Nitrogen+Syngas 383 May-Jun 2023
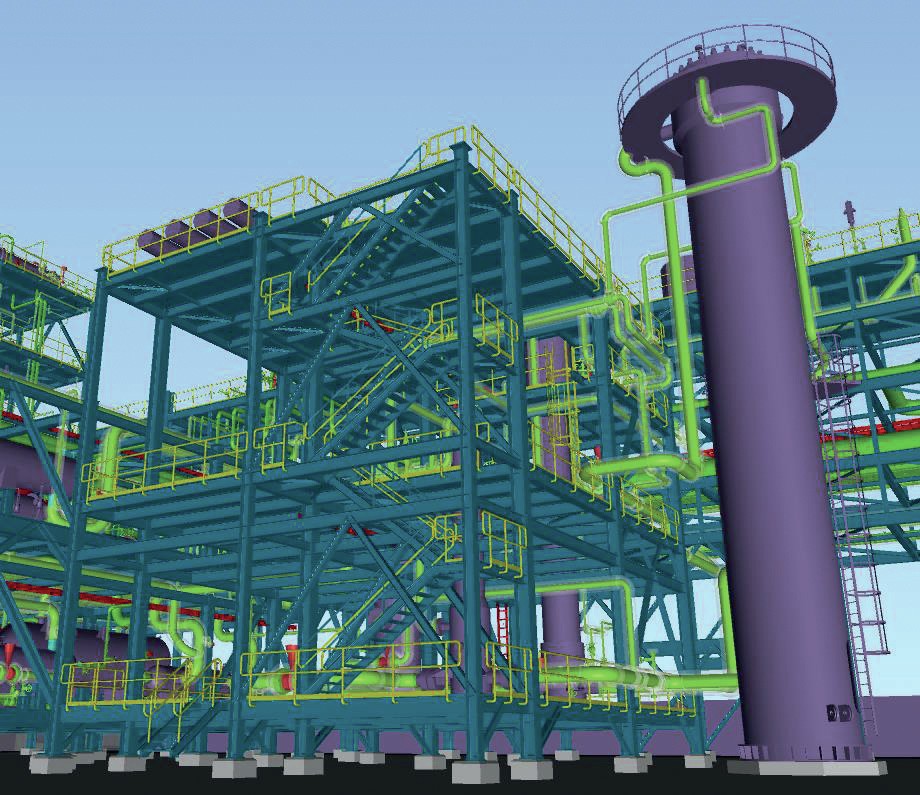
31 May 2023
Modularisation, front and centre
GREEN AMMONIA
Modularisation, front and centre
With the market for green ammonia set to grow significantly in the coming years, modularisation of ammonia plants can bring many benefits to new projects, including optimised cost, speed of delivery and reducing overall risks. thyssenkrupp Uhde is committed to further develop standardised, modular solutions for its clients. Tobias Birwe and Dustin Mayor explain the company’s modularisation concept.
Even in times of a slowing global economy with several countries on the brink of a recession, labour markets are persistently tight in most parts of the world – this is true for many branches from leisure and hospitality to engineering and especially so for the construction industry. For example, the total unemployment rate in the US has remained almost unchanged from its very low levels of 3.6% in March 2022 down to 3.5% in March this year.
Furthermore, there has been a significant shift of investments from conventional, grey, fossil fuelled technologies to blue and green alternatives, especially in the US, Europe, Middle East and Australia.
thyssenkrupp Uhde expects the market for green ammonia to outperform traditional ammonia markets as early as 2026, followed by a very dynamic market growth afterwards. For Australia alone, this could lead to a clean ammonia capacity of approximately five million tonnes per annum by 2030.
Green solutions have even higher demands in terms of optimised cost, speed of delivery, higher predictability especially in terms of supply chain security and therefore reduced overall execution risks. This is why, despite the already known benefits like better safety performance, potential cost savings and higher price and schedule accuracy, modularisation is becoming front and centre in the development phase of many capital projects. thyssenkrupp Uhde is therefore committed to further develop standardised, modular solutions for its clients, supporting the decision process for the application of modularisation and to increase its modular footprint.
For more than 100 years, thyssenkrupp Uhde has been successfully serving its clients with its ammonia plants. Together with its competence centre for modularisation in Thailand, the concepts of prefabrication, preassembly, modularisation and offsite fabrication (PPMOF) are also increasingly applied to its core technologies, offering a range of modularisation services from project management, concept planning, preliminary engineering, detailed design, procurement up to construction management and commissioning.
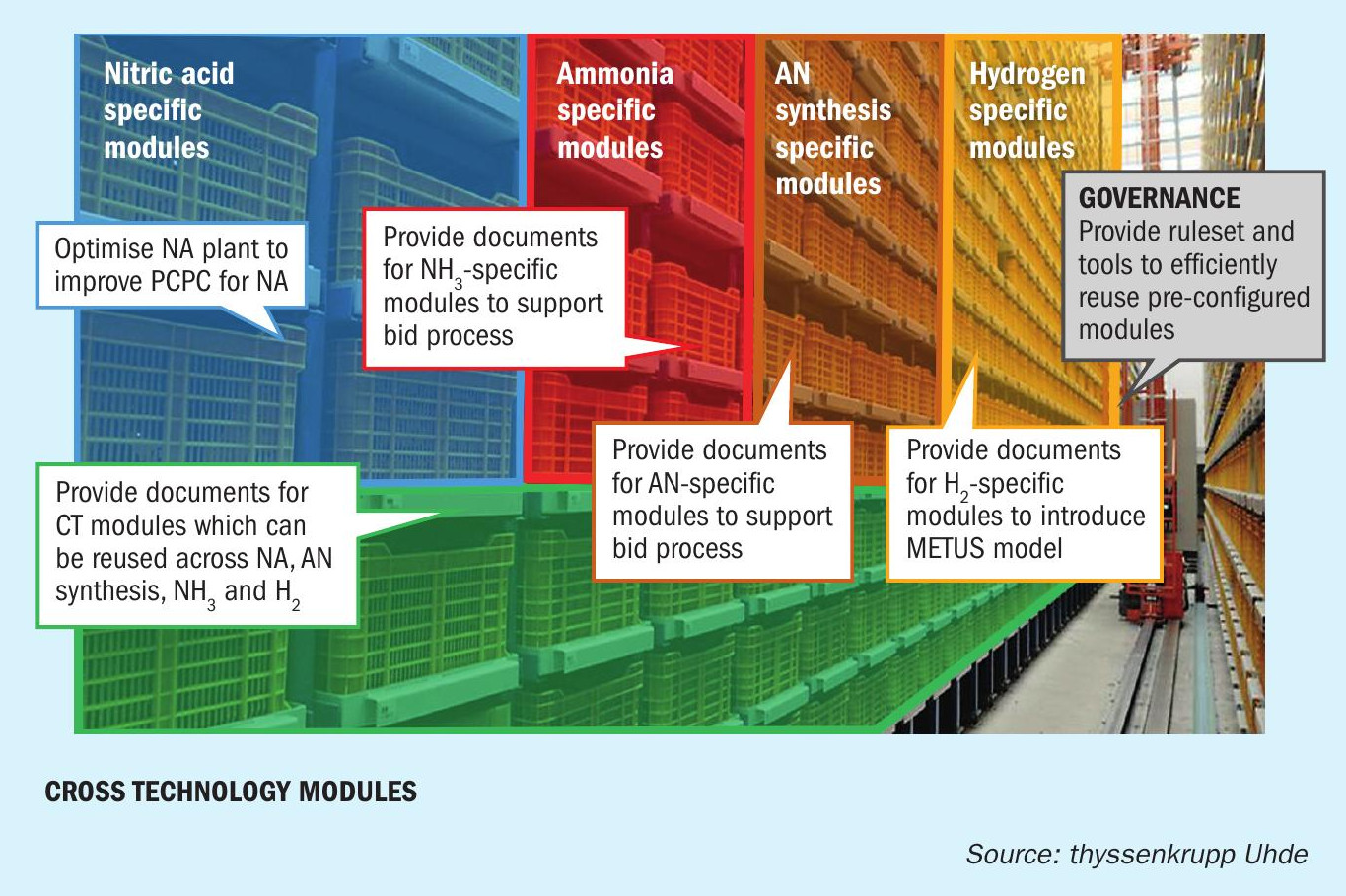
thyssenkrupp Uhde differentiates its modularisation efforts into geometrical and functional modularisation. While geometrical modularisation describes the planning, engineering and fabrication of a physical module, functional modularisation defines the plant process from a predefined standard plant as per the relevant, specific requirements of the project.
Functional modularisation
Functional modularisation is done through thyssenkrupp Uhde’s self-developed preconfigured plant concept (PCPC). As briefly outlined already, it looks at modularisation from another angle. Plants configured by PCPC are adapted to the specific project requirements starting from a well defined standard plant. These standard plants divided into functional modules have been developed not only for ammonia plants, but also other technologies including nitric acid, ammonium nitrate and hydrogen. thyssenkrupp Uhde illustrates these functional modules as standards which can be taken from a “plant warehouse” (see Fig. 1). Deviations from specific project requirements to the standard plants are identified and can be linked directly to the functional modules using so-called variant drivers.
While functional modularisation is already the standard for certain technologies at thyssenkrupp Uhde, the extent of application of geometrical modularisation on a specific project must be determined individually for each project. This is done by an analysis of the value-add in terms of reduction of risks and cost advantages versus conventional stick-built solutions. Geometrical modularisation is applied so that the overall benefits to the project outweigh the additional challenges and cost imposed to the project, which result among others from the addition of material (especially steel), logistic complexity and transportation cost and higher engineering costs.
In addition, thyssenkrupp Uhde’s approach for functional modularisation increases the quality of its early engineering deliverables through its standardised and pre-defined approach. Further, it shortens the time required for their development. Therefore, this concept enables the fast and early development of a clear set of engineering documents as a starting point which allows the customer to evaluate the impact of their project requirements on the plant design at an earlier stage. In this way, different project scenarios can be evaluated efficiently together with customers.
Geometric modularisation
geometric modularisation instead is defined as “the method of plant design which enables fabrication and assembly of a large proportion of the plant to take place in a location remote from the project site”, typically consisting of four categories:
- PAU/PAM (pre-assembled units/modules);
- PAR (pre-assembled racks);
- VAU (vendor assembled unit);
- VPU (vendor packaged unit).
Other aspects of PPMOF include precast concrete, dressed columns and prefabricated buildings.
Modules generally consist of equipment items arranged in modular steel structures and buildings that can be assembled off-site, transported to site and lifted into place. The equipment is connected with piping to the fullest practical extent, instrumentation is installed and cabled to junction boxes, lighting and cabling is installed, steelwork is fireproofed up to the connection points, tracing and insulation on equipment and piping, and painting is completed as far as is practical, as illustrated also in Fig. 2.
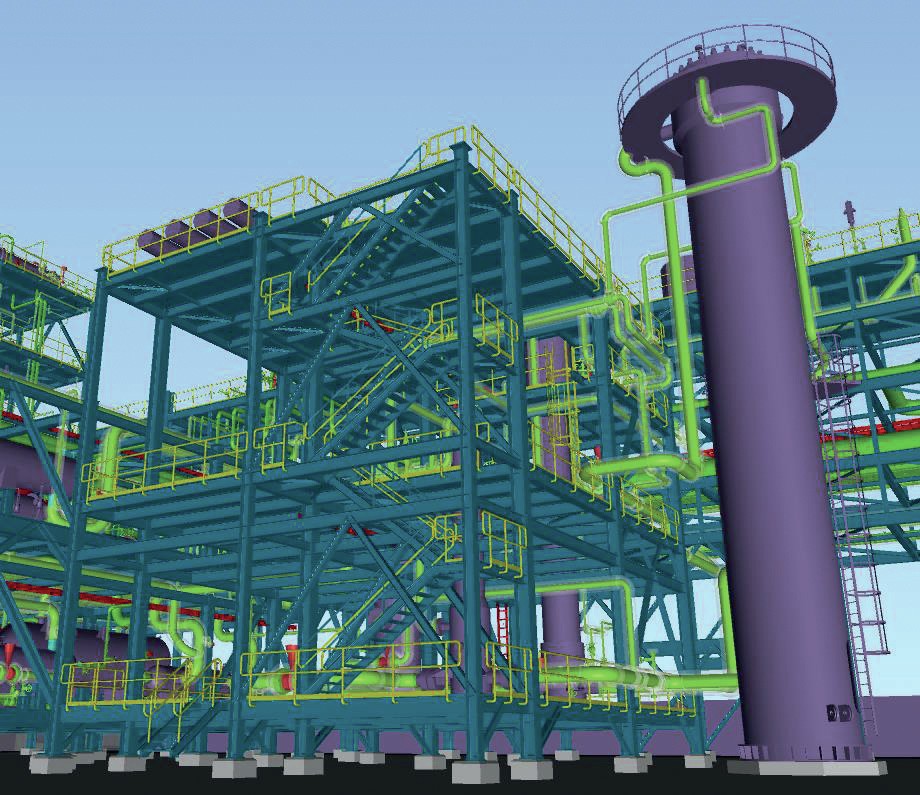
The size and scope of modules are only limited by the physical constraints of the transportation route to the site location and the available capacity of heavy lift and transportation equipment. Therefore, a preliminary transportation study, undertaken during the feasibility stage, is essential for any modular project. However, in case of the development of a standardised, modular plant, it is recommended to target smaller, truckable modules to be applicable for most site locations.
For standardised, modular plants, these modularisation concepts should be applied in a way that the plant process is split system-wise into physical modules (and submodules). The final module allocation of each component is shown in all relevant execution documentation. It is further understood as good engineering practice to arrange and connect such resulting process modules alongside and to a central pipe rack and avoid any inter-module piping connections. A constructability study finally assures the proper consideration of construction knowledge already in the early project phases especially related to erection sequencing on site and planning of heavy lifts.
For many applications, this value-add is given since geometric modularisation is a very effective way to improve quality by fabricating modules in more controlled environments off-site. It also increases productivity, enables cost savings from shifting site costs to workshop costs, increases reliability of schedules and mitigates site risks. Another significant lever for cost reduction results from the potentially smaller footprint required for a modular plant compared to a stick-built arrangement. Past engineering studies carried out by thyssenkrupp Uhde resulted in a reduction of land requirements of up to 30% – an achievement thyssenkrupp Uhde also seeks to increasingly apply to its ammonia plants. Further, it increases HSE and industrial relations performance. Finally, geometrical modularisation enables more sustainable project delivery through the reduction of impacts on local communities and infrastructure.
Conclusion
thyssenkrupp Uhde and many of its customers recognise that both concepts combined, functional and geometrical modularisation, yield a powerful basis for efficient project development and execution, with a significant value-add for many project applications. Especially within the last two years there has been a rapid increase in modularisation applications, in order to increase project predictability, mitigate labour shortages and reduce overall risks – a trend which is expected to continue. n