Fertilizer International 515 Jul-Aug 2023
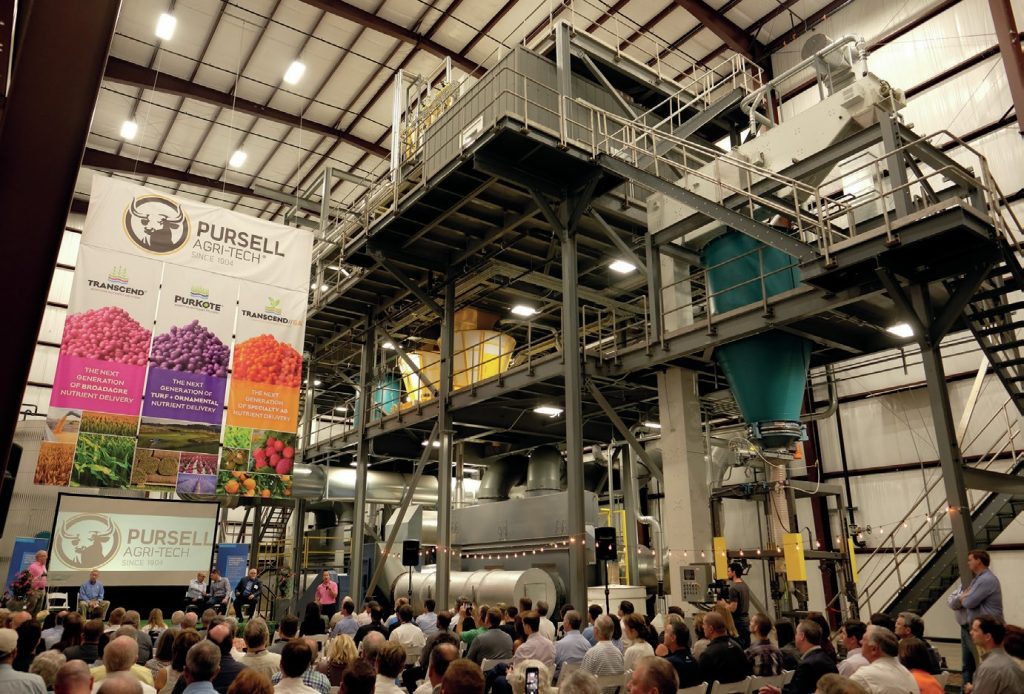
31 July 2023
Fertilizer technologies – innovating for the future
INNOVATION SHOWCASE
Fertilizer technologies – innovating for the future
Technological innovation is vital to solving the global food challenge and delivering the transition to a low-carbon economy. Pejman Djavdan, Stamicarbon’s CEO, sets out his vision for a future-proof fertilizer industry – one that will enable the sustainable intensification of agriculture while also protecting the environment.

One of the most pressing problems confronting humanity this century is how to feed a growing global population in a sustainable way, in harmony with the planet and its finite resources.
The second United Nations (UN) Sustainable Development Goal (SDG) is to “end hunger, achieve food security and improved nutrition and promote sustainable agriculture”. This is a fundamentally important and ambitious goal, especially as the world’s population continues to increase rapidly – from around two billion in 1927 to three billion in 1960, then more than doubling to seven billion in 2011. By 2055, this figure is predicted to be around ten billion.
In addition to exponential population growth, the amount of food consumed per capita is also on the rise. Consequently the UN’s Food and Agriculture Organisation (FAO) has estimated that global crop production needs to increase by more than 45 percent by 2050 if we want to end hunger and malnutrition.
Stamicarbon, the nitrogen technology licensor of MAIRE Group, believes that technological innovation is vital to solving this global food challenge – by intensifying agriculture while at the same time protecting the environment.
Sustainability is also at the heart of the world’s climate challenge and – by transforming both processes and economic systems – is enabling the transition from traditional fossil-based industries to sustainable lowcarbon-based models. The fertilizer industry is no exception. Stamicarbon is therefore helping to accelerate the energy transition by developing and investing in cutting-edge technologies for future-proof fertilizer production.
Stamicarbon has the following two aims as part of its ‘Vision 2030’ innovation agenda: firstly, reducing the emissions and energy consumption of fertilizer plants and, secondly, improving the nutrient use efficiency (NUE) of fertilizers. To achieve this, the company is focusing its innovation efforts in three particular areas:
- The sustainable production of nitrogen-based fertilizers from renewable feedstocks using renewable energy
- Making fertilizers more effective and efficient by increasing their NUE
- The digitalisation of fertilizer plants to improve their energy consumption and reduce emissions.
Green ammonia
Fertilizers increase crop yields by adding nutrients to plants – allowing them to grow faster and stronger. Using fertilizers to intensify agriculture is therefore vital for feeding the world’s growing population. Equally, it is also clear that the environmental impacts of fertilizer production and on-farm use need to be reduced significantly.
In the past, economy of scale was the primary motivation for building large capacity fertilizer plants. Nowadays, however, a shift in the industry’s approach can be seen. This is illustrated by the increasing number of projects for smaller, distributed ammonia production units. These are powered by renewable electricity from small-and medium-scale hydro, wind and solar installations, helping the industry move towards an environmentally-friendly future. This type of distributed production is vital in the transition from fossil fuels to renewable energy resources.
By enabling the production of ammonia using nitrogen captured from the air and hydrogen generated via water electrolysis, Stami Green Ammonia technology (Figure 1) is a significant leap forward for fertilizer industry sustainability. Unlike traditional ammonia production, this process does not use fossil fuel feedstocks such as natural gas or coal. This innovation will therefore help to significantly reduce ammonia production emissions, which currently comprise about one percent of all greenhouse gas (GHG) emissions.
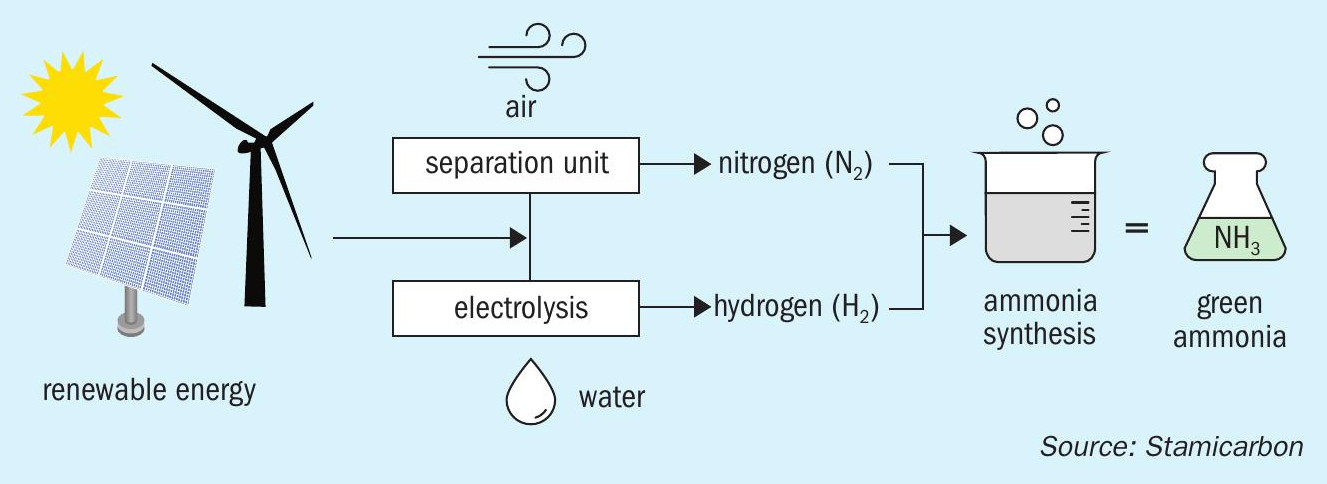
The Stami Green Ammonia process – being powered by renewable or carbon-free energy sources – enables the sustainable production of green nitrogen fertilizers like ammonium nitrate or calcium ammonium nitrate from a green ammonia feedstock. The green ammonia generated can also be used as a shipping fuel or energy carrier, as well as in fertilizer production.
Distributed ammonia production in sub-Saharan Africa
Distributed ammonia production is particularly important in areas with low fertilizer availability. Sub-Saharan Africa is one region where local, small-scale production can effectively contribute to regional self-sufficiency in fertilizers. Stamicarbon recently completed a pre-feasibility technical study with Minbos Resources to determine the most effective plant configuration for a green nitrates production complex in Malanje Province, Angola. The complex combines Stami Green Ammonia and Nitric Acid technologies. It will be powered using 200 MW of 100 percent renewable electricity supplied by the nearby Capanda Hydroelectric Dam. The study assessed the production of two kinds of nitrates: calcium ammonium nitrate (CAN) fertilizer for domestic use and low-density ammonium nitrate (LDAN) for the mining industry in neighbouring nations.
Enhanced efficiency fertilizers (EEFs)
As well as producing fertilizers sustainably from renewable resources, it is also important to improve the use efficiency of fertilizers. The introduction of innovative fertilizers that are more effective and efficient is enabling the industry to make this sustainable transition.
Nutrients such as nitrogen, phosphorus, potassium and sulphur are vital for plant growth. They do, however, tend to volatilise into the air or leach into the soil with regular fertilizer application – leaving less nutrients available for plants. These losses have undesirable consequences for the environment and human health, by causing high levels of nitrates and phosphorus in groundwater, ammonia volatilisation into the atmosphere, and nitrogen oxide and nitrous oxide emissions. These harm the environment and, ultimately, the planet.
Improving the nutrient use efficiency (NUE) – the ratio between the nutrient input from fertilizers and the nutrient output via crops – can help prevent these losses while providing farmers with economic benefits. Improving the NUE for farmers in China, for example, can reduce fertilizer applications. Elsewhere, enhancing NUE can help increase yields in sub-Saharan Africa, and decrease the environmental impacts of fertilizer use in Europe and the USA.
The adoption of enhanced efficiency fertilizers (EEFs) can deliver the increases in NUE needed. EEFs include controlled-release, slow-release, and inhibited fertilizers. These innovative fertilizers prevent nutrient losses by inhibiting natural processes in the soil (inhibited fertilizers) or controlling the delivery of nutrients to plants (slow- and controlled-release fertilizers).
Nitrogen is essential for plant growth, yet up to half of this nutrient is lost to air or surface water when applied. Nitrogen-based EEFs are therefore increasingly common. Coating urea with sulphur or a permeable membrane, for example, helps control the release of nutrients into the soil. These products use the 4Rs principle (delivering the right nutrients at the right time, place and rate) to prevent the oversupply of nutrients and minimise their loss to the air or groundwater (Figure 2).
Coating urea to improve NUE
In 2018, Stamicarbon collaborated with Pursell Agri-Tech in the United States to develop and license controlled-release fertilizer (CRF) production technology. At the heart of this technology is a modular coating plant with a compact design and a relatively low capex. These characteristics allow such plants to be constructed close to existing logistics centres near end-user markets. The first commercial reference plant based on Stamicarbon’s Controlled-release Fertilizer Design is located in Sylacauga, Alabama, USA (see main photo). This has the capacity to produce about 275 tonnes per day of CRF and is operated by partner company Pursell Agri-Tech on a 24 hour basis for five days per week. Stamicarbon is also collaborating with partners on biodegradable CRF coatings and CRFs containing added (micro-)nutrients.
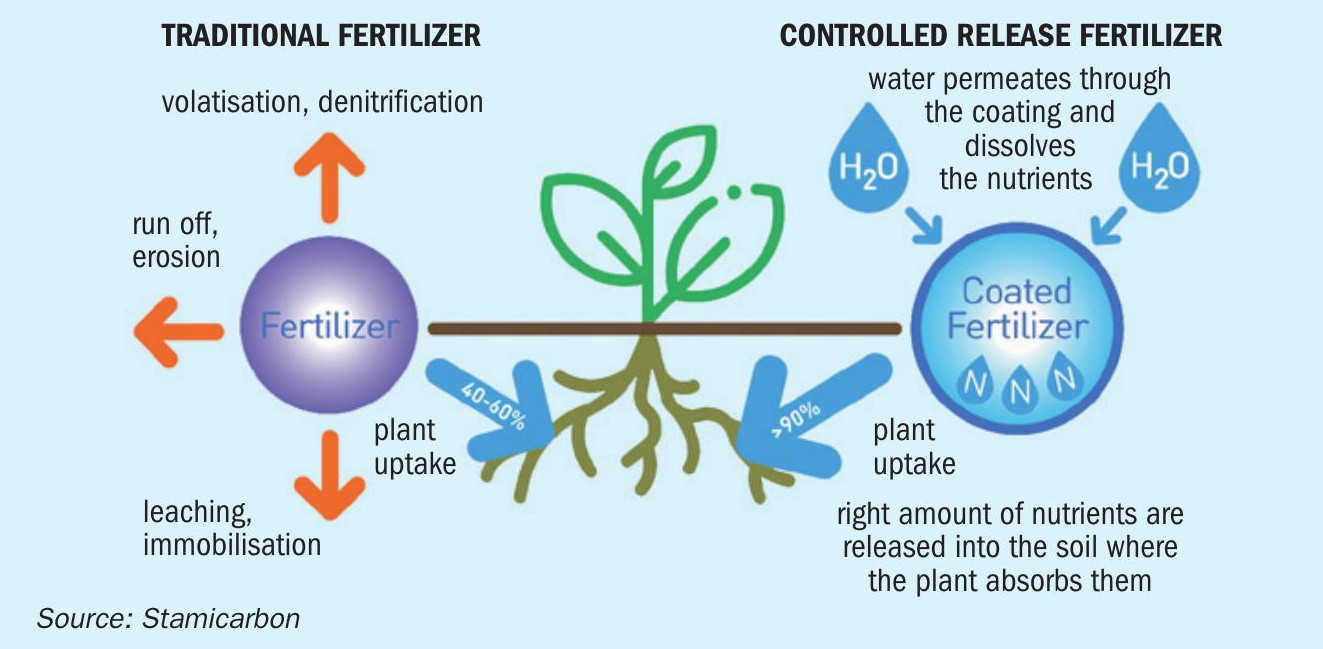

Optimising fertilizer plants
Digitalisation is becoming increasingly important in the process industry, as it can deliver benefits for technology licensors and fertilizer producers alike. Digital tools, by enabling the collection, analysis and exchange of data, enhance plant efficiency and productivity. The resulting transformation of real-time plant data into meaningful information offers valuable process insights and enhances plant control. This, in turn, drives continuous optimisation by improving production efficiency, reducing plant operating costs and minimising health, safety and environmental issues.
Although the chemisty of urea plants is fundamentally simple, the underlying physics of urea and carbamate mixtures is complex. To cope with this complexity, Stamicarbon offers a Process Monitor as part of its digital portfolio. This is driven by a process model of the plant and helps improve plant load and reduce energy consumption. This model calculates two types of critical parameters from real-time plant data: key performance indicators (KPIs) and soft-sensor key variables (KVs). KPIs include figures such as plant load, energy consumption and emission figures, while KVs include values such as equipment efficiency, equipment load and reactor conversion. Having processed the real-time data, the Process Monitor presents this information via customisable dashboards (Figure 3).
The Process Monitor’s engine operates in a secure cloud environment and receives real-time plant data unidirectionally (Figure 4). Urea plants can generate millions of data outputs on any given day. Having complete access to all of this available information in real-time therefore enables operators to better understand plant data and make informed operational decisions.
Process Monitor case study
A Process Monitor has been installed at Nutrien’s Borger urea plant, Texas, USA. This digital tool is used in combination with Advance Consult ™ to evaluate the process data and better understand the meaning of the KPIs and KVs. This has allowed Nutrien to optimise the Borger’s plant performance. Measurement errors, equipment bottlenecks and inefficiencies were detected. Deviating operating strategies developed from the model data have also proved very efficient. One such deviating operating strategy, for example, delivered three percent extra production capacity and a steam saving equivalent to 0.3 MMBTU/st urea.
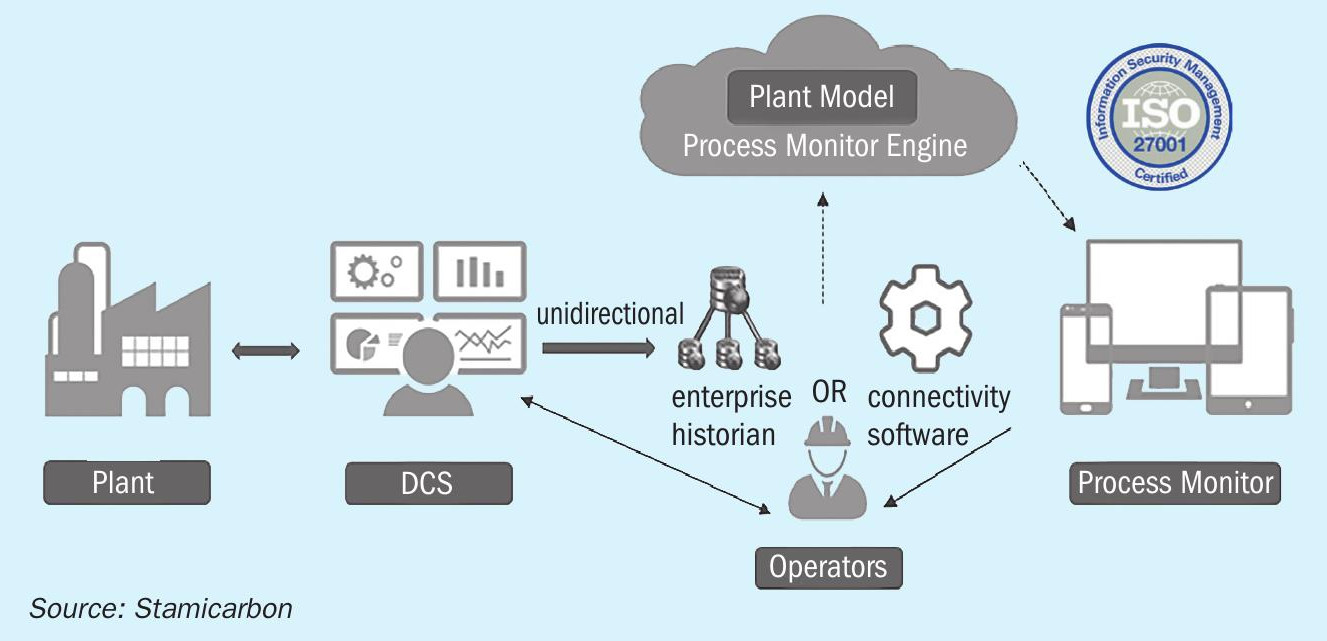
Stamicarbon’s Vision 2030
The fertilizer industry – and society as a whole – are aware of the power of innovative technologies for increasing agricultural productivity while simultaneously reducing agriculture’s impact on the environment. In response, Stamicarbon is constantly innovating to build a future where people, businesses and the planet can thrive in 2030 and beyond. The company is delivering on the innovation ambitions outlined in its Vision 2030 strategy by focusing on three main areas, as described above.
The sustainable transformation of the fertilizer industry is ongoing and requires ground-breaking solutions to key global challenges – enabling the world to feed itself and improving our quality of life. Stamicarbon, by constantly developing new technologies, collaborating with our partners, customers, and suppliers, and challenging the status quo, is determined to be a part of the solution.