Nitrogen+Syngas 381 Jan-Feb 2023
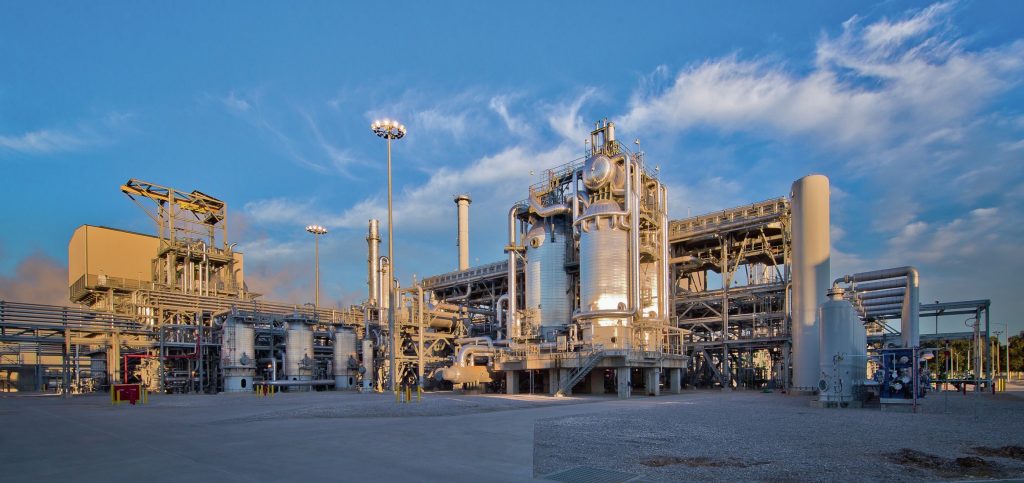
31 January 2023
Decentralised small scale methanol plants
METHANOL PLANTS
Decentralised small scale methanol plants
Air Liquide presents the results of an internal study to identify preferred natural gas-based plant configurations at a methanol capacity of 250 t/d. Delivering small capacity plants requires a focus on the total cost of ownership (TCO) for the economics to be successful, in addition to the CO 2 footprint of the operation. As found by this study, SMR concepts are naturally power balanced for standalone greenfield operations and show no particular advantage for power import in a brownfield setting. POX and ATR cases are greatly improved and even advantaged in a brownfield setting compared to SMR when shifting from power balance to power import cases.
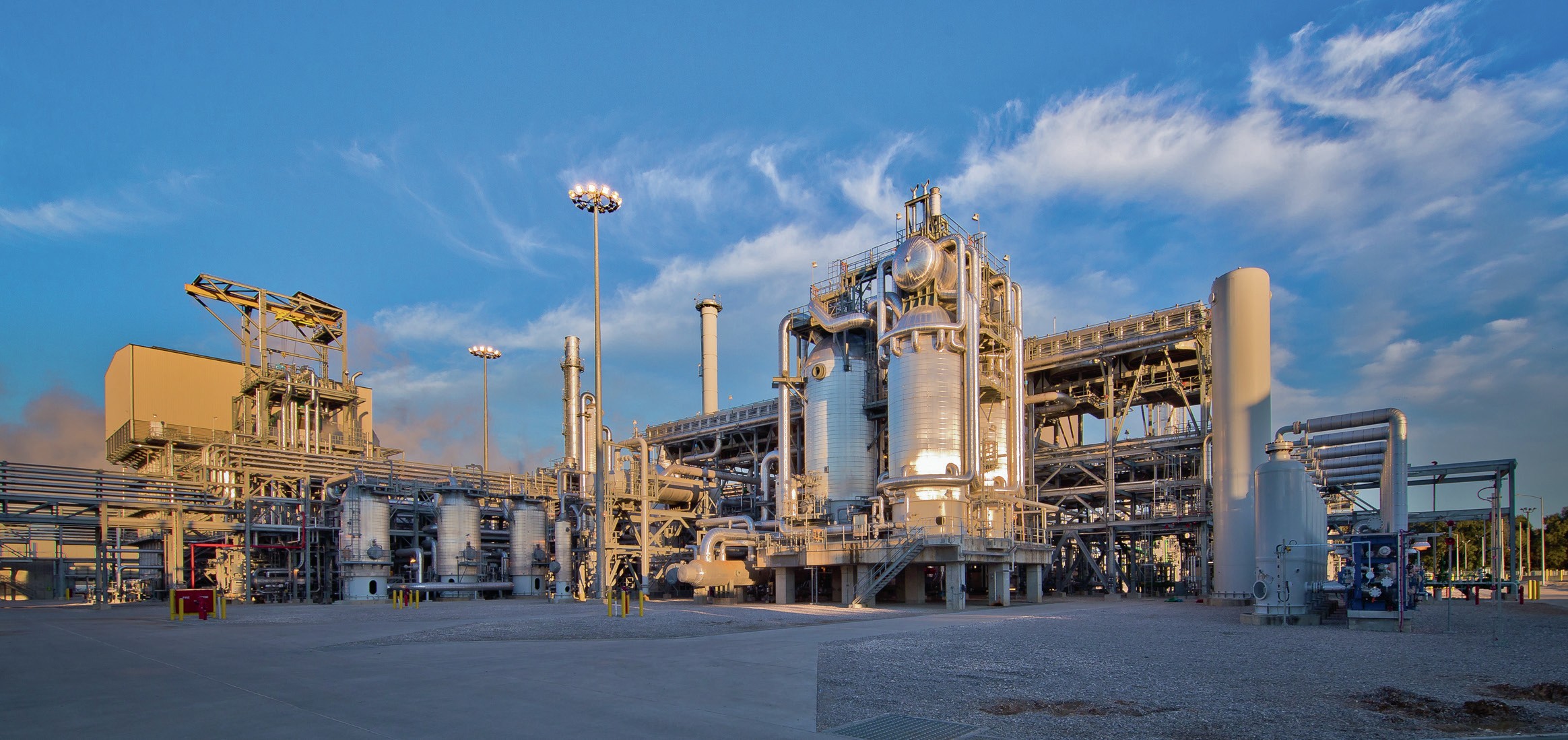
Methanol is an important building block for producing high value chemicals and is a perfect fit for energy storage and for producing clean fuels. Methanol is a molecule fully mastered by Air Liquide 1-7 . Air Liquide Engineering & Construction is a leading technology provider and licensor for methanol production plants with a methanol technology market share of more than 45% (2000-2017 based on plant capacities). Methanol plant designs are available for all capacities up to 10,000 metric tonnes per day (single train), based on a variety of diff erent hydrocarbon-containing feedstocks. Since 1969, more than 68 licenses have been sold globally for a capacity of more than 55.5 million tonnes per year of methanol production. The predominant route to produce methanol uses natural gas as feedstock. Fig. 1 shows a large methanol plant in North America using the Lurgi MegaMethanol ™ process to produce 5,000 t/d of methanol, based on natural gas feedstock. Air Liquide’s scope of work for this plant included the license, basic engineering, detailed engineering and proprietary equipment.
In addition to its R&D and various commercial products in its portfolio, including the Lurgi ™ Methanol and Lurgi MegaMethanol ™ technologies 8-10 , Air Liquide is also well-known for its syngas generation and synthesis units, for the production of oxygen such as air separation units (ASU) as well as for hydrogen recovery such as pressure swing adsorption units (PSA), making it a one-stop shop for customers wanting to build small-scale methanol plants.
Despite the trend for designing large-scale methanol plants, smaller capacities in specific geographies are also of interest for customers that have a source of natural gas available. Therefore, small-scale plants at a capacity of about 250 t/d can be useful in specific situat ions and locations. Small-scale methanol based upon natural gas makes particular sense for distributed production to monetise remote gas supplies (e.g. flare gas). In this case, the avoided emissions are significant, irrespective of the plant efficiency, because the gas would have otherwise been directly flared. Alternatively, small plants can be used to locally produce methanol and avoid difficult (costly) logistical supply – thus avoiding the emissions of transport. A large margin exists between local gas prices and the cost remote customers are required to pay for methanol.
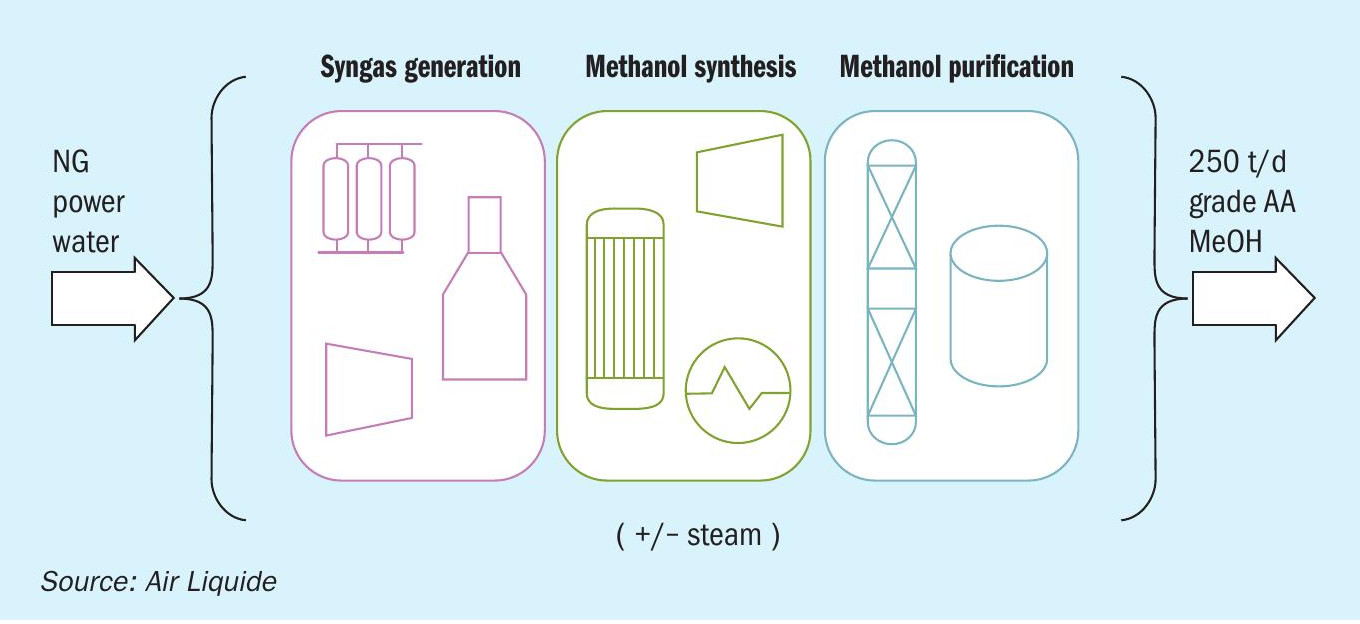
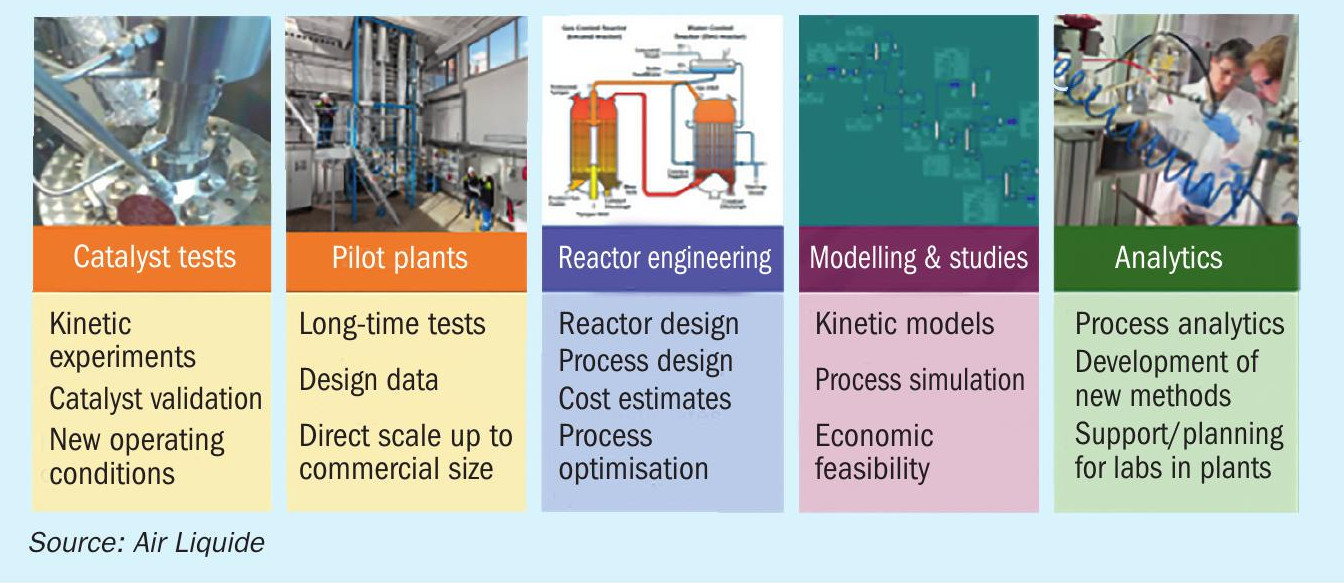
The study
Delivering small capacity plants requires a focus on the total cost of ownership (TCO) for the economics to be successful, in addition to the CO 2 footprint of the operation. In this article, Air Liquide presents the results of a study to identify preferred natural gas-based plant configurations at a capacity of 250 t/d of methanol (Fig. 2).
Without economies of scale, smaller plant capital costs (e.g. capex) for equipment, engineering and construction contribute the majority of the TCO in comparison to operating costs, which includes the feedstock and utilities. Thus, a particular focus was placed on the syngas generation section of the plant where the majority of the capex is located. Another focus was to ensure that the carbon footprint of these small-scale units can be minimised.
Use of remote/stranded gas is seen as a major field of application in connection with the geographically dispersed and oversupplied US market, but also in other regions where gas associated with crude production is routinely flared. In these locations, production of a liquid methanol product represents monetisation of an otherwise wasted resource and the avoidance of greenhouse gas emissions (either as methane or CO 2 ). In some locations, such as North America, government regulations and public pressure are driving the reduction of flare usage. US Methanol has seen some success based upon the relocation of older, small-scale assets to new locations, but these opportunities are limited.
Another potential market is underutilised syngas-producing assets. Converting syngas assets partly (or fully) to methanol synthesis units can be successful because the capital-intensive syngas asset already exists and therefore, the incremental investment costs for methanol are low. In addition, integration at an existing site for a small methanol unit for captive use will offer benefits on utility investment. Furthermore, recent changes in the tax credits in the US amplify the potential value of these opportunities for hydrogen producing assets. Avoidance of CO 2 emissions of existing steam methane reforming (SMR) plants can have a significant financial impact in these geographies.
Thirdly, integration with methanol consumers is also foreseen to be an interesting market. Of these, the largest downstream market for methanol is formaldehyde. Potential customers could be methanol consumers at locations where transport of methanol is costly due to distances from major ports and at the same time, local supplies of natural gas are available.
Air Liquide leverages competencies in engineering and construction as well as pilot studies which are able to generate results that can be scaled up for design and optimisation of commercial offers. Fig. 3 provides an overview of the capabilities and expertise of Air Liquide R&D. Linking to the small-scale methanol topic from natural gas, these pilots are used to de-risk more aggressive operating conditions, to fine tune existing kinetics and to estimate the amount of by-products produced within the methanol synthesis. These aspects are key elements in order to make small-scale setups more attractive.
Results
Screening of different syngas generation processes
After the syngas generation section, the process flowsheet of the methanol synthesis and distillation sections were held more or less constant for the screening of the syngas generation process. The synthesis section is composed of a syngas compressor, an interchanger, a water-cooled reactor, a final cooler, a crude methanol separator and a recycle compressor – the same assumption is taken for all cases. The design of the underlying equipment and operating conditions were optimised for the respective syngas of each case studied. In the distillation section, an optimised system was consistently used to produce Grade AA methanol product. In some cases, specific heat integrations were modified for better operating costs.
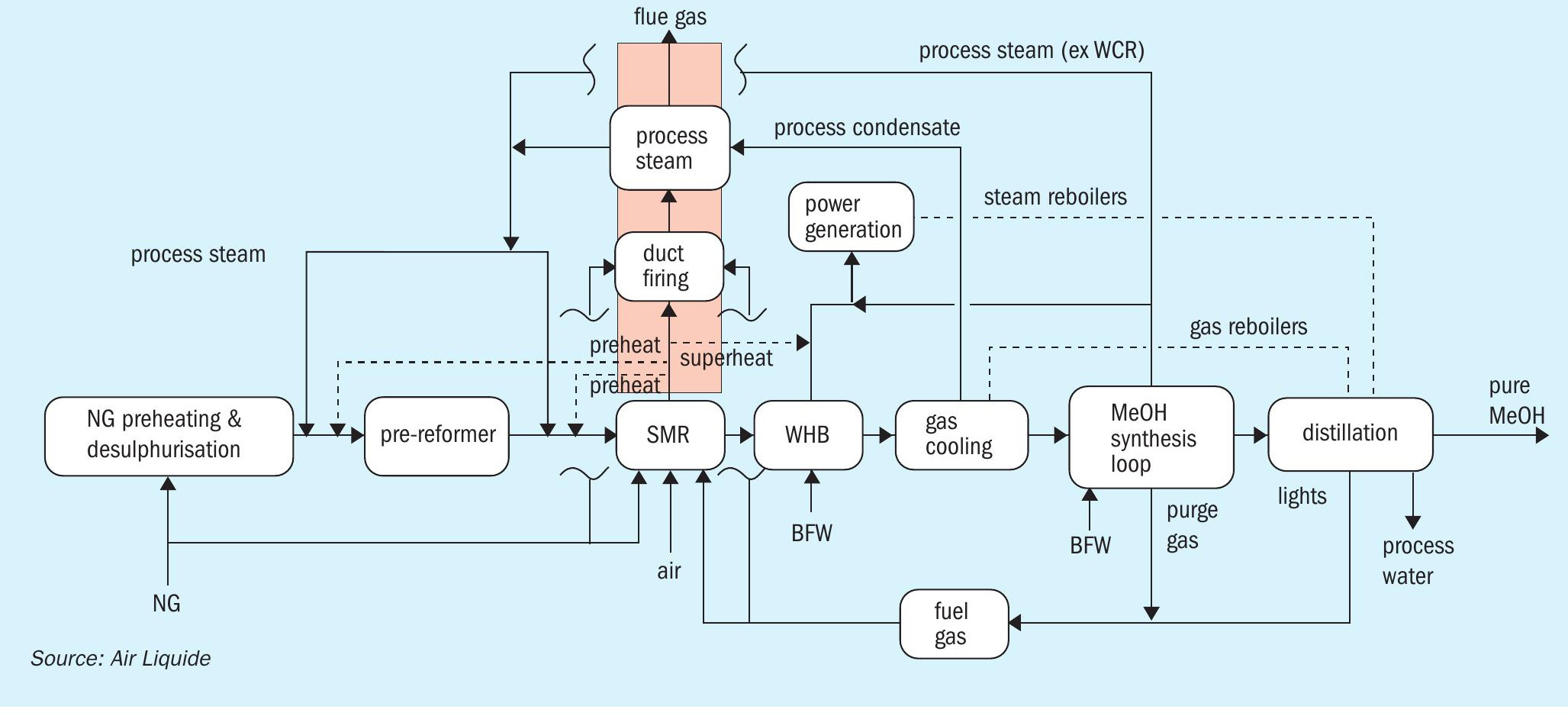
POX and ATR-based process set-ups always require a PSA unit to recover hydrogen from the methanol synthesis purge gas. This hydrogen is added to the reformed gas to manage the stoichiometric number (SN) of the make-up gas mixture composition. Oxygen production for the POX and ATR cases were included within the plant scope – either by modular, standardised cryogenic air separation units, vacuum swing adsorption units or other air separation technologies developed by Air Liquide.
The various process setups have been compared as stand-alone units that were independent of imported utilities, except for gas and water. Thus, power demand was balanced by on-site production within the scope of the plant. The equipment and operating costs for this are included in the total cost of ownership (TCO). The TCO includes both depreciation and operating costs per tonne of methanol product. When import power was used, the indirect emissions were estimated assuming a carbon loading of 500 kg CO 2 per MWh, a midrange carbon loading considered typical for the US power grid.
Basic equipment designs were made and the capital costs were estimated from reference projects executed by Air Liquide Engineering & Construction and internal cost databases. Operating costs were estimated by validated simulation tools – the same used to design world-scale plants. Taken together, the TCO was calculated, including the capital portion as a depreciation charge, to represent the gate cost of methanol using a consistent set of assumptions.
Definition of a base case
The SMR case depicted in Fig. 4 was used as the base for this study. Syngas by POX and ATR can also be considered for methanol production, however, more than one reforming step was not considered to be economically feasible for small-scale methanol plants. Each case considered different configurations or operating conditions for syngas production by SMR, ATR or POX.
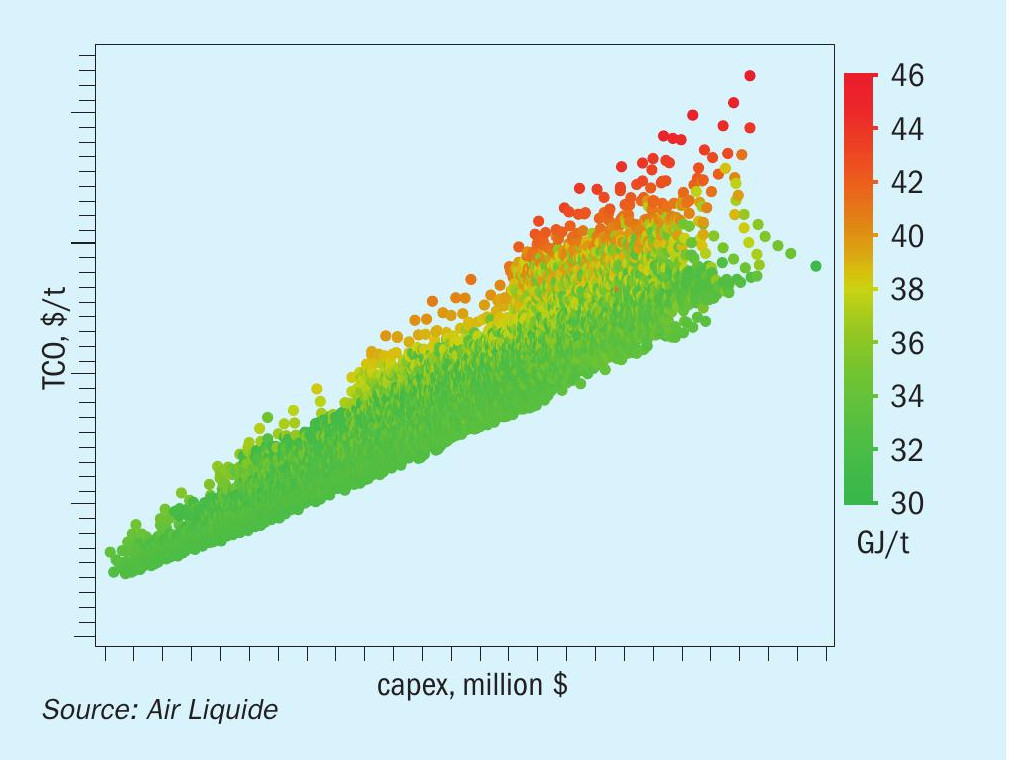
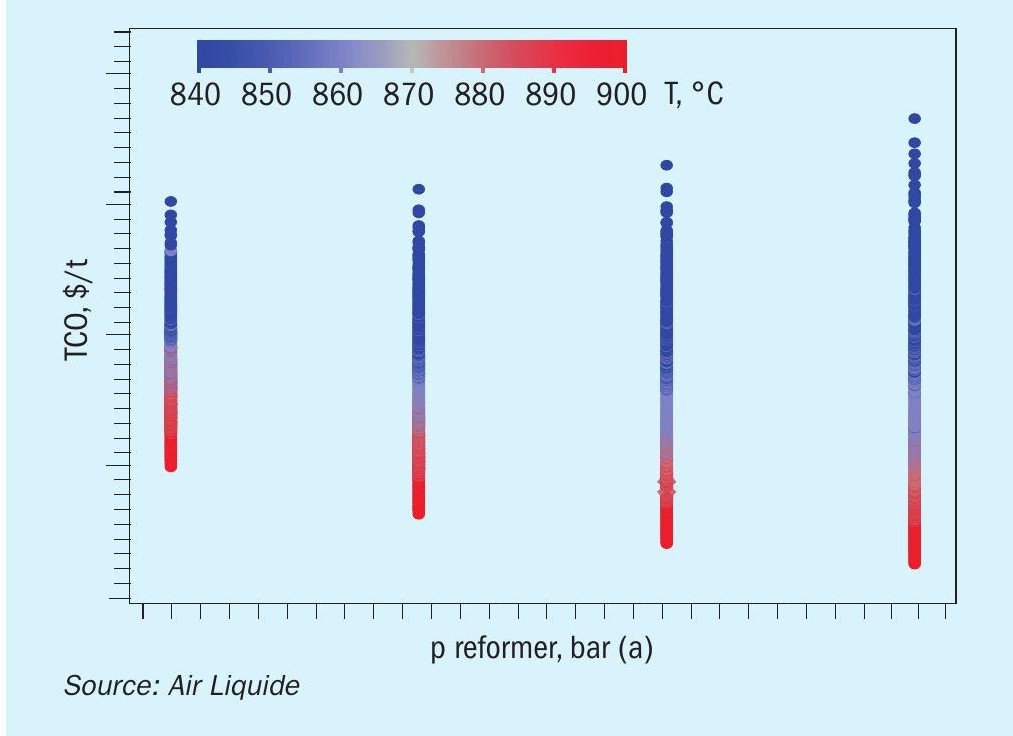
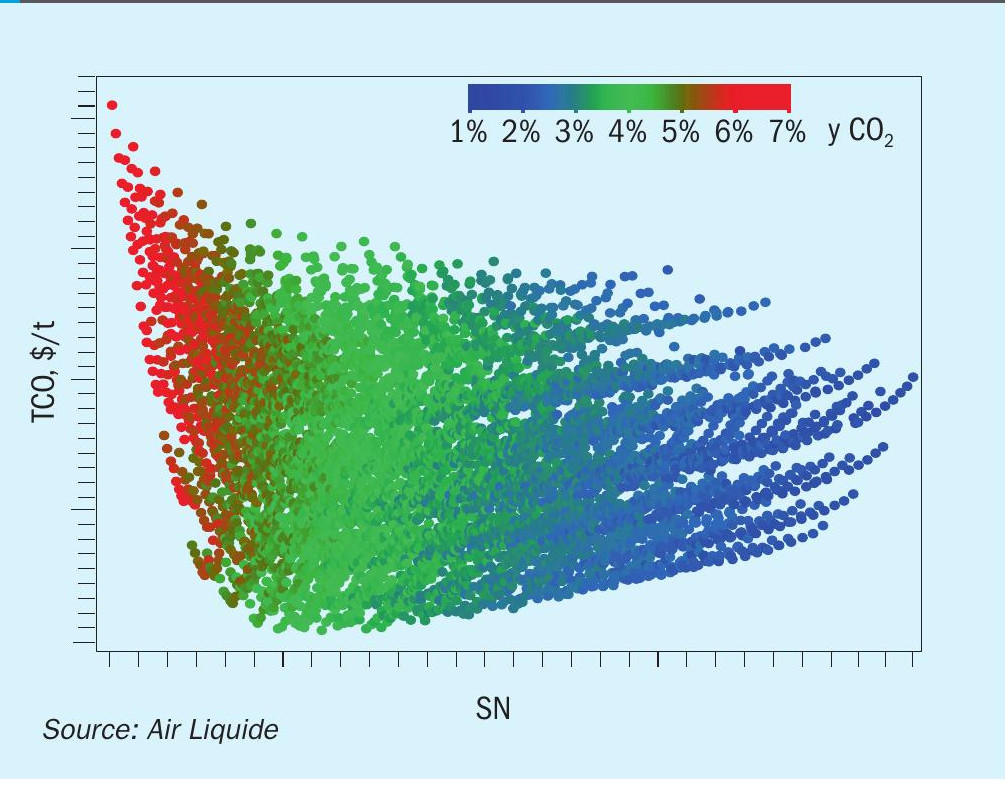
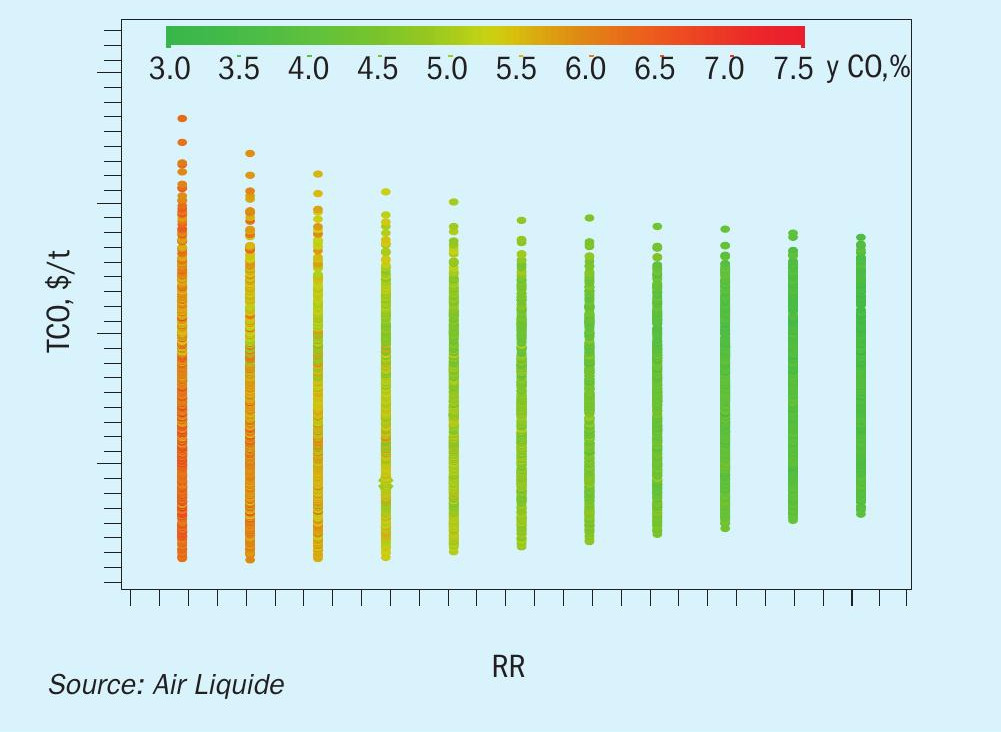
Grade AA methanol product makes sense for a standard product offer, as it provides maximum flexibility for downstream applications. A lower grade could be offered by eliminating or adjusting the final purification column. Some formaldehyde producers accept up to 15% water content, for example – a capital and energy savings versus production of Grade AA. Nevertheless, in this work, only Grade AA methanol has been considered.
A sensitivity analysis for the SMR base case has been performed. Parameters such as steam to carbon ratio (S/C), SMR temperature and pressure and synthesis loop pressure and recycle ratio were all investigated:
- steam/carbon ratio (S/C)= 2-2.7;
- SMR temperature = 840-900 °C;
- SMR pressure = 16-25 bar;
- recycle ratio (RR) for the methanol synthesis = 2-4;
- methanol loop pressure = 60-80 bar;
- stoichiometric number at methanol reactor inlet:
SN = (H 2 -CO 2 )/(CO + CO 2 ) in vol-%.
Many parameters can affect the TCO and can be optimised regarding the specific location and environment of such a small-scale methanol unit. For example, the main factors that affect the TCO for the SMR cases are:
- The reformer temperature – higher temperatures lead to lower TCO.
- Higher reformer pressures are beneficial for optimum TCO for intermediate S/C, CO, CO 2 and RR.
- Higher loop pressures are preferred for methanol synthesis.
- In general, more aggressive (lower SN) conditions help to lower TCO but shouldn’t be too extreme both for TCO and also feasibility reasons.
The results for the SMR cases regarding TCO are illustrated in Figs 5-8. This extensive study allows optimised process parameters versus TCO for each situation inside a given flowsheet. In these figures, a wide parameter space was studied to determine the limiting Pareto front for capex (and TCO), in relation to operating conditions for the SMR and synthesis.
Any of the three technologies SMR, ATR and POX could be used upstream of the methanol synthesis. Besides the TCO, particular attention has been given to the estimation of the CO 2 emissions in comparison to the reference case presented in this section.
Power balance cases
The three main options for syngas generation from natural gas (POX, ATR and SMR) were evaluated by constructing process simulations and estimating the TCO of the produced methanol as seen in the upper portion of Table 1.
The power balanced cases show that both POX and ATR solutions have a higher TCO than SMR. This is because the waste heat in the SMR case is sufficient for the required power production. The oxygen-based solutions require additional gas (beyond tail gas) for dedicated power, impacting the relative efficiency and CO 2 emissions.
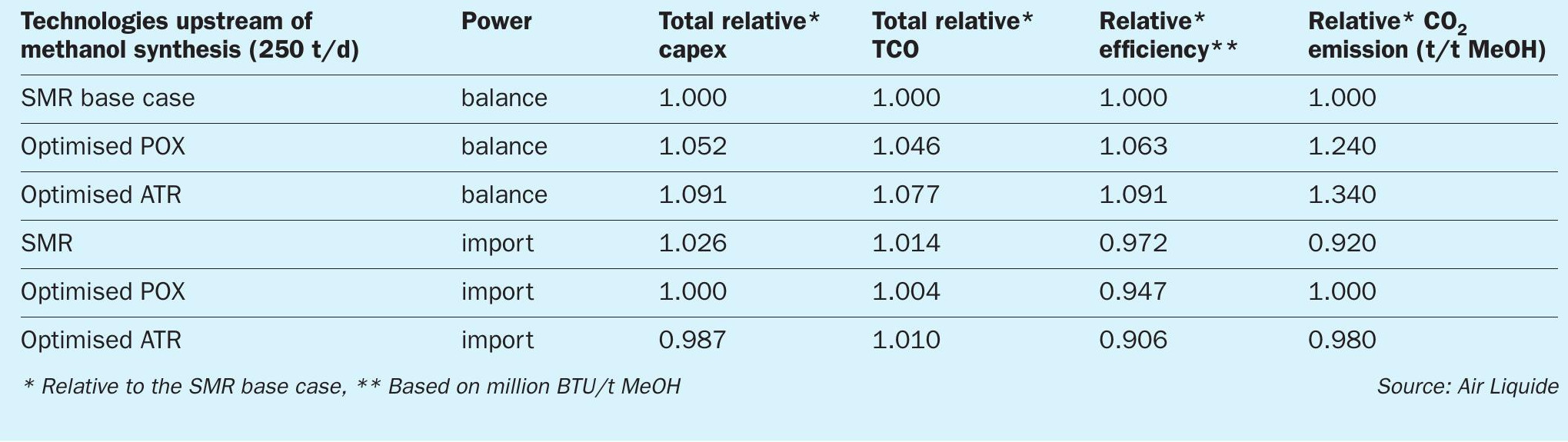
Power import cases
With power import possible, both POX and ATR designs could be competitive with the SMR on the basis of both TCO and CO 2 emissions as can be observed in the lower portion of Table 1. This is at least partly attributed to the more aggressive reactor and catalyst conditions. Developments on a brownfield site would strongly benefit from existing utilities that can be easily expanded, such as cooling water, oxygen supply, low carbon hydrogen supply or demand for co-product CO, all of which would tip the balance in favour of POX and ATR solutions.
The best options to produce 250 t/d methanol at low TCO were generally quite similar in cost, process efficiency and CO 2 emissions. However, they rely on different methanol reactor inlet gas compositions; many of which were quite aggressive and below what has been commercially proven. This is why an extensive test campaign of more than 2000 hours on stream in the pilot plant at Air Liquide R&D – Innovation Campus Frankfurt (ICF) was performed under different conditions, sometimes far from conventional operation, to better understand the limitations of some of the possible solutions proposed during the study.
Results of experimental test campaign
Like all methanol synthesis units for syngas from conventional feedstocks, the pilot plant at Innovation Campus Frankfurt is equipped with a tubular water-cooled reactor and a recycle for unconverted syngas (see Fig. 9). The reactor tube of the pilot unit has dimensions comparable to commercial plants. Scale-up from the pilot unit to any commercial size unit is performed by multiplying the number of reactor tubes with the ratio of the respective production capacities.
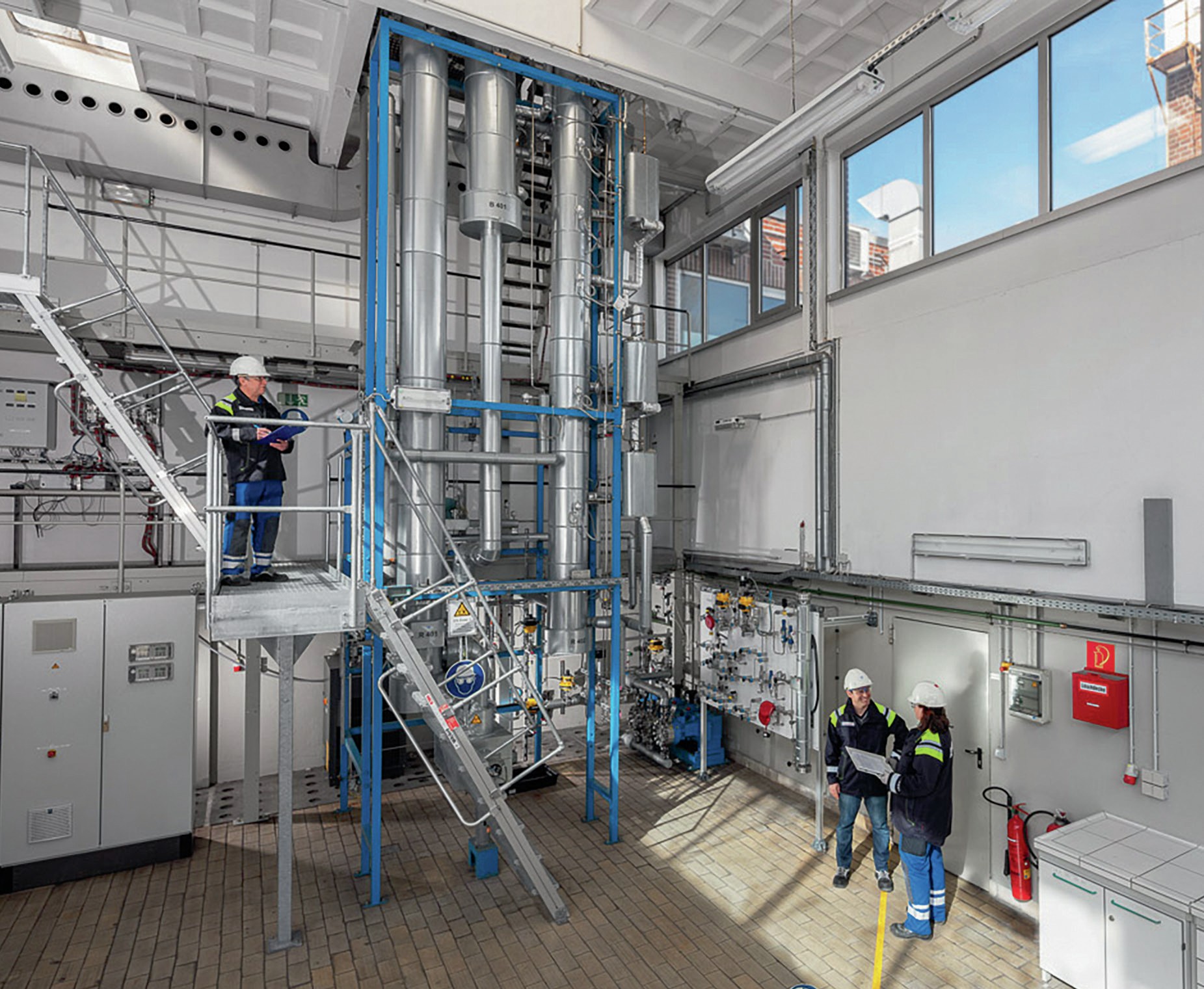
Some results of the test campaign are given in Table 2. Experiments with several different operating conditions and gas compositions were performed. Therefore, the amount of by-products produced with more aggressive conditions has been carefully analysed and quantified, especially for lower SNs at the methanol reactor inlet. Hence, this test campaign was completed in order to define the boundaries of possible operations for conditions that are not usual for methanol synthesis.
A critical variable is the SN = (H 2 -CO 2 )/ (CO + CO 2 ) in vol-% at the inlet of the reactor. An SN of 2 represents enough hydrogen for all carbon-containing molecules to react to methanol. Typically, the SN focus is on the make-up syngas to the synthesis loop. While the SN of the make-up and reactor inlet are not completely unrelated, these studies have shown that it is more important to focus on the SN at the reactor inlet 11 :
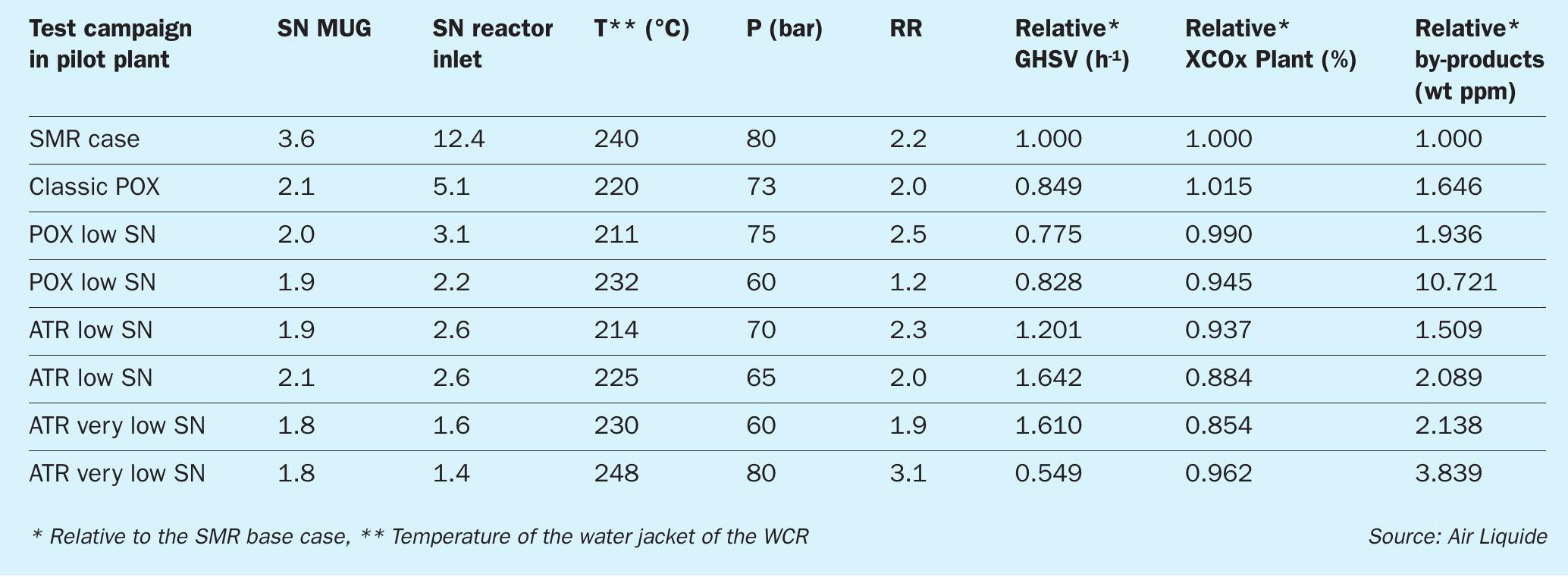
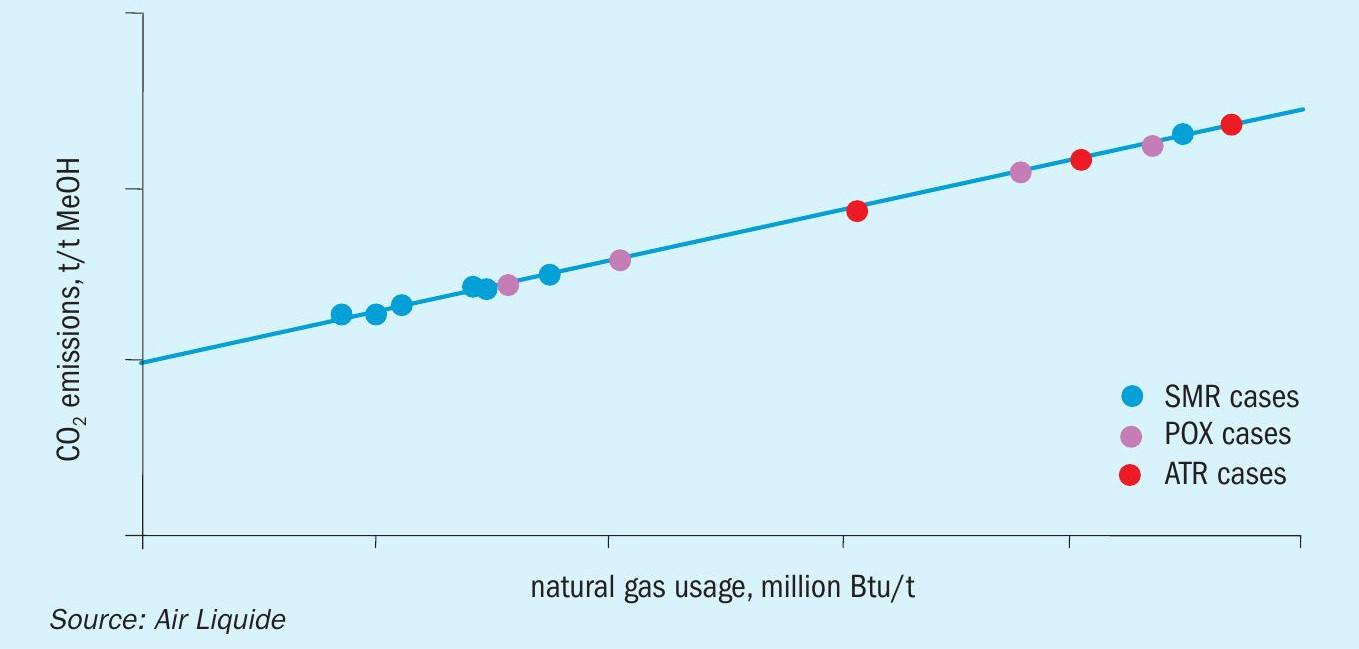
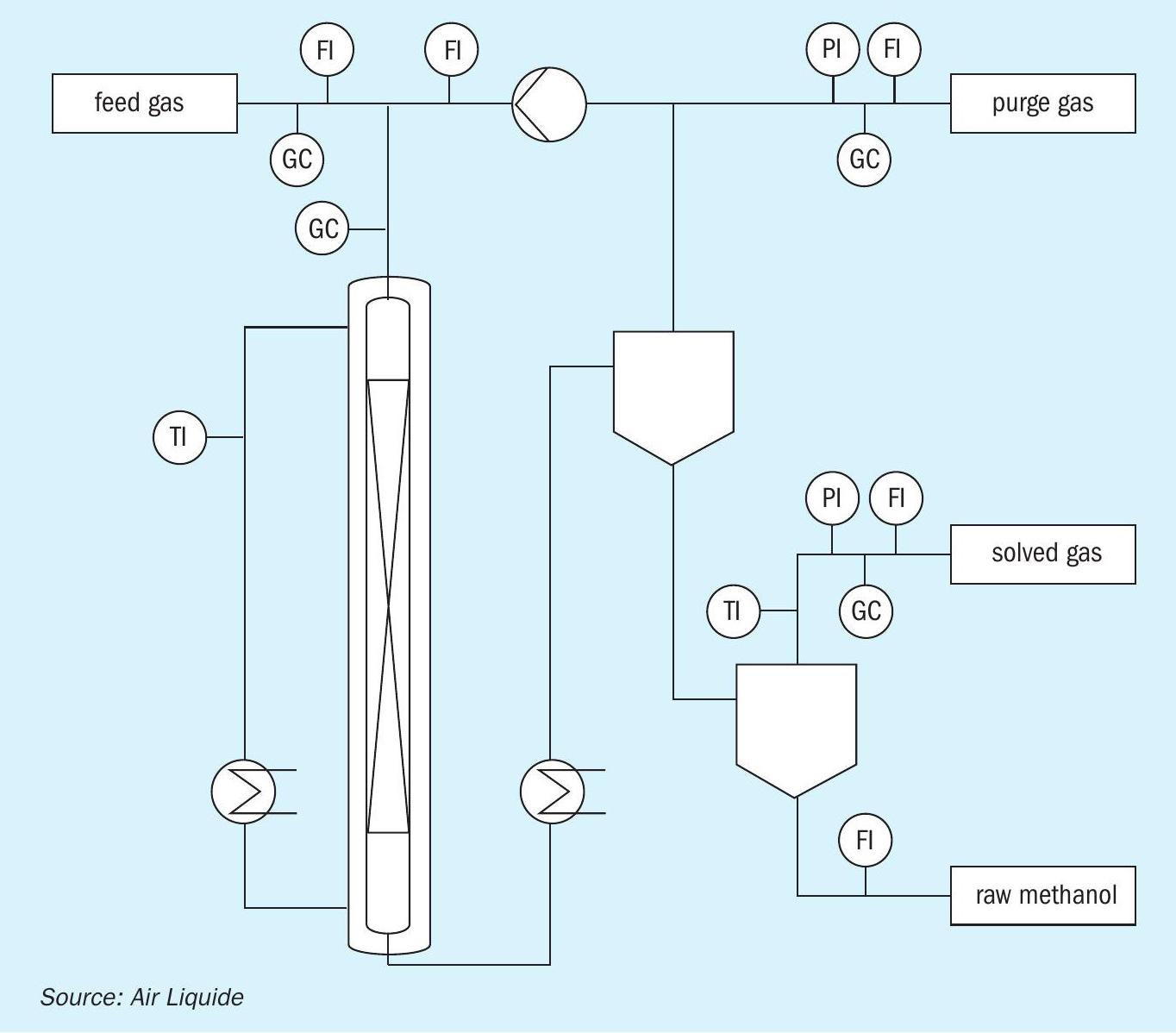
- SN is not an issue for SMR as there is excess H 2 ;
- commercially) proven conditions when SN > 3.
- low SN conditions when SN < 3.
- very low SN conditions when SN = 1.6 – 1.8.
As can be observed in Table 2, the amount of by-products produced during the methanol synthesis is very sensitive to operating conditions and gas compositions. It is crucial to manage the amount of the different by-products present in the crude methanol with adequate and feasible conditions in order to allow a proper distillation to obtain a Grade AA methanol product at the end of the process.
Discussion
Firstly, any of the three technologies can be the basis for technically viable options. The most important distinction for the technical options is the power balance. The SMR as studied is naturally power balanced and shows no particular advantage for power import. Steam produced in the waste heat boiler and burning of off gas streams provides enough steam for power production to run the plant. As will be described, the POX and ATR cases are greatly improved when shifting from power balance to power import cases.
A long-established and intuitive result was that CO 2 emissions are linearly related to overall natural gas usage (feed + fuel) for all power balanced cases, independent of the technology. It can be seen in Fig. 10 that a range of SMR, ATR and POX cases were checked, all landing on the same trend line. Power balance is best suited for the remote gas case. Among these the SMR gave the lowest specific usage and emissions. The most economic case (lowest TCO) did not correspond to the lowest emissions. Thus, the trade-off between capex and opex at small capacities favours capex reduction over feedstock minimisation. The opposite is typically true at 5,000 t/d scale.
The favourable SMR results under power balanced conditions can be understood as the power requirements of the air separation unit in POX and ATR cases drive on-site utility demand and require additional investment and gas usage for on-site power production.
The SMR case not only shows better TCO figures than ATR and POX, but the CO 2 emissions are also significantly lower than for the oxidative processes. This can be observed for several SMR cases with different options as shown in Fig. 10 in comparison to ATR and POX for power balanced scenarios.
All three syngas technologies can be made to work in a competitive fashion – economically and environmentally. The SMR is likely best suited to remote, standalone operation. The oxygen-based POX and ATR solutions compete better on a developed site with local methanol demand and import power 12-13 . As is usually the case, the optimal solution depends on specific local conditions. If the complete avoidance of CO 2 emissions is the main target for a small-scale methanol plant, access to a low carbon hydrogen and energy supply enables utilisation of CO 2 captured from other processes for direct conversion into methanol.
Dedicated CO 2 capture was excluded from this analysis. However, based upon the higher portion of CO 2 that is produced at pressure within the syngas process for POX and ATR, these processes would also be favoured versus SMR which has a higher portion of the CO 2 in low pressure flue gas.
Materials and methods Experimental setup
The test points were performed in the pilot plant at Innovation Campus Frankfurt. This pilot plant incorporates gas recycling and online analytics to follow conversion and selectivity over time. A scheme of the methanol synthesis pilot plant setup is shown in Fig. 11. For the syngas fed to the pilot plant, the term feed gas and/or makeup gas (MUG) is also used. The syngas is mixed from cylinder gases in technical quality in a mixing station. Therefore, the syngas is free of sulphur and ammonia.
The essential data for a complete process characterisation are the temperature profiles, pressure profiles, mass flows, gas compositions (feed gas or make-upgas, reactor inlet, reactor outlet, purge gas and solved gas) as well as the composition of raw methanol after the water-cooled reactor (WCR).
The tube dimension of the WCR is comparable to the commercial scale WCR. In the tube centre, an additional tube is placed for measurement of the temperature profile. A catalytic bed of five metres has been filled into the WCR with a commercial methanol catalyst delivered by Clariant.
Using the composition and flow data, complete material balances are established for all C, H, O and N components, thereby establishing catalyst parameters such as conversion and selectivity.
Gas composition used in the test campaign
Table 3 provides the gas compositions of the different feedstock used to generate the data available in Table 2.
Conclusions
Air Liquide is able to perform such an in-depth analysis since it owns all the syngas technology.
The SMR front end provides commercially referenced conditions and is conveniently in power balance. Moreover, SMR generally allows the lowest CO 2 emissions of all cases. The amount of by-products present in the crude methanol is also very low with a feedstock for the methanol synthesis coming from a SMR unit.
Nevertheless, ATR as an alternative offer can be suitable for specific cases especially if oxygen is available. Therefore, some ATR cases show lowest capex (also lowest TCO) of commercially referenced synthesis conditions. For the reason, the trade-off between lower capex and higher opex has to be studied carefully for each location.
Some POX cases under high-CO/low SN conditions for the methanol synthesis allow the cheapest TCO. Nevertheless, these synthesis conditions are too extreme for conventional operating parameters but could be the focus for future lab tests and catalyst developments.
On request, this study can also be performed with additional boundaries including abatement of CO 2 , considering individual geographical constraints.
References
Acknowledgments
The authors want to acknowledge Clariant as a catalyst supplier and a long-time partner for providing the commercial catalyst used in the test campaigns at Air Liquide R&D.
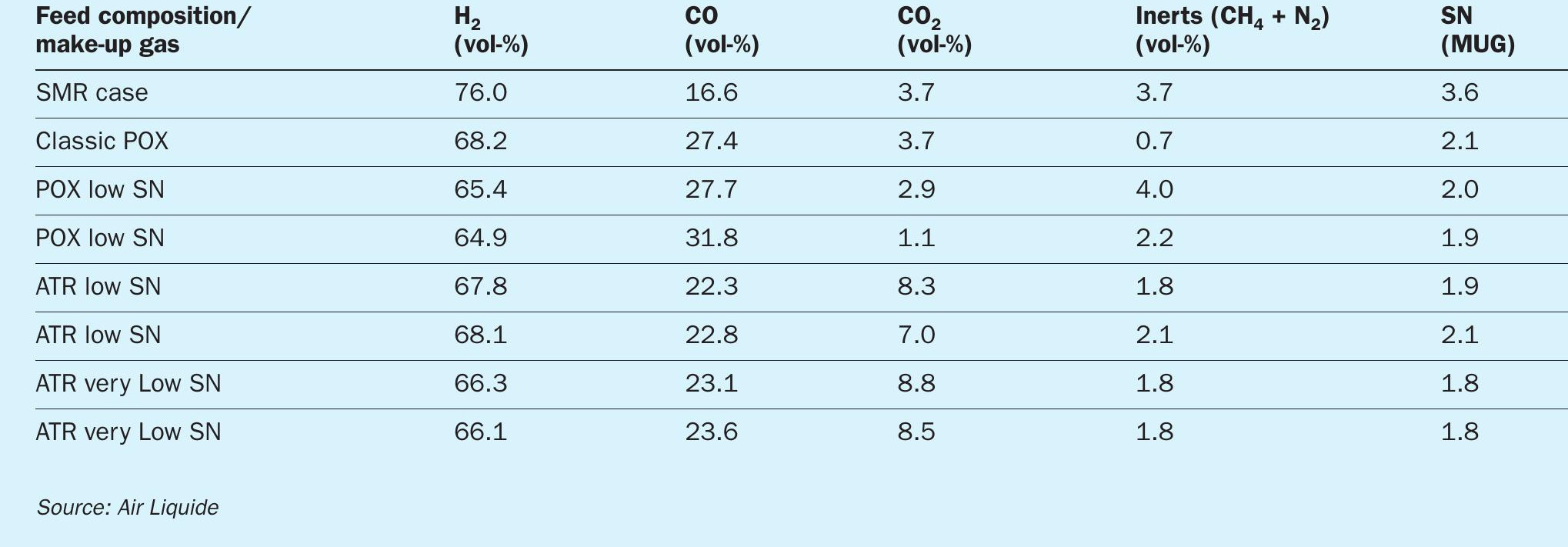