Fertilizer International 511 Nov-Dec 2022
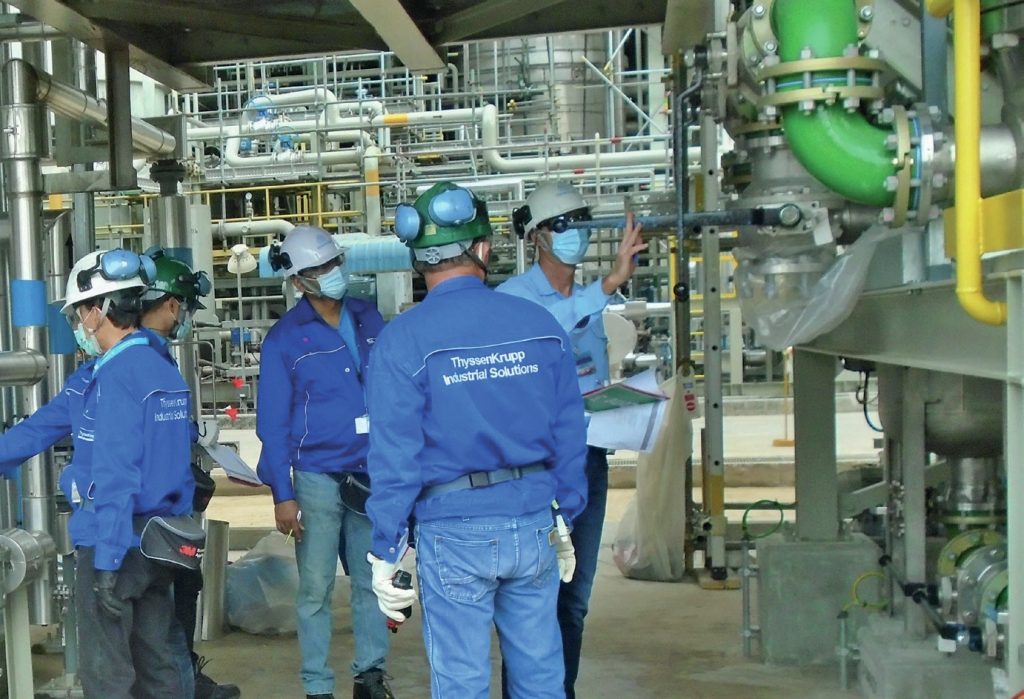
30 November 2022
Making fertilizer plant construction safer
PROJECT SAFETY
Making fertilizer plant construction safer
The fertilizer industry’s leading engineering, procurement and construction (EPC) companies, by setting zero incident safety goals, are making construction sites across world safer. In this article, we highlight the safety advantages of modular construction and digital approaches to safety at construction sites.
THYSSENKRUPP INDUSTRIAL SOLUTIONS (THAILAND) LTD
Modularisation: the safer construction option
Construction site safety is always a top concern. Given that construction is a comparatively high risk activity, it comes as no surprise that the industry’s fatalities accounted for around one-fifth of all deaths at work in the United States from 2016 to 2020, corresponding to around 1,000 lost lives annually (Figure 1).
Half of these fatalities are caused by falls and people getting struck by objects. Fortunately, both of these incident types can be significantly mitigated by using modularisation in construction. Modularisation offers safety benefits by shifting work from construction sites to more controlled areas in fabrication yards and by moving construction activity from higher elevations to ground level.
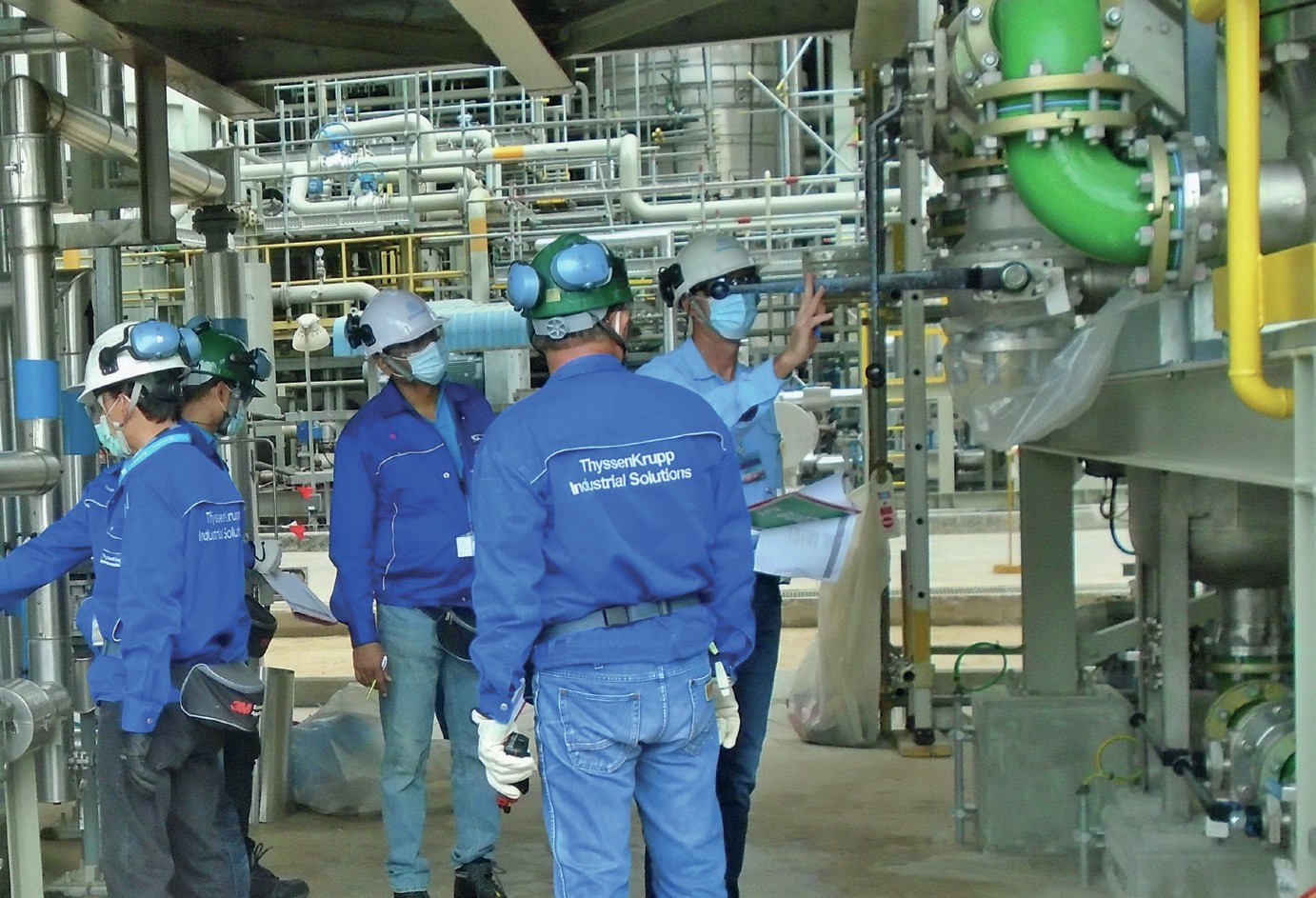
Safety culture
thyssenkrupp Industrial Solutions (Thailand) Ltd is committed to a ‘zero accidents’ philosophy to protect the health and safety of its employees, our most valuable asset. Our safety mantra is: “Make sure everyone goes home safely, every day to their loved ones and families.”
Company safety culture is further enhanced by operating HSE programmes based on behaviour-based safety (BBS) principles. Our ‘Spot safety recognition programme’, for example, increases on-site housekeeping standards through a weekly cleaning routine. This is positively reinforced by free lunch packages and drinks for the participants. Good house-keeping practice enables us to mitigate several risks. The risk from falling objects, for example, can be reduced by removing unused materials from work areas and storing these in a proper and safe location.
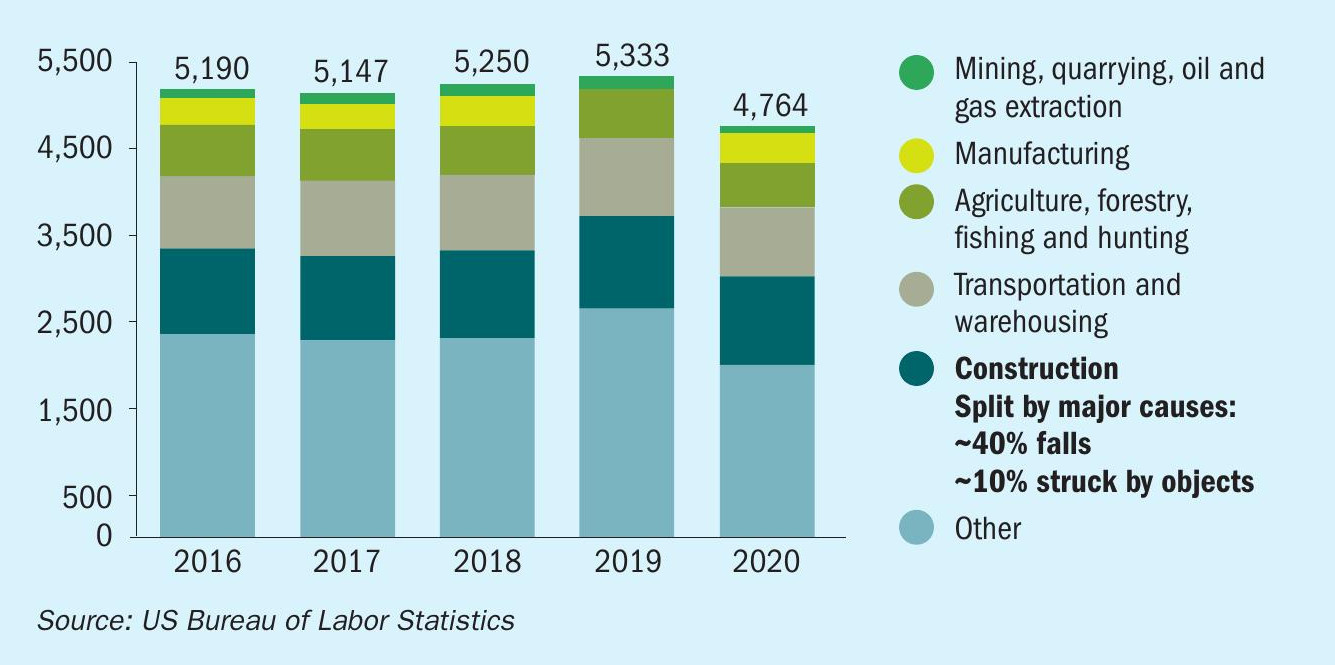
The positive safety behaviour of our site staff is regularly rewarded by safety certificates which highlight and recognise safe working. Leadership participation is also seen as one of our key success factors. thyssenkrupp Industrial Solutions (Thailand) Ltd therefore conducts monthly ‘Gemba’ safety walks on our sites with our top management (see photo).
As a result, we are extremely proud of our safety performance. To date, we have accumulated over 42.4 million project work hours without a single lost time incident (LTI).
Safety is also one reason why modularisation is at the core of our project execution strategy. Our full range of in-house modularisation services covers:
- Project management
- Concept planning
- Preliminary engineering
- Detailed design
- Procurement
- Construction management
- Commissioning.
What is modularisation?
The term modularisation includes prefabrication, preassembly, modularisation and offsite fabrication (PPMOF) activities and typically encompasses four distinct categories:
- PAU/PAM: pre-assembled units/modules
- PAR: pre-assembled racks
- VAU: vendor assembled unit
- VPU: vendor packaged unit
Other aspects of PPMOF include precast concrete, dressed columns and prefabricated buildings.
Modules consist of equipment items arranged in modular steel structures and buildings that can be assembled off-site. These are then transported to the site and lifted into place. Modularisation includes the following activities:
- Equipment is connected with piping
- Instrumentation is installed and cabled to junction boxes
- Lighting and cabling is installed
- Steelwork is fireproofed up to the connection points
- Tracing and insulation on equipment and piping are completed
- Painting is carried out.
Safety and other benefits
Compared to on-site construction, modularisation works can be executed at a higher number of parallel work-fronts closer to ground level, reducing scaffolding requirements and lifting activities. Modularisation also results in a shift from a higher number of smaller lifting activities to a smaller number of heavy lifts performed under more tightly controlled conditions using exclusion zones.
Apart from creating safer work environments on construction sites, modularisation delivers several other benefits to customers. Modular construction is a very effective way of improving quality and productivity and can deliver cost savings by shifting potentially expensive site hours to cheaper workshop hours with higher productivity. Modularisation also increases the reliability of construction schedules and mitigates other site risks such as industrial relations performance. Furthermore, modularisation results in more sustainable project delivery by reducing the impacts of construction on local communities and infrastructure.
TOYO ENGINEERING CORPORATION (TOYO)
Improving safety with digital technology
The rapid worldwide spread of digital technology is influencing work on construction sites and the EPC contracting industry. Japan’s Toyo Engineering Corporation (Toyo) is embracing this digital transformation and the new approaches to safety it offers, including:
- Smartphones
- Digital signage
- Artificial intelligence (AI) speakers These are highlighted below.
Smartphones
Toyo has been working continuously to implement and improve Health, Safety, Security and Environment (HSSE) at construction sites to protect its workers. Previously, the company’s standard HSSE procedure was developed from past knowledge and experiences. But it was recognised that a new paperless procedure would be needed in future to replace the traditional paper-based approach.
To achieve this, Toyo’s turned to Microsoft Power Apps. This standard tool creates new paperless apps that can be used easily without any special skills. These apps are helping Toyo achieve a dynamic change of culture at construction sites and the desired switch to paperless working.
As a first step, Toyo recently developed a new app named BBO (Behaviour Based Observation) Report Application (Figure 1). This app is designed to eliminate the paperwork associated with reporting near miss accident reports at construction sites. Previously, BBO reports were submitted in a paper format by workers, supervisors and site personnel, and then registered digitally on Microsoft Excel spreadsheets by a data entry clerk. The task took a long time to complete and was occasionally prone to input errors.
The new app has features which allow users to take photos and input information using a dropdown menu on a smartphone, tablet and/or laptop etc. Entered information is submitted directly to a database. This database information is then analysed by Microsoft Power BI, a business analytic service offered by Microsoft. This allows anyone at the construction site to check event trends and use the data to prepare HSE flash reports, weekly reports and safety awareness posters etc.
The new app target 500+ members of staff directly employed by Toyo and has resulted in three unanticipated positive benefits:
- Automatically provides an accurate log from users (staff) during working hours
- Offers time savings for both the applicant and administrators
- Prevents submissions and actions from being overlooked.
The switch from a paper-based system to the new paperless app – by providing an easy and timely method of collecting data on field activities and behaviour – can be used to implement preventative HSSE measures. Consequently, Toyo is now recommending the adoption of this paperless system at all its construction sites.
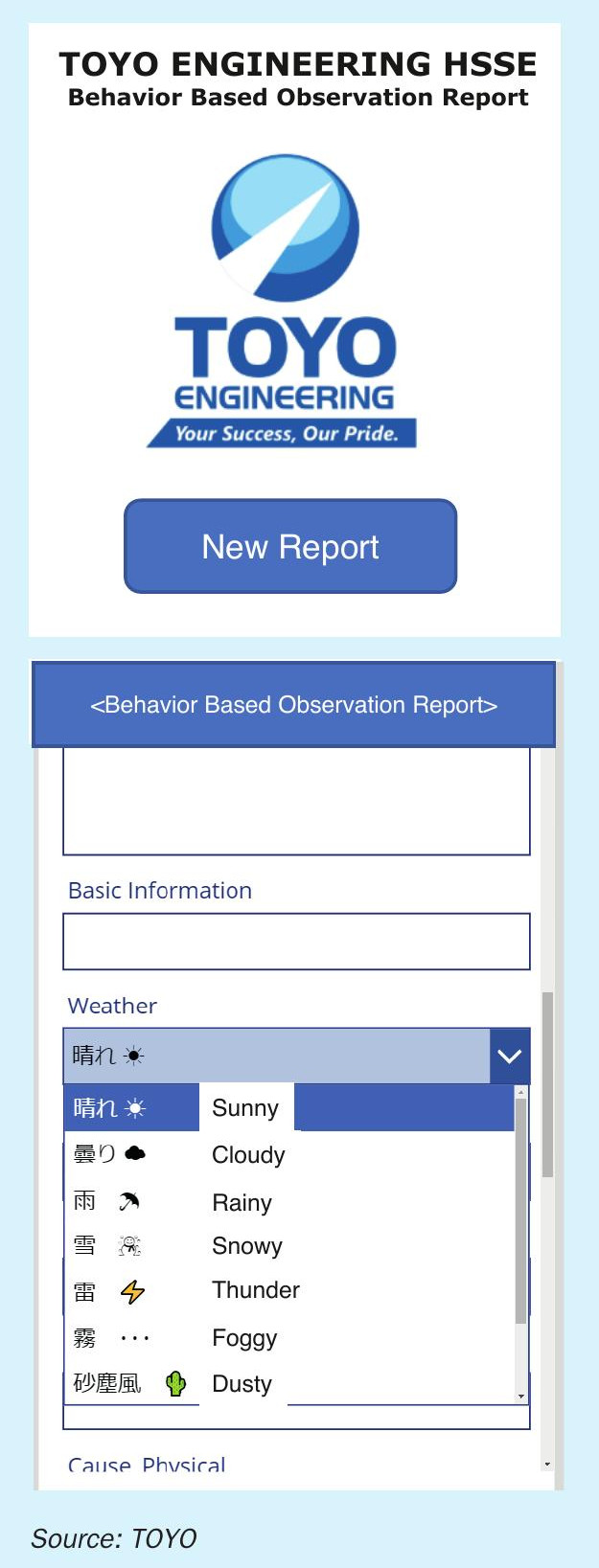
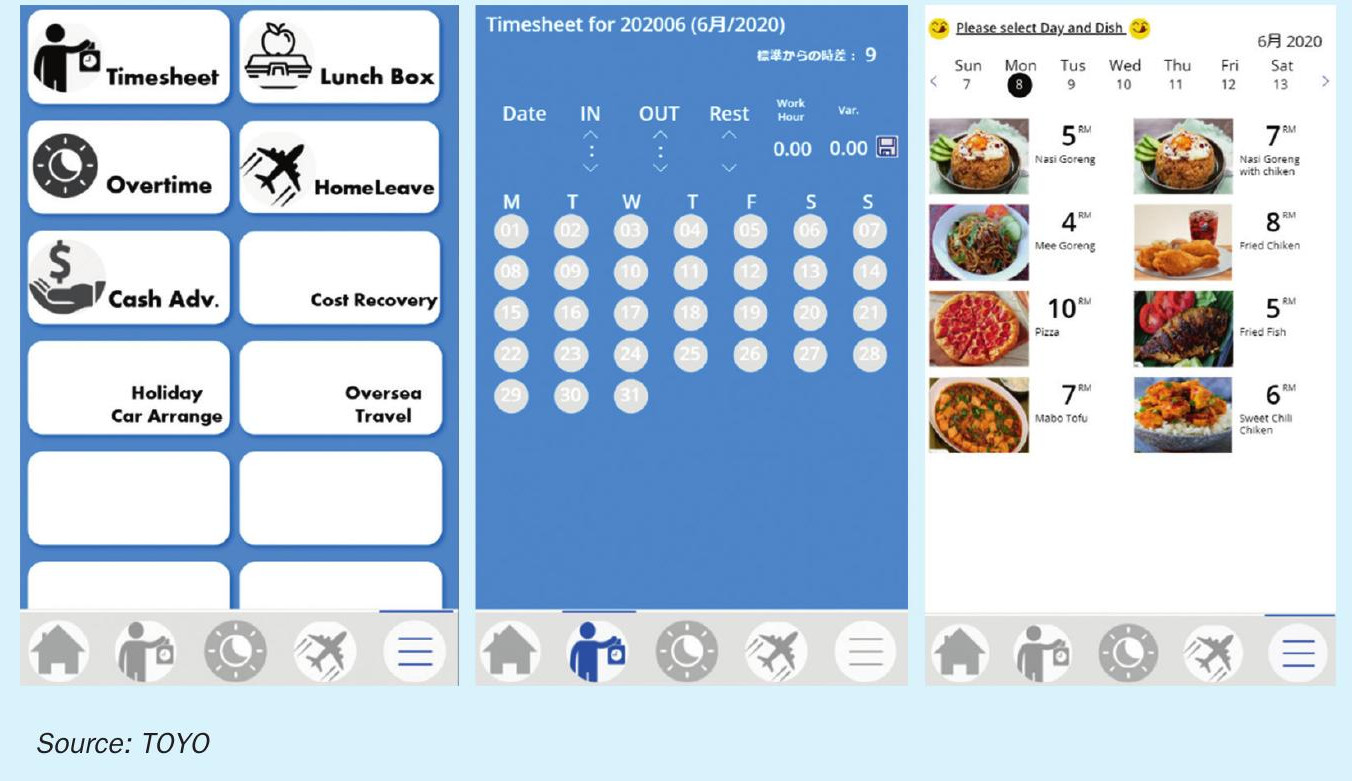
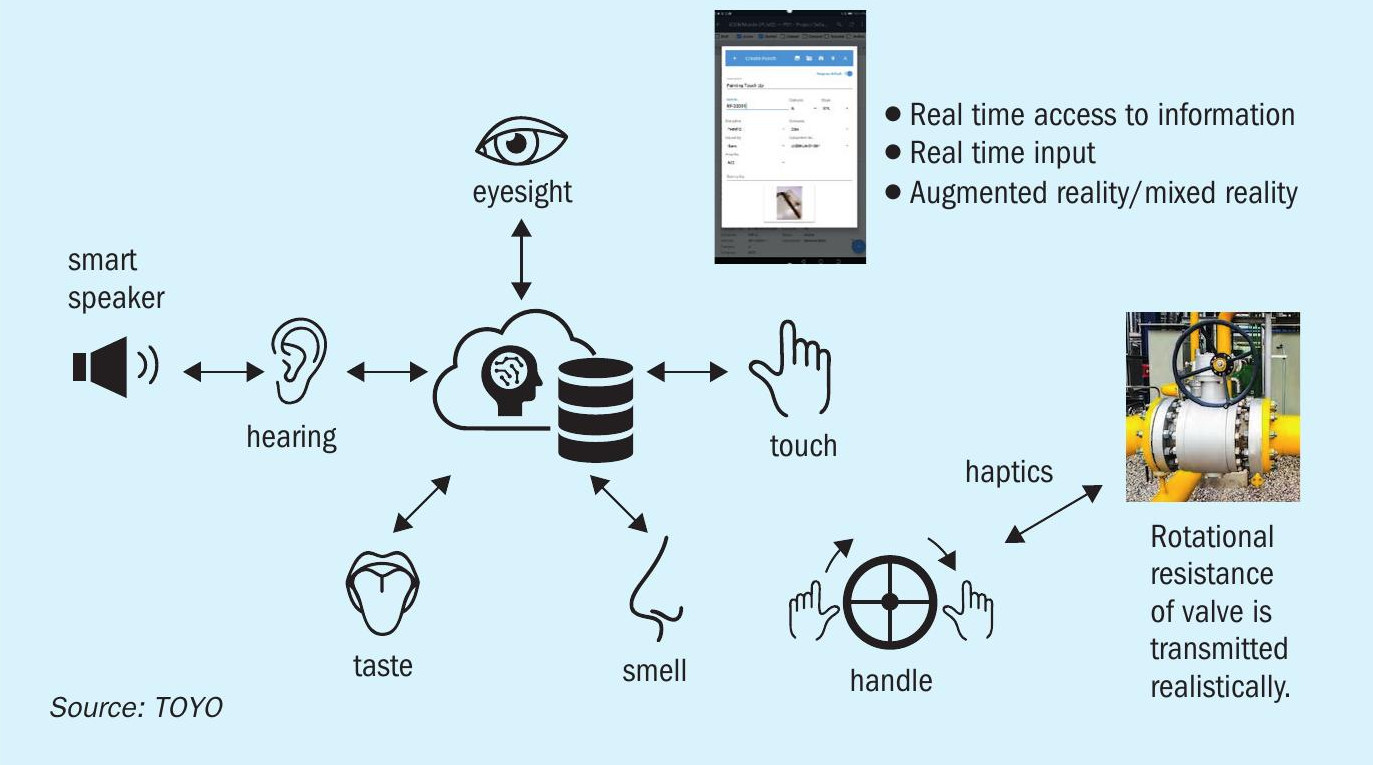
Toyo is also making use of several other apps at construction sites. These can be used to request personal protective equipment (PPE), for transportation requests, and to input timesheets, for example. There is even an app which allows construction workers to request lunch boxes/ midnight snacks from anywhere on site, making life more comfortable for everyone. This is clearly good for human health and has a positive effect on the performance of daily tasks (Figure 2).
Digital signage
Throughout its EPC projects, Toyo has always recognised the truth and importance of two sayings: ‘seeing is believing and ‘a picture is worth a thousand words’. In our experience, presenting information visually is usually the most effective form of communication. The use of moving images, such as movies or videos, is also becoming increasingly popular.
The use of digital display boards at construction sites is helpful in situations where people need to deliver and visualise messages more clearly. The use of better visual tools also has an important and positive impact on HSSE management for staff at EPC construction sites.
To meet HSSE requirements, Toyo recently launched electronic displays – so-called digital signage – at a construction site in Japan. This displays the important HSSE information announced daily to all staff members at their morning toolbox meeting. At given times, the digital sign can:
- Display construction progress with drone aerial video
- Alert staff and workers to prevent personnel from entering restricted areas by showing a map
- Announce major activities or site events such as heavy lifting, power receiving, steam blowing, or VIP visits.
Digital signage allows the relevant information to be shown effectively in a visual manner – whereas conventionally in toolbox meetings messages were delivered via voice messages only. Because it was necessary to translate messages into all the different languages spoken by site personnel (Japanese, English, Bangladeshi, Malaysian, Singaporean, Chinese etc.), in some cases it was quite difficult to provide a clear message to all staff. Visualisation using digital signage was found to be a much more effective way of providing information that avoided some of these language and translation concerns. Toyo also plans to use projection mapping in the near future. This should make messages even more powerful and keep construction site workers safe by ensuring good communications.
AI speaker (Safety Smart Speaker)
Thanks to recent advances in the internet of things (IoT) and artificial intelligence (AI), information and communications technology (ICT) is now available that can interact with all five human senses. Speaking to smart speakers has been identified as a particularly useful and effective form of hands-free communication, especially at construction sites. From a safety point of view, it is important that construction crews can receive information without picking up paper, documents, or mobile phones. Usefully, smart speakers can also use voice recognition to identify different individuals in the construction crew.
Toyo’s smart speaker concept for construction sites is shown in Figure 3. The company built a prototype Safety Smart Speaker in 2021. When users say certain keywords, this speaker responds by giving highly relevant alerts/reminders by showing past incident cases with appropriate safety measures. The speaker provides a voice reading of incident cases as well as displaying the information.
“Toyo is developing powerful digital technologies that can improve safety culture by appealing to our five senses.”
Currently, the screen for showing past incident cases is being improved to enable the display of a risk ranking alongside search results (Figure 4).
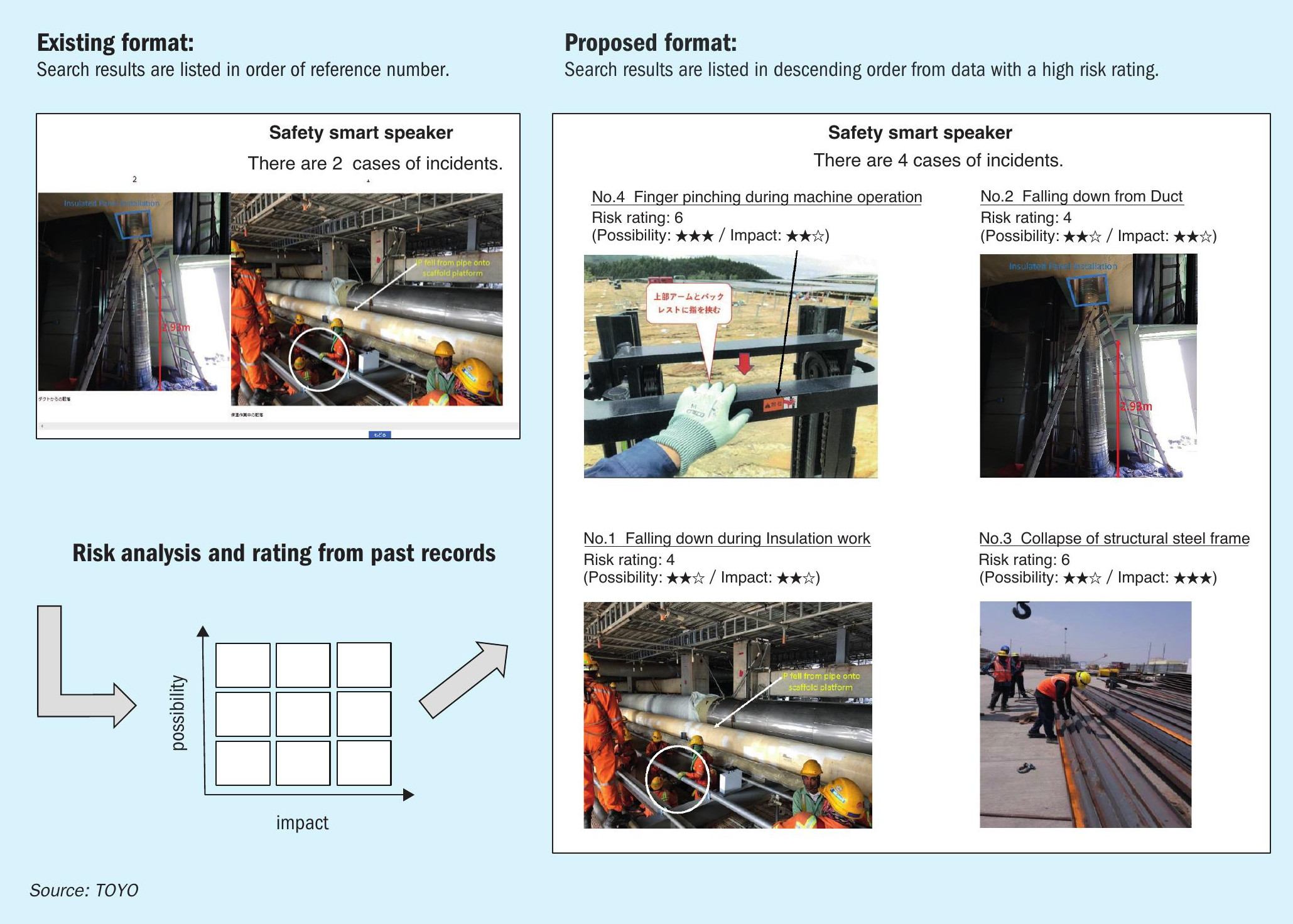
Smart speakers can be used in the following situations:
- At the safety training centre: Instead of passively reading a paper bulletin, workers can easily increase their safety awareness by talking to a Safety Smart Speaker and getting a reply.
- For regular inspections: The Safety Smart Speaker can also be used for regular inspections as well as for safety. The speaker enables inspectors to continue to work using the inspection tools in their hands by providing a hands-free voice checklist. This saves times as, previously, the inspectors needed to stop working to pick up the paper checklist.
- Receiving site feedback: Workers can send feedback through the Safety Smart Speaker. This is an effective way of proactively raising safety awareness on-site, and not just give workers information on past incidents.
Toyo is planning to introduce Safety Smart Speakers as standard in the above three work settings soon. The company is continuing to develop powerful digital technologies that can promote and improve safety culture by appealing to our five senses.