Nitrogen+Syngas 383 May-Jun 2023
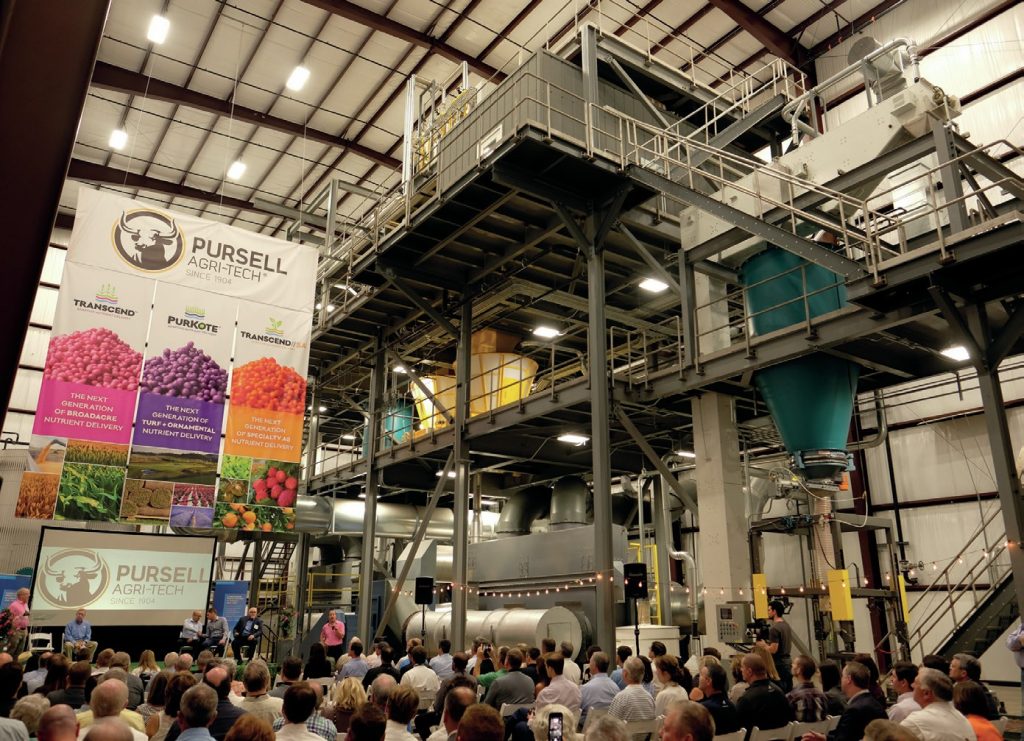
31 May 2023
Sustainable fertilizer production
FERTILIZERS
Sustainable fertilizer production
Pejman Djavdan, CEO of Stamicarbon looks at the ways in which the fertilizer industry must grapple with issues such as decarbonisation, sustainability and more efficient use of nutrients.
One of the most urgent problems confronting humanity this century is how to feed a growing global population in a sustainable way, in harmony with the planet and its finite resources. The second United Nations Sustainable Development Goal is to “end hunger, achieve food security and improved nutrition and promote sustainable agriculture.” It is an important and ambitious goal, especially as the world’s population continues to increase rapidly – from around two billion in 1927 to three billion in 1960 and more than doubling to seven billion in 2011. By 2055, this figure is predicted to be around ten billion. In addition to exponential population growth, we also see an increase in the amount of food consumed per capita. The Food and Agriculture Organisation (FAO) of the United Nations has estimated that global crop production needs to increase by more than 45% by 2050 if we want to end hunger and malnutrition1 .
It is clear that we need to intensify crop and food production to be able to feed the world population and achieve food security. The urgent and challenging question is how to do this in a sustainable manner. How do we make sure that we grow sufficient crops and produce sufficient food that has better quality, is economically available for everyone and has less impact on the environment and our planet?
Mineral fertilizers play a significant role in the intensification of agriculture – responsible for more than half of the world’s food production – but their production and application also present several challenges. Stamicarbon, MAIRE’s innovation and licensing company engaged in nitrogen technologies believes that technological innovations are vital in contributing to solving global food challenges by intensifying agriculture while at the same time protecting the environment.
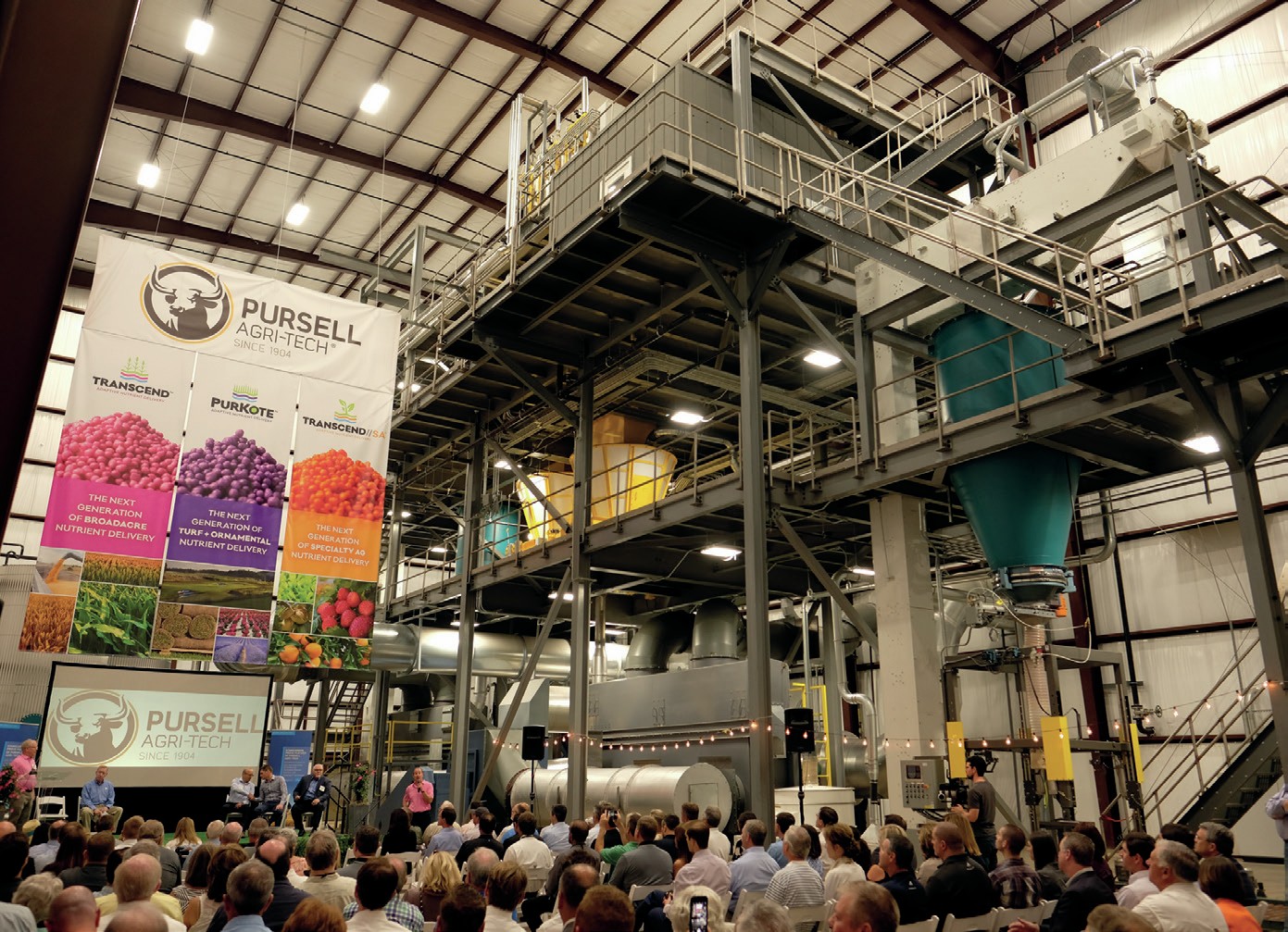
The company aims to decrease emissions and energy consumption and increase fertilizers’ nutrient use efficiency (NUE). To achieve that, Stamicarbon is focusing its strategic research and development efforts on two main areas:
- Sustainable production of nitrogen-based fertilizers from sustainable feedstocks and renewable energy sources;
- Making fertilizers more efficient and effective to increase their NUE.
Sustainable fertilizer production
In the past, most technological innovations in the fertilizer sector were driven by economies of scale and capacity increases. Today, the industry must focus on producing and using fertilizers with the lowest possible environmental impact. Adding nutrients to plants allows them to grow faster and stronger, resulting in higher yields and wider availability of certain foods. But this comes with a price for the environment, with global fertilizer production responsible for about 1.4% of CO2 emissions yearly2 .
There is an evident need to balance using fertilizers for intensifying agriculture and reducing their carbon footprint. Conventional processes that rely on fossil fuels (such as coal and natural gas) for fertilizer production must be redefined to ensure a sustainable, environmentally-friendly future. To address this challenge, Stamicarbon introduced its Stami Green Ammonia technology while further investigating the production of nitrates directly from renewable energy and renewable resources.
Green ammonia production relies on water electrolysis to produce green hydrogen instead of using natural gas or coal as feedstock. In the green ammonia process, green hydrogen from electrolysis is used together with nitrogen from air, and the entire ammonia production is powered by renewable or carbon-free energy resources (see Figure 1). The resulting green ammonia is then used to produce nitrogen fertilizers such as ammonium nitrate.
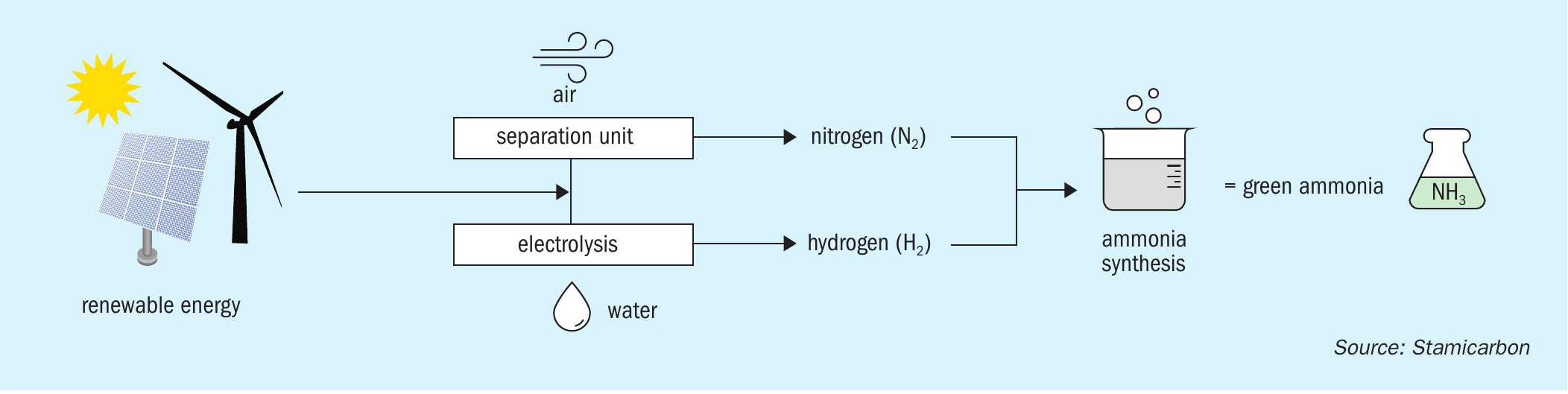
Considering that ammonia production causes about 1% of total greenhouse gas emissions, green ammonia represents a significant leap forward for sustainability in the fertilizer industry while also offering opportunities for collaboration between the fertilizer and energy markets. This collaboration is already being explored by Stamicarbon in the EU-funded INITIATE project to use carbon-rich off-gases from steel mills as feedstock for fertilizer production.
Green ammonia project highlight
Stamicarbon has recently completed a pre-feasibility technical study with Minbos Resources to determine the most suitable plant configuration for producing green nitrate products from renewable electricity in Angola. The green ammonium nitrate production complex is to be located in Malanje Province, east of the capital Luanda.
The study assessed the production of two types of nitrates: calcium ammonium nitrate to be used as a fertilizer in the domestic market and low density ammonium nitrate for the mining industry in neighbouring countries. The production complex combines Stami Green Ammonia and Nitric Acid technologies, including the nitrates finishing in partnership with INCRO. The complex will use up to 200 MW of 100% renewable electricity from the nearby Capanda hydroelectric dam.
Sustainable fertilizers
Not only will the production of fertilizers become increasingly more sustainable in the future, but fertilizers themselves need to become more effective, efficient and environmentally friendly. Here NUE plays an important role. NUE can be described as the ratio between the nutrient input of fertilizers and the nutrient output of harvested crops.
The challenge with existing fertilizers is that many nutrients are lost to the environment as they volatilize into the air or leach into the soil. Consider that: up to 60% of nitrogen ends up in the air or surface water3 ; up to 85% of phosphorus is unused in the first year of application4 ; up to 80% of potassium is not taken up by cereal crops5 ; and up to 80% of sulphur is immobilised or lost to surface water6 .
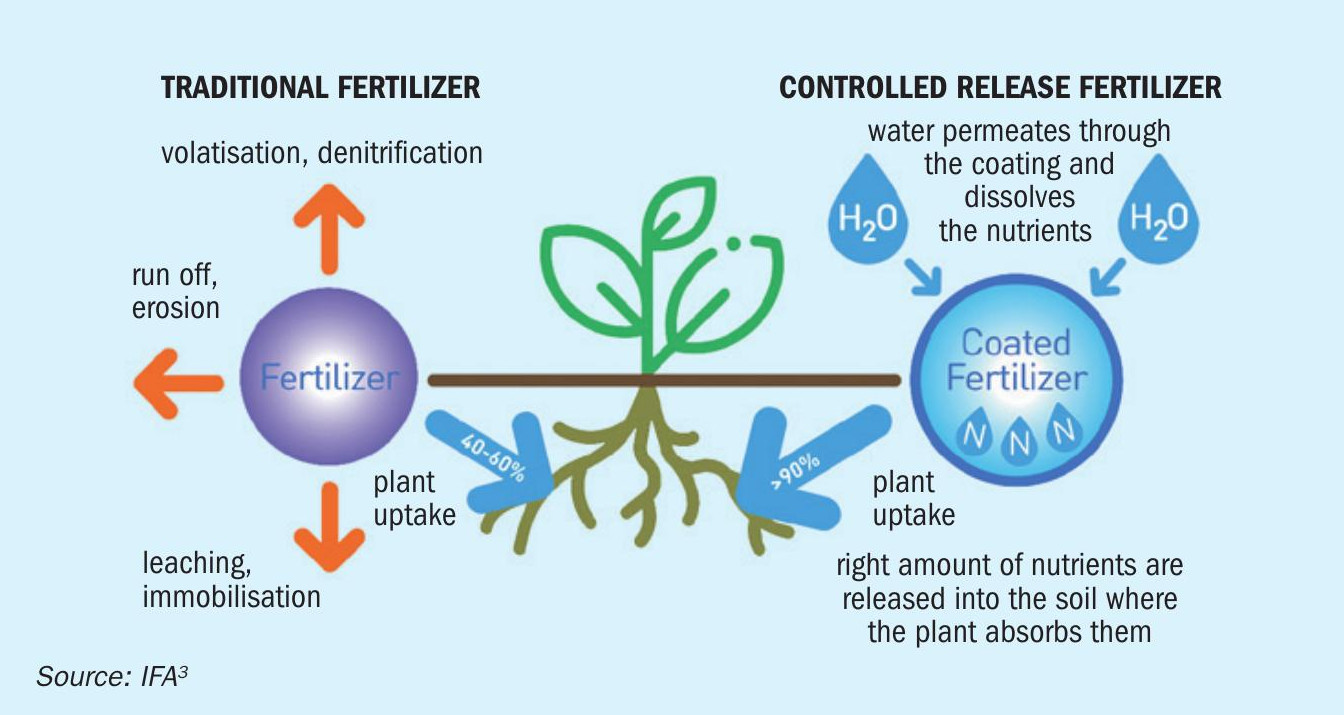
These losses can have undesirable consequences for the environment and human health, such as high levels of nitrates and phosphorus in groundwater, ammonia volatilisation, and emissions of nitrogen oxides and nitrous oxide. Enhanced efficiency fertilizers (EEFs) and multi-nutrient fertilizers are essential in mitigating nutrient losses from fertilization and improving the NUE.
Enhanced efficiency fertilizers
EEFs include controlled-release, slow-release and inhibited fertilizers. These innovative fertilizers prevent nutrient losses by inhibiting the biological transformations in the soil (inhibited fertilizers) or controlling the release of nutrients (slow- and controlled-release fertilizers). Most commonly EEFs are nitrogen products. For example, urea can be coated with sulphur, supplying nutrients at the same rate as the uptake by the plant, with the added benefit of delivering a small amount of sulphur. Another example is a coating where a membrane around urea facilitates the controlled release of nutrients to the soil, preventing the oversupply of nutrients after fertilizer application and minimising nutrient losses to air or ground water.
Innovative fertilizers apply the 4R principle: they deliver the right nutrients at the right time, place, and rate. Stamicarbon partnered with Pursell Agri-Tech in the USA to further develop and license controlled-release fertilizer technology in 2018 (see photo). This technology minimises nutrient losses during fertilization, improving the NUE (see Figure 2) and helping to address the challenge of feeding the growing population with – and decreasing the environmental impact of – fertilizer use. As a next step, the company is currently working with partners on developing biodegradable coatings for controlled-release fertilizers and adding (micro)nutrients to fertilizers.
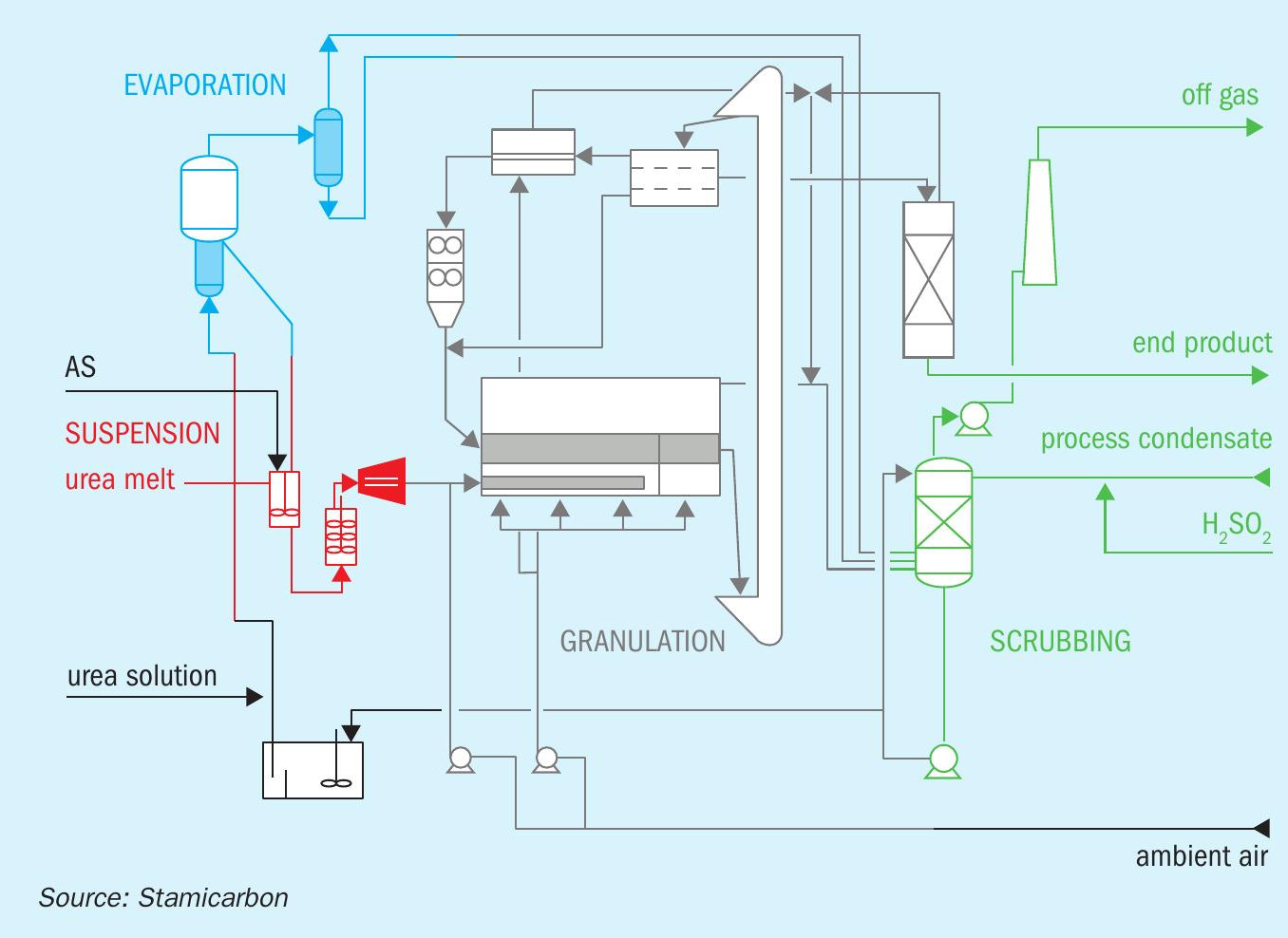
Multi-nutrient fertilizers
For a long time, farmers relied on single-nutrient applications, most commonly with a nitrogen-based fertilizer. However, different crops require different macronutrients (e.g., potassium, phosphorus, calcium, magnesium and sulphur) and micronutrients (e.g., boron, iron, zinc and copper) for optimal growth. The required amounts and ratios of those nutrients change during the growth cycle. Adding the necessary macro-and micro-nutrients in a single fertilizer granule could help improve the NUE.
Flexible technologies for compounding urea or ammonium nitrate with other nutrients can increase the NUE by offering the plants the right nutrients at the right time. Stamicarbon has developed a process for producing granular urea ammonium sulphate (UAS) that will help to reduce nutrient loss due to ammonia volatilisation (see Figure 3). UAS applied to the soil will improve crop quality and yields and can be used for various crops, such as barley, wheat, oats, grassland, rapeseed, etc. The UAS process is flexible and enables the production of urea with the addition of other macro- and micronutrients.
Geographic location, type of crop and soil conditions will determine the economic advantages of improved NUE for farmers. In China, where the overapplication of nitrogen has presented a challenge, farmers can benefit from savings on fertilizer usage. In areas with nutrient depletion and lower crop yields, such as sub-Saharan Africa, improving NUE will help increase yields. And in Europe and the USA, where yields are high and the NUE is improved, reducing the environmental impact of fertilizers could play a decisive role in the choice of fertilizer.
A new era
On March 2, 2023, MAIRE announced its 2023-2032 strategic plan; “Unbox the Future.” The strategic plan maps out a new phase in the Group’s industrial cycle, building on its innovative technologies and engineering capabilities based on more than 100 years of history in chemistry. The Group is accelerating its positioning in the energy transition by leveraging its two new business units: Sustainable Technology Solutions and Integrated Engineering and Construction Solutions.
Stamicarbon is ready to further accelerate the energy transition in the fertilizer industry, leveraging cutting-edge technologies for future-proof fertilizer production. The future demands a high level of sustainability and industries are stepping up their investment in the production of sustainable fertilizers. Sustainability involves transitioning from a traditional fossil-based industrial model to a new low-carbon-based model through transforming processes and economic systems. This transition is also supported by governmental incentives and regulations.
The future of fertilizers
There is awareness both in the fertilizer industry and wider society about the increasing need to boost agricultural productivity while at the same time reducing its environmental impact. These two may seem contradictory when viewed from a polarizing angle, however, both are important and need to be addressed simultaneously.
A change is needed to build a future where humanity, industries and the planet can thrive. This involves continuous transformation aimed at solving global challenges with breakthrough solutions.
Stamicarbon is determined to be part of the solution by continuously innovating and improving technologies, collaborating with its partners, customers and suppliers and challenging the status quo.
Stamicarbon is pioneering with a higher purpose to enable the world to feed itself and improve quality of life.
References