissions.
“Commercial superphosphate production requires Broadfield process equipment that is both rugged and flexible.”
Reaction surface area. Reaction rate (as measured by two percent citric acid solubility, Figure 8) is affected by the available reaction surface area, which in turn is influenced by particle-size distribution, particle porosity, and crystal structure. Available surface reaction area is increased by milling fineness – although it is important to note that fineness:
- Only affects rock reactivity
- Does not change overall conversion
- Has a strong effect on reactive rock, but a weak effect on non-reactive rock.
Summary
Large-scale commercial superphosphate production requires Broadfield process equipment that is rugged enough to:
- Continuously crush up to 50 t/h of phosphate rock
- Mix it with a steady stream of acid
- Enable the exothermic reaction required for proper acidulation.
Yet, this large-scale equipment must also be flexible enough to cope with, and adjust for, unavoidable changes to process variables – such as the natural disparities in phosphate rock chemistry. At any given time, the ongoing process reaction will be affected by:
- Reactivity of the rock and mill fineness
- Acid strength
- Reaction temperature
- Acid-to-rock ratio
- Mixing efficiency (mixer performance, time in mixer)
- Impurities, poisons and blinding effects.
In our experience, if just one of the above conditions is not correctly adjusted for, then acidulation will be sub-optimal.