Nitrogen+Syngas 384 Jul-Aug 2023
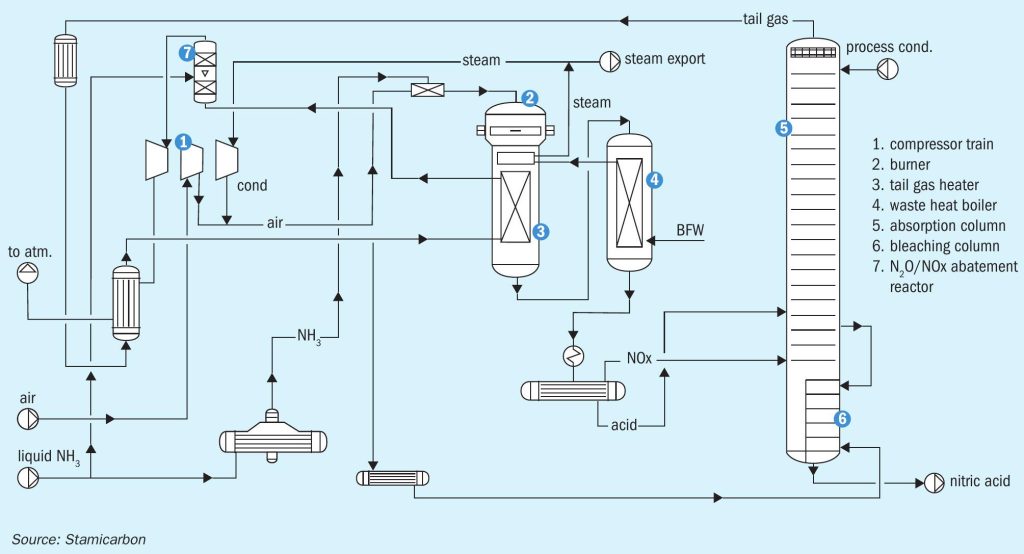
31 July 2023
Future-proofing nitric acid plants
NITRIC ACID TECHNOLOGY
Future-proofing nitric acid plants
Paz Muñoz and Carmen Perez of Stamicarbon discuss the strategic selection of future-proof technology for nitric acid plants. To produce nitric acid in a feasible and sustainable way, manufacturers must carefully choose the right technology and consider the capex and opex involved in the production process to ensure long-term profitability.
The continuous increase in the world’s population results in rising global food demand. Furthermore, production processes need to be optimised to combat the effects of climate change, with the shift towards more productive agriculture and fossil-free feedstock alternatives.
Major players in the fertilizer industry worldwide are taking steps towards reducing the carbon footprint of fertilizer production. Using renewable energy to produce ammonia paves the way for green fertilizers, including nitric acid, leading to a higher independence from gas production and a more stable market.
Green fertilizer production will become a more prominent theme in the industry, together with maximising the energy recovery of nitric acid plants, and Stamicarbon, nitrogen technology licensor of Maire Group, already plays a role in facilitating this transition. In addition, there is a trend to move towards small-scale production. Producers are striving to decentralise and minimise the need of external resources.
Stami Nitric Acid technology
Stamicarbon’s nitric acid technology uses the Ostwald process, where ammonia is converted to nitric acid in two main steps, relying on either mono- or dual-pressure design:
- the oxidation of ammonia (NH3 ) to form nitric oxide (NO), which is further oxidised to nitrogen dioxide (NO2 );
- The absorption of the nitrogen dioxide (NO2 ) in water (H2 O) to form nitric acid (HNO3 ).
One of the key advantages of Stamicarbon’s nitric acid technology is its high energy efficiency. The process is designed to minimise heat losses and maximise the recovery of heat from the process streams. This decreases the internal consumption of steam and lowers the operational costs. In addition, Stamicarbon’s technology can be combined with co-generation systems to produce electricity.
Stamicarbon’s nitric acid technology is also designed with environmental concerns in mind. The technology incorporates measures to minimise emissions of greenhouse gases and other pollutants. The use of modern abatement technology allows for the reduction of nitrogen oxides and nitrous oxide, which can be reduced to almost zero, disposing an environmentally safe tail gas to the atmosphere.
Stamicarbon’s expertise in nitric acid technology allows it to provide customised solutions to meet specific customer needs and challenges, ensuring nitric acid production with long-term success and profitability.
In the mono-pressure process (see Fig. 1), oxidation and absorption sections operate at the same pressure level. Different pressure levels are used for the oxidation and absorption sections in the dual-pressure process (see Fig. 2). The oxidation section is operated at pressures between 4 and 6 bar(a), while the absorption section operates between 8 and 12 bar(a), combining the advantages of medium-pressure combustion with the efficiency of high-pressure absorption.
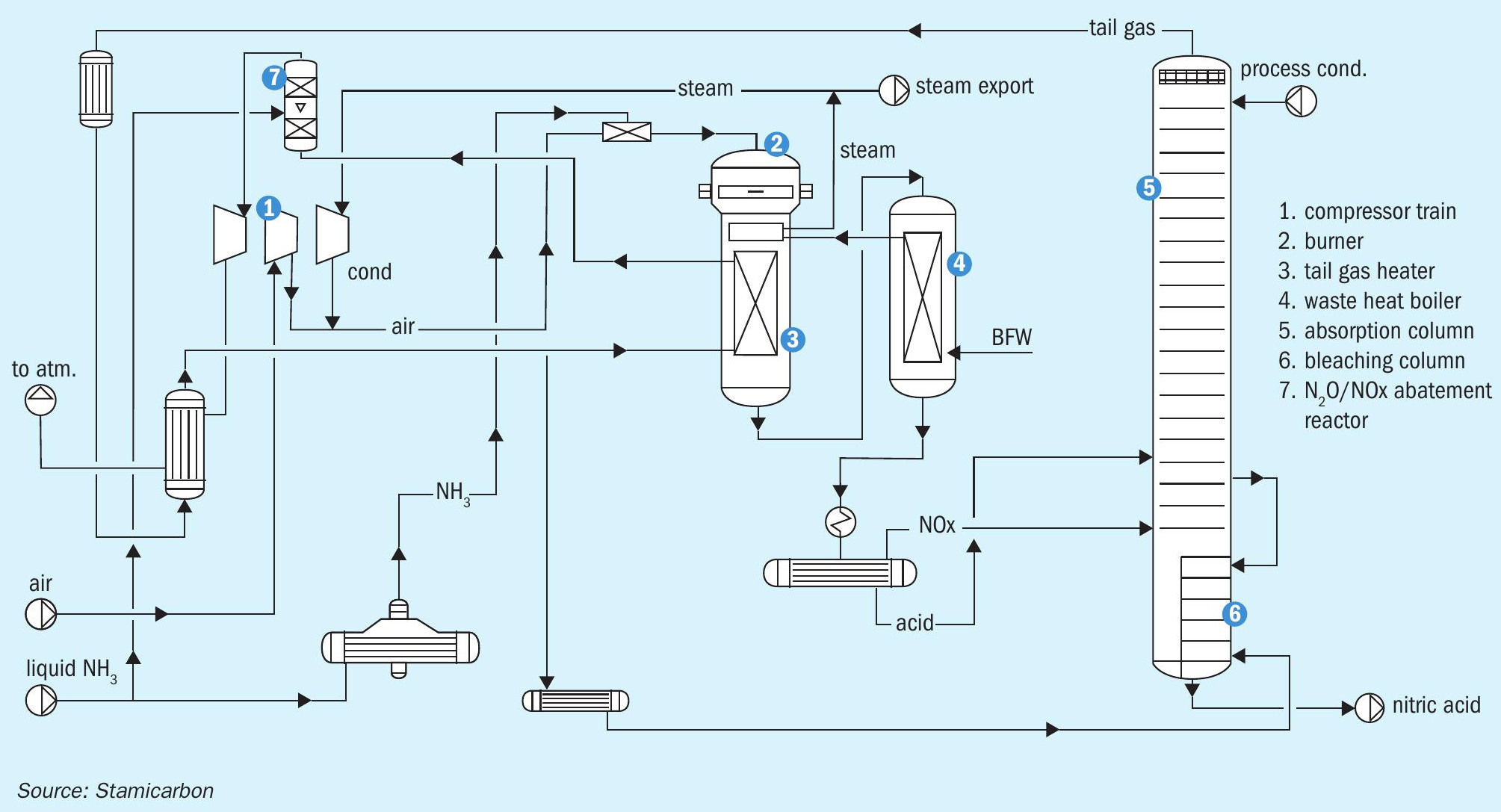
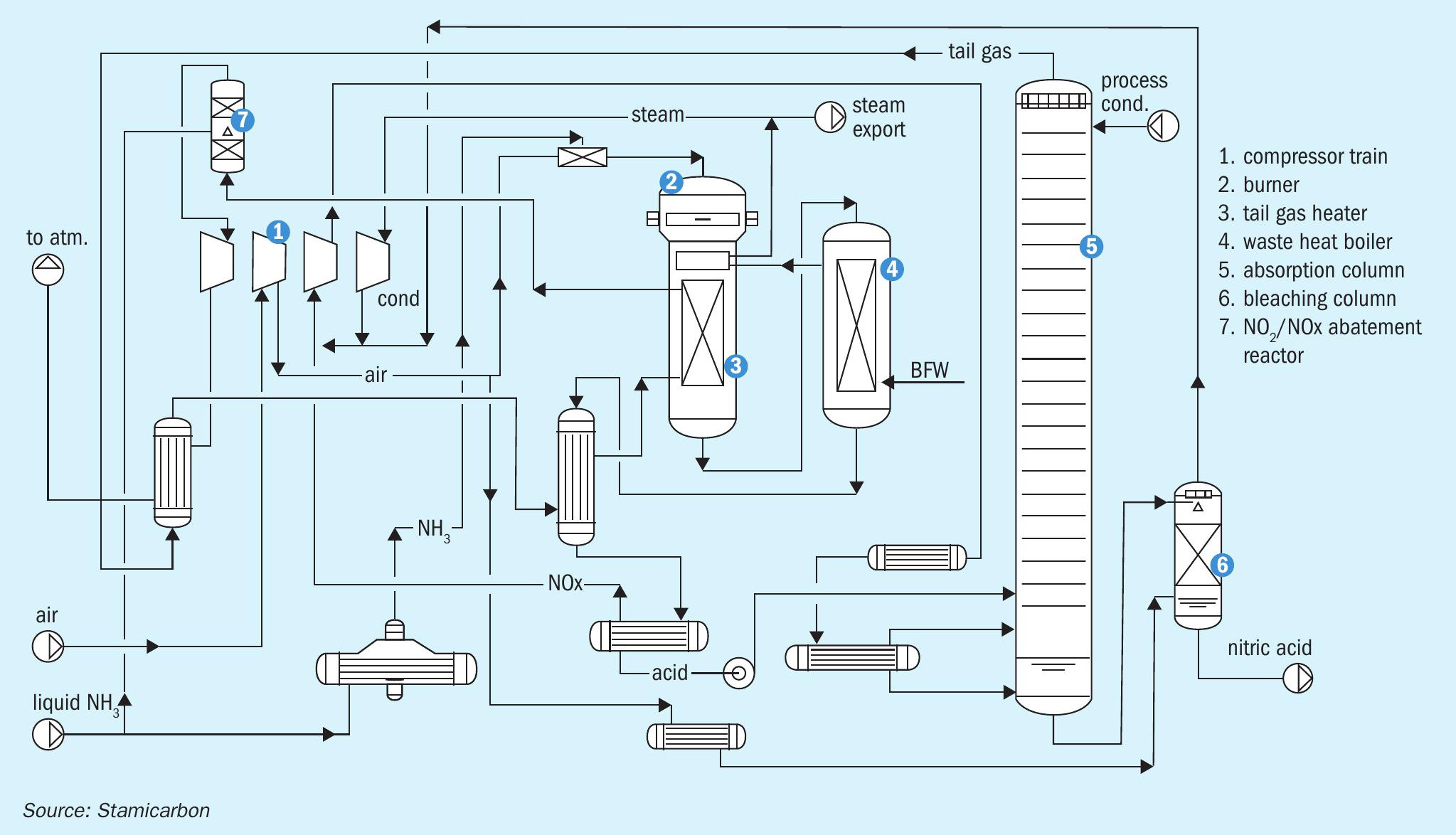
The main characteristic of both processes is a specific heat exchanger network downstream of ammonia oxidation. This configuration has several advantages. On the one hand, the heat exchanging network has specific process conditions selected to prevent corrosion and ensure that no proprietary materials are required for equipment manufacturing. On the other hand, the placement of the third tail gas heater in the ammonia burner vessel, closer to the platinum (Pt) gauzes, enables a tail gas temperature of 480°C to be achieved, which has several advantages:
- the operation of the tertiary abatement system with no addition of a reducing agent (like natural gas) for the nitrous oxide (N2 O) decomposition;
- higher power generation in the expansion turbine, leading to lower steam consumption of the compressor train and higher steam export;
- extra heat recovery step before releasing the tail gas into the atmosphere;
- reduced area required for the heat exchanging section.
Capex and opex analysis
Capital expenditure (capex) and operational expenditure (opex) are important considerations when designing, building, and operating a nitric acid plant. Capex refers to the initial investment or the cost of building a new nitric acid plant or expanding an existing one. This includes the cost of equipment, materials, and labour required to construct the plant. Capex can vary based on the size of the plant, the complexity of the production process, and the location of the facility. Building a large, advanced nitric acid plant can require significant capital investment, while expanding an existing plant may involve less capital expenditure.
Opex refers to the ongoing costs of running the nitric acid plant. This includes the cost of raw materials, energy, maintenance, and labour required for the ongoing production process. Opex costs can vary based on the operational efficiency of the plant, output volume, and regional factors like energy costs and regulations.
Overall, capex and opex are key metrics that must be carefully managed to ensure profitability in the nitric acid industry. Manufacturers can increase their profit margins and remain competitive in the global market by reducing capex and optimising opex.
Stamicarbon is able to advise producers on the best technology to select based on specific plant requirements and plant capacity. The choice of nitric acid technology and the careful management of capex and opex are critical factors in the success and profitability of production. Similarly, when considering opex, Stamicarbon’s nitric acid technology offers a range of options to reduce operational expenses, especially by maximising steam export.
The simplicity of the compressor train in a mono-pressure plant and the reduced number of equipment items make the mono-pressure technology more competitive from a capex point of view. However, operating the process at constant pressure compromises the process efficiency. The oxidation of NH3 to NO on Pt gauzes is more efficient when operating at a lower pressure, while the absorption column is more effective when operating at higher pressure. The use of dual-pressure technology overcomes this challenge since both sections are able to operate at a more optimal pressure, increasing the process efficiency and reducing the total operational costs. However, the compressor train design is more complex, and more items of equipment are required, especially extra heat exchangers, to eliminate the extra compression heat.
Based on these considerations, mono-pressure technology is advised for low plant capacities, while dual-pressure is mostly used for higher plant capacities. It is well known that the threshold for this selection is usually around 400-600 t/d (100% HNO3 ). However, producers tend to hesitate on which technology to select when their target production capacity belongs to this range. There is no universal answer to this question since local energy costs and regulations have a strong impact during the plant’s lifetime.
Case study
Stamicarbon together with Ballestra S.p.A performed an analysis for a nitric acid plant in Western Asia with a capacity of 450 t/d operating with Stamicarbon’s technology. For this capacity, capital and operational expenditures have been studied for both technologies, mono- and dual-pressure, in order to provide a better overview to the customer and help them with their final decision.
The calculations estimated that a dual-pressure plant requires around 25% higher capital expenditure than a mono-pressure plant.
To estimate the operational expenditures of the plants, the following parameters have been considered:
- total NH3 consumption;
- demin water consumption;
- cooling water consumption;
- demin water consumption;
- steam export HP;
- steam consumption LP;
- electricity consumption;
- precious metal losses.
Other operational expenditures like labour required to operate the plants are considered to be similar for both technologies and not relevant in the comparison. There is an operational cost difference of approx. 1.2m $/year between operating a mono- or a dual-pressure plant. For this specific case, the nitric acid producer could recover the extra cost paid for installing dual-pressure technology in nine years.
Technology integration in a fertilizer complex
Having a whole portfolio of technologies from green ammonia to ammonium nitrate allows Stamicarbon to improve its integration between plants and consequently optimise different technologies to make the full complex more attractive from an economic point of view.
Stamicarbon is integrating Stami Nitric Acid with Stami Green Ammonia in a green fertilizer complex, as already designed for projects in South America and Africa (see Fig. 3).
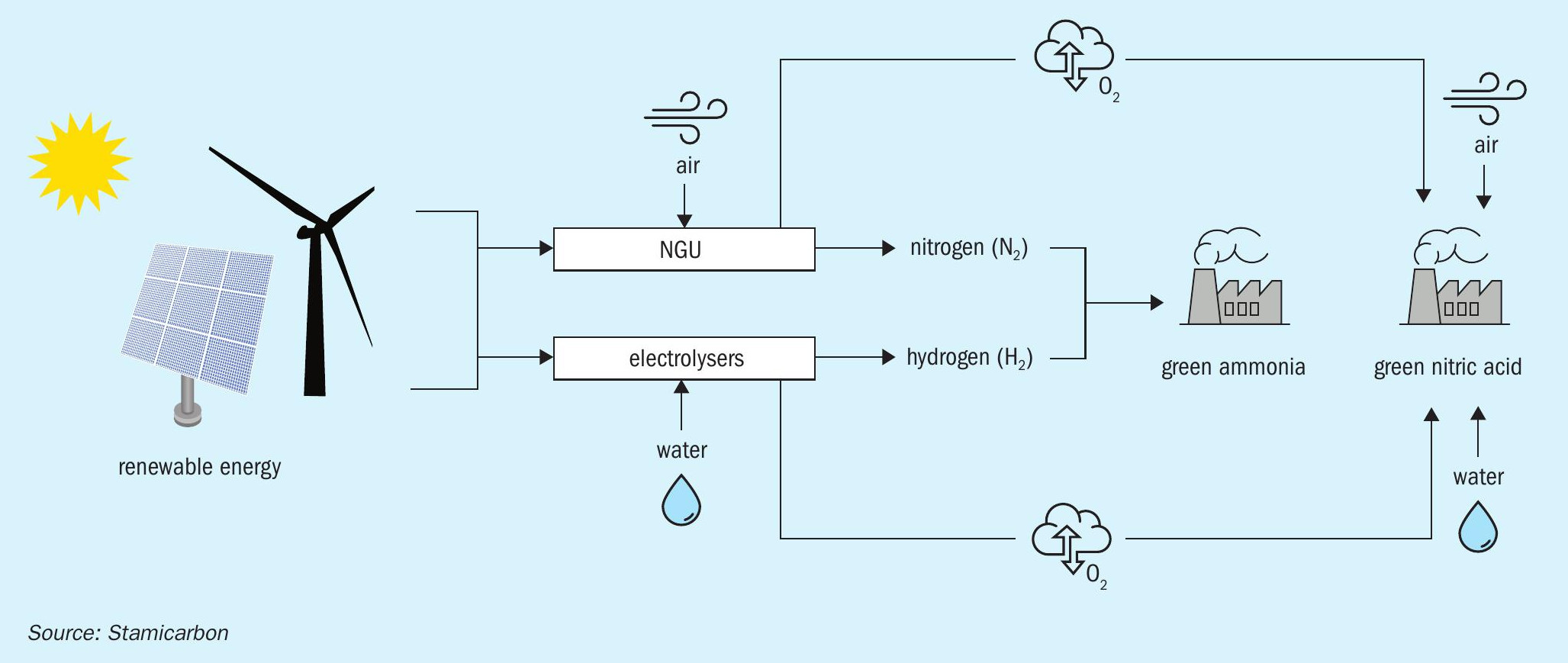
The innovative process to integrate the production of green ammonia and nitric acid allows the use of pure O2 in the nitric acid plant (Fig. 4). This reduces the volume of air needed to oxidise ammonia in the first step of nitric acid production. In turn, this can be translated into an increase in steam export and a reduction of the total amount of tail gas released to the atmosphere. As a result, the compressor train and the tail gas treatment section can be downsized and, subsequently, the capex of the plant can be reduced.
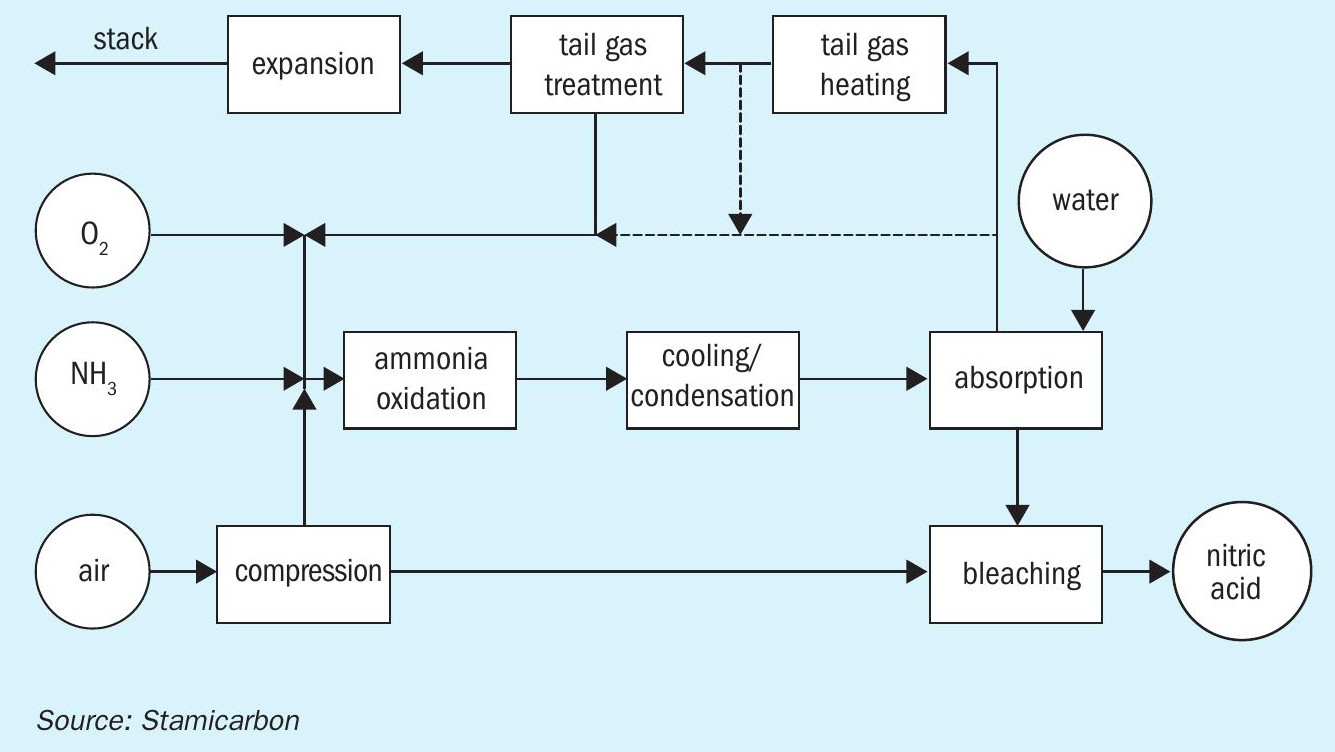
This optimised process has several advantages over the conventional method:
- Reduced emissions by recirculating a portion of the tail gas: Even without the change in NOx concentration in the off-gas after treatment, the total amount of pollutants emitted will be lower, reducing the total flow of NOx and N2 O sent to the environment by about 40%.
- Lower catalyst demand due to a lower flow rate through the abatement system: Even at a constant target concentration of NOx and N2 O, the cross-section and reactor height will be downsized, reducing the total volume of the catalyst by up to 40%.
- More positive power balance, therefore steam export increases by more than 30%.
- Less ammonia consumed by the NOx abatement system.
- Conversion increase potential by looping NOx gases back into the reaction (into the burner, bleacher, or both).
These advantages of integrating the oxygen stream into the standard technology (mono- or dual-pressure) can be translated into a reduction of capex and opex.
Regarding opex, it is important to consider the increase in steam export and the reduction of N2 O emissions, since the N2 O can be translated into CO2 equivalents, converted into savings of operational cost.
Based on the local prices and considering only the increase in steam export, the cost reduction is higher than 5 $/t of nitric acid, compared to the conventional mono-pressure concept. This is equivalent to more than one million USD per year of savings for a plant of 450 t/d.
Besides, carbon taxes and/or even carbon capture benefits are being implemented in an increasing number of locations around the globe. If this reduction is considered and the N2 O sent to the atmosphere is converted into CO2 equivalents, by implementing the integrated concept with oxygen addition, the cost reduction might be higher than 1% of the total operational costs when considering a capacity of 450 t/d. It is important to be aware that this tax is being applied in more and more locations and it is continuously being increased over the years, which implies a more significant reduction of operational costs in the upcoming future.
The following advantages refer to capital costs of the oxygen integration concept over the conventional mono-pressure technology. These advantages are not quantified in terms of capex savings.
- Regarding the absorption column there would be a reduction in height due to the higher oxygen content in the stream, while maintaining the diameter as in the conventional concept.
- The air compressor needed requires about 50% less power than in the standard concept.
- The tail gas expander could be smaller since the flow of tail gas that is sent to the stack is reduced by more than 40%.
- The size of the tertiary abatement reactor is reduced in the oxygen integration concept since there is less tail gas to be treated, which involves a reduction of the catalyst volume for the N2 O and NOx removal beds of about 40%.
“Capex and opex are key metrics that must be carefully managed to ensure profitability in the nitric acid industry.”
Alongside this reduction of capital costs, there is an additional component that needs to be added to the capital costs of the oxygen integration concept in the case of mono-pressure technology: a small compressor to overcome the pressure drop in the tail gas to be recirculated is needed.
By implementing the O2 integration concept, not only is it possible to provide a use for the O2 , usually considered a side product and vented to the atmosphere, it also provides a significant reduction in capital cost compared to a standard mono-pressure technology, while reducing the operational costs as well.
Most of the integrations of green ammonia and nitric acid are done in order to produce green nitrates or UAN as a final product. Several synergies can also be found in the waste streams of some processes, such as urea or AN production, that might be used as feed streams in other plants. Integration is also important in the utilities network to match the balances of steam and cooling water.
The road ahead – digitalisation
The biggest challenges to optimising the operation of a plant are maximising the capacity, bringing it to its best point of steady production and at the same time reducing the plant downtime aiming to improve margins. Besides these challenges, the world is committed to building a greener, better world in the upcoming years. Digital tools provide solutions to increase plant efficiency and reduce total operational costs by allowing users to control and optimise their processes and systems through well-trained and well-informed personnel. This will enable the producers to reduce waste, save energy and produce fertilizers in a safe, cost-effective, profitable and sustainable way.
Stamicarbon is now offering the Operator Training Simulator and the Process Monitor as part of grass root projects and for existing plants. While the Training Simulator focuses on well-trained operators and engineers, the Stami Digital Process Monitor provides operators, engineers, and management with real-time insight into their plant performance. These solutions are available for all the products in Stamicarbon’s portfolio, including the nitric acid technology.