Nitrogen+Syngas 384 Jul-Aug 2023
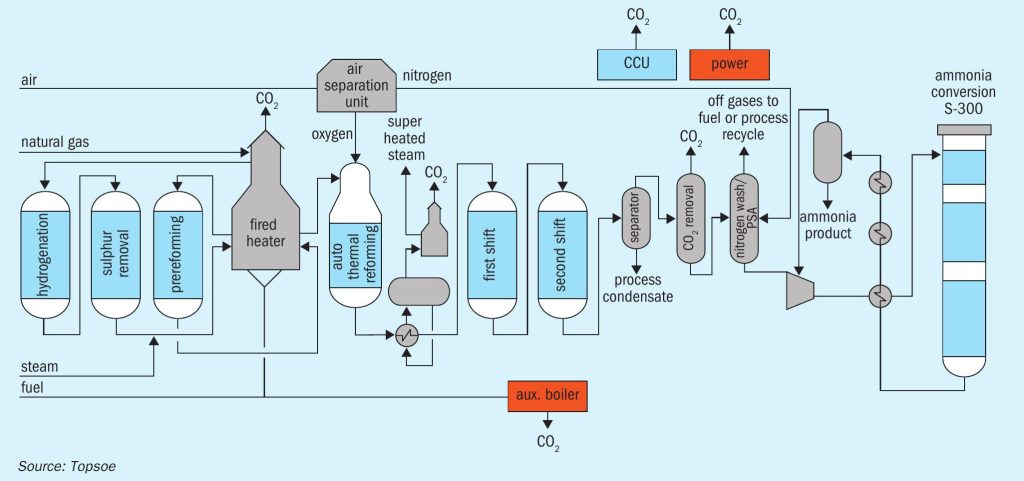
31 July 2023
Ammonia production at scale with the lowest carbon intensity
BLUE AMMONIA
Ammonia production at scale with the lowest carbon intensity
Hydrocarbon-based production of ammonia carries an unavoidable carbon footprint. But one of the best methods for mitigating that footprint is already here: ultra-low carbon-intensity ammonia production, also known as “blue” ammonia. With blue ammonia production, a typical ammonia plant can sequester or repurpose game-changing volumes of carbon dioxide that would otherwise end up in the atmosphere. To help foster an optimal understanding of the benefits, Ameet Kakoti and Per Juul Dahl of Topsoe A/S provide an overview of the technologies that can help any ammonia operation achieve and maintain sustainable operations – sooner rather than later.
The world depends on ammonia for a variety of reasons and lately it has been gaining traction for use as an energy carrier and/or source. High-volume production of ammonia necessitates the use of fossil sources, the environmental impact of which will need to be controlled and reduced as the energy transition progresses.
The production of ammonia releases CO2 during two key processes:
- syngas preparation, which delivers a CO2 stream that is pure enough for immediate sequestration or use;
- flue gas emission from steam reformers and fired heaters, which often delivers a CO2 stream of insufficient purity, thereby necessitating additional separation costs.
Reducing the financial impact of carbon-footprint management entails reducing flue gas emissions and capturing as much of the remainder CO2 as possible in the syngas preparation stage for removal. Rather than viewing this as a business obstacle, Topsoe encourages producers to embrace an opportunity to implement process solutions that can transform business for the better.
Establishing a low-carbon ammonia standard
Conventional ammonia production, which is based on steam-methane reformer (SMR) technology, emits around 0.48 kg of CO2 per kg of ammonia in the flue gas stream. Topsoe’s SynCOR™ technology can reduce that volume to approximately 0.31 kg CO2 per kg of ammonia.
An international standard for blue production doesn’t exist yet; such production is typically classified as resulting in less than 0.2 kg of CO2 per kg of ammonia, which can be met by Topsoe’s ultra-low carbon-intensity process – SynCOR Ammonia™ , which can reduce emissions by more than 99%. Such market-leading efficiency is facilitated by process layouts that integrate systems capable of removing maximised volumes of pure CO2 from syngas, as well as the use of high-performance flue gas-capture units.
CO2 capture percentage standards are driven by the expectation that these emissions will be taxed more heavily in the coming years, and that captured CO2 will generate income from its sale and repurposing. As such, the higher the standard maintained, the greater the overall profitability of the operation.
The Topsoe ammonia process can be configured in a variety of ways governing energy import and export. Some process schemes produce their own power, while others may need power import. As such, when comparing different process schemes, it’s important to include the CO2 emission value of any imports and exclude the emission value of any exports. This provides the most accurate comparison of process designs and ensures that the right selection is made.
Preparing for the future
Hydrocarbon feeds aren’t going away anytime soon, so in order to produce blue ammonia, what needs to change is how those feeds are processed. Carbon emissions from ammonia production fall into two categories, indirect or direct emissions. Indirect emissions are related to power import and emissions from the auxiliary boiler, and direct emissions are driven by the heat required for the reforming process and the removal of carbon from the feedstock to prepare synthesis gas for ammonia production.
Indirect emissions need to be addressed and it is a process which is expected to be central to the gas and power producers to minimise emissions at source (Scope 2 and Scope 3). With time, more and more renewable power coming onstream, Scope 2 emissions will trend favourably toward minimal to no emissions. The same applies for carbon emissions from leakages as that is a major emission source and high on the agenda to be cut. This is already done in practice in gas piped in Norway with lowest emissions.
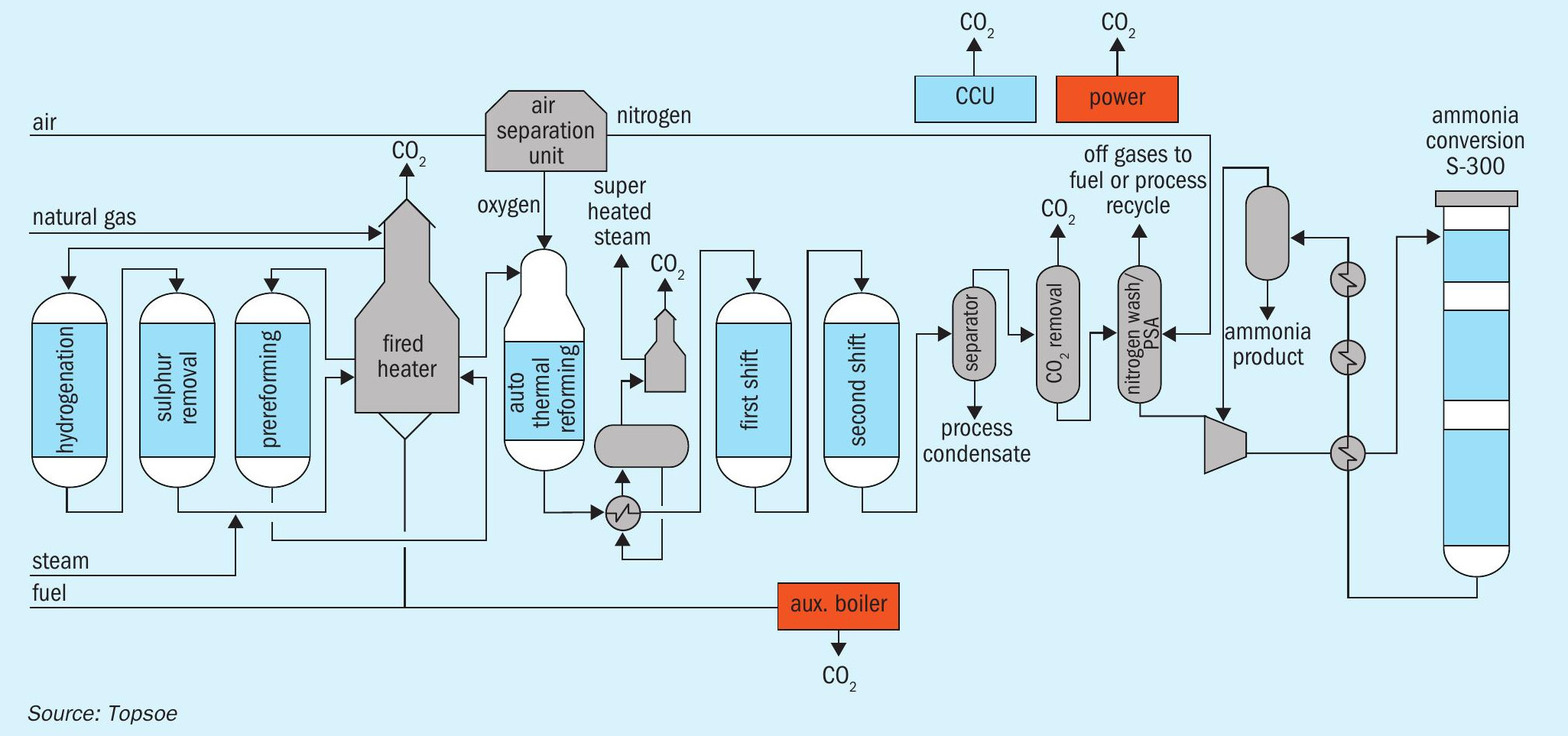
In the syngas conversion process, carbon released from pre-combustion capture is sufficiently pure for further repurposing. Carbon is also released during the reforming step, which requires significant heat. The heat is typically provided by burning hydrocarbon fuels, resulting in flue gas emissions containing large quantities of CO2 . There are two ways to reduce these flue gas emissions:
- integration of flue gas capture systems, which capture more than 90% of the emissions; such systems have been available for decades and are often utilised in revamps of existing plants;
- increasing syngas-generation capacity, resulting in greater CO2 volume and excess hydrogen; the hydrogen can be used as fuel during the reforming process.
While the former method can help position older setups for profitable business in the sustainable era, the latter is ideal for new ammonia plants, as it proves advantageous when pursuing decarbonisation goals. Producing usable hydrogen is, in most cases, far more cost-efficient than removing and purifying the carbon from the flue gas stream.
Reforming technologies
The optimisation of the decarbonisation is then directed towards the required heat input for the reforming section, as it is one of the largest point sources of CO2 , besides the captured CO2 from the synthesis gas.
Almost all ammonia plants in operation, use steam reforming as part of the synthesis gas generation. More than 20 years ago, i.e., before decarbonisation took off, Topsoe introduced the SynCOR concept for large-scale synthesis gas generation. The SynCOR concept is a synthesis gas generation technology using autothermal reforming, operating with a steam to carbon ratio, typically at 0.6. The technology has today achieved more than 300 operating years of large to very large scale industrial reliable operation.
A typical SynCOR Ammonia plant is shown in Fig. 1. Synthesis-gas generation corresponding to 10,000 t/d ammonia can be produced in one SynCOR reactor which makes it fundamentally different from all other available reforming solutions. The major difference is the operation with a low steam-to-carbon ratio of 0.6, which is about 4-5 times less steam than required for tubular steam reforming. This reduces the amount of heat input for the reforming section drastically, and thereby the fuel requirement directly leading to a lower CO2 emission.
Therefore, the use of SynCOR is beneficial in cases where there is a desire to decarbonise, since it requires either a smaller flue gas capture unit or has less need for excess hydrogen for fuel. This is a major advantage compared to steam reformer-based solutions. And with SynCOR Ammonia, carbon intensity is much lower when compared to a traditional steam methane reformer. SynCOR Ammonia starts with a carbon capture rate of about 87% compared to an SMR plant with a carbon capture rate of about 75% directly from the process gas, pre-combustion process, which is inherently present in an ammonia process.
Case comparison
Regardless of the technology selected, the blue ammonia production process is already well defined and reliably proven, so what matters is the parameters driving production: carbon intensity (CI), carbon recovery (CR), and the levelised cost of ammonia (LCOA). These parameters will impact the facility’s energy balance, as shown in Fig. 2.
CI and CR are currently regarded as the most effective means of measuring the success of blue production in terms of CO2 reduction, and a plant’s CR goals will impact overall capex and opex. With that in mind, a SynCOR Ammonia plant can start with a lower capture rate before revamping increasing to a higher rate as needed.
Topsoe has the widest portfolio of reforming technologies available in the market, so if large- or mega-scale output is the goal, SynCOR is the ideal choice on account of its low capex and opex, owing to its single-reactor layout and optimised steam-to-carbon ratio. All of this allow a SynCOR-equipped facility to benefit from economy of scale.
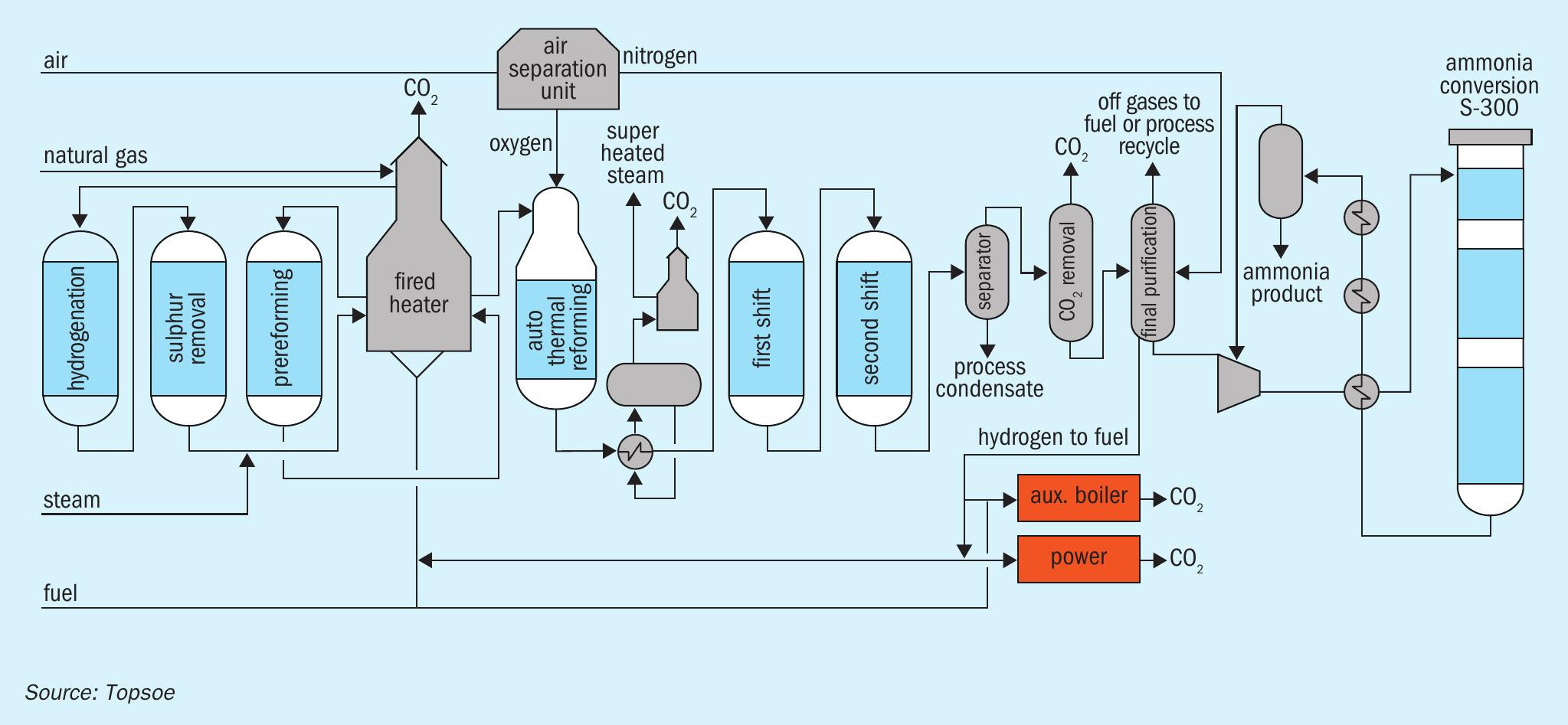
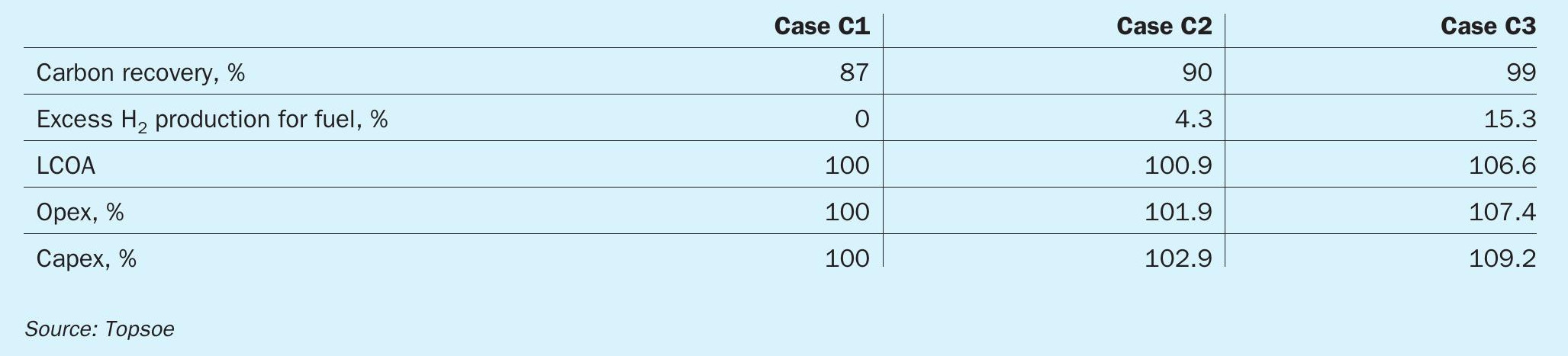
The reduction of CI through pre-combustion capture, which utilises a CO2 removal process inherent to the process itself, is a simpler matter than flue gas capture (post combustion capture), so many blue processes begin there. This is instrumental in SynCOR’s ability to minimise CI, for example.
To provide a fair comparison, Topsoe has compiled three cases involving Syn-COR plants at a capacity of 4,000 t/d.
Case 1 (Base case): A newly built unit with a shift section and pre-combustion carbon capture, as is common in traditional ammonia plants. The captured CO2 is compressed to 162 barg before being liquefied for transport or storage, while the syngas is purified in a cryogenic nitrogen wash unit, resulting in inert, free makeup gas to the ammonia synthesis loop.
Case 2 (Minimal hydrogen firing): This case is similar to the base case, but a portion of the syngas/hydrogen-rich gas serves as fuel, increasing carbon recovery to 90%. As a result of hydrogen firing, additional syngas is produced.
Case 3 (Hydrogen-rich gas as main fuel): Here, the fuel setup enables an even higher carbon recovery rate of 99%. The major difference from the second case lies in the minimisation of natural-gas volume, supplemented in turn by hydrogen-rich gas. Under normal conditions, methane containing off gases from the purification unit would be recycled to the reforming stage, but with hydrogen firing, additional syngas is instead produced – a net win in terms of operational efficiency and energy savings. Topsoe has a patent pending for this technology.
Table 1 illustrates opex and capex for each of the four cases, in conjunction with the assumptions listed in Tables 2 and 3.
Based on the data obtained, it can be concluded that:
- Case C1 provides for the lowest opex and capex.
- Case C2 demonstrates attractive capex as a result of burning a limited amount of excess hydrogen as a fuel replacement, with a 90% capture rate and lower LCOA.
- Case C3 shows that a certain increase in both capex and opex can be expected as carbon-capture rates progress toward 99%.
All of this helps us understand that technology selection ultimately hinges on the need to achieve certain targets in as cost-effective a manner as possible. LCOA is certainly important, as it influences the plant’s layout according to utility costs, CO2 taxes and credits, and opex/capex. The case study makes it clear that, as expected, reducing emissions will cost a bit more, but it also shows that selection of the correct technology, in accordance with boundary conditions, can also impact results.
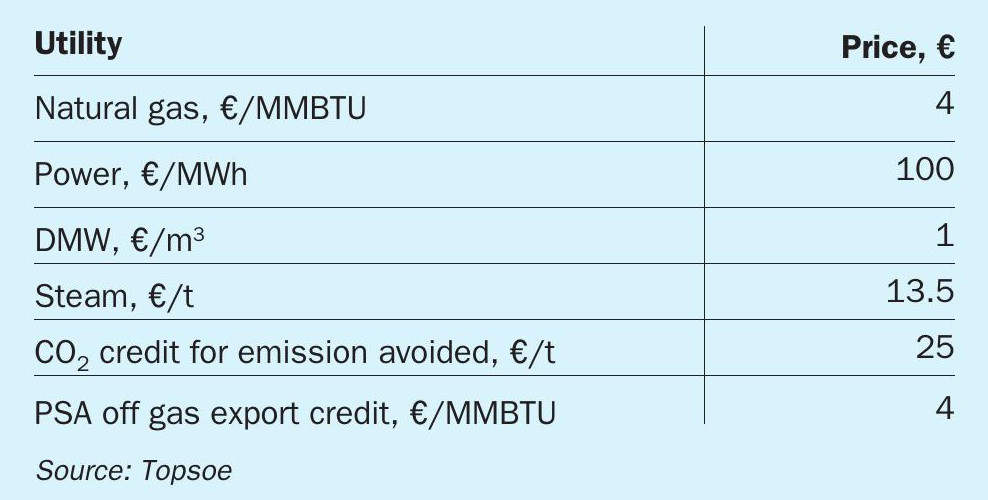
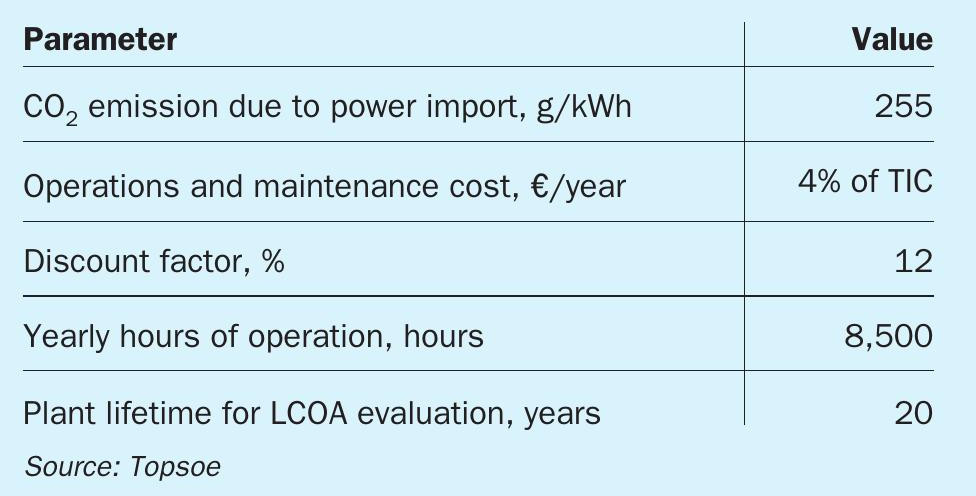
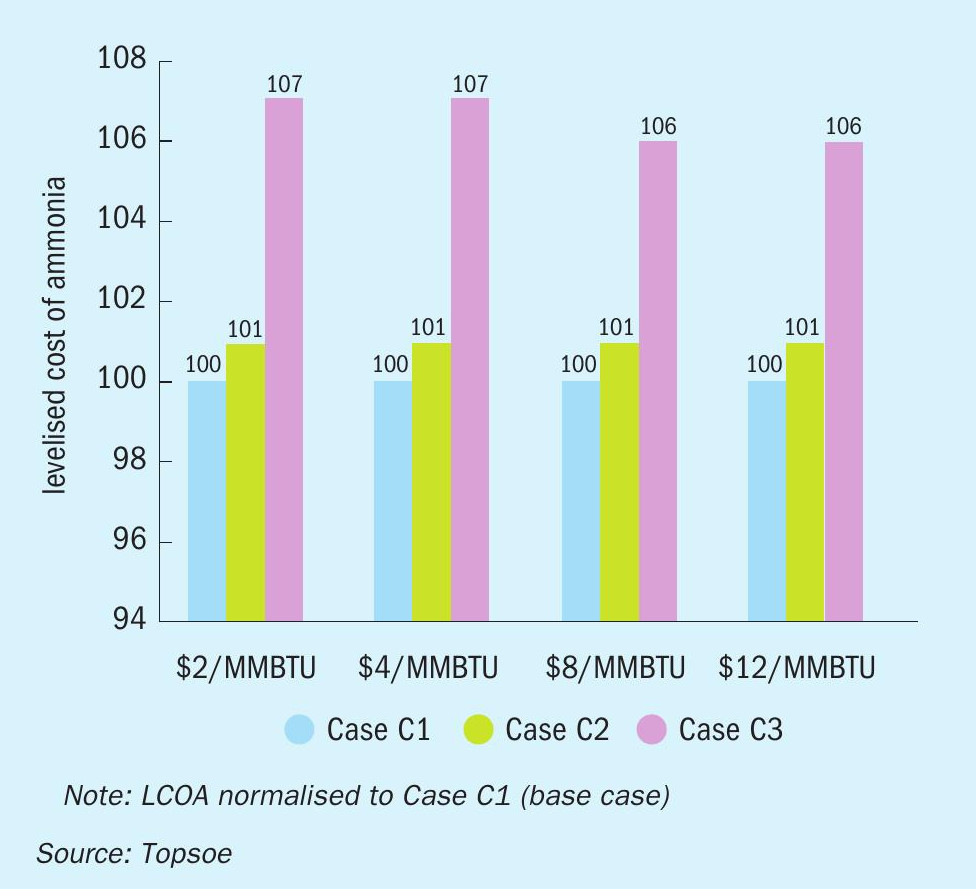
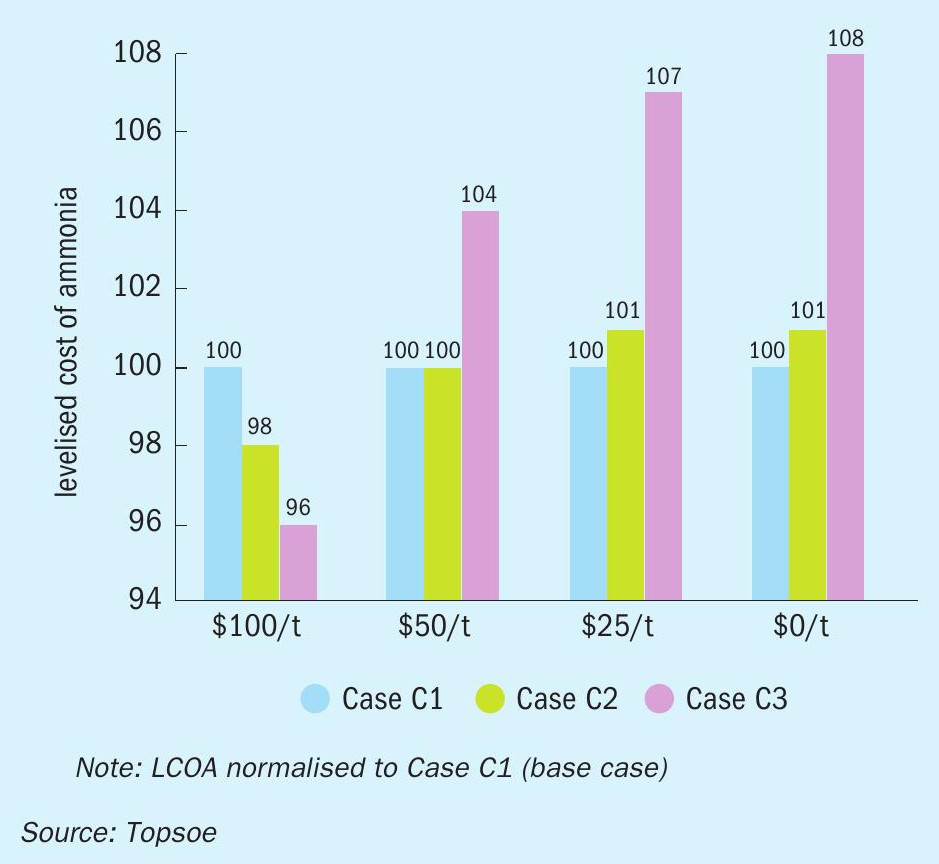
Thus, the key takeaway is that when it comes to blue production, there’s no onesize-fits-all solution, which is a good thing. Adjustable concepts can be optimised more readily and effectively.
Fig. 3 exhibits that case C3 has the highest LCOA because of excess hydrogen production and increased capex, while Case C1 exhibits the lowest LCOA – and these conditions remain valid across a broad spectrum of natural-gas prices, implying that the levelised cost of ammonia production is not very sensitive to NG prices over different CI.
What changes things is carbon credit, which makes layout selection much more crucial, as shown in Fig. 4.
Here, it becomes clear that credit variation has an impact on LCOA; without credit, Case C3 delivers the highest LCOA, while C1 delivers the lowest, but when CO2 taxes are higher, C3 suddenly becomes much more attractive.
As with the energy transition policies announced globally, carbon credits and carbon pricing mechanisms/carbon emission penalties are imminent and thereby higher carbon capture rate/ lower carbon intensity will secure a long-term sustainable ammonia production for the investors.
Conclusion
As a major component of the sustainable energy transition, blue ammonia will need to be produced at never-beforeseen capacities. This will challenge traditional, tubular reformer-based solutions, both in terms of opex and capex but also in terms of emission management, which will necessitate additional expenditure. The cost effectiveness of Topsoe’s SynCOR Ammonia process stands out when compared to other available reforming technologies.
Instead of following the traditional steam methane reforming process scheme, nowadays several well-proven, mature options are available and much more suited for high-efficiency blue production. As SynCOR plants already begin with the lowest CI, it will be relatively easier to transition to blue ammonia production at large scale when compared to traditional reforming technologies. Depending on operational criteria and future availability of renewable power, SynCOR can deliver the lowest LCOA in addition to the lowest CI, all at economy of scale, while future proofing ammonia businesses with the means to integrate zero-carbon power for the lowest possible emissions.