Fertilizer International 512 Jan-Feb 2023
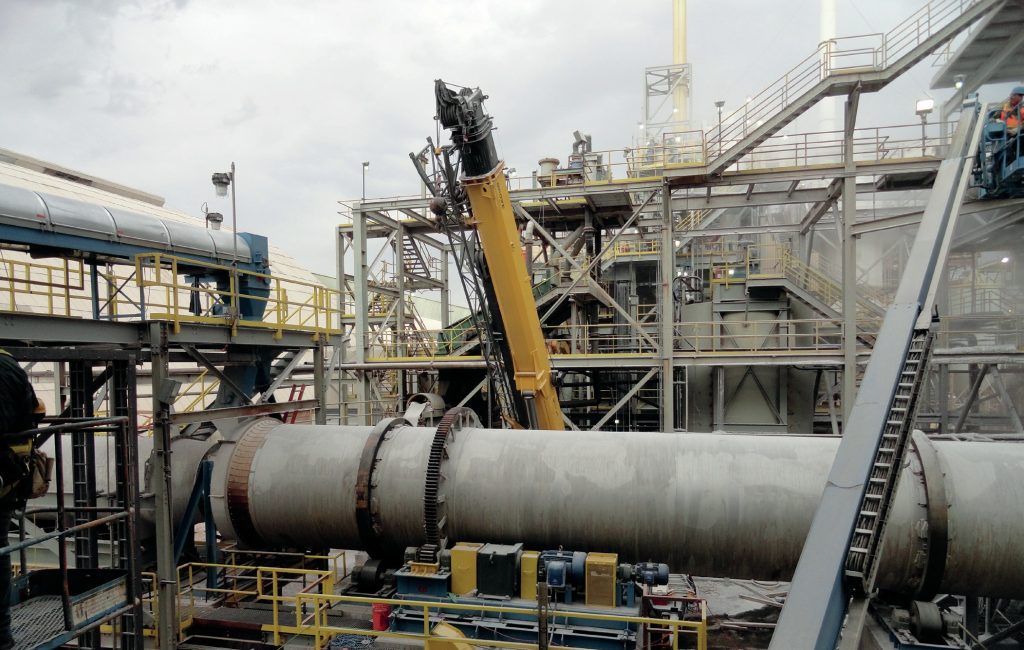
31 January 2023
Phosphate process improvements
PHOSPHATE EQUIPMENT & TECHNOLOGY
Phosphate process improvements
Advances in technology, equipment and reagents are enhancing phosphate fertilizer production. Optimisation of standard equipment is also vital for ensuring process efficiency.
FEECO INTERNATIONAL
Rotary dryers for phosphates
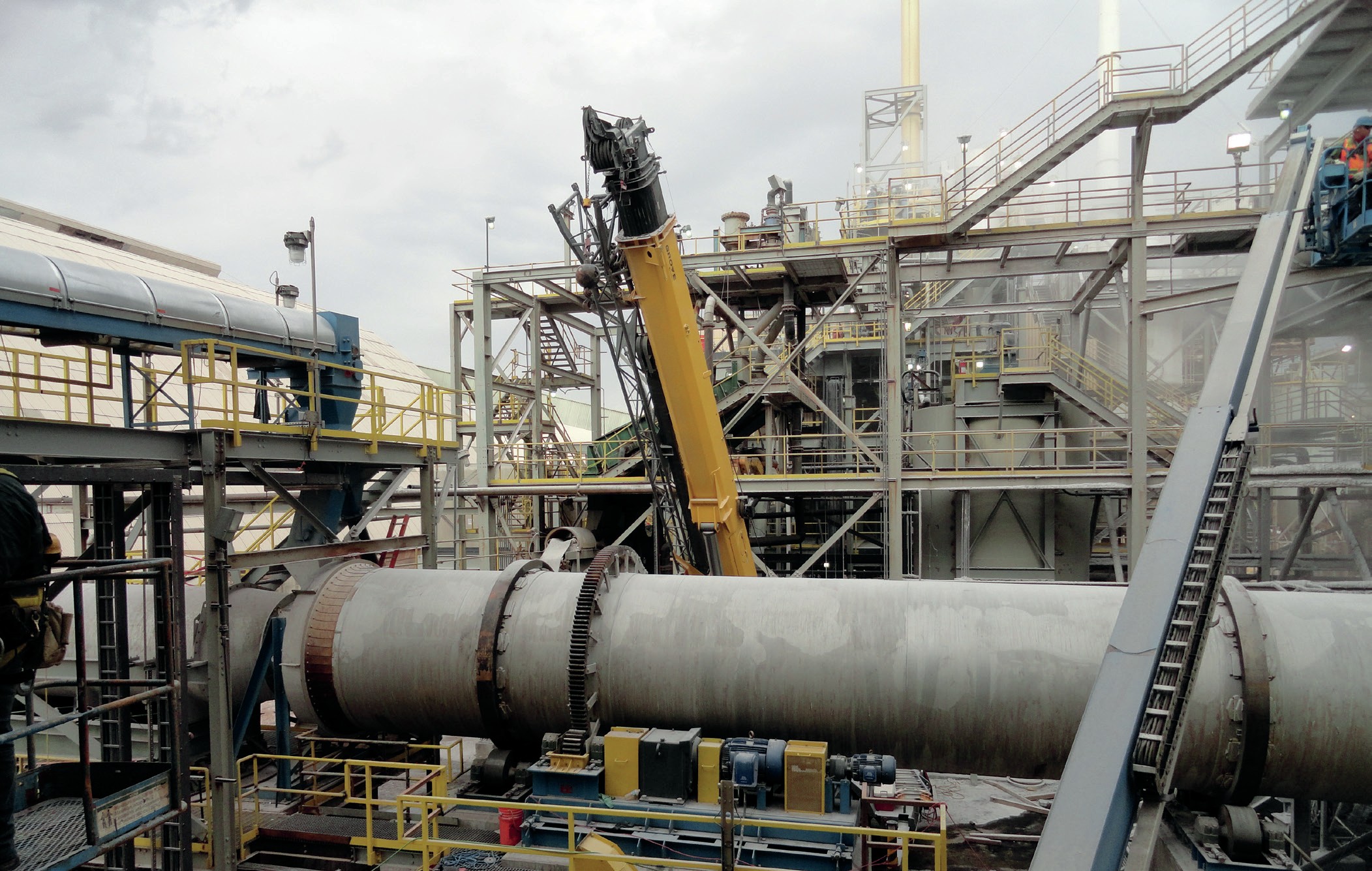
Rotary dryers have long been the standard option for drying bulk solids in industrial settings, whether at mine sites or production facilities. This certainly holds true when it comes to the phosphates industry. Miners rely on rotary dryers for drying phosphate rock, while fertilizer producers rely on them for finishing granular fertilizer products for market.
In this article, we outline how rotary dryers function, show why they are the equipment of choice for phosphate fertilizer producers, and describe individual phosphate industry applications. Unique considerations for plant managers when drying phosphate materials are also highlighted.
Phosphate rock applications
Rotary dryers are commonly found at phosphate mine sites where washing is used in ore beneficiation as this necessitates a drying step. In this application, drying is advantageous as it:
- Improves shipping economics
- Enhances handling and flowability
- Reduces the potential clogging of downstream equipment.
Rotary dryers are ideal for processing phosphate rock, thanks to their high throughput – more than 200 tonnes per hour – and durable design. They are also favoured for their tolerance to feedstock variations, which commonly occur at phosphate mining sites.
Finished phosphate applications
Rotary dryers frequently play a critical role in fertilizer finishing plants, particularly in wet granulation where a drying step is necessary to bring the final product to its target moisture content. In this application, drying is essential for meeting shipping, storage, and shelf life specifications.
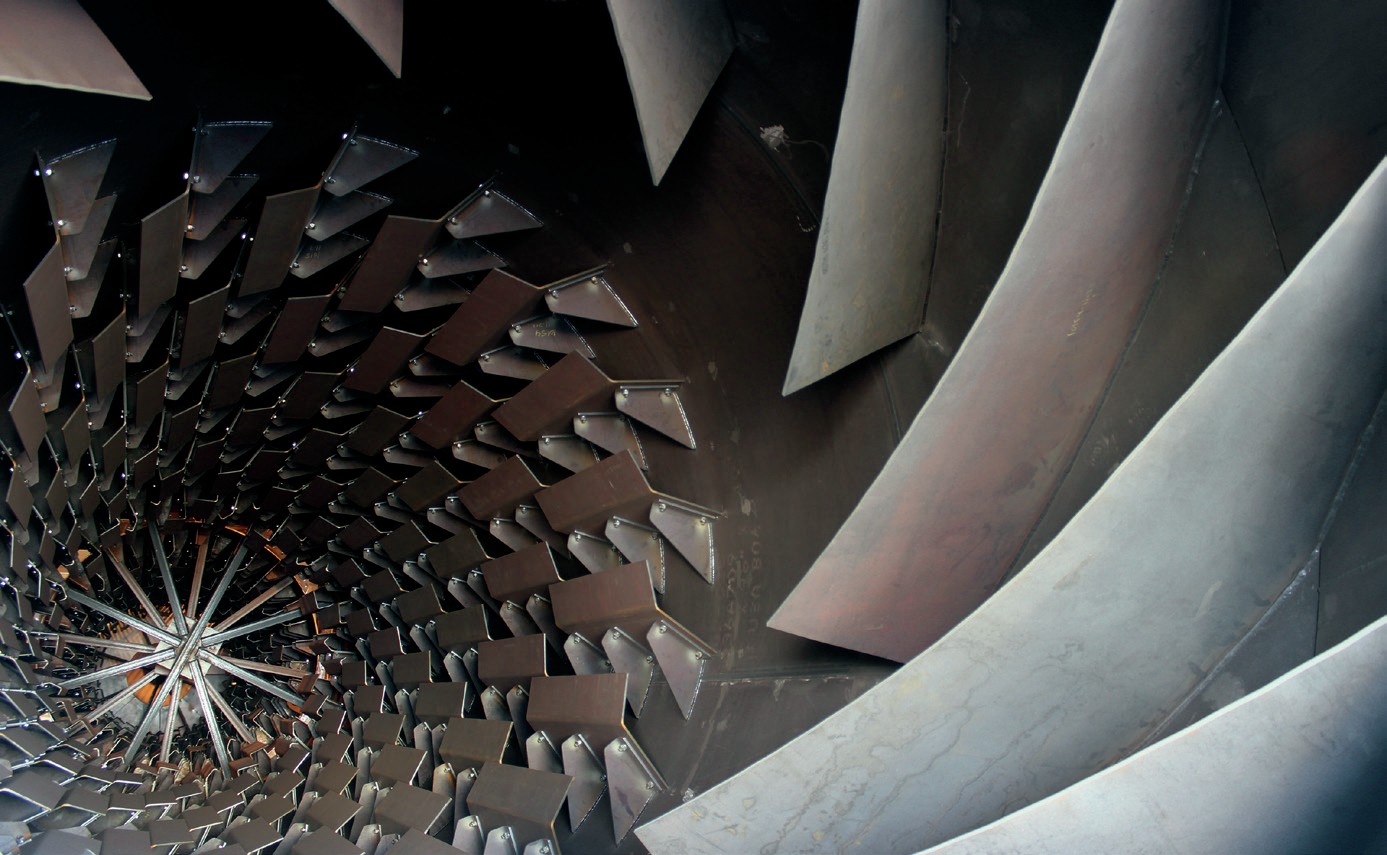
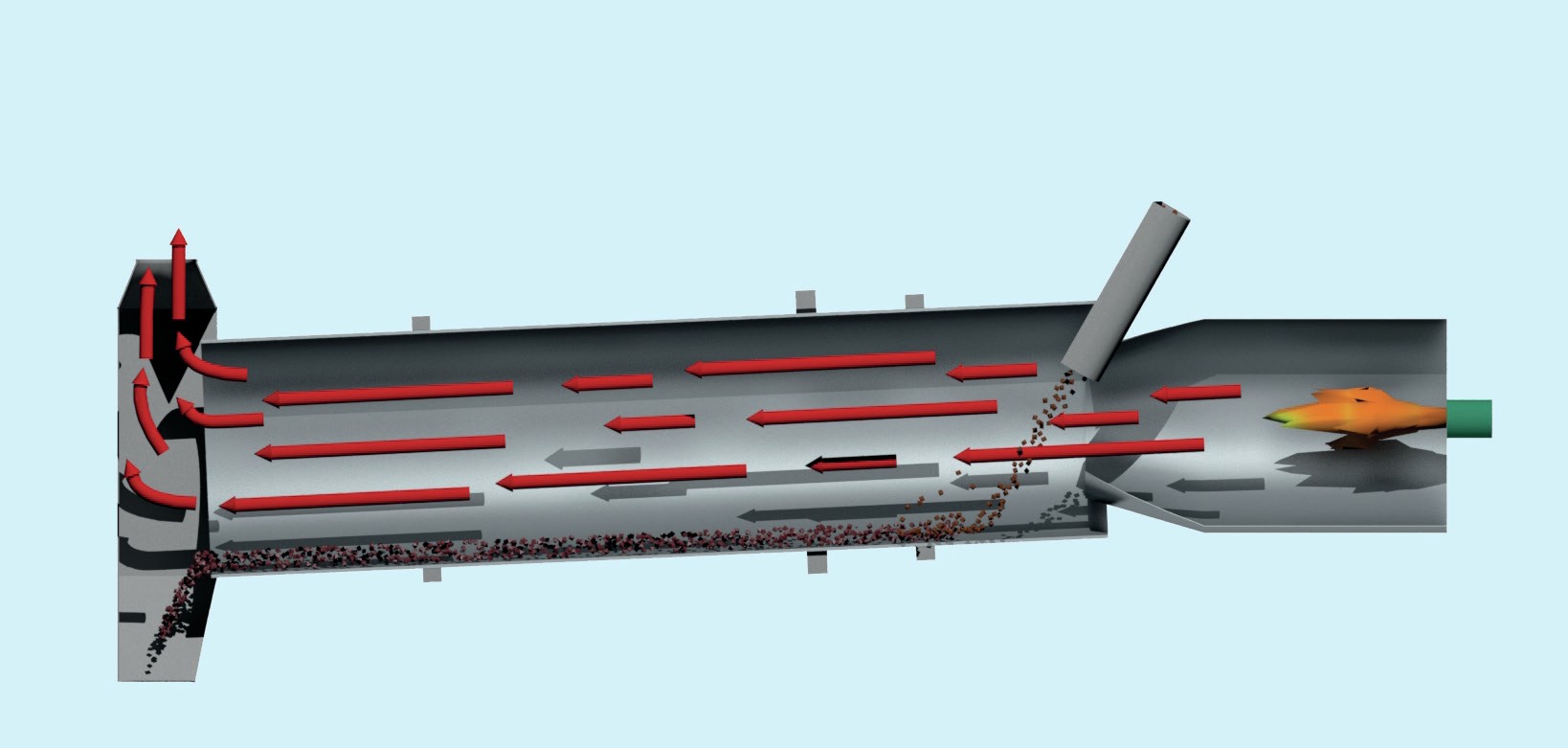
As with phosphate rock processing, rotary dryers are often favoured in granulation processes because of their high throughput and durability. They also offer additional benefits during product granulation – as the tumbling action of rotating drums helps to polish granules, rounding and refining them into a premium end-product.
Operating principles
Rotary dryers which extract moisture via convection are typically employed in phosphates processing. In these direct dryers, material passing through a rotating drum comes into direct contact with hot air and combustion products. (While indirect rotary dryers are also available – configured so that the heating medium and materials are kept separate – these are not generally used by phosphate producers.)
Flights pick up the material and drop it through a stream of hot air as the drum rotates (see photo). This creates a cascading curtain of material in the drum’s cross section. (It is for this reason that rotary dryers are sometimes referred to as cascade dryers). The ideal curtain maximises heat transfer by matching the flight design and pattern to the material’s specific characteristics.
The phosphates industry typically uses rotary dryers with a co-current design. This means that the material and combustion products flow through the unit in the same direction (Figure 1).
This configuration is used at both phosphate mine sites and phosphate granulation plants. At the mine, a co-current configuration helps to ‘flash off’ surface moisture and dry rock particles to their core as they move through the drum. At the granulation plant, a co-current configuration avoids the overheating of products when they reach their driest point and helps prevent product attrition, degradation and the generation of fines.
Predetermined air flow velocity, retention time, and temperature profiles all ensure that phosphate materials are dried according to specification.
In both ore processing and granulation plant applications, phosphate producers frequently incorporate a combustion chamber at the inlet end of the dryer. By stopping the burner flame from coming into direct contact with the material being dried, this helps prevent product degradation, discolouration, and attrition.
Phosphate materials can cause issues during drying due to several challenging characteristics. The following qualities must therefore be considered when working with phosphates:
Corrosion
Because of the incorporation of phosphoric acid, corrosion can be a concern when drying phosphate fertilizers. This is particularly true at the inlet of the dryer where the moisture content is high. Phosphate fertilizers are all corrosive to some extent, although the exact level of corrosion will vary depending on their composition.
When selecting drying equipment, phosphate producers should work with an experienced rotary dryer manufacturer to prevent corrosion. Constructing the dryer using corrosion-resistant alloys and reinforcing high-wear areas are both recommended.
Additionally, welds should be ground smooth in fabrication to eliminate potential catch points where material could begin to collect and corrode the unit. Internal flights should also be full welded on both sides to deter corrosion.
In existing units that are already operational, plant managers can also opt to replace or reinforce key sections with more corrosion-resistant alloys.
Abrasion
Abrasion can also be a concern during phosphate rock processing and phosphate fertilizer granulation. Particle size and impurities in process materials can increase abrasion potential in the dryer. Reinforcing high-wear areas with abrasion-resistant steels can therefore help to minimise wear.
Clumping & build-up
Phosphate materials are also prone to clumping and build-up – tendencies that can cause a range of problems for both product quality and consistency, as well as dryer longevity. Fortunately, producers have the following options available for minimising build-up:
- Most often, producers incorporate some type of knocking system on the drum (see pneumatic hammer photo).
This knocks the drum on a wear band to dislodge any potential build-up on the drum’s interior as it rotates. Various knocker designs are available.
- A screw conveyor may also be employed at the inlet. This projects or ‘flings’ material into the unit, causing clumps to break apart as they enter the dryer.
- Materials of construction, such as stainless steel with a 2B finish, can also help to prevent build-up.
- On the discharge end, a circular trommel screen or ‘grizzly’ (see photo) can break up any clumps that may have formed (or not broken up) during the drying process, while also aiding size separation.
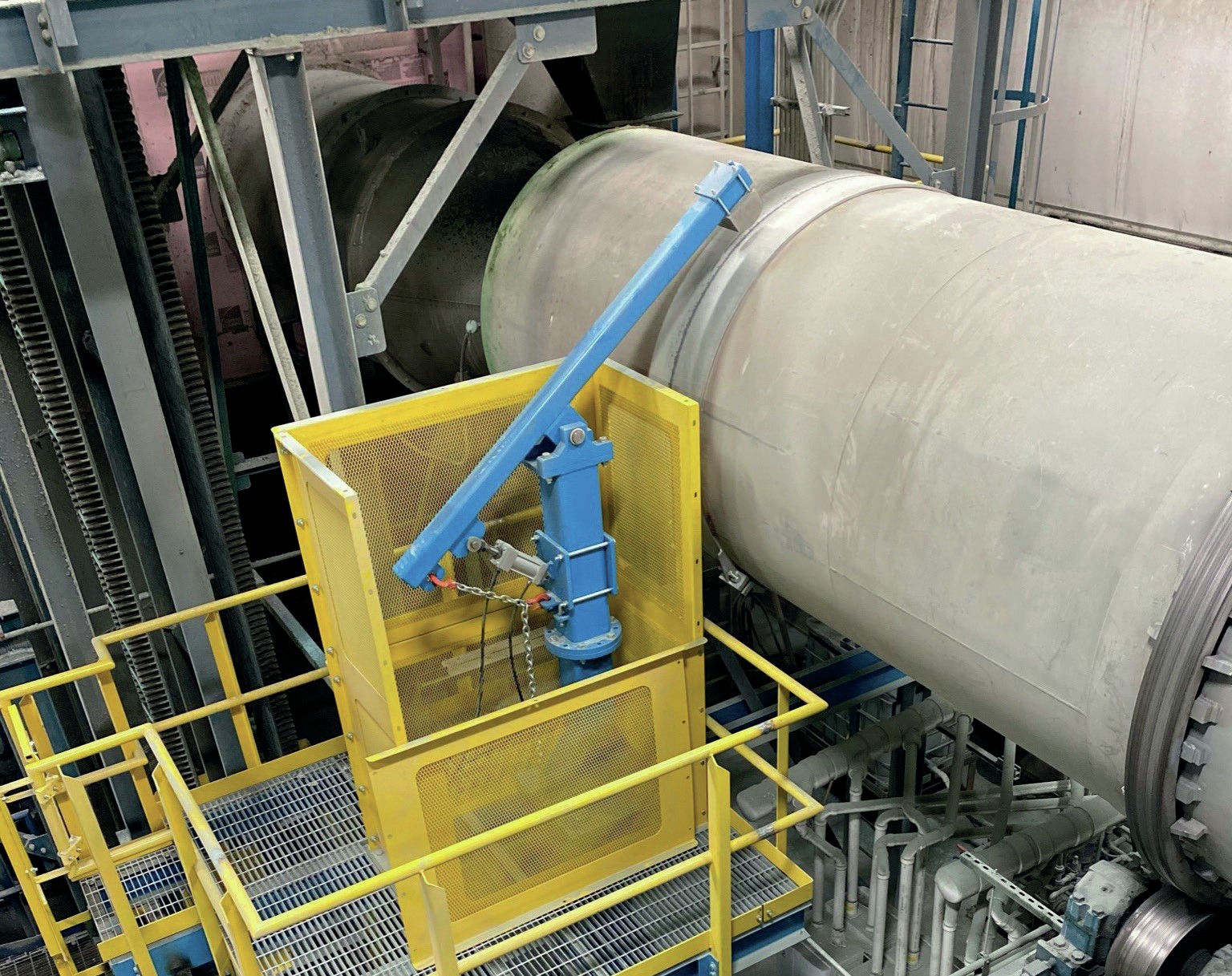
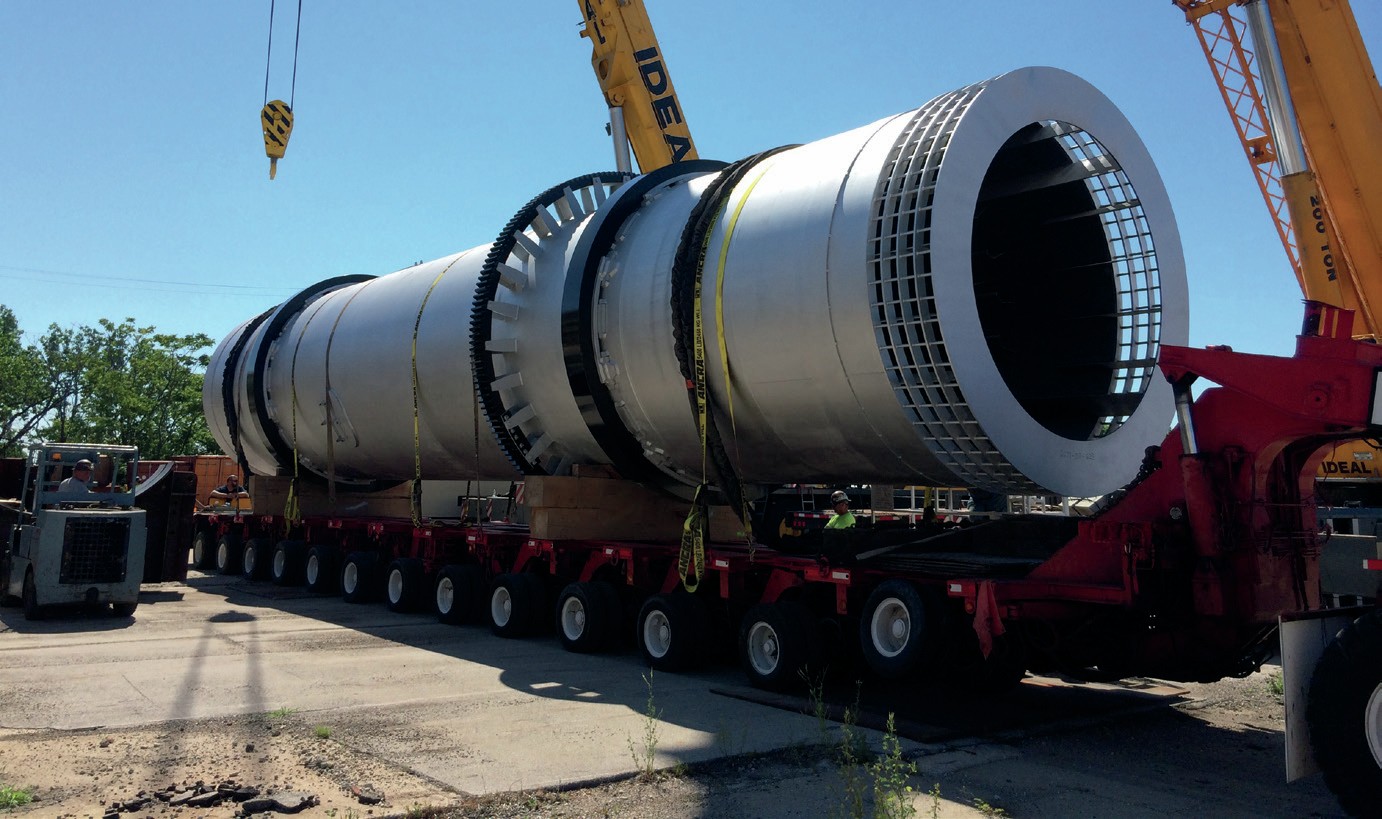
Dust
Excessive dust can be a problem during phosphate processing – primarily at the mine site – if the dryer is not designed properly. A cyclone can be added to deal with excess dust. This is installed prior to the baghouse or scrubber to capture the dust and return it to the process.
Feedstock variation
Although less of a concern during fertilizer granulation, feedstock variation can be a real issue for phosphate rock processing as physical properties and chemical composition can vary considerably. This makes familiarity with the specific characteristics of the individual phosphate rock source essential prior to processing.
Testing at a facility such as FEECO’s Innovation Center may therefore be necessary to evaluate the material and establish key operating parameters. Results can then be used to establish a suitable and robust design for a commercial-scale dryer.
Inspections
The challenging characteristics of phosphate materials, along with their potential to cause damage, make regular inspections especially important for rotary dryers operating in the phosphate industry.
As well as ensuring operators and maintenance personnel are properly trained in dryer operation and maintenance, phosphate plant managers should also mandate routine external and internal inspection of their unit(s). This allows problems to be caught early before they have a chance to escalate into more serious damage.
FEECO also recommends having the dryer more thoroughly inspected on an annual basis by the original equipment manufacturer (OEM) or a third-party service provider. Catching and addressing potential issues at their onset can help to avoid unnecessary downtime and extra maintenance costs in the future.
Concluding remarks
Rotary dryers offer an effective and reliable solution at phosphate mine sites and phosphate fertilizer plants – being suitable for drying both phosphate rock and/ or finished phosphate products. Their high throughput, longevity, tolerance to variation, and ability to polish granules have made them a favoured and reliable option for drying phosphates.
Nevertheless, phosphate-based materials do present unique challenges. Thoughtful design is therefore required to maximise dryer service life and ensure high product quality and consistency. Regular inspection and maintenance are also essential in keeping these dryers running at their best for years to come.
Dicalcium phosphate: the versatile phosphorus source
Marc Sonveaux, HCl-based processes technology lead
Dicalcium phosphate offers a highly versatile source of phosphorus for animal feed and phosphate fertilizer production. In this article, Prayon outlines how DCP production can benefit product purity, increase resource availability and improve phosphate supply chains.
Why DCP?
Dicalcium phosphate (DCP) – in either its dihydrate or anhydrous form – is valued as a concentrated phosphorus source. DCP can be derived directly from phosphate rock or obtained by digesting phosphate rock (with hydrochloric acid or sulphuric acid) and then neutralising the solution generated (with calcium carbonate or calcium hydroxide). Prayon has developed and industrialised the acid digestion route to deliver two commercial processes:
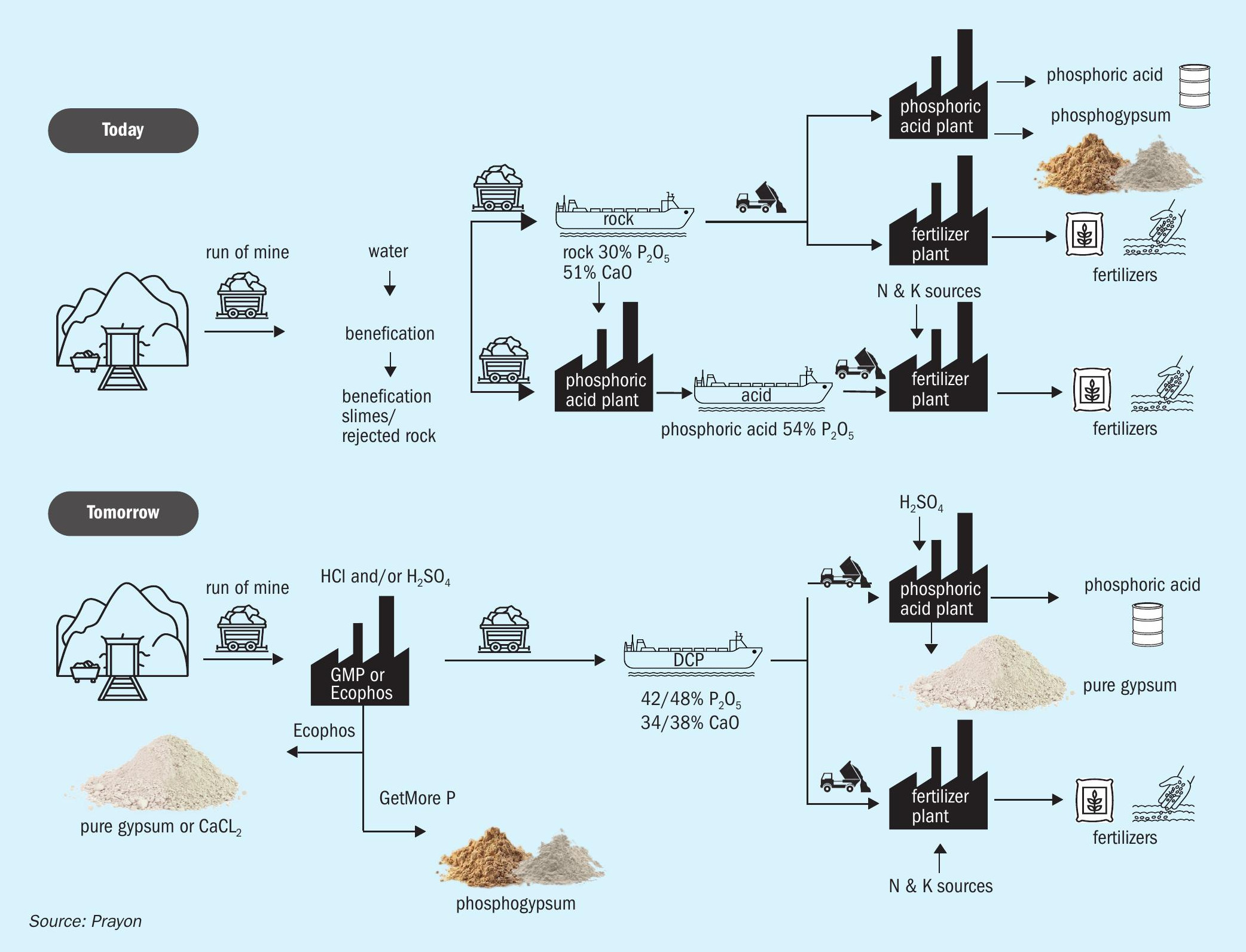
- The HCl-based Ecophos process
- The H2 SO4 -based GetMoreP process.
Both processes can cope with different phosphate rock quality and can consume low- to high-grade rock types.
DCP is inherently versatile. As well as being a pure final product, DCP can be used as a concentrated intermediate to manufacture a range of different phosphates, as described in this article.
Imagining a new supply chain
Today, high quality phosphate rock mined at a limited number of global locations is used to produce phosphoric acid, fertilizers, and other derivative products. The phosphate rock extracted from these mines is typically beneficiated to concentrate phosphate and reduce impurities. However, beneficiation is expensive, consumes significant water and energy, and results in P2 O5 losses by generating rejects such as tailings and slimes.
The beneficiated phosphate rock concentrates obtained are dried and then transported from mine sites to phosphoric acid or fertilizer plants (often located close to a port) or traded commercially. Massive quantities of phosphate rock concentrate, usually containing 30-33 percent P2 O5 , are exported to manufacturing plants all around the world. Liquid phosphoric acid, generated by plants located close to mining sites at a concentration of 52-54 percent P2 O5 , is also traded commercially. But shipping this acid across oceans is expensive and can be environmentally risky.
Replacing current large-scale transportation of phosphate rock or phosphoric acid with DCP is one alternative – an option called the ‘super rock’ approach. DCP is attractive as it can produced either directly from runof-mine phosphate rock or through limited chemical beneficiation. The DCP obtained is suitable for transport to different factories worldwide. It can also be transformed into fertilizers or higher quality phosphoric acid using existing or new production plants.
The DCP ‘super rock’ approach simplifies the supply chain (Figure 1) as it avoids the transport or phosphoric acid or the large amounts of unwanted and undesirable components (such as clays, sand, calcium fluoride, organic matter etc.) that are usually present in phosphate rock. Last but not least, the DCP produced by Prayon’s two processes is a higher quality product that is free from the heavy metals (including cadmium) and radioactive elements that are present in the original phosphate rock.
Two processes, one product
As previously indicated, Prayon offers two process technologies for DCP production:
- The Ecophos process – based on hydrochloric acid (HCl)
- The GetMoreP (GMP) process – based on sulphuric acid (H2 SO4 ).
Both technologies are built around the same concept, i.e., the partial digestion of phosphate rock that avoids dissolving most of the impurities. In both instances, the phosphate solution obtained, after filtration to remove residual insoluble materials, is neutralised using lime or limestone to produce DCP. In the final process step, solid DCP is separated from the mother solution by filtration and then dried (Figure 2). The DCP obtained can ultimately be granulated if necessary.
In the Ecophos process, the residue left after the digestion of the rock (this containing undigested impurities) is neutralised. These residues can be stored or converted into single superphosphate (SSP) in certain projects. A mother liquor of calcium chloride remains after the filtration of DCP. This can be dried or reacted with sulphuric acid. The latter converts the calcium chloride back to hydrochloric acid and generates an extremely pure gypsum by-product. This is free from radioactivity and suitable for use in the plaster and cement industry.
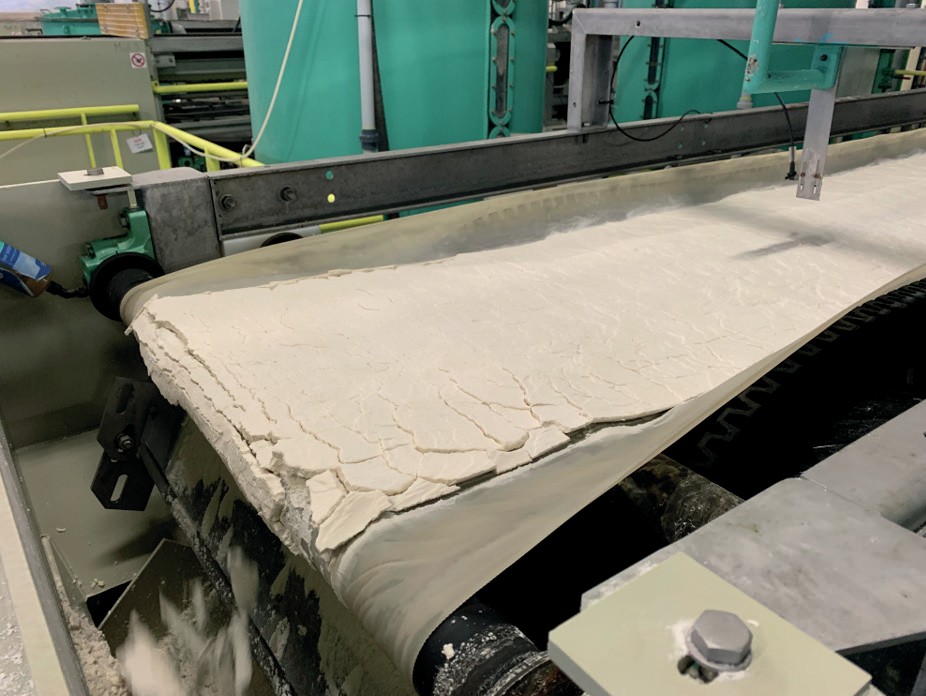
The Ecophos process is normally selected when:
- Hydrochloric acid is available
- The phosphate rock contains high levels of magnesium
- The generation and storage of phosphogypsum is an issue.
The Ecophos process also generates the highest quality DCP suitable for animal feed applications.
In the GMP process, the phosphogypsum by-product left after digestion is potentially suitable for agronomic use. The mother liquor obtained is water. This can be returned to the process after an optional treatment step. The GMP process is normally selected when sulphuric acid is available and where there is storage space or a market for the phosphogypsum generated.
Is DCP production economic?
The key aspect of this new phosphate industry supply chain philosophy (Fig. 1) is the ability to produce DCP at the lowest possible cost.
There are six main operational principles for keeping DCP production costs low:
1. Use low-grade phosphate rock: Low-grade rock is much cheaper and widely available worldwide Typically, a run-ofmine grade of 10% P2 O5 and above is suitable for both the Ecophos or GMP processes. The presence of high levels of impurities (e.g., magnesium, iron, aluminium, silicates, fluoride etc.) is generally not an issue.
2. Avoid beneficiation: The Ecophos and GMP processes both provide chemical beneficiation. Therefore, in most cases, DCP can be produced without the need for additional beneficiation. This boosts P2 O5 recovery and avoids the need for large-scale investment in a beneficiation plant. Prayon’s DCP processes typically deliver a P2 O5 yield of 80-90 percent, compared to the 30-60 percent yield obtained using a conventional beneficiation approach. (Indeed, the waste generated by conventional beneficiation plants can sometimes be used as a raw material for DCP production.)
3. Use secondary acid sources (spent acids): These can be found at low cost in some locations. Sulphuric acid can be sourced as a smelter by product, while hydrochloric acid is generated as a co-product from the manufacture of potassium sulphate (SOP), caustic soda and polymers.
4. Flexibility: Each phosphate rock is compositionally different. It is therefore possible to adapt the DCP production process to match the phosphate rock source with the end-product. Project capex and opex can then be optimised by selecting the correct process or combination of processes.
5. Capacity impact: the use of a large DCP unit as a hub for downstream production processes helps optimise the overall capex of the phosphate production plant.
6. Location selection: The DCP plant can be located at either the phosphate mine or the shipping port. Co-location at the mine allows storage of the gypsum generated by the process (GMP) or the remaining part of the rock (Ecophos). Location at the port, meanwhile, helps reduce logistics costs.
In addition, DCP has valuable technical characteristics compared to phosphate rock (e.g., its purity and P2 O5 concentration) that can justify a price premium relative to phosphate rock.
A wide range of end products can be derived using DCP as an intermediate (Figure 3), for example:
- Animal feed DCP. This is characterised by its high purity with less than 5 ppm heavy metals, less than 0.2 percent fluoride and high phosphate concentration (up to 42 percent P2 O5 ). DCP also has the desired high biodigestibility when produced in dihydrate form.
- Monocalcium phosphate (MCP). This can be produced directly from DCP by mixing with phosphoric acid – enabling 52 percent P2 O5 content to be reached. The product is then granulated and dried.
- Triple superphosphate (TSP). This is conventionally produced by mixing phosphate rock and phosphoric acid followed by granulation and maturation. Using DCP as a phosphate source instead enables much purer TSP to be produced, with low cadmium, low radioactivity and low heavy metal content. This process also reduces industrial plant costs as no maturation step is needed. The sulphate content of TSP, which is produced in the same way as MCP, can be adjusted with sulphuric acid if required.
- NPK fertilizers. Various NPK grades can be produced from DCP by blending or chemical reaction with different raw materials (KCl, SOP, K2 CO3 , HNO3 , urea, nitrates etc.) The NPKs obtained will be highly pure, with low cadmium, low radioactivity and low heavy metal content. These can be granulated and acidified to ensure optimal phosphorus solubility in water.
- Purified phosphoric acid (PPA). This can be produced from DCP due to its lack of impurities. This is a simple way of purifying phosphoric acid to a technical- or food-grade standard.
Advantageously, DCP can also replace phosphate rock in phosphoric acid production (PAP). The major advantages include: l Lowers transport cost and potentially lowers steam consumption in PAP due to the higher P2 O5 of the DCP
- Generation of purer phosphoric acid with less impurities
- Less gypsum is produced and plant capacity increases because of the low calcium content of DCP
- Longer mine life thanks to the use of low-grade – and previously unexploitable – phosphate rock
- The pure gypsum by-product generated complies with plaster industry requirements
- The high purity of DCP simplifies the layout of the phosphoric acid plant and its maintenance programme
- The phosphoric acid produced from DCP is pure enough for downstream production of monoammonium phosphate (MAP) and other water-soluble fertilizers.
Circumstances that favour DCP use
There are plenty of industrial situations that favour the use of DCP. For example:
- DCP is suitable for companies wishing to produce clean phosphate fertilizers and who need to adjust phosphate solubility to suit the soil types of their farmers.
- Using DCP instead of phosphate rock is advantageous for phosphoric acid producers encountering environmental issues with phosphogypsum storage. The lower quantity of gypsum generated from DCP also increases production capacity at existing plants. The gypsum generated will be cleaner and therefore usable in the cement industry, agronomy and even for plaster in the construction market. The phosphoric acid obtained is also cleaner and less viscous.
- Companies using technologies that currently require the most expensive and highest quality phosphate rock can lower their costs by substituting DCP instead.
- Mining companies extracting highly impure phosphate rock, or facing decreasing ore quality and resource depletion, could blend its phosphate rock source with DCP to upgrade and standardise phosphate feed quality to the downstream phosphoric acid plant.
Conclusions
As high-grade phosphate rock resources become depleted, we will need to manufacture phosphate products – such as fertilizers and industrial, food and feed phosphates – using lower quality raw materials. Widely available low-grade phosphate rocks (and secondary phosphate sources) can be transformed into highly pure DCP using Prayon’s Ecophos or GetMoreP technologies. This ability to exploit lower quality rock has the potential to greatly expand exploitable phosphate resources globally.
The DCP generated by Ecophos or Get-MoreP processes can be used as a building block to produce many different types of phosphate products for animal feed, fertilizer, technical and food applications.
The construction of large capacity DCP plants close to existing phosphate mines could generate calcium phosphate in a highly pure and concentrated form suitable for export – before being converted into final products at its end destination.
DCP, being a solid product, offers important logistical advantages, as it is much easier to transport than phosphoric acid. It also has a much higher P2 O5 content than phosphate rock concentrate. Widespread introduction of DCP production capacity could therefore improve the industry’s sustainability – by creating a new phosphate supply chain that significantly reduces transport CO2 emissions.
In addition to the company’s well known and widely installed phosphoric acid production processes, Prayon Technologies can support the entire DCP plant concept. This includes projects to convert phosphate rock to DCP as well as projects that convert DCP into phosphoric acid and phosphate end-products.
A practical solution for reducing phosphoric acid impurities
Kevin Song
In recent years, with the continuing decline in ore grades, the proportion of various impurities present in phosphate rock has gradually increased – these including iron, magnesium, aluminium and acid insoluble substances. In the wet phosphoric process, almost all of these impurities enter solution. This means that the impurity content of phosphoric acid is also on the increase. This results in phosphoric acid with a relatively high minor element ratio (MER), thicker viscosity and containing more suspended solids. Unfortunately, when impurity levels are high, the utilisation value of phosphoric acid is correspondingly low.
Phosphoric acid production
During the concentration process, the impurities in phosphoric acid can cause blockages in the heat exchanger and increase scaling. This seriously affects the normal, continuous operation of the concentration unit due to the following undesirable consequences:
- The service life of the equipment is shortened
- The heat energy utilisation rate is reduced
- Steam consumption is increased
- The capacity of the concentration unit is sharply reduced.
As phosphoric acid becomes more concentrated, the solubility of impurities decreases and they precipitate out. The presence of impurities as dissolved metal ions also increases the viscosity of phosphoric acid, reduces settling rate and increases the clarification time. Other process problems associated with phosphoric acid impurities include large heat losses and a large increase in sludge discharge from the concentrated acid storage tank.
There are knock on effects too. Low-quality concentrated acid inevitably causes quality problems in the downstream production of phosphate products, and can even cause the shutdown of downstream processes. The presence of excess impurities within phosphoric acid also reduces the effective production capacity of the whole phosphates complex, increases production costs, and results in significant economic losses at phosphate production plants.
Downstream production
The presence of impurities in phosphoric acid has three main effects on the downstream production of phosphate fertilizers such as diammonium phosphate (DAP) and monoammonium phosphate (MAP).
Increases the viscosity of the ammoniated slurry. Ammonia can react with impurities in phosphoric acid (e.g., iron, magnesium and aluminium) to form various complex ammonium phosphate compounds. These have the following undesirable properties and behaviour:
- Raising the viscosity and specific gravity of ammonium phosphate slurry, negatively affecting its rheological properties
- Creates inconsistent local variations in ammonia content
- Causes production equipment blockages – and ultimately equipment failures that can result in shutdowns.
Lower DAP/MAP product quality. The presence of large amounts of iron, aluminium and magnesium in phosphoric acid reduce its pH value. This can lead to poor neutralisation if the quantity of liquid ammonia added is insufficient. This in turn can generate final products with lower-thanexpected nitrogen content. Furthermore, the ammonium phosphate salts generated (iron, aluminium and magnesium types) are insoluble and therefore reduce the available P2 O5 in the final product, especially water-soluble P2 O5 . This reduces the nutrients available for release by the fertilizer and typically results in poor quality products.
Undesirable colour and physical properties. The use of poor-quality phosphoric acid with high total impurity levels can alter the colour of the final phosphate product. It also generates irregular and poor strength product granules. The presence of magnesium phosphate salts (which are soluble in citric acid) also makes the final product prone to undesirable moisture absorption and caking.
Phosphoric acid impurities
Traditional flocculants and settling agents can only reduce impurities to certain levels and, consequently, the specification of weak/strong phosphoric acid may not satisfy downstream production requirements.
Wuhan Fertchem Technology Co., Ltd. has addressed this problem by modifying and optimising conventional flocculants and settling agents to produce a new and superior purifying agent (NPA100). This multifunctional phosphoric acid additive is designed to solve practical production problems to deliver the maximum benefit. It reacts well with dissolved impurities to allow their easy separation and removal. This reduces costs and improves the efficiency of subsequent purification steps.
NPA100 is an easy-to-handle liquid that contains chelating agents, settling agents, decolourants and surfactants. It functions by:
- Decreasing the surface tension and hence the viscosity of phosphoric acid l Chelating with calcium, magnesium, iron, aluminium and other dissolved metal ions
- Forming low solubility chelates in phosphoric acid that settle as non-phosphate metal precipitates
- Allowing suspended solids to settle and be adsorbed more easily by altering their surface electrostatic repulsion
- Acting as a flocculant that captures and sweeps away suspended solid impurities
- Having a decolourisation effect via redox reactions.
NPA100 delivers significant benefits for different strength phosphoric acids (2060% P2 O5 ). It has the ability to:
- Reduce minor element ratio (MER) and P2 O5 losses
- Improve settling rate by 50 percent
- Efficiently remove solids and dissolved metal ions
- Reduce phosphoric acid viscosity
- Deliver cleaner phosphoric acid with improved colour
- Improve the quality of downstream fertilizer end products
- Shorten the clarification time in the settling tank by 50 percent
- Increase the capacity of the phosphoric acid clarification unit
- Enable the utilisation of low quality phosphate ore.
Cutting the cost of phosphates processing
Jens-Michael Bergmann, TOMRA’s area sales manager for Europe, MENA and India
An array of four TOMRA sorting machines at the MWSPC mega project in Saudi Arabia.
The use of TOMRA sorting machines at a major new phosphate mining and processing operation is showing how phosphorus can be extracted from ore with greater environmental and economic efficiency.
Transforming phosphate rock into a high-quality and commercially-usable concentrate can be costly, logistically complex and technically-demanding. Fortunately, the introduction of innovative and pioneering sorting technology is now helping to improve the efficiency of phosphate fertilizer production.
Indeed, over the last two years, the installation of TOMRA sorting machines at a new large-scale phosphates mining and processing complex in Saudi Arabia has shown how it is possible to cut production costs – while at the same time turning traditionally discarded waste into usable phosphate.
The massive complex, located in the remote north of the Kingdom, is run by the Ma’aden Wa’ad al Shamal Phosphate Company (MWSPC), an $8 billion joint venture between Saudi mining giant Ma’aden, Saudi Basic Industries Corporation (SABIC) and US-based Mosaic, a leading international fertilizer producer. The successful completion of the MWSPC project in 2018 has turned Saudi Arabia into the second-largest phosphate producer in the Middle East.
The biggest challenge at the MWSPC plant – in common with many other phosphate operations around the world – is removing significant amounts of unwanted silica, also known as flintstone or chert. This needs to be eliminated from run-of-mine material to improve its quality and ensure that phosphate rock concentrates are suitable for downstream chemical processing.
This challenge is even tougher for MWSPC. That’s because contaminants are traditionally removed from phosphate ore using large quantities of water (and chemicals). Yet this is not possible at the company’s arid inland desert location due to the lack of a natural rain-fed water supply.
TOMRA therefore collaborated closely with the designers of the MWSPC plant to find a way of reducing water (and electricity) consumption in downstream production processes. The installation of high-capacity TOMRA sorting machines emerged as the most viable and practical option. These machines are capable of efficiently identifying and ejecting unwanted silica from large volumes of phosphate feed materials.
Following their installation, TOMRA’s XRT (X-Ray Transmission) machines are now pre-processing more than half of the total 13.5 million tonnes of phosphate ore handled by the MWSPC plant every year. Running at a rate of 1,800-2,000 tonnes per hour, the XRT machines recognise and separate materials according to their specific atomic density. Advantageously, this process is completely dry and avoids the need for wet, water-based cleaning of materials.
The sorting machines have performed remarkably well at the MWSPC plant, delivering large efficiency gains and cost savings. “Now that this plant has been running for two years, the effectiveness of XRT sorting is clear,” comments Jens-Michael
Bergmann, TOMRA’s area sales manager for Europe, MENA and India. “By making it possible to remove 98 percent or more of liberated silica contaminants, XRT has reduced the workload and costs of crushing by about 75 percent, reduced the costs of milling by 45 percent, and reduced water consumption by 45 percent.”
He adds: “What’s more, the ability to reduce the size of the flotation plant has saved millions of dollars in construction costs, and continues to save about $10 million per year in the cost of flotation reagents alone.”
XRT sorting technology can perform equally well at improving the phosphate-processing efficiencies of many other operations globally. That’s the main lesson from the successful installation of TOMRA sorting machines at the MWSPC plant – in some of the most hostile working conditions on earth.