Sulphur 403 Nov-Dec 2022
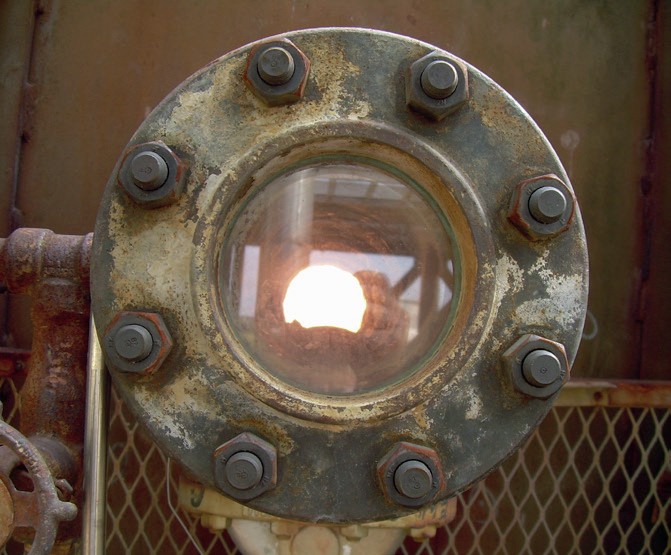
30 November 2022
A novel thermal stage process camera for sulphur plants
SULPHUR PLANT MONITORING
A novel thermal stage process camera for sulphur plants
Enhancing the reliability of sulphur plant starts in the thermal stage. Matt Coady and Martin McCallister of Delta Controls report on a recently developed and launched insertable process camera that monitors the vessel interior of online Claus thermal reactors, providing valuable process data which will allow plants to make better informed operation decisions.
Over the past decade, the refining industry has seen a shift from achieving environmental targets to emphasising reliability. Unreliable sulphur plants now have financial implications by posing the risk of reducing refinery throughput. In addition, long term plant reliability is a priority as runtimes are being extended between planned shutdowns. How can the reliability of sulphur plant operations increase to maintain throughput and avoid outages? A logical place to start is with the Claus thermal reactor in the sulphur recovery unit (SRU) as the thermal stage is most prone to fail due to intense operating conditions. Thus, reliability improvements made here are beneficial to the entire SRU performance.
However, improving reliability is a complex and challenging task. The trend of increasing instrumentation installed on the thermal reactor to achieve more process awareness is common. Instrumentation – including analysers, flame scanners, and temperature indicating devices such as pyrometers and thermocouples – is often connected to the SIS system and is key to understanding the process status. While these instruments provide critical process data, there still remains many unknowns when it comes to the health of the thermal reactor. Current instrumentation cannot effectively detect damage to the burner, refractory or tubesheet protection system. Often an operator’s only method for visual inspection is through sight ports, which have a number of common issues. Sight ports fundamentally suffer from a narrow field of view due to the constriction of the bore along the sight path. Additionally, sulphur often occludes on the glass or in the bore which limits the view as seen in Fig. 1.
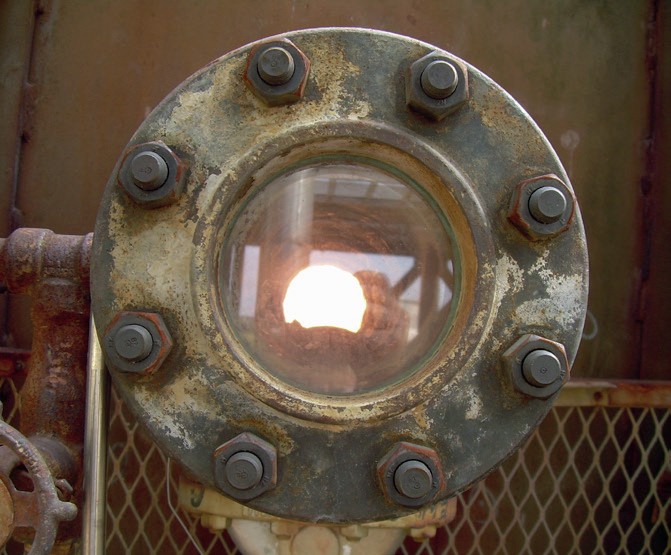
In the effort to increase reliability, the challenge becomes how to predict and identify a root cause before symptoms appear or are detected by current instruments. The ability to internally view the inside of a vessel will allow users to make pre-emptive operational decisions based on the condition of the burner, tubesheet, and refractory. High resolution images and video feed of these reactor components provide the data needed to make informed decisions, avoid major equipment failures, and reduce vessel downtime. Delta Controls Corporation is excited to announce the launch of ProSpection™ , a process camera designed for continuous online inspection of the SRU thermal reactor.
ProSpection™ process inspection camera
The primary design considerations for the process inspection camera include achieving the best view of the vessel’s interior, the camera’s usability and reliability, and most importantly the camera assembly’s safety.
A wide-angle lens placed at the refractory hot face with an insertable probe assembly provides the most useful view of the critical components of the vessel interior (Fig. 2). A number of significant challenges for this design were taken into consideration by the Delta Controls design team. For example, the camera and lens have a melting point near 65°C, which requires the use of a consistent cooling system to survive the internal operating temperature of the Claus reactor. Another challenge was developing a stainless steel probe assembly that could be sufficiently cooled while accurately maintaining a surface temperature above the sulphur dew point corrosion but also below high temperature sulphidation.
To overcome these material, corrosion, and temperature limitations, the camera design incorporates a patent pending thermal regulation system that uses water or air circulated through a series of channels to accurately regulate the probe’s temperature between the sulphur dewpoint corrosion and high temperature sulphidation limits, as well as maintain the camera circuitry within its temperature limits. Furthermore, the thermal regulation system maintains the lens temperature above sulphur’s freezing point to prevent lens occlusion.
PROSPECTION™
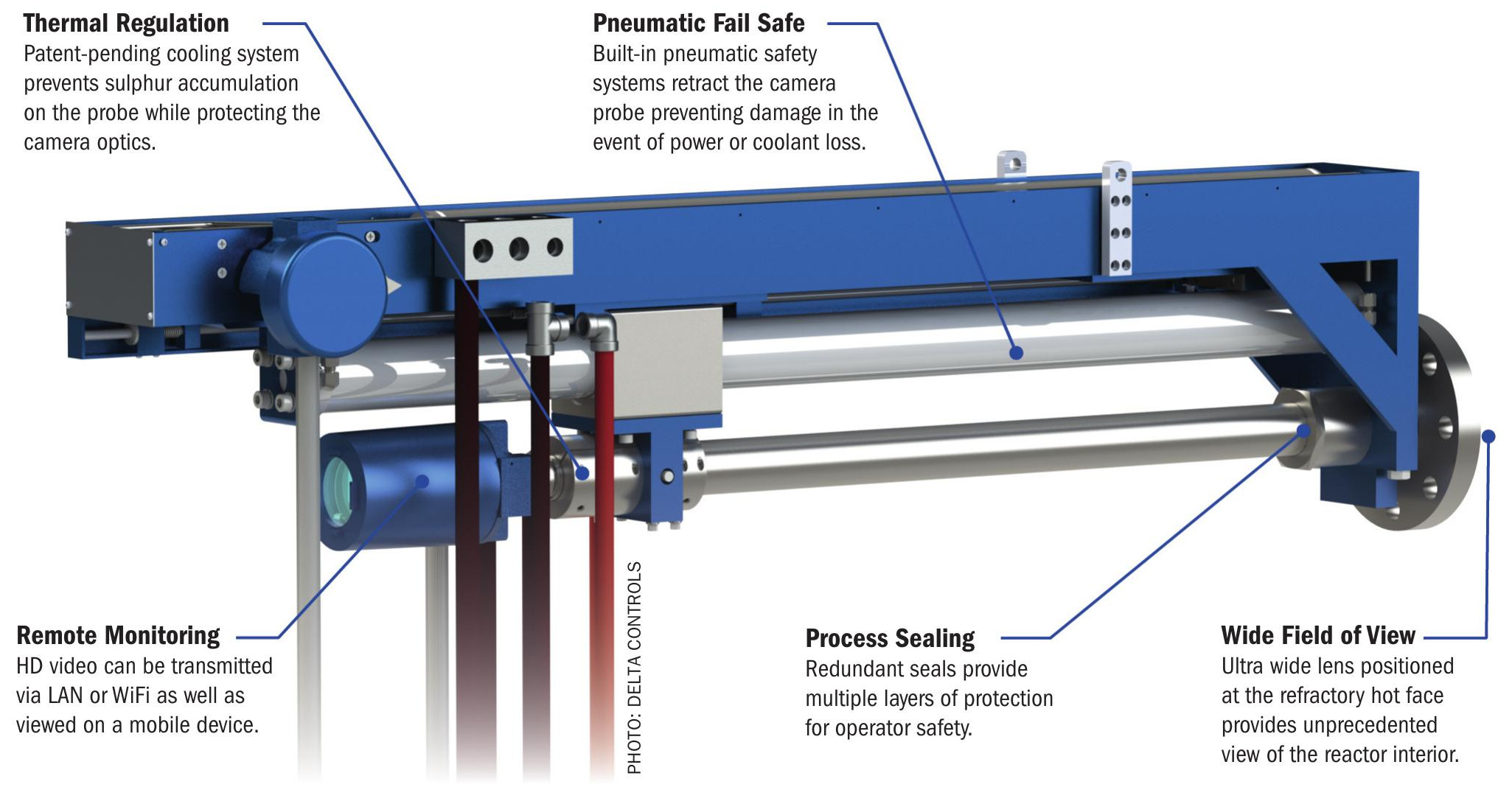
The camera probe assembly is designed to be inserted through an isolation valve while a vessel is online and is either left installed indefinitely for long term monitoring or used for a temporary inspection. A flanged seal assembly mounts to a three-inch or larger nozzle flange and incorporates multiple redundant seals to allow for the camera to insert and retract without process leakage. As an added safety feature, a nitrogen supply applies a positive back pressure to the seals that is higher than the process pressure. Thus, in the event that a seal is compromised, nitrogen would flow through the damaged seal and into the reactor. An inline flow meter would indicate flow and therefore that a seal had been compromised. This system serves to prevent any process gas leakage as well as an indication of seal integrity.
To automate the insertion and retraction of the camera probe assembly, the ProSpection™ inspection camera utilises a pneumatically driven extraction system that actuates the camera into and out of the vessel through the flanged seal assembly. This system allows for failsafe features to optimise the camera for long-term operation. The camera can automatically order its own retraction from the process for any number of fault conditions such as loss of coolant, rising camera temperature, loss of power, or loss of instrument air. As an additional fail-safe feature, the system also contains an onboard air tank with enough air capacity to safely remove the camera in the event of an air supply loss.
To support the camera and the extraction assembly on a nozzle flange, the Delta Controls engineering team designed a suspension system that offloads any force from the nozzle (Fig. 3). The suspension system supports the weight of the camera system and allows for the entire assembly to freely move as a vessel thermally expands. This support design allows for travel in multiple directions as the vessel expands radially and longitudinally during start-up. Additionally, the system provides uniform support as the assembly’s centre of gravity changes when the camera moves from the inserted or retracted state. There is a supplemental spring and damper assembly that stabilises the camera when the vessel experiences vibration.
The camera’s optical design is optimised for the incandescent environment found inside a sulphur recovery unit. A series of optical filters protect the camera lens from infrared energy and filter specific light wavelengths. Video and images are sent to the control room in the visual spectrum and can be set to provide continuous live video or capture still images from specified intervals. The ProSpection™ process inspection camera is designed to function well with units using conventional firing as well as the brighter interior of a unit using oxygen enrichment.
Use cases: monitoring critical components
The ProSpection™ process inspection camera allows new views into online reactors that provide more information and thus can better guide decision-making. Common critical areas of interest include the burner, refractory lining and tubesheet protection system. Catching early failures in any one of these areas can be a huge benefit to the unit operator.
Starting with the burner, continuous monitoring with a camera can provide significant data improvements over other instrumentation such as flame scanners. Burners are oftentimes the root cause of many larger failures seen in sulphur plants. A failing or poor performing burner can not only cause poor chemistry but also damage to the refractory, waste heat boiler, checker wall and tubesheet. The camera’s view allows operators to detect a burner tip that has become distorted or out of alignment. A loss of tip concentricity can lead to flame impingement on the refractory, poor mixing, and further damage to the burner assembly. The end result is extremely poor reactor performance that likely would not be detected using traditional methods. Burner tips can also suffer from other failure mechanisms, such as back burning and the tip metal being consumed by the flame front. These changes in the burner structure would be visible by comparing images taken during routine inspections using the camera. If the burner is found to be compromised, operators could choose to take actions such as reducing flow rates to the burner or shifting throughput to another unit. All of this can be done before further damage is made to the refractory, tubesheet, waste heat boiler, and vessel.
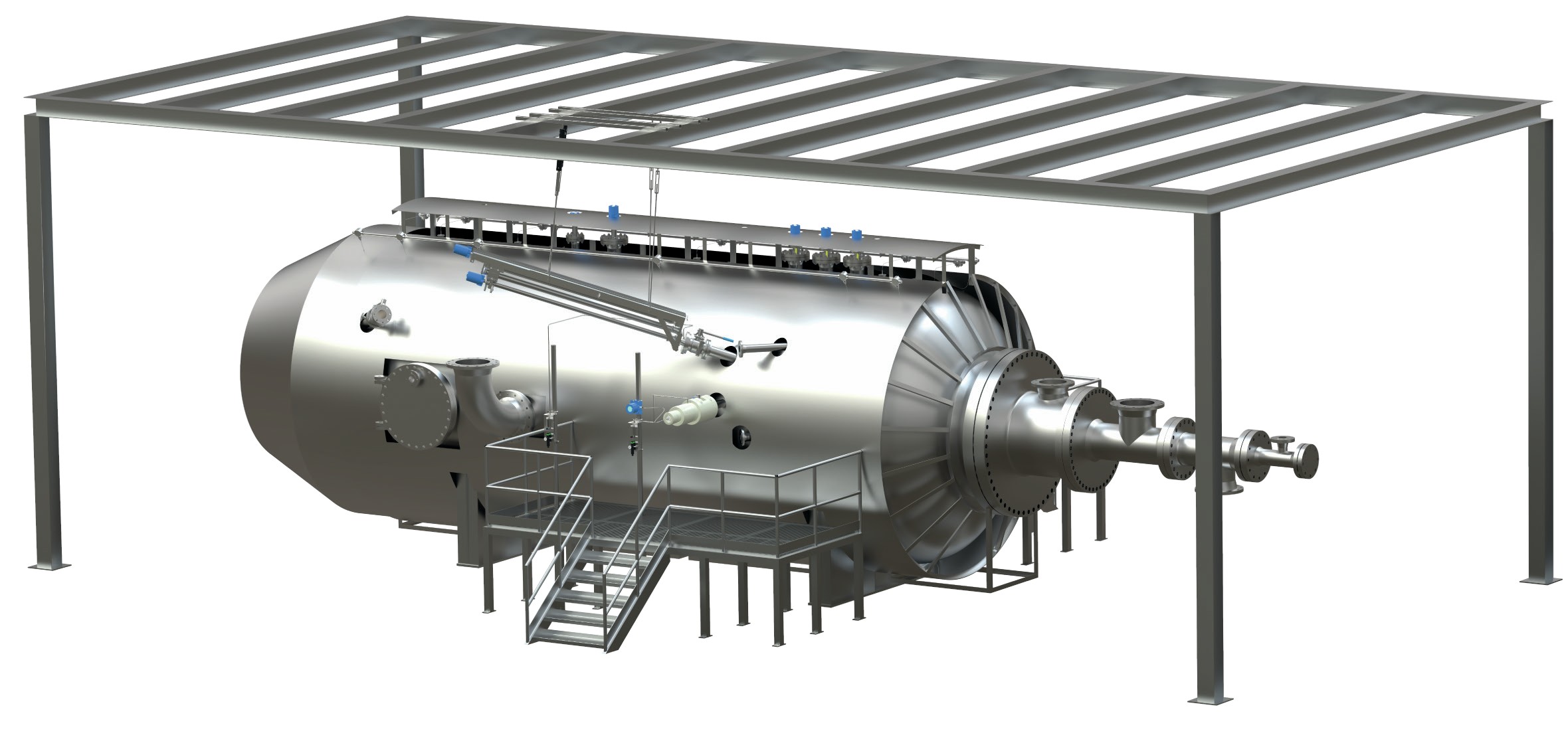
Identifying refractory damage early can prevent major failures such as burn throughs, corrosion problems, and further refractory collapse. The camera’s wide-angle view at the refractory hot face could identify sagging or shifting within the vessel. It could also identify early stages of refractory damage such as vitrification of the refractory brick from direct burner impingement, which could lead to cracking. Since refractory often suffers a point failure and temperature measurement is a bulk measurement, the camera identifies problems that traditional temperature instrumentation might not detect. Comparing images taken at regular intervals over a period of time allows operators to detect subtle shifts in any of the refractory components. The refractory images are also valuable before and after a start-up or shutdown event when thermal cycling can stress the refractory. Furthermore, the camera can be used to verify the completion of a refractory dry out, with a camera inspection replacing the need of a physical re-entry for a refractory inspection. Additionally, the camera may prevent the need for a shutdown if there is a suspected problem. Users can identify problems with the refractory before it devolves into larger issues such as a burn through, shell corrosion, or complete refractory failure. This information can lead to operational decisions, such as reducing the vessel load, planning for refractory replacement, or contacting vendors for root cause assistance.
A final focus for camera inspection is the transition to the waste heat boiler: the tubesheet protection system, including ceramic ferrules. Regular inspection can provide insights into reactor performance and avoid major failures related to the waste heat boiler operation. Any process disturbance which affects the reliability of the ferrules would be visible upon inspection. During oxygen enrichment, fuel gas firing or any other thermal event, it is possible to vitrify and or damage the microstructure of the ceramic ferrules. The process camera could be used for in-situ inspection of the ferrules with the potential to identify differences in surface texture, development of crack formation as well as any shift in the position of the ferrule lining (Fig. 4). It would also be able to identify a leaking boiler tube as the water would stain the surrounding area. Identifying these types of problems in service will help identify any issues in the early stages and potentially prevent extensive damage of the boiler equipment. The digital images of the in-situ tubesheet condition can be a useful tool during any root cause analysis that is performed following a major shutdown.
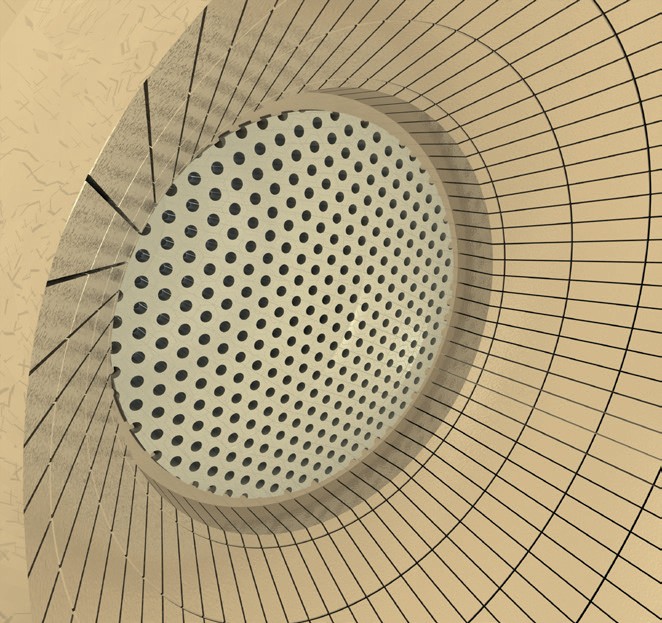
Conclusion
Utilising the ProSpection™ camera allows operators to make more informed operational decisions early on and potentially avoid unnecessary shutdowns and equipment failures. Avoiding unnecessary downtime using photo or video inspections leads to large cost savings. Pre-turnaround discovery can now be done prior to shutdown, allowing users to shorten scheduled or unscheduled turnarounds with fewer surprises in the thermal reactor. Delta Controls Corporation firmly believes the ProSpection™ will be of significant value to the sulphur recovery industry by providing more data about an online SRU reactor than available before. Now operators can shorten downtime, avoid major equipment failures, and make more informed decisions with the ProSpection™ process inspection camera.