Nitrogen+Syngas 384 Jul-Aug 2023
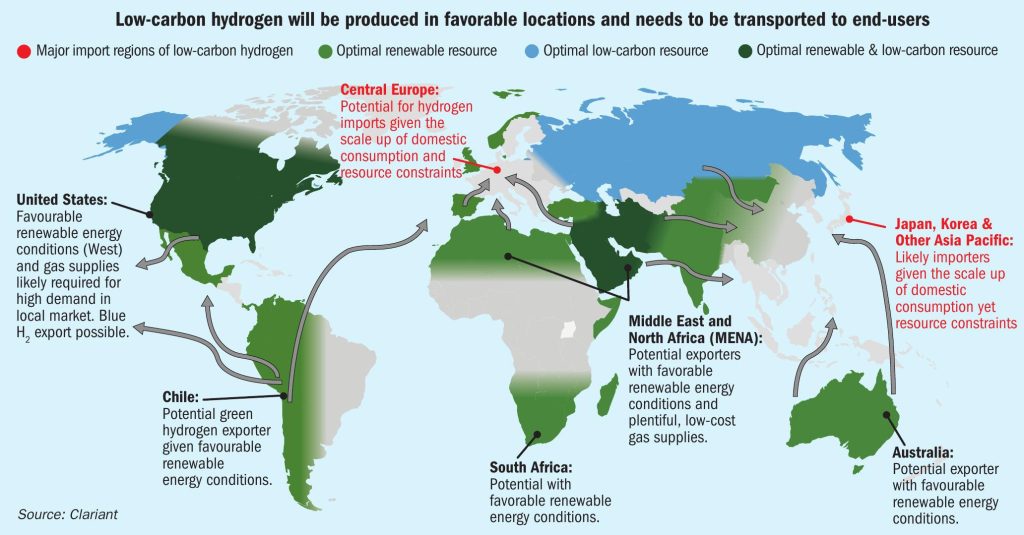
31 July 2023
Catalysts to tackle the challenges of ammonia cracking
GREEN HYDROGEN ECONOMY
Catalysts to tackle the challenges of ammonia cracking
Highly efficient ammonia synthesis and subsequent cracking to hydrogen are key processes in the transition to the green hydrogen economy. Catalysts play an important role in the ammonia cracking process. Clariant offers both nickel and precious metal catalysts for this application and research on robust catalysts that allow lower temperatures for increased energy efficiency is ongoing.
Demand for clean energy is driving interest in green hydrogen (H2 ) worldwide, with further impetus coming from the need for energy independence. While hydrogen is a proven and clean-burning fuel, it also involves several logistical challenges, especially in the case of green hydrogen. Produced using renewable energy sources, green hydrogen requires long-range transport from the Global South, where solar power is in abundance and growing, to northern geographies (Fig. 1). Conversion to ammonia (NH3 ) for storage and transportation, then reconversion to hydrogen at the point of use, offers the safest and most cost-effective solution.
Central Europe and the Asia Pacific region, particularly Japan and Korea, have huge potential as markets for hydrogen due to their high energy consumption and resource constraints. Blue hydrogen, produced by non-renewable energy sources, is seen critical by certain governmental bodies and an increasingly aware public. Nevertheless, it can be an important stepping stone on the path to low greenhouse gas (GHG) emissions, as the CO2 emissions resulting from its production can be reduced by up to more than 99% through the use of a suitable carbon capture and sequestration (CCS) technology.
Considering Germany’s position as Europe’s economic and industrial powerhouse, it is no surprise that representatives of the Berlin government have recently discussed green hydrogen on state visits to Africa and South Asia as well as to southern European countries. These regions are predestined to produce renewable-based hydrogen at low cost.
The long haul to the green hydrogen economy
This brings us back to the question of logistics. Currently, hydrogen is transported and stored mainly in the form of liquid compressed hydrogen. This has the disadvantage of needing to be stored either under high pressure (350-700 bar) or at extremely low temperatures (-253°C). This specialised handling raises costs. Another possible technology, known as liquid organic hydrogen carriers (LOHC), is a non-toxic solution that can be applied within the existing fuel network. Clariant is involved in this hydrogen transportation technology, supplying its EleMax® catalysts to the LOHC technology provider Hydrogenious.
However, where long-range transport is required, by far the most efficient and cost-effective solution to date is conversion to ammonia, thanks to its stability and very high energy density (Fig. 2). Ammonia can then be shipped to markets using the existing global ammonia infrastructure and is classified as non-flammable in transit.
Ammonia is the second-most widely produced commodity chemical in the world (after sulphuric acid), with a production volume of 183 million tonnes in 2020. As around 18-20 million t/a is already shipped internationally, its worldwide distribution system, which mainly serves the fertilizer and chemicals industries, is safe and well-established. (Reference: Irena Innovation Outlook Renewable Ammonia 2022).
The subsequent cracking process to reconvert ammonia to hydrogen can then take place in centralised large-scale plants located near ports or in smaller decentralised facilities e.g., in urban areas.
Centralised and decentralised ammonia cracking each have certain advantages, depending on the intended point of use. For large-scale processing of more than, e.g., 1,000 t/d of ammonia to feed hydrogen into the energy grid, major industrial plants are clearly favourable. These can be built to employ proven nickel catalysts to meet the needs of industrial consumers like municipalities or steel, cement and chemical companies. Decentralised facilities, in contrast, are suitable for small-scale processing of several hundred kilos of ammonia per hour using ruthenium catalysts, resulting in high-purity hydrogen e.g., for fuel cell applications. Ideal locations are near filling stations supplying hydrogen for vehicles.
Ammonia cracking: already proven on a small scale
Ammonia cracking, or dissociation, is an endothermic reaction requiring 46 kJ per mole of ammonia. The thermodynamic equilibrium favours high temperatures and low pressures (see Fig. 3).
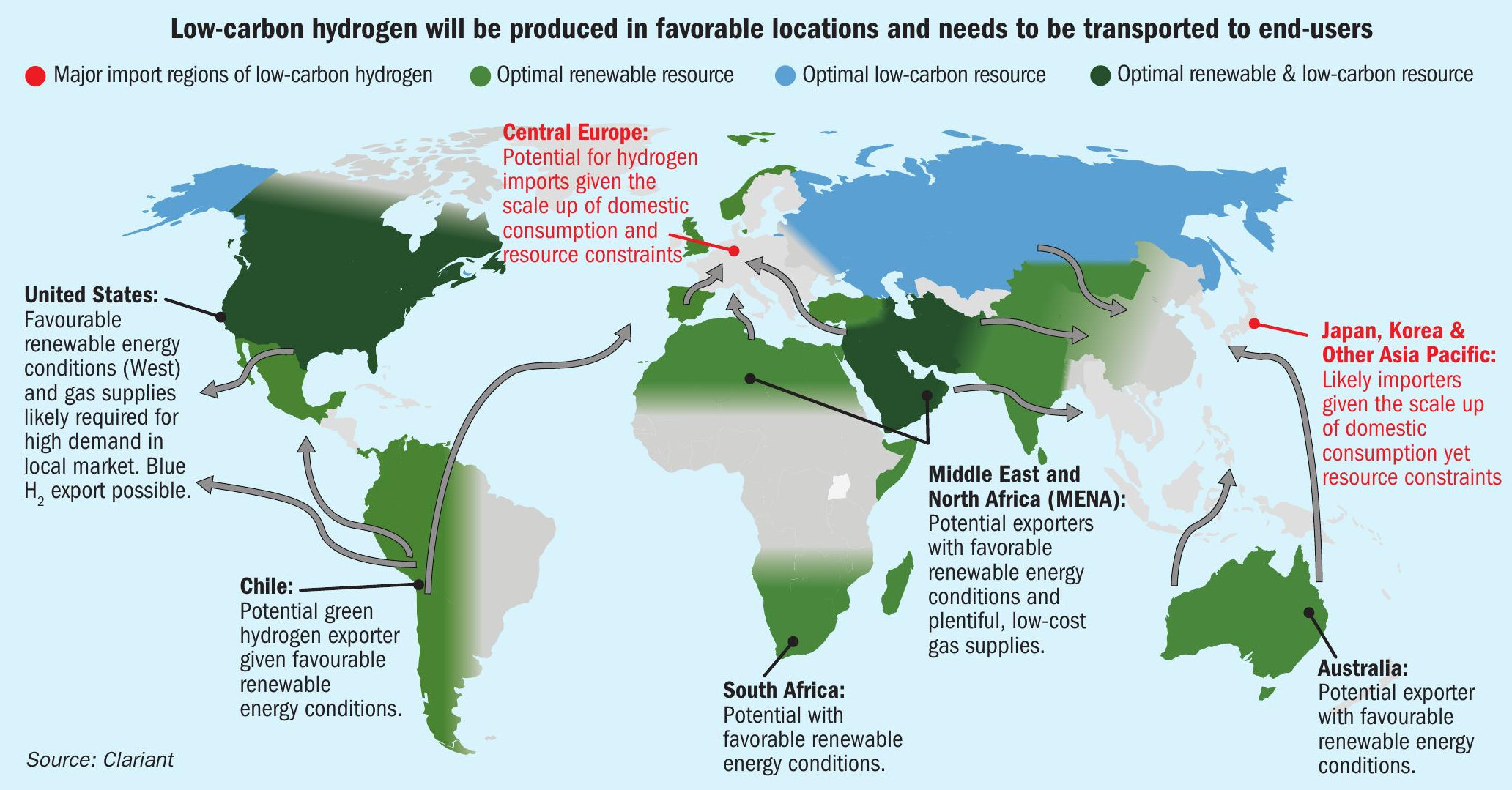
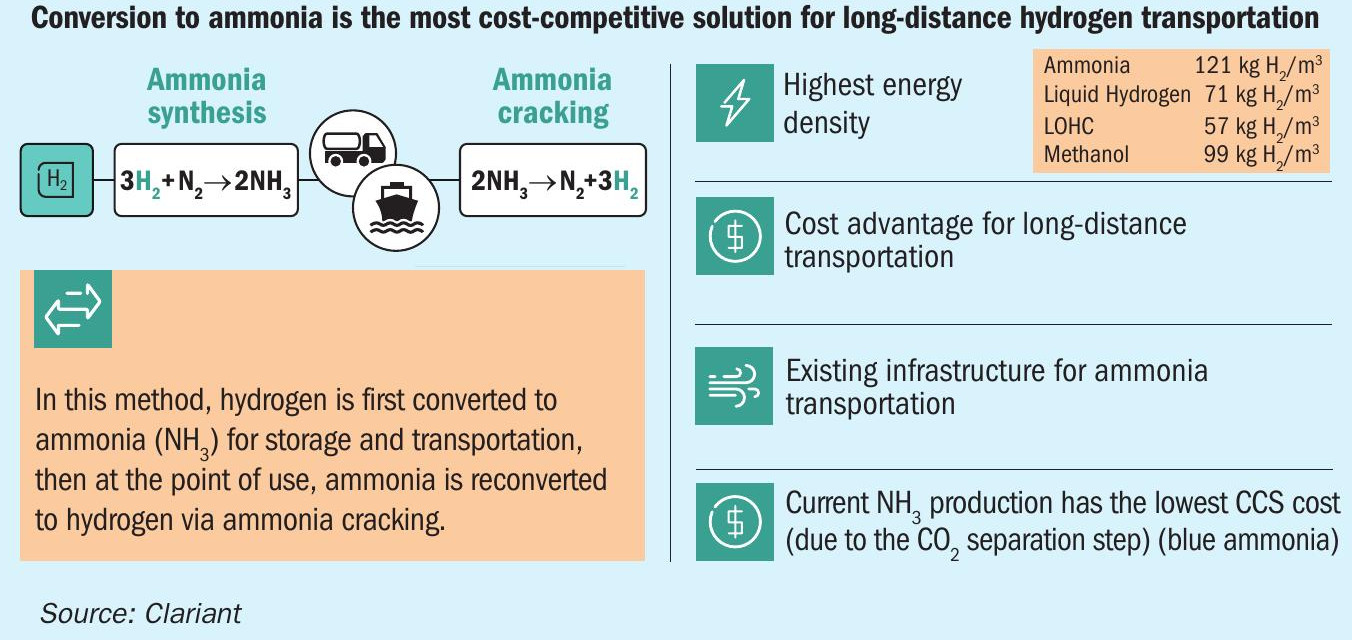
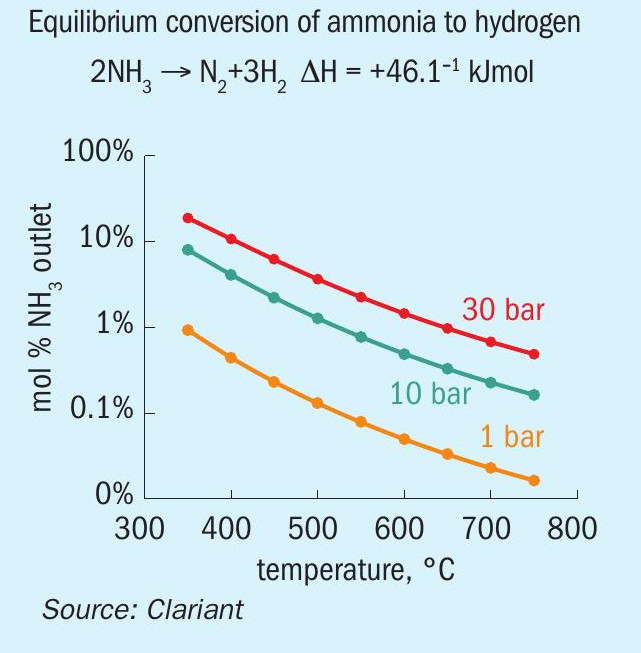
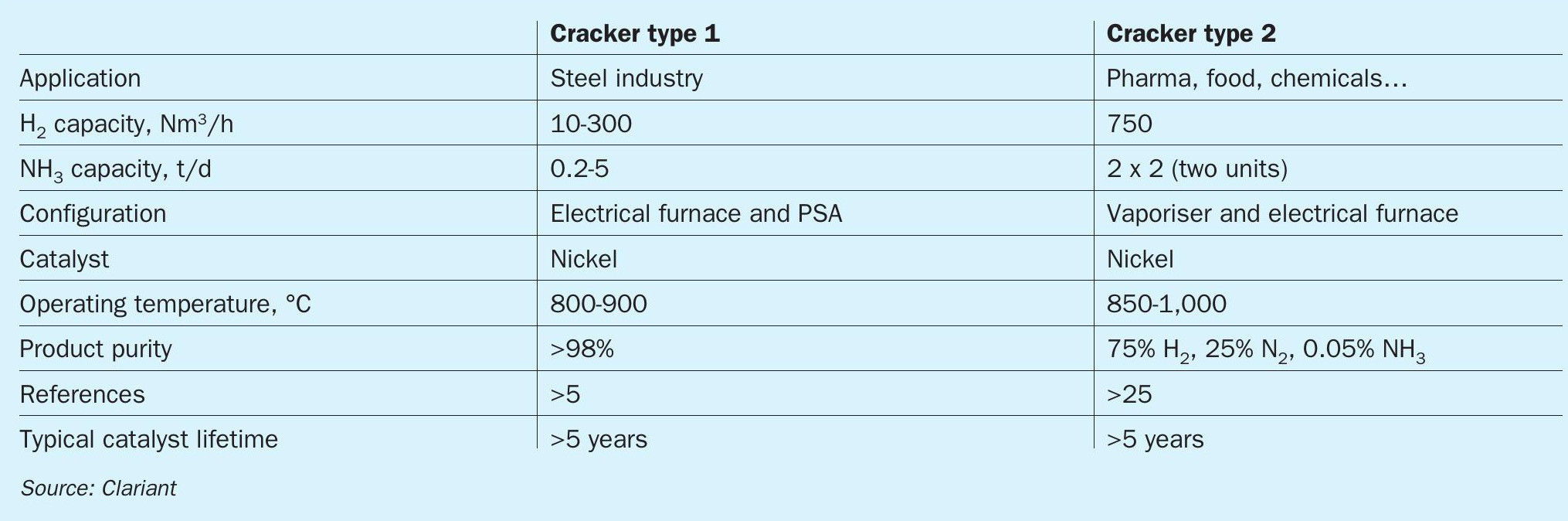
Depending on the temperatures used in the reaction, catalysts based on either precious metal or nickel are applied. Typical flow sheets comprise the following process steps: ammonia vaporisation, cracking, heat recovery and hydrogen separation/purification.
Small ammonia crackers have already been in operation for more than 50 years, especially in India, where they are used in different industries on a small scale. These small crackers with a capacity of around 10-750 Nm3 /h H2 typically run at low pressures and high temperatures. They are not optimised for energy-efficient operation (see Table 1).
The new generation of centralised crackers to meet industrial and municipal needs must run with a higher level of efficiency to deliver cost-effective green hydrogen. For this reason, these are not directly comparable to the small-scale crackers in India.
In most cases, ammonia cracking plants will have two types of reactors, as shown in Fig. 4.
Adiabatic reactors
In the pre-cracker reactor (adiabatic), partial conversion of the ammonia occurs in order to reduce the heat duty required in the downstream fired tubular reactor. Inlet temperatures of the pre-cracker are up to 650°C, while outlet temperatures are around 400°C. Pressures of up to 50 bar are applied, depending on the needed application for the hydrogen. In terms of catalyst type, nickel-based catalysts like HyProGen 820 DCARB show excellent stability against sintering as well as high activity (Fig. 5). This catalyst has been stress tested under harsh conditions: 600°C, high GHSV of 15,000 h–1 , and it maintained stable activity with a high and stable conversion.
Another nickel-based catalyst, HyProGen® 821 DCARB, is even more active and therefore offers an energy-efficient alternative to ruthenium-based catalysts in adiabatic reactors. In testing (Fig. 6), it has exhibited more robustness against water than its ruthenium counterparts. Ruthenium catalysts have two main downsides, which hamper their application in large-scale crackers: Their activity decreases strongly with pressure, and they tend to suffer from deactivation at moderate to high temperatures.
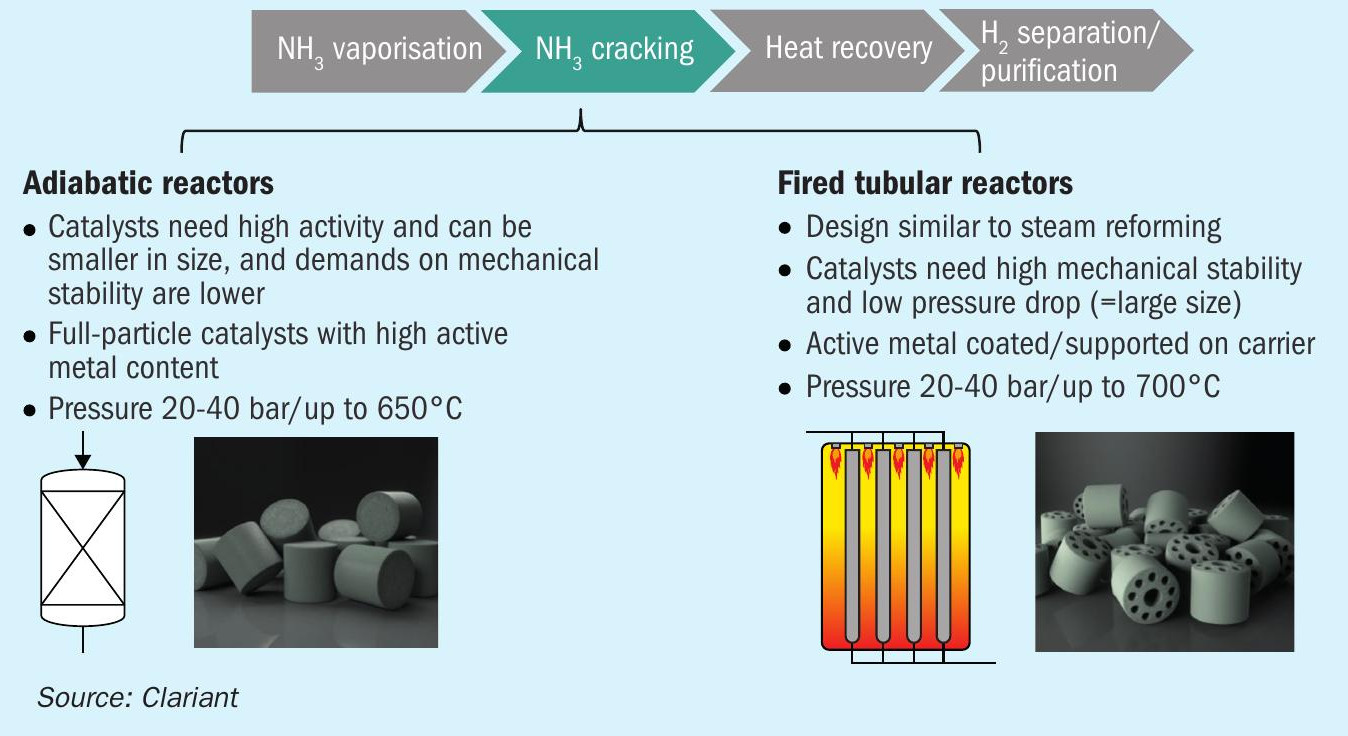
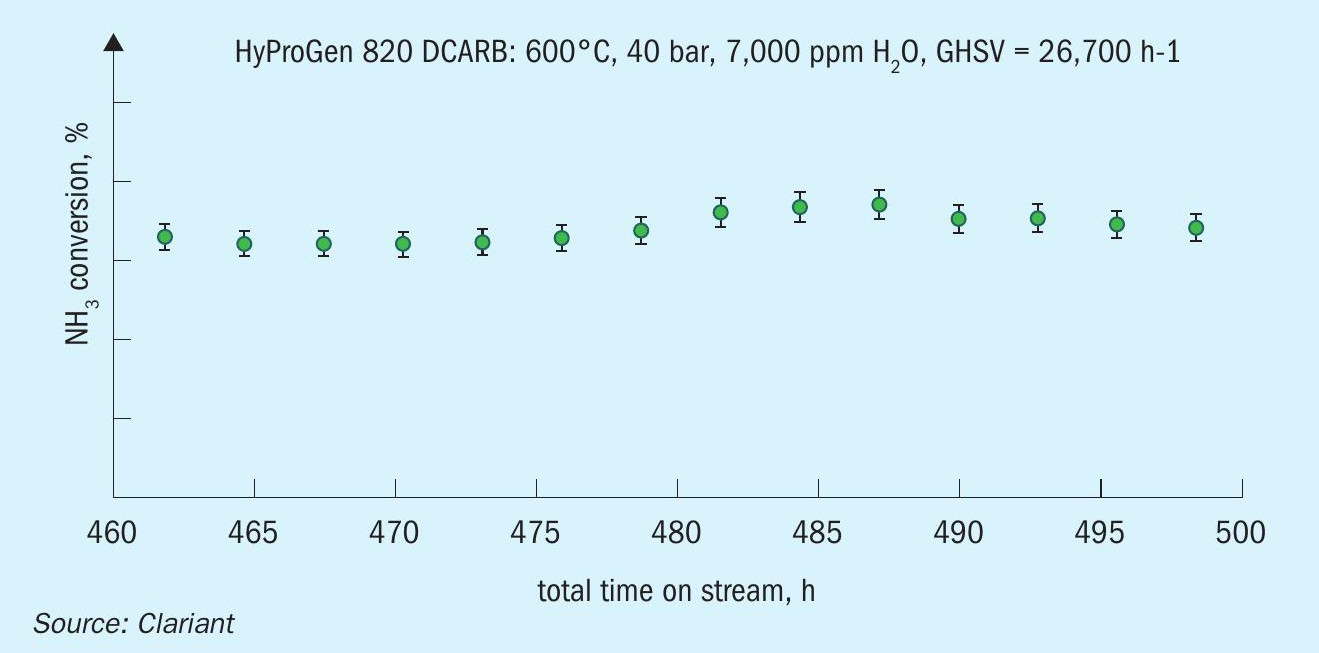
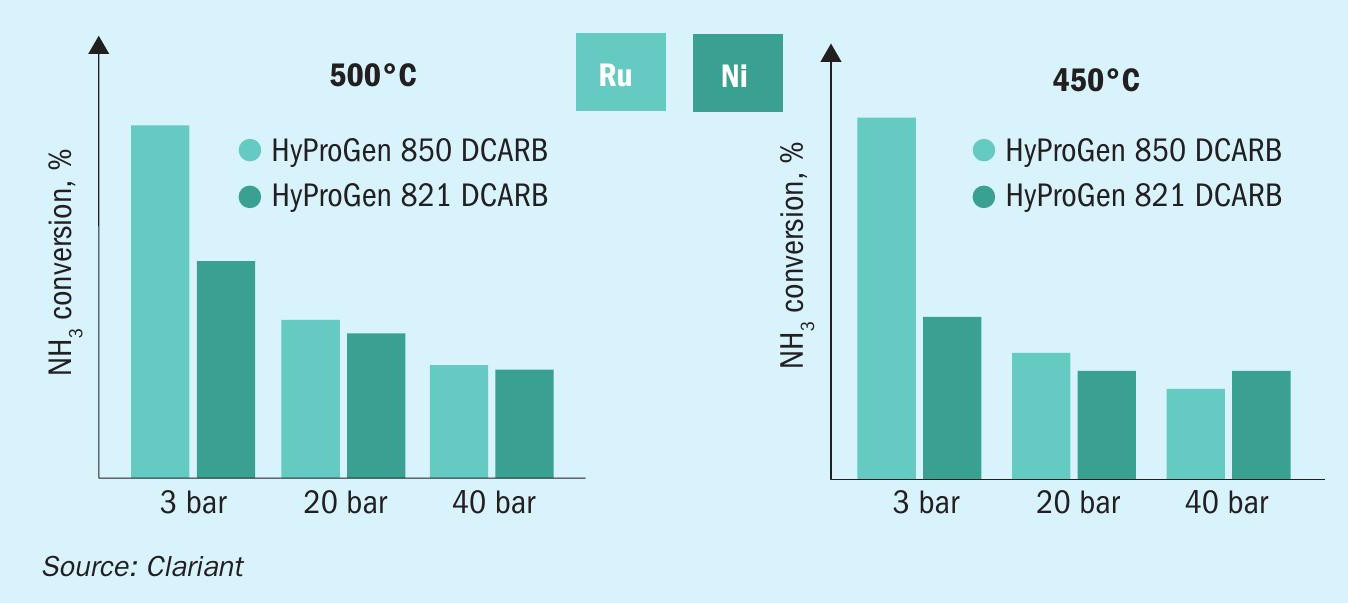
Fired tubular reactors
In the fired multi-tubular reactors, comparable to a steam reformer, the main conversions occur at temperatures up to 700°C. For this type of application, the catalyst needs to show good activity and, more importantly, excellent mechanical stability as well as a low pressure drop. Clariant has been producing such catalysts since the 1950s, which operate in steam reforming applications at temperatures over 800°C and pressures exceeding 40 bars.
Fig. 7 illustrates the high-pressure performance of three different nickel catalysts. Benchmark 1 shows high thermal stability but low activity, while benchmark 2 shows high activity but low thermal stability. Only HyProGen 830 DCARB combines high activity with good thermal stability. This catalyst has already been proven in commercial fired multi-tubular reactors, where it shows tremendous mechanical stability.
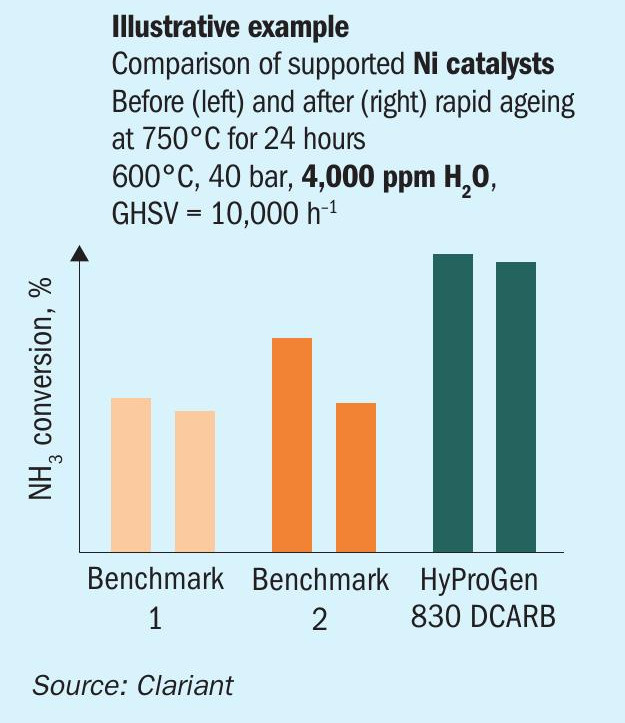
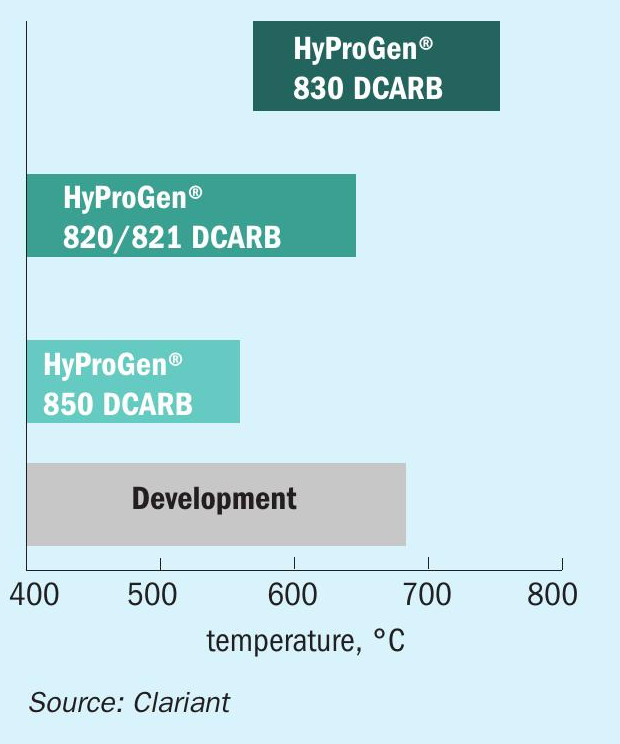
The future of catalysts: Nickel vs. precious metal
Clariant’s catalyst portfolio covers a wide range of solutions, which is continuously expanding. These include: HyProGen® 830 DCARB, a nickel-based catalyst designed for high-temperature applications, which – thanks to its mechanical robustness – is suitable for reformer-type fired tubular reactors; HyProGen® 820 DCARB and 821 DCARB nickel-based catalysts designed for moderate-temperature applications in adiabatic reactors, which combine superior activity with high thermal resistance against deactivation; HyProGen® 850 DCARB, a highly active ruthenium-based catalyst designed for low-temperature applications. Research on robust catalysts that allow lower temperatures for increased energy efficiency is ongoing (Fig. 8).
Ultimately, Clariant researchers foresee the greatest potential in nickel-based catalysts in both adiabatic and fired tubular reactors. One consideration is that ruthenium is one of the rarest metals on the planet, while nickel ore is mined on several continents in abundance. In addition, nickel is readily recyclable, contributing to the circular economy.
Ongoing research indicates that nickel-based catalysts can offer versatility in adiabatic and fired tubular systems of various sizes.