Nitrogen+Syngas 383 May-Jun 2023
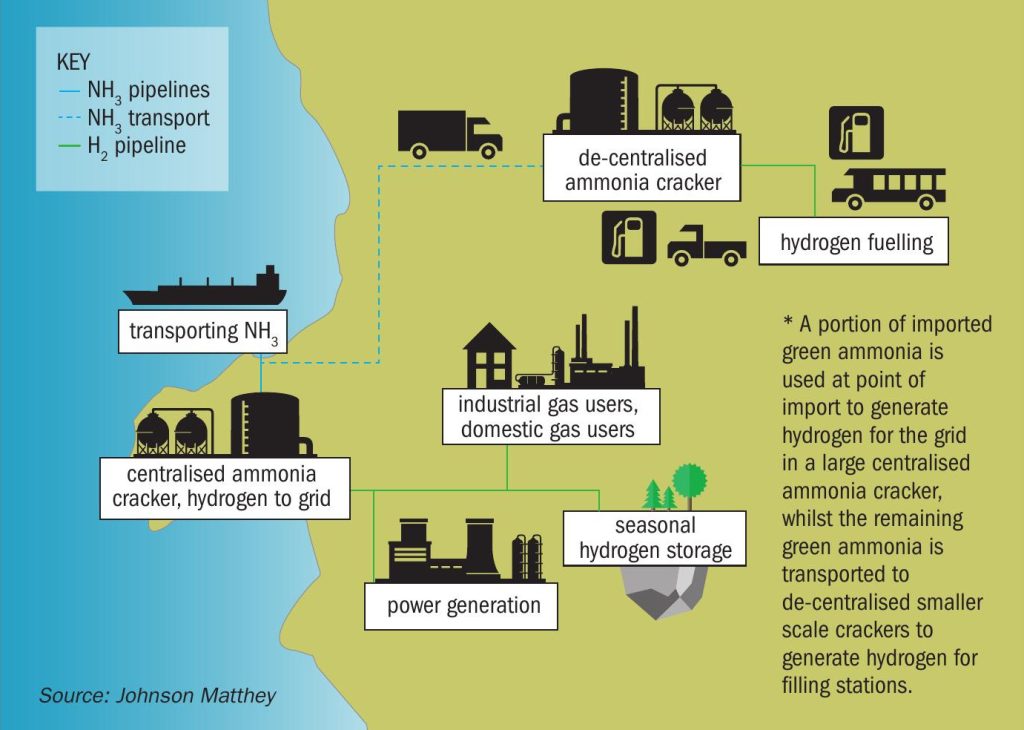
31 May 2023
Converting clean ammonia back into hydrogen
AMMONIA CRACKING
Converting clean ammonia back into hydrogen
Advances in clean hydrogen and ammonia production is fuelling worldwide interest in a new market for hydrogen and ammonia to provide a reliable low-carbon energy future. Ammonia cracking, the dissociation of ammonia back into hydrogen, delivers a pathway to large-scale sustainable hydrogen production. In this article KBR, Johnson Matthey, thyssenkrupp Uhde, Duiker, Proton Ventures and Casale report on their technologies and approaches to ammonia cracking in a low carbon economy.
The world is facing an incredible challenge in the race to decarbonisation, imposing a change of landscape in the technologies and fuels used to support sustainable modern-day life in the future.
The journey towards Net Zero by 2050 requires double digit trillion dollars investment in technologies and infrastructure for low carbon fuels and electrification.
Both hydrogen and ammonia are predicted to play a major role in this journey, to support the decarbonisation of industries and regions which are either hard or uneconomical to electrify. Clean hydrogen is taking a leading position as a sustainable fuel of the future, while ammonia can serve as a clean fuel on its own or as a carrier of hydrogen.
The majority of these key molecules are expected to be produced via renewable power and electrolysis, often designated green, but a significant share will be produced via reforming of fossil fuels and carbon capture, often designated blue, as a cost-effective first step to a sustainable future.
Ammonia as an energy vector
Ammonia is the most promising clean hydrogen carrier for long distances in the short to medium term.
Advantages
Ammonia has a high hydrogen storage density and can be liquefied at -33°C at atmospheric pressure, providing a low energy intensity means of hydrogen storage and transportation. Ammonia production technologies are mature and efficient, already operating at large scale. Ammonia can rely on well-established and rapidly advancing infrastructure for storage, loading, unloading and transportation. Both ammonia production and transportation are already expanding to the growing demand for ammonia as an energy vector. An additional advantage of ammonia is that it can be used directly as fuel, such as in co-firing with coal, helping to abate existing coal-based power plants.
Safety
Ammonia toxicity is similar to other hydrogen carriers such as methanol, methylcyclohexane (MCH) and toluene. Ammonia may be a toxic chemical, but one that is already produced, stored and transported safely around the world today. It is harmful to health at concentrations in excess of 400 ppm but its odour is an advantage in leak detection, with the pungent smell of ammonia in the air detectable at concentrations as low as 5 ppm. It is lighter than air, so it rapidly diffuses and oxidises on leakage making inhalation or contact less likely. Ammonia flammability is lower than other hydrogen carriers, with a high auto-ignition temperature of 650°C, rendering it safer to transport.
Comparison to other hydrogen carriers
The ammonia carrier value chain has the lowest levelised cost and carbon intensity, with energy output similar to liquefied hydrogen. Today, liquid hydrogen is limited by the liquefaction step, with train capacities ~30t/d limiting the ability for vessels to scale past 10,000 m3 . Methanol is constrained due to its need for carbon capture, utilisation and storage while MCH has significantly higher cost and carbon intensity, with lower energy output and technology readiness.
The ammonia dissociation reaction
Ammonia decomposition is an endothermic reaction (1), needing 46 kJ for one mole of ammonia to dissociate into nitrogen and hydrogen.

Thermodynamically, equilibrium is favoured by high temperature and low pressure. Theoretically, the reaction is near completion:
- at > 550°C @ 1 bara
- at > 800°C @ 5 bara
- at > 1,000°C @ 30 bara
Catalysts can be used to improve the rate of reaction and lower reaction temperature, improving the efficiency of the ammonia cracking process. Both base and precious metals can be used to promote the reaction, with nickel-based catalysts in successful commercial operation today.
KBR
From clean energy source to sustainable hydrogen supply
As a technology powerhouse with decades of know-how in efficient ammonia processes and reliable equipment design, coupled with market proven capability for scale-up and commercialisation, KBR offers technologies across the full sustainable hydrogen and ammonia value chain, completed by the advent of KBR’s ammonia dissociation technology, H2ACTSM (Fig. 1).
H2ACTSM new market, established technology
Today, ammonia dissociation technology is available in the market serving a different purpose. The installed units are fully electricity driven, very small capacity and operate at equilibrium-favoured conditions (low pressure, high temperature) to supply hydrogen or nitrogen as utilities in remote locations and without emphasis on energy efficiency or carbon intensity. While these units serve the installed purpose, they are not suitable for what industry is demanding for energy transition, with new technology required to produce at larger scale, sustainably and efficiently.
While the market for ammonia dissociation for decarbonisation is new, the technology elements to dissociate ammonia at scale are established and proven in operation, bearing great resemblance to steam methane reforming of natural gas for syngas generation.
KBR’s ammonia cracking technology, H2ACTSM , is built on a legacy of technology innovation and industry records in ammonia production. It completes the pathway to large scale, sustainable hydrogen production, with efficiency and high technology readiness at the heart of the process.
Process flow scheme overview
In a typical ammonia cracking unit, liquid ammonia from storage is pumped to the required pressure, vaporised and preheated in preparation for decomposition to hydrogen and nitrogen.
Ammonia cracking is largely driven by a fuel-fired cracker, leveraging on decades of KBR experience in furnace design in industrial steam methane reforming. The furnace design is based on the well-proven KBR down-fired primary reformer design with hundreds of references from small to large scale capacity and decades of experience and know-how in robust, safe and efficient design of this equipment.
The cracking reaction is performed under the presence of catalyst with heat supplied by combustion of clean fuel via the down-fired burners. The heat source for the cracker is fuel from the process, consisting of tail gas from the hydrogen purification section, supplemented by cracked gas (H2 /N2 ) if necessary.
The ammonia cracking furnace is designed to attain maximum thermal efficiency by utilising process waste gases as part of the fuel, as well as by recovering heat in the convection section from the flue gases, to drive dissociation, feedstock vaporisation and preheat.
The furnace convection section is furnished with a selective catalytic reduction (SCR) system as standard, able to meet the most stringent environmental emission requirements.
Cracked product purification, where necessary, is based on well-proven and commonly used industrial processes:
- Ammonia recovery: Remove ammonia by simple water-based ammonia absorption/distillation unit – designed and in operation in a multitude of KBR ammonia plants worldwide;
- Product purification: Remove nitrogen by Hydrogen PSA technology – proven, reliable cost-effective and used in a variety of industries.
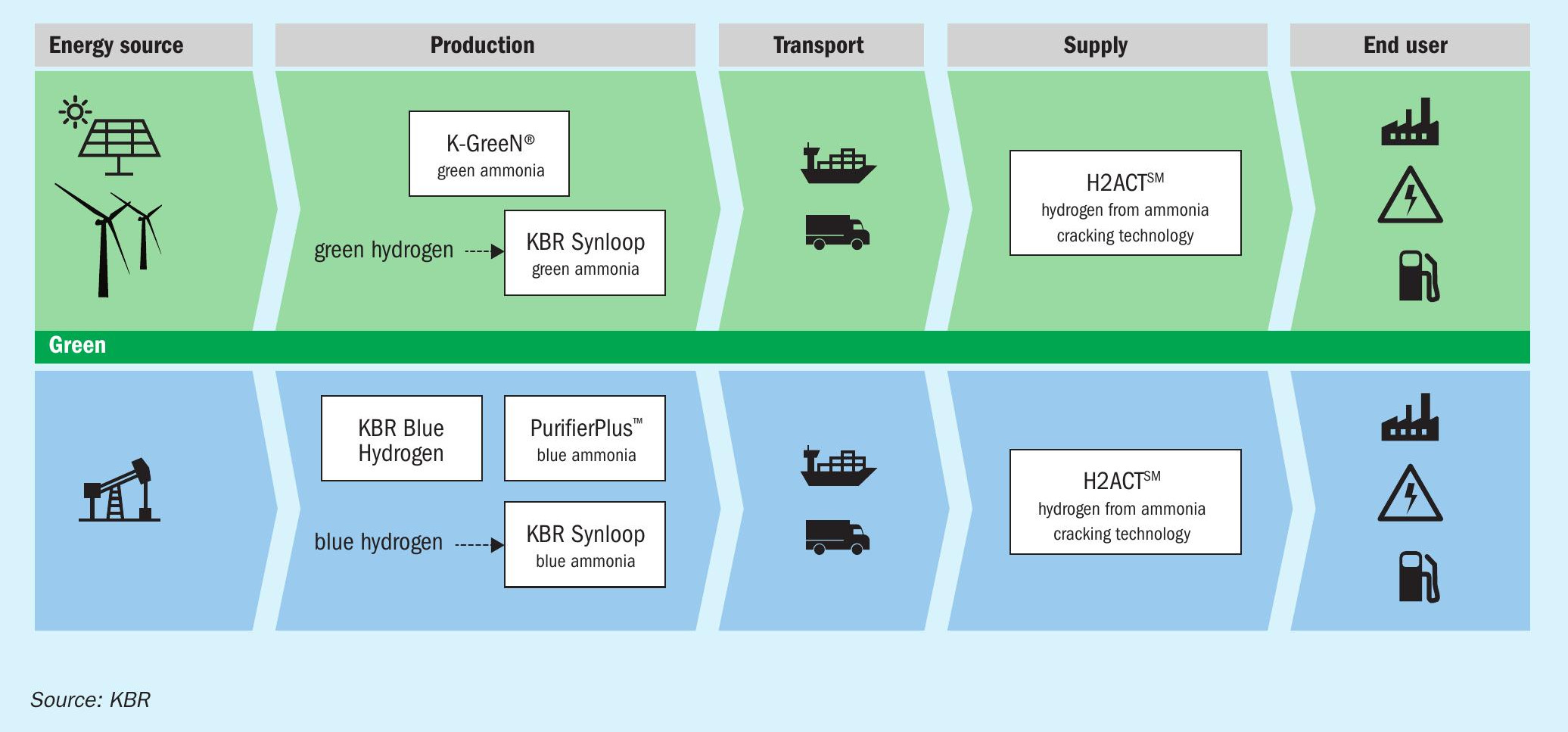
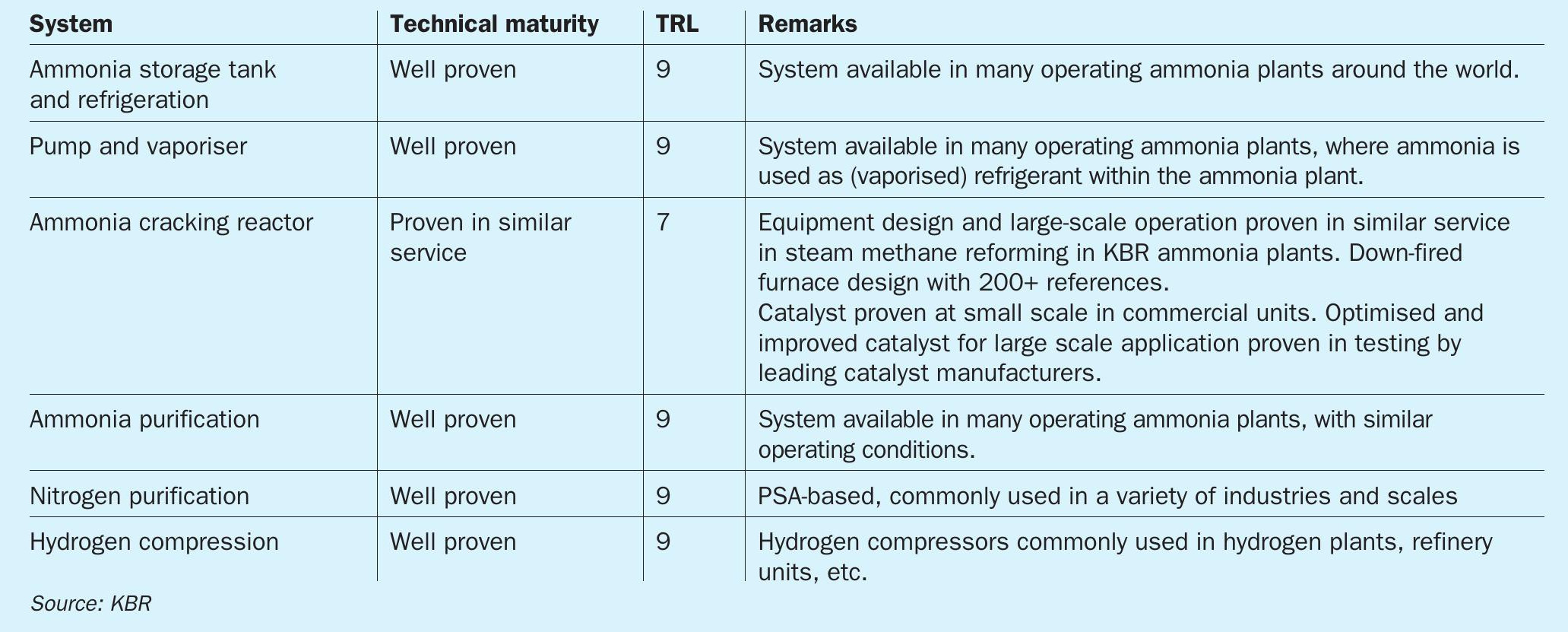
Typical hydrogen delivery pressure of around 30-40 barg is achievable without additional hydrogen compression. If higher delivery pressure is required, compression can be added, and the flow-scheme will be optimised for the higher delivery pressure.
Technical maturity level
Table 1 presents an evaluation of the technical maturity for each system (block) within the H2ACTSM ammonia cracking plant.
Key performance data
H2ACTSM can deliver hydrogen at any purity required depending on the industrial application the ammonia cracking plant is serving.
Key performance indicators such as efficiency, hydrogen yield and levelised cost of production will vary depending on the industry the cracking unit is serving, carbon intensity requirements and opportunity for integration with existing facilities.
Nonetheless, for a given application, the performance of the H2ACTSM ammonia cracking plant is consistently maintained across the entire capacity range, from small to mega-scale production.
Indicatively, Table 2 presents typical performance for an H2ACTSM ammonia cracking unit, based on zero direct carbon intensity production, using only proven technology elements (i.e., using most proven commercially available nickel-based catalysts, no ammonia co-firing, conventional PSA unit, etc).
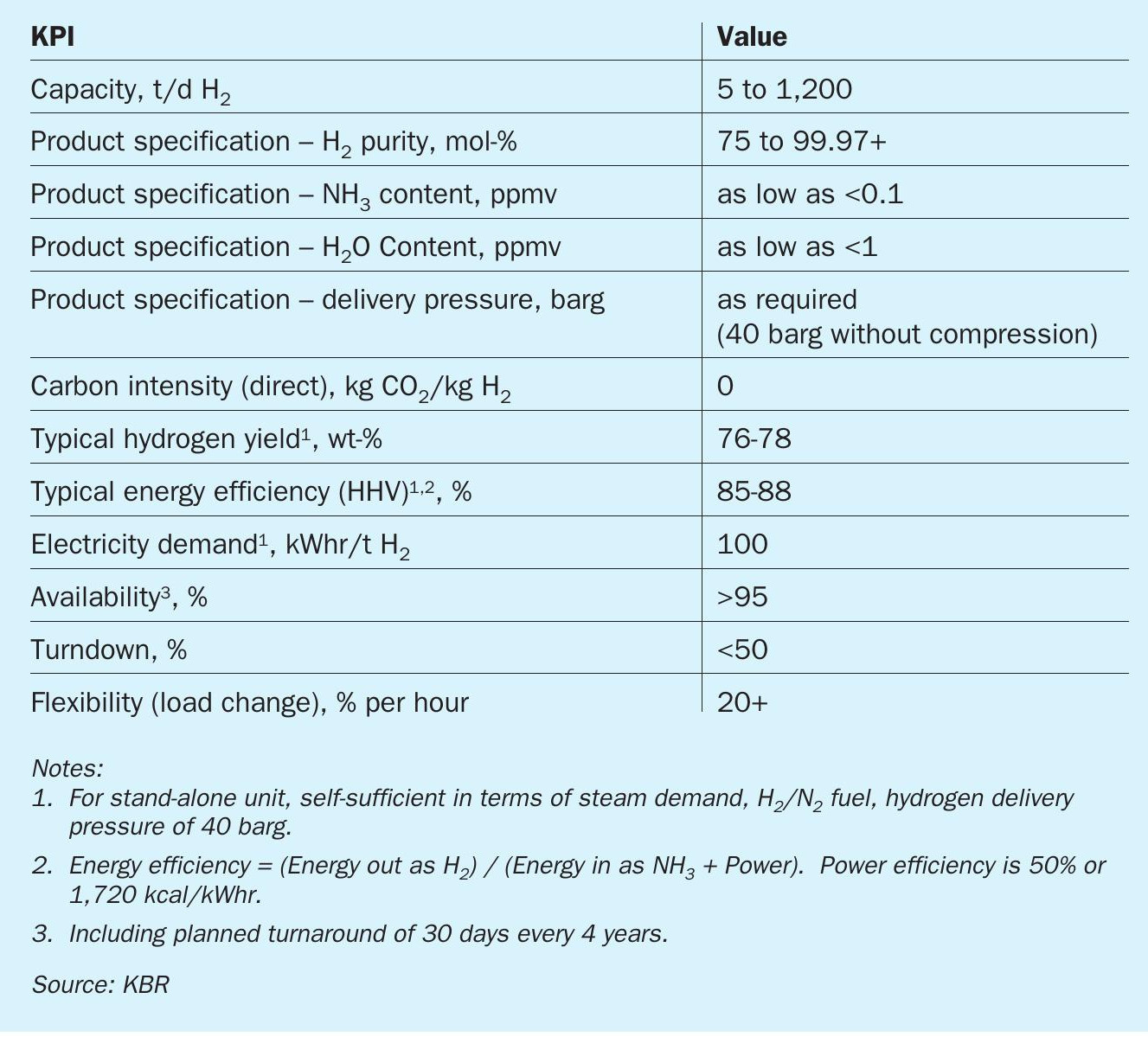
Flexibility and turndown
The typical turndown capacity for the H2ACTSM cracking unit is 50%, however the plant can be designed to be operated at lower turndown if necessary.
The typical ramp-up/ramp-down rate is 20% per hour, suitable for most industrial applications. The plant load can vary frequently and daily between nominal capacity and turndown without adverse impact on plant integrity. This can be improved significantly if additional operational flexibility is required (e.g., for power generation industry) to match offtaker variability, minimising or eliminating hydrogen storage requirements.
On-stream time, reliability and availability
KBR ammonia plants are among the most reliable in the industry, with records in on-stream time. As compared to an ammonia production facility, nearly all critical equipment in the ammonia cracking plant operates at milder conditions. The ammonia feedstock quality is consistent, without catalyst poisons such as sulphur or chlorides and no side reactions. Hence, maintenance and replacement costs are expected to be comparatively lower and plant reliability equal or higher to ammonia production.
Generally, time required between turnaround is dependent on maintenance demands for rotating equipment (such as the hydrogen compressor if applicable) and the catalyst life. The typical recent benchmark for turnaround period for similar industrial plants including reformers is four years with 30-40 days for maintenance works, therefore on-stream time for the ammonia cracking unit of 8,400 hours per calendar year is realistic and easily achievable for KBR design and technology.
Scale-up and commercialisation
KBR offers optimised designs to the market for capacities ranging from 5 to 1,200 t/d hydrogen production. H2ACTSM is versatile, with design features tailored to individual project requirements such as carbon intensity, product quality and pressure, delivering the lowest levelised cost of cracked hydrogen product for each client and industry application.
KBR can support clients taking different routes for technology scale-up and commercialisation of ammonia cracking technology. Fig. 2 presents three routes to reach commercial scale hydrogen production via a KBR H2ACTSM plant.
A small-scale ammonia cracking plant refers to a demonstration or a pilot ammonia cracking plant. Depending on budget allocated and specific demonstration objectives required, the design of this small-scale plant can range from a full to a simplified process scheme.
- A simplified pilot plant could demonstrate ammonia dissociation in a fired tube (or radiant tube) furnace under chosen catalyst at projected operating pressure and temperature, proving catalyst performance.
- A full design pilot plant could additionally prove equipment design, energy efficiency and product purity.
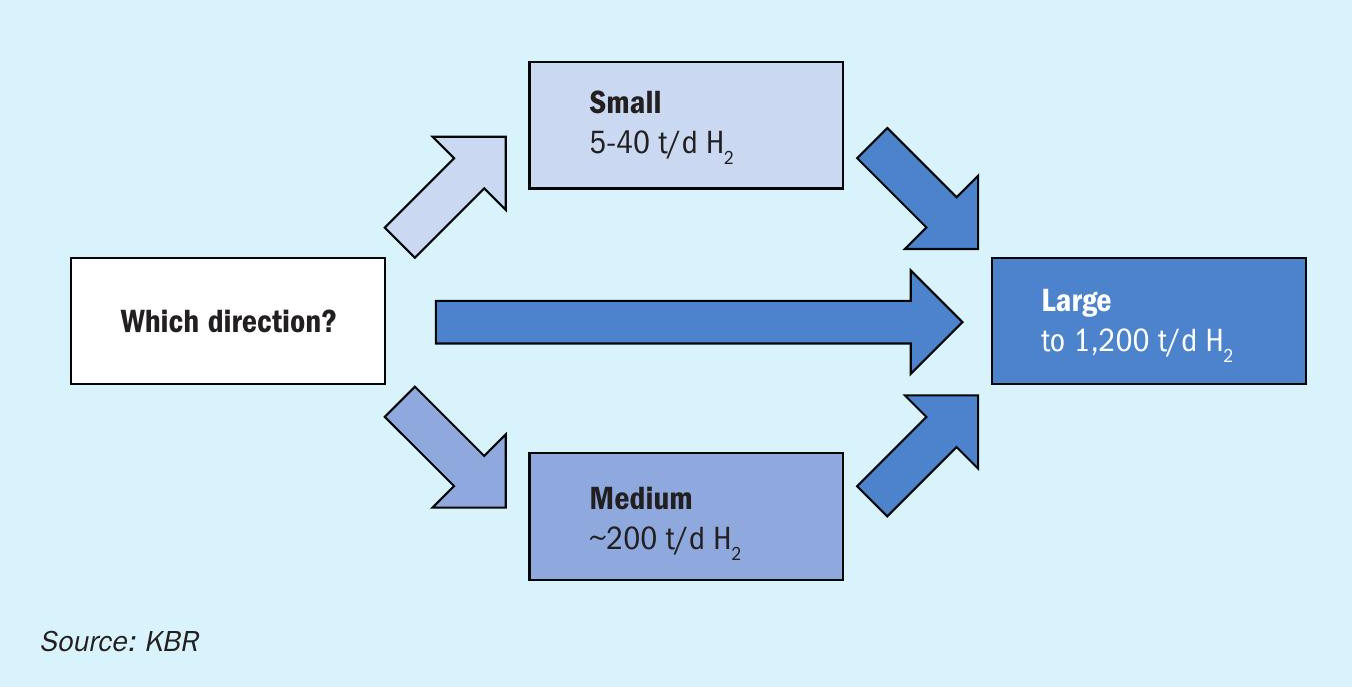
A medium-scale ammonia cracking plant is a commercial unit engineered and constructed based on a complete process scheme. It can serve decentralised ammonia cracking applications e.g., for decarbonising existing industrial sites. The medium-scale plant is an ideal candidate for phased approach to centralised world-scale cracking applications, staggering the production in line with feedstock supply availability or offtaker demand. Lessons-learned from commercial operation of the medium-scale plant can be applied to improve the next generation units, both in terms of technology and operation.
KBR is ready to license and guarantee H2ACTSM at large scale today, as technology features are well-proven and ammonia cracker equipment design is already available. As with any new technology, cracking ammonia is expected to advance rapidly in the short-to-medium term. KBR anticipates a flexible and pro-active approach to engineering and design of the first commercial units, ensuring that technology advances (such as catalysts or burner technology) can be incorporated in the design or easily retrofitted in existing units. As a result, KBR’s low risk, maximum opportunity flow-scheme can support first-mover advantage in this new market, leveraging on experience of successful technology commercialisation over 80 years. n
THYSSENKRUPP UHDE
Getting the optimum from ammonia cracking
The cracking of ammonia is a technology almost as old as its synthesis. The study of this reaction commenced as early as the 1920s, and for the last about five decades, small scale cracker units have been commercially available. But with the wide availability of industrial hydrogen, ammonia cracking was used for niche applications only.
With growing interest in ammonia cracking, this article discusses different process options and optimisation approaches for large-scale decomposition applications considering investment, operation cost, product yield and greenhouse gas (GHG) emissions.
Process options
Factors shaping the final ammonia cracking process, depicted in a simplified manner in Fig. 1, are, amongst others, shown in the following:
Source of reaction heat and selection of temperature profile
Same as the steam reforming reaction, the cracking reaction is a strongly endothermic reaction that is best carried out at elevated temperature (above 600°C) in one single pass. Therefore, the mechanical and thermal design of the cracking reactor, the furnace and its energy supply can also be selected in analogy to the well-proven design of the steam reformer. In the fired version, this is the optimum approach for large commercial-scale crackers.

Selection of catalyst
The catalyst to drive the ammonia cracking reaction is a field of intense study at present. Historically, nickel and ruthenium are known to be efficient catalysts and are commercially available. Nickel currently seems to be the catalyst of choice with reaction temperatures of 500 to 900°C. Ruthenium is more active at lower temperatures of less than 500°C. However, its scarcity and cost currently do not make its large-scale application seem feasible.
Reaction parameters
The optimal process conditions seem to be an elevated, but not very high pressure to cap the capital cost of the plant, but also to avoid the detrimental effect of pressure on the kinetics of the reaction, and high, but not extreme temperature to achieve high reaction rates, but also to avoid the worst of the adverse material effects of both, feedstock and product.
Process comparison
From the parameters discussed above a range of possible plant configurations arise. The following have been investigated in more detail by thyssenkrupp Uhde and distinguished by energy supply:
- Case 1: Self-sustaining process: The required energy is provided by combustion of a part of the feed and/or product stream. Two versions were evaluated as Cases 1a and 1b (with or without fixed-bed pre-reactors)
- Case 2: Process with external fuel source.
Process efficiency
The basic process from Case 1 is greatly improved with regard to its efficiency by adding an adiabatic pre-reactor, referred to as Case 1b, see Fig. 2. This efficiency increase mostly originates from lower overall firing duty and less heat loss with the flue gas.
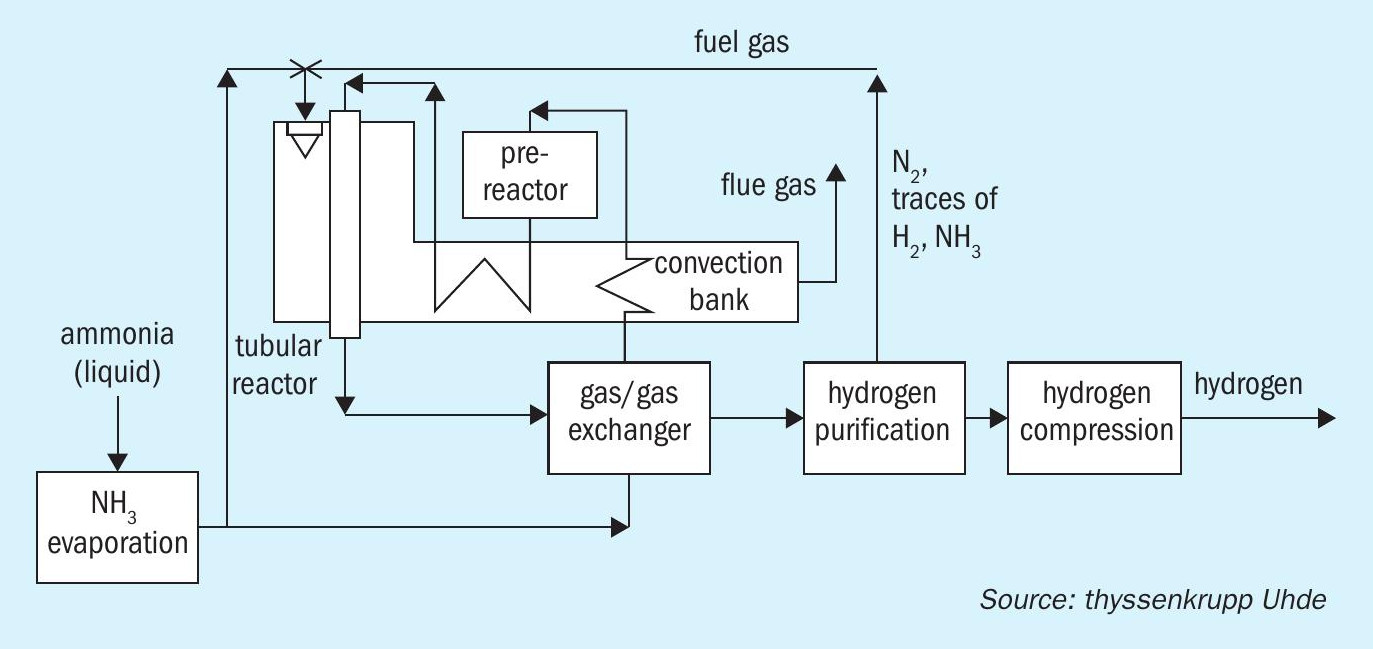
It is obvious that the molar efficiency from Cases 1a and 1b can be increased if less feed/product is used for heating by replacing it by another fuel like natural gas (Case 2). The theoretical maximum plant yield is therefore determined by the hydrogen yield of the pressure swing adsorption unit. However, this does not necessarily increase the energy efficiency. For a fair comparison, the additional fuel must be accounted for by its heating value, in the same way as the other contributions.
CO2 emission
Another way to compare process efficiency is to look at the CO2 emission of the whole process chain of ammonia production and cracking. This is done by assuming different ammonia production pathways (green and blue). For Case 2, comparison with 1b shows that heating by natural gas increases the specific CO2 emission despite increasing the total production of hydrogen.
Heating with electrical power was not considered. One has to bear in mind that the purpose of using ammonia as a hydrogen carrier is based on the idea that ammonia is produced in a place where renewable power is abundantly available at low cost and it is transported to a place where such renewable power is expensive (like Europe). Therefore, it is realistic that at the cracker location renewable power is available in limited amount at high cost only and hence not applicable for large scale commercial crackers.
Summary
Ammonia decomposition or cracking to hydrogen is an important process step in the context of CO2 avoidance in a future hydrogen economy and the use of ammonia as transport medium for hydrogen. All steps of this process chain (green hydrogen, green or blue ammonia technology, ammonia decomposition to hydrogen) are offered by thyssenkrupp Uhde.
The ammonia cracking process requires a minimum consumption of the energy contained in the ammonia. This energy can be obtained by combustion of a part of the feed or product or from an external fuel source. While the latter variant increases the hydrogen yield per tonne of ammonia input, it also increases the specific CO2 emission.
For future centralised clean hydrogen production, ammonia cracking in large centralised units are the optimum, due to process economics and avoidance of CO2 emissions.
JOHNSON MATTHEY
Ammonia cracking technology and its place in the low carbon economy
As part of a global focus on reducing greenhouse gas (GHG) emissions, there is significant interest in the use of hydrogen as a carbon-free fuel. Green hydrogen can be manufactured through electrolysis and transported from areas with excess renewable electricity to areas with less abundant renewable electricity. However, there are significant challenges associated with the transport of hydrogen; compressed hydrogen gas has a relatively low energy density (42 kg H2 per m3 at 700 bar), resulting in a reduction in energy density per shipment, and liquefied hydrogen, while having a higher energy density at 72 kg H2 per m3 , must undergo inefficient and expensive liquefaction prior to transport.
As a result, other hydrogen transport vectors are being considered with ammonia a favoured hydrogen transport vector due to a high hydrogen density (108 kg H2 per m3 ) and the existing technologies for storage and transportation at scale developed within the mature fertiliser and chemicals industry. Ammonia cracking will therefore play a key role in allowing ease of transport of green hydrogen, as green ammonia, around the globe from regions with sufficient renewable energy to manufacture green hydrogen. An important step to unlock ammonia’s potential as a hydrogen vector is the development of an efficient ammonia cracking process at large scale, given the large amount of energy that is required to decompose ammonia. The efficiency of the ammonia cracking process is critical to the success of ammonia as a hydrogen carrier.
The development of ammonia cracking flowsheets requires novel process technology combined with optimised catalysts to maximise the hydrogen recovery and energy efficiency for each unit operation within the supply chain.
Ammonia cracking
Chemistry
Following transportation of green or blue ammonia to the desired location, the ammonia must be converted back to hydrogen. The cracking reaction (equation 1) is endothermic, requiring an input of 46 kJ per mole of ammonia, and the equilibrium position favours hydrogen production at high temperatures.

The combination of an endothermic reaction and operation at relatively high temperatures results in an energy intensive process. To minimise the external energy input required to maintain the cracking reaction, there will be a requirement for significant heat integration and for optimal design of high temperature equipment within the flowsheet.
Flowsheet
The basic flowsheet requirements for ammonia cracking, shown in Fig. 1, include a vaporisation and pre-heating stage before the ammonia cracking reactor which is based on Johnson Matthey’s (JM) proven top-fired furnace design. As ammonia cracking is an equilibrium-limited reaction, there will be residual ammonia in the cracked gas feed. The cracked gas will undergo a separation stage, to produce a hydrogen stream at the required purity that can be compressed to the required pressure. The separation stage will generate a tail gas that has the potential to be used as a fuel source.
Industrial ammonia cracking
It is likely that a portion of ammonia decomposition will occur close to the import location with hydrogen being fed into a gas grid, whilst some ammonia will be transported further inland and undergo decomposition at the location where hydrogen is required. These two scenarios, illustrated in Fig. 2, will have distinct benefits, drawbacks, and challenges, as summarised in Table 1.
For centralised ammonia cracking, the ammonia is transported to an import facility situated at a port, where Johnson Matthey can offer a market leading high efficiency ammonia cracking process for the conversion of ammonia to hydrogen at scale. The technology builds on over 90 years’ experience with ammonia cracking and high temperature fired reactor designs for hydrogen, ammonia and methanol production, including the world’s largest modularised tubular furnace reactors, which have been selected as they offer the opportunity for the most efficient construction at a port site.
The process offers best in class environmental performance with a low emission process in which off-gases are fed back to the crackers as a fuel for the endothermic reaction. At the heart of the process is the interaction between Johnson Matthey’s industrially proven KATALCO™ 27-series catalyst and its top-fired ammonia cracking reactor.
The hydrogen is distributed through new or repurposed pipelines, with this hydrogen grid replacing the conventional natural gas grid. The hydrogen purity specification for this application can be achieved using well-established separation technology, with pressure swing absorption able to deliver high recovery rates at the required purity.
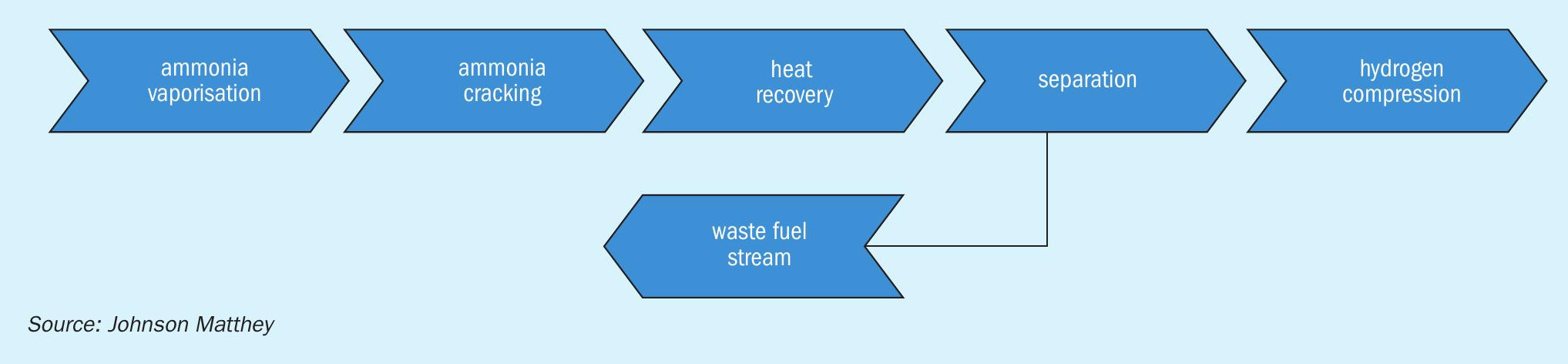
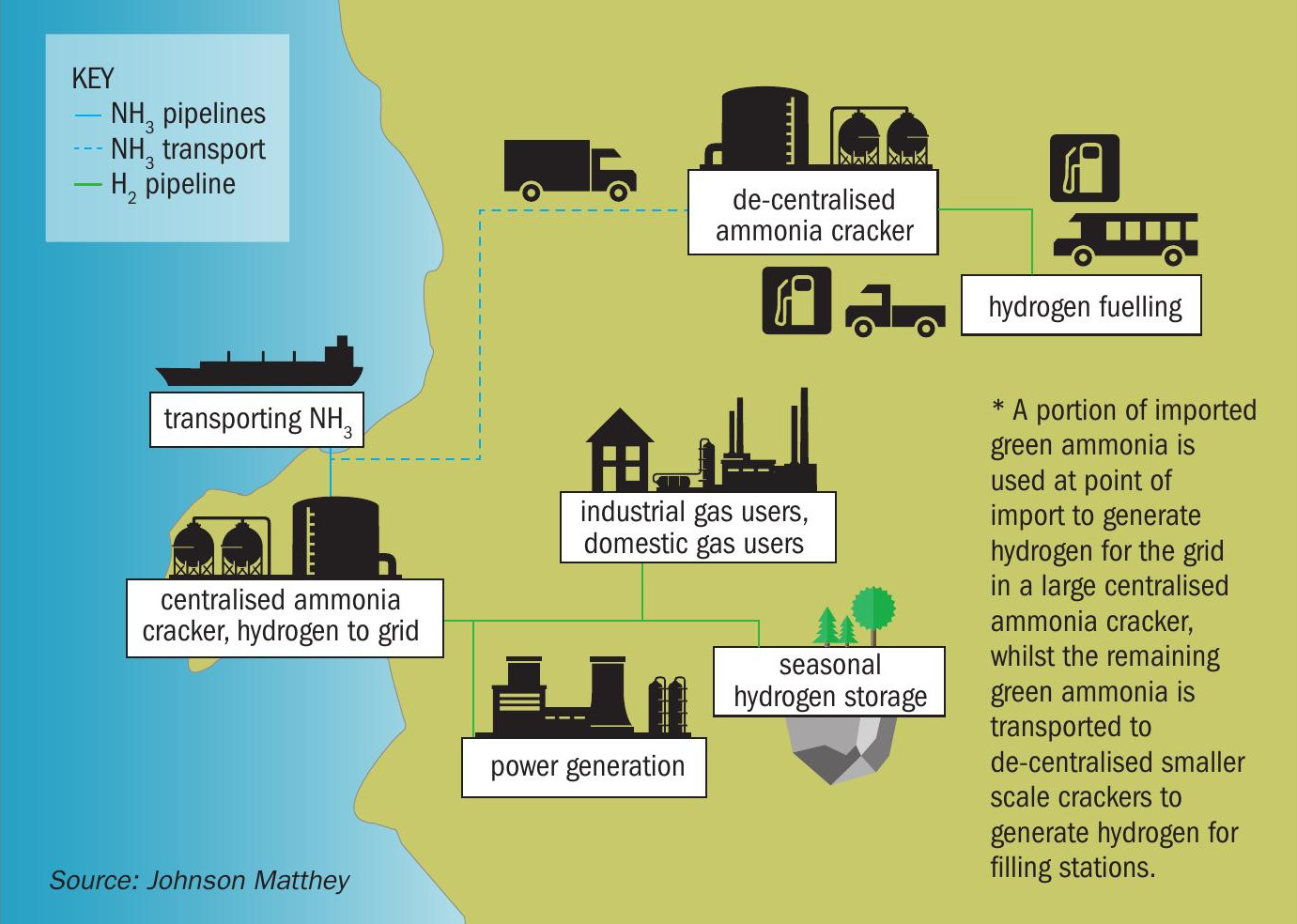
In the decentralised scenario, ammonia is transported to point of use, and cracked onsite to produce hydrogen. Hydrogen generation at fuel stations for fuel cell electric vehicles and localised hydrogen generation for off-grid users would benefit from this type of application. The purity requirement for hydrogen within fuel cell applications is extremely high; ammonia levels over 0.1 ppmv and nitrogen levels over 300 ppmv are not acceptable. As a result, the purification stage for this application may need to utilise technologies such as palladium membrane separation, which while technically proven are not operating on a significant scale within any markets today.
The common features to both flowsheets are the requirement for efficient heat transfer and recovery from the system, in order to maximise the hydrogen recovery and energy efficiency of the process. Large-scale ammonia cracking may be similar to primary steam-methane reforming technologies, with management of heat transfer critical to successful operation of a large-scale ammonia cracking reactor. The design of the reactor and the catalyst plays a part in optimising performance. De-centralised cracking will be on a significantly smaller scale but will benefit when designed with knowledge of heat transfer and high temperature applications.
The separation stage within both large-and small-scale applications generates a waste gas stream containing mostly nitrogen, along with the residual ammonia and unrecovered hydrogen. Within ammonia cracking applications, energy efficiency must be maximised. Within large-scale applications, the waste gas can be used as a fuel source to drive the cracking reaction, increasing the energy efficiency of the process. For electrical crackers, this may not be feasible and other options must be considered, such as using the waste stream to drive a turbine and recover the energy as electricity. However, there are further losses associated with any multistage energy recovery system.
Endothermic reactions such as ammonia cracking benefit from being carried out within a multi-tubular reactor, with an external heat source providing radiant and convective heat to the tubes. Regardless of the energy source there will be heat loss across the tube wall and tube, however this can be minimised through selection of the optimal catalyst pellet. Formation of a gas film at the tube wall limits heat transfer, however this can be managed with the correct catalyst pellet shape and size. A catalyst with good packing characteristics can minimise this effect, causing the flow to be more turbulent with an associated smaller gas film at the tube wall. This increases the heat transfer into the catalyst to drive the endothermic reaction, which can result in lower tube wall temperatures and a more efficient process.
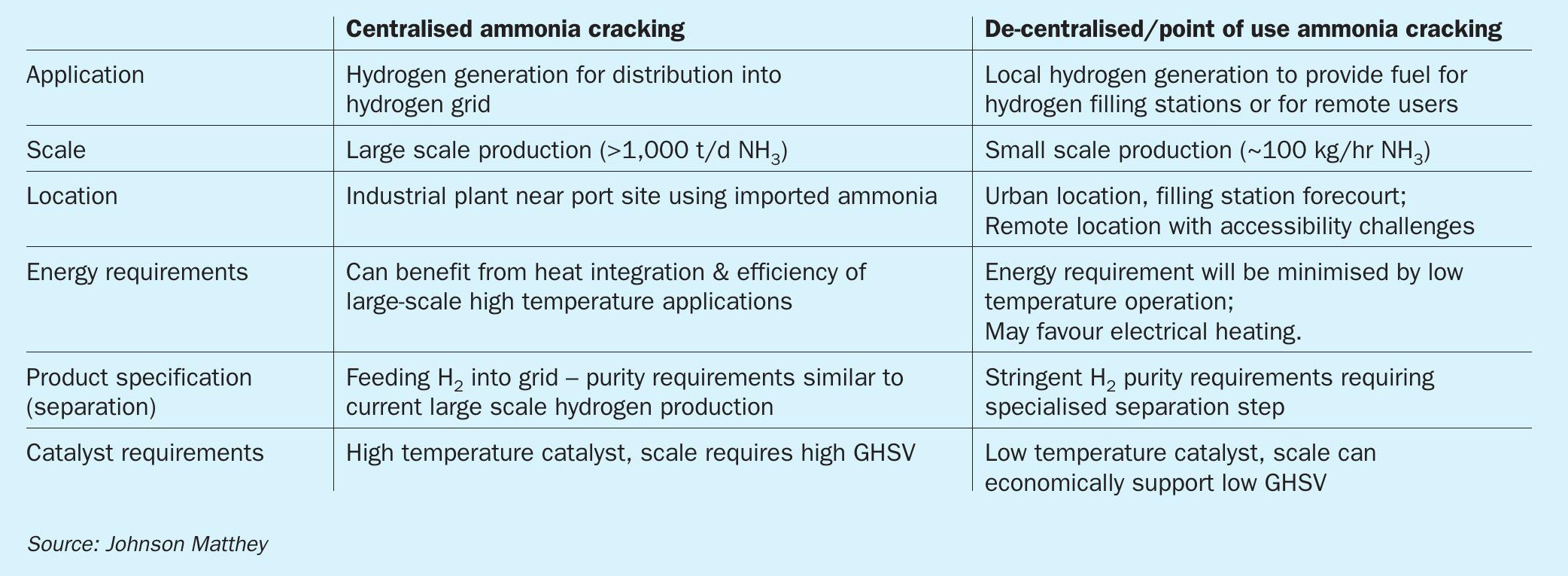
Johnson Matthey has a long history and significant experience in the development and design of reforming processes and reactors, including pre-reforming, primary reforming and secondary reforming which all have different design requirements. Maximising performance from a reformer-style ammonia cracking reactor requires knowledge of both reactor design and catalyst design, which are both areas Johnson Matthey has significant experience and knowledge.
Ammonia cracking catalysts
Base-metal ammonia cracking catalysts have a long history within industry, with applications including the production of forming gas for welding and generation of nitrogen at chemical plants, through cracking of ammonia and combustion of hydrogen. These catalysts are active at high temperatures, and as a result achieve very low ammonia slip.
Johnson Matthey’s KATALCO 27-2 is a nickel-based ammonia cracking catalyst that has been supplied for ammonia cracking applications for over 50 years. It is a highly active catalyst that typically operates in the range 700-950°C, giving high hydrogen recovery due to the low residual ammonia levels at this temperature range.
Nickel based catalysts are very suitable for use in high-temperature applications, providing a robust and stable product that combines good activity with a relatively high tolerance to poisons in the process feed.
For large-scale cracking processes Johnson Matthey proposes a high-temperature catalyst, KATALCO 27-200MQ, a nickel-based ammonia cracking catalyst, which combines high surface area with low pressure drop due to the QUADRALOBE™ pellet shape. This high-temperature ammonia cracking catalyst achieves high activity and near-equilibrium conversion when operated between 650 and 900°C. Due to the high activity of the catalyst, relatively high gas hourly space velocities (GHSV) can be used to achieve the required conversion, minimising catalyst volume requirements and, as a result, minimising the ammonia cracker size.
As the interest in ammonia as an energy vector supporting green hydrogen fuel has grown, there has been a focus on reducing the energy requirements demanded by the cracking process, and subsequent research on the feasibility of ammonia cracking at low temperatures. KATALCO 27-612, a commercially available pgm-based ammonia cracking catalyst, was developed in response to this market need. This catalyst typically operates in the range 450-500°C, substantially extending the available operating range for ammonia cracking applications. The overall economics of a low temperature application will be a balance between the savings associated with lower temperature operation and the increased catalyst costs for pgm-based catalysts.
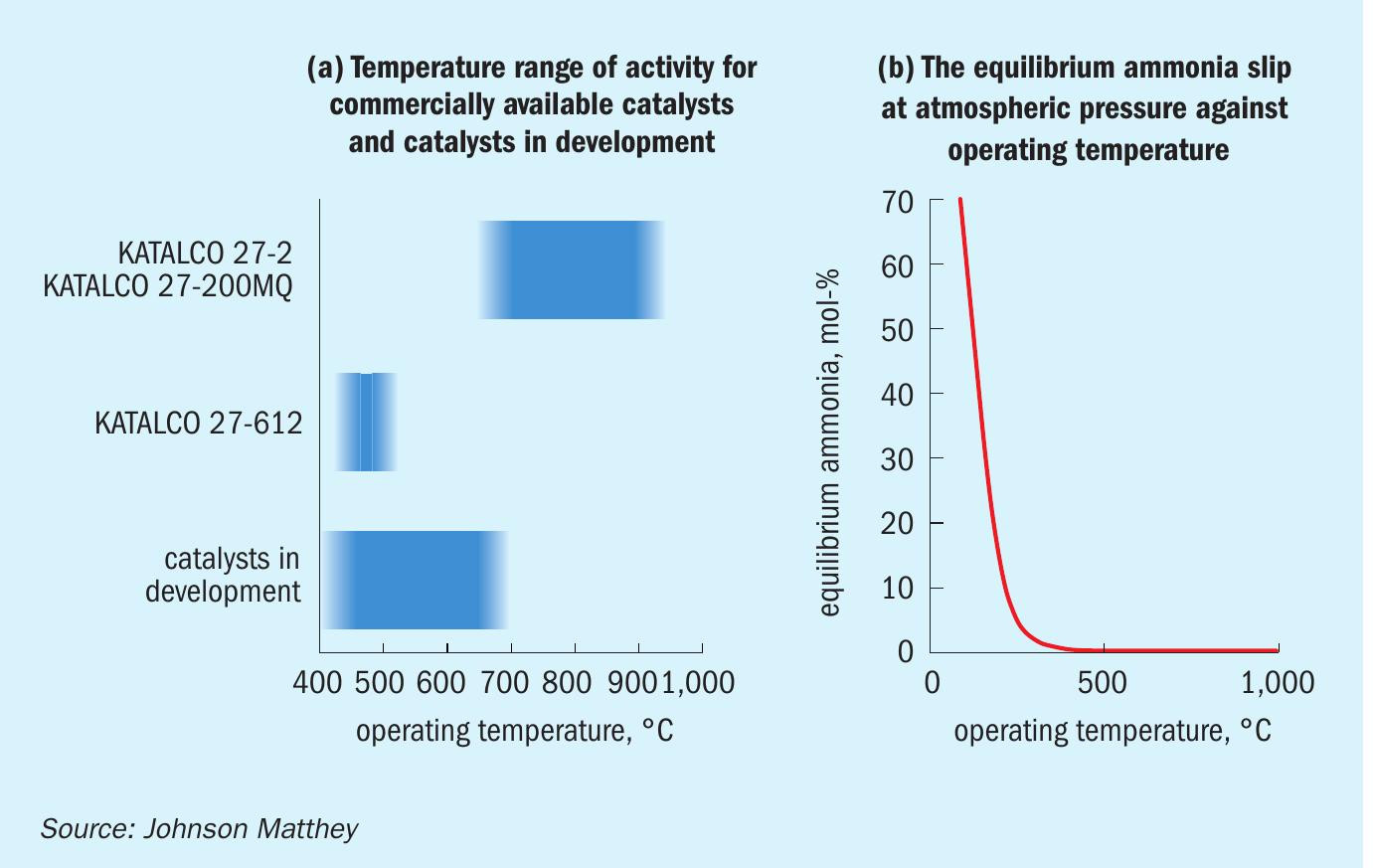
In addition to these commercially available catalysts, Johnson Matthey continues to develop and evaluate alternative ammonia cracking catalyst technologies, with a view to further extend the operating range to lower and intermediate temperatures. However, as the reaction is equilibrium limited, there is a limit on the lowest feasible operating temperature. For atmospheric pressure operation, ammonia equilibrium levels increase drastically below 250°C, and this minimum viable temperature increases with operating pressure, reaching 450°C at 35 bar g operation.
Hydrogen-fuelled power plants in South Korea
Johnson Matthey and Doosan Enerbility have signed an agreement to develop hydrogen-fuelled power plants in South Korea. The partnership supports the South Korean Government’s plans to increase the share of clean hydrogen-based power generation from 0% in 2022 by 2.1% by 2030 and 7.1% by 2036.
JM will provide innovative ammonia cracking technology and catalyst, which converts clean ammonia into nitrogen and hydrogen. The clean hydrogen can then be used to power turbines, which are key components of hydrogen-fuelled or hydrogen-LNG fuelled combined cycle power plants.
Analysis from the Korea Institute of Machinery & Materials shows that using ammonia cracking technology to enable hydrogen-fuelled turbines could reduce carbon emissions by 10.4% when a gas turbine is fired up with 30% hydrogen. It can be lowered to 21.4% when there is 50% hydrogen present. According to data from IHS Markit, hydrogen demand in 2030 for power and heat generation is set to be 2.1 to 4.6 million tonnes globally.
Conclusion
Ammonia is expected to play a key role as a transport vector for green hydrogen, and as a result ammonia cracking is an area of increasing interest and development. Johnson Matthey has developed processes for highly efficient ammonia cracking which improve energy and feedstock efficiency, providing cost efficient conversion and a low emission process.
On-going development within Johnson Matthey has resulted in the development of KATALCO 27-612, a low temperature ammonia cracking catalyst, as well as high temperature catalysts such as KATALCO 27-200MQ which allows flexibility in the operating temperature range for cracking. n
DUIKER COMBUSTION ENGINEERS
Duiker ammonia cracking technology
Duiker Combustion Engineers is a Dutch process technology solution provider with a rich history dating back to 1919. Duiker has developed to become a world leader in providing process solutions for sulphur recovery and ammonia valorisation. Since the installation of the first Luynet Multipe Vortex (LMV) burners at Shell Godorf-Hafen in 1961, Duiker rapidly established a sound track record in the global energy industry and has built up more than a decade of experience in low NOx ammonia combustion. Driven by its mission to serve people and the planet, Duiker has developed an advanced, highly energy-efficient, innovative ammonia cracking technology.
Ammonia, in liquid form, can be utilised as an energy carrier. It can be produced from hydrogen in regions with abundant renewable energy sources such as sun, water, geothermal and wind. A global supply chain infrastructure is already in place for large-scale production, transportation and utilisation to serve various industries. This allows countries with abundant renewable energy sources to produce and export ammonia to end users across the globe, where it can be used as a direct fuel or converted back to hydrogen to enable the decarbonisation of industry, power generation, and mobility. A schematic overview of the ammonia-hydrogen supply chain is shown in Fig. 1.
Duiker offers solutions for direct utilisation in industrial steam boilers as well as in ammonia cracking. The Duiker developed ammonia cracking technical solution focuses on delivering highly efficient, economic and environmentally sustainable processes by combining state-of-the-art equipment with a high technology readiness level.
Hydrogen is a commodity product that is currently often labelled by the colours “grey”, “blue” and “green” depending on the way it is produced. However, in Duiker’s view these coloured labels will likely soon fade away and be replaced by a number that reflects the carbon footprint during its entire production and supply chain. As such, the only difference will be the levelised cost of hydrogen. For this reason, Duiker has focused on economies of scale during its cracker technology development, to achieve the lowest cost price for hydrogen from cracked ammonia. Duiker’s cracking technology results in very low prices for the cracking itself, whilst offering extremely high reliability, availability and energy efficiency.
The novel Duiker Ammonia to Hydrogen Converter (AHC) converts green ammonia, the feedstock, into green hydrogen, the product.
Proprietary SCO technology and nitrogen related emissions
The SCO technology has been developed for valorising ammonia-rich gases in refineries (Fig. 2). The first commercial-scale SCO unit was put into operation in 2009. Since then, Duiker has gained significant know-how and experience in low NOx ammonia combustion. The NOx levels from SCO installations are so low that they operate within existing permits for the refineries and without the necessity for additional DeNOx units.
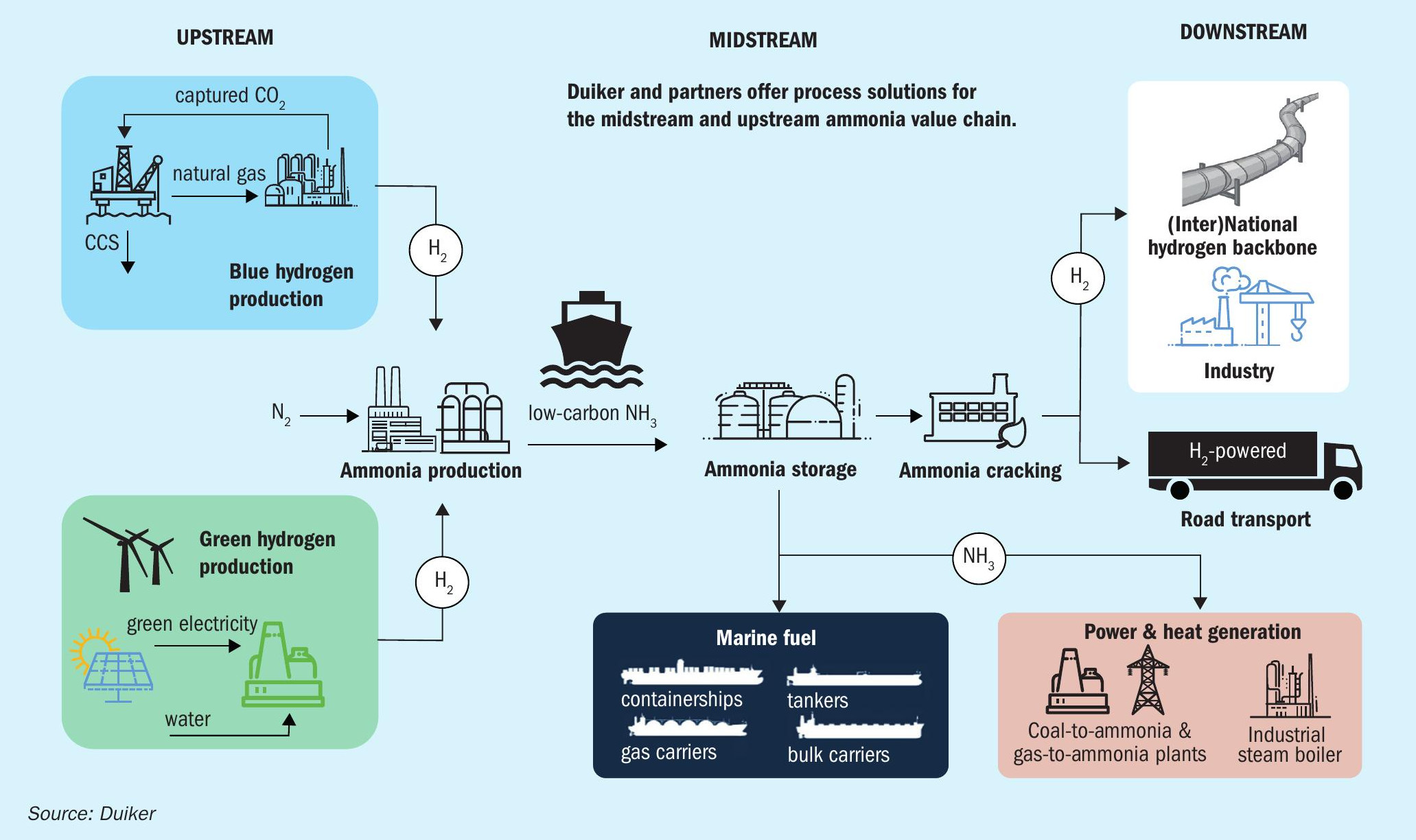
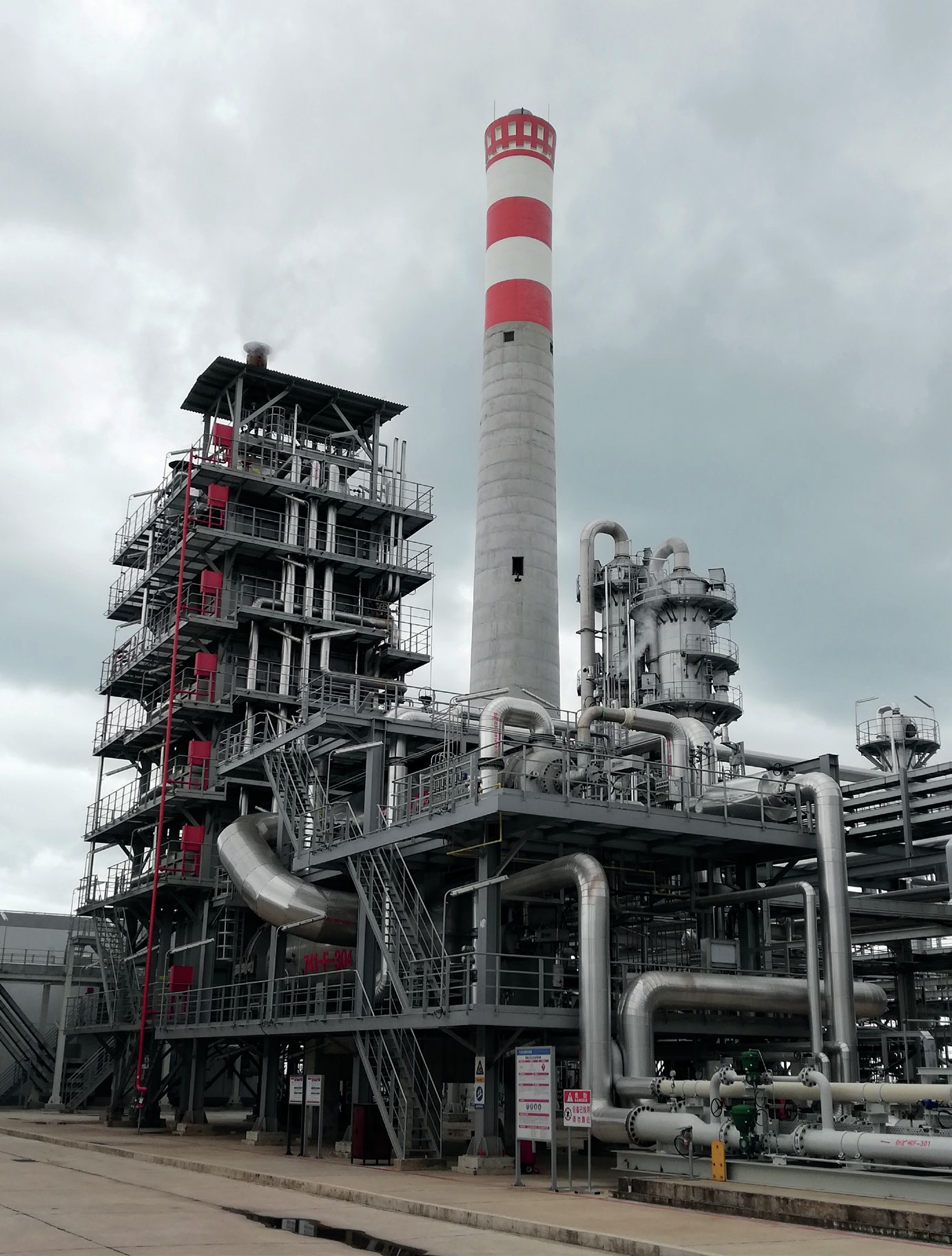
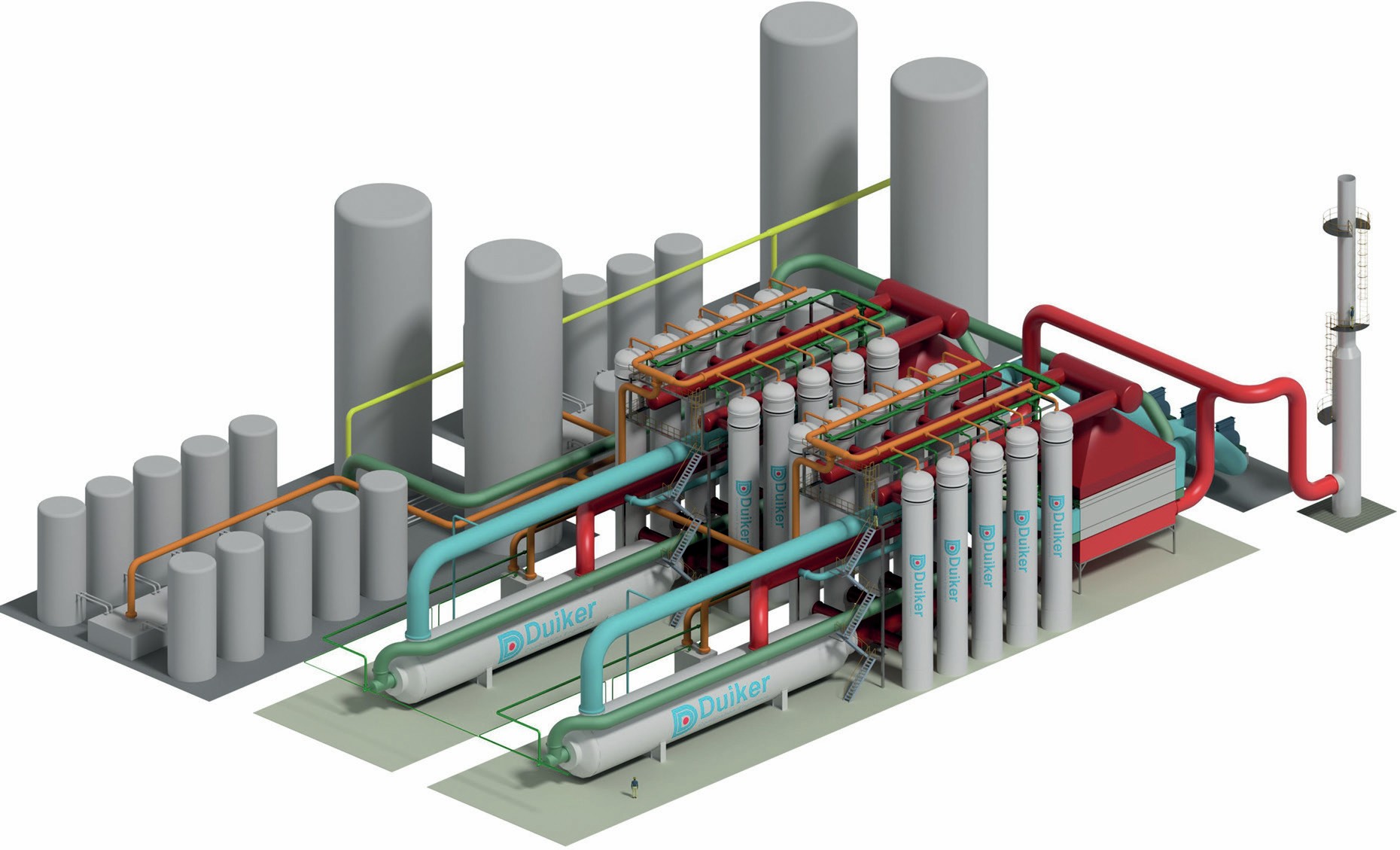
Duiker can maintain the NOx level of the ammonia cracking plant at 60 ppm (v) @ 3% O2 dry without a DeNOx unit. Duiker can also limit these emissions to practically a few ppm in case of lower NOx requirements.
If ammonia cracking is to be ubiquitous, the emissions from these plants must be strictly managed. Uncontrolled combustion of ammonia or hydrogen can lead to high NOx levels in the 1,000s of ppm. These emissions will require large DeNOx units and the addition of ammonia (NH3 ). However, the production of N2 O, a potent greenhouse gas, NH3 slip are inherent to NOx removal where starting NOx levels are high. The SCO technology will safeguard its users from NH3 slippage, greatly facilitating the environmental permitting process.
Key parameters
Important features of the Duiker AHC technology are listed below:
- Efficiency: The overall efficiency of the process based on the lower heating values (LHV) of ammonia and hydrogen, electricity consumption and counting for heat losses is 90% on an end-of-run basis.
- Utilities:
– The only required utility of the AHC is considered to be electricity.
– No cooling water or demi water is required.
- Plot space: Duiker’s design for the ammonia to hydrogen converter is compact and can be flexibly adapted to customer requirements. An initial indication for the total plot footprint of the plant consisting of all necessary equipment can be quickly estimated for different sizes. For instance, a total plot footprint of 3,000 m2 for a 180 t/d H2 (@ 99.97% H2 ) plant.
- Emissions and effluents:
– During regular operations the only effluent of the AHC is flue gas that exits the system via the stack.
– NOx emissions are below 5 ppm.
– NH3 emissions are below 1 ppm.
– Zero CO2 Scope 1 emission.
– Zero liquid waste streams are produced in this process.
- Output H2 : m Purity in accordance with the ISO 14687:2019
- Technology readiness level: m Based on the equipment that the AHC comprises, the technology readiness level (TRL) is 8.
Large scale
The Duiker ammonia cracking technology can be scaled up to world-scale needs (Fig. 3). The plot space of the large-scale plant is highly flexible and can be further reduced according to customer requirements.
PROTON VENTURES
Ammonia cracking as part of the ammonia value chain
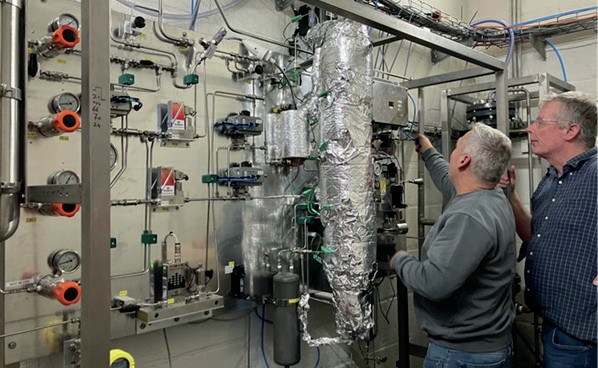
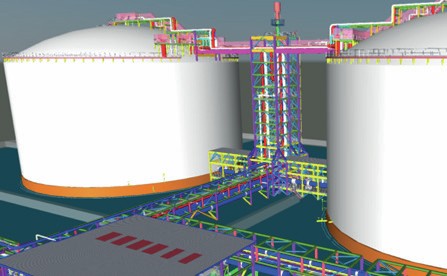
Proton Ventures is an engineering solutions provider in the (green) ammonia industry. The company was founded in 2001 by former CEO Hans Vrijenhoef, who had previously been the plant manager of a now defunct ammonia plant in Rozenburg, The Netherlands. Even in the early days, Hans already had the vision to use ammonia as a zero-carbon fuel and hydrogen carrier. Some 20 years later, this vision is taking shape with weekly announcements of green ammonia production plants.
Proton Ventures has its fair share of projects in this emerging landscape. These range from scoping studies, feasibility studies, FEEDs (front end engineering designs), and EPC (engineering, procurement & construction) projects. One of the distinguishing strengths of Proton Ventures is its technology agnostic approach as system integrator, which allows Proton Ventures to select the most suitable licensors and original equipment suppliers (OEMs) for the specific project.
Ammonia cracking for large-scale sustainable hydrogen production
Ammonia is increasingly considered as a zero-carbon fuel and hydrogen carrier in a decarbonised energy and food landscape. As ammonia will become more abundant as an energy vector, its use as a hydrogen carrier is set to increase. Ammonia cracker facilities for hydrogen production are currently being considered in various northern European ports, such as Rotterdam and Wilhelmshaven. Proton Ventures has performed various studies on ammonia cracking for clients and remains active within various research consortia. Such centralised ammonia cracker solutions for pure hydrogen production are functionally very similar to natural gas processing plants for hydrogen production. Alternatively, decentralised ammonia cracker solutions are currently being developed, which do not always require full conversion and purification of the hydrogen, thereby improving the energy efficiency of the system and the cost.
To consolidate Proton Ventures’ solutions for ammonia cracking, the company is currently operating a high-pressure ammonia cracking testing facility at the high-pressure laboratory at the University of Twente, the Netherlands (Fig. 1). This is critical to validate operational performance under industrially relevant conditions, while also allowing the testing of novel cracker concepts.
The next aim is to build a commercial pilot for ammonia cracking, which is an essential intermediate step for the industry to move toward world-scale hydrogen production facilities. A pilot plant is necessary, as performance in terms of ammonia feedstock utilisation is key for the cost of produced hydrogen. The ammonia feedstock cost can account for over 90% of the total levelised cost of hydrogen from ammonia cracking. Thus, ensuring minimal ammonia feedstock utilisation is paramount. At Proton Ventures, efficient process integrations in the developed processes allow for the lowest cost of hydrogen.
Ammonia storage and handling
Every ammonia cracker needs ammonia storage and handling. Some of the largest projects executed by Proton Ventures are its refrigerated storage tanks in Estonia (BCT & Eurochem) and Bulgaria (Agropolychim), which are among the largest operating ammonia storage tanks in Europe. For example, the tanks in Estonia each have a capacity for 30 kilotonnes of refrigerated ammonia at -33°C. The tanks are double containment storage tanks complying with modern safety standards. The facilities in Estonia also consist of railcar loading and unloading systems, a marine loading arm facility, and four UAN tanks of 20 kilotonnes each. Full containment storage tanks can also be realised with Proton Ventures.
The global trade of ammonia is set to expand over the coming decade, as the use of ammonia as shipping fuel, as stationary fuel, and as hydrogen carrier is taking off. In light of these developments, Proton Ventures and consortium partners have been awarded a turnkey contract by OCP Group for two refrigerated ammonia storage tanks in Jorf Lasfar, Morocco. Also, Proton Ventures is currently investigating the revamping of two storage tanks operated by Vesta Terminals in Vlissingen, The Netherlands.
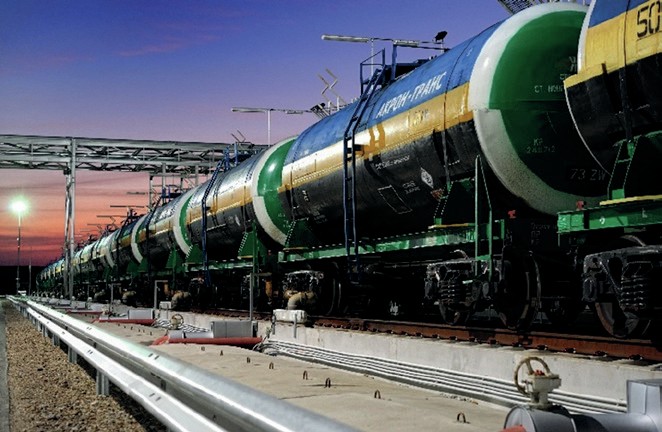
Proton Ventures complies with stateof-the-art requirements for new ammonia storage tanks, even when these are located in desert areas with temperatures sometimes measured in excess of 50°C. Recently, a FEED+ engineering package was completed for a new ammonia export terminal in the United Arab Emirates. Intermittent flaring and an interconnecting bridge between the two storage tanks with a combined staircase optimises the capital investment, spatial utilisation and simplicity. Furthermore, the refrigeration system design is optimised for hot climate operations and a low operational cost.
Project development for large-scale green ammonia production
Large-scale ammonia crackers also require large-scale green ammonia production. This is most economical in locations with optimal solar PV and wind electricity. These renewables are coupled with electrolysis for hydrogen production, air separation for nitrogen purification, and a Haber-Bosch plant for ammonia production.
Proton Ventures is active within the TransHydrogen Alliance (THA), which aims to produce ammonia in areas with abundant solar and wind resources, such as Brazil and Morocco, with subsequent transport and cracking of ammonia to hydrogen in Rotterdam, the Netherlands. Herein, the aim is to produce ammonia at world scale, e.g., producing up to several millions of tonnes/annum. The benefit of the Trans Hydrogen Alliance is that production and utilisation are coupled, ensuring supply, while keeping the overall system cost low.
In February 2023, Casa dos Ventos and Comerc Eficiência, an energy efficiency company of the Comerc Energia Group, signed a partnership with the TransHydrogen Alliance. The purpose of the agreement is to enable the export of green ammonia produced in the Industrial and Port Complex of Pecém (CIPP), in Ceará. The plant is to be built on a 60-hectare site with a capacity of up to 2.4 GW of electrolysis, producing 960 t/d of hydrogen, and with all phases implemented, will enable the production of 2.2 million t/a of ammonia. The parties signed a memorandum of understanding to jointly develop a viable partnership targeting production of the first phase for export to Europe through the Port of Rotterdam, in the Netherlands in the year 2026.
Leading by example
The ammonia economy will likely become a reality soon. Various decarbonisation projects for existing ammonia plants have already been realised, with new build green ammonia plants under construction. Various consortia are commercialising ammonia energy solutions.
Proton Ventures has been at the forefront of these discussion with the initiation of the NH3 Event Europe in 2017, which was the first European conference focused on low carbon ammonia production, as well as its utilisation as a low carbon fertilizer, zero-carbon fuel, and hydrogen carrier. The conference boasts a strong industrial presence, as well as various excellent academic speakers. On the 8th and 9th of June 2023, the NH3 Event Europe will be held for the sixth time, returning to its iconic venue: Diergaarde Blijdorp in Rotterdam, the Netherlands.
Twenty years ago, even five years ago, very few believed in ammonia as an energy carrier. Over the last two decades Proton Ventures has established itself as an engineering solutions expert in the green ammonia landscape.
CASALE
A pathway to large-scale sustainable hydrogen production
Casale is highly committed to supporting and accelerating the energy transition through innovation and advanced technology, offering its customers decarbonised and cost-effective solutions for ammonia and hydrogen production.
Ammonia for generating CO2 -free energy
Ammonia cracking technology represents a fundamental path towards sustainability as it enables green ammonia produced in regions where renewable energy resources are available to be converted back to green hydrogen in places where renewable energy resources are not available to produce it.
While ammonia cracking technology for generating CO 2 -free energy is new to the market, industrially the concept of an ammonia cracker is not new. Many plants were developed in the past where a so-called “ammonia dissociator” was installed to provide small amount of hydrogen for start-up activities.
Nowadays this operation is commonly achieved through the steam methane reformer which is actually used as an ammonia cracker during the start-up operation in several ammonia plants for this purpose.
However, despite being a well-known technology, today there are no available or known processes to decompose ammonia at large scale quantities.
Most commercially available solutions offer an electric-based furnace solution with a production capacity ranging from 1 to 2 t/d and rarely include any additional steps to produce hydrogen at high purities.
To meet the new challenges of the green revolution, Casale has developed a new process for converting ammonia synthesised from renewable resources into pure hydrogen via the Casale ammonia cracking technology. The Casale ammonia cracker design is applicable for a wide range of hydrogen plant capacities. All single components of the Casale process scheme are proven technologies with the ammonia cracker at the heart of the process.
Casale ammonia cracking technology is based on a simple, highly efficient and reliable scheme able to produce high purity hydrogen (up to Grade 5 hydrogen purity). It belongs to the Casale Flexigreen ® family which includes a wide range of innovative products and technologies within the Casale portfolio dedicated to “Green” production (Fig. 1).
In the Casale ammonia cracking scheme, liquid ammonia from storage is evaporated and preheated before being fed to the Casale ammonia cracker, where the ammonia decomposition reaction takes place. The ammonia decomposition reaction is an endothermic reaction promoted by high temperature and low pressure. To achieve the desired efficiency, it is performed in the presence of a catalyst while the heat is provided by the combustion of clean fuel (the tail gas coming from the hydrogen purification unit). The product from the ammonia cracking reactor is then cooled and purified in the separation unit where high purity hydrogen is recovered.
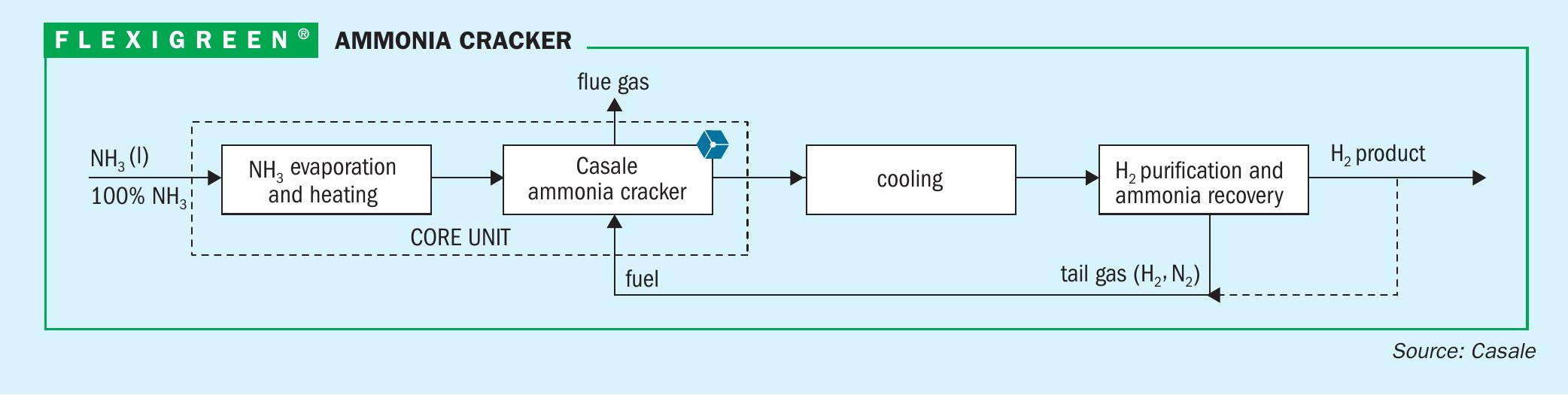
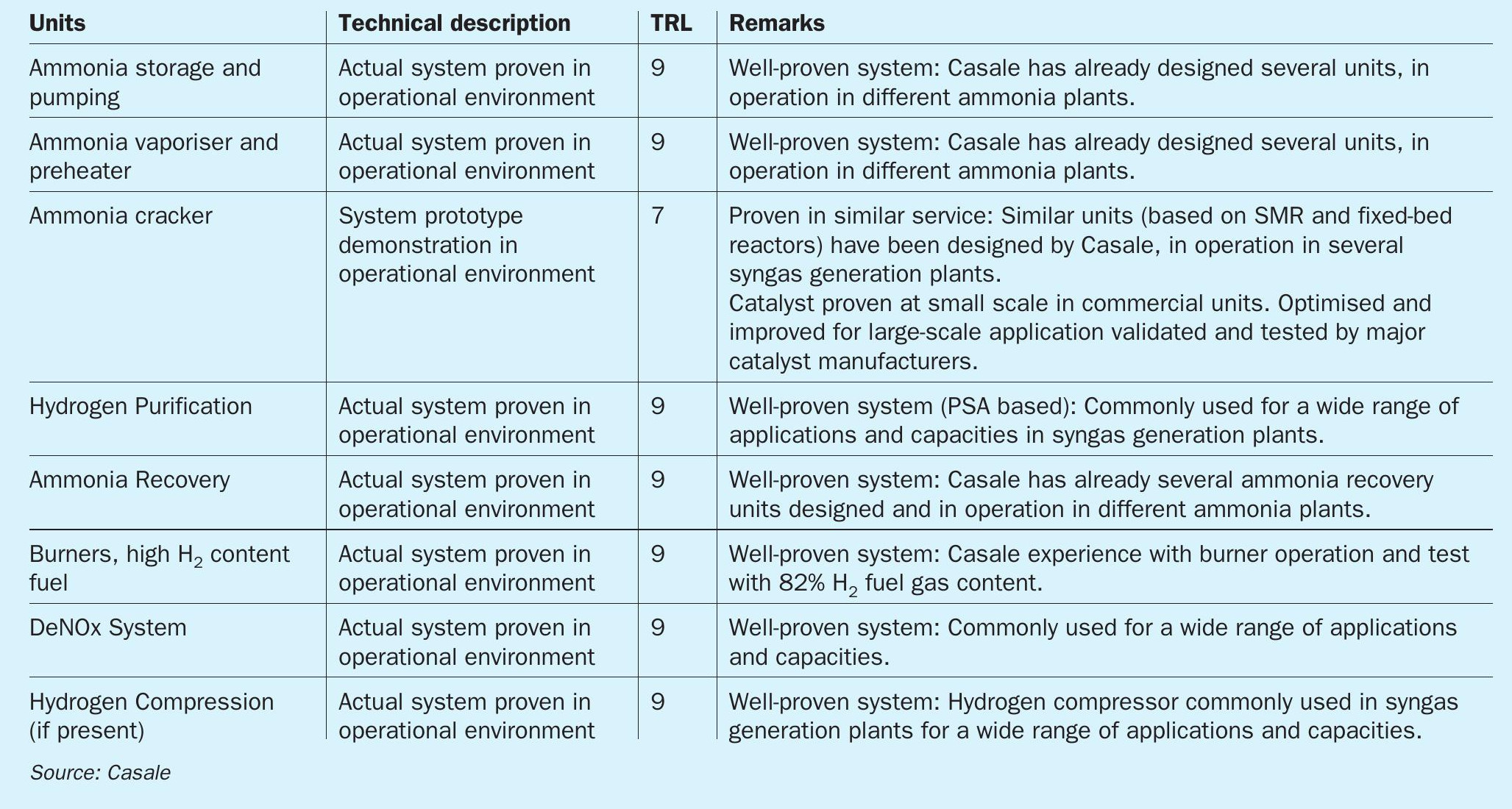
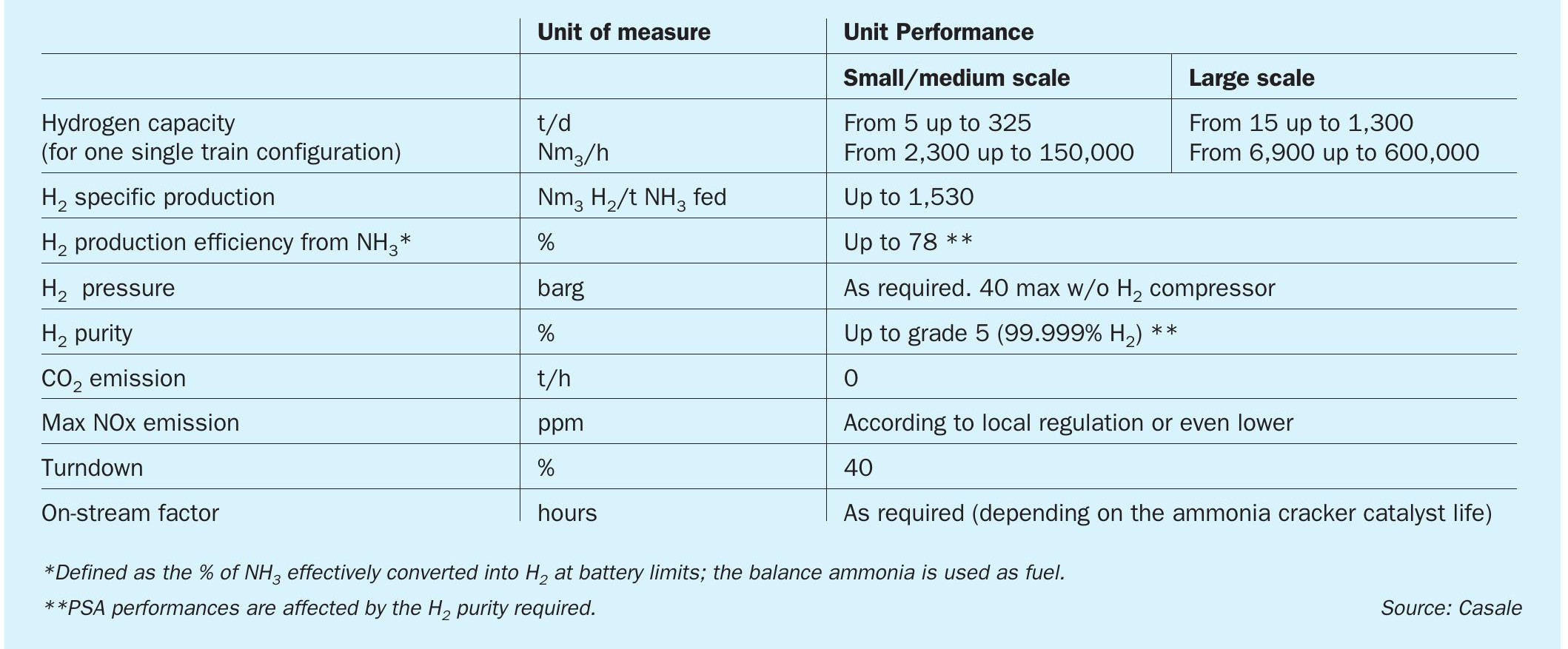
The hydrogen purification units consist of well-know and proven technologies commonly used in different industrial processes:
- hydrogen PSA unit;
- ammonia recovery unit: based on H2O/ NH3 absorption and distillation technologies where ammonia is recovered and recycled back to reduce ammonia consumption.
The by-product coming from the separation unit is recovered as the main fuel providing the heat required for the reaction; a limited quantity of hydrogen is used as make-up fuel.
Casale can offer different ammonia cracking reactor design concepts depending on the size of the hydrogen production plant. Proposed solutions are tailored according to specific users’ needs.
Ammonia cracking technology main features
The main features of the new process are:
- totally carbon-free operation; l high efficiency;
- high reliability;
- simple and flexible;
- very high H2 purity;
- completely self sustainable;
- highest single train capacity on the market;
- continuous operation;
- NOx emission controlled according to local regulations;
- no steam export;
- high pressure H2 production without the need of a compressor;
- high modularisation grade approach;
- solution immediately available;
- wide range of hydrogen capacities in a single train configuration.
The process scheme selection is a function of the specific client requirements in terms of performance and investment cost.
Ammonia cracker furnace main features
The Casale ammonia cracker furnace design duplicates concepts from proven reaction furnaces designs, like the steam methane reformer, wherever practical, coupled with Casale’s know-how of material behaviour exposed to an ammonia environment (nitriding).
Casale has the longest, successful experience in material selection for processes operated in an NH3 environment at high pressure and temperature. This will likely be one of the most critical factors to be considered for a reliable and steady operation of an ammonia cracker process.
The similarity principles used are:
- physical similarity for process variables;
- duty similarity for endothermicity of the reaction;
- geometric similarity for shape considerations and flow symmetry (large size);
- metallurgy similarity: creep, hydrogen environment, nitriding.
Large-scale ammonia cracker furnace
The Casale large-scale ammonia cracking furnace is comprises multi parallel catalyst-filled tubes located inside a radiant section (multi shape design). The nickel-based catalyst is the current benchmark for non PGM catalyst used for ammonia cracking. The Casale ammonia cracker design has been developed in close cooperation with a major catalyst manufacturer.
The radiant chamber is provided with a combustion system able to operate with a wide range of free carbon fuels. The flue gases from the radiant section are collected in the convection section where all the available heat is recovered, and all pollutants are treated to achieve the required environmental limits. A further recovery step with a combustion air preheating facility is added to improve the overall furnace efficiency before the flue gases are sent to the atmosphere.
This scheme is suitable for a hydrogen plant capacity from 6,900 Nm3 /h (15 t/d) up to 600,000 Nm3 /h (1,500 t/d).
Small/medium-scale ammonia cracker furnace
The Casale small/medium-scale ammonia cracking furnace comprises a radiant section and a convective section in which different steps for preheating of the ammonia vapour are foreseen to supply the required heat for the ammonia dissociation reaction.
This scheme is suitable for a hydrogen plant capacity from 2,300 Nm3 /h (5 t/d) up to 150,000 Nm3 /h (about 325 t/d).
A similar approach to the previous large-scale cracker concept has been applied for the combustion system.
The main advantage of this scheme is a lower operating temperature allowing a reduction in the investment cost, but is limited in the maximum hydrogen capacity achievable.
Process technology readiness levels (TRL)
The technology readiness level (TRL) for the Casale ammonia cracker process is 7, mainly due to the catalytic furnace for medium/large scale applications (see Table 1).
The TRL assigned to the other ammonia cracking scheme components is 9 as they are all well-proven technologies commonly used in a wide range of applications and in which Casale already has experience.
Regarding the ammonia cracker, Casale has designed many steam reformers for both ammonia and methanol plant production with similar capacity/duty or higher, whose technology can be totally applied to the Casale ammonia cracking furnace.
Scalability of the plant is mainly limited by the size of the catalytic furnace unit and the performance of current catalysts available on the market.
Key performance indicators
Key performance indicators for Casale ammonia cracking are provided in Table 2.
Summary
Thanks to its background and experience, Casale can provide a simple, flexible and customised technology which can be tailored to specific plant needs with a well proven solution that is immediately available.
Covered by two different patent pending applications, Casale ammonia cracking technology covers a wide range of hydrogen plant capacities ranging from 5 t/d of pure hydrogen to 1,300 t/d of pure hydrogen, currently the highest single train plant capacity available on the market.
Casale is ready to support possible partners in various way starting from the engineering and design to product scale up for commercialisation of the first industrial-scale unit. n