Fertilizer International 513 Mar-Apr 2023
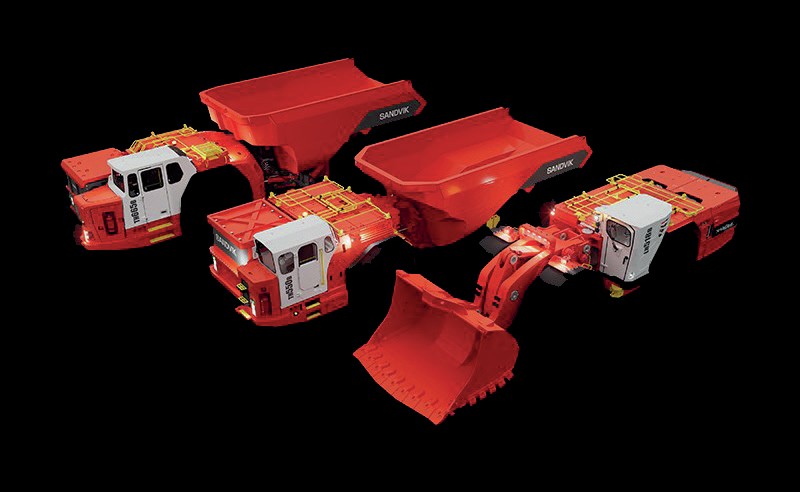
31 March 2023
New developments in potash mining and processing
POTASH TECHNOLOGY
New developments in potash mining and processing
Potash production improvements are being made in areas such as ore extraction, cooling and froth flotation. We review technological developments from Sandvik, Eriez, Nouryon and Solex Thermal Science.
SANDVIK
Sandvik wins major Jansen mine orders
Sandvik Mining and Rock Solutions has secured a major order for 10 battery-electric vehicles (BEVs) from BHP, along with one electric tethered loader, for the first phase of its Jansen potash project in Canada. These BEV loaders and other equipment are scheduled to be delivered between 2023 and 2025.
The order for battery-electric loaders, placed last June, reflects BHP’s focus on both sustainability and advanced technology for the Jansen mine. Sandvik’s BEV loaders are designed for minimal underground mining infrastructure – as they eliminate the need for overhead cranes and other heavy handling equipment.
“Electric mining equipment is essential to meeting our goals to reduce emissions, improve productivity and most importantly protect the health of our employees underground. Jansen will have the lowest carbon emissions per tonne of product produced compared to any potash mine operating today in Saskatchewan,” said Simon Thomas, BHP’s president, potash.
“We are excited to partner with BHP and proud to contribute to the sustainability and productivity of this project. Sandvik electric loaders have been designed to best utilise innovative technology of its battery pack and electric driveline, and maximise the capabilities of our battery technology,” said Alex Willows, business line manager for Sandvik Canada.
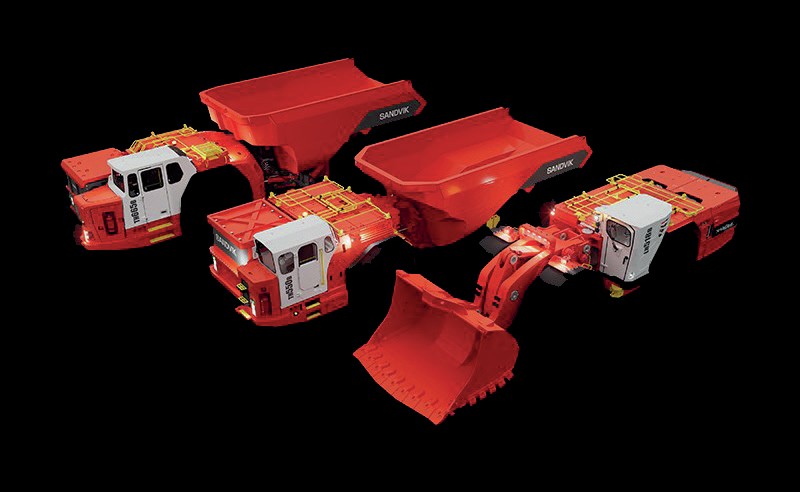
“Jansen will have the lowest carbon emissions per tonne of product compared to any Saskatchewan potash mine currently operating.”
This latest order follows a SEK 2 billion ($216 million) mining systems contract for the Jansen project won by Sandvik in February 2022. This commits Sandvik to supplying a fleet of electric, cable-connected MF460 borer miners between the third-quarter of 2023 and 2026. These borers have been especially developed for the project following several years of Sandvik-BHP collaboration.
The Jansen potash project is located around 140 kilometres east of Saskatoon in Saskatchewan, Canada. Targeting an initial capacity of 4.35 million t/a, Jansen will be world’s largest-scale and most advanced potash mine when it enters production in 2027. Once commissioned, the mine is expected to operate for up to 100 years.
NOURYON
Advances in potash mining reagents
Enhancing potash recovery
Nouryon offers innovative and individually customised flotation agents for unique ores including potash (Fertilizer International 506, p41). These deliver superior performance combined with a strong focus on sustainability. Such capabilities are possible thanks to decades of mineral processing expertise and the company’s track record of customer collaboration.
For Nouryon, environmental stewardship starts with the sustainable sourcing of bio-based raw materials. Nouryon has a broad portfolio of flotation agents for the potash industry. The company’s main potash processing products are listed in Table 1 together with their respective functions.
The use of selective collectors that efficiently make mineral surfaces hydrophobic – and therefore susceptible to separation – is critical for successful flotation. To this end, Nouryon has designed and developed several collectors suitable for diverse potassium-bearing minerals and conditions. Many of these are based on fatty amine technology, one of Nouryon’s core areas of expertise.
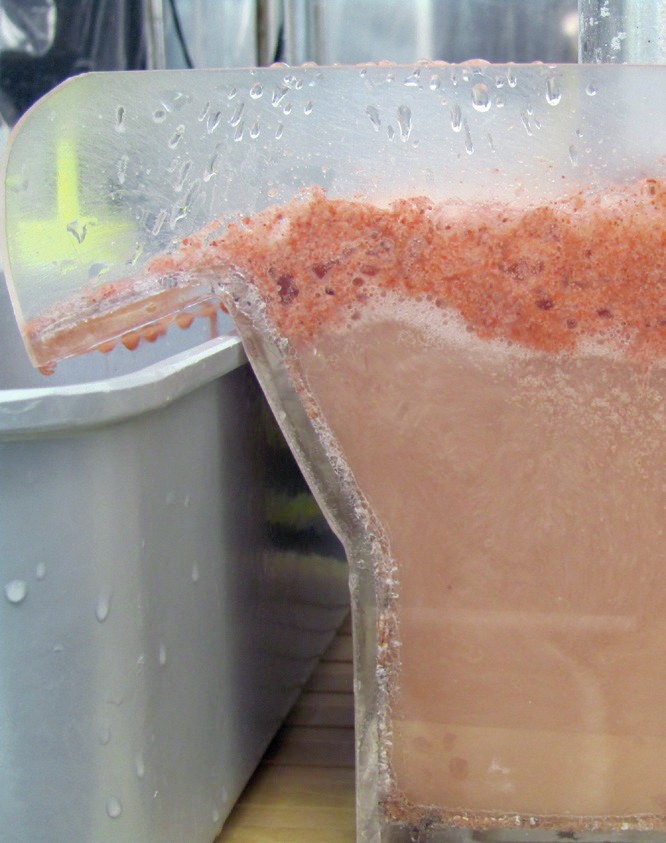
“Our collectors can efficiently balance recovery and selectivity during the flotation of sylvite from sylvinite in MOP production across a variety of ore types, brine compositions, and process temperatures,” says Henrik Nordberg, global section manager for mining at Nouryon.
Figure 1 illustrates the performance of amine blends used in potash flotation.
Reverse flotation for halite removal
Nouryon’s Armoflote® 619 collector is unique, as it enables the successful reverse flotation of halite (sodium chloride) from carnallite (a potassium chloride and magnesium chloride mixture) and other double salts such as schoenite (a mixture of potassium and magnesium sulphates). In reverse flotation, the unwanted gangue mineral is floated while the valuable mineral remains as the bottom product. When used as collector in carnallite flotation, Armoflote619 exhibits an impressive ability to remove halite from the valuable potash-bearing mineral (Figure 2).
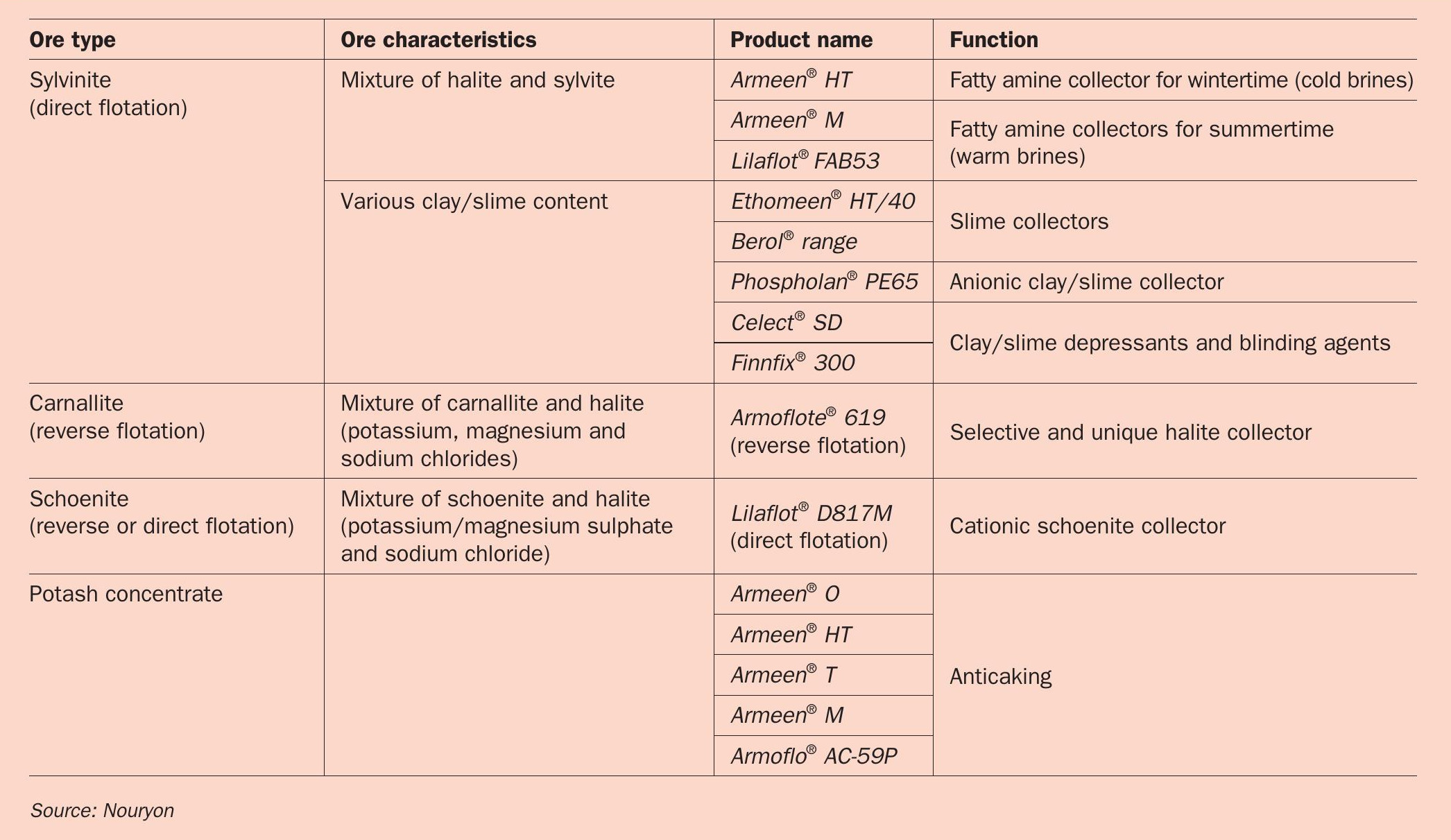
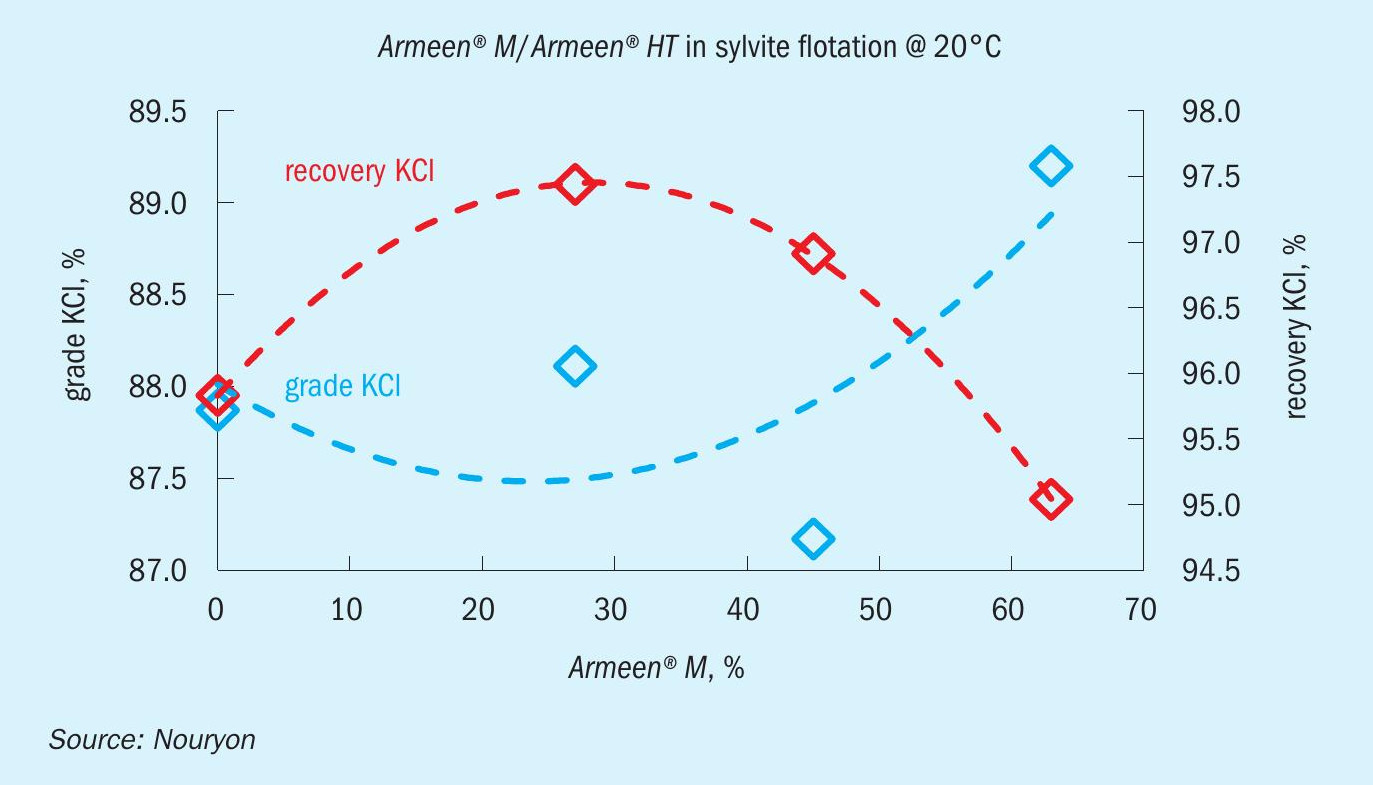
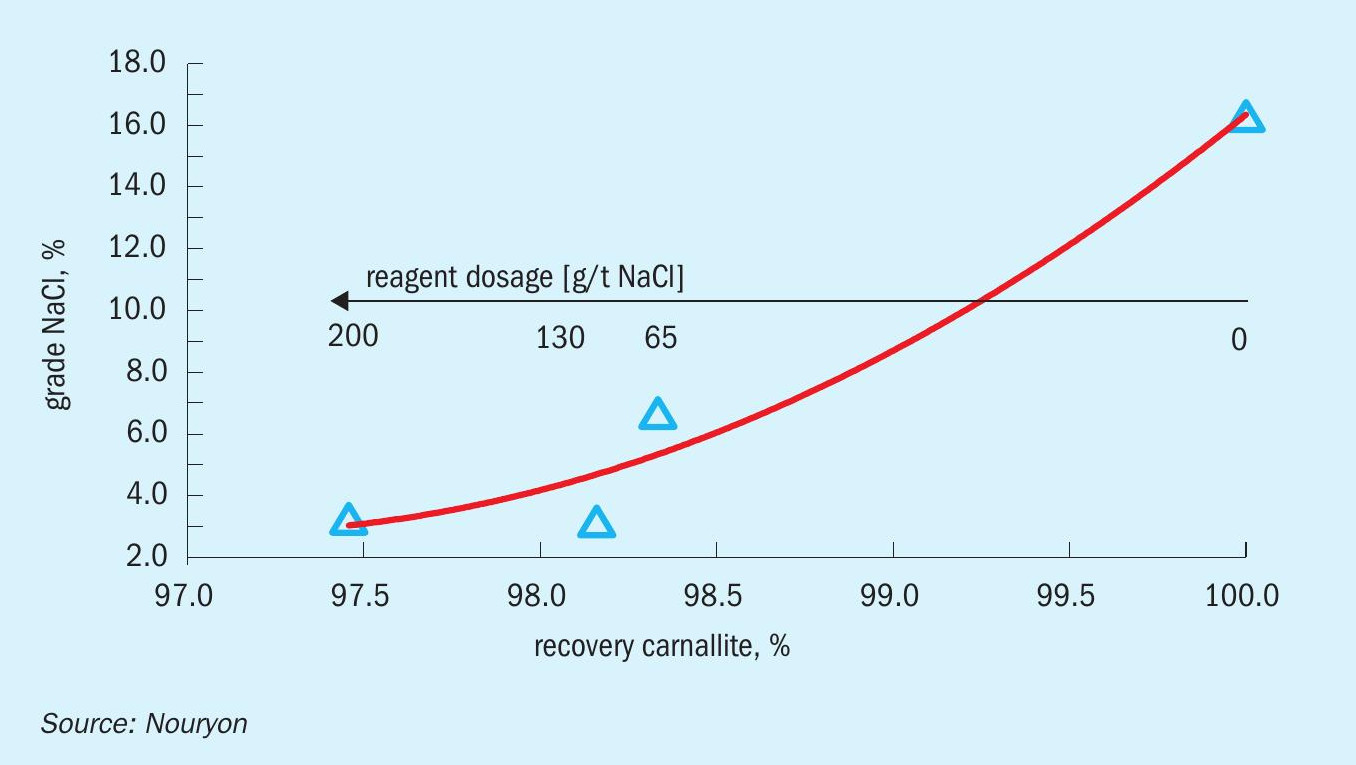
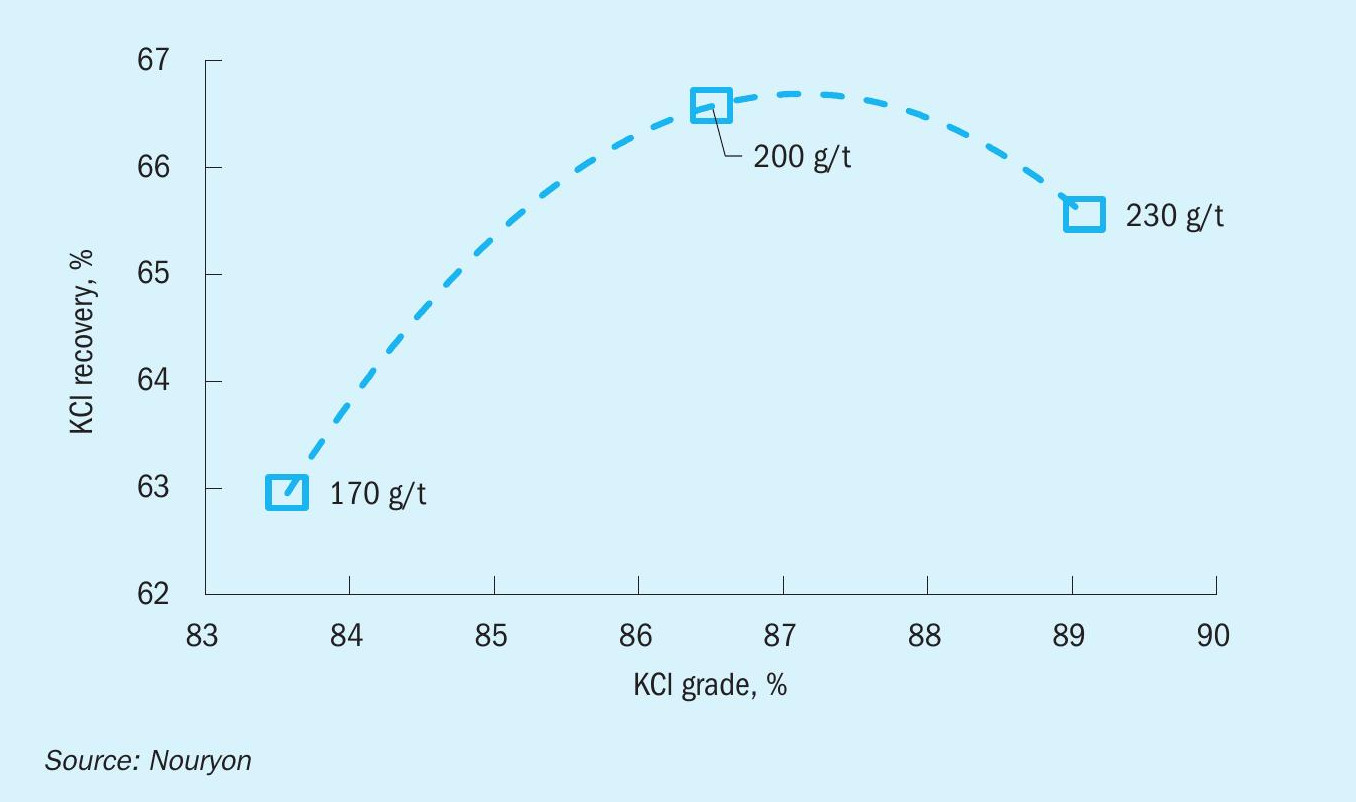
Removal of slimes
Certain potash ores contain clay minerals in addition to the salt minerals that typically occur. These fine clay particles – also known as slimes – negatively impact potash flotation due to their high charge and high surface area. This prevents separation by depleting collector concentration. Solutions to this problem include:
- Mechanical desliming using hydro separators and cyclones
- Physico-chemical separation via slime flotation or the use of a depressant that blocks slime surfaces from interfering with sylvite flotation.
Of these two options, physico-chemical separation via flotation is usually preferred, since mechanical desliming causes the loss of fine potash particles, while total potash recovery can also be improved through selective reverse flotation of the slimes. A range of products demonstrates Nouryon’s proficiency with slime collectors. These include Ethomeen® HT/40 and Berol® non-ionic collectors as well as the Phospholan® PE65 anionic collector.
Nouryon is also a leading global manufacturer of carboxymethylcellulose (CMC) depressants (Celect® and Finnfix® ) for mining applications. This enables the company to maximise recovery grade profiles for its customers by offering holistic and individually tailored flotation options. CMC, a bio-based anionic polymer, functions as an efficient depressant in the flotation of a wide variety of minerals, including potash. CMC optimises sylvite recovery (Figure 3) by ensuring that flotation collectors are fully adsorbed on the surface of the target mineral by ‘blinding out’ the active surface area of clays.
Potash coating
Once successfully separated via froth flotation, the high quality potash concentrates obtained need to be prepared for storage and transportation. This is usually achieved by applying a mineral coating, typically an anticaking agent, to prevent potash adsorbing water and becoming lumpy and sticky. Nouryon offers a range of anticaking agents (Armeen® HT, Armeen® T, Armeen® O, Armeen® M, and Armoflo® AC-59P) which use fatty amine technology to preserve potash concentrates in their desired form until they reach their ultimate destination.
SOLEX THERMAL SCIENCE
Potash cooling – the decarbonisation challenge
Raw bulk materials go through numerous steps while being transformed into valuable products. Yet these steps often require emissions-intensive equipment and high energy inputs – which carry considerable operational costs.
Such equipment creates a dilemma for today’s fertilizer producers who, as they seek to minimise the environmental impacts of their operations, require scalable and low-cost options for decarbonising production. These low-carbon production options also need to achieve a high return on investment while still delivering high-quality final products.
In December 2015, 196 countries famously adopted the Paris Agreement, the central aim of which was to limit global temperature rise to 1.5°C above pre-industrial levels by 2030. However, late last year, the UN Environment Programme (UNEP) reported that, to meet Paris Agreement commitments, a cut in global annual greenhouse gas (GHG) emissions of 45 percent was still necessary, compared with emissions projections under policies currently in place. These reductions also need to be accomplished in less than eight years. This represents a mammoth challenge, particularly for energy-intensive industries such as fertilizer production.
Potash producers take action
For the potash sector, this struggle is playing out in real time. Potash producers have already acted – or are committed to firm future targets – to improve their energy efficiency, reduce their operational carbon intensity and make the transition to renewable energy. The industry is also exploring the potential for capturing production emissions using carbon capture and storage (CCS) technology.
Despite this, many common pieces of production technology that are still in place in the potash industry today are actively working against the sector’s carbon-cutting efforts. The cooling stage being one example.
During its processing, potash must be cooled to a specific temperature – typically 50°C or lower – before it can be safely stored and transported. Yet traditional direct-contact (e.g., convection) cooling equipment, such as fluidised beds and rotary drums, require large energy inputs to get the job done and can also generate significant dust and GHG emissions.
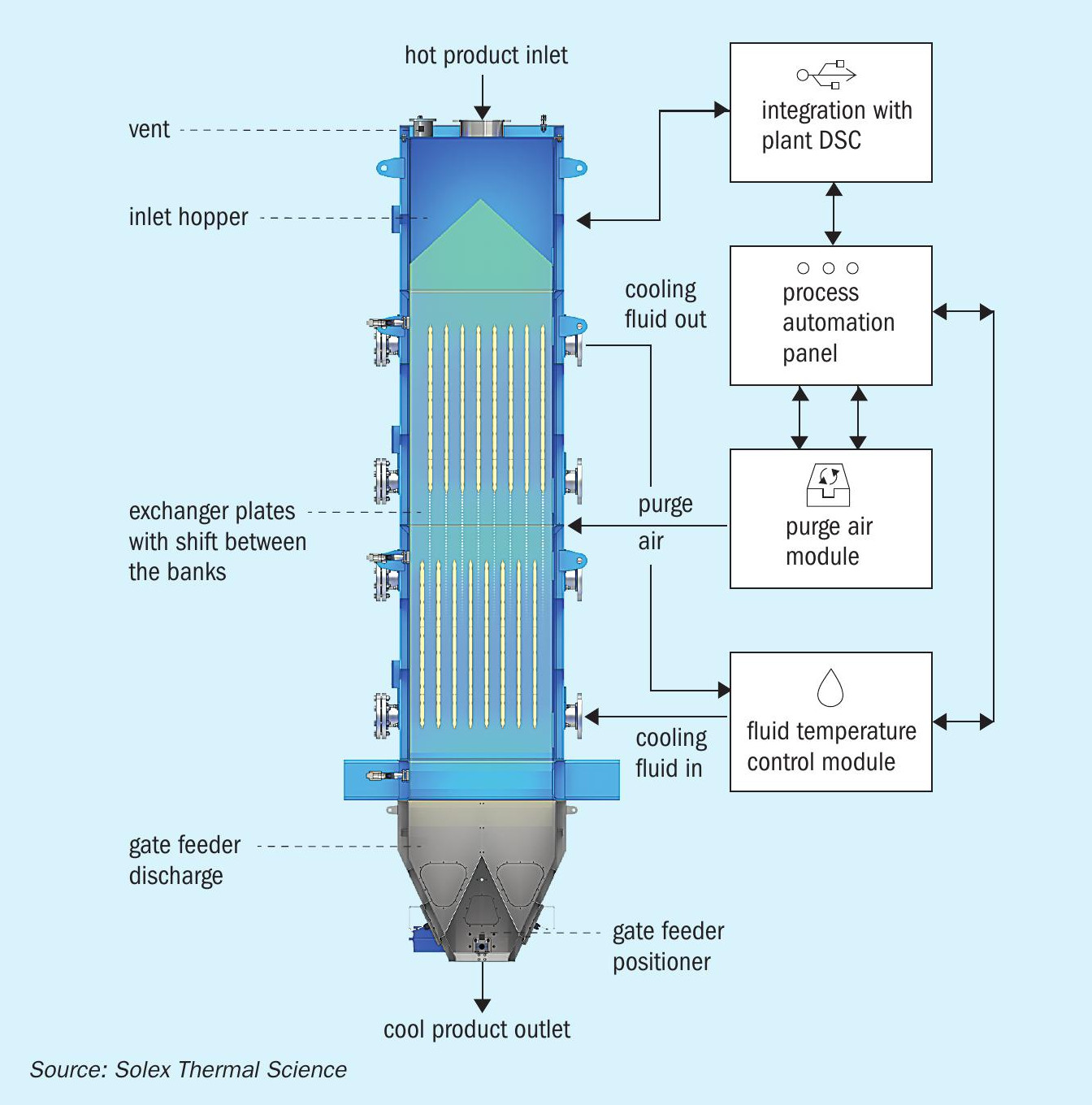
Moving bed heat exchangers (MBHEs) based on vertical plate technology are emerging as an increasingly popular cooling equipment choice within the fertilizer industry. This is particularly true for those potash producers who are looking to improve the overall energy status of plant operations, cut dust emissions and reduce their carbon footprint, while still producing a high-quality product.
In fact, MBHEs have been proven to reduce energy demand at the cooling stage to one tenth of normal. Also, new advances in MBHE processes now provide potash producers with the ability to recover energy at the cooling stage for use elsewhere in the plant. This reduces fossil fuel consumption further and delivers extra energy savings that translate into reduced GHG emissions.
The advantages of MBHEs
One of the biggest differences between plate-based MBHEs and direct-contact alternatives is how heat transfer occurs. With MBHEs, potash enters through the top of unit and flows by gravity through banks of parallel vertical stainless-steel plates. At the same time, a heat transfer fluid – typically water – passes through the plates to cool the potash by conduction (Figure 1).
This passive, indirect form of heat transfer – the flow velocity of the potash is typically less than 0.3 m/min – means MBHEs do not contribute to any additional dust emissions or the degradation of potash granules. In contrast, fluidised beds operate by forcing air through the solid material within the fluid bed. Rotary drums, meanwhile, rotate and lift the potash through a counter-current air stream.
Both these direct-contact methods involve a lot of agitation and can therefore cause abrasion, attrition and dust emissions. Critically, they also require high-horsepower blowers, ducting and associated air-handling and -cleaning equipment to circulate the air and then clean it before it can be discharged to the environment. Heat recovery from these air streams is generally not technically or economically viable, so the thermal energy is simply lost to the environment.
MBHEs, meanwhile, do not use air to get the job done, and therefore do not need these ancillary pieces of equipment. The associated savings are therefore substantial.
In a standard 75-tph cooling system, for example, a plate-based MBHE requires only 90 kW of installed power (Figure 2). By comparison, a rotary drum needs 365 kW and a fluidised bed 612.5 kW. Annually, based on 8,000 operating hours and $0.17/kW, it costs just $122,400 to operate a plate-based MBHE, compared with $496,400 and $833,000 for a rotary drum and fluidised bed, respectively.
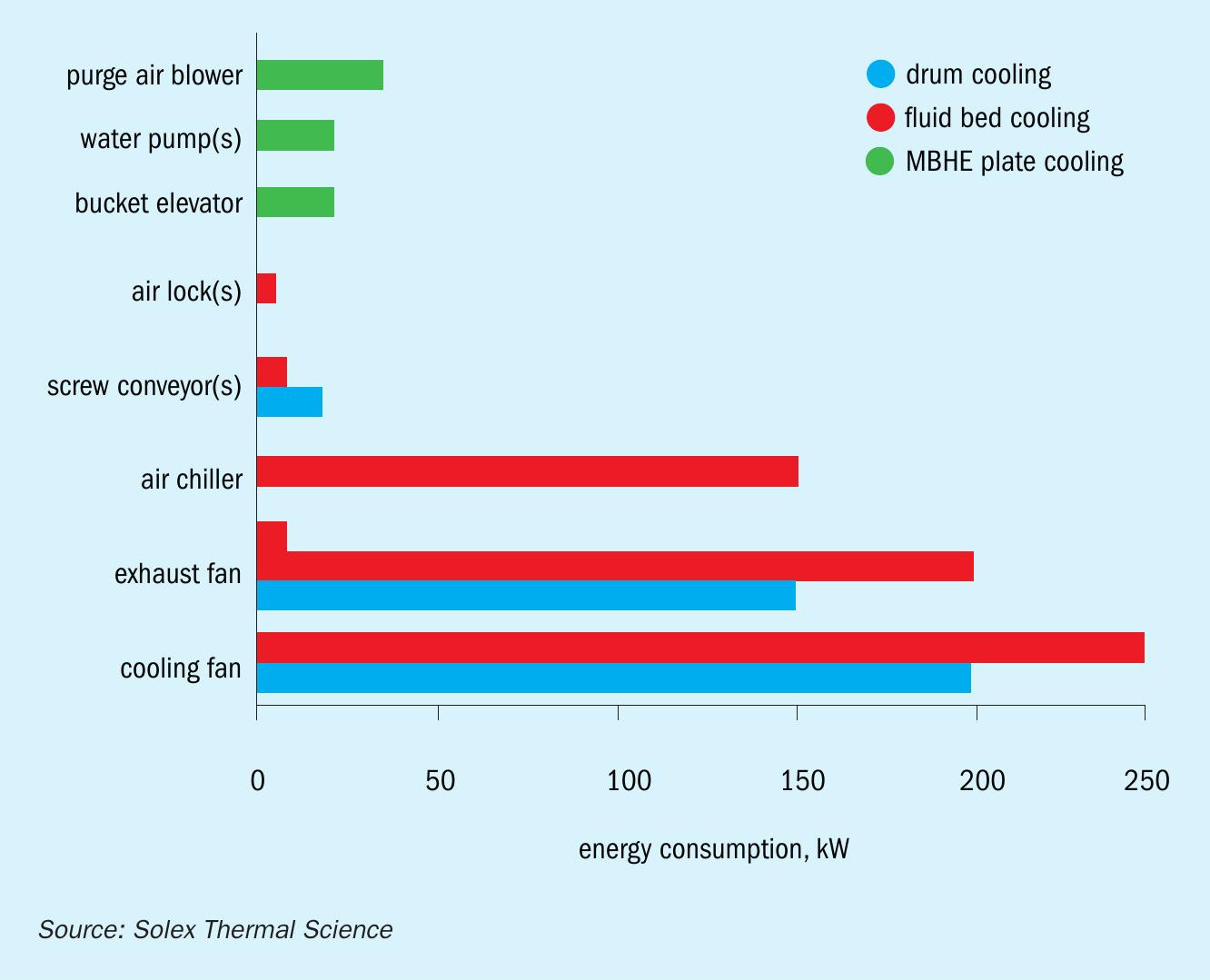
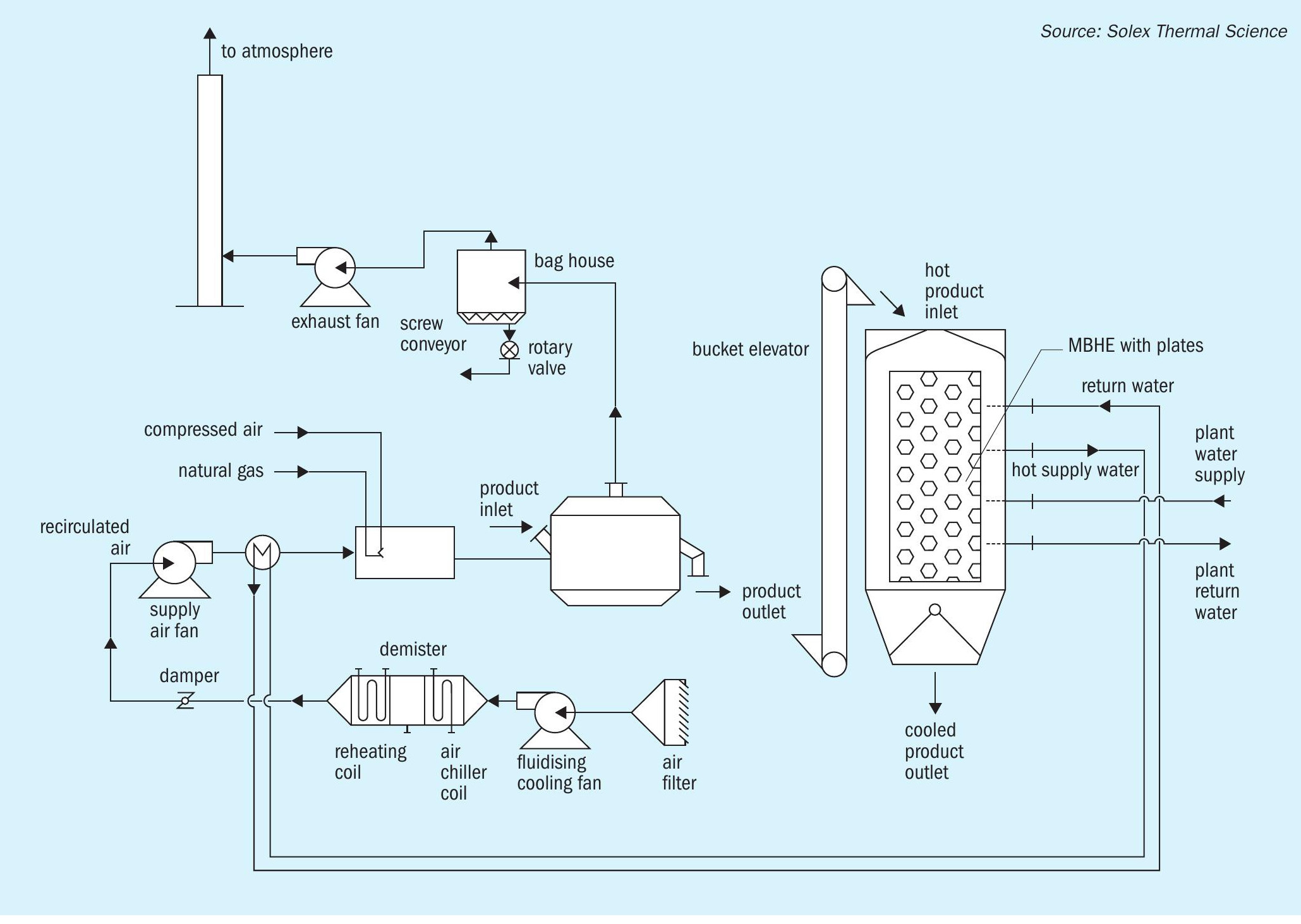
By cutting energy consumption, potash producers also have an opportunity to reduce CO2 emissions. Based on 0.19 kg of CO2 e per kW, the carbon footprint of a plate-based MBHE is 138,960 kg – compared with 563,560 kg for a rotary drum and 945,700 kg for a fluidised bed.
Capture of low-grade thermal energy
Furthermore, during cooling, MBHEs produce a hot transfer fluid that can provide low-grade thermal energy for use elsewhere in the plant. This can be converted to hot air using a finned-tube heat exchanger and then ducted to various points for end-use.
One upstream use for this recovered low-grade thermal energy is the pre-heating of combustion air, via an air-to-fluid preheater, for equipment such as a fluid bed dryer (Figure 3) or rotary drum dryer. This, in turn, can significantly cut natural gas consumption, further reducing both energy costs and the plant’s carbon footprint.
“During cooling, MBHEs produce a hot transfer fluid that can provide low-grade thermal energy for use elsewhere in the plant.”
The cooling of the transfer fluid, via the finned-tube heat exchanger, also reduces the load on the plant’s cooling water system. This working fluid requires only minimal cooling as it is returned to the water module at a temperature well below 70°C.
Conclusion
In its report last year, the UNEP notes that many industrial sectors already have the necessary technology to hit their GHG emissions reduction targets. What’s needed instead is a more robust audit to identify whether all the equipment still in place can deliver on these targets. If not, a rapid transition to equipment that that can deliver on energy and climate targets will be necessary.
In the case of potash cooling, moving bed heat exchangers (MBHEs) based on vertical plate technology are providing potash producers with the necessary means to reduce their emissions. By design, MBHEs are a near-zero-emissions, low-energy cooling option – one that has been proven to reduce the carbon footprint of operations around the world. What’s even more exciting is how recent improvements in MBHE technology are helping to further decarbonise operations – by using a new waste heat recovery process that can cut natural gas consumption.
Fertilizer production technology will undoubtedly need to improve and do more in future – to align with companies’ ESG commitments and allow plant operators to make changes that positively affect the world around us. By moving to near-zeroemissions equipment and recovering waste heat, potash producers now have a real opportunity to move closer to achieving their shared climate ambitions.
ERIEZ FLOTATION
Flotation innovations unlock value at potash mines
As global demand for fertilizers continues to grow and geopolitical events disrupt supply from Russia and Belarus, operators are focused on finding innovative ways to improve efficiencies for new and existing potash mines.
Flotation is a critical step in the potash production process as it removes impurities from the ore to achieve commercial concentrate grades required for fertilizer production.
Historically, most potash mines employ conventional mechanical flotation technology with several stages of cleaning and scavenging to achieve acceptable product grades and recoveries. In some cases, where potash can be liberated from gangue minerals at coarse sizes (i.e., +3-mm), separate coarse and fine flotation circuits have been designed to improve flotation performance. Nonetheless, legacy technologies for particle classification and flotation present inherent challenges to efficient and low-cost production of potash.
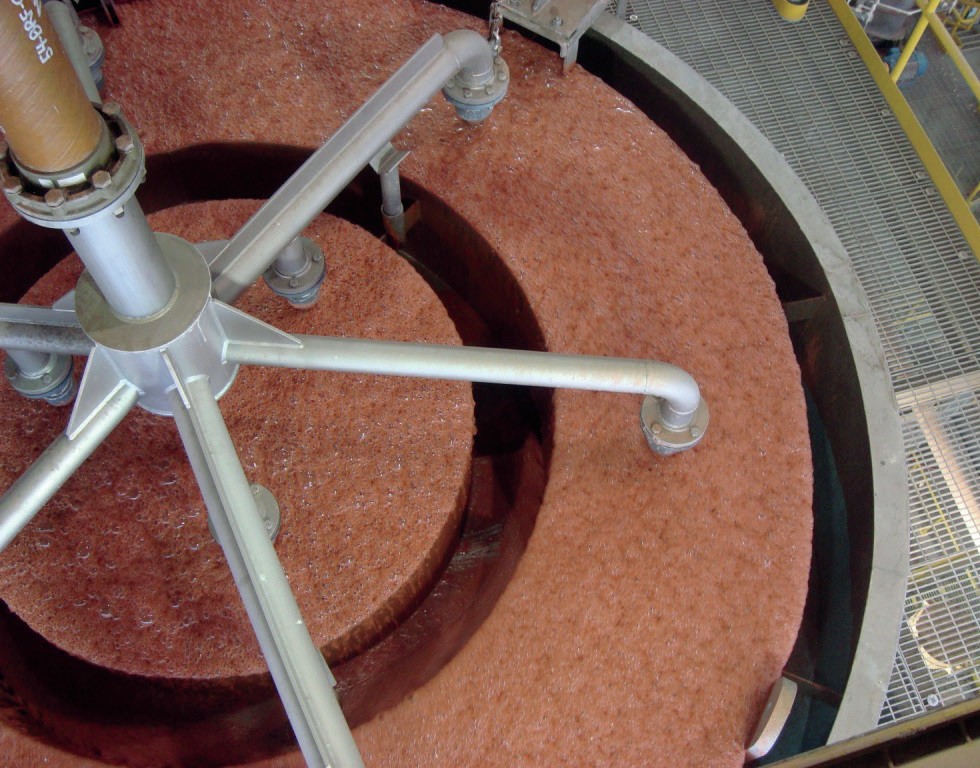
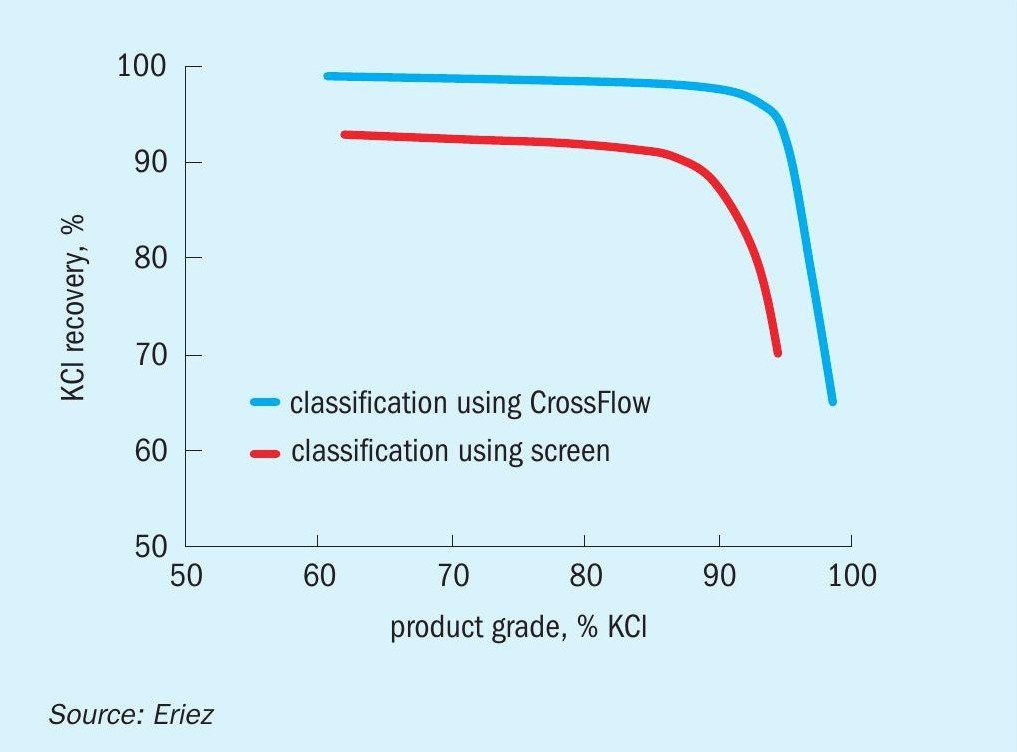
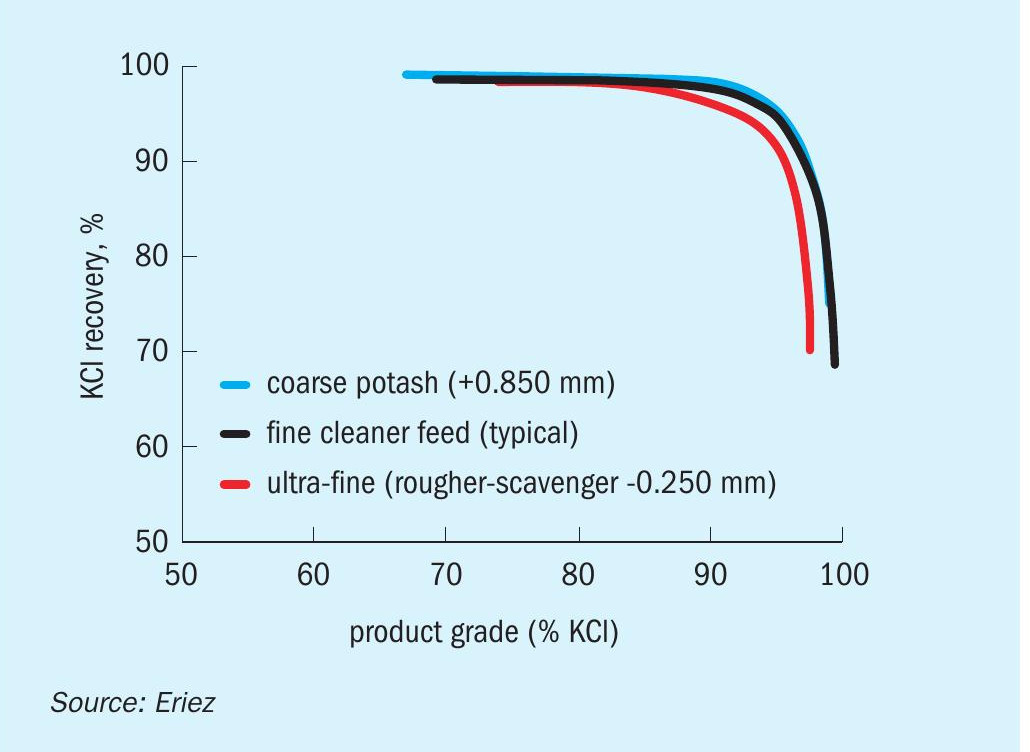
Eriez CrossFlow separator
The CrossFlow® is a teeter-bed classification technology that replaces vibrating screens and cyclones in potash processing to:
- Enhance sizing efficiency
- Prevent fines bypass
- Reduce the plant’s footprint.
Due to its inherent water split, the Cross-Flow separator minimises misplaced material that occurs in screens and cyclones due to inefficient washing or overloaded conditions and underflow bypass. Misplaced material can significantly impact the flotation process, negatively affecting final product grades and recoveries. The CrossFlow separator’s high efficiency mitigates this issue, resulting in minimal or no misplaced material, within coarse or fine flotation feedstocks (Figure 1).
Eriez CavTube column flotation
CavTube® column flotation cells have been successfully implemented to improve the flotation of fine potash by:
- Increasing bubble surface area flux
- Developing a deep froth phase
- Enabling the use of counter-current wash brine to remove impurities from the froth concentrate.
The high air rates and stable froth phase formed using these cells ensures both high recovery and also a high-grade product that can exceed 95 percent KCl (Figure 2). Fine effluent streams are also best treated using the CavTube system. Accept- able recovery (95%) and grade have (+90% KCl) been obtained in either a rougher-only or rougher-scavenger configuration.

Eriez HydroFloat separator
The HydroFloat® is an air-assisted teeter-bed separator used in potash processing to enhance the selective recovery of coarse particles up to 4-mm in size. In conventional mechanical flotation cells, flooding the cells to improve coarse particle recovery results in poor product grade as gangue minerals unselectively report to the concentrate. Whereas the HydroFloat’s fluidised bed decreases turbulence and detachment, while improving the flotation rate of the coarsest material. As a result, the HydroFloat achieves over 95 percent KCl recoveries during coarse particle flotation while maintaining concentrate grade targets of more than 90 percent KCl.
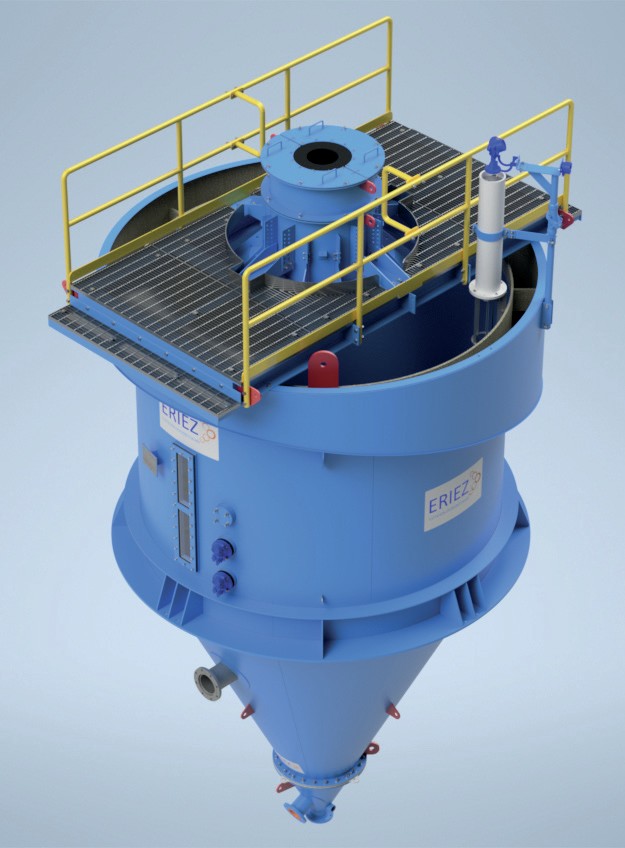
Project experience
The success of the CrossFlow, CavTube Column, and HydroFloat in retrofit and expansion projects has led to the implementation of these innovative technologies at the largest greenfield potash project in the world. As operators seek innovative methods to maximise the use of natural resources, optimise costs, and reduce environmental impacts of their operations, Eriez serves as a partner to unlock existing value through process optimisation.