Fertilizer International 511 Nov-Dec 2022
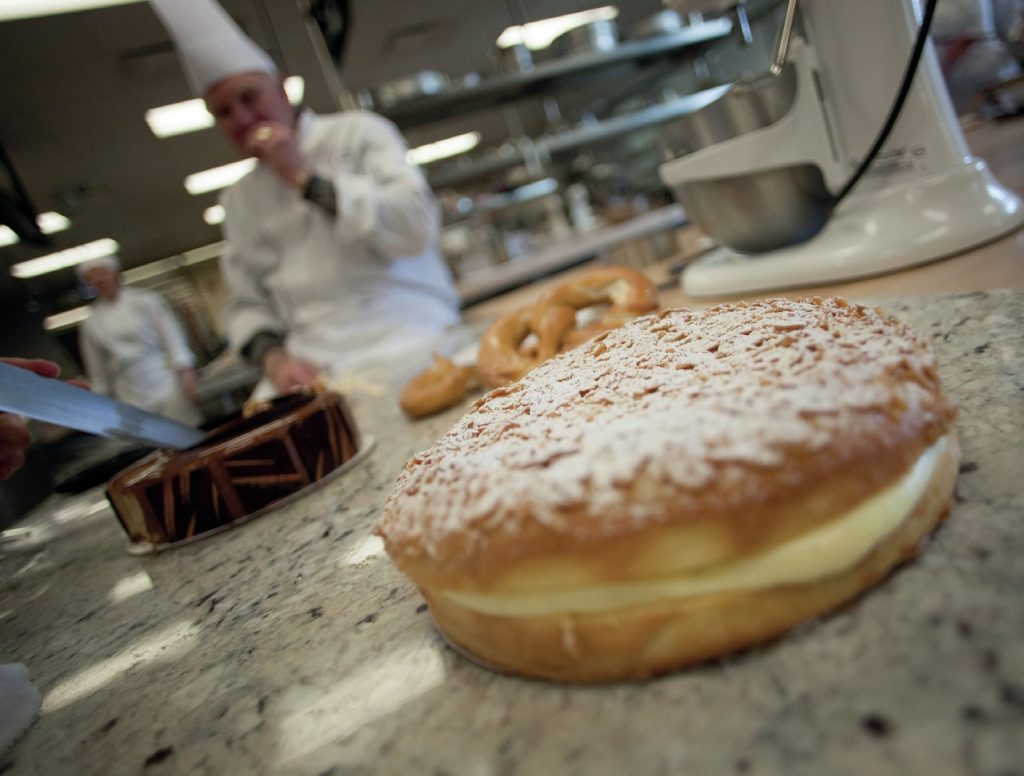
30 November 2022
Food- and industrial-grade phosphates
MARKET REPORT
Food- and industrial-grade phosphates
Industrial end-markets and food manufacturing provide significant global demand for pure and high value phosphate products. The growth potential for lithium iron phosphate (LFP) used in vehicle batteries is also a major industry talking point currently, as Alberto Persona, Fertecon’s principal phosphates analyst, explains.
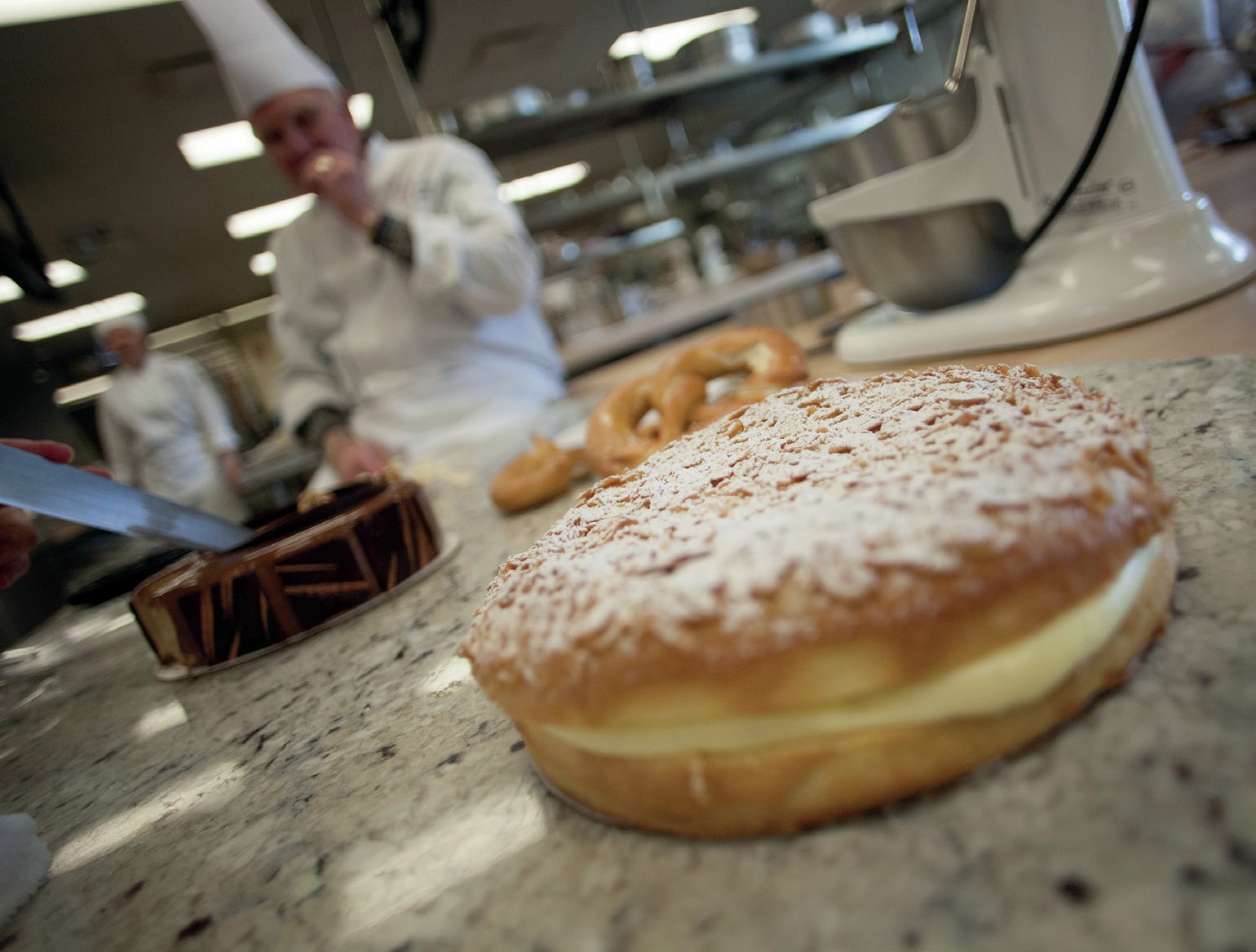
Climate change adaptation and mitigation are two topics that won’t have eluded readers of this magazine. Within the fertilizer world, adaptation has been a prominent and widely discussed issue in recent years – for example, ‘climate-smart’ products that can help stabilise crop yields in response to ever-changing and more extreme weather.
Mitigation has also risen up the policy agenda, with some governments moving more quickly than others in setting CO2 emissions reduction targets. Here, our industry is also beginning to act and contribute by pursuing the decarbonisation of ammonia production.
While nitrogen fertilizer producers clearly have an imperative to move away from natural gas and other fossil fuel feedstocks, the phosphate industry also has important climate and environmental obligations. Phosphate fertilizers have a role to play in limiting land use conversion from forests to cropland, for example, and in supporting investments in fertigation in arid regions. But industrial-grade and food-grade phosphates – a less discussed segment of the phosphate market – could also deliver positive climate benefits due to their incorporation in electric vehicle batteries.
Phosphate market fundamentals
First things first, though: some information on market size. Overall, the global phosphates industry produces around 60 million tonnes (P2 O5 ) of various downstream products annually. At around 85-90 percent of the total, fertilizers represent the largest share by far, while feed-grade supplements account for a further 3-5 percent, with industrial- and food-grade phosphates making up the remaining 5-10 percent share. Fertecon data indicate that around 5.2 million tonnes (P2 O5 ) of industrial/food phosphates were manufactured in 2021.
The terms ‘industrial-grade’ and ‘foodgrade’ cover a large series of phosphate products that cater for disparate end-uses. Major end-use categories (and their respective sub-categories) include:
- Consumer goods (detergents, toothpaste)
- Pesticides
- Industrial applications (metal bright-dipping, semiconductors, industrial cleaners)
- Flame retardants l Processed food (cola manufacture, meat and dairy, sugar refining, leavening agents).
An additional niche sector, one that requires exceptional product purity, is the pharmaceutical industry. Monocalcium phosphate, for example, is a component in most vaccines, including those developed to fight the SARS-Covid19 virus.
Industrial and food phosphates are also commonly classified by their chemical composition. This takes into account the additional raw materials used in their manufacture and includes:
- Phosphorus chlorides
- Phosphorus sulphites
- Phosphinates and phosphonates
- Ammoniated phosphates
- Calcium phosphates
- Potassium phosphates
- Sodium phosphates
- Metal phosphates.
Manufacturing routes
The third way of segmenting the food and industrial phosphate market is classifying products by their production process. Broadly speaking, the market divides between two main processes – the thermal route and the wet route.
The wet route is part of the traditional phosphate value chain, being based on the production of phosphoric acid via the reaction of phosphate rock with (commonly) sulphuric acid. A series of purification steps are then necessary, as most of the impurities present in the original rock feedstock end up being transferred to the acid product generated. Common processes for purifying phosphoric acid include:
- Gas or ammonia scrubbing to remove fluorine and metal oxides
- Filtration l Crystallisation
- Solvent extraction.
While the additional cash cost of removing impurities is factored into product pricing, developing commercial purification processes requires extensive R&D and expert control is necessary for their successful operation. Companies offering purification technologies are also highly protective of their intellectual property and are very active patent publishers. All of these factors combined create a market barrier to new entrants. Consequently, producers of purified phosphoric acid (PPA) with access to their own proprietary technology tend to dominate – and are in a position to impose significant licensing costs on other players wishing to enter the market.
The thermal route starts with the production of elemental phosphorus in an electric-arc furnace. Phosphate rock is firstly blended with thermal coal and silica. This mixture is heated until phosphorus reaches its volatilisation temperature and turns into a gas. Volatilised phosphorus is then recovered as a highly flammable white/yellow solid. Elemental phosphorus in this form needs to be stored carefully due to its low ignition point.
By controlling the overall reaction temperature, or calcining phosphate rock, impurities with a lower volatilisation point than phosphorus – notably arsenic – can be removed relatively easily. Elemental phosphorus is then either converted into different allotropes (e.g., red phosphorus) or used in downstream chemicals production.
The thermal route, while significantly more costly than the wet route, has the distinct advantage of being a much simpler and easily replicable way of obtaining high-purity phosphoric acid. Simply reacting elemental phosphorus with water will yield phosphoric acid of naturally high purity. This avoids the need for licensed and patent-protected purification steps associated with the wet process route, as discussed above.
Clearly, the different classifications for industrial and food phosphates – whether based on end-use, process or chemical composition – are interlinked and overlap. Certain phosphate compounds can be produced via the wet or thermal process routes and sold in more than one market segment.
Rather than getting bogged down in the minutiae of classification, this article instead focusses on three key market topics: product certification, the switchover from the thermal to the wet process route, and demand trends for food-grade and industrial-grade phosphates.
Product certification
End users will generally demand certification as a guarantee of product quality and purity. This is a highly important consideration in the industrial and food phosphates market. It is also a determinant of the industry’s structure – as, implicitly, certification carries high costs which can act to exclude new players wishing to enter the market. Trading blocs and individual nations, and even regional administrations within countries, can impose their own quality requirements and checks with different degrees of stringency. To access these markets, at least one participant (often the industrial and food phosphate producer, but possibly importers and distributors too) needs to prove that defined standards are being met – an exercise which requires dedication and commitment to passing testing and quality inspections.
While these impositions and their costs can be worthwhile when gaining access to larger markets, they can be too burdensome for smaller players accessing smaller markets – irrespective of whether their food and industrial phosphate products meet the required specifications or not. In effect, certification requirements, by reducing competition, offer large-scale chemical distributors significant advantages, particularly at times of oversupply. This can provide the big, established producers with a strong, almost unopposed position in key markets. New producers, in contrast, are likely to struggle to find market opportunities, unless distributors need to replace one of their suppliers and can assist in obtaining the required certifications.
Similar barriers to entry apply to so-called ‘formulation producers’ – companies which sell tailored blends of ingredients that include phosphate salts to specific customers. This generally favours stable, long-term relationships with proven ‘legacy’ suppliers, as the risks involved in switching to a new supplier need to be carefully judged.
The switchover to the wet process route
Despite the barriers faced by new entrants, market change is happening. This is shown by the shift from the thermal process route to the wet route, a trend that is particularly evident in mainland China. The Chinese market has long been notable for the presence of numerous phosphorus furnaces and standalone thermal acid producers. Nevertheless, the market has changed considerably since the mid-2010s, a period which saw major Chinese phosphate players switch to the wet process. GPC (formerly Wengfu), for example, was able to successfully replicate and install Bateman’s purification technology, while YTH formed a partnership with Israel’s ICL. Hubei Xingfa, although originally focussed on the thermal route, has also diversified its product offering.
These ground-breaking developments have allowed China’s domestic phosphate industry to access integrated purification technology – overcoming licensing issues and paving the way for widespread installation. GPC, for example, has installed purification lines at all its phosphate units. This has enabled the company to easily displace sales of higher-cost thermal phosphoric acid and emerge as a true market leader in an already oversupplied market.
Market trends
This leads on to the major high-level trends affecting the demand for food and industrial phosphates. As explained, the increased availability of purified phosphoric acid via the wet route is already weighing on the thermal phosphorus industry. Market sentiment is even more bearish given the continuing downwards trend in the pesticides market, a key industrial end use. In this market segment, the combination of improved formulations, precision application methods and stricter regulations are significantly reducing the general demand for organophosphates.
The mood in the food-grade phosphate industry, in contrast, has been much more positive and – to date – has more than compensated for the simultaneous reduction in pesticides sector demand. Indeed, food-grade salts used to extend the shelf life of dairy and meat products are enjoying particularly strong momentum due to their direct and positive impacts on food storage and availability.
Process routes and process flexibility also play a significant role in the diverging fortunes of these two end-markets. While the production of organophosphates requires elemental phosphorus generated by the thermal route, the production of food phosphates can in most cases switch between thermal and wet phosphoric acid processes.
Clearly, the thermal route continues to face ever-growing challenges, even at a time when overall global demand for industrial and food phosphates is growing firmly. For phosphorus – in keeping with its nickname the ‘devil’s element’ – the devil is truly in the detail.
The industry’s future
While the three preceding sections have covered key factors governing the industry today, two additional topics – carbon emissions and lithium batteries – are likely to shape the industry in future.
Attentive readers will have noticed the four-letter word ‘coal’ in our description of the thermal route. That’s because elemental phosphorus manufacture currently consumes this solid fossil fuel as a reducing agent. The resulting high carbon footprint leaves the thermal route particularly exposed to emissions tariffs and similar policies such as carbon taxes.
The decarbonisation of phosphorus production is, surprsingly, a rarely discussed theme, given that the steel industry has already made significant progress in the use of hydrogen as a reducing agent. The author would therefore like to encourage a broader debate about how to make phosphorus more environmentally friendly. After all, if ‘green steel’ is a possibility then ‘green phosphorus’ should surely become a viable future option too.
A more widely discussed and less niche topic is the batteries market. The electrification of the world’s vehicle fleet is without question a global trend. It is even taking place in countries (e.g. mainland China and, to an extent, the United States) where transport emissions are not being prioritised as much as the carbon reduction targets being set for electricity and heat generation.
Electric vehicles require a battery to work. In turn, a battery needs an anode, a cathode, and an electrolyte to function. Fortunately, our friend phosphorus has a role to play in all three of these components. For example:
- Black and red phosphorus are being actively studied as a potential basis for anodes
- Lithium hexafluorophosphate is already a commercially available electrolyte
- Crucially, lithium iron phosphate (LFP) has become one of the hottest talking points in the cathode world – ever since Tesla announced it will use it as the option of choice in its Shanghai mega-factory.
“As much as the phosphate world may want to get involved in the LFP ‘revolution’, there is an argument that LFP will largely remain a lithium success story.
LFP is not a new material. It has been produced for decades and is commonly found in batteries for portable electronic devices such as smartphones and tablets. LFP-based batteries, while offering somewhat lower performance compared to nickel-manganese-cobalt (NMC) batteries – in terms of charge duration and total battery life – are considerably cheaper to produce, and therefore find a natural market in lower-value products.
Why then the excitement about LFPs for higher-value markets such as electric vehicles? The answer is ‘scalability’. The overall size of the world’s car fleet is of such magnitude that the total demand volumes for battery raw materials will increase significantly, even assuming cautious electric vehicle penetration rates.
When it comes to scalability and supply security, cobalt required in NMC batteries has come under particular scrutiny, due to the concentration of mining in the Democratic Republic of the Congo and the consequent risk of supply interruptions. In contrast, phosphorus resources are comparatively diversified and more widely available than cobalt, despite their concentration in a limited number of countries such as Morocco and China.
Growing excitement about the LFP market and its potential is such that its difficult to find a phosphate player that does not mention LFP batteries in its long-term strategic plans. From established producers to junior projects, it seems that everyone wants to ride the LFP wave. Fertecon does, however, issue a ‘health warning’ for LFP on both the demand and supply side.
Yes, LFP demand is set to increase at a faster rate than many other industrial end-uses for phosphates. Yet capacity developments are already outpacing our demand projections. Between 2020 and 2025, capacity for LFP in mainland China alone is expected to grow more than ten-fold to 4.5 million t/a. That far exceeds what is arguably an optimistic demand expectation of less than two million t/a by 2025. Elsewhere, increasing concerns over the supply security of critical raw materials has led to further capacity additions being actively discussed in regions such as Europe and North America.
On the supply side, our advice is not to put too much emphasis on the phosphorus component of LFP. One tonne of LFP consists of about 0.05 tonnes of Li, 0.35 tonnes of Fe and 0.20 tonnes of P. While there is four times more P present in LFP than Li in volume terms, it is actually their relative price that largely determines the economic dividend. Elemental phosphorus is rarely priced above $3,000/t, for example, while one single tonne of lithium carbonate (containing 18% Li) was recently traded on the Chinese market at above $75,000/t.
Therefore, as much as the phosphate world may want to get involved in the LFP ‘revolution’, there is an argument that LFP will largely remain a lithium success story. Concentrating on more conventional industrial-grade and food-grade phosphate markets, while perhaps not as exciting, is likely to be a safer bet in our view.