Nitrogen+Syngas 380 Nov-Dec 2022
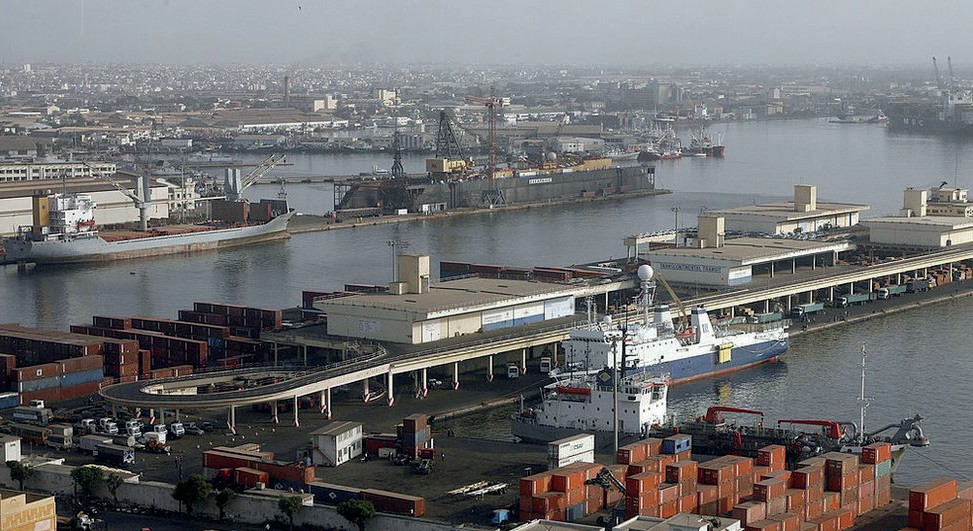
30 November 2022
The Dakar ammonia accident
AMMONIA SAFETY
The Dakar ammonia accident
Seshu Dharmavaram of Air Products and Venkat Pattabathula of SVP Chemical Plant Services describe the Dakar ammonia accident, which occurred in Senegal on March 24th, 1992. It is claimed to be the worst industrial ammonia accident ever, leaving 129 dead and 1,150 injured.
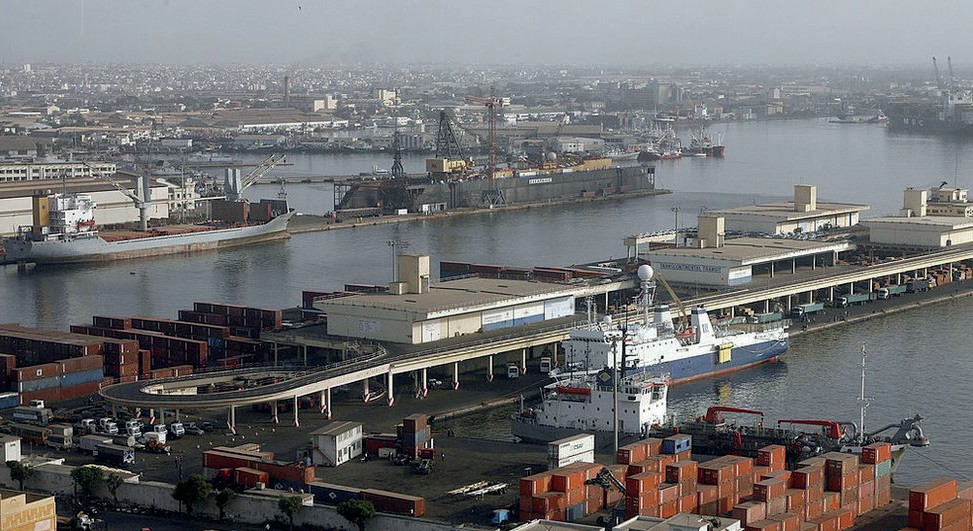
Understanding and managing the hazards of pressurised anhydrous ammonia is extremely important to prevent significant accidents. Many incidents have occurred in the industry in producing, transporting, and using anhydrous ammonia. The Dakar accident is the worst ammonia accident in terms of fatalities and this article describes the incident and an analysis of the consequences observed. It is important to review the details of the accident to derive lessons that all stakeholders can utilise.
The Dakar accident
The accident happened at a peanut oil processing facility operated by Sonacas SA, where ammonia was used to detoxify the product. Anhydrous ammonia was stored in a portable tank commissioned in 1983 and repaired in 1991, before the incident. The weld repairs made were on cracks detected on the tank’s surface. Frequent overfilling of the tank (which was “authorized” to hold 17.7 tonnes) was one of the primary causes noted in the reports. An overpressure inside the tank led to its catastrophic failure. The debris from the explosion of the tank truck also pierced process equipment (e.g. hoses) containing liquid ammonia under pressure. The release of 22 tonnes of liquid ammonia was reported. A two-phase flow of ammonia fluid (vapor plus liquid as fine aerosol) formed a dense vapor cloud and spread over a significant distance resulting in injuries and fatalities. The dense plume settled over the oil mill, nearby offices, and adjacent restaurants where people were present at lunchtime. Forty-one people died immediately, and many others were transported to the nearest trauma center. Ultimately (after a month), the total numbers were determined to be one hundred twenty-nine fatalities and 1,150 injuries.
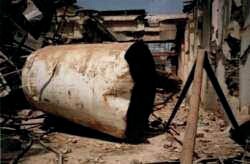
Most of the injuries and fatalities resulted from inhalation of ammonia at high enough concentrations to cause respiratory lesions, edema in the lungs, and skin/eyes irritation. Near the release location, many of the fatalities resulted from direct skin exposure and cold burns and inhalation of high concentrations. Fortunately, because of the Ramadan holidays, the schools nearby were closed, and restaurants were less crowded. Otherwise, the number of fatalities and injuries could have been much higher.
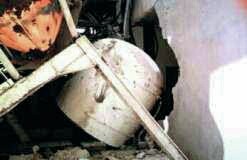
Process operation
Peanuts and peanut oil were among the top commodities exported from Senegal in the 1990s. To extract peanut oil from peanuts, anhydrous ammonia was used to detoxify the product at a peanut oil mill in Dakar which Sonacos SA owned. Anhydrous ammonia was brought to the mill by a road truck from a fertilizer company nearby that stored large quantities of cold liquid ammonia in spheres. The tank was then placed at the mill for use as a storage vessel since no other storage tanks were present at the mill.
The details of the ammonia tank that exploded were as follows:
Diameter: 2.2 m
Thickness: 11 mm
Volume: 33.5 m3
Construction material: Annealed hardened steel
Construction year: 1983
Last maintenance year: 1991
The tank was built by a French company in 1983 and certified as compliant with regulations. From 1983 to 1991, the tank truck was frequently overfilled beyond the authorised 17.7-tonne filling limit. The overfilling led to overpressure and crack formation that was detected in 1991. The crack was welded but not annealed. After the repairs were done, the truck continued to be overfilled on the day before the accident. The tank was filled with 22,180 kg of liquid ammonia under pressure and was placed at the mill.
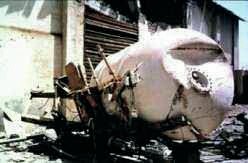
Around 1:30 to 2:00 PM (during a shift change), on March 24, 1992, the tank suddenly burst open along the middle with the two portions propelled in different directions. The collision from the tank contacting the buildings caused significant damage and debris (Figs. 1-3). The chassis and axle from the truck were found up to 200 meters away beyond the facility boundary. Anhydrous ammonia from the tank was re-leased almost instantaneously, and heavy, dense clouds spread well beyond the facility into the industrial and residential neighborhoods. The debris caused the failure of a hose connected to the process vessel, with the discharge continuing for at least half an hour.
Weather
During the time of the accident, the temperature was 26°C, with a wind speed of 4 ms-1 from the north. These weather conditions were used for the consequence analysis discussed below.
Medical treatment
On April 2, 1992, US Ambassador Katherine Shirley declared a disaster and requested the purchase of emergency respiratory and cardiac monitoring equipment. Pulse oximeters and ECG cardio-scopes with accessories were procured and immediately dispatched to Senegal. The equipment was donated to the intensive care unit at Dakar’s Trauma Center, where victims seriously injured by accident were being treated. Nine days after the equipment was received, USAID/Senegal representatives met with the Trauma Center staff and were told by the physician in charge that the equipment had made a difference between life and death. Of the more than 400 patients admitted to the Center, only 31 remained under treatment. In mid-April. the total death count from the accident was 129 people.
The patients treated for minor skin lesions developed pulmonary edema (fluid build-up in the lungs) in the trauma center. Most of the people killed near the tank explosion and release were in semi-confined locations (mill, restaurants, damaged buildings, and in the streets nearby). Among the injured were emergency responders that were ill-prepared to deal with an event of this magnitude.
A detailed chronological study based on an autopsy of people that died revealed that the victims were between 3 months and 74 years old. The cause of death was identified as the aftereffects of pneumopathy (pulmonary infection, bronchiectasis, and pulmonary fibrosis). The intensity of lesions and mortality was pro-portional to the quantity of inhaled ammonia per m3 of air.
Primary cause: overfilling
A systematic root cause analysis of the Dakar accident can yield multiple causal factors (related to design, operation, hazards management, etc.) resulting in the incident. However, there is one primary cause (overfilling) that is obvious and has resulted in and continues to cause numerous incidents throughout the world.
Understanding the hazards of overfilling and determining the ‘filling ratio’ for a variety of containers (cylinders, tanks, etc.) to avoid incidents like this Dakar accident has been widely recognised. Overfilling of high pressure compressed gases can result in overpressure and loss of containment.
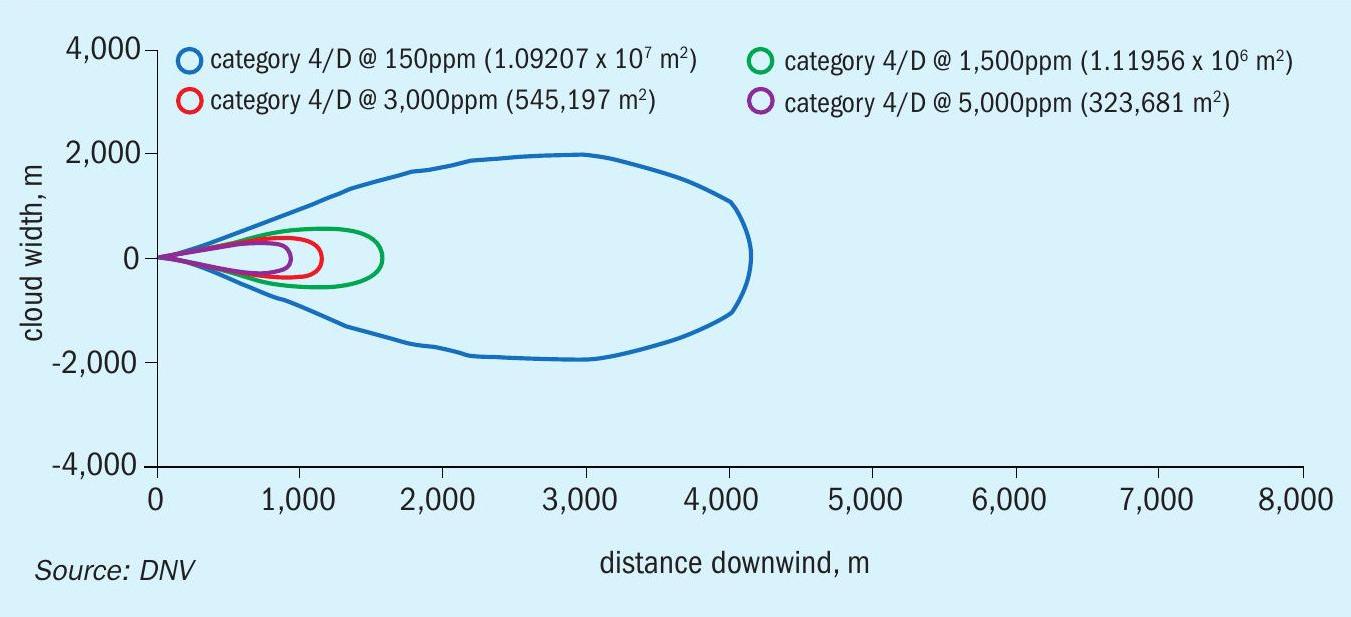
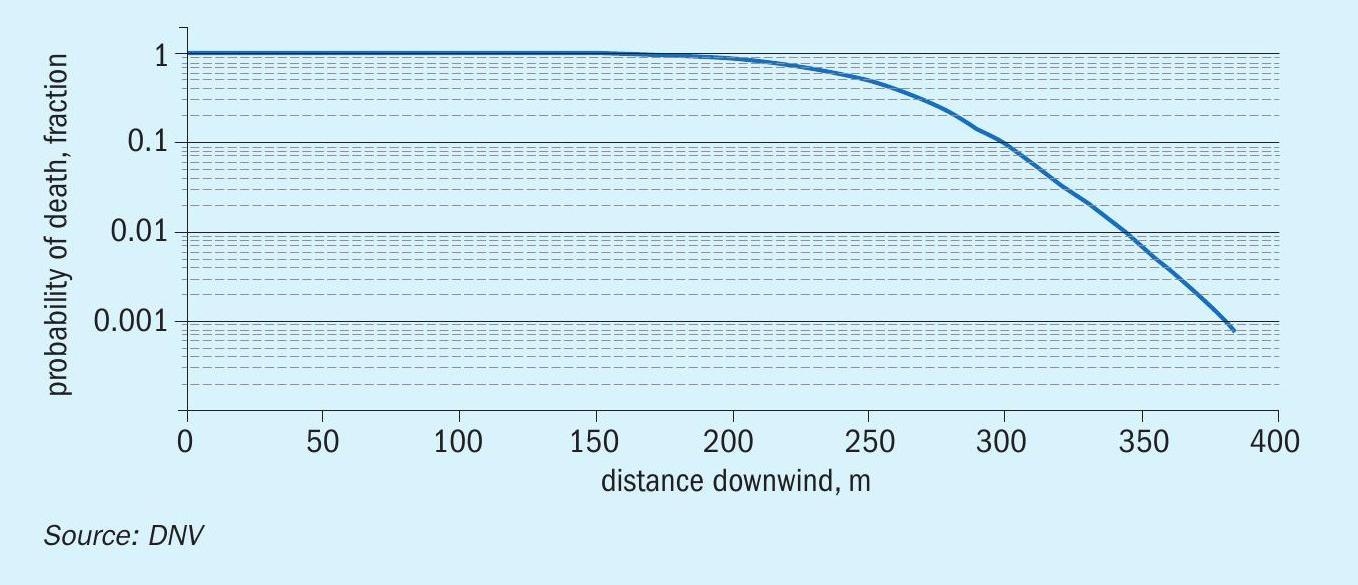
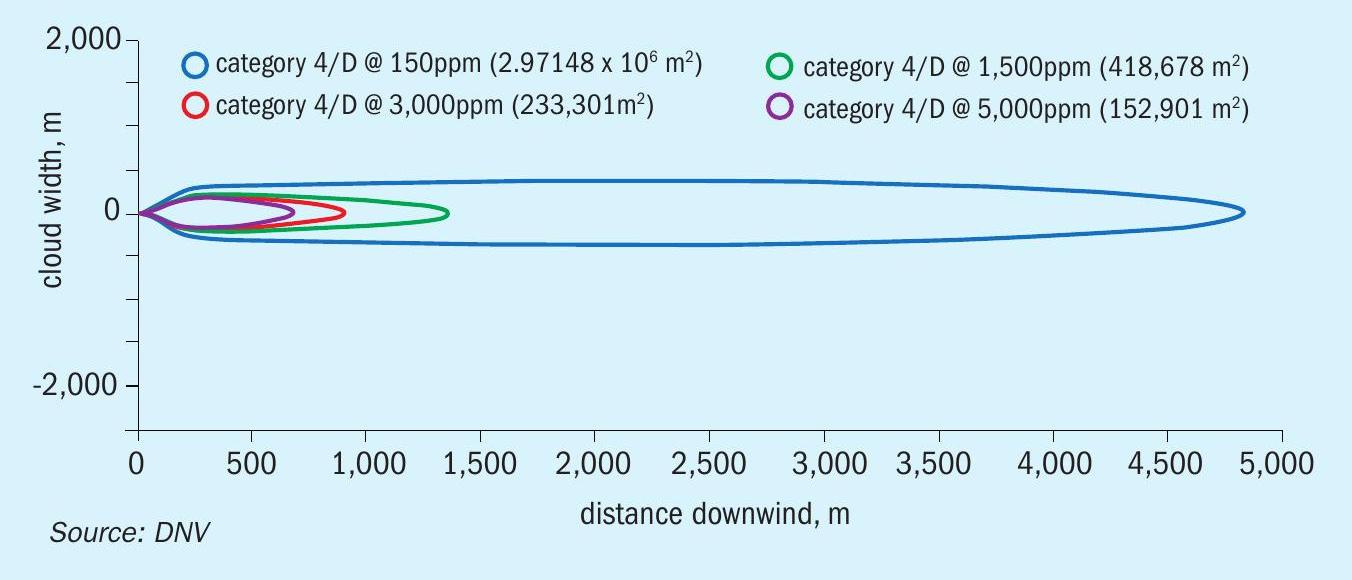
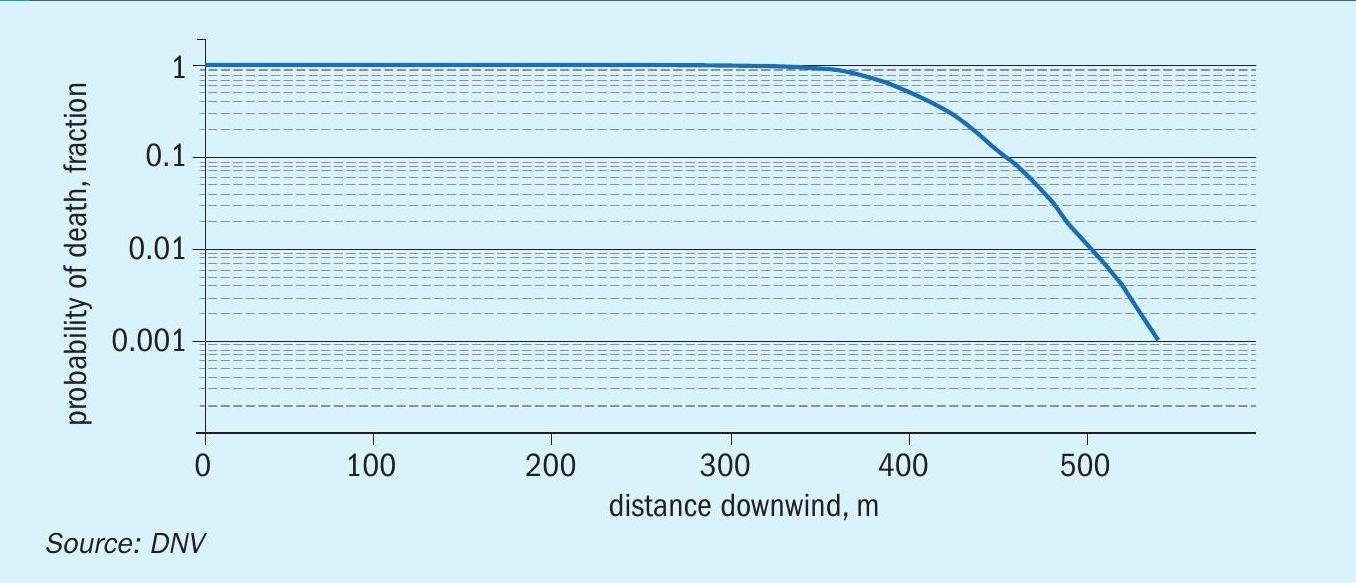
The filling ratio is defined as: “the ratio of the mass of gas to the mass of water at 15°C that would fill completely fitted ready for use”. For high-pressure liquified gases (like anhydrous ammonia), the filling ratio is determined such that the settled pressure at 65°C does not exceed the test pressure of the pressure receptacles. The minimum test pressure typically re-quired is 1 MPa (10 bar). If relevant data are not available for high-pressure liquified gases, the maximum filling ratio is determined as follows:
FR = 8.5 x 10-4 x dg x Ph where
dg = gas density (at 15°C, 1 bar) (in kg/m3 )
Ph = minimum test pressure (in bar)
For a tank (or any other receptacle) containing anhydrous ammonia under pressure, it is best to ensure that the filling ratio does not exceed 0.53. The tank in the Dakar accident was overfilled to almost the full volumetric capacity of the vessel (33.5 m3 ) before the day of the accident.
Consequence analysis
An analysis of the consequences of the ammonia releases during the incident on March 24, 1992, can be done using the release and weather data that is available. The Emergency Response Planning Guideline (ERPG) concentrations published by the American Industrial Hygienists Association can be used to determine the acute toxicity effects. The ERPG-2 and ERPG-3 concentrations for ammonia are 150 ppm and 1,500 ppm, respectively. ERPG-2 is a concentration above which irreversible injuries can occur. Very serious injuries and potential fatalities can occur based on exposure time at concentrations above ERPG-3.
The probability of fatality can be determined using Specified Level of Toxicity (SLOT) and Significant Likelihood of Death (SLOD), and Dangerous Toxic Load (DTL) data published by the UK Health and Safety Executive. On March 24, 1992, around 22 tonnes were instantaneously released when the tank exploded. In addition, loss of containment from a hose connected to the process tank continued for a significant period of time.
The DNV PHAST model was used to model the release and dispersion of the heavy gas cloud from the two scenarios (instantaneous release: 22 tonnes; and continuous release: hose failure). The maximum footprint generated by the instantaneous release of 22 tonnes is shown in Figure 4.
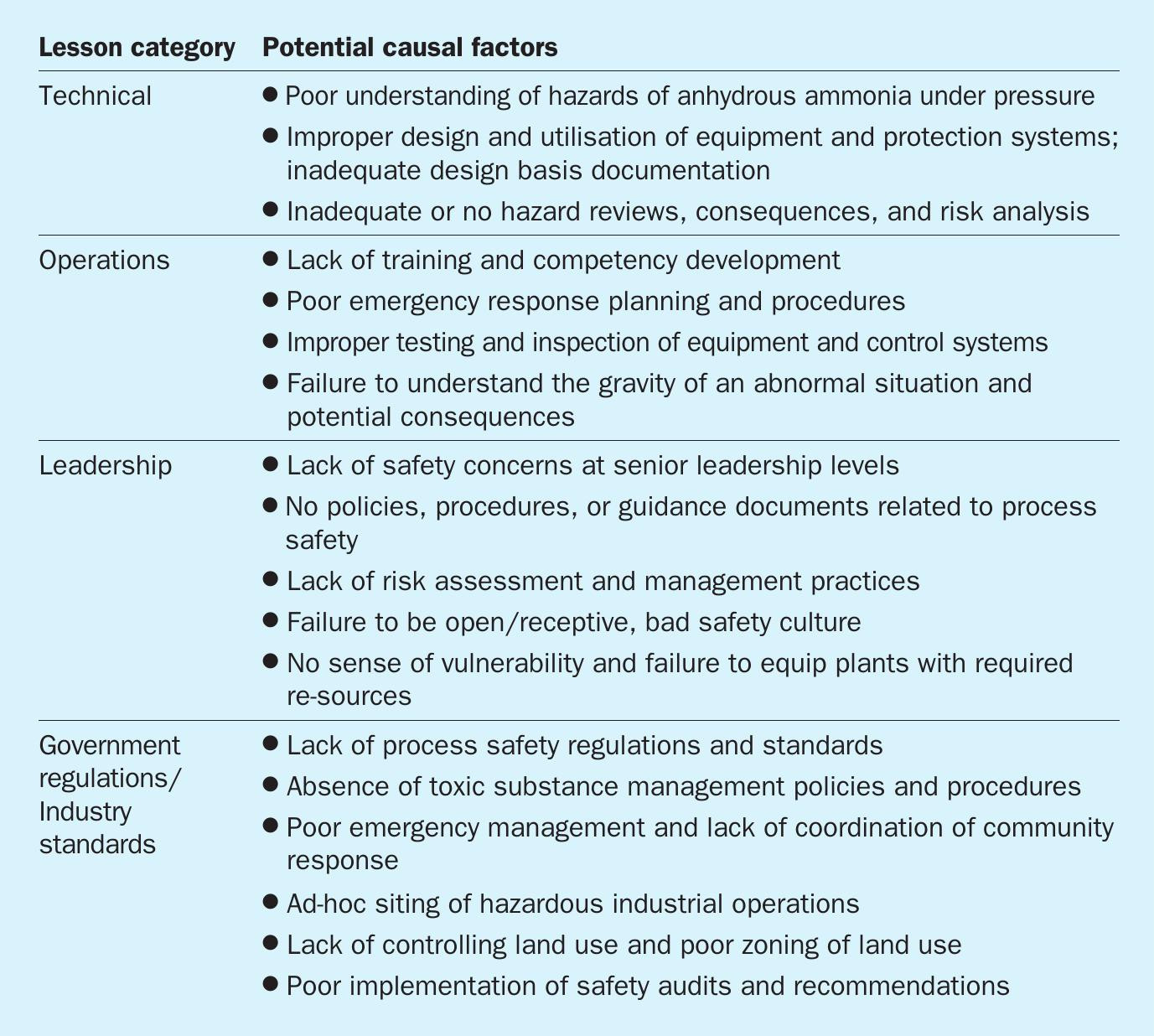
The injury concentrations (ERPG-2) extend to more than 4 km and with a width of about 4 km. The distance to ERPG-3 is about 1.5 km, the zone within which there might have been serious injuries and fatalities. The cloud would have been visible only up to a 900 m. Figure 5 shows an estimate of distances for the higher probability of fatalities. Up to a distance to almost 200 m, the probability of fatality is 100%, and then it drops to 0.1% by 500 m, primarily because the exposure time is shorter for an instantaneous release.
The maximum footprint generated by the continuous release from a 3-inch hole (e.g., hose failure) is shown in Figure 6. The plume is narrower (less than 1 km), but the injury concentrations (ERPG-2) extend to almost 5 km. The distance to ERPG-3 is less than 1.5 km, again the zone where there might have been serious injuries and fatalities. The visible range would have also been around 900 m. Figure 10 shows an estimate of distances to a high probability of fatalities. Up to a distance of almost 400 m, the probability of fatality is 100%.
Based on the proximity of the population near the paper mill that has been reported, it is therefore not surprising that 1,150 people were injured, and there were 129 fatalities. Because of a religious holiday (Ramadan), the population off-site, especially in nearby schools and restaurants, was a lot lower. If this incident had occurred on any other day, the injuries and fatalities would have been higher.
Lessons learned
A detailed analysis of the causal factors can only be done using evidence (preserved/protected) and related data from the day of the accident. After a period of 30 years, it is almost impossible to reconstruct all the details based on limited data that is currently available in public literature. However, some general lesson categories (related to technology, operations, management, etc.) and generic causes can still be extracted. Table 1 below provides a summary of lesson categories and high-level causes, that can be broadly leveraged to prevent such incidents from happening.
In addition to the primary cause (i.e. overfilling) noted above, there were many failures in the following categories: technical; operations; facility/corporate leadership; government oversight; and industrial standards/governance. These are all important for safe operation of ammonia facilities in all global locations.
An industrial standards organisation for ammonia (such as exist for other chemicals like chlorine – Chlorine Institute, Eurochlor) might improve process safety performance in all jurisdictions, particularly in developing countries. The production and use of anhydrous ammonia is expected to increase dramatically across the world in the next few years.
In Senegal, anhydrous ammonia will continue to be used in large quantities since it is needed to detoxify agricultural commodities (i.e. nut oils) to eliminate aflatoxins. The demand is high and likely to increase over time. Ammonia is currently seen as a “formidable and indispensable killer” resulting from the Dakar accident in Senegal. Lessons from Dakar and other incidents can be effectively used and leveraged to improve the perception of ammonia and promote its safe handling everywhere.
Summary
The Bhopal accident was the worst industrial accident, but the Dakar accident on March 24, 1992, is the worst ammonia industrial accident ever. It was also the worst industrial accident in Senegal. High pressure in a portable tank resulted in the crack spreading and splitting the tank into two parts and a loss of containment of 22 tonnes of ammonia. The debris also damaged process equipment and resulted in an extended release from a hose failure.
An analysis of the consequences of the ammonia release scenarios demonstrates that the estimated distances for potential fatalities (1 km) and injuries (4 to 5 km) is very significant, with 129 fatalities and 1,150 injuries that occurred on March 24, 1992.
It has been well argued and proven that accidents like those that occurred at Bhopal and Dakar in developing countries (India and Senegal), can occur in developed countries, too, even with more robust regulations and industry standards. But it is essential to continue developing and implementing standards for safe designs, operations, and governance and thus improve process safety performance at anhydrous ammonia storage and handling facilities.