Sulphur 405 Mar-Apr 2023
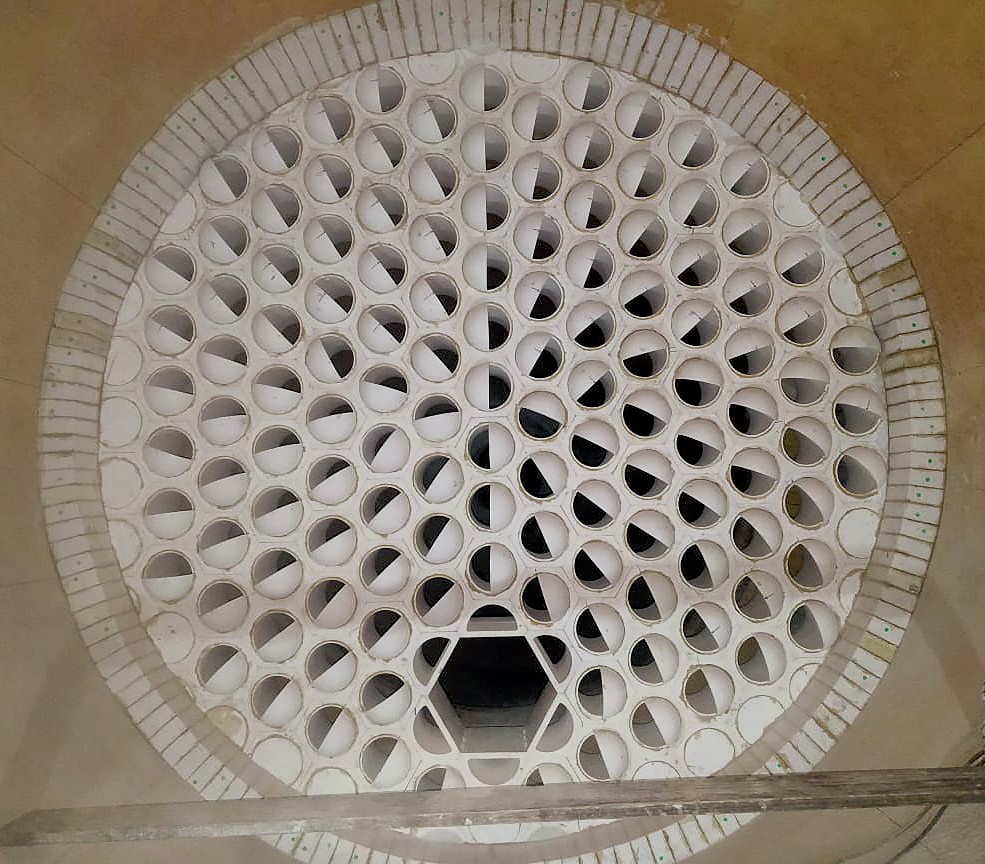
31 March 2023
Improving the performance of the SRU thermal incinerator
SRU THERMAL INCINERATOR DESIGN
Improving the performance of the SRU thermal incinerator
Following the success of VectorWalls™ in the reaction furnace of sulphur recovery units over many years, VectorWalls™ are now delivering similar benefits in SRU thermal incinerators. Uday N. Parekh of Blasch Precision Ceramics reports on the deployment of VectorWalls™ to improve the performance of the SRU thermal incinerator and provide benefits such as lower fuel gas consumption and lower CO2 emissions.
Thermal incinerators treat the tail gas effluent from SRUs prior to emitting the waste gas to the atmosphere. Their key function is to facilitate the combustion / oxidation of H2 S, COS, CS2 , sulphur vapour, H2 and CO to the mandated stack gas outlet specs for CO, TRS, etc. Achieving this objective requires the careful optimisation of various input parameters: Higher incinerator temperatures and excess oxygen in the stack improve the ability to meet performance specs but with an economic penalty of higher fuel gas consumption and an environmental penalty of higher CO2 emissions. Also, higher residence times in the incinerator achieved via larger incinerator size can help but this comes with higher capital cost. So, these parameters must be optimised to minimise capital costs and more importantly the operating costs and CO2 (GHG) emissions.
This article describes the deployment of customised checkerwalls (VectorWalls, Fig. 1) to improve the performance of the incinerator. For background, these walls were developed for use in the SRU reaction furnace (RF), first to offer improved structural integrity, but were subsequently refined to provide better RF performance via tighter residence time distribution, higher front-end temperatures and enhanced turbulence for better mixing (Fig. 2), the three Ts of combustion1 . These have been successfully deployed at hundreds of SRUs worldwide over the past 20+ years, significantly improving RF conversion and contaminant destruction. Based on this success there has been a strong interest in these VectorWalls™ delivering similar benefits in the thermal incinerator. These walls have been recently deployed in a few incinerators in the Middle East and have yielded the desired performance benefits via providing better mixing, and higher temperatures and residence times. Specifically, they have resulted in lower fuel gas consumption contributing to operating cost savings and also lower CO2 emissions that are becoming increasingly desirable.
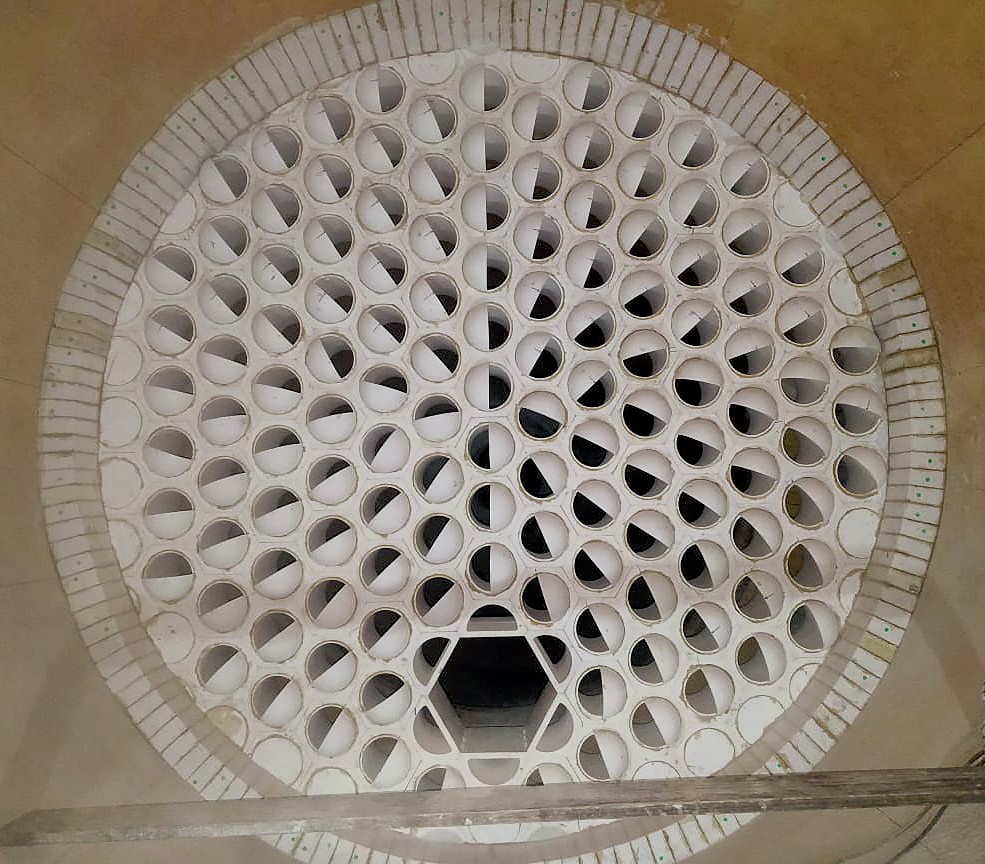
Incinerator theory
Sophisticated models based on rigorous theory and empirical correlations are used for the design and optimisation of the thermal incinerator. These models honed through the years using field measurements to develop kinetic correlations help predict the extent of the various oxidation reactions and breakthrough of H2 S, COS, CS2 , H2 and CO2 . The correlations predict exit species concentration as a function of inlet compositions, excess O2 at the stack outlet, incinerator temperature, residence time and a kinetic design factor “K”. K is an empirical factor which describes the extent of mixing between the various process streams entering the system and is equipment and design specific. A higher K value results in lower component breakthrough; alternatively same exit compositions can be achieved at lower temperatures and fuel gas consumption resulting in substantially lower CO2 emissions.
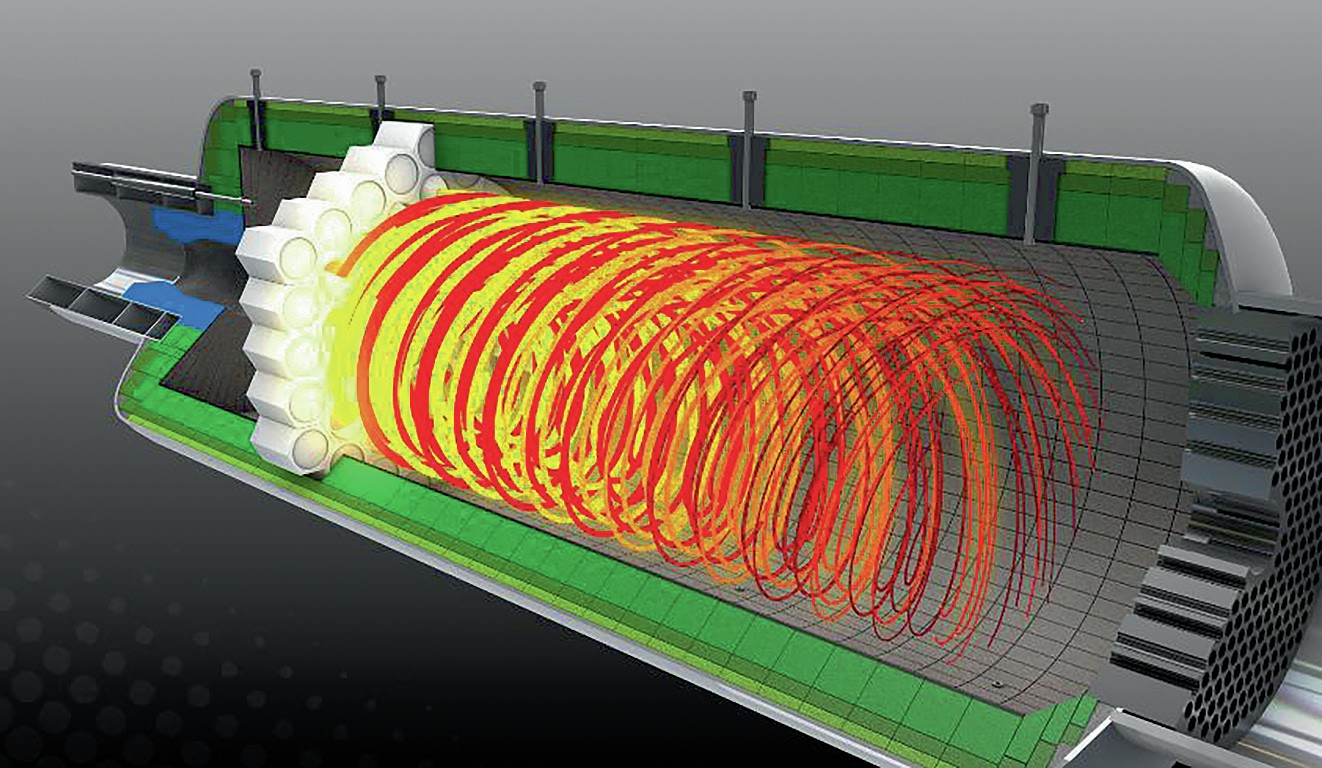
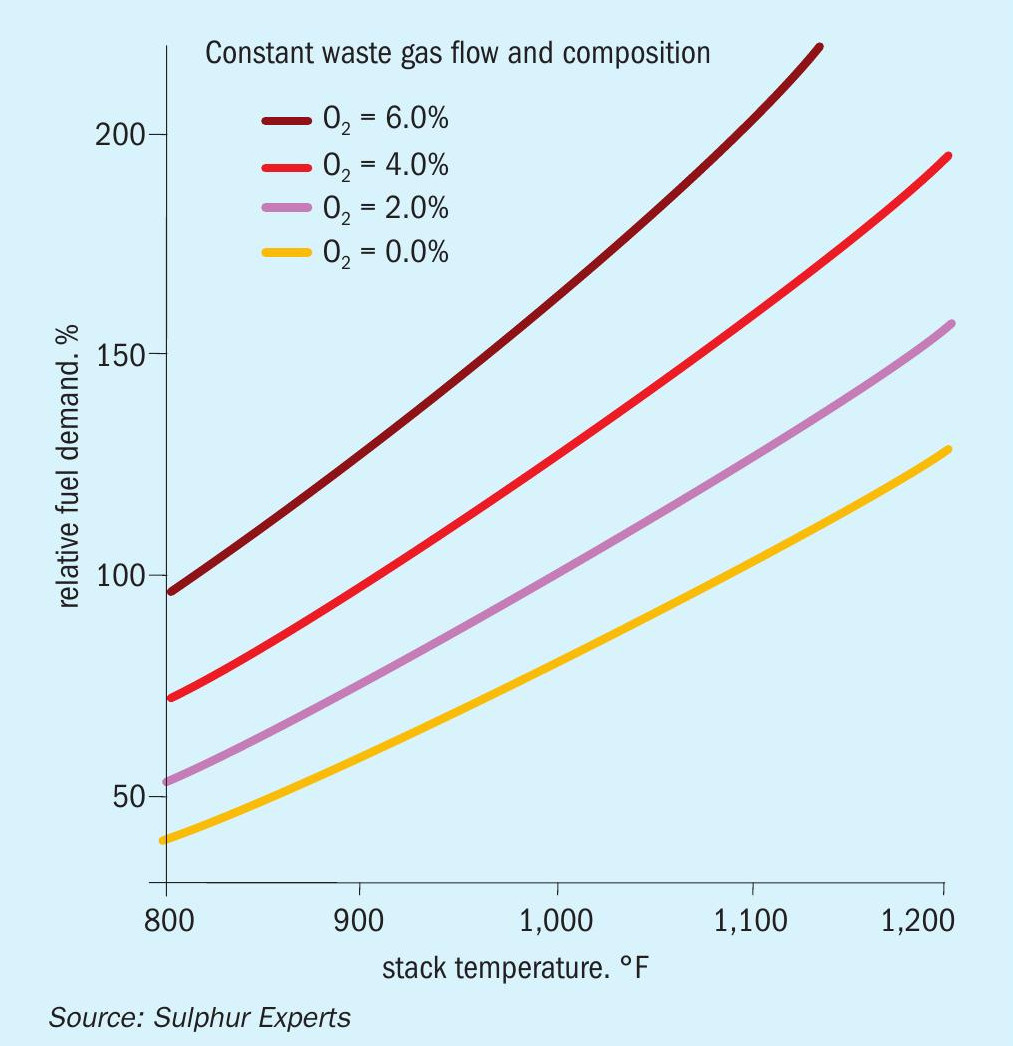
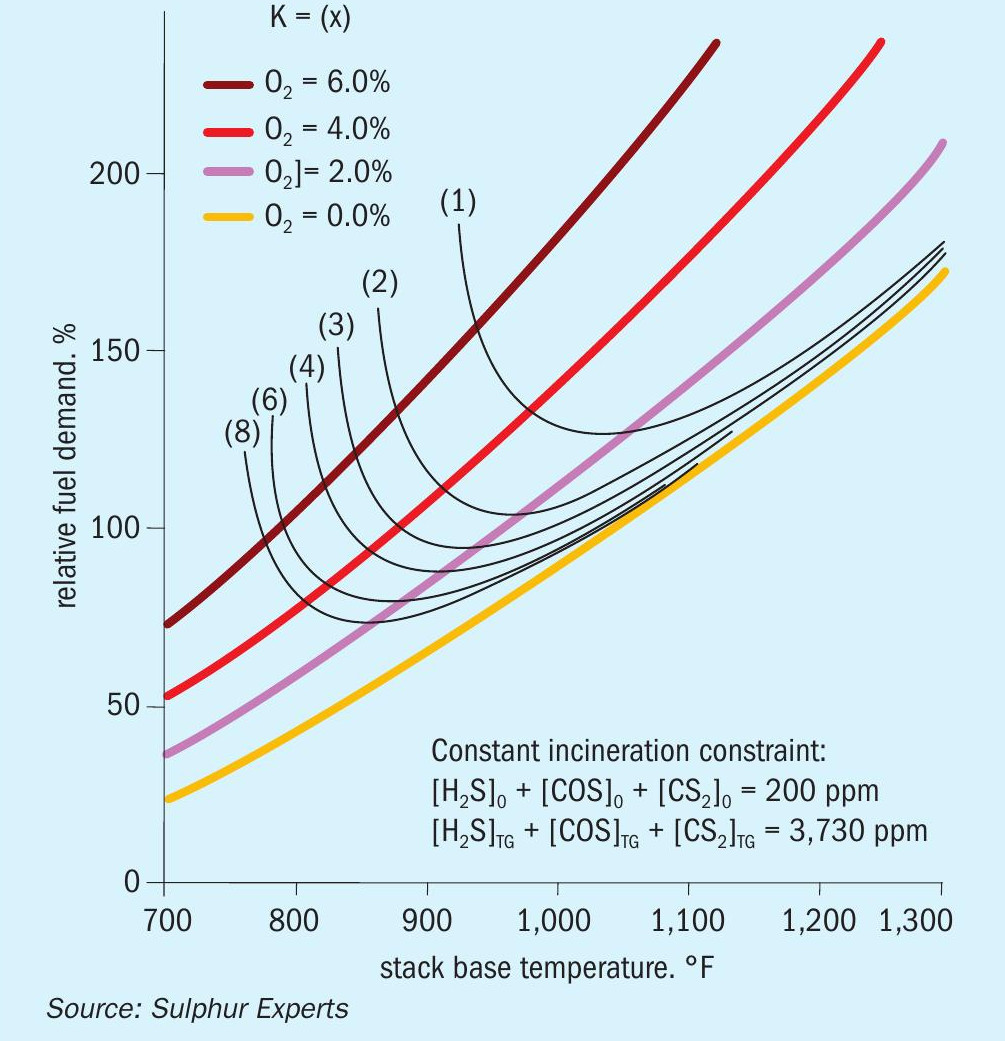
Fig. 3 depicts how higher temperature and excess oxygen result in better thermal incinerator performance but at the cost of higher fuel gas consumption and hence CO2 emissions. Figs 4 and 5 demonstrate the dramatic decrease in fuel gas consumption and H2 S emissions respectively from higher K factors. So, besides the design parameters of operating temperature and excess oxygen it can be seen that higher K factors can also significantly improve the performance of the incinerator and importantly this is achieved without the direct penalty of higher CO2 emissions. Blasch VectorWalls™ through their ability to provide extremely enhanced mixing, have been discovered to be ideally suited to provide higher K factors and improved incinerator performance. Additionally, the shielding of the heat loss by the Vector tiles provides higher frontend incinerator temperatures and improved kinetics resulting in improved incinerator performance. Further, Blasch has developed different tile geometries that can provide even better capture of the heat in the incinerator (Fig. 6) resulting in even greater fuel savings and these will be tested in collaboration with one of the operating companies.
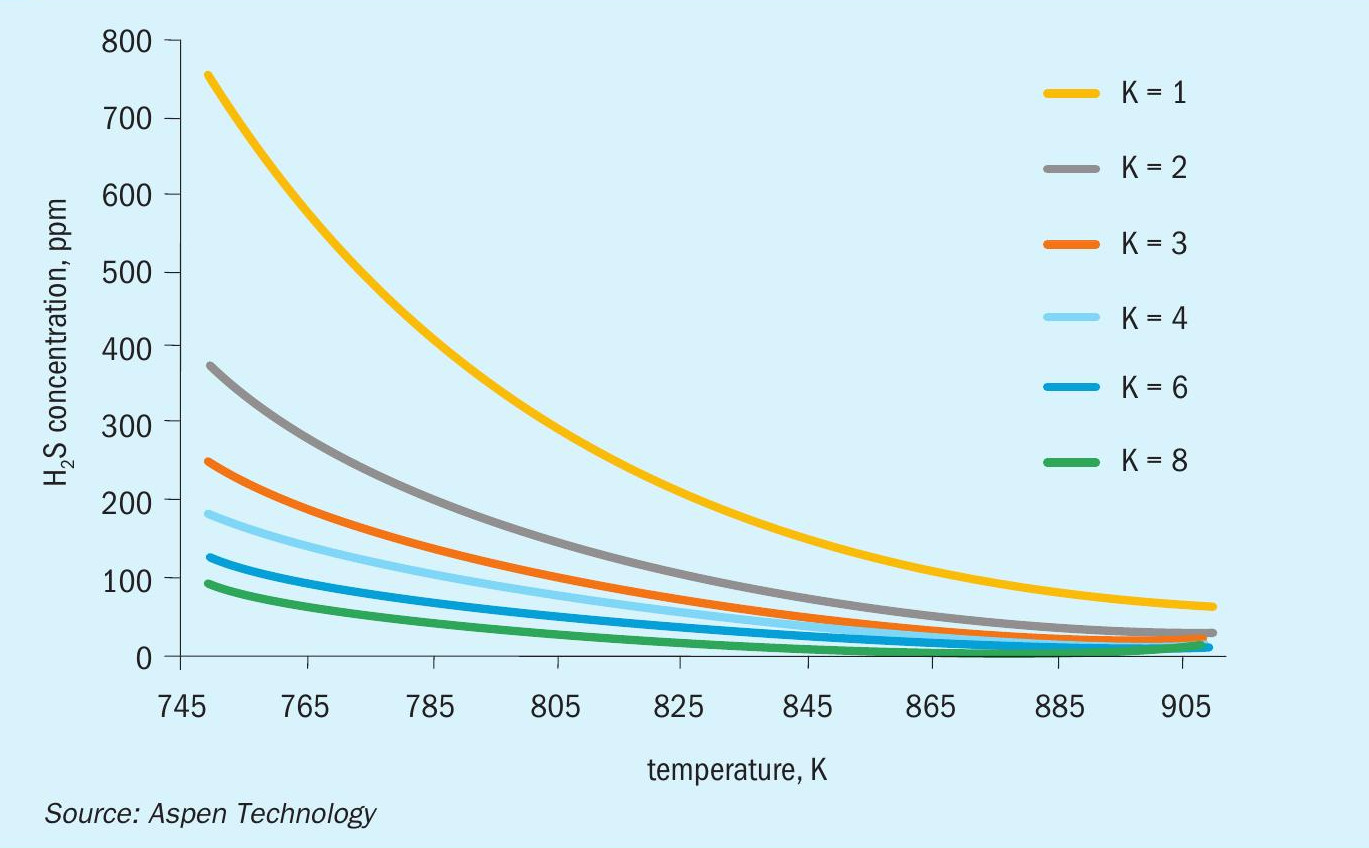
The benefits of better mixing (higher K factor) and higher temperatures in the incinerator offers the following options to an operating company based on where they stand with current operations:
- same performance at lower temperature and fuel gas consumption;
- better performance at same temperature and fuel gas consumption.
Fig. 7 depicts the relationship between CO concentration and incinerator temperature for an operating unit in the UAE. It shows that a slightly higher temperature than 700°C is required to achieve the CO limit of 400 ppmv. This is an ideal case where deployment of a VectorWall™ would aid in achieving the higher incinerator temperature needed without the need for firing additional fuel gas with its attendant higher CO2 emissions.
Operating results
The preliminary results from the deployment of the Blasch VectorWalls™ in the thermal incinerator have been very encouraging. Fuel savings of close to 10% have been realised and it is anticipated that this can be further enhanced with the Gen 3 Vector Tile designs that can offer even higher front-end incinerator temperatures and resultant greater fuel gas savings. Applying these fuel savings to say a 1,500 t/d gas plant SRU will result in operating cost savings of about USD one million per year plus the associated carbon credits.
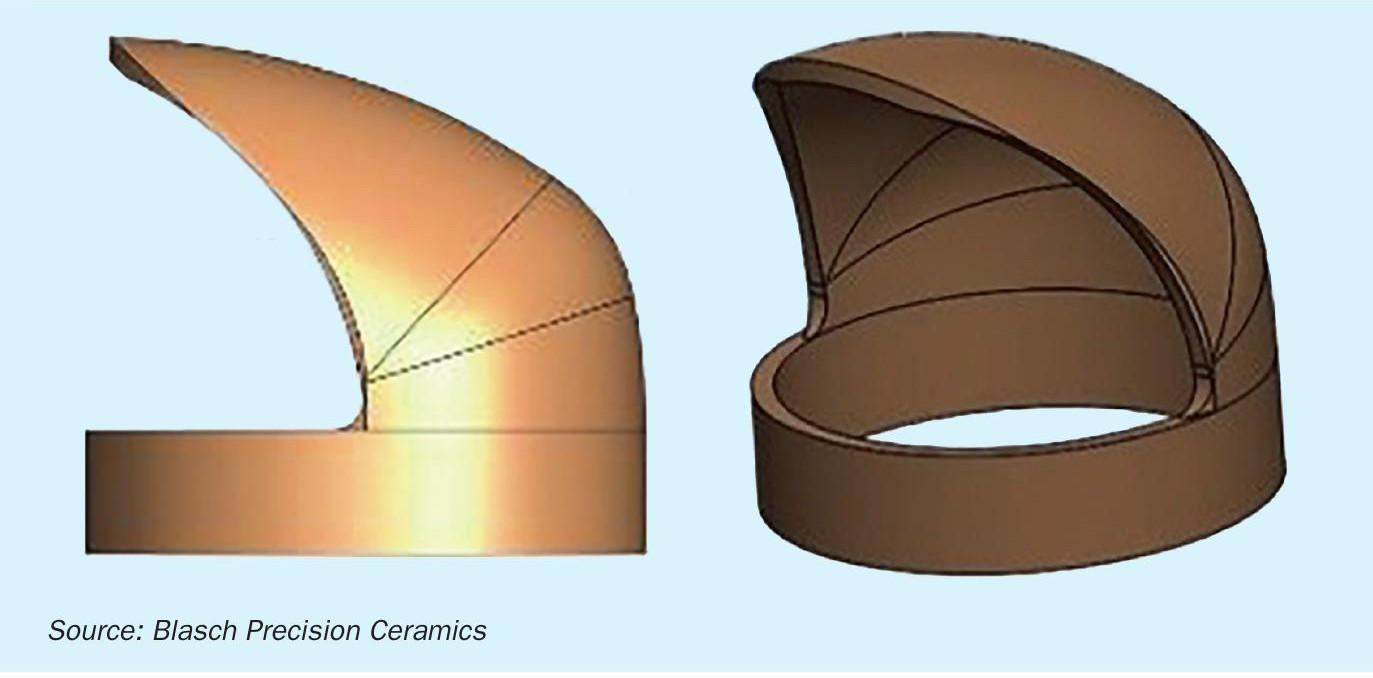
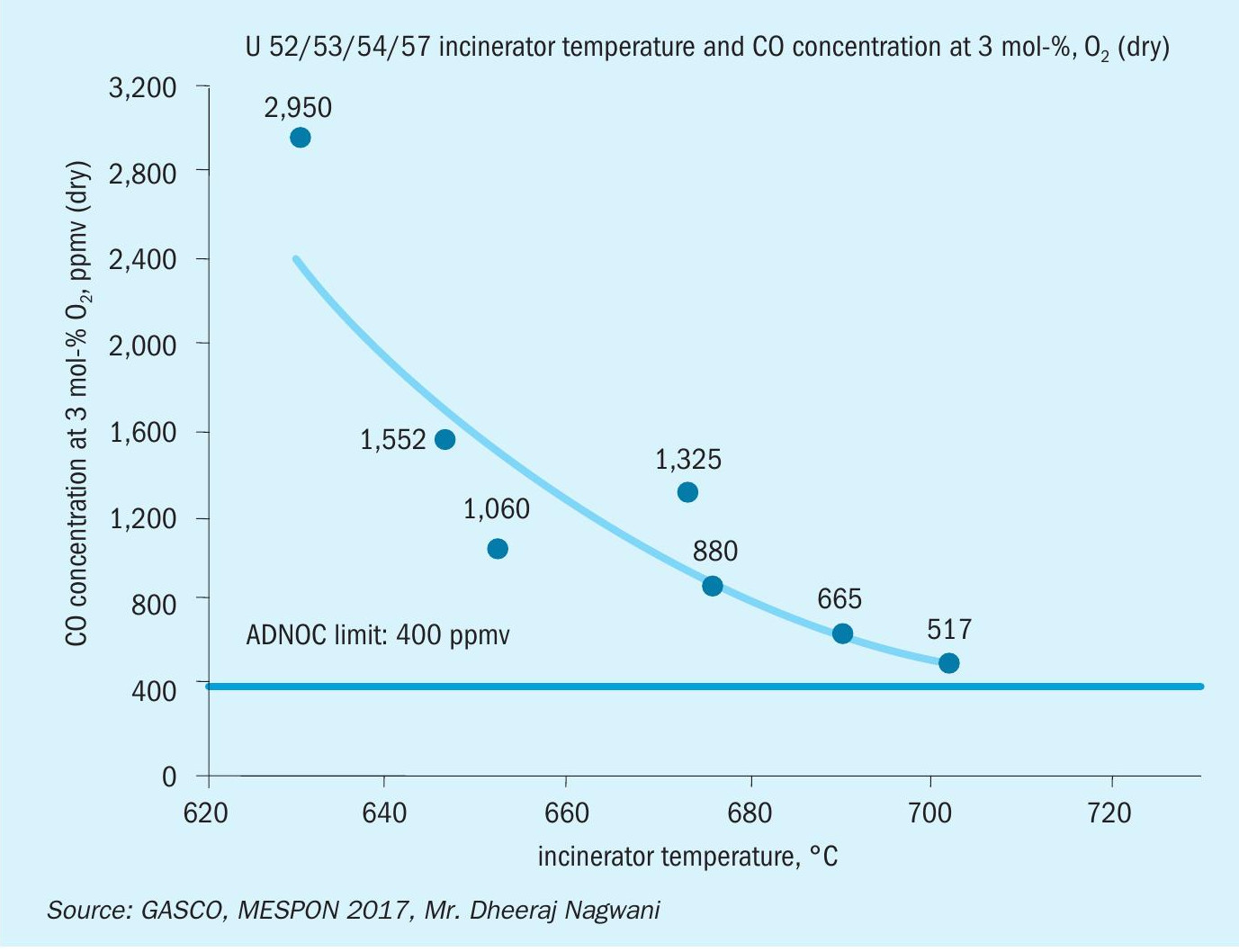
Conclusion
The various avenues to improve the performance of the SRU thermal incinerator include:
- reduce COS and CS2 load to the incinerator via specialised catalysts in the first converter;
- higher residence times in the incinerator;
- higher fuel gas firing to provide higher temperature to meet CO and other emission regulations;
- high efficiency burners; l oxygen enrichment
A VectorWall™ through its unique ability to improve mixing and front-end temperatures can supplement or even be a substitute for some of the above options, offering operational savings, lower CO2 emissions and an improved margin for operating within the specified emission regime.
References