Fertilizer International 514 May-Jun 2023
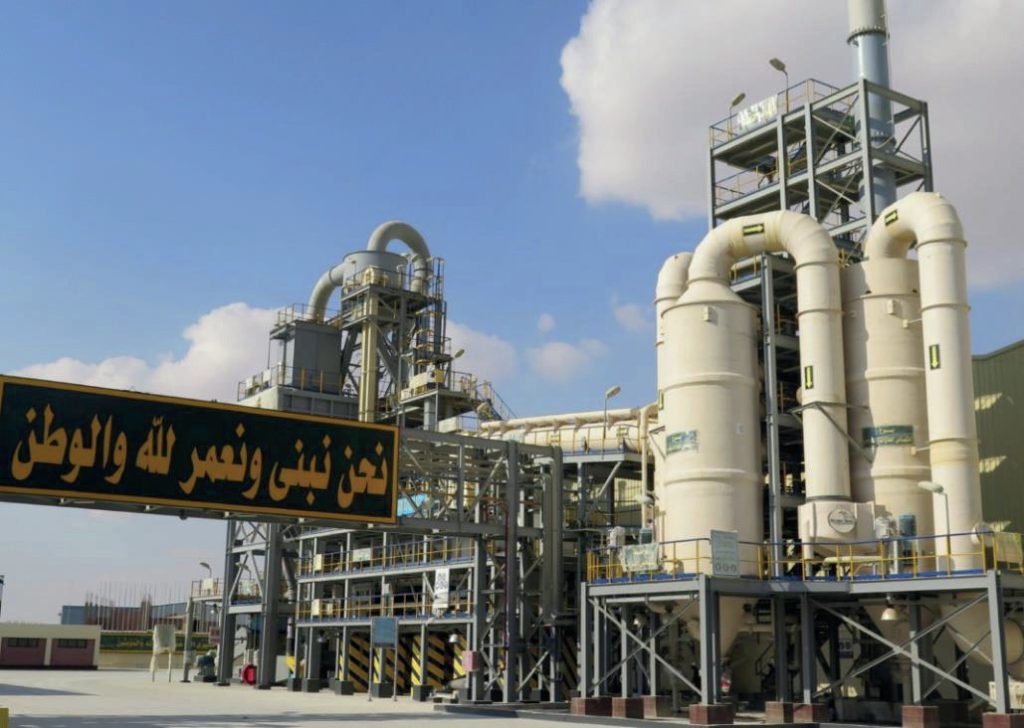
31 May 2023
Innovative gas scrubbing at SSP plants
PHOSPHATE TECHNOLOGY
Innovative gas scrubbing at SSP plants
Single superphosphate (SSP) is relatively easy and cheap to make. Yet traditional gas scrubbers often limit production and create plant maintenance issues.Fortunately, an innovative scrubbing technology developed by Armatec Environmental can overcome many of these problems.Based on high efficiency void towers, this new approach helps SSP producers meet stringent global emissions standards, explains Armatec’s Shane Pope, while simultaneously maximising production and improving worker conditions.
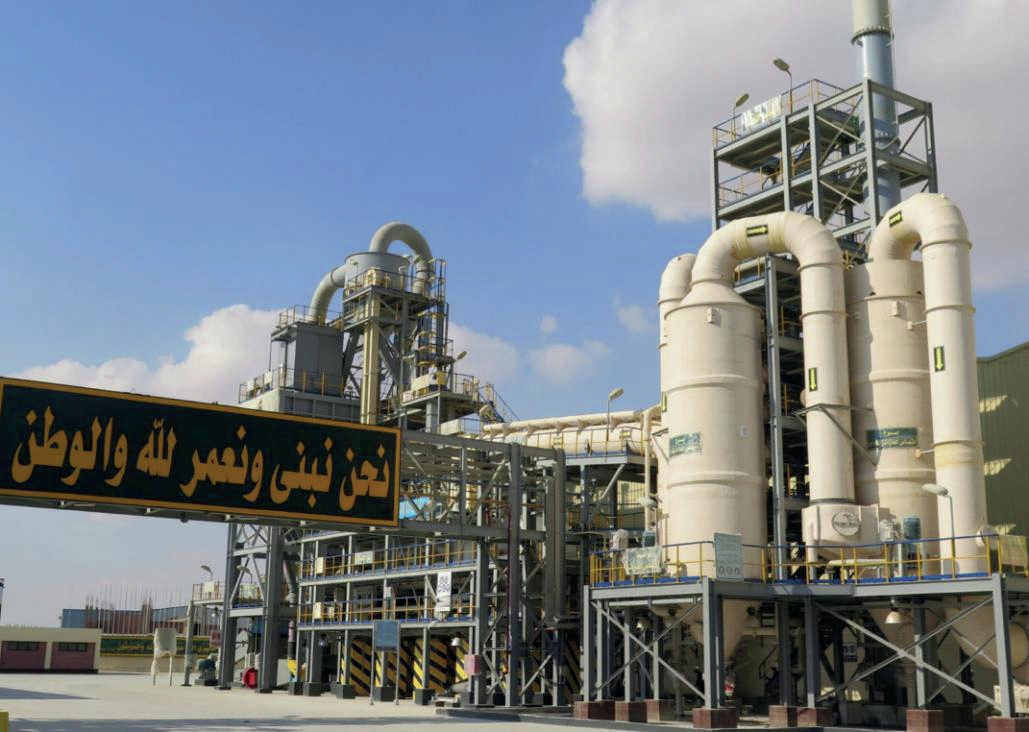
Single superphosphate (SSP) is a well-known and long-established fertilizer. Currently, it is seeing a resurgence in popularity as other energy-intensive fertilizers have become more costly to make.
SSP is produced by reacting phosphate rock with sulphuric acid in a mixer. The resulting mixture is then cured – usually in a den with a moving floor. The process reaction produces steam and fumes that contain numerous contaminants. These must be scrubbed before discharging to the atmosphere.
From a scrubbing perspective, the most challenging contaminant is fluoride, evolved as both hydrogen fluoride (HF) and silicon tetrafluoride (SiF4 ). In wet scrubbers, fluoride is absorbed by water to produce hydrofluorosilicic acid (H2 SiF6 ), known as FSA or HFA. The cleaned gas is then discharged to the atmosphere via a stack.
Emissions limits
In recent years, many countries have reduced the allowable discharge of fluoride from the stack plumes of phosphate fertilizer plants. This is due to the increasing awareness of the atmospheric pollution from these emissions.
A total fluoride limit of 5 mg/Nm3 , as recommended by the World Bank and others, is now being used as a common benchmark around the world. This mean that many phosphate plant scrubber systems, which may have been acceptable previously, are no longer capable of meeting discharge requirements. Upgrades are therefore required to meet the new and more stringent emissions limit.
The scrubbing challenge
The scrubbing of fumes generated by the SPP production process is uniquely challenging:
1. Very high removal efficiency is required. Fluoride levels in the fumes emitted from the den can range from 5,000-50,000 mg/Nm3 . To reduce these to the current global standard of 5 mg/Nm3 therefore requires a scrubber efficiency in excess of 99.9 percent.
2. The hydrofluorosilicic acid (FSA) resulting from the scrubbing process is noxious, corrosive and dangerous. Traditional materials such as steel quickly corrode. The FSA is also laden with silica solids, making it even more difficult to handle.
3. The silica produced as an unavoidable scrubbing reaction by-product deposits itself throughout the system, creating blockages in pipes, ducts and spray nozzles if not carefully managed. Regular cleaning is therefore vital to maintain plant operation.
4. The cleaning of traditional scrubber systems can be dangerous, especially where entry to confined spaces is required. The corrosive acid present during cleaning, along with the potential for injury from falling solids, are hazardous to workers.
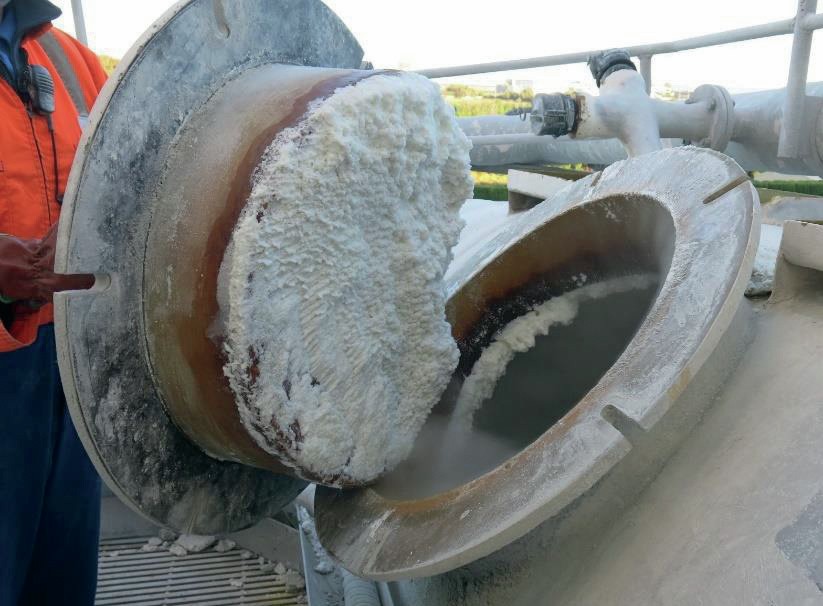
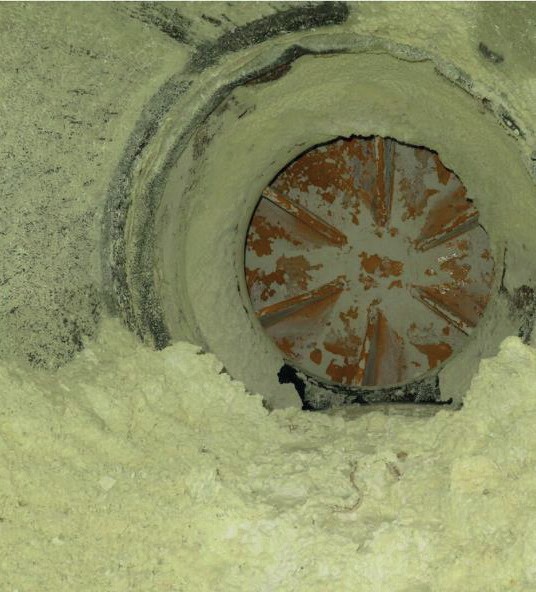
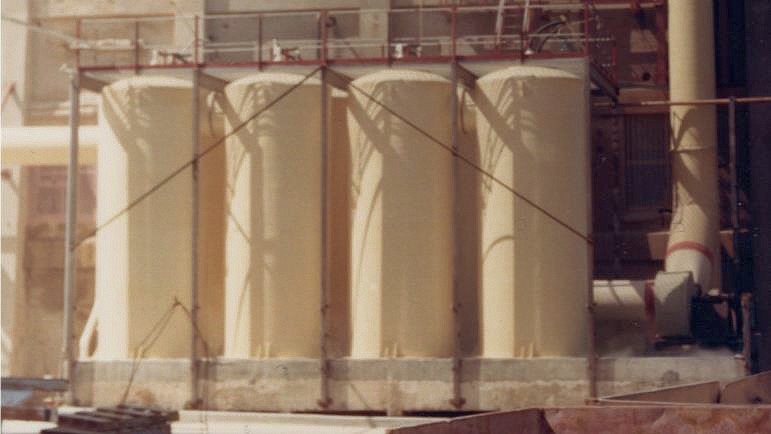
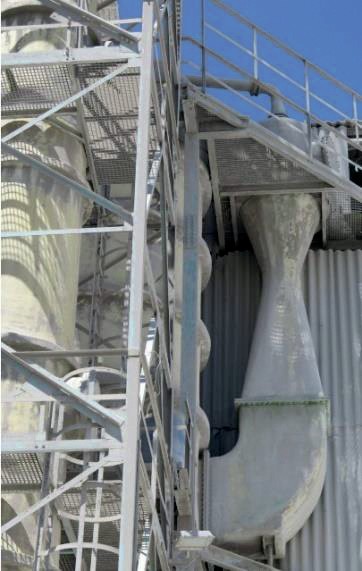
Because of these challenges, many SSP plants face the following difficulties with their scrubber systems:
- They have to run at reduced production rates so as not to exceed stack emissions limits
- They face regular, often unexpected, plant shutdowns to clear blockages
- Operation and maintenance of scrubber systems can be risky and hazardous for workers.
As a consequence, the scrubber system ends up becoming the bottleneck for plant production.
Yet it shouldn’t be this way – as clever design can manage these myriad challenges. What’s needed is a high efficiency, multi-stage scrubbing system that is robust and easy to operate and maintain.
Traditional scrubbing approaches
Historically, three different approaches to scrubbing have been used at SSP plants.
Void towers are one traditional approach. At the top of these is a single spray nozzle, often arranged in multiple stages over a common sump, with scrubbing achieved using both counter-current and co-current water flow.
The benefit of void towers is that scrubbing efficiency is not significantly affected by silica build-up. They don’t block like packed towers can, and their scrubbing efficiency is not highly dependent on geometry like a venturi scrubber. This means that scrubbers can continue to operate even with significant silica deposits.
There are, however, several problems with traditional void towers:
- The systems have limited removal rates and struggle to achieve today’s strict emissions limits.
- Having the scrubbers installed over a common open sump means that workers are continually exposed to FSA liquor and fumes.
- Access for maintenance and cleaning can also be difficult and dangerous.
Another approach is to use a crossflow scrubber. In these systems, air passes horizontally through a packed bed and is contacted with scrubber liquor sprayed onto and flowing down through the packing. While crossflow scrubbers can achieve higher removal rates than traditional void towers, there is significant risk of the packing blocking with silica deposits. If this happens, cleaning can be difficult and time-consuming.
The third approach seen at SSP plants is venturi scrubbers. These can achieve quite high removal rates and have a smaller footprint relative to void towers. Nonetheless, Armatec has observed several limitations with venturi scrubber systems:
- A high energy requirement is necessary to overcome the pressure drop required for contaminant removal. Because of this, multiple fans are sometimes needed to move the air through the system.
- Mist carryover can limit overall system efficiency. Mist eliminators are needed at each scrubbing stage to address this. These can be prone to silica blockages, depending on the style of mist eliminator.
- Scrubber efficiency is highly dependent on the geometry inside the venturi throat. This geometry is affected by silica deposits with scrubbing efficiency decreasing as silica builds up – putting the plant at risk of exceeding its stack emissions limits.
Because of the above limitations, clients in New Zealand and elsewhere are now replacing their venturi scrubber systems and adopting a new approach instead.
High efficiency void towers
To overcome the limitations seen in other systems, Armatec has developed a new approach based on high efficiency void towers. Known as Fluorisorb, the full system comprises:
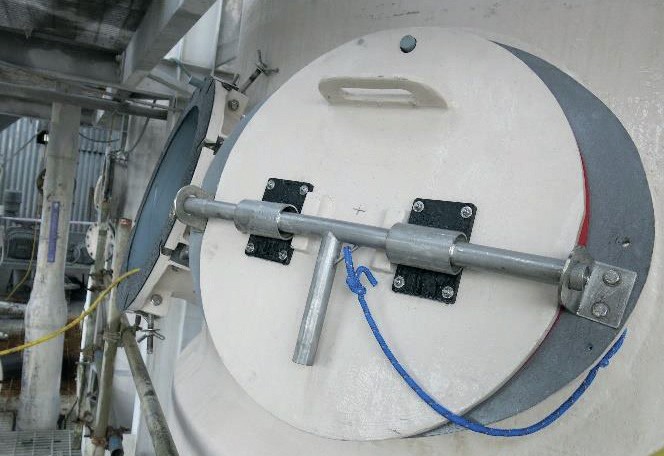

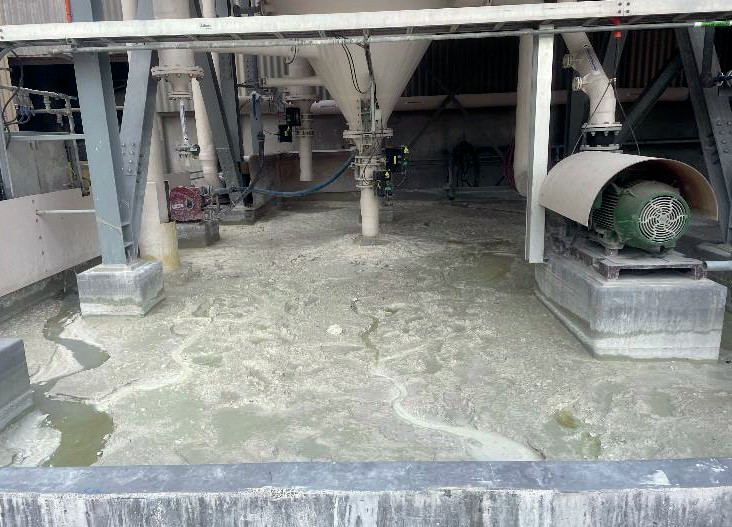
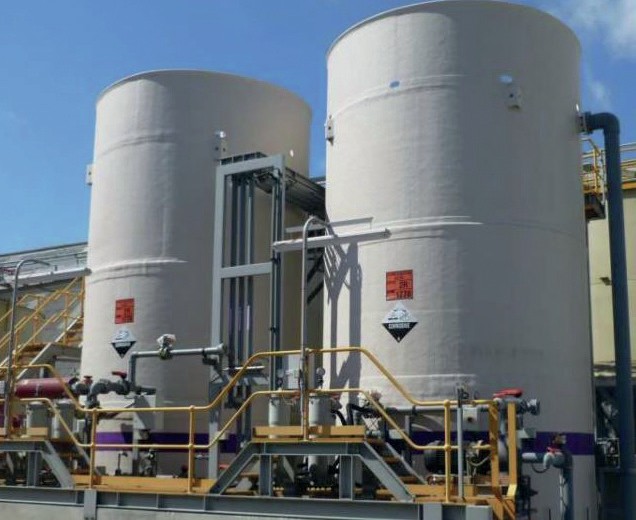
- Multiple stages of high efficiency void towers to provide the high removal rates needed to meet the most stringent emissions standards
- Liquid flows counter-current to the gas stream to maximise efficiency
- Scrubber liquors are contained to prevent worker exposure to corrosive acid and fumes
- Quick and safe access for inspection and maintenance is provided.
Scrubbing systems based on Armatec’s Fluorisorb technology provide the following benefits:
- By using void towers, robust operation with high scrubbing efficiency is guaranteed, even in the presence of silica deposits
- High efficiency scrubbing is achieved by the system’s true counter-current design and the use of multiple sprays
- The incorporation of design features to handle silica deposits reduces blockages and subsequent down-time
- Clever design and strategically placed quick release access hatches provide quick and safe cleaning without entry to confined spaces.
Fluorisorb systems can be tailored to site-specific operating conditions. In some upgrade projects, for example, clients opt for a new Armatec system to completely replace their old scrubbing system. Others want to incorporate new Armatec technology within their existing scrubbing system to achieve improved performance while minimising costs. As engineers, we enjoy the challenge of finding the best solution for each client!
In summary, clients who have upgraded to Armatec scrubbing systems can run their plants at higher capacity rates without fear of exceeding emissions limits. They can also plan production around scheduled maintenance shutdowns for cleaning. Maintenance and cleaning are simple and safe and unscheduled stoppages due to blockages are extremely rare.
Eliminating Effluent
A further benefit to Armatec scrubber systems is the opportunity to eliminate liquid effluent.
Wet scrubbing at SSP plants, as previously mentioned, produces silica-laden hydrofluorosilicic acid (FSA) – leaving operators with the challenge of what to do with this scrubber liquor. Some clients concentrate and purify the FSA and then sell it for water fluoridation. Others neutralise and dispose of the FSA through a wastewater treatment system, although this solution can be costly.
A more attractive option for plant operators is to return the FSA to the process. This is achieved by introducing FSA to the mixer, alongside the sulphuric acid, so that it takes part in the reaction. This reduces – and even entirely eliminates – the amount of FSA handled elsewhere in the process.
But there is a potential difficulty with this approach: returning FSA to the mixer results in a significant amount of the fluoride being re-evolved back to the scrubbers. This can increase the fluoride load on the scrubbers anywhere from two to ten times. Therefore, to cope with this extra load, the scrubbing system must have a removal efficiency capable of achieving the required stack emissions, even with significantly higher incoming fluoride.
Armatec can design systems with the necessary efficiency to maintain stack emissions within required limits, even when 100 percent of the FSA is returned to the mixer. This provides operators with a zero effluent process as a potential option. Some alterations to the mixer are necessary to achieve this – which Armatec is well equipped to advise on.
Armatec has developed the Fluorisorb system based on its work with SSP clients for 30+ years. This technology can be applied to new SSP projects or incorporated as an upgrade at existing SSP plants. Case studies of two projects carried out with clients to upgrade their SSP scrubbers are provided below.
Case study 1: Replacing venturis
Prior to the upgrade, this client was using a scrubbing system comprised of three venturis. These had been acquired from another site and re-purposed. The system had a number of failings:
- SPP production was limited by scrubber performance
- Silica was being deposited throughout the system including in the fan
- Cleaning and maintenance were also difficult
- Caustic consumption at the plant was high to try to compensate for poor scrubber performance.
In the first phase of the upgrade, Armatec replaced the first venturi with a high efficiency void tower. Scrubbing performance immediately improved, and cleaning and maintenance became easier. The client could produce high strength FSA for sale for water fluoridation. But there were still issues.
The second phase of the upgrade saw the replacement of the second and third venturis with two more high efficiency void towers. All client goals were achieved:
- Scrubbing efficiency was maintained with a 47 percent higher air flow rate and 20 percent less water consumption
- The prevention of further silica deposition in the fan improved plant operation and reliability
- Caustic consumption was greatly reduced.
The site engineer reported that, “The scrubbers take everything we throw at them!”
Case study 2: Zero effluent system
Prior to the upgrade, this client’s traditional void tower scrubber system had the following performance issues:
- The site was not meeting its stack emission consent limits
- Production was being limited to try to reduce these stack exceedances.
The client wanted to upgrade the scrubber system to unlock more production while at the same time meeting their consent conditions.
In the first phase of the upgrade, Armatec retrofitted the existing towers to improve their performance and added a new Armatec high efficiency void tower. As a result:
- The client was able to unlock additional production capacity and meet their emissions limits
- The upgrade also enabled the site to eliminate their liquid effluent, which led to the operator winning an environmental award for their work.
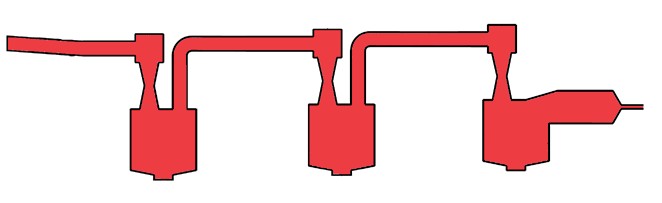
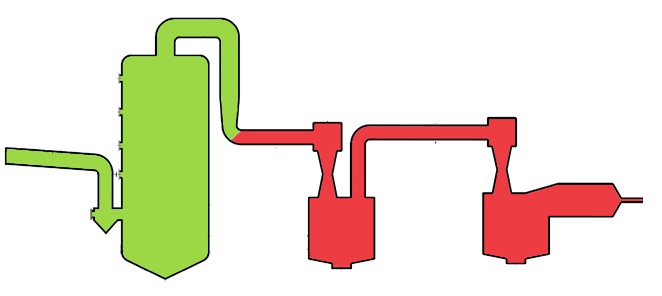
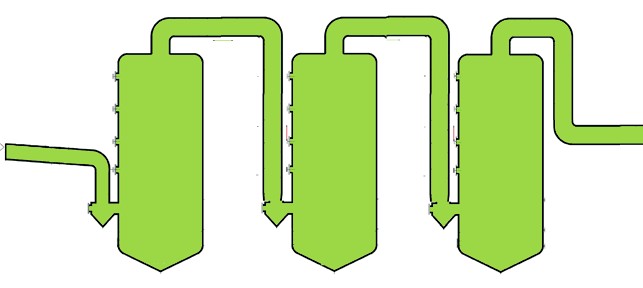
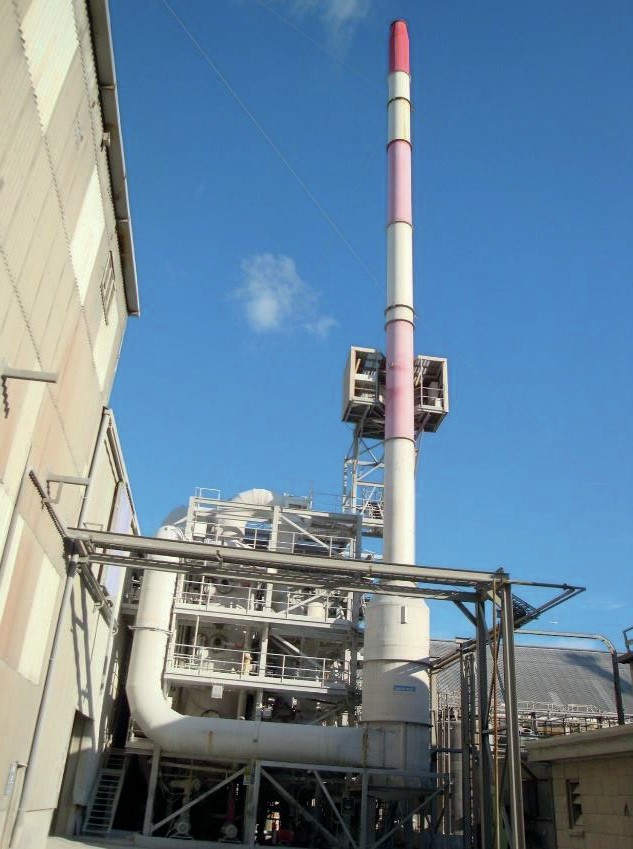
The old towers, which were at end of their useful life, have now been replaced as part of the recently completed second phase of the upgrade. This has improved system reliability and unlocked extra production capacity while still complying with emissions regulations.
Conclusion
Single superphosphate (SSP) production is often limited by poor scrubber systems that limit plant output, exceed emissions limits, and cause hazards for workers. By understanding the limitations of previous approaches, Armatec developed its Fluorisorb scrubber system to help plant operators meet emissions limits while unlocking production capacity and making plant operation and maintenance simple and safe.
This innovative scrubbing technology is based on 30+ years of working with SSP clients in New Zealand and elsewhere. Fluorisorb systems are now being sought all over the world, as clients seek to meet stringent global emissions standards, while simultaneously maximising their production and improving conditions for their workers.
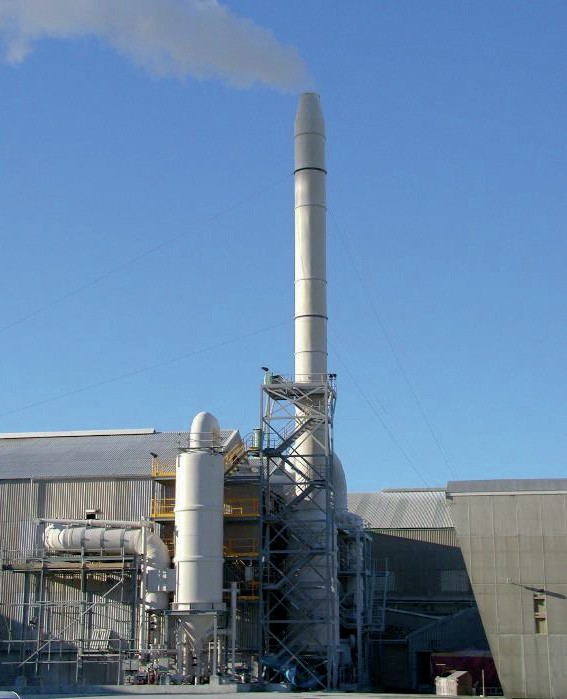
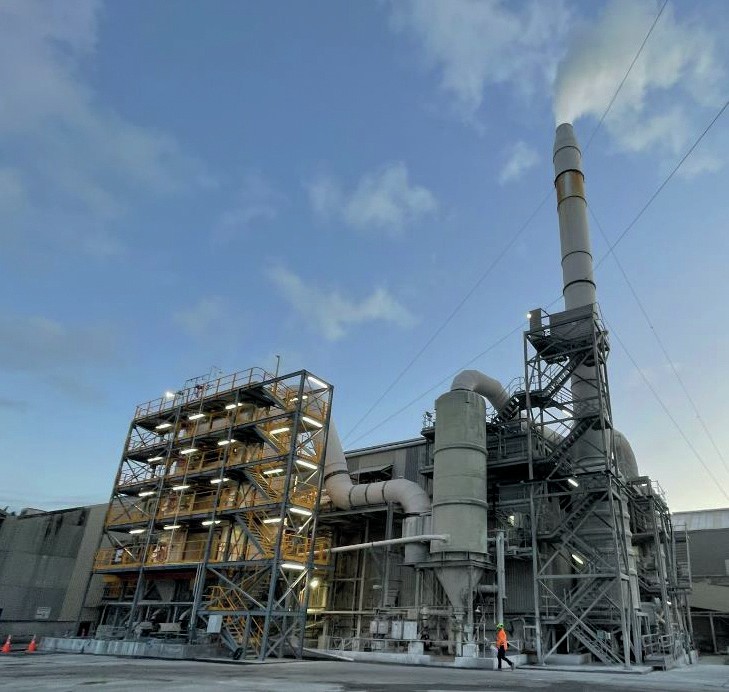