Fertilizer International 511 Nov-Dec 2022
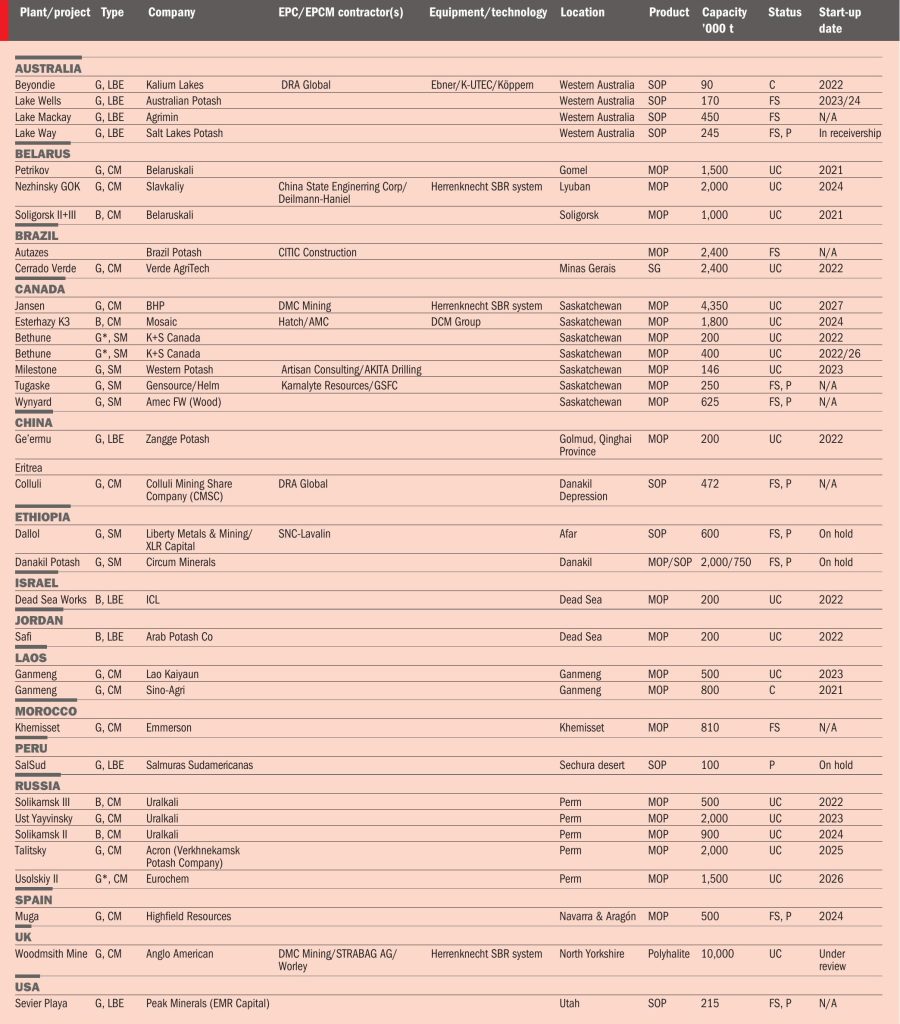
30 November 2022
Potash project listing 2022
PROJECT LISTING
Potash project listing 2022
Fertilizer International presents a global round-up of current potash projects.

NOTES:
- Greenfield projects (G): generally, these must have reached the detailed/bankable feasibility study (FS) stage for inclusion.
- Brownfield expansions (B): capacity indicates incremental additions, not total capacity.
PROJECT TYPE:
G Greenfield
G* Greenfield ramp-up/expansion
B Brownfield expansion
CM Conventional mine
SM Solution mine
LBE Lake brine extraction
PRODUCT:
MOP Muriate of potash, KCl
SOP Sulphate of potash, K2 S04
SG Super Greensand, glauconite
START-UP DATE:
N/A Not available or provided
PROJECT STAGE:
FS Feasibility study
P Permitted
UC Under construction
C Completed/commissioned
PEAK MINERALS
Sevier Playa SOP project, Millard County, Utah
Peak Minerals Inc. (Peak) is developing the Sevier Playa sulphate of potash (SOP) project in Millard County, Utah.
The project has the potential to become America’s largest SOP producer, targeting eventual production of 474,000 t/a under its second phase expansion plans. Peak’s two-phase, 25-year mine plan for Sevier Playa will utilise just 53 percent of the underlying recoverable indicated SOP resources.
Sevier Playa is the only fully permitted, brine-sourced SOP project under development in North America. The project is well positioned to become the region’s lowest cost SOP producer – with a position in the bottom of the second quartile of the global industry’s cost curve. Its Utah location is also well situated to serve the large domestic US market as well as growing markets in Mexico and South America, according to Peak.
Private equity firm EMR Capital acquired 100 percent ownership of Sevier Playa in October 2020, having been an investor since 2015. More than $100m has already been invested in this ‘shovel ready’ project over the past decade.
Sevier Playa will use a proven, brine-based solar evaporation method. This offers cost advantages over other SOP production methods, such as those based on the secondary Mannheim process, suggests Peak. Extracting SOP using solar energy also helps to minimise the project’s environmental footprint while at the same time producing a natural, organic-certified product.
Sevier Playa has probable SOP reserves of 3.4 million tons and in-situ measured and indicated resources of more than 38 million tons. The plan is to extract economically valuable brines from the playa via trenches. These provide uniform grades and flow rates and are more efficient than wells – although well extraction could provide an opportunity to extract brine from deeper layers of the playa in the future.
The extracted brine will be fed via a network of canals to pre-concentration ponds where halite is precipitated. The pre-concentrated brine will then be channelled to production ponds where valuable solid mineral salts are precipitated. These salts will be transported to the nearby processing plant by truck.
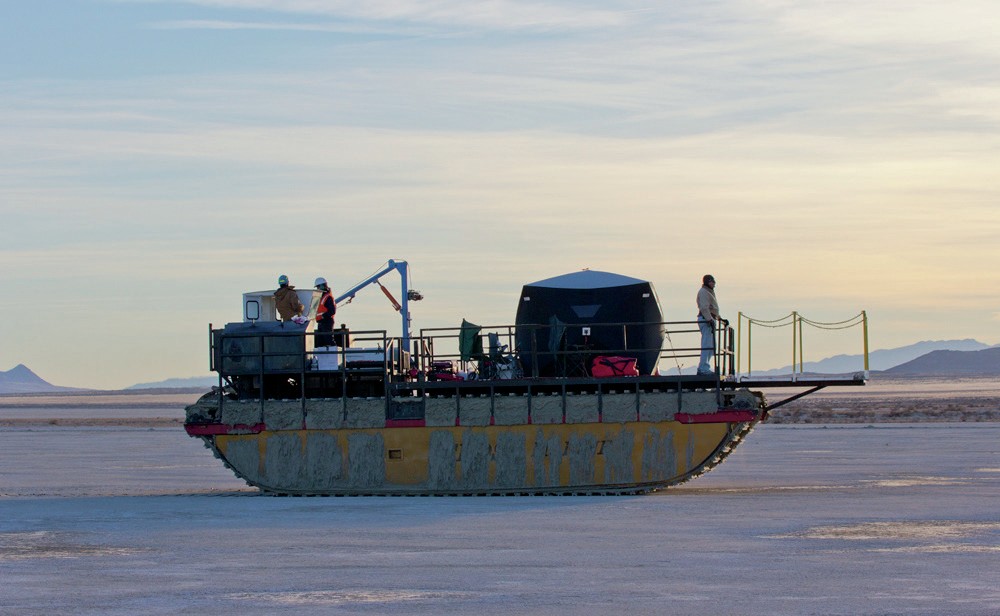
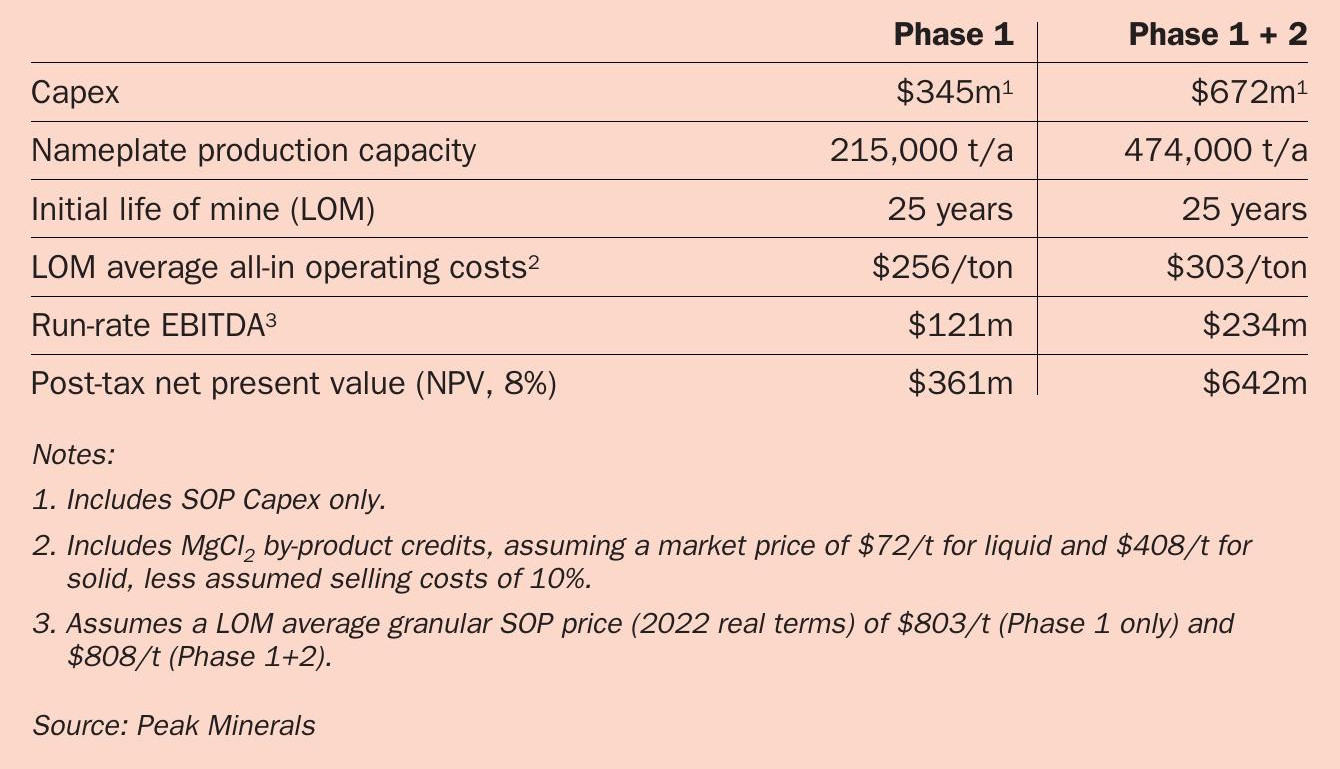
At the processing facility, the solid minerals will be crushed, turned into a slurry and pumped through a flotation circuit. This simple process circuit purifies the SOP product and crystalises it into its final form while rejecting waste materials.
Peak identified the following opportunities to optimise the project during its recent feasibility study update (Table 1):
- Phased development reduces project risk. The 215,000 t/a capacity Phase 1 production focuses on the southern playa, later expanding to 474,000 t/a capacity in Phase 2 which includes northern playa. This phased approach reduces operational risks and improves project flexibility.
- Capex optimisation. This includes measures to optimise trench profiles, on-playa brine infrastructure, production pond placement and powerline routing. It also reduces evaporation pond sizes, and recommends the outsourcing of harvesting/hauling and using a third-party built and owned rail transload facility. The cost estimate for the Rocky Mountain Power interconnection has also been updated.
- Process improvements. Adopting a back-mix process would maximise reacted MOP production and sulphate recovery while lowering costs. There is also potential to optimise the leach unit operation. The use of wet harvesting also lowers costs, improves recovery, and removes the need for costly and logistically challenging berm raises.
The Phase 1 mine plan for Sevier Playa concentrates on the southern part of the playa only and captures around 27 percent of the total recoverable resource. Peak is targeting a production start date of 2027 for this initial phase.
Next steps for the Sevier Playa project include completion of front-end engineering and design (FEED), securing project funding and awarding the contract for the playa/ ponds. Funding arrangements have already commenced to raise around $25 million in new funding to complete the FEED and support the construction financing process in 2023. The pursuit of an additional financing partner is also underway. A project finance adviser, meanwhile, has been appointed to examine debt funding alternatives.
Peak Minerals is aiming to finalise all studies, FEED and project financing within the next 12 months – so it is in a position to commence construction towards the end of next year.
EBNER
Ebner: evaporation and crystallisation specialist
Germany’s Ebner GmbH & Co KG is a family-owned specialist designer and manufacturer of evaporation and crystallisation plants. The company develops tailor-made plants completely in-house, from the customer’s first enquiry to final delivery, having expertise that encompasses plant design, fabrication, erection, and start-up.
Ebner is an established global player. To date, the company has successfully constructed 600 new evaporation and crystallisation plants and optimised more than 200 other plants worldwide.
The company has extensive experience in the design and manufacture of evaporators and crystallisers for the potash industry. These are suitable for a range of fertilizer salts including potassium chloride (KCl), widely known as MOP (muriate of potash), and potassium sulphate (K2 SO4 ) referred to in the industry as SOP (sulphate of potash). The plant production capacities for these salts can vary from a few kg/h to more than 200,000 kg/h.
In addition to offering basic engineering services, Ebner says it is the only worldwide plant manufacturer with in-house capabilities for the following spectrum of project activities:
- Different process route studies
- Experimental trials to validate test data using remote pilot plants or mobile pilot plants located on-site
- Final plant design and selection of suitable subcontractors
- Static and strength computations for components
- Complete engineering for measurement and control technology
- 3D planning of the entire plant with consideration of assembly/maintenance concepts
- Fabrication of apparatus and piping in its own in-house workshop
-
Assembly of the complete plant as a turnkey project, if requested
-
Commissioning of the plant including performance testing
-
After-sales services such as annual optimisation via a remote connection to the customer’s programmable logic controller (PLC)
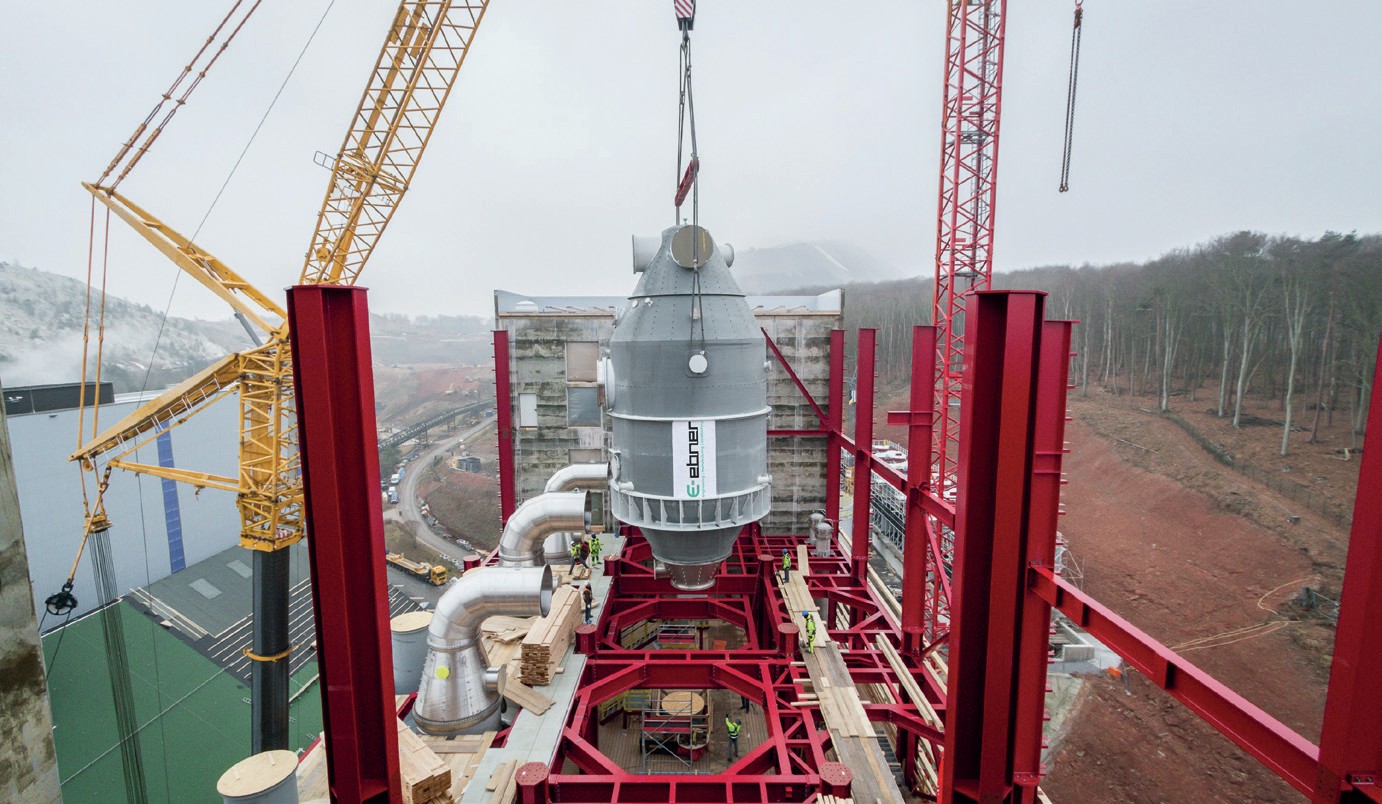
In offering these services, Ebner can draw on decades of experience and data collection. The company also benefits from experienced and flexible personnel with efficient plant handling expertise. These staff can also advise customers on change-management, if necessary. Ebner has more than 100 employees – many of whom have been with the company for decades.
These strengths enabled Ebner to deliver Belaruskali’s last large-scale MOP plant with a production capacity of 190 t/h. This successfully entered full operation after only five days of commissioning.
This is just one of numerous plants Ebner has executed for many leading potash producers such as K+S Mineral and Agriculture GmbH. The company was involved in one of K+S’s largest single investments in Europe. Ebner designed, supplied and installed for K+S a 180 t/h capacity evaporation plant that crystallises several individual salts.
Ebner is currently preparing a major 30 t/h capacity MOP project in Saskatchewan, Canada. Project engineering has already been completed with Ebner selected as the plant equipment supplier. This plant will operate with a new type of solution mining process and, unusually, the entire complex will operate without above ground evaporation ponds and salt tailings.
Ebner, as well as installing new plants, also undertakes plant conversions and retrofits. There is increasing demand for projects which upgrade and replace process technology and reduce energy consumption. This trend is linked to rising energy costs and, consequently, retrofitting is proving to be an increasingly important part of Ebner’s work portfolio.
KALIUM LAKES
Beyondie SOP project, Pilbara, Western Australia
Kalium Lakes Limited (KLL) confirmed that the Beyondie project produced its first batch of SOP in early October 2021 during commissioning.
This makes KLL Australia’s first SOP producer, the company said in an Australian stock exchange (ASX) release. The company later passed another critical milestone in 2022 with its first commercial sale of SOP in July.
The 90,000-tonne capacity SOP project is located in the remote Pilbara region of Western Australia, about 1,400 kilometres north of Perth. The project includes the construction of trenches, pumping stations, ponds, a processing plant, gas power station, airstrip, access road and an 80-kilometre gas pipeline.
The SOP product obtained will be trucked by road from Beyondie to Perth. On arrival, it will either be collected by local domestic customers, or shipped by sea to the east coast of Australia and New Zealand. The company plans to ship excess product to South East Asian markets.
The AUD 280 million project reached financial close at the end of 2019. Project financing included:
- AUD 102 million of senior debt funding from KfW IPEX-Bank, with approximately half of this amount supported by a guarantee from Euler Hermes, the German government’s export credit agency
- AUD 74 million loan package from the Northern Australia Infrastructure Facility (NAIF).
The company subsequently raised an additional AUD 50 million in capital at the end of 2021 to expand Beyondie’s production output to 120,000 t/a.
KLL has a 10-year take-or-pay offtake agreement with German potash producer K+S for 120,000 t/a of the project’s production volume. This will allow K+S – already the world’s largest SOP producer outside China – to deliver SOP from Beyondie to supply its existing market share in Australia, New Zealand and South East Asia.
Production expertise, equipment and technology for the project is being provided by Germany’s Ebner, K-UTEC and Köppern (Fertilizer International 501, p52).
The project has experienced commissioning and start-up delays in the last 12 months. The SOP purification plant was idled at the start of 2022, pending the harvesting of more high-grade potassium salts from evaporation ponds and to allow plant rectification work to take place. Commissioning of the purification plant subsequently resumed in mid-April.
The SOP plant was due to fully re-start in June 2022, following validation of the process design, with commercial SOP sales being targeted from July onwards.
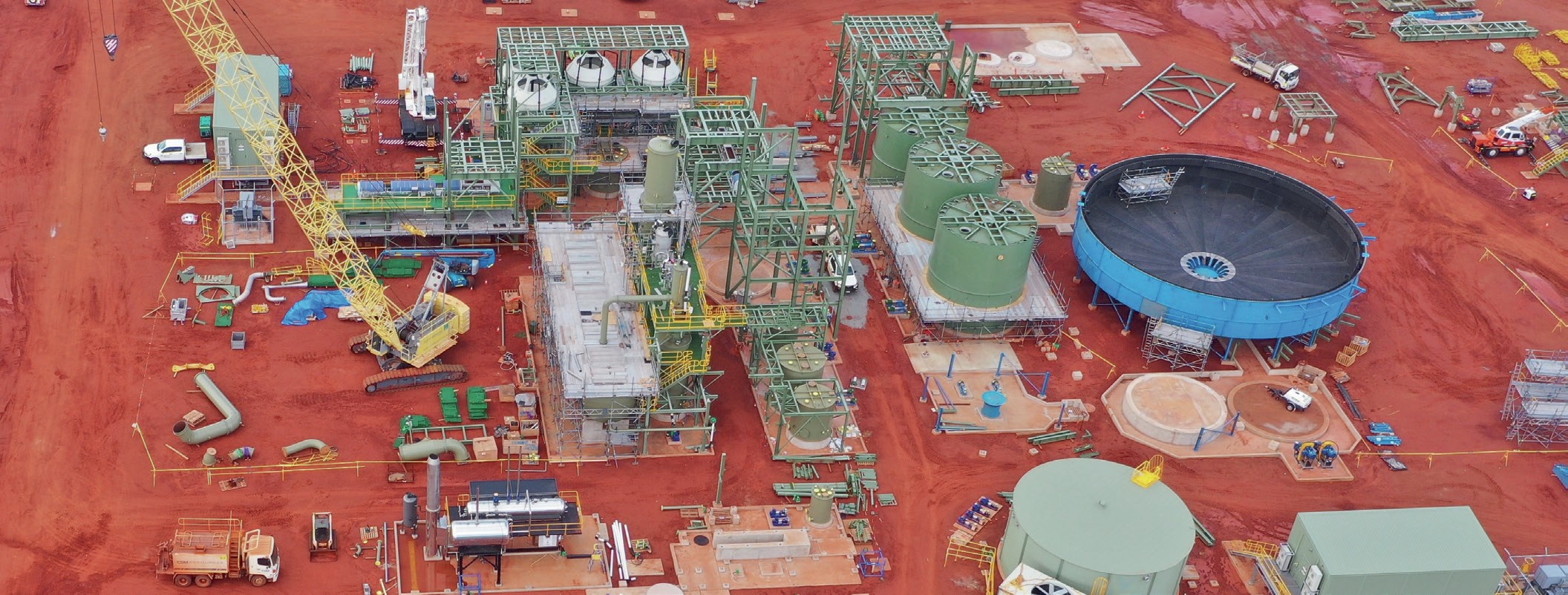
Kalium reported that around 1,000 tonnes of commercially saleable SOP had been produced by the end of June. The inaugural commercial SOP sale to Western Australian fertilizer manufacturer and distributor CSBP Fertilisers was subsequently made on 31st July, under its offtake agreement with K+S.
Commenting on this, Len Jubber, Kalium’s CEO, said: “A critical milestone came with the first commercial sale of SOP in July 2022. This heralded the start of the era of domestic SOP production in Australia for distribution to the Australian and international agricultural markets.”
The purification plant was shutdown again in August, to allow further equipment testing, but resumed operations in mid-September. Following these commissioning delays, Kalium successfully raised AUD 34 million to provide additional working capital and for debt restructuring.
Kalium Lakes now expects the Beyondie project to be operating at an SOP production capacity of around 80,000 t/a by the first-quarter of 2023, with this ramping up to a production target of 120,000 t/a by the third-quarter of 2024.
KÖPPERN
Köppern: the compaction-granulation experts
Köppern, a family-run business founded in Hattingen, Germany, has been manufacturing briquetting, compaction and comminution machinery since 1898. The company has been supplying compaction and granulation equipment and plants to the fertilizer industry for more than 70 years. Its sales include several hundred roller presses in over 60 countries.
Granular potash is produced almost exclusively by a compaction-granulation process. Fine-grained potash feed is generally compacted on roller presses to produce flakes with a density close to that (>95%) of natural potash. These flakes are then crushed and screened to produce a closely-sized (often 2-4 mm) granular product.
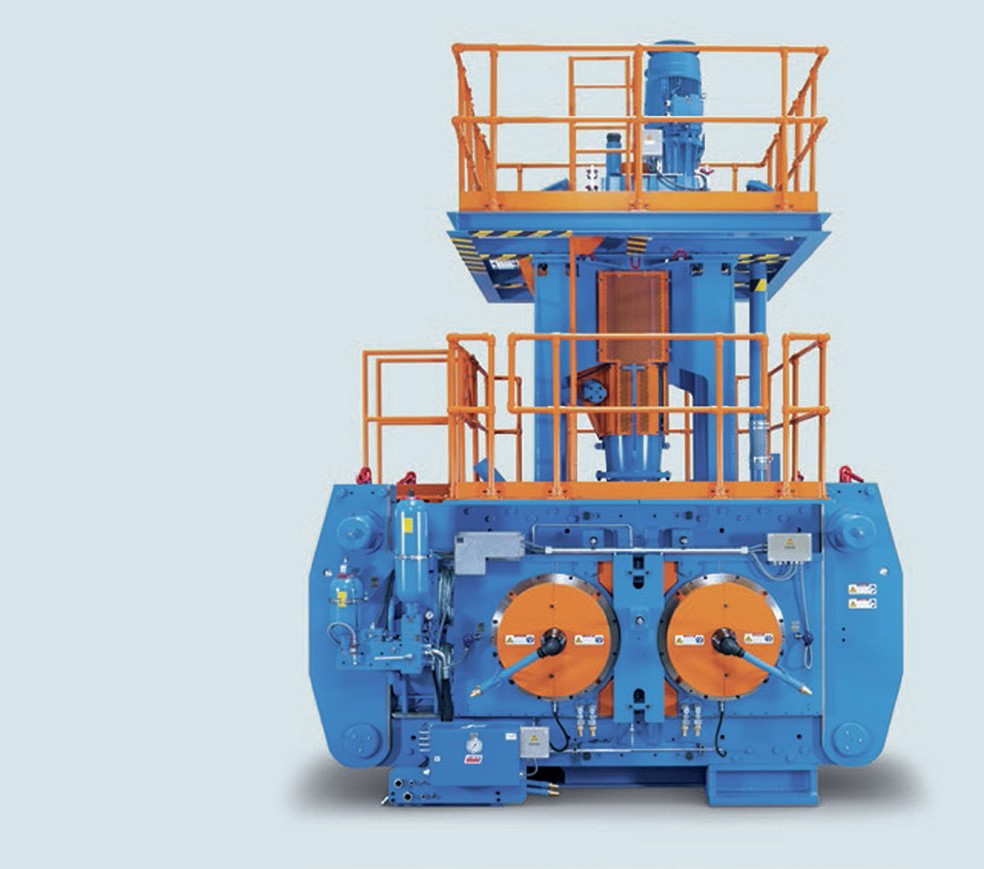
“Granular potash is produced almost exclusively by a compaction-granulation process.”
Three key components
A typical compaction-granulation plant for MOP (muriate of potash) consists of three key components – roller presses (compactors), crushers and screens – configured in closed-circuit. The feed is firstly compacted at an elevated temperature. Köppern typically installs compactors with a 1,150 mm diameter and 1,000 mm working width. Multiple compactors are often installed within one potash plant. These presses have a maximum flake throughput of approximately 140 t/h and a gross granular potash capacity of 40-50 t/h. After compaction, impact and roller mills, working in a closed-loop cycle with multi-deck screens, crush the flakes into granulate with an approximate density of 1.9-1.95 g/cm3 .
Since the 1990s, the preferred flake capacity of potash compactors has increased to 110-130 t/h. The majority of new compactor investments made by potash producers in recent years have been in designs of at least 100 t/h flake.
Design innovation
Köppern has introduced a number of innovations and design changes to ensure compactors of this size are safe, reliable to operate and deliver excellent flake quality. This has involved the modification of various subassemblies, including the frame, feeder, roll design, roll drive and the hydraulic systems.
Vibrations are a particular operational problem when de-aerating and compacting potash – as they can result in severe juddering that damages equipment. The risk of this can be reduced by lowering roll speed and/or feed rate. However, changing the compactor drive design to increase mechanical stiffness is a preferable way of solving this problem at source. This approach also maintains throughput, and is therefore less of a compromise for customers.
For many years, Köppern has stiffened the drive train of large roller presses by manufacturing these with planetary gear reducers mounted directly onto the roll shafts. The company delivered its first large potash compactor (130 t/h) with this drive technology to Germany in 1998. Since then, compactors with this drive design have been widely-adopted worldwide. For example, Köppern’s fertilizer compaction customers in Brazil, Canada, China, Croatia. Hungary, Jordan, Italy, Russia, Serbia and Spain have either modified or ordered new roller presses fitted with this type of main drive.
All large potash compactors supplied by Köppern since the early 1990s have also been supplied with a hinged frame. This allows quick access to rollers for assembly or maintenance. Rollers can be picked up easily without dismantling any part of the frame or feeder.
The feeder is an important component of the compactor. It needs to transport large volumes of material, de-aerate this effectively and distribute it evenly over the entire working width of the roller. The ability to independently adjust screw speeds also prevents misalignment by controlling the gap between rollers. Meeting these requirements prompted Köppern to develop a special double-screw feeder design. This design was first introduced into the potash industry in the mid-1990s in roller press upgrades in Germany and Belarus. The newly developed double-screw feeder was subsequently supplied to K+S in Germany and further clients in Canada, Chile and Belarus.
It is also economically advantageous to provide the roller body with exchangeable tyres, as this allows refurbishment of the tyre profile after wear.
Most of the above improvements and new design features, developed by Köppern over the years, can be found in many compactors used today by the global potash industry.