Sulphur 405 Mar-Apr 2023
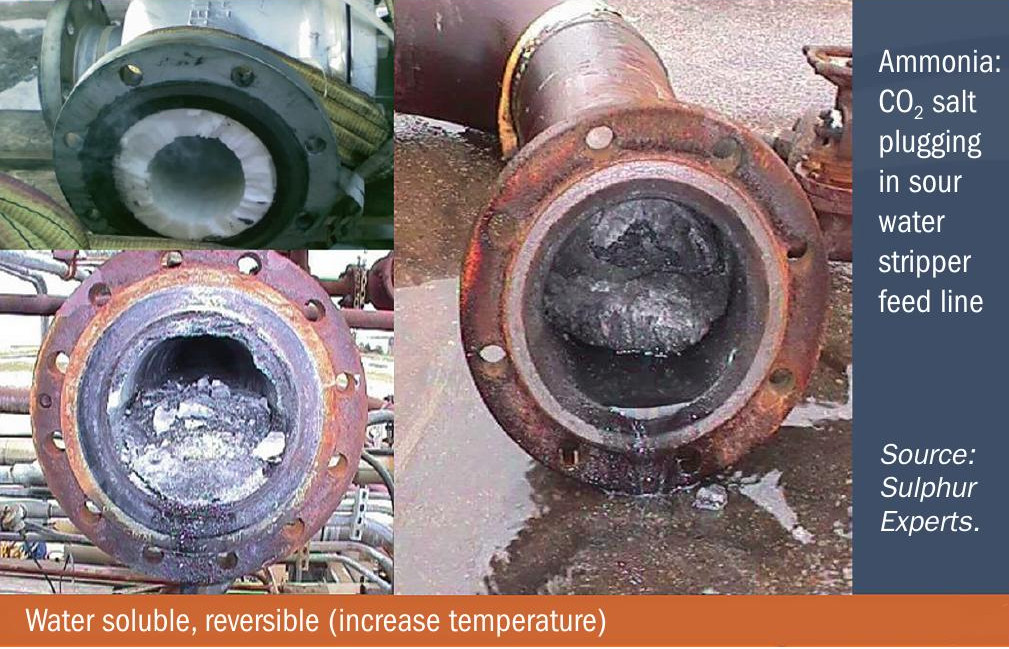
31 March 2023
A better understanding of SRU ammonia salt formation
PROCESSING SWS GAS
A better understanding of SRU ammonia salt formation
Gerald Bohme and Joe Brindle of Sulphur Experts Inc. combine new learnings, historical data, and recent onsite experience from operating companies to show what factors really impact ammonia plugging risk and what can be done to control them in order to allow for a wider operating range for SWS processing in the refinery SRU.
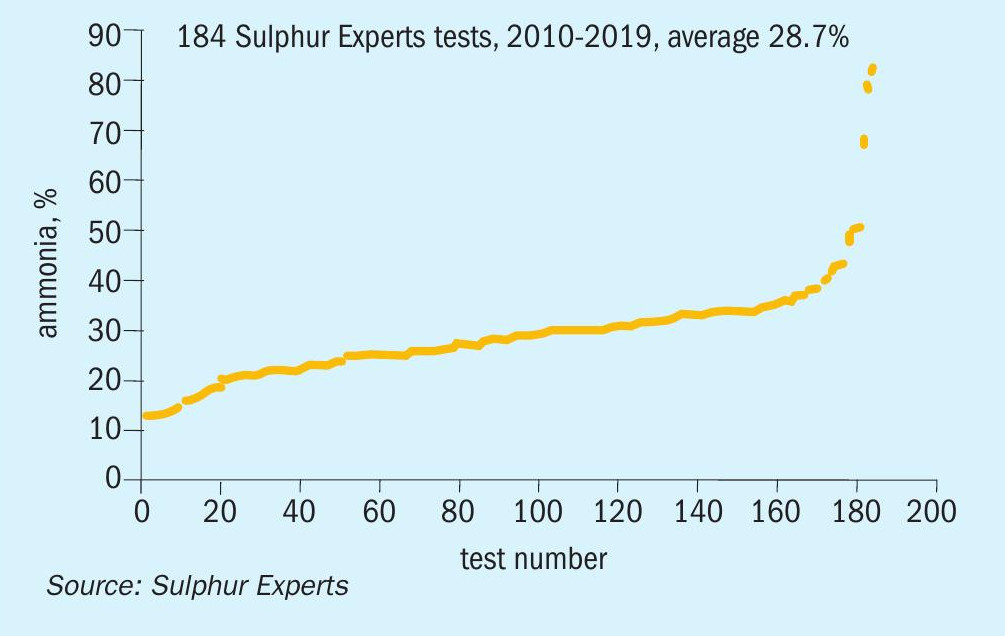
Processing sour water stripper (SWS) gas in the refinery sulphur recovery unit (SRU) has always come with warnings about plugging downstream of the reaction furnace due to ammonia salt formation. These warnings usually result in self-imposed operating limits for SWS gas that may not be required and may limit production for the refinery.
Apart from some scientifically validated knowledge about minimum effective furnace temperatures for ammonia destruction, rules of thumb are generally used to establish the safe operating envelope for SWS gas processing in the refinery SRU.
The need to properly understand the science behind the processing of ammonia-bearing streams in the Modified-Claus sulphur recovery unit (SRU) continues to increase as evolving refinery operations, including processing of bio feeds, result in ever-increasing ammonia concentrations in SRU feed gas streams1 . The potential risks associated with improper ammonia processing, primarily the concern regarding SRU plugging due to ammonia salt deposition, have resulted in several historical operating recommendations designed to minimise these risks.
As our understanding of ammonia processing continues to grow, however, and as more and more facilities have difficulty meeting these historical guidelines due to evolving refinery operations, many of these past recommendations are being called into question. Although many papers have been written on the topic of ammonia processing in the SRU in the past2 , this paper offers a number of important updates based on the following:
- A recent compilation of all of Sulphur Experts field data on ammonia processing from 2010 to 2019, which represents a very significant increase in actual field results on the subject.
- A number of recent case studies which provide results that deviate significantly from the historical and conventional expectations.
- New lab research (by Alberta Sulphur Research Ltd – ASRL) regarding the chemistry behind ammonia salt deposition3 .
The primary purpose of this article is to re-examine these historical ammonia processing recommendations and to determine if they are supported by the updated laboratory and field data. Where appropriate, suggested changes to the historical processing recommendations are provided.
Typical ammonia sources
It is well documented that ammonia is a common product component from various oil refining processes and is usually collected in a plant sour water processing unit4 . The facility operator can either recover the ammonia as a usable by-product or must dispose of the streams in an environmentally acceptable manner.
There are various processes available which recover the ammonia and H2 S as separate streams during sour water processing, potentially eliminating the need for processing of the ammonia bearing stream in the SRU process. In general, however, these processes have not been incorporated into most facilities due to capital cost issues and stream purity issues.
These sour water streams, therefore, are normally treated in a traditional single stage sour water stripper process in these single stage strippers, the ammonia is stripped from the water simultaneously with the H2 S, with both ending up together in a sour water stripper (SWS) gas stream. A typical SWS off gas will contain roughly equal parts (i.e. one-third each) hydrogen sulphide (H2 S), water, and ammonia (NH3 ), along with small amounts of hydrocarbon and other contaminants. A compilation of Sulphur Experts’ SWS gas analyses from 184 field tests (Fig. 1) shows reasonable agreement with this general expectation, although some SWS compositions can vary significantly from this expected one-third NH3 value and field verification of the SWS composition is always recommended for design and operational purposes5 .
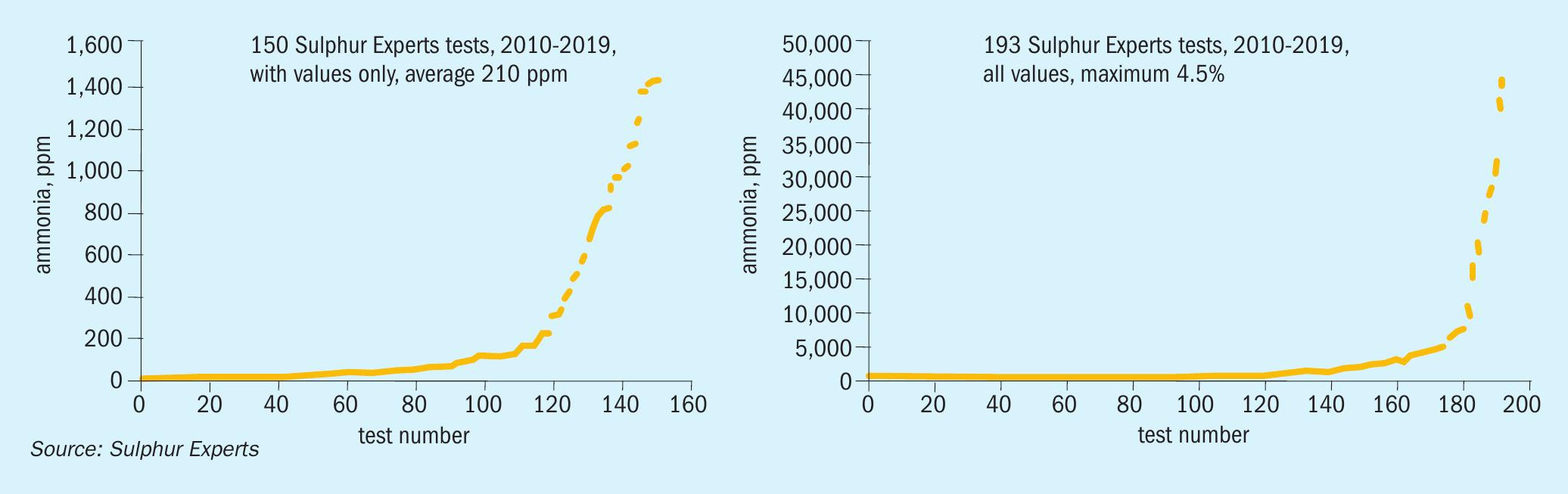
To a lesser extent, ammonia may also be present in acid gas feed streams which come from the various amine treating systems. A compilation of Sulphur Experts’ acid gas analyses from 193 field tests (Fig. 2) shows average ammonia concentrations of around 200 ppm for most streams, although with highly contaminated absorber feed streams and/or poorly controlled amine regenerator systems ammonia levels of 1 to 4+% have been observed. Problems associated with elevated ammonia levels in the amine acid gas stream can be mitigated by either pre-treating the sour gas streams to remove the ammonia or by rejecting the absorbed ammonia from the stripper’s overhead reflux water stream4 .
Concerns associated with ammonia processing
The primary concern associated with the processing of ammonia-bearing gases is that the chemically “basic” ammonia can react with the chemically “acidic” components present in the process gas streams to create salts.
In the feed gases, where no oxidised sulphur species have yet been created, the primary salt that can be created is from the reaction between ammonia and CO2 . There are a variety of salts that can be created in the SRU feed lines, with an associated variety of solidification temperatures, and a complete discussion of this topic is outside the scope of this paper. It is generally accepted, however, and it is well supported by actual plant operations, that keeping the ammonia bearing SWS gas stream above 85°C (185°F) will prevent formation of any salts in these feed lines. If salts are created at temperatures below these values (Fig. 3), experience has shown that they can be easily removed or reversed simply by increasing the temperature and allowing them to sublimate, or by washing them out of the system with hot water.
Downstream of the SRU thermal reactor, where oxidised sulphur species like SO2 are now present, additional salt species are now possible again with their own variety of solidification temperatures. Although a detailed review of all potential salt species and their formation temperatures is again outside the scope of this article, decades of SRU experience has shown that these salts can be created even at “normal” SRU condenser temperatures of 125 to 150+°C (260 to 300+°F). The industry belief is that the salts generated under these conditions are not easily reversed or removed, meaning that the potential for downstream SRU plugging (and associated loss of processing capacity) associated with these salts (Fig. 4) has always been of strong concern to SRU operators.
Ammonia destruction chemistry
To eliminate or minimise the risk of downstream SRU plugging from ammonia salts, a high degree of ammonia destruction in the SRU thermal reactor has always been desired. Previous research has shown the variety of chemical pathways that play a role in ammonia destruction6 . Potential pathways are displayed in Fig. 5 and are not discussed further in this article.
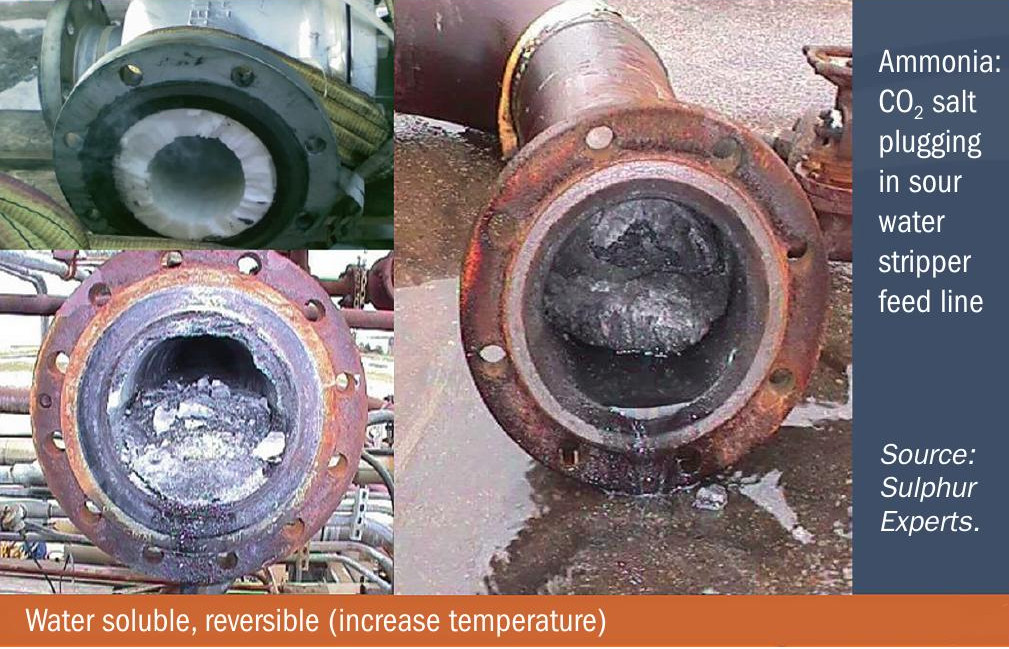
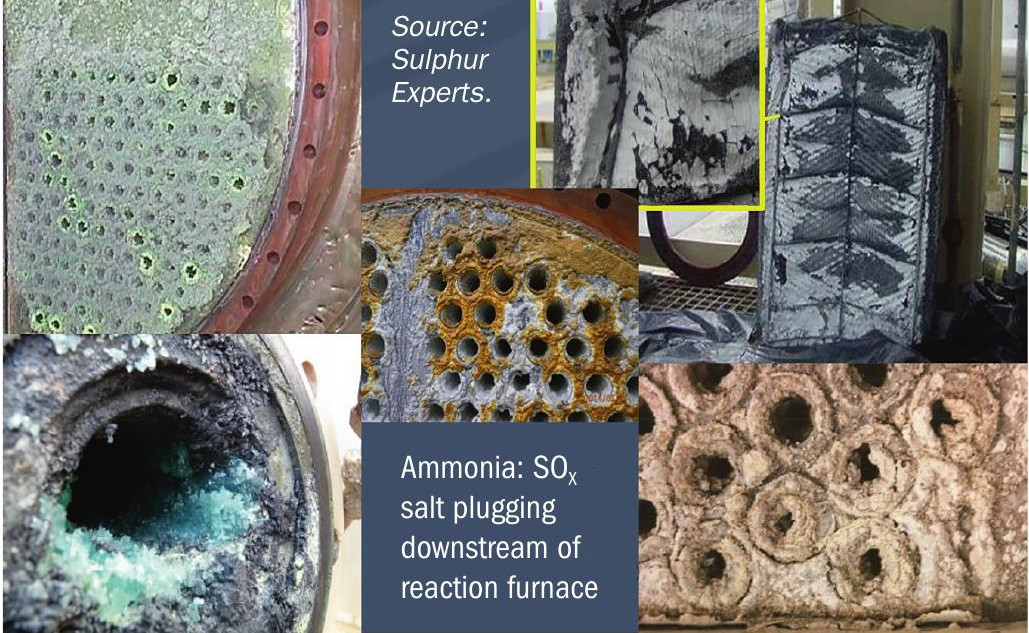
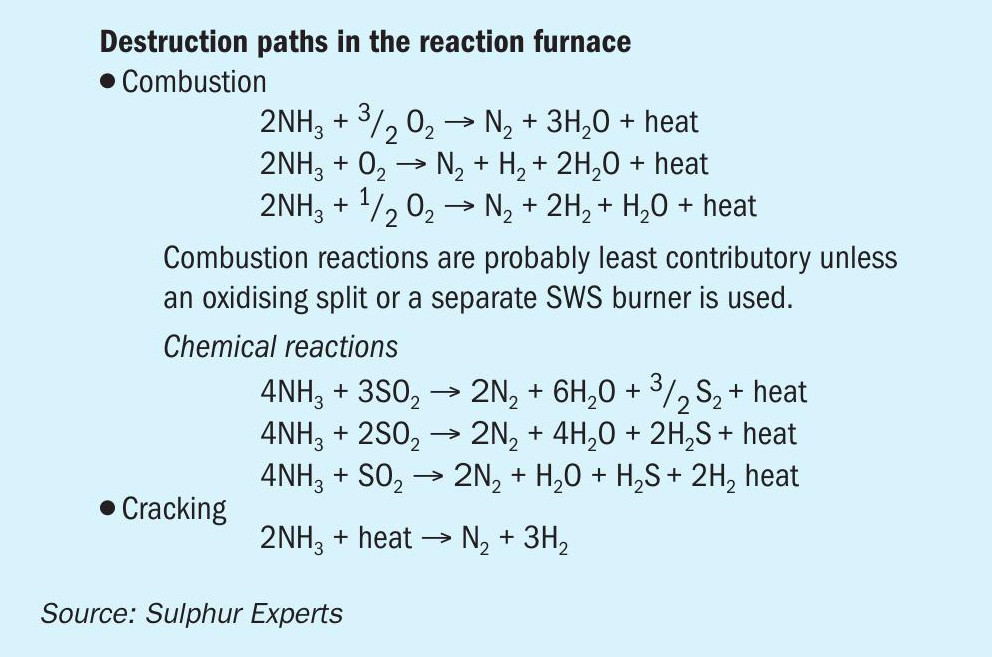
Regardless of the actual destruction chemistry, both historical lab work and historical field work have proven that complete ammonia destruction is not possible under any conditions in the SRU thermal reactor, meaning that the potential for ammonia salt formation in the downstream equipment is always present. Historical destruction recommendations, therefore, have primarily focussed on minimising ammonia breakthrough levels from the thermal reactor, with some additional focus on downstream SRU operating temperatures.
Historical rules for ammonia processing
Some of the earliest lab and field work that first attempted to specifically define the conditions required for optimising ammonia destruction and minimising ammonia salt risk was conducted in the early 1990s, and many of the historical “rules” for SWS gas processing come from this work7,8 . This early work was followed up later by detailed lab studies which more clearly defined the thermal reactor residence times and temperatures required to provide high ammonia destruction levels9 , as well as by additional field work that confirmed these lab studies in real world settings (Fig. 6)2 .
Based on this historical work, a set of “accepted” ammonia processing rules were gradually developed and that most SRUs follow to this day. These rules include:
- Optimal ammonia destruction requires thermal reactor temperatures of 1,250+°C (2,300+°F). Most SRUs use 1,200 to 1,300°C (2,200 to 2,350°F) as processing guidelines.
- Optimal ammonia destruction requires “long” thermal reactor residence times. Guidelines range from 0.8 to 2.0 seconds. There is no consensus, although times closer to the upper end of this range are becoming more common.
- Good mixing efficiencies in the thermal reactor are desired; mixing efficiency is primarily determined by the burner design.
- Residual ammonia levels downstream of the thermal reactor should ideally be less than 30 to 50 ppm. Values below 150 ppm have been considered to be “adequate” while residual concentrations over 300 ppm have been considered to significantly increase salt possibility.
- The amount of ammonia present in the feed (combined acid gas and SWS gas feed) should be minimised where possible. Different upper limits for ammonia in the combined feed have been suggested, with 25% being the highest accepted value. This is often expressed as a minimum acceptable acid gas:SWS gas ratio for a facility; 2:1 minimums are the most conservative used in the industry, with 1.5:1 and 1:1 ratios also commonly used. Processing of SWS gas alone (without acid gas) is considered extremely risky.
- The exact origins of many of these rules are unknown, and many are likely anecdotal and based on individual experiences rather than based on solid lab or field data.
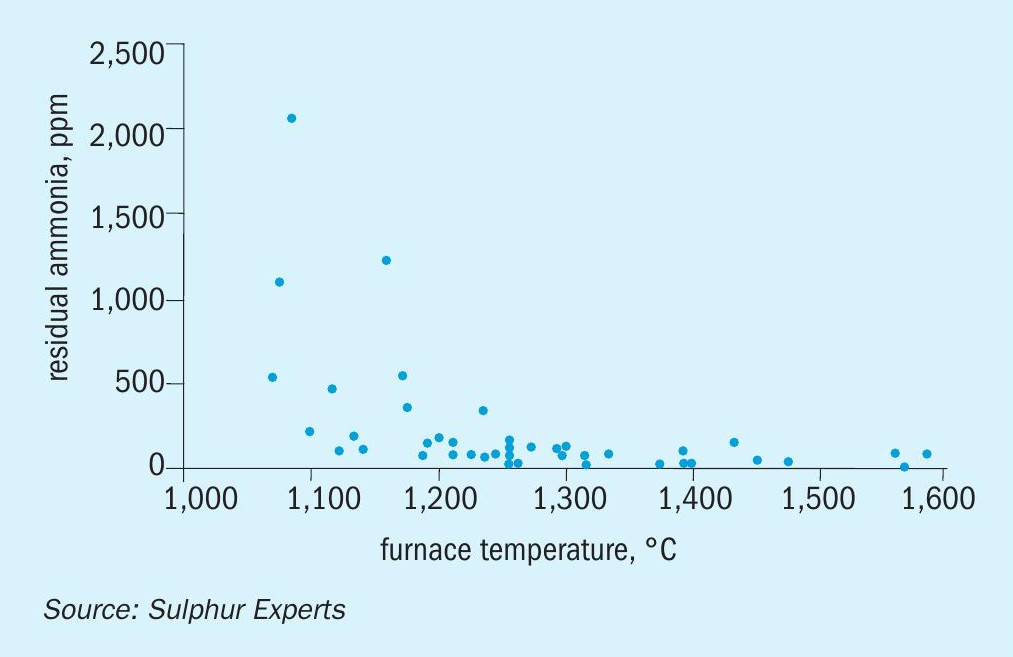
Even though many of these “rules of thumb” were initially meant to be general guidelines, many sites have accepted them as hard limits. In some refineries these hard limits on the SRU are already acting as bottlenecks on upstream amine and SWS operation, which in turn limit refinery throughputs and directly affect operating profits. For these SRU-limited facilities, and even for other facilities that have previously had no problems following these rules, changes to refinery operations that affect thermal reactor temperature (i.e. elevated CO2 levels in acid gas streams) or result in increased SWS gas production relative to acid gas production (i.e. processing of bio feeds) are resulting in increased scrutiny of these historical guidelines and questions about their necessity.
The other reason that these historical rules are being called into question is the increasing anecdotal operating evidence that has been gathered over the years that contradicts these rules. In general, this anecdotal evidence includes cases where the guidelines have not been met and/or where elevated ammonia breakthrough levels have been measured, but where no ammonia issues have been noted. This anecdotal evidence also includes cases where the guidelines have been strictly followed and where very low ammonia levels are noted, yet ammonia salt plugging has been reported.
Updated field data on ammonia processing
Sulphur Experts has recently been able to compile a data base of most of its field test results from ammonia processing SRUs from the years 2010 to 2019, and this data has been reviewed with respect to the historical processing guidelines. Although this data set does not include residence time data and is also not able to take “mixing efficiency” into account due to the inability to determine the condition of the burner and thermal reactor internals, it can be used to examine the effect of thermal reactor temperature and feed gas ammonia concentrations on ammonia destruction.
Fig. 7 shows residual ammonia concentrations measured downstream of the thermal reactor relative to the adiabatic (calculated) front chamber thermal reactor temperature. Although this data set does confirm that some of the highest residual ammonia levels correspond to some of the lowest thermal reactor temperatures, it shows many cases where the residual levels exceed the historical guidelines regardless of the temperature. It should be noted that none of these cases of elevated breakthrough, regardless of whether they were associated with high temperatures or low temperatures, resulted in known ammonia deposition issues in any of these cases.
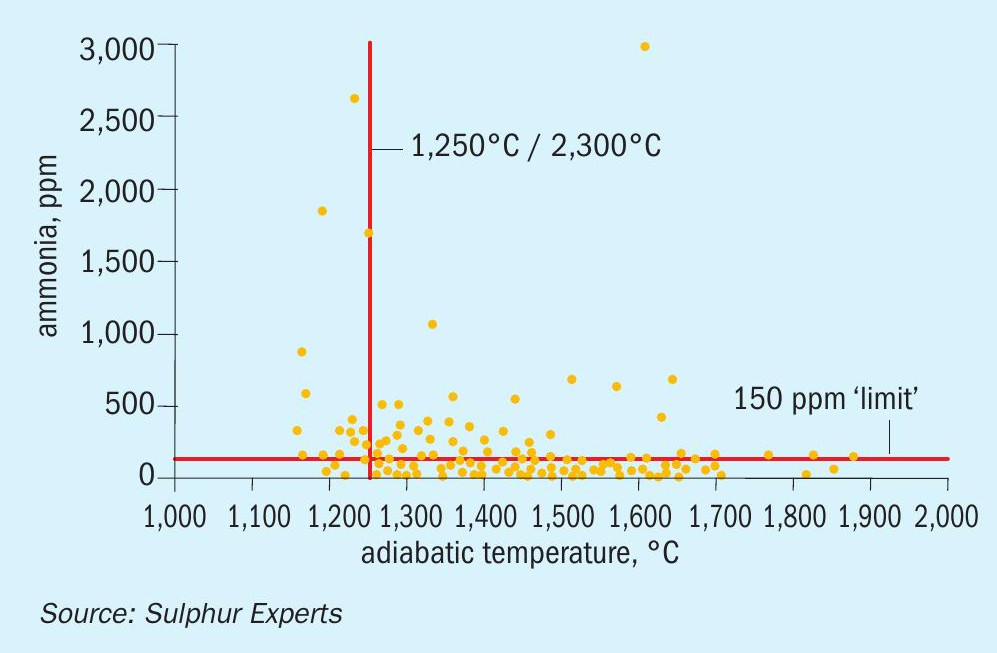
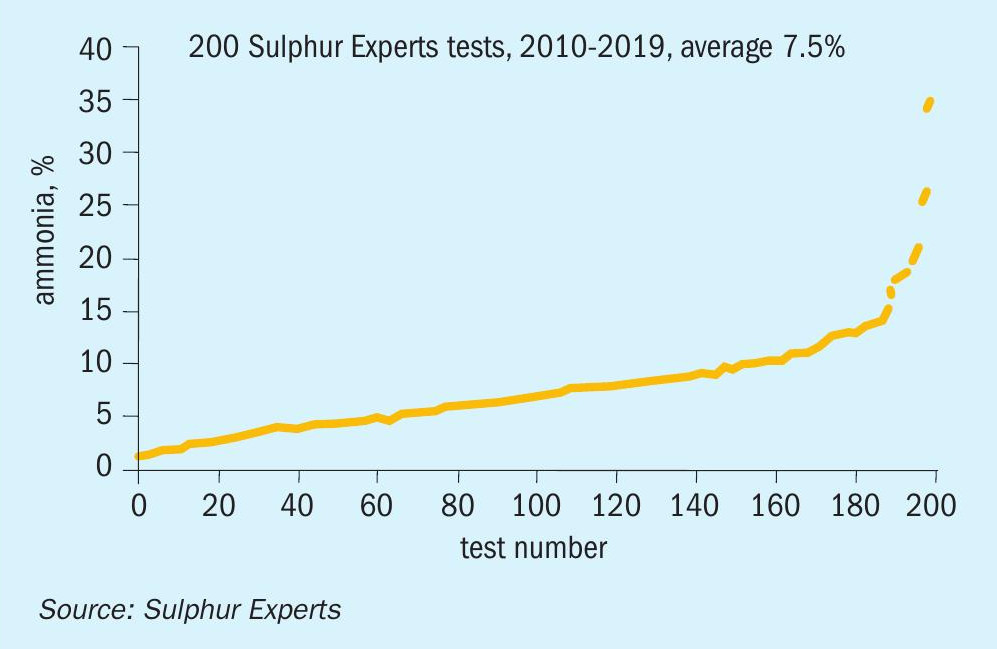
The cause(s) of the elevated breakthrough levels for many of the cases at higher thermal reactor temperatures was not immediately evident from the operating data or design reviews. The elevated values did not appear to be related to issues with low residence time but may have been due to such issues as high heat losses (low actual thermal reactor temperatures), burner damage or other mixing issues, or ammonia present in the acid gas being bypassed to the colder rear zones. In any case, the lack of relationship between breakthrough levels and ammonia salt deposition likely makes further review of the cause(s) of the elevated residual levels less important.
Fig. 8 shows the range of feed gas ammonia concentrations taken from the same data set. It confirms that, as expected, the large majority of SRUs process feeds well below the maximum recommended guidelines (average feed gas ammonia content was 7.5%); this guideline has been easy to meet for most facilities since most refineries create acid gas stream flows much higher than SWS gas stream flows.
Many facilities, however, process over 10% ammonia in the feed gas, with some exceeding even the most generous historical maximum guideline of 25%.
In order to see if there is any trend between feed gas ammonia and ammonia breakthrough, the data set was graphed in two different ways. Fig. 9 shows ammonia breakthrough directly relative to feed ammonia, while Fig. 10 shows the same ammonia breakthrough results relative to the feed SWS:acid gas feed flow ratio (reversed from acid gas:SWS ratio in order for a better display of the results).
These two graphs again both show a large number of cases where the residual ammonia levels exceed the historical guidelines regardless of the feed gas ratio or combined ammonia concentration. In addition, they don’t show any distinct trend towards increasing breakthrough of ammonia at elevated feed ammonia levels or SWS:acid gas ratios.
As with the previous graphs, it should be noted that none of these cases of elevated breakthrough, regardless of whether they were associated with meeting or exceeding the historical guidelines for feed, resulted in known ammonia deposition issues in any of these cases.
Overall, even though the data set generally confirms what was already known about improved ammonia destruction at elevated thermal reactor temperatures, it does not support the historical rules regarding feed concentrations and ratios and does also not show any link between residual ammonia and ammonia salt plugging risk (at least within the range of breakthrough ammonia values measured by the data set).
This clearly points to the fact that factors other than what were covered by the historical rules are likely related to ammonia salt risk.
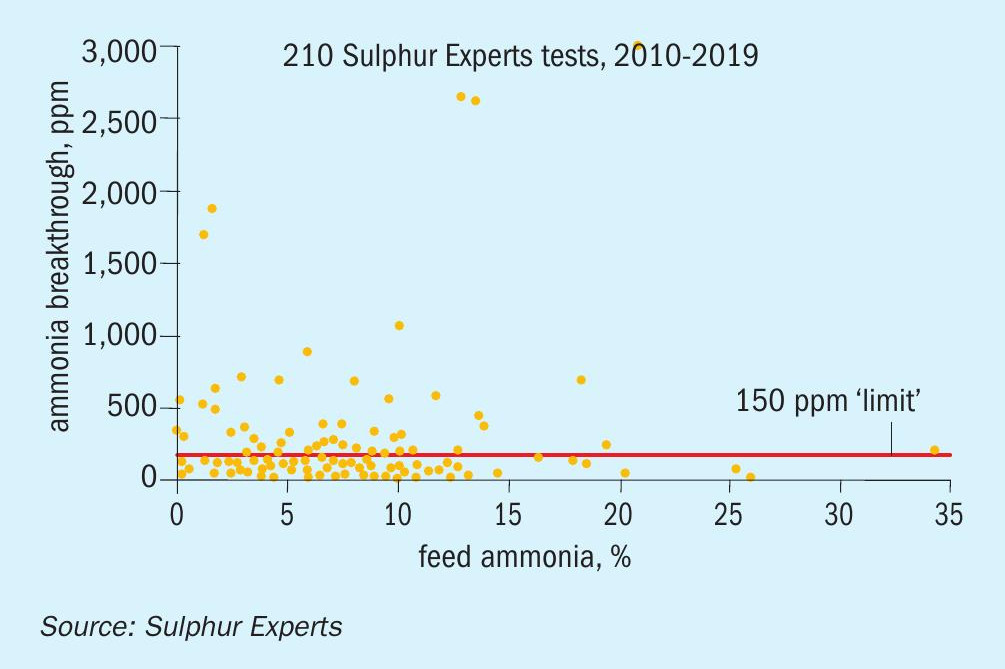
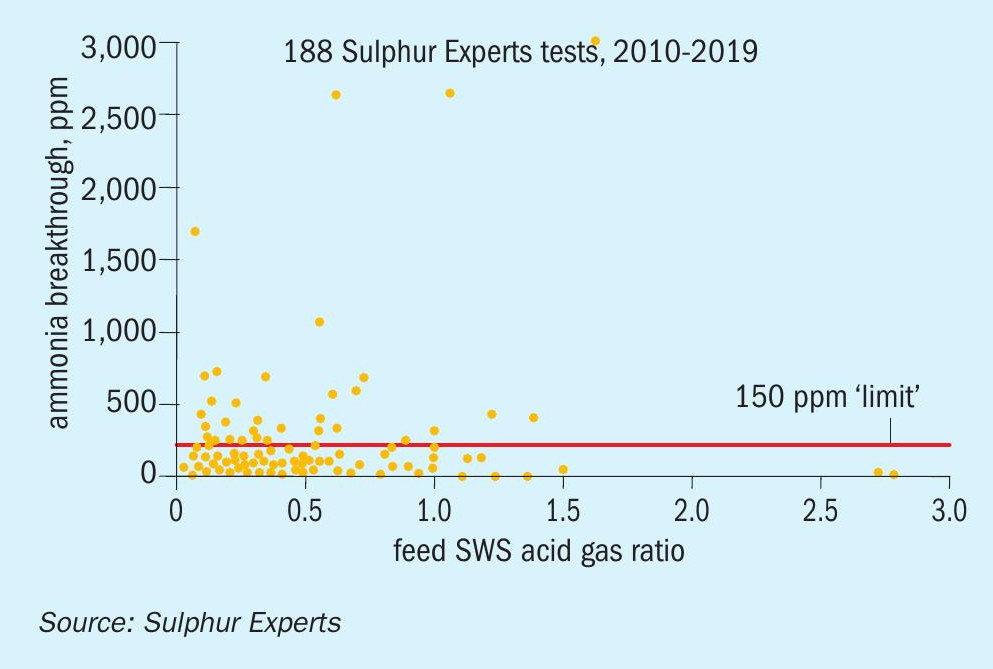
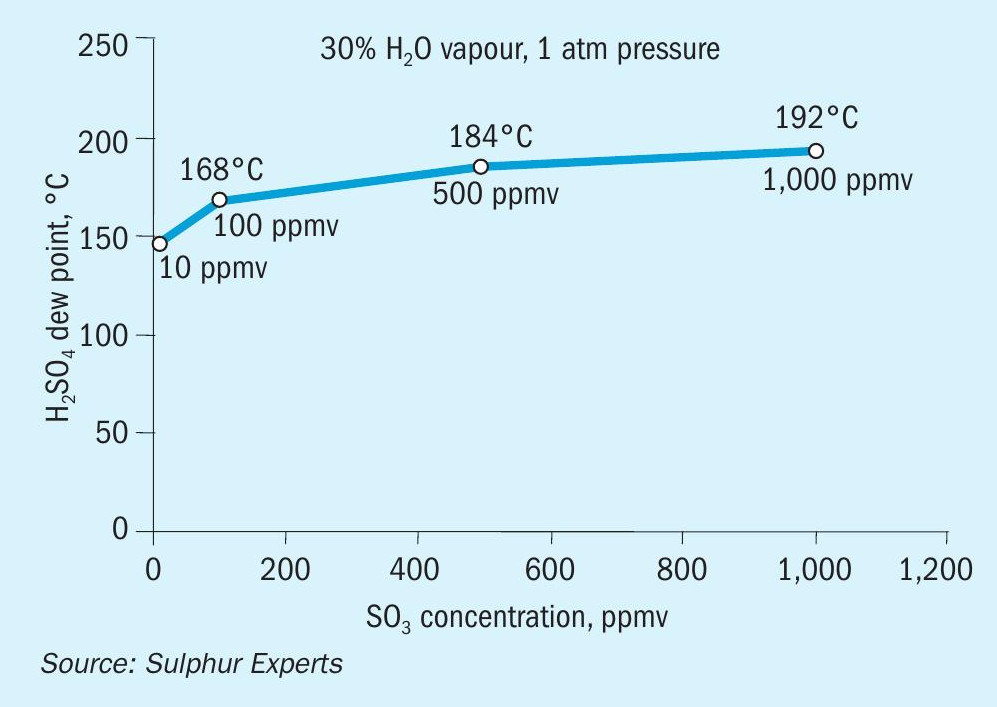
Updated lab data on ammonia processing
The most significant new research that provides an updated understanding of ammonia salt deposition was released by ASRL in 20213 . The full results of this study are available in their paper, however the key findings related to ammonia residuals reacting with SO2 are summarised below, along with Sulphur Experts’ interpretations of these results:
- With typical ammonia residuals and no SO3 , ammonia salts will not form at temperatures above 98°C (208°F) for any range of NH3 or SO2 that might normally be expected in SRU process gases, even in a significant SO2 or NH3 upset case.
- The exact temperature of the salt formation depends on the partial pressures of SO2 and NH3 in the gas, however, again these salts will only be created at temperatures below the freezing point of sulphur under any normally expected conditions.
- To form salts at the 125+°C / 265+°F process temperatures seen even in the coldest areas of the SRU (condensers) required percent levels of NH3 in the lab version of Claus tail gas with normal SO2 content and no SO3 .
- In short, ammonia + SO2 salts will likely only form at temperatures well below the sulphur freezing point. In this case, the frozen sulphur is the root plugging problem despite the fact that the salt may also be present in samples of the solid plugging material.
- Massive upsets (extremely high SO2 / extremely high ammonia slip) might cause salt formation at normal SRU temperatures; however, any level of “normal” ammonia slip will NOT create salts at typical SRU temperatures without SO3 present.
Instead of ammonia:SO2 reactions causing SRU salts, the same ASRL research showed the role of SO3 in salt formation. Again, the full results of this study are available in their paper, however the key findings related to ammonia residuals reacting with SO3 are summarised below, along with Sulphur Experts’ interpretations of these results:
- The presence of SO3 means that sulphuric acid can form by acid condensation.
- SO3 dewpoints overlap Claus operating temperatures; even single digit ppm levels of SO3 will condense at normal Claus condenser temperatures (Fig. 11)10 .
- The sulphuric acid created during condensation readily reacts with ammonia to form salts; these salts are the same types are usually identified in ammonia salt plugging cases
NH3 + H2 SO4 → NH4 HSO4
NH3 + NH4 HSO4 → (NH4 )2 SO4
- In short, any ppm levels of SO3 will react with any ppm levels of NH3 to create ammonia salts.
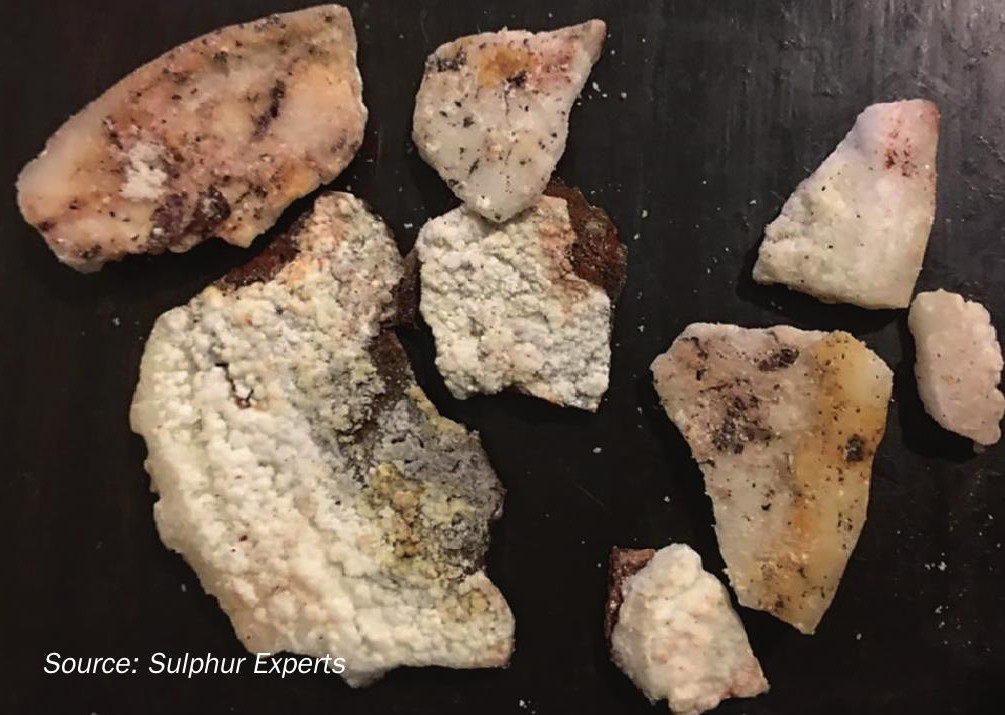
SO3 formation
The chemistry required for optimal sulphur plant operations dictates that only one third of the H2 S entering the sulphur plant be combusted to SO2 in the thermal reactor, with H2 S and SO2 then reacting in a 2:1 ratio throughout the rest of the SRU11 . This initial one-third combustion of H2 S means that the thermal reactor is a very reducing atmosphere, and even large upset conditions will almost never end in an oxidising atmosphere. Because of this extremely reducing condition, and because of the high thermal reactor temperatures, any SO3 that might be created in the combustion zone of the thermal reactor would not be stable and would reduce back to SO2 before exiting the thermal stage. This typical lack of any SO3 formation from the thermal reactor is confirmed by the low prevalence of ammonia salt problems in the industry; if the presence of SO3 exiting the thermal reactor was common, then ammonia salt issues would be equally common.
Laboratory research has shown that SO3 can be released by sulphated alumina catalyst12 . Once again, however, the generally low level of ammonia salt problems in the industry suggests that any SO3 present in the sulphur plant process gas due to this chemical pathway must be extremely low.
The one place in an SRU where SO3 is almost always created is in the sulphur plant incinerator/thermal oxidiser. The same oxidising conditions, however, that create the SO3 would also destroy any ammonia present at this point, meaning that ammonia salt deposits in the incinerator are not a common issue. Sulphur Experts has, however, worked with plants where incinerator SO3 and incinerator NH3 are both present, and rapid and constant ammonia salt deposition in the relatively cold incinerator emission monitoring systems at these locations (Fig. 12) have confirmed that salting and plugging are an issue.
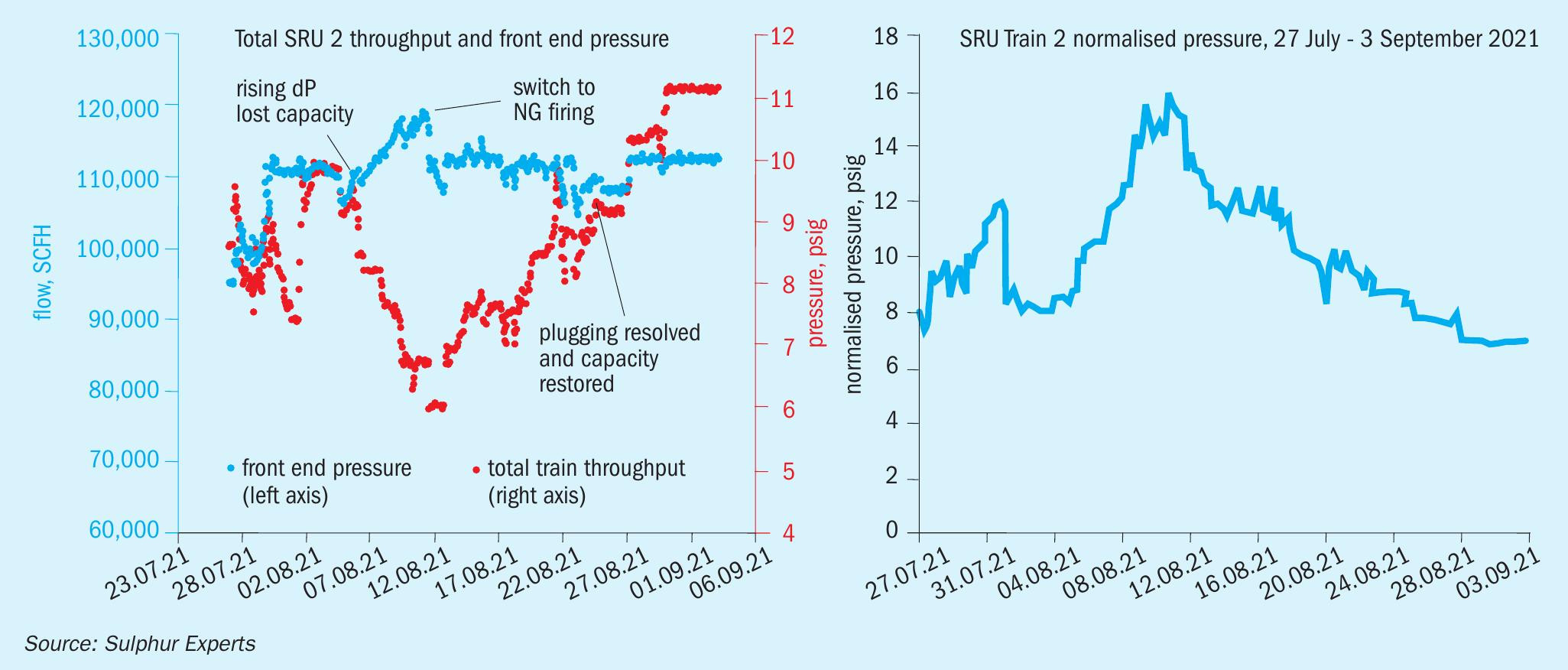
The most likely location where SO3 could be created and sustained upstream of an SRU incinerator is in an acid gas fired reheater (also commonly called an acid gas-fired auxiliary burner). These reheaters burn a slipstream of the feed acid gas in a fired heater, which then mixes with the cool upstream process gas from an SRU condenser before entering the downstream catalyst bed and then the next condenser. Although these reheaters are designed to operate under substoichiometric (reducing) conditions, usually 60 to 75% of stoichiometry13 , they could operate either partially or fully under oxidising conditions in cases such as inaccurate metering, use of air for burner purges, or damaged burners where multiple stoichiometry zones are present. Since this reheater stream is immediately cooled/quenched by mixing with the relatively cold condenser outlet stream, the further reaction of SO3 back to SO2 downstream of the reheater may not be possible. This SO3 would then condense when it drops below its dewpoint, most likely in the next condenser, and be available to react with whatever NH3 is present at that point.
Other sources of SO3 could also be present in a sulphur plant, including SO3 created by fires within the SRU during poorly controlled shutdowns or hot standby operations, 100+% combustion of acid gas in the thermal reactor, or any other type of SRU operation that results in an oxidising atmosphere in any part of the plant.
Case studies supporting new lab data – example 1
In 2021, Sulphur Experts was involved with an SRU plugging study for a USA refinery where this knowledge of the role of SO3 could be put to a real-world test. The background behind the request for assistance was:
- Two identical SRUs both processing similar acid gas and SWS gas volumes and having similar thermal reactor operating conditions.
- Both SRUs use three fired reheaters which normally operate on acid gas, although they were also capable of operating on natural gas.
- Only previous plugging history had been due to carbon soot deposition, with the plugging materials analysed and confirmed to be ammonia free (carbon and sulphur only).
- Sudden onset of rapid and persistent plugging in the final condenser of one SRU only. Resulting pressure drop issues were reducing the capacity of the SRU and, correspondingly, of the entire refinery.
The first round of Sulphur Experts’ analytical testing of the affected SRU determined the following conditions:
- Normal SWS composition; approximately one-third NH3.
- Clean acid gas; 16 ppm NH3 .
- Measured thermal reactor temperature 1,298 to 1,358°C (2,370 to 2,477°F), consistent with historical operation.
- Measured ammonia residuals 65 ppm. l Near identical conditions for the second (unaffected) SRU.
- Third reheater showed variable oxygen exiting the reheater of 650 to 4,200 ppm which could not be eliminated by ratio changes.
Although direct measurement of SO3 from the reheater was not undertaken due to the lack of reliable field test methods for this type of analysis, the measured excess oxygen confirmed an oxidising atmosphere in the reheater. Although the metered air and acid gas flows to the reheater were consistent with significantly substoichiometric operation, a visual examination of the burner through the site glass showed obvious burner damage meaning that poor mixing efficiency and simultaneous high/ low stoichiometry zones within the same burner were likely. This poor mixing efficiency was also evident from other analytical results, which showed that a portion of the hydrocarbons present in the acid gas feeding the burner were not combusted.
Since oxygen (SO3 ) could not be eliminated by ratio changes to the acid gas burner, the reheater was switched to a sub-stoichiometric natural gas burning mode, which used a separate undamaged burner assembly within the same reheater chamber. This change resulted in the immediate elimination of measured oxygen (and hydrocarbon) from the reheater effluent.
As soon as the switch to natural gas was conducted, the rapid increases in pressure drop that had been noted through the sulphur plant for the previous week of operation immediately stopped (Fig. 13). In an even better, and unexpected, outcome for the plant, the pressure drop actually started to gradually decline and within two weeks the pressure drop and plant throughput were both back to, or even slightly better than, normal.
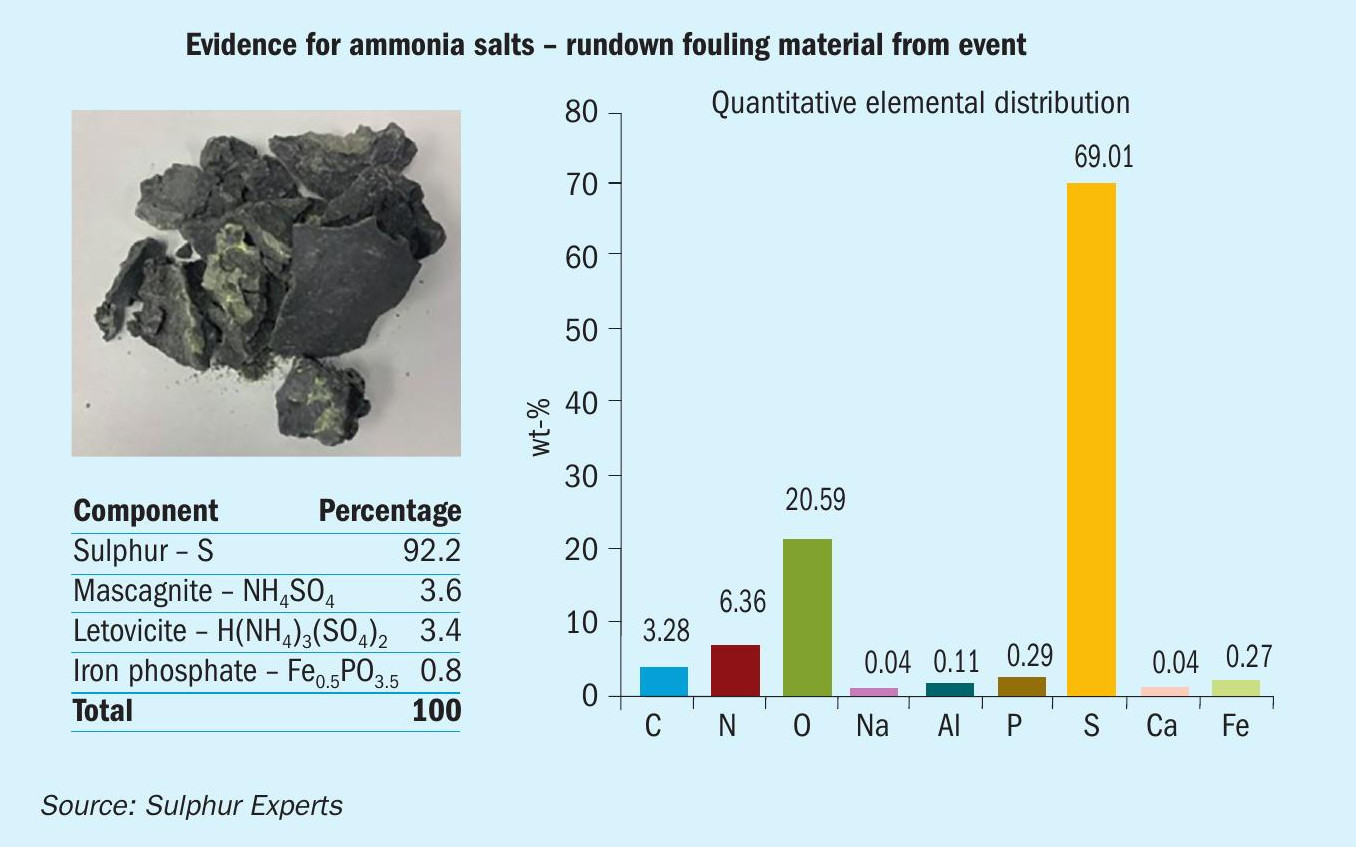

Prior to the reheater changes, plugging material was also collected from the final condenser, since some of these materials were present as solids in the rundown system. Analysis of these materials confirmed the presence of ammonia salts (Fig. 14) confirming that the plugging was indeed ammonia related.
It should be noted that no other changes to the SRU operation were conducted other than switching the reheater fuel source; both the thermal reactor temperature and the final condenser temperature remained unchanged.
The only difference was the elimination of the reheater oxidising atmosphere, meaning the minimisation or elimination of the possibility of forming SO3 in the reheater. The reduction of the pressure drop after the SO3 formation was eliminated suggests that the ammonia salts that had been formed were disappearing, either being physically washed from the system by the liquid sulphur flow or by some type of chemical decomposition.
It is notable that this case study was consistent with other Sulphur Experts’ past troubleshooting experiences where ammonia salt plugging issues occurred almost exclusively in sulphur plants with fired reheaters, and where modifications to these reheaters were the ultimate solution (as opposed to trying to change the ammonia breakthrough levels). This case study, as well as these other field experiences, are completely in keeping with the ASRL work showing that the presence of any SO3 even with low ammonia residuals leads to salt formation, and the elimination of the SO3 is the key to stopping the salt formation. The reversal / removal of the salts in this field result case provides optimism that ammonia salt issues in other facilities can not only be stopped through SO3 elimination, but that lost capacity can actually be recovered once the ongoing salting issue has been corrected.
Case studies supporting new lab data – example 2
The data presented above, including Sulphur Experts’ historical data, the ASRL findings, and supportive case studies, have resulted in an increased willingness by Sulphur Experts and some of its clients to question and even abandon (at least temporarily) some of the historical rules regarding ammonia processing. In a second case study, a client with a strong operational incentive to process only SWS gas when acid gas was not available was encouraged enough by the changed understanding of ammonia processing to attempt a five-day run on SWS only. The plant data collected from the SWS-only run is shown in Fig. 15.
Although on-site analyses were not collected for this test run, Sulphur Experts provided advice on operating conditions (primarily regarding maintaining acceptable reaction furnace temperatures through the cofiring of natural gas) and advice on process monitoring (constant pressure monitoring as an indication of any ammonia salt deposition). The refinery design included high pressure steam reheaters only, so the possibility of SO3 formation downstream of the thermal reactor was considered to be zero. Using the updated understanding of ammonia salt deposition, this meant that the risk of ammonia salt deposition, despite running SWS gas only (33% NH3 ) was also near zero.
The Fig. 15 data shows that no increase in normalised pressure through the SRU was noted during the five day run, and no operational issues overall were encountered. This has provided the client with the confirmation needed to conduct further SWS-only operational periods when no other economic alternative to this mode is available in the future (i.e. when acid gas is unavailable and when sour water storage is also not available).
Case studies supporting new lab data – example 3
A final recent case study that once again supports the new understanding of ammonia processing comes from a non-traditional sulphur plant that treats H2 S on a batch (instead of continuous) basis. Despite having no SWS gas and having only small ppm levels of ammonia in the acid gas feed, and despite test results showing less than 20 ppm of ammonia exiting the thermal reactor, the plant has experienced ongoing plugging issues with both ammonia salts and corrosion products appearing in analyses of the plugging materials (Fig. 16). Preliminary troubleshooting for the site confirmed periods of overall oxidising operation within the sulphur plant related to the batch nature of the operation, which likely lead to periods of SO3 formation and subsequently to both the corrosion and the ammonia salt formation. Using the new understanding of ammonia processing, the site is currently focussing on eliminating the SO3 formation rather than on any attempts to control ammonia feed or residual values.
Conclusions/summary
The data presented in this article has given Sulphur Experts a high degree of confidence that cases of ammonia salt deposition are primarily related to rare instances of SO3 formation within sulphur plants and that ammonia salt formation has a much lower connection with ammonia feed or breakthrough values than historically believed. Although Sulphur Experts is not ready to fully abandon the old rules, and believes that further research and further field studies and cases will be required before an industry-wide modification of the rules can be recommended, the modified conclusions and recommendations that Sulphur Experts currently provides to industry clients can be summarised as follows: l High destruction of ammonia is still generally desirable in order to limit the quantity of ammonia available for salt formation. Exact ammonia breakthrough concentrations, however, are not a primary determinant of plugging risk at any reasonable levels – don’t fixate on exact levels or limits. l Reasonable reaction furnace temperatures are still desirable, but again are not a primary determinant of plugging risk.
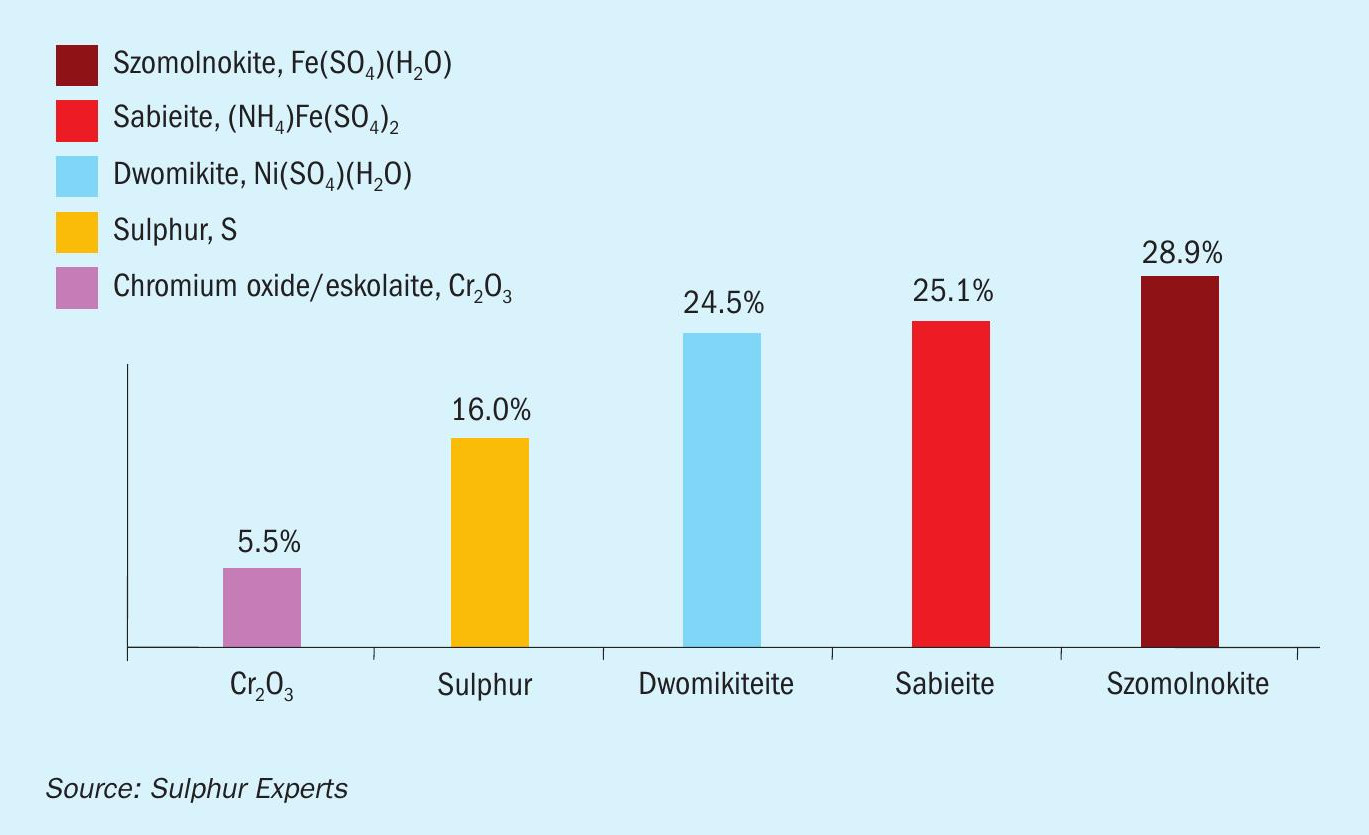
- Minimum acid gas to SWS ratios and/ or maximum total feed NH3 levels are likely not required; focus on temperature regardless of ratio.
- When deviating from the historical rules for the first time, keep a close eye on SRU pressure profiles. As long as pressures don’t change, ammonia salts are likely not occurring to any extent that you care about.
- For any pressure issues believed to be associated with ammonia salts, focus first on possible sources of SO3 formation. Acid gas fired reheaters are the most likely source, although SO3 could also be created under other oxidising conditions.
- Be aware that ammonia salts may also be present due to SO2 + NH3 reactions at temperatures below the freezing point of sulphur. In these cases, however, the low temperature (frozen sulphur) is the root cause of plugging problem and the fact that ammonia salt is also present does not mean that poor ammonia processing is at fault.
References