Sulphur 403 Nov-Dec 2022
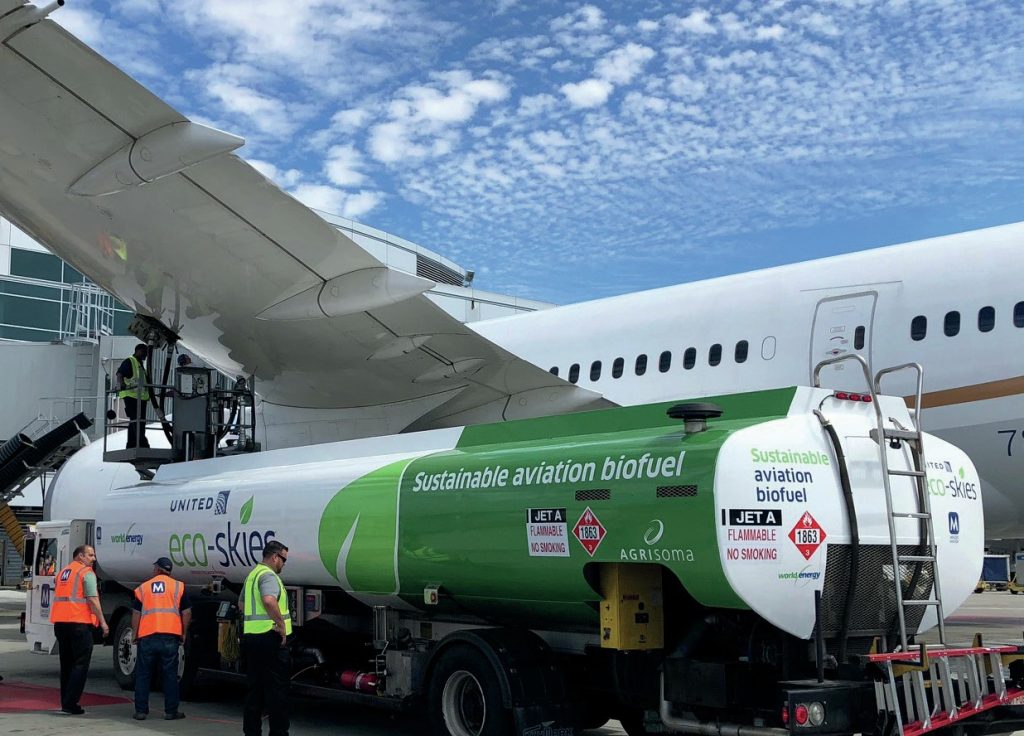
30 November 2022
Sulphur and the aviation industry
AVIATION FUEL
Sulphur and the aviation industry
A move towards so-called ‘sustainable aviation fuels’ (SAF) could see refineries having to recast their operations. What might this mean for sulphur production?
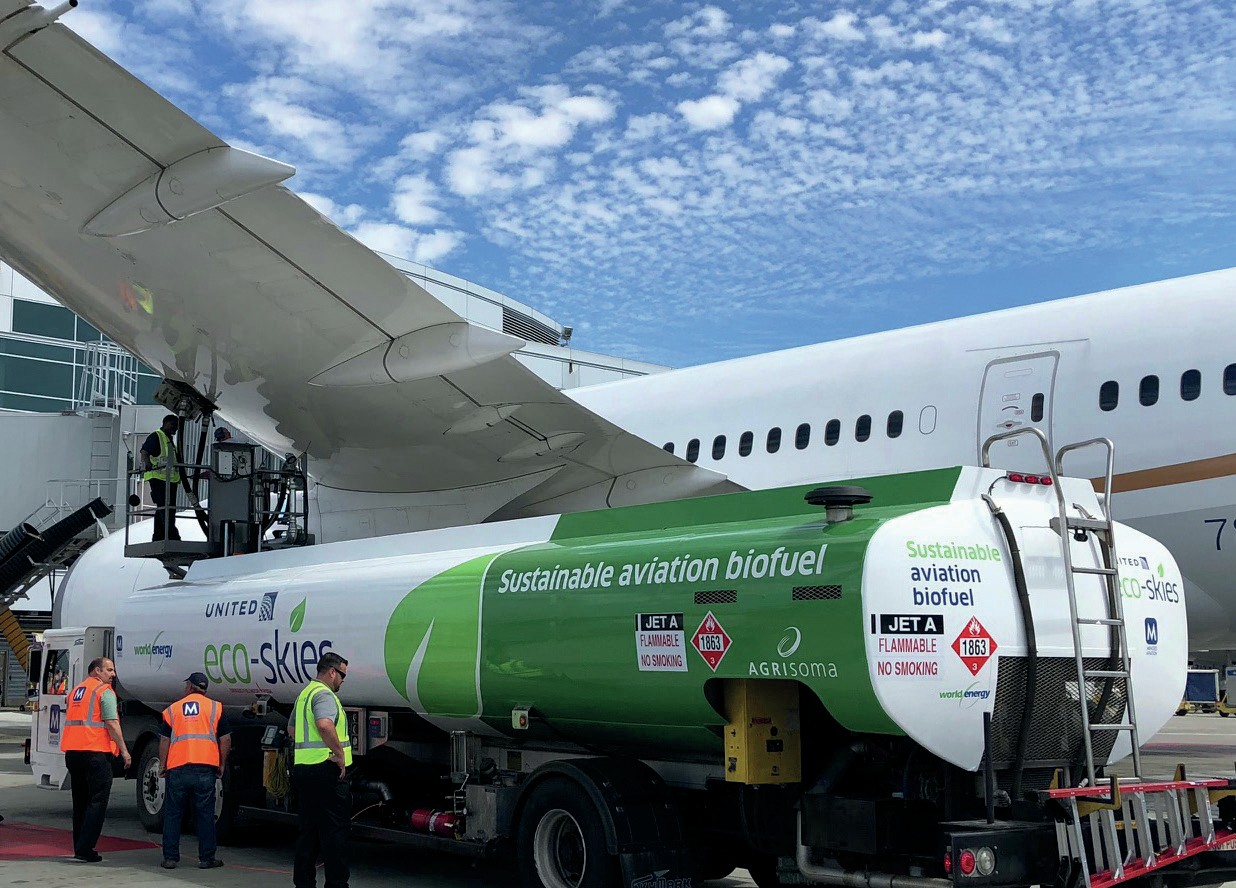
National governments are beginning to bear down increasingly heavily on reduction of carbon dioxide and carbon dioxide equivalent emissions in order to head off potentially disastrous climate change. In the transport sector, road vehicles are moving towards electric power trains, while shipping is looking at a number of low carbon fuels including green ammonia or methanol. The aviation industry, however, responsible for about 2.5% of all greenhouse gas emissions, has a tougher prospect for change ahead of it.
Two factors are shaping the way that the industry is approaching the coming energy transition. The first is the cost of commercial aircraft. Most commercial airliners cost in the region of $80-100 million. For this reason they are often kept in service almost continuously for long periods in order to recover and amortise this cost. This means that aircraft being purchased today may well still be in service in 2050 – the target date that many see as crucial for transition to a ‘net zero’ carbon economy. The other is that aircraft, unlike road vehicles, cannot be electrified – in order to store the same energy that an airliner can carry in its fuel tanks, it would need batteries that weight 30 or so times the weight of aviation fuel; impractical for an aircraft. While hydrogen from renewable sources has been suggested as a future aviation fuel, the fuel tanks would take up most of the fuselage as well as the wings even if the hydrogen were liquid, and will likely require new designs of plane. The assumption therefore is that aircraft will be using liquid hydrocarbon-based fuels not dissimilar to the ones they currently use for the foreseeable future. This leads to the concept of so-called sustainable aviation fuels (SAF).
Sustainable fuels
Sustainable aviation fuel has been defined by the International Civil Aviation Organization (ICAO) as a fuel that achieves net greenhouse gas emission reductions on a life-cycle basis; respects biodiversity conservation and ecosystems from where the feedstock is harvested; contributes to local social and economic development; and where the source of the biomass for this fuel does not compete with food and water requirements for humanity.
The main way that SAF is produced at the moment is via what are known as hydrotreated esters and fatty acids (HEFA). These use lower carbon sources of vegetable oils and fats, such as triglycerides and fatty acids from vegetable oils, (e.g. rapeseed, soybean and corn oil), tall oil, (a co-product from the pulp and paper industry), animal fats, and used cooking oil. The oils are then hydrotreated using hydrogen to remove oxygen and produce a form of diesel which has come to be known as ‘biojet’.
Alcohols such as butanol and ethanol could be used as aviation fuels, and can be produced via fermentation or other biological processes. Other alternatives include gasification and Fischer-Tropsch (F-T) synthesis. Fischer-Tropsch is in effect a carbon polymerisation reaction, and means that a variety of feedstocks, from methane to various gasified solid feeds, can be used to generate the synthesis gas used in the reaction. It has been the basis of so-called gas to liquids (GTL) plants such as Oryx in Qatar. More recently there has been a focus on lower carbon solid feedstocks such as municipal solid waste (MSW), or biomass, e.g. from paper mills or other plant processing. Forms of pyrolysis or torrefaction have also been applied to biomass to generate liquid fuels, but these have not been widely commercialised. Most recently, there has been considerable interest in using hydrogen from electrolysis using renewable power as part of the syngas mix. The theory is that it would be used in conjunction with carbon dioxide captured from industrial processes or even the air to produce a diesel via F-T conversion that is effectively zero carbon. This does of course require access to cheap, renewable electricity, and direct air capture of CO2 remains expensive and at early stages of development, with concentrated sources of waste gases a more likely source of feedstock gas.
Co-processing
Most of the above technologies are effectively stand alone, and do not need to be near or integrated into existing refineries. For refiners, however, co-processing of liquid intermediates in existing refineries is attracting interest. The most likely insertion points are the fluid catalytic cracker (FCC) and the diesel hydrotreater, with the latter the more suitable for SAF production. Currently only 5% blends of lipids and F-T liquids are allowed under ASTM D1655 (coprocessing), though across the whole refining industry this could still make for significant volumes overall.
Production at scale
If SAF is to play a major role in reduction of aviation industry emissions, large volumes will be required, estimated at more than 100 billion litres per year by the International Energy Agency. However, to date, commercialisation has been slow. The total volume of SAF being produced has increased substantially, from around 10 million litres/year in 2018 to around 150 million litres by 2021, but this represents only 0.1% or less of current aviation fuel, and forecasts for 2026 are only around 0.8% of aviation fuel. Most of these are likely to be using HEFA.
New ‘biorefineries’ are being built. Neste has been a pioneer, producing 100,000 t/a of MY Sustainable Aviation Fuel™ which reduces greenhouse gas emissions by up to 80% compared to fossil jet fuel. This will increase to 1.5 million t/a (around 1.88 billion litres) by the end of 2023. It is targeting large expansions in Rotterdam and Singapore which could take this to 4.5 million t/a over the next few years.
Eni is manufactures SAF at its Taranto refinery via co-feeding conventional plants with amounts of used cooking oil. It is also converting its Livorno refinery to distil bio-components produced at the Gela biorefinery via its proprietary Ecofining™ technology. Growth will continue from 2024 with the start of Eni Biojet production at Gela, where a project is already underway that will allow for an additional 150,000 t/a produced from renewable raw materials to be placed on the market, which will meet the Italian market’s potential requirements by 2025.
TotalEnergies says it has begun production of SAF at its Gonfreville refinery in Normandy. It also has some capacity at La Mede refinery and Oudalle, and will produce SAF at its Grandpuits zero-crude refinery starting in 2024. All the biojet will be supplied to French airports and will be produced from waste and residue sourced from the circular economy.
Brasil BioFuels is using Topsoe’s Hydro-Flex™ and H2bridge™ technologies for a new biorefinery being built in Manaus, Brazil, with a production capacity of 500,000 t/a. The plant is expected to start in 2025. H2bridge captures waste propane and carbon off-gas from the refining process, and converts it into hydrogen to be included in powering facility operations.
Chevron is teaming up with Gevo, Inc. to process inedible corn to produce SAF and corn oil and renewable blending components for gasoline to lower its carbon intensity. In addition to co-investing with Gevo in one or more projects, Chevron would have the right to offtake approximately 150 million gallons per year to market to customers. Chevron expects to create the capacity to produce 100,000 bbl/d of renewable fuels by 2030.
“Co-processing of liquid intermediates in existing refineries is attracting interest.”
OMV says that its production of sustainable fuels and chemical feedstock will increase to 1.5 million t/a by 2030, with sustainable aviation fuels accounting for almost half the volume. OMV said it was also aiming to boost sales of SAF to more than 700,000 t/a by 2030.
However, although HEFA is the most widely used SAF pathway today, it is regarded the least scalable one in the long term because of the limitation on sufficient vegetable oil feedstock. A recent industry report suggested it might only be capable of providing 10% SAF by 2050 due to feedstock limitations, with alcohols and Fisher Tropsch pathways accounting for about 40% of the total and the remaining 50% from Power-to-Liquid, identified as being the most scalable in the future in terms of feedstock availability.
Impact on refineries
Although sulphur levels in ground vehicle fuels have been steadily declining over the past couple of decades, down to 10-15 ppm in much of the developed world, and the International Maritime Organisation (IMO) has taken steps to sulphur dioxide emissions from ships, especially in designated ‘emission control zones’ near heavily populated areas, the sulphur content of conventional aviation fuel still remains comparatively loosely regulated. Sulphur content of aviation fuels is capped at 3,000 ppm, though the average is currently around 600 ppm. Though there have been moves to lower this level, there is no regulation currently in the pipeline.
Production of sustainable aviation fuels bypasses this question by producing lower sulphur fuels as a matter of course, though SAF production will alter the sulphur balance according to the process. For biojet from hydrotreated vegetable oils, the sulphur content of the original seeds can be quite high – up to 1.0-1.5% for rapeseed or mustard seed. But most of this remains in the seed when the oil is extracted. Rapeseed oil, for example, only has a sulphur content of around 10-15 ppm, and this level is even lower for other vegetable oils. Gasification also varies widely according to the feed. The sulphur content of municipal solid waste is around 0.1%, all of which must be removed prior to the Fischer-Tropsch step, while for power to liquids, there is of course essentially zero sulphur in a process using pure hydrogen and carbon dioxide.
Co-production of HEFA can probably be accomplished using existing refinery sulphur recovery sections, but grassroots plants will be dealing with much lower levels of sulphur and may need appropriate dedicated solutions such as scavengers or bioprocessing. Either way sulphur output will be appreciably lower if there is a large scale switch to biojet, as seems to be the case.