Sulphur 406 May-Jun 2023
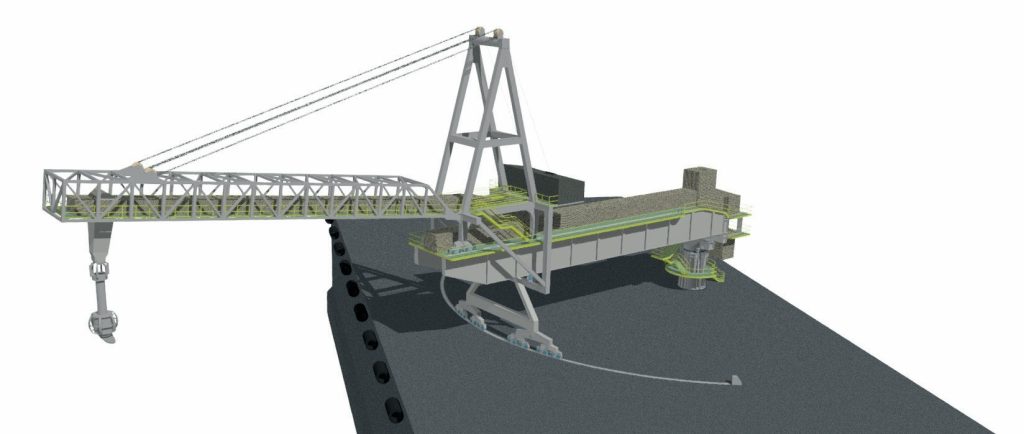
31 May 2023
Sulphur Industry News Roundup
Bedeschi to supply sulphur handling equipment
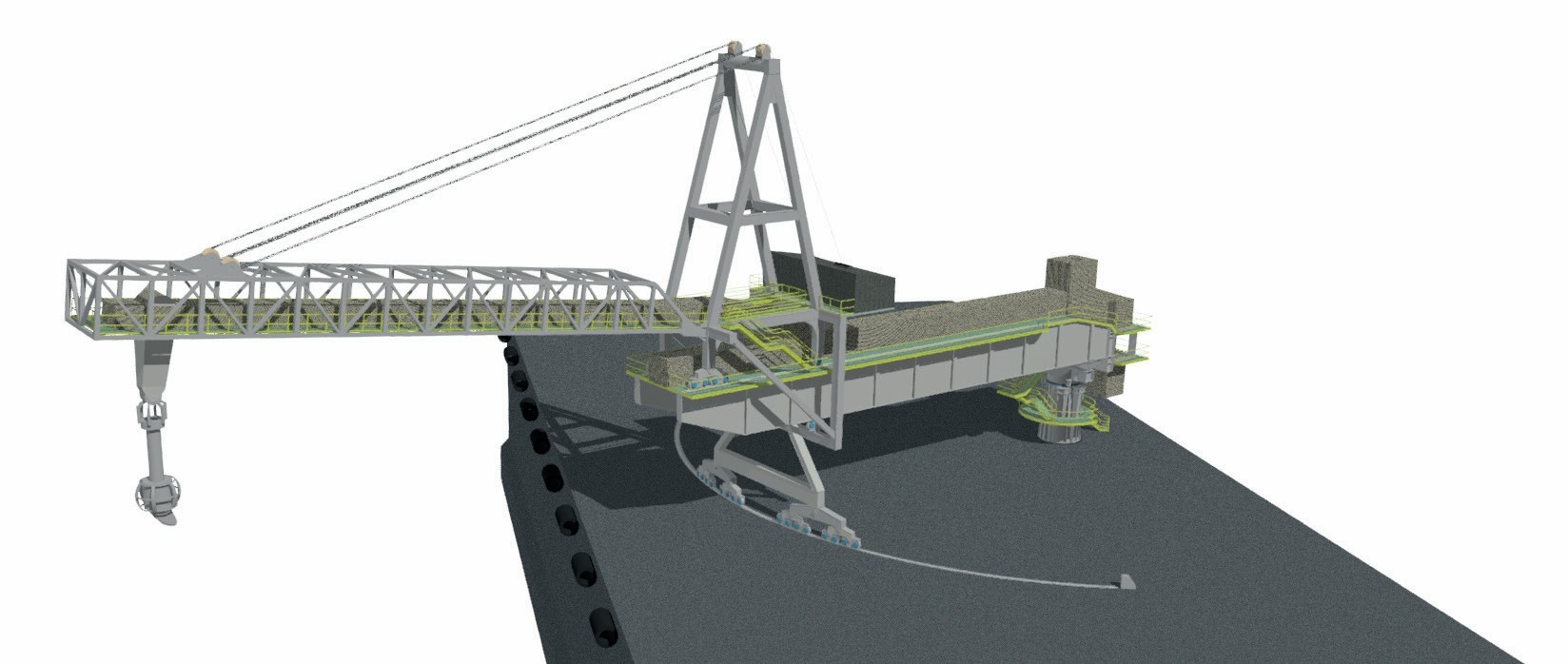
Bedeschi has been awarded a contract by Tecnicas Reunidas and Wison Engineering for the engineering and supply of new sulphur-handling equipment. Tecnicas Reunidas and Wison Engineering are working in a 70-30 joint venture partnership on the North Field Expansion Project (NFXP) Sulphur Project, which forms part of the overall Qatar North Field Expansion Project. Last year were awarded a $600 million contract to process and export sulphur from the projected expansion of the liquefied natural gas (LNG) facilities in Ras Laffan Industrial City. The new sulphur plant will have the capacity to process an average of 5,000 t/d of molten sulphur.
As part of their contract, Bedeschi will supply six conveyor belts with a total length of 1,400 meters with a capacity of 550 t/h, including galleries and transfer towers; four conveyor belts with a total length of 480 meters with a capacity of 2,000 t/h, including galleries and transfer towers; one conveyor belt with a total length of 120 meters with a capacity of 3,700 t/h, with gallery and transfer tower; two trippers with a capacity of 550 t/h; a double arm portal reclaimer with a capacity of 2,000 t/h; a travelling slewing shiploader with a capacity of 2,000 t/h; and a radial shiploader with a capacity of 3,700 tonnes per hour.
KUWAIT
Axens to license technology for gas-treatment plants
Axens says that it is supplying the process design packages for the gas treatment of two gas plants in North Kuwait. The engineering, procurement and construction contract is being managed respectively by SPETCO and Jereh. Axens is licensing two HySWEET units for acid gas removal, as well as two Smartsulf units for the sulphur recovery and two triethylene glycol (TEG) units for gas drying. The units for both gas plants are now under process design phase and the plants will be commissioned in early 2024. Each HySWEET unit will treat 163.4 million scf/d of gas to remove the acid gases including H2S, CO2 , COS and mercaptans to meet sales gas specifications.
HySWEET is a hybrid process for simultaneous removal of mercaptans and acid gases from natural gas, developed by TotalEnergies and commercialised by Axens. It is based on the selection of the most suitable non-proprietary physical solvent for blending a variety of commercial amines (DEA, MDEA, formulated MDEA) and maximises mercaptans removal along with the absorption of the acidic species while minimising hydrocarbon co-absorption which can potentially be harmful for the downstream sulphur recovery unit.
KAZAKHSTAN
NCOC sued for excess sulphur storage
The Kazakhstan Ministry of Ecology and Natural Resources says that it has filed a lawsuit against the North Caspian Operating Company (NCOC) consortium, the operator of the Kashagan oil field, for breaching safety guidelines for storing sulphur. The country’s Oil and Gas Strategic Partnership Development Council (Petrocouncil) further reports that the Ministry is suing for a total of $5.1 billion for what it describes as “environmental pollution”. At issue is the volume of sulphur being stored at the Bolashak oil and gas treatment plant, which receives and processes associated gas from the giant offshore Kashagan field. There are six sulphur pads with a reported total permitted capacity of 730,000 tonnes, but according to a government environmental audit seen by Petrocouncil, total storage allegedly reached 1.7 million tonnes in November 2022. The Ministry also alleges that the sulphur was not covered with a membrane as per local regulations to prevent sulphur dust being carried away from the site. Other allegations include a lack of dust suppression, dumping waste water without treatment and failure to recycle water, and lack of automated emissions monitoring. NCOC said in response that it had no information about the government lawsuit and that the company carries out its sulphur management activities responsibly and in accordance with the laws of Kazakhstan, as well as in accordance with applicable standards and best practice.
This is not the first time that the Kazakh authorities have cracked down on operating companies in the country over alleged environmental breaches. In 2012 Kazakhstan obtained a 10% stake in the Karachaganak Petroleum Operating Company project as a result of the settlement of a dispute running back several years, and again including alleged violations of sulphur storage regulations and H2 S emissions monitoring, and there are suggestions in local media that the government is “flexing its muscles” to try and put pressure on operators to extract more money or a better deal over upcoming projects. The government is also looking to increase transhipment costs for oil by up to three times their current value by May 1st.
NCOC normally produces around 1.4 million t/a of sulphur and exports 1.0-1.2 million t/a of this overseas.
UNITED STATES
Battery can use non-chemical grade sulphur
Houston-based Zeta Energy says that it has developed a safe, low-cost, high performance, and sustainable battery for the electric vehicle and energy storage markets, which can use ‘unrefined’ sulphur in its proprietary lithium sulphur battery technology with no loss of performance. This means Zeta can produce batteries with locally available sulphur just about anywhere in the world rather than having to use highly pure chemical-grade sulphur.
Sulphur is considered an ideal battery material because of its potential for extremely high energy density, low weight and low cost, but historically a problem known as the “polysulfide shuttle effect” has resulted in low cyclability of sulphur-based batteries. Zeta uses a proprietary sulphurised carbon material which prevents this effect, resulting in sulphur-based cathodes with better stability and performance.
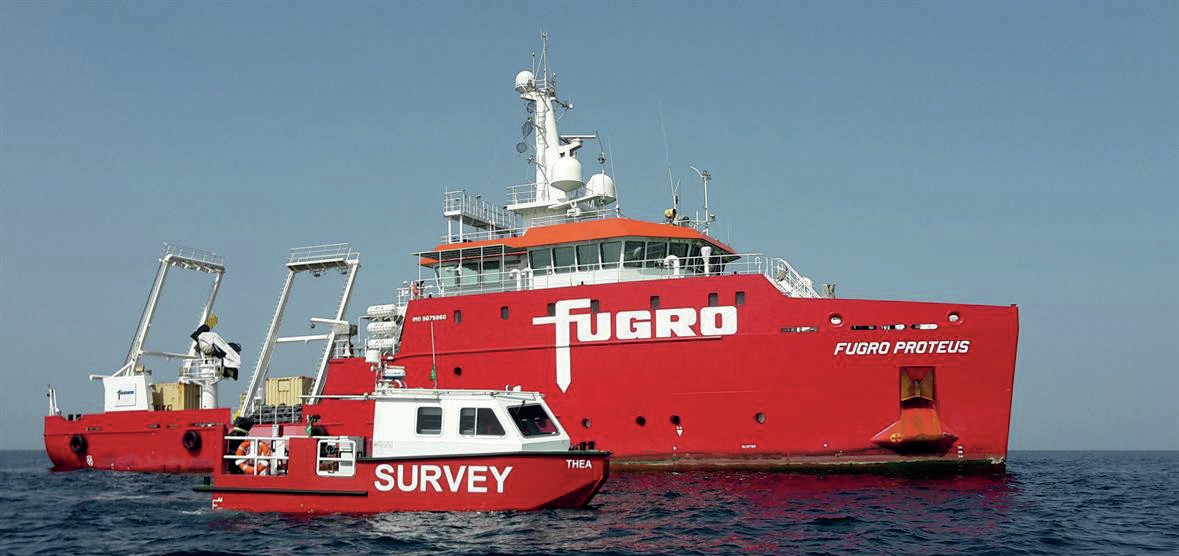
Chief Science Officer Rodrigo Salvatierra commented, “We are absolutely thrilled with these results. Most companies working with sulphur use highly purified chemical grade sulphur, which has higher cost and requires more energy and processing time. We have now shown that our processes work with unrefined sulphur, such as that derived from oil refining or used in the fertilizer industry, with no additional refining steps. This gives us a big advantage in our ability to meet the actual low cost of sulphur, and increase the sustainability, of making batteries.”
LIBYA
Bids invited for gas processing complex
Libya’s state-owned National Oil Corporation (NOC) has invited prequalification bids from contractors to build a major new gas production complex and export pipeline at its Atshan project in the onshire Murzuq basin. In 2019, NOC gave the go-ahead for its wholly-owned subsidiary the Zallaf Oil & Gas Exploration and Production Company to begin work on a plan to process large volumes of associated gas from the Murzuq basin, lose to the border with Algeria. The pipeline specifications call for a 24” line which can transport up to 200 million scf/d of treated dry gas from the Atshan field to the Obari power plant. The power plant is currently fuelled by oil and switching to gas will allow Libya to export an addition 15,000 bbl/d of oil. The Atshan gas processing plant will have a capacity of 280 million scf/d of gas. Libyan gas is typically around 0.6-1.0% hydrogen sulphide.
UNITED ARAB EMIRATES
Contract for offshore services
Fugro says that it has been awarded a contract for site characterisation services in support of “one of the largest long-term field development programmes in the United Arab Emirates”. Although Fugro did not name the project, ADNOC’s largest offshore development is the Upper Zakum field; the fourth largest oil field in the world. Production currently runs at 750,000 bbl/d, but ADNOC plans to lift that to 1.0 million bbl/d next year and has further expansion plans out to 2030.
Fugro says that from April 2023, it will perform a series of offshore surveys including geophysical, geotechnical and remotely operated vehicle (ROV) inspections supported by advanced engineering and geo-consulting studies to help inform the Front End Engineering Design (FEED). The project consists of approximately 600 km pipeline route assessment with 800 crossings, 49 jacket surveys and island offshore surveys.
Tim Lyle, Group Director Middle East and India at Fugro said: “We are delighted to be supporting a project of such calibre. This significant award will allow Fugro to support our client’s vision and sustainability targets whilst strengthening our commitment to in-country value (ICV) by working closely with our local supply chain.”
SAUDI ARABIA
Aramco to begin refinery construction
Aramco and joint venture partners NORINCO Group and Panjin Xincheng Industrial Group say that they will start construction of a major integrated refinery and petrochemical complex in northeast China in the second quarter of 2023. Huajin Aramco Petrochemical Company (HAPCO), a joint venture between Aramco (30%), NORINCO Group (51%) and Panjin Xincheng Industrial Group (19%), is developing the complex. It will combine a 300,000 bbl/d refinery and a petrochemical plant with a production capacity of 1.65 million t/a of ethylene and 2 million t/a of paraxylene. Construction is due to start in the second quarter of 2023 after the project secured the required administrative approvals. It is expected to be fully operational by 2026. Aramco will supply up to 210,000 bpd of crude oil feedstock to the complex, which is being built in the city of Panjin, in China’s Liaoning province.
Mohammed Y. Al Qahtani, Aramco Executive Vice President of Downstream, said: “This important project will support China’s growing demand across fuel and chemical products. It also represents a major milestone in our ongoing downstream expansion strategy in China and the wider region, which is an increasingly significant driver of global petrochemical demand. “
Zou Wenchao, NORINCO Group Deputy General Manager, said: “This large-scale refinery and petrochemical complex is a key project of NORINCO Group to implement and realize the joint development of the high-quality Belt and Road initiative, promote industrial restructuring, and enhance the oil and petrochemical sector to become stronger, better and larger. It will play an important role in deepening economic and trade cooperation between China and Saudi Arabia, and achieving common development and prosperity.”
Jia Fei, Panjin Xincheng Chairman of the Board, said: “The project is of great significance for Panjin to promote increasing chemicals and specialty products, strengthening integration of the refining and chemical industry. It is a symbolic project for Panjin as it seeks to accelerate the development of an important national petrochemical and fine chemical industry base.”
Aramco has also made other recent investments in China. It has agreed to acquire a 10% stake in the private Rongsheng Petrochemical Co Ltd for about $3.6 billion. The deal includes the supply of 480,000 bbl/d of crude oil to the Rongsheng-controlled Zhejiang Petrochemical Corp (ZPC) for 20 years. Aramco has also signed a memorandum of understanding with the southern Chinese province of Guangdong to explore cooperation in sectors including energy, finance, research and innovations.