Sulphur 406 May-Jun 2023
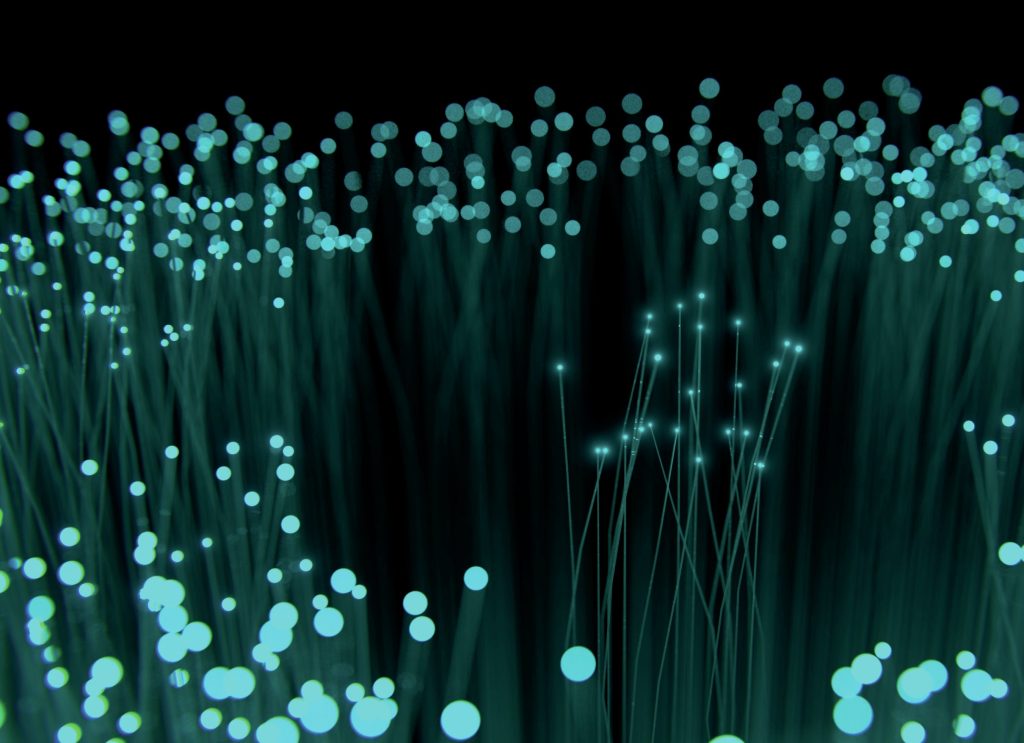
31 May 2023
Developments in sulphur polymers
POLYMERS
Developments in sulphur polymers
Incorporating sulphur into polymers is known to improve their properties. New research is looking into the varied world of sulphur co-polymers, unlocking new materials for batteries, structural applications and clean technology.
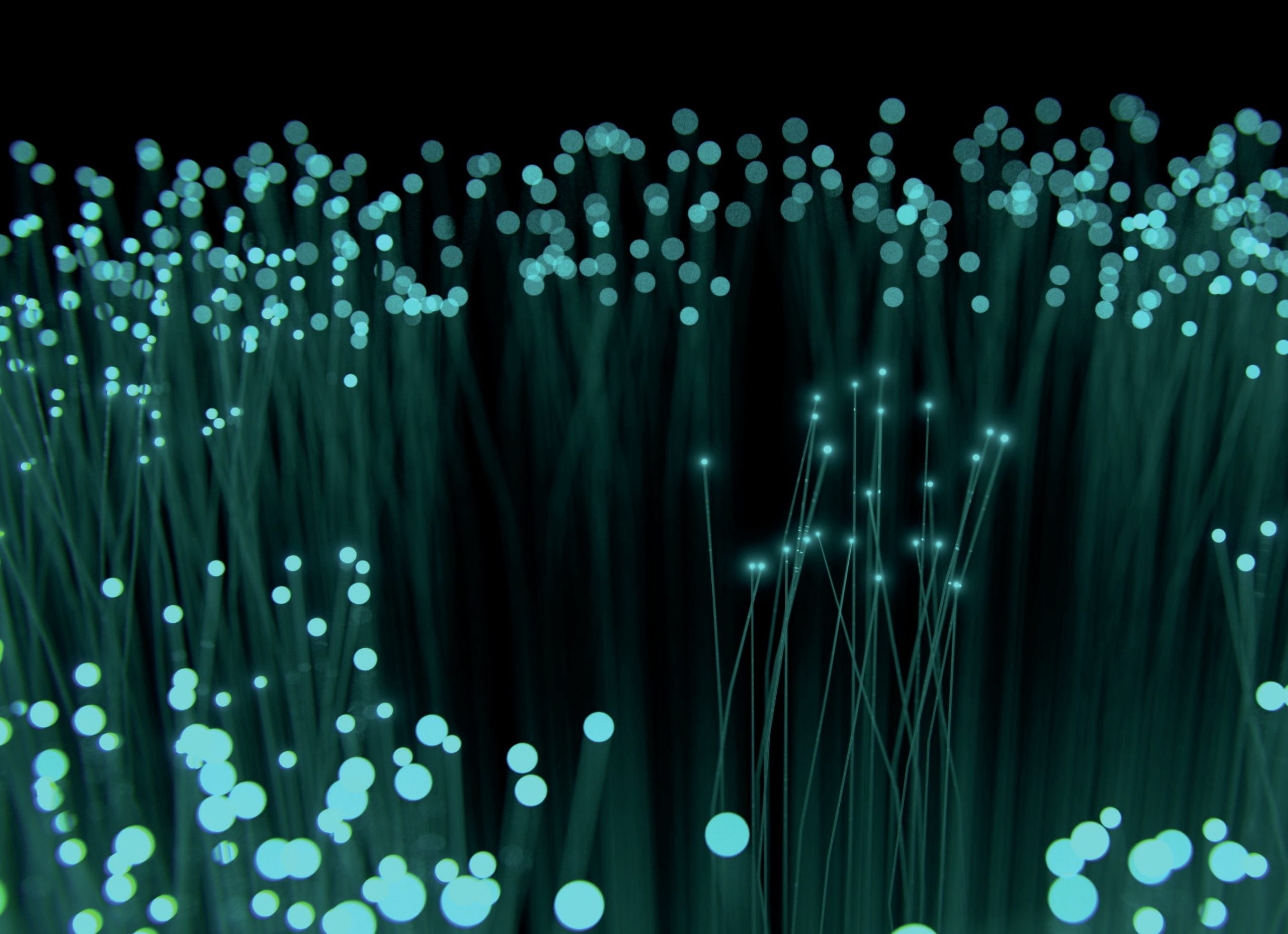
“Sulphur copolymers have also been found to have a high refractive index. Refractive index determines… the light-guiding nature of optical fibres.”
Sulphur’s versatility as an atom is well known; almost as versatile as carbon. Its ability to form chains and rings are responsible for many of its unique properties as a material. Throughout the long history of sulphur’s use, various attempts have been made to harness these properties to enhance the properties of other materials. Perhaps the most widely known is that of so-called vulcanisation of rubber, developed in the 1830s by Henry Goodyear to solve a problem he was having with his rubber tyres – that during hot road conditions the rubber would become sticky and collect debris. He discovered that by heating rubber with sulphur at 140-160°C, the rubber became strengthened and less subject to tackiness at high road temperatures. What had happened was that the sulphur had formed bridging strands of sulphur atoms between the long polymer chains of the rubber, creating a more stable composite material.
For a long time vulcanisation was the main way of incorporating sulphur (not usually in its pure state, but as a disulphide) into materials. However, during the 1960s and 70s, the generation of large volumes of elemental sulphur from sour gas and refinery processing meant the ready availability of elemental sulphur on a large scale and at relatively low cost, and so there were attempts to find uses for all of this excess sulphur. This broadly coalesced into two thrusts; using sulphur as a binder in concrete, and using sulphur as a binder in asphalt. In concrete, sulphur is used at roughly a 20% concentration to replace the cement binder. It produces a faster curing, harder and more wear resistant material with good resistance to acidic conditions. It also avoids some of the CO2 emissions involved in conventional concrete production. Sulphur concrete is licensed by Shell as Thiocrete, and has been used, e.g. for railway sleepers on French and Belgian railways. However, it is generally more expensive than ordinary concrete, and this has limited its use to some niche applications.
In asphalt, sulphur is able to mix more intimately with the various carbon compounds that make up the bituminous base. Sulphur is mixed at around one third to two thirds bitumen in sulphur-extended asphalt (SEA). As with vulcanisation, it is able to cross-link and harden the asphalt, and forms a more durable road material. Shell also produces a pellet additive using sulphur and wax to make SEA, which they market as Thiopave. During the 2000s, Qatar became interested in SEA as a use for large quantities of sulphur being recovered from gas processing, and conducted a programme of research, leading to SEA being used on some roads in the Kingdom. However, concerns about recyclability of the sulphur asphalt (asphalt is often remelted and relaid for road repairs) and the potential for the evolution of hydrogen sulphide during the process, as well as the additional expense of the sulphur, again constrained wider adoption of SEA.
Inverse vulcanisation
More recently, research on sulphur-based materials has begun to focus on the phenomenon of so-called ‘inverse vulcanisation’. Here, rather than sulphur acting as a bridge between carbon polymer chains, sulphur itself can act as a monomer, developing long chains stabilised by carbon bridges instead. Elemental sulphur exists mainly as an eight-atom ring, but this melts at about 159°C to form thiyl radical chains with bi-radical ends forming linear sulphur polymers (polysulphanes). Polysulphanes are unstable and readily depolymerise back to octet rings. But in its molten state is can directly copolymerise with hydrocarbon co-monomers.
In the early 2010s, again due to concerns about the large volumes of sulphur that would be produced from ADNOC’s sour gas extraction, Abu Dhabi’s Petroleum Institute investigated the addition of up to 15% sulphur to low- and high-density polyethylene, as well as polypropylene and engineering plastics such as polyamide. In high density polyethylene (HDPE), the researchers found that the plastic’s elongation at break was increased by up to 50% with the addition of 15% by weight sulphur. This in effect can improve the plastic’s toughness.
Further research has been conducted by other institutes on vinyl copolymers with sulphur, again showing that they have improved tensile strength and breaking strain, toughness and hardness. The cross-linked polymers were also found to be resistant to common solvents but could be chemically dissolved and recycled in dimethylformamide, dimethylacetamide, or n-methyl-2-pyrrolidone (NMP), which could allow intentional removal and recovery. Additionally, despite their cross-linked structure and improved mechanical properties, the polymers were found to still maintain highly recoverable thermal recycling and showed excellent shape memory behaviour even with complex shaped designs, which would not be possible to achieve with poor mechanical properties.
Refractive index
Sulphur copolymers have also been found to have a high refractive index. Refractive index determines the focusing power of lenses, the dispersive power of prisms, the reflectivity of lens coatings, and the light-guiding nature of optical fibres. High refractive index materials are particularly sought for applications requiring high transmission of light, but these are often brittle inorganic materials such as glass, while more flexible materials like plastics often have a low refractive index. A team of researchers at Khalifa University in the UAE has made stable sulphur polymers by reacting elemental sulphur with 1,3-di-isopropenylbenzene cross-linker inside a polystyrene matrix, where it diffuses into the matrix, ensuring even dispersion of the sulphur. The refractive index of the final polymer can be tuned as needed by varying the amount of cross-linkers. These polymers can be molded into obkects or films without altering transparency. And, since they are highly soluble in most organic solvents, they can be made into ultra-thin films that are clear and stable.
Low thermal conductivity
The same team at Khalifa University have also been working on porous sulphur foams with very low thermal conductivity. Water-soluble template-embedded cross-linked polysulphides were prepared and hot-pressed to the required shape and size. Pores were then generated by dissolving the template in water. The porosity of the foam was altered by varying the particle size of template materials. The sulphur foam with a smaller pore size and high porosity showed a significant decrease in thermal conductivity, much lower than that of pristine sulphur and close to high performance insulating materials. The method also allows flexibility to modify the foam structure and properties during preparation and processing.
Environmental sorbents
Sulphur has long been known to form strong bonds with heavy metals such as mercury. Research has therefore also been ongoing on developing sorbents for toxic heavy metals such as mercury using sulphur polymers. As with the thermal foam, above, sodium chloride can be used at up to 70% during the formation process and then dissolved to leave a porous structure which has a higher surface area for binding to mercury.
Lithium sulphur batteries
Finally, sulphur copolymers are finding application in lithium sulphur battery materials. Rechargeable lithium sulphur batteries are a very promising line of battery research with much higher capacities than conventional lithium ion batteries. have drawn significant attention as next-generation energy storage systems, but have suffered from comparatively low numbers of recharge cycles due to the migration of sulphur from cathode to anode. Sulphur copolymers are a promising alternative cathode material to elemental sulphur as they can mitigate this problem. Recent research shown that polysulphides hs can be tuned in terms of sulphide chain lengths and the resulting reaction pathways during electrochemical cycling. The improved cyclability of these cathodes comes from carbon cross-links acting as anchors that fix the polysulphides to the polymeric network during cycling, preventing their diffusion into the electrolyte.
Early days
This is clearly a very promising field of study, but one of the more surprising things about current research into sulphur copolymers is how little studied they are, especially structurally. In part this is due to them often having low solubility in organic solvents that allow them to be processed in IR spectrophotometers etc. In terms of new uses for sulphur there are clearly many different avenues potentially open, with battery cathodes one of the largest scale potential uses, although the impact on the overall sulphur market for such high performance and relatively niche uses is likely to be limited. Perhaps this is just as well; one of the things that tends to be repeated in the preambles to papers on the subject is the notion that sulphur is widely available and cheap. As anyone who buys or sells sulphur knows; this is not necessarily always the case, and as fossil fuels are phased out, sulphur may become more expensive and sought after.
References