Fertilizer International 510 Sept-Oct 2022
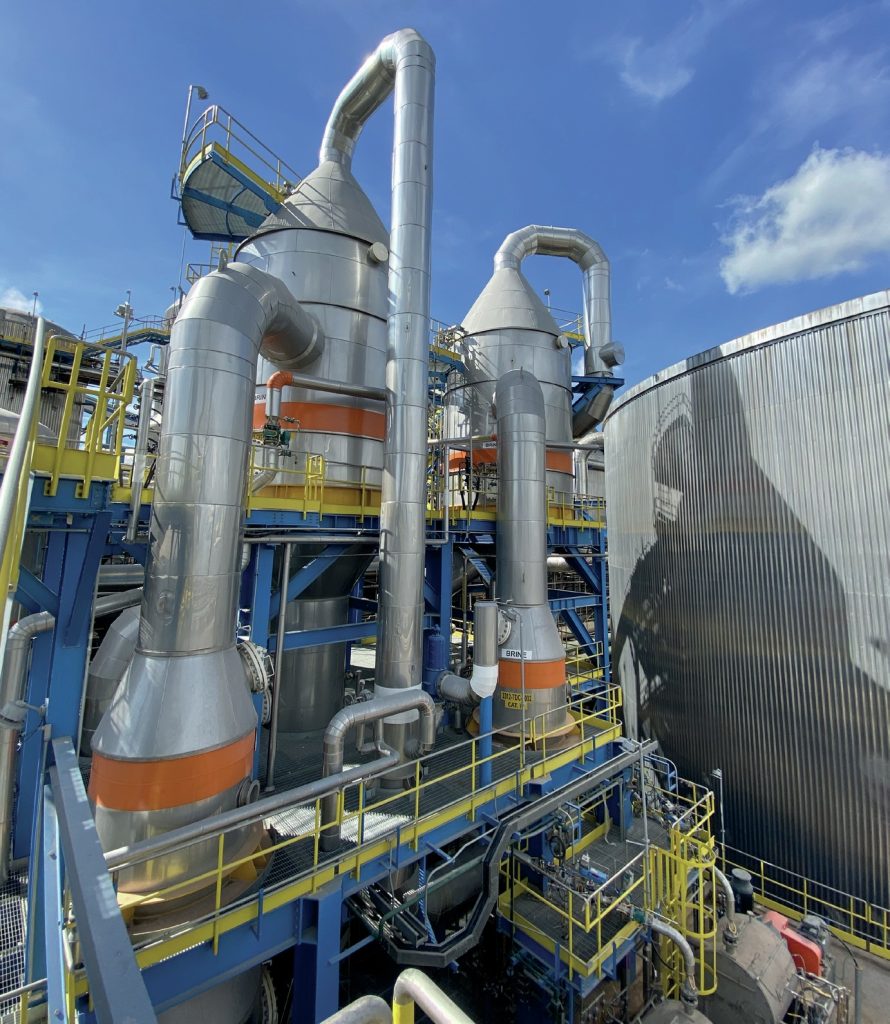
30 September 2022
Wastewater treatment technologies
NUTRIENT RECOVERY
Wastewater treatment technologies
Effective and efficient wastewater management is a vital task that is being aided by the introduction of new treatment technologies. The recovery of economically-valuable nutrients from wastewaters is another priority.
VEOLIA WATER TECHNOLOGIES
Creating SOP from wastewater
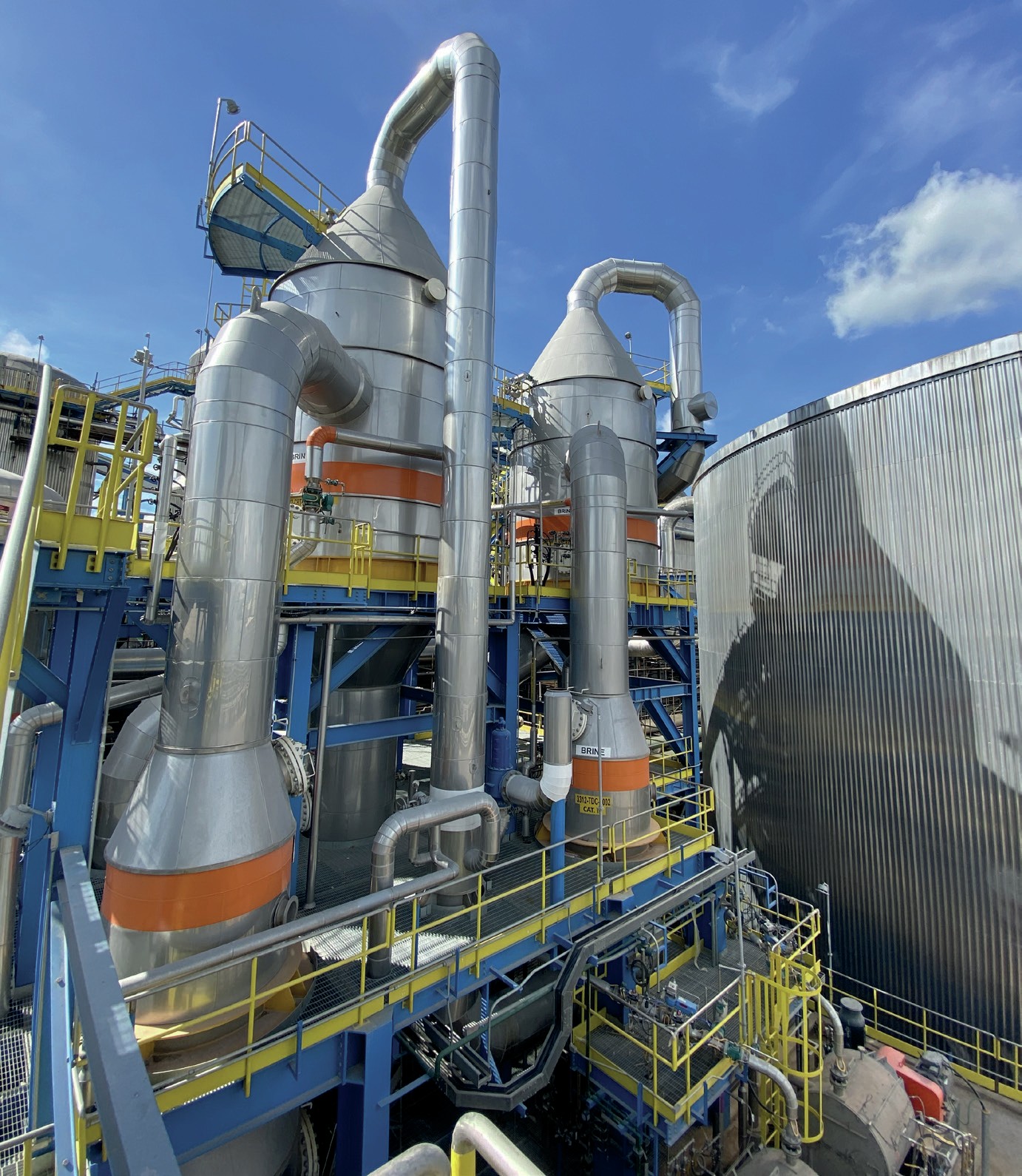
As we move to a more circular economy, companies will increasingly be looking to minimise their waste generation by investing in sustainable processes. This will shift the focus onto proven and successful production technologies that offer a triple win – for the bottom line, the environment and society.
SOP for the future
Veolia’s HPD® crystallisation technology is capable of manufacturing high-quality water-soluble potassium sulphate (SOP, sulphate of potash, K2 SO4 ) using a range of different feedstocks. One innovative production option is to manufacture SOP from the wastewater generated at pulp and paper mills.
In this process, glaserite (a double salt of SOP and sodium sulphate) is initially recovered via a black liquor ash treatment system and then converted into highquality SOP crystals for fertilizer use. For this and other feedstock options, the crystallisation process holds the key when it comes to controlling the purity and size of the final SOP crystals.
Case study
A pulping production plant in Brazil uses a washing process to increase the purity of the pulp. This generates an organic-rich liquor stream that is recovered for energy production. It is necessary, however, to remove chemicals from this liquor to avoid the undesirable build-up of chloride and potassium during the recovery cycle, as these can create corrosion and boiler fouling if left uncontrolled.
To prevent this fouling and corrosion, 650 t/d of precipitator ash from the boiler is being treated using Veolia’s proprietary Enhanced Chloride Removal Process (ECRP™). This crystallisation technology is highly effective at removing undesirable impurities. Valuably, the system is also able to take a previously unwanted waste material and turn it into a useful fertilizer product for growing the next crop of trees for pulp production.
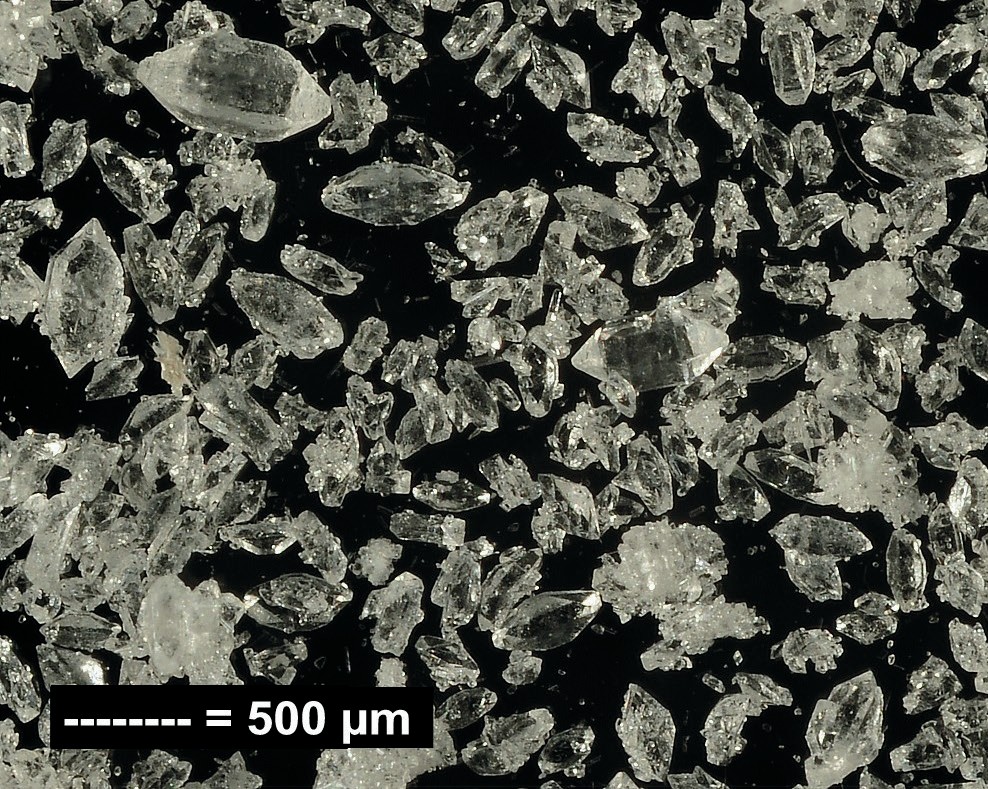
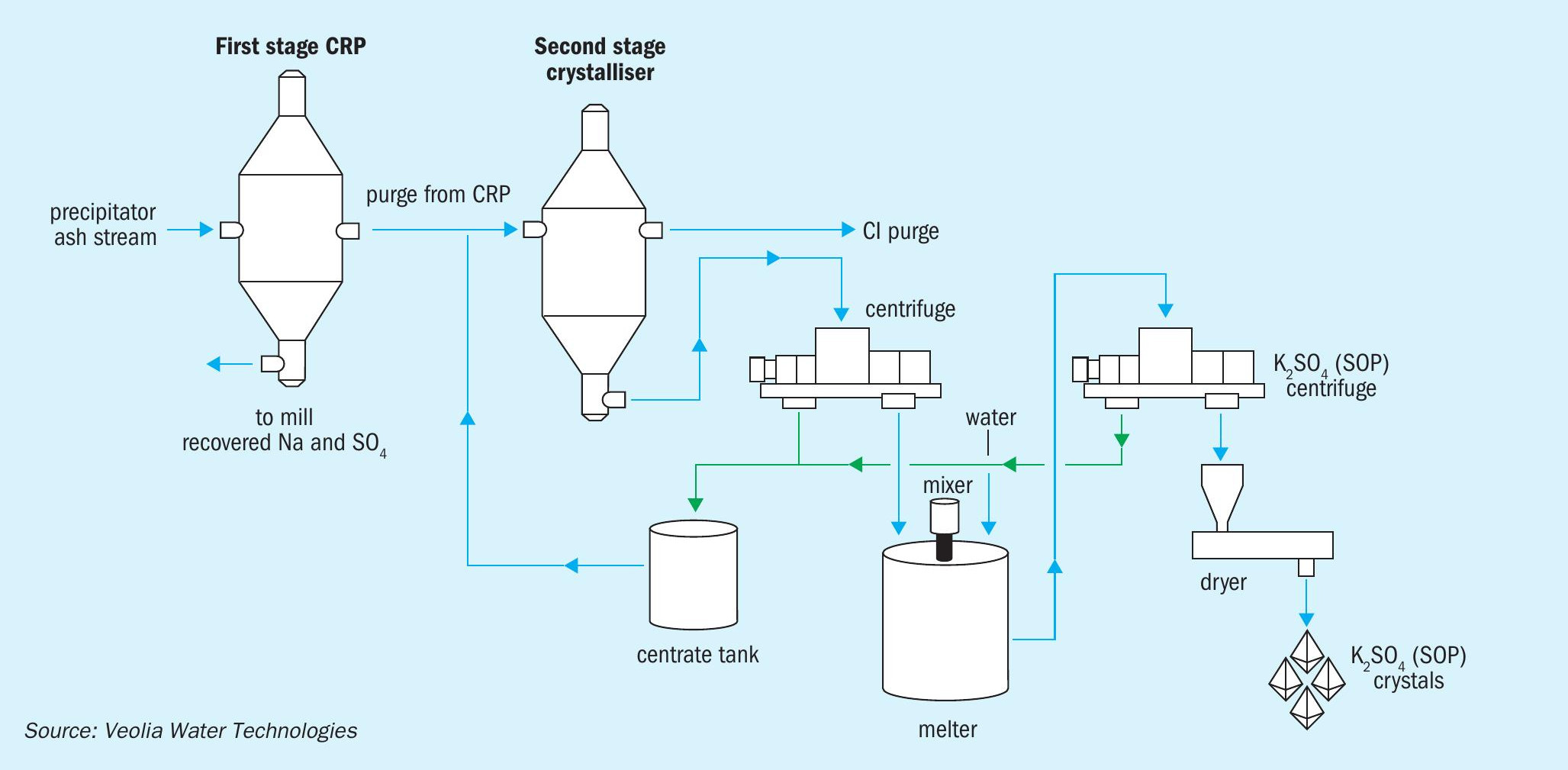
Key advantages of ECRP™
Veolia’s ECRP™ system enables the recovery of fertilizer from ash treatment purge. This allows mills with high potassium inputs to achieve high chloride and potassium removal rates while minimising sodium losses. The system provides: l Rapid operational payback l Reduced sulphate levels in mill effluent l Returns potassium back to the forest via the production of SOP fertilizer – creating a closed nutrient loop l Saves on cost and usage of chemical consumables such as caustic and sodium sulphate.
Enhancing chloride removal
With ECRP™ technology, Veolia has enhanced the chloride removal process (CRP) by:
- Increasing its efficiency
- Reducing discharge volumes
- Recovering high value SOP fertilizer.
At most pulp mills, the focus of chloride removal is to minimise corrosion and boiler fouling. A conventional CRP is therefore typically operated to maximise chloride removal while minimising soda losses. Potassium removal, however, is not controlled and generally ‘floats’ in the 70-90 percent range.
“Veolia’s HPD® crystallisation technology is capable of manufacturing high-quality water-soluble potassium sulphate from pulp and paper mill waste streams.”
Additionally, in conventional CRP, optimising potassium and chloride removal can only be achieved by reducing sodium recovery to 60-80 percent. ECRP™ , in contrast, can maximise chloride and potassium removal while maintaining high sodium recovery.
The ECRP™ process
ECRP™ is a two-stage crystallisation process (Figure 1). The first stage consists of a conventional CRP system operating close to atmospheric pressure. This crystallises sodium salts and returns these to the recovery cycle.
The second stage crystalliser, by operating at a lower temperature to reduce solubility, recovers the remaining potassium salts as crystallised solids. These are dewatered in a centrifuge and then partially ‘melted’ with water in mixer. Purified, high quality SOP crystals are finally obtained following subsequent centrifuge and drying steps.
A portion of the second stage crystalliser mother liquor is purged from the mill to further enhance overall chloride removal efficiency. The remainder of the mother liquor, meanwhile, is recycled to the first stage crystalliser to recover sodium salts.
As well as generating a valuable speciality fertilizer, Veolia’s ECRP™ system is capable of achieving the following removal efficiencies:
- Chloride removal of 90-95 percent
- Potassium removal of 95-99 percent
- Sodium recovery of 90-95 percent.
Conclusion
Forward-looking companies can now seize on higher-margin opportunities in the fast-growing agricultural market by producing specialty fertilizer products. As the above case study demonstrates, these can be manufactured from previously unexploited feed stocks, both profitably and sustainably, by incorporating innovative processes such as HPD® ECRP™ crystallisation technology.
ORGANICS GROUP
Ammonia recovery from wastewater
At a time when resource recovery and the circular economy are of growing importance, this article highlights the exciting opportunity to remove, recover and recycle ammonia from wastewater using waste heat.
Anaerobic digestion – a commercial success story
In recent times, anaerobic digestion (AD) has become firmly established as a commercially viable form of renewable energy generation. For example, there are now 486 operational AD plants in the UK, according to the National Non-Food Crops Centre (NFCC), with a further 343 under development.
The AD process produces biogas. This consists of methane and carbon dioxide, as well as various traces gases, and is used in two main ways:
- It can generate power directly via combined heat and power (CHP) gas engines
- Alternatively, it can be upgraded into natural gas-quality biomethane for grid distribution.
Nutrient-rich digestate, a by-product generated by AD, can also be used as fertilizer.
Ammonia and anaerobic digestion
Ammonia is released in the AD process by amino acid degradation during acidogenesis. Although ammonia is an important nutrient source for bacterial growth during AD, at high concentrations it can be lethally toxic to bacteria – having an inhibitory effect on bacteria that benefitted from its presence at lower concentrations.
Due to the increasing global use of highly calorific food waste as a biogas-producing AD feedstock, examples of ammonia poisoning are now being encountered more frequently at AD plants.
Proteins generate ammonia
Protein-rich substrates in food waste make particularly good starting materials for methane generation, and are therefore of great interest for commercial biogas production. Unfortunately, high loadings with such materials often correlate with process instability, as they are associated with increased ammonia release during the acidogenesis phase of AD.
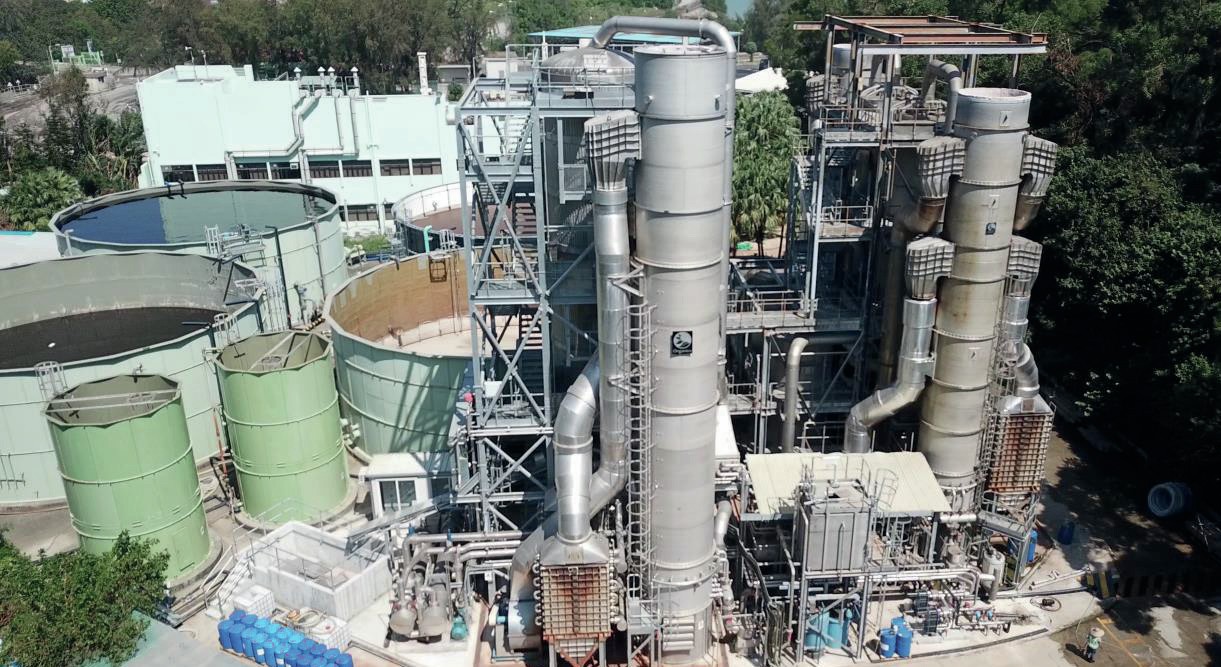
The same issues arise within landfill sites. In Hong Kong, for example, the high loadings of protein in the waste streams entering landfills, namely meat and meat products, have resulted in high ammonia concentrations within the landfill leachate. Readings of up to 6,000 mg/L are common. Similarly, during the outbreak of mad-cow disease in the UK, it was necessary to dispose of animal carcasses within sanitary landfills. In such sites, leachate was encountered containing ammonia concentrations of up to 9,000 mg/L.
Managing excess ammonia
Ammonia exists in two forms in wastewater – ammonia gas (NH3 ) and ammonium ions (NH4+ ). Both forms can directly and indirectly cause inhibition in an AD system, although NH3 is generally recognised as the main inhibitor.
Although the exact threshold will vary, biogas production (i.e., AD performance) typically drops off as ammonium concentration in the anaerobic digester increases above 1,000 mg/L – with digestion fully inhibited at around 5,000 mg/L concentration. Effective control of ammonia levels is therefore a key requirement at AD plants. Fortunately, a wide range of options are available to achieve this.
In the past, lowering the pH to decrease the free ammonia concentration, or dilution of the digester contents with water, were the two most common ammonia control methods used at AD plants. Alternatively, adding lignocellulosic biomass can also successfully increase the C:N ratio of the substrate in the digester.
Thermal ammonia stripping
The Organics Group has developed another option to control and remove ammonia at AD plants – a thermally-driven air-stripping process capable of achieving 98.5 percent ammonia removal. pH adjustment is not usually a requirement in this thermally-driven process, and the air flow necessary is substantially less than the requirement for pH-driven air-stripping. Heat is, however, essential to raise the temperature of the wastewater stream. This can lead to significant operational costs if a source of waste heat is not available.
Thermal ammonia stripping and pH-driven ammonia stripping have a similar underlying approach to ammonia removal and employ similar techniques to achieve this. Both use air-stripping as a simple desorption process. The ammonium ion is also broken in both cases, by either heat (thermally-driven process) or the addition of a base (pH-driven process). While pH-driven ammonia stripping requires considerably larger quantities of air, as much as ten-fold higher, this process is not as temperature dependent as thermal stripping, which can be halted by a temperature drop.
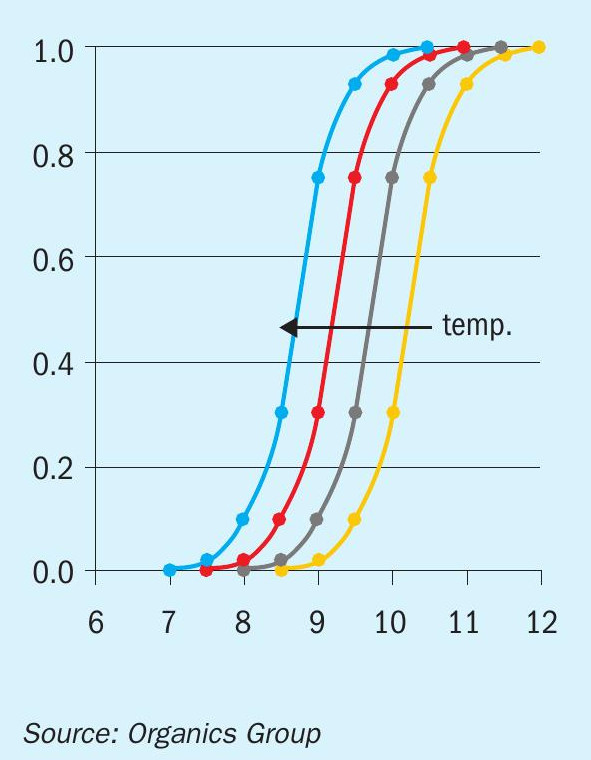
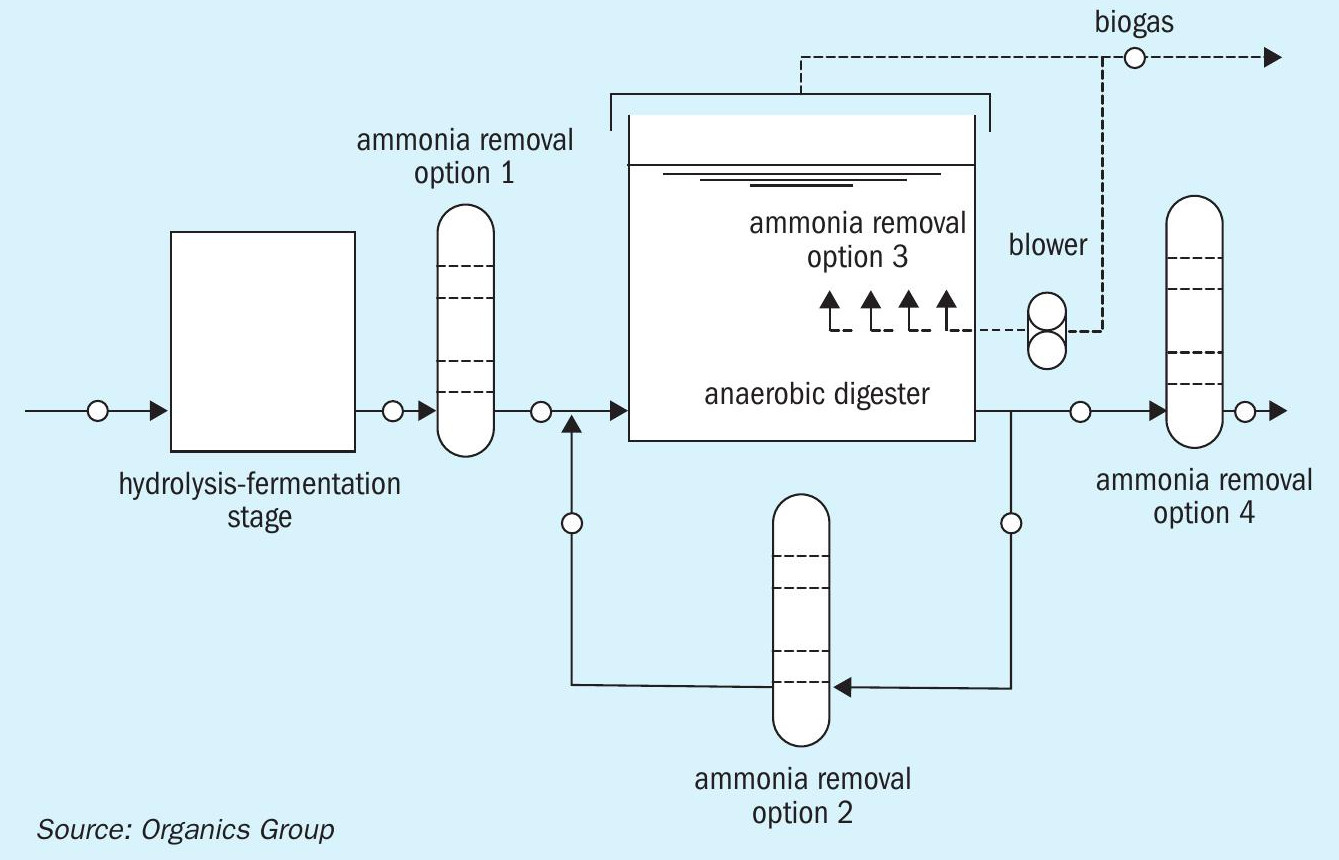
Process fundamentals
As mentioned above, the ionic form (NH4+ ) and the gaseous form (NH3 ) of ammonia are encountered in wastewater. The equation governing the relationship between these two forms is as follows:
In this reaction, dissociated ammonia ion (NH4+ ) is converted to undissociated ammonia gas (NH3 ) by the addition of a base (OH– ), such as sodium hydroxide. As the temperature of the water increases, so the amount of free ammonia gas also increases. The balance of this equation is therefore a function of both pH and temperature – with low pH and/or low temperature pushing the balance towards NH4+ .
The ratio of ammonia in the gas phase (NH3 ) to the total ammoniacal nitrogen (NH3 + NH4+ ), known as ‘f‘, is expressed as follows:

A family of curves illustrating the relationship between ‘f’ and pH at different temperatures is shown in Figure 1.
As the temperature increases (arrow to the left, Figure 1), the pH necessary to maintain a value of ‘f’ decreases. This shows the basic function of the thermal ammonia stripper, i.e., to reduce the need to increase pH while maintaining ammonia removal performance.
Examples of thermal ammonia stripping
Thermal ammonia stripping has been used in Hong Kong since 1997, the year the former crown colony reverted to Chinese sovereignty. The technology has been applied in Hong Kong to leachate from landfill sites, as well as the effluent from a food waste AD plant.
it is not surprising that Hong Kong has been the incubator for this world-leading technology, given its high population density, coupled with the demanding environmental standards enforced by its Environmental Protection Department.
The removal of ammonia is a recurrent challenge for wastewater engineers. In Hong Kong, this is accomplished with low operating costs, to high standards, by equipment with a small footprint, using novel thermal ammonia stripping technology. While, to date, thermal ammonia stripping installations have focused on the needs of Hong Kong, the technology is gaining ground in other countries where environmental compliance is being taken seriously. Its prime function is also moving from leachate clean-up applications into AD.
The systems developed in Hong Kong are for discharge flows. Thermally-driven air stripping was chosen in 1997 as the core nitrogen removal process for the West New Territories (WENT) landfill site in Hong Kong, currently operated by Suez. At the time, thermal efficiency was not a performance criterion. This was because, with a design flow rate of 1,800 m3 /day, recently upgraded to 3,350 m3 /day, as much landfill gas as necessary was available for use.
The initial design duty for this first plant was to reduce an influent ammonium concentration of 6,700 mg/L to 100 mg/L in the effluent. The WENT installation now removes 14.5 tonnes of ammonia daily. Building on this success, similar processes have been installed at six additional sites around Hong Kong subsequently.
Impressive efficiency gains
Landfill gas in Hong Kong was once seen to be more of a nuisance than an opportunity. However, thermal efficiency has gradually moved up the list of performance priorities since the first plant was commissioned, to the point where it is now a tightly measured variable. Impressively, the thermal power requirements of the ammonia removal process have been reduced to just 20 percent of that first 1997 installation – thanks to improvements in energy recovery, process optimisation and patented innovation. Options to capture and use waste heat have also been developed.
Ammonia removal options for AD
Over time, thermal ammonia air stripping technology has also become less specific to Hong Kong, due to the above efficiency improvements and a deeper operational understanding. This means the process is now better adapted for use in a range of varied applications in other countries. One major interest is its use for ammonia management in anaerobic digestion, both for ammonia process control purposes and for preventing the environmental release of ammonia in discharge flows.
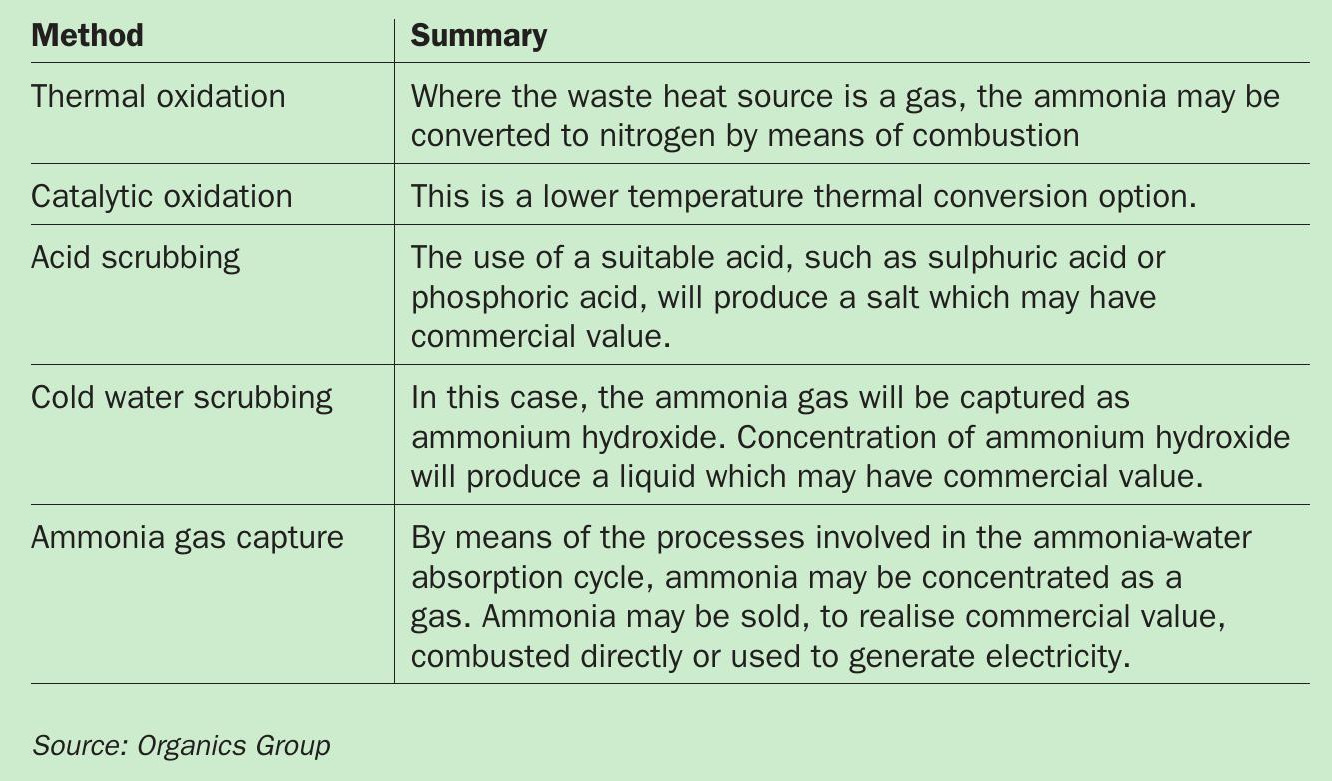
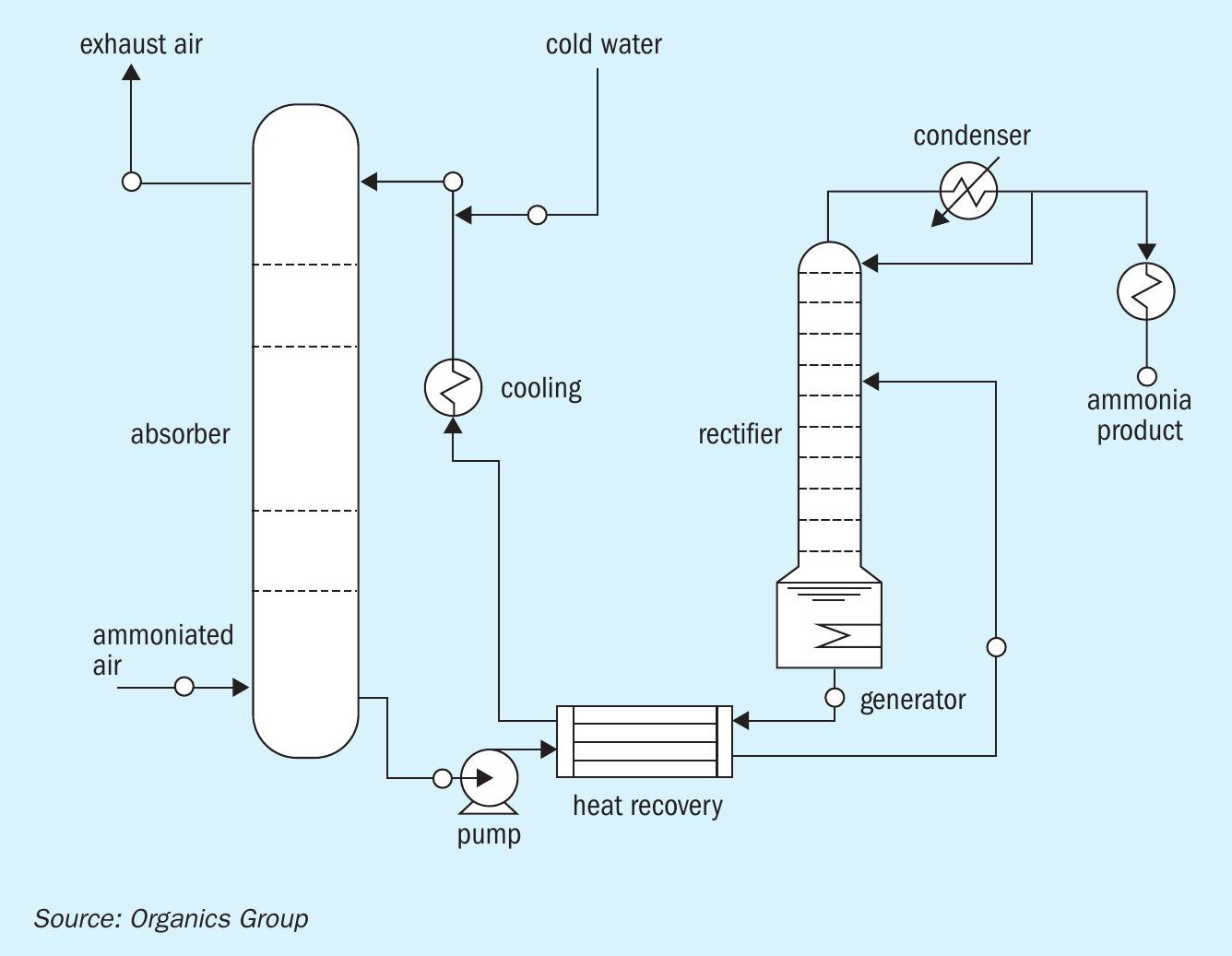
Within a typical AD unit, there are four locations where reduction or removal of ammonia is possible. 1. At the hydrolysis-fermentation stage prior to digestion 2. In a recycle flow during digestion 3. Within the main digester vessel during digestion 4. Or post digestion, prior to discharge.
These four removal options are shown schematically in Figure 2.
Research into the feasibility of removing ammonia during or after the hydrolysis-fermentation stage (option 1) has met with limited success. The most practical removal options are therefore within the digester itself (option 3), in a recycle flow (option 2) or from the effluent (option 4).
Option 3 – stripping ammonia within the digester vessel – leaves limited scope for process control. However, work on this option has been successfully completed by several researchers using biogas as a stripping medium. Therefore, with low-strength ammonia, this may well be an option to consider in our view.
Options 2 and 4 – ammonia removal from recycle and discharge flows – therefore offer the main opportunities for ammonia control in large-scale commercial AD plants. While the former option will impact the AD process and lead to improved performance, the latter is essentially a matter of discharge compliance.
Key performance strengths
In reality, there are no perfect solutions for dealing with ammonia removal from wastewater in the industrial sector. The performance characteristics of each technology need to match up with the specific application and individual circumstances. For thermally-driven ammonia stripping, the following attributable benefits can help indicate situations where performance is optimised and deployment is merited:
- High removal rates may be achieved in a relatively small footprint
- The process is particularly suited to high-strength ammoniated wastewater
- No major costs are incurred for chemical additions
- Greenhouse gas (GHG) production is mitigated by avoiding nitrous oxide formation
- Compared to biological processes, relatively rapid start-up can be achieved (1 or 2 hours)
- There is no risk of biology failure
- Substantial savings may be available through the avoidance of carbon-source costs
- There is no sludge formation
- The system is relatively easy to operate compared to biological processes.
Ammonia recovery and use
Subsequent to ammonia stripping from wastewater, there is a need to remove ammonia gas from the stripping air. This can be recovered or disposed of, according to the operator’s requirements. Several methods/routes for removing ammonia from stripper air are shown in Table 1.
Organics Group has developed a process that enables the recovery of either ammonium hydroxide or anhydrous ammonia. This approach further develops our two key, overriding process themes:
1. Employing waste heat
2. Avoiding the use of chemicals.
Ammonia-water systems are also already well understood, being widely applied in refrigeration and adsorption cooling.
The process flow diagram (PFD) for Organics Group’s ammonia recovery system is shown in Figure 3. Clean, cold water is used to remove ammonia from stripping air. The water is then heated to concentrate the ammonia gas as ammonium hydroxide. Additional concentration and separation then makes the formation of anhydrous ammonia possible.
The obvious corollary to the recovery of ammonia is the question of what to do with it. In fact, there are many end-use options, ranging from simple on-site combustion, to use as an on-site fuel for modified engines or fuel cells, or various commercial applications requiring aqueous ammonia, anhydrous ammonia or ammonium salts. However, the main market for ammonia remains agriculture, with 85 percent of current global ammonia production being used in fertilizers.
Pilot projects
The waste and wastewater industry has recently woken up to the commercial opportunities presented by ammonia recovery, including its potential as a hydrogen carrier and source. The Organics Group – through our participation in two pilot projects – is at the vanguard in the wastewater sector when it comes to the practical implementation of innovations to recover ammonia and generate hydrogen.
The Organics Group, together with Northumbrian Water, Anglian Water, Cranfield University, Warwick University, and the Wood Group, has successfully won funding from the UK government’s water regulator Ofwat. The six partners are collaborating on a pilot plant to recover ammonia from highly ammoniated wastewater generated by a large sewage treatment plant in northeast England. The aim is to produce green hydrogen – a first for the global wastewater industry – by cracking the recovered ammonia. The funding for this was secured through a competition launched by Ofwat to encourage innovation in wastewater treatment.
Organics Group is also investigating resource recovery from wastewater as part of a multi-partner pilot project funded by the Europe-wide REWAISE R&D programme. The project is led by the Spanish utility Aqualia, with Severn Trent and Coventry University also participating. It will firstly recover and concentrate ammonia and then produce hydrogen from wastewater via an enhanced electrolysis process.
Both projects take advantage of Organic Group’s experience and track record in full-scale ammonia recovery from the wastewaters generated at landfill sites and anaerobic digesters located in Hong Kong.
Water utility companies the world over are seeking to mitigate their energy use and reduce GHG emissions. Indeed, many of these water companies, including those in the UK, are now committed to achieving the challenging target of net zero CO2 emissions within the next 10 years.
Looking ahead, given the highly promising technological achievements to date, the impact of energy costs on conventional operations, and with the encouragement of forward-looking legislation, it is highly likely that ammonia recovery will be a key component in the drive for greater efficiency and carbon neutrality in the wastewater treatment sector.