Nitrogen+Syngas 385 Sept-Oct 2023
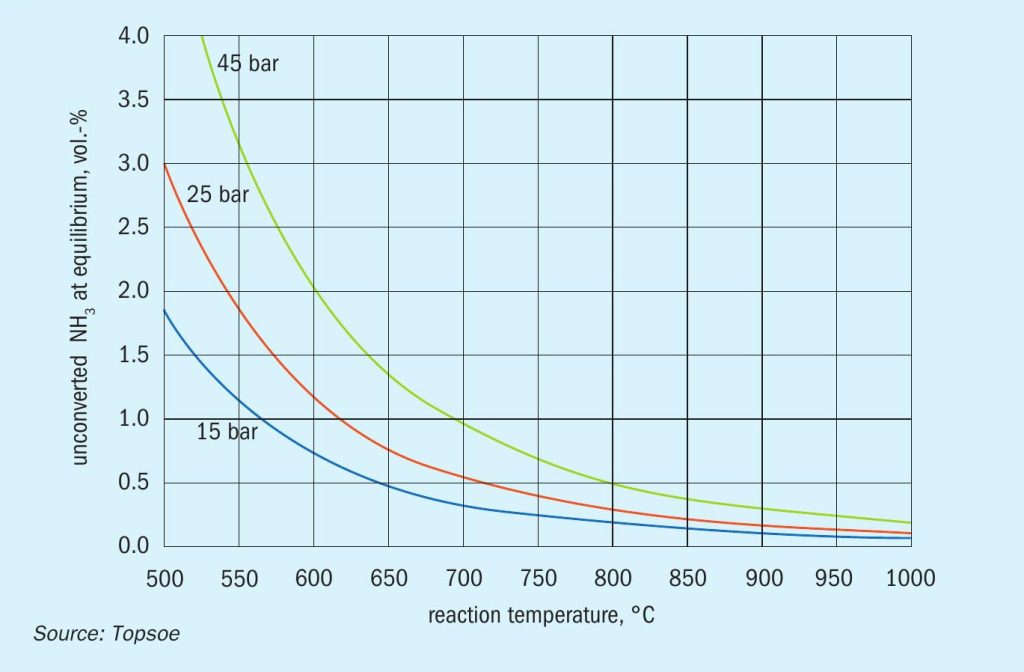
30 September 2023
Efficient and proven ammonia cracking at scale
AMMONIA CRACKING
Efficient and proven ammonia cracking at scale
Large-scale ammonia cracking for conversion of ammonia to hydrogen is a proven technology with decades of industrial experience. Topsoe shares its experience within ammonia cracking and presents an improved and highly energy-efficient (96%) ammonia cracking technology, H2Retake™ , developed based on Topsoe’s proven technology and industrial experience.
Ammonia has, for a long time, been identified as the energy carrier and storage medium of the future. But only recently, has it become a reality. Up until now, oil and fossil fuels have been the dominant media for global scale energy export, import and storage. However, the industrial transition, driven by the global ambitions to limit greenhouse gas (GHG) emissions, and the continuous reduction of renewable electricity costs are changing the landscape. Carbon-containing energy carriers and fuels will co-exist with ammonia, but due to the scarcity of sustainable carbon, they are not fully scalable and will only be available in applications allowing for higher pricing compared to the cost of ammonia as an energy carrier.
Introduction to ammonia cracking
The ammonia supply chain is robust and scalable. More than 20 million tonnes of ammonia are already being traded and transported across the globe. Mega-scale blue ammonia projects involving carbon capture and sequestration are currently being contracted, bringing high volumes of low carbon intensity ammonia to the market. Simultaneously, the market for green ammonia, based on renewable electricity, is developing with many mega-scale projects in the pipeline.
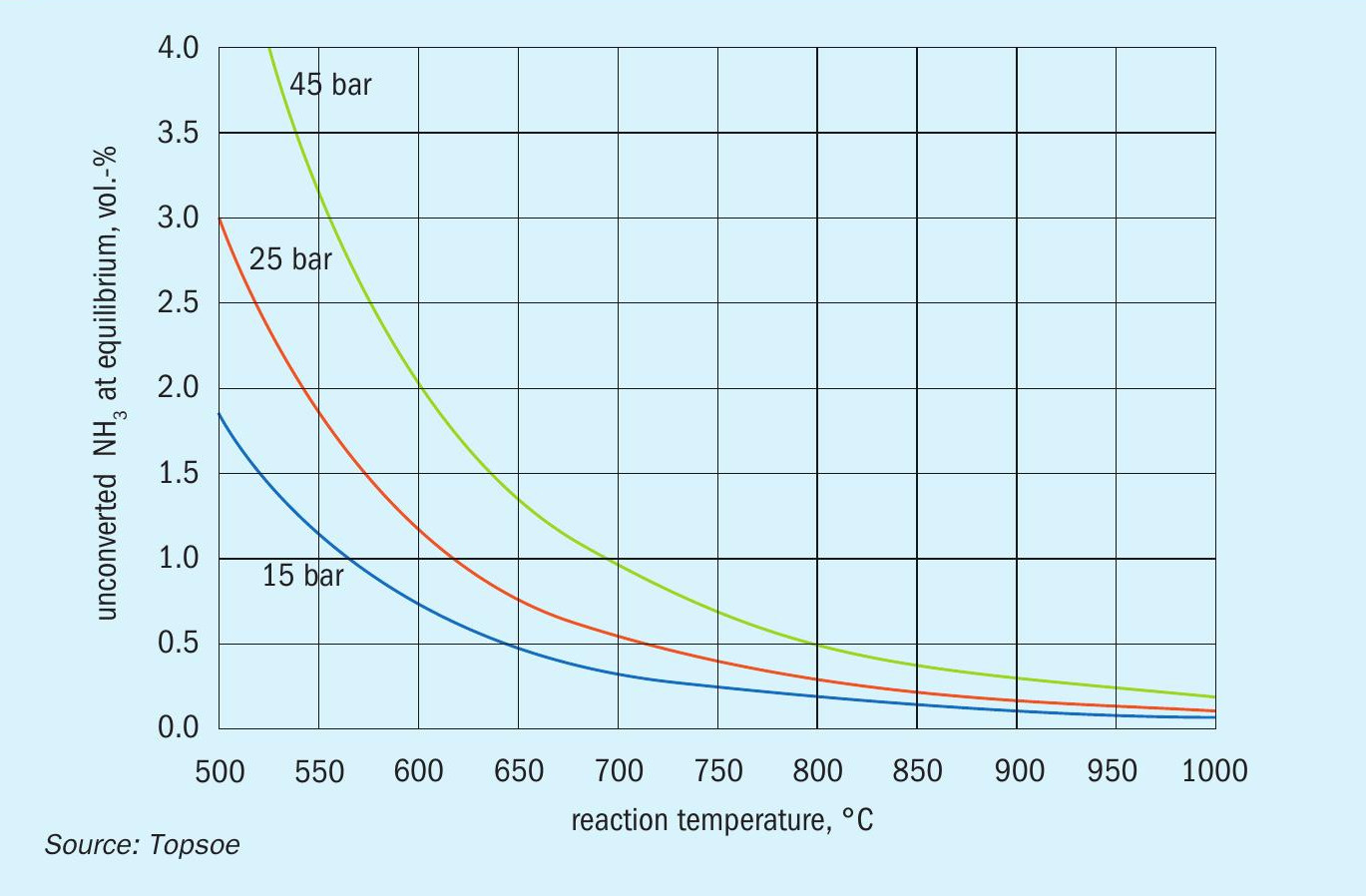
Ammonia cracking is the enabling technology for using ammonia as an energy source for applications driven by energy in the gas form. Applications of hydrogen or cracked gas (H2 /N2 ) from ammonia will include:
- substitution of conventional hydrogen in all existing industrial hydrogen applications and their future analogues, for example biorefineries;
- natural gas replacement in industrial applications such as gas turbines, gas engines, gas furnaces and boilers, as well as partial substitution in natural gas grids;
- future hydrogen applications such as hydrogen for road transportation.
Ammonia cracking can be:
- centralised, and large to mega-scale with hydrogen transported to the end-use in extended hydrogen grids, as planned in Europe;
- decentralised, large-scale and colocated with large hydrogen off-takers possibly via local hydrogen grids;
- small-scale decentralised for example at hydrogen filling stations.
Ammonia cracking theory
Ammonia is transported and stored as a liquid, typically at atmospheric pressure and -33°C. The first step in an ammonia cracking plant involves preheating and evaporating the ammonia. Evaporation of liquid ammonia requires 23 kJ/mol.
Cracking of ammonia to nitrogen and hydrogen is an endothermic reaction limited by chemical equilibrium.
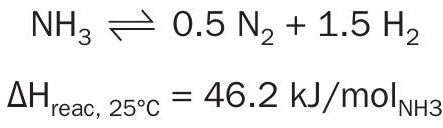
The endothermicity and the stoichiometry of reaction above means that ammonia cracking is favoured at high temperatures and low pressures. This is clearly observed in Fig. 1, which shows the dependence of the equilibrium conversion of ammonia on temperature and pressure.
Unconverted ammonia will leave the reactor as ammonia slip. In practice, the maximum temperature is limited by construction materials and cost. The optimal pressures are typically around 25–45 bar which will eliminate the need for a hydrogen compressor in many cases.
From these considerations, it is evident that the most basic layout for an ammonia cracking process includes at least the following steps:
- vaporisation and preheating of the raw ammonia feed;
- catalytic decomposition of ammonia;
- removal of unconverted ammonia and purification of the hydrogen product.
The minimum process energy input to convert -33°C liquid ammonia to 25 barg hydrogen can be estimated at ~72kJ/ molNH3 , dominated by the heat of evaporation and the cracking reaction.
The heat input for the process can be supplied in different ways. The choice of the energy source will depend on factors such the availability, costs, plant scale, emission constraints and product carbon intensity target.
The ammonia cracking process is typically characterised by two metrics: the hydrogen efficiency, and the energy efficiency. The hydrogen efficiency represents the fraction of hydrogen atoms in the raw ammonia that ends up as hydrogen product.
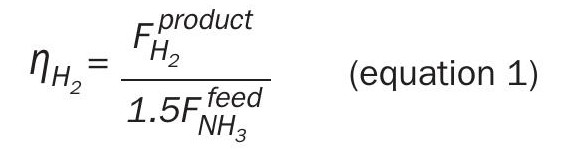
where is the molar flowrate of hydrogen produced and
is the molar flowrate of ammonia in the feed.
The energy efficiency is defined as the ratio of the energy of the product hydrogen to the total energy of the ammonia feed stream and any external fuel plus any power consumption:
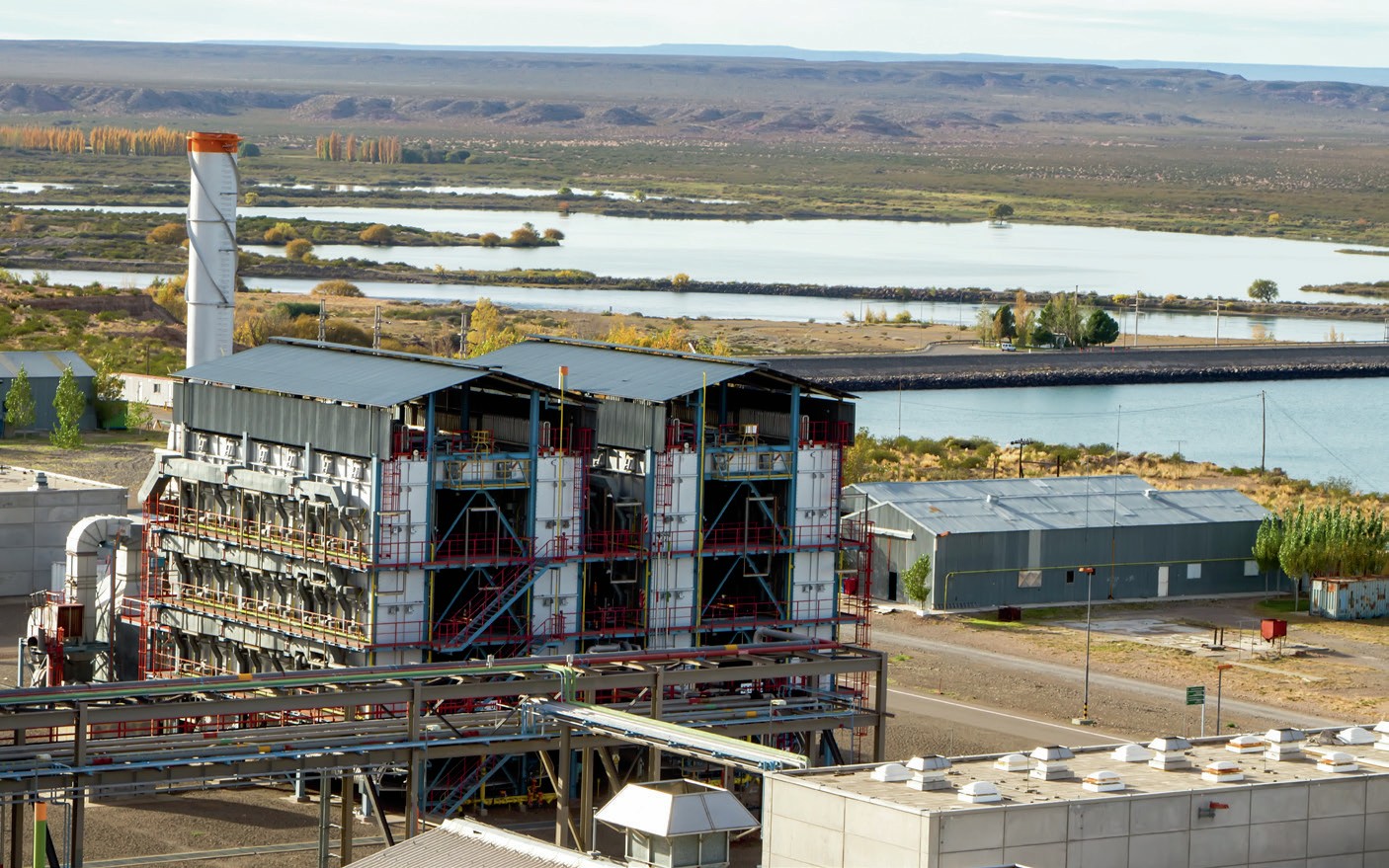
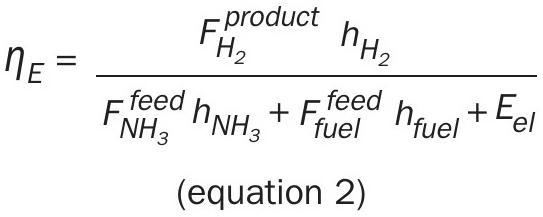
hi is the specific mole-based energy of compound i referenced to the standard conditions (25°C and 1.01 bar) and Eel the input of electric work.
Ammonia cracking references
Topsoe commissioned its first plant back in 1978. Since then, Topsoe has designed and commissioned several other large-scale ammonia crackers for application in heavy water production by the so-called monothermal ammonia-hydrogen exchange process.
Topsoe’s largest ammonia cracker to date was commissioned in 1993 in Arroyito, Argentina. It is referred to as the Planta Industrial de Agua Pesada (PIAP). The PIAP plant has two parallel lines, and each line has an ammonia cracker decomposing 2,400 t/d of ammonia (see Fig. 2). Topsoe’s plants are specially designed to withstand the harsh operating conditions and the risk of nitridation. The plants are also supplied with a tailored Topsoe ammonia cracking catalyst with proven performance.
H2Retake™
In 2022, Topsoe launched an ammonia cracking technology which conservatively updated the industrial ammonia crackers from the heavy water application to a hydrogen process. The 2022 version of the ammonia cracking technology is a fully proven technology albeit not fully optimised.
In 2023, Topsoe is launching the H2Retake™ ammonia cracking technology which builds and improves on the proven fired cracking technology and decades of industrial experience to achieve very high energy and hydrogen efficiencies. A simplified diagram of the H2Retake process layout is shown in Fig. 3.
In Topsoe’s H2Retake technology, the liquid ammonia feed is pumped to a pressure above that required for H2 delivery (typically 25-45 bar g). The ammonia is vaporised and preheated by transferring heat directly from the hot process and flue gases, which avoids the cost and complexity of having a steam system.
The decomposition of ammonia into hydrogen and nitrogen takes place in an adiabatic pre-converter followed by a fired tubular cracker. Pre-conversion decreases the fuel demand of the fired cracker and makes the best use of the flue gas energy from the firing.
The heart of the ammonia cracking technology is the well-proven fired cracker installed in Topsoe’s referenced plants. Multiple parallel tubes filled with catalyst are heated by burners placed on the walls at various elevations to secure a good temperature control. The burner flames are directed backwards against the furnace wall, eliminating any risk of flame impingement of the catalyst tubes. Despite overall similarities in the design with conventional steam methane reformers, very important differences in the choice of materials exist, which must tolerate harsh nitridation conditions in the ammonia cracker, and in the choice of catalyst.
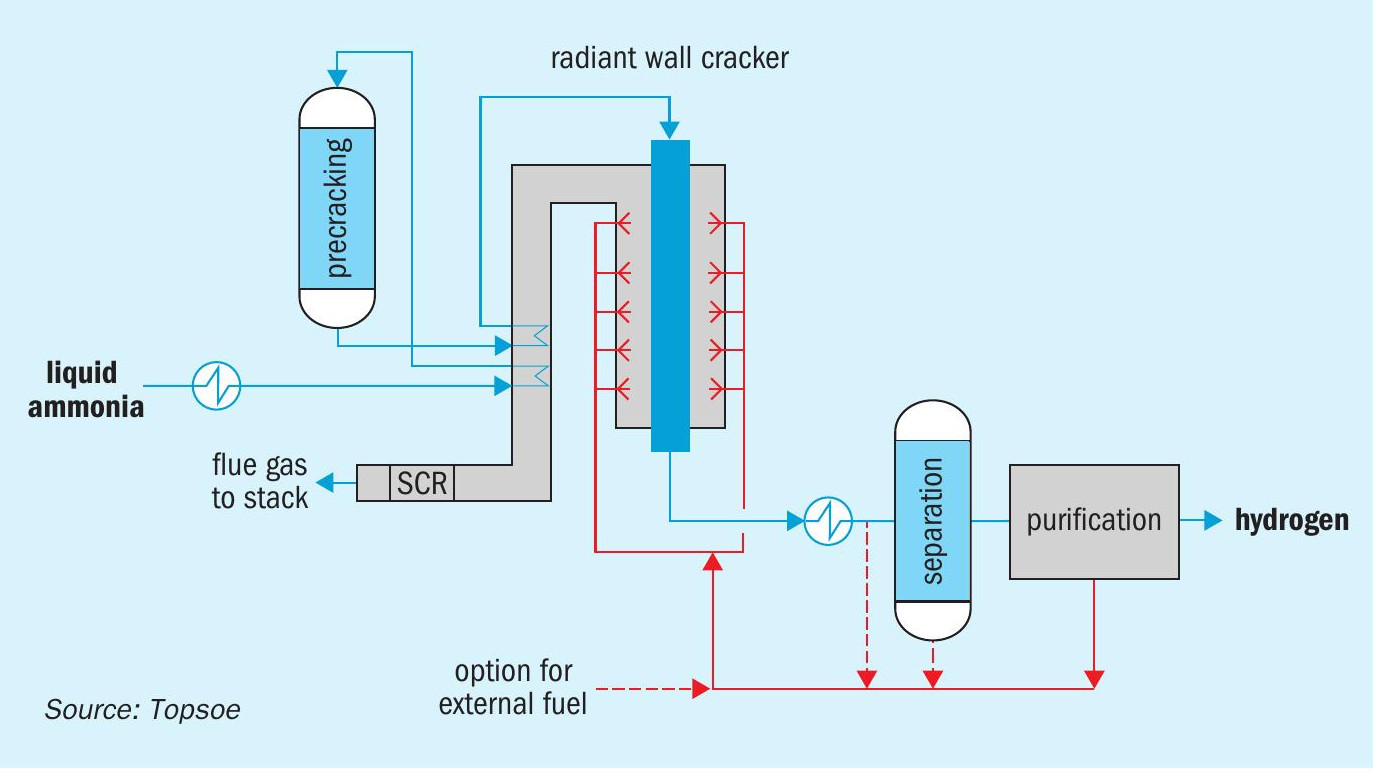
The process gas leaving the fired cracker contains a small amount of unreacted ammonia due to the reaction equilibrium. This ammonia is removed from the cracked gas before it enters the pressure swing adsorption (PSA) columns, where the final purification of the hydrogen product takes place. The residual ammonia is separated from the gas by a simple water wash. It is then recovered, mixed with the PSA tail gas and sent to the cracker furnace where it is used as fuel. A selective catalytic reduction (SCR) unit located in the exhaust of the fired cracker ensures that the NOx and N2 O emissions remain within project requirements.
A range of supporting technologies for ammonia cracking, such as ammonia storage, ammonia recovery, hydrogen compression, and high hydrogen fuelled burners, have been extensively proven, documented, and successfully utilised in similar applications for decades and can as such be viewed as TRL 9. It is important to note, as mentioned, that these supporting technologies are not the core components in an ammonia cracking plant. The core components encompass the ammonia cracker, the ammonia cracking catalyst, the hydrogen purification system, and the SCR DeNOx system.
Topsoe is in a unique position where all these core components have reached technology readiness level (TRL) 9 as indicated in Table 1 and have been thoroughly proven on an industrial scale.
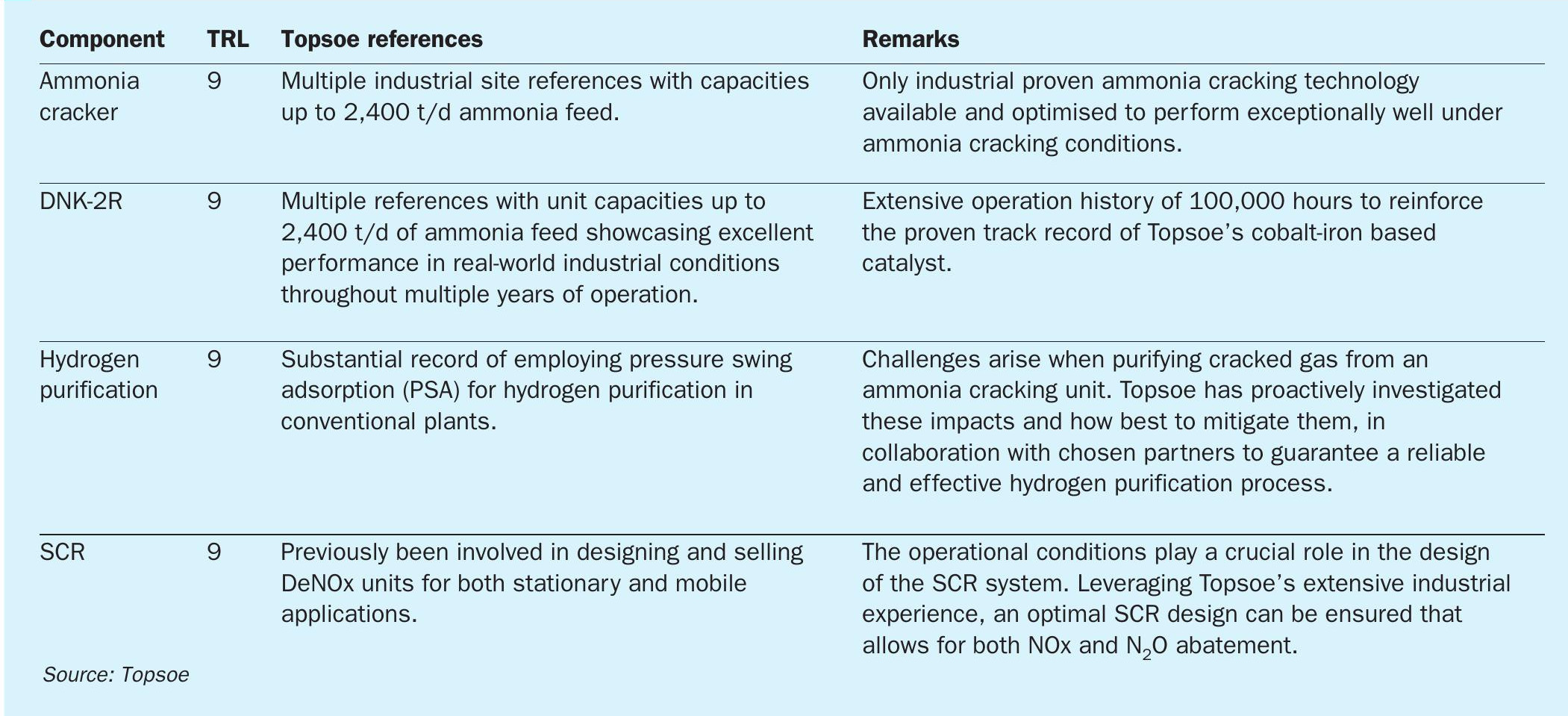
Ammonia cracking catalysts
Commercial grade ammonia contains 0.2-0.5 wt-% H2 O to prevent corrosion during transportation and storage. In the energy and cost efficient H2Retake technology, the ammonia carries this humidity through the catalyst beds. This makes catalyst selection non-trivial because water adversely affects the activity of ammonia cracking catalysts by two different mechanisms:
l Water competes with ammonia for the available active sites, thereby inhibiting the cracking reaction. The effect is reversible, meaning that if the water is removed, so is the inhibition. Catalysts operating at low temperatures are particularly susceptible to this mode of deactivation, for example those based on noble metals.
l At higher temperatures, the water will accelerate sintering, and a catalyst may deactivate irreversibly due to the loss of active surface area. Catalysts operating at high temperatures are particularly susceptible to this mode of deactivation, although well-designed catalysts can be very stable.
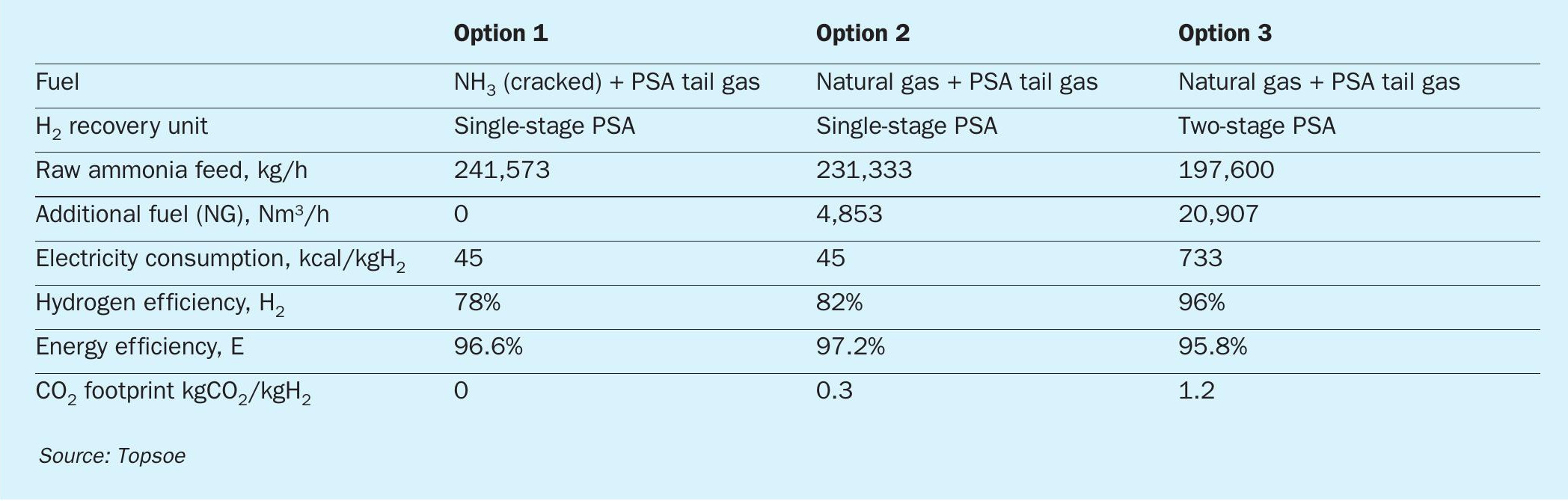
Due to their lower cost, catalyst formulations using base metals are preferred over catalysts containing noble metals. Nickel catalysts are the most widely used in small-scale ammonia crackers. However, not all nickel catalysts can perform satisfactorily in industrial crackers where energy efficiency is crucial. Most of them exhibit low activity and poor stability in the presence of the water levels usually found in commercial ammonia. This is exemplified in Fig. 4, which compares a conventional Ni-catalyst against Topsoe’s stabilised Ni-catalyst DNK-20. The performance is comparable in a water-free atmosphere, but the activity of the conventional Ni-catalyst drops dramatically with exposure to 0.2 vol-% H2 O. In contrast, due to a careful selection of structural and electronic promoters, Topsoe’s DNK-20 displays high and stable activity even in the presence of water.
“Ammonia as the energy carrier and storage medium of the future is becoming a reality, …
Topsoe’s portfolio also includes the ironcobalt-based catalyst DNK-2R, a market leading non-noble metal catalyst, fully proven in heavy water plant ammonia crackers. It is almost twice as active as the best nickel catalyst, and it can operate in a water-containing gas down to 400°C. Topsoe’s ammonia cracking catalysts are the only ones with references in large-scale crackers.
Process merits
In H2Retake, the energy input to the fired ammonia cracker is efficiently utilised to drive the decomposition reaction and to evaporate and preheat the raw feed with minimal waste. As a result, an energy efficiency of 96% is achieved and a hydrogen efficiency of up to 96% depending on the fuel choice (see Table 2).
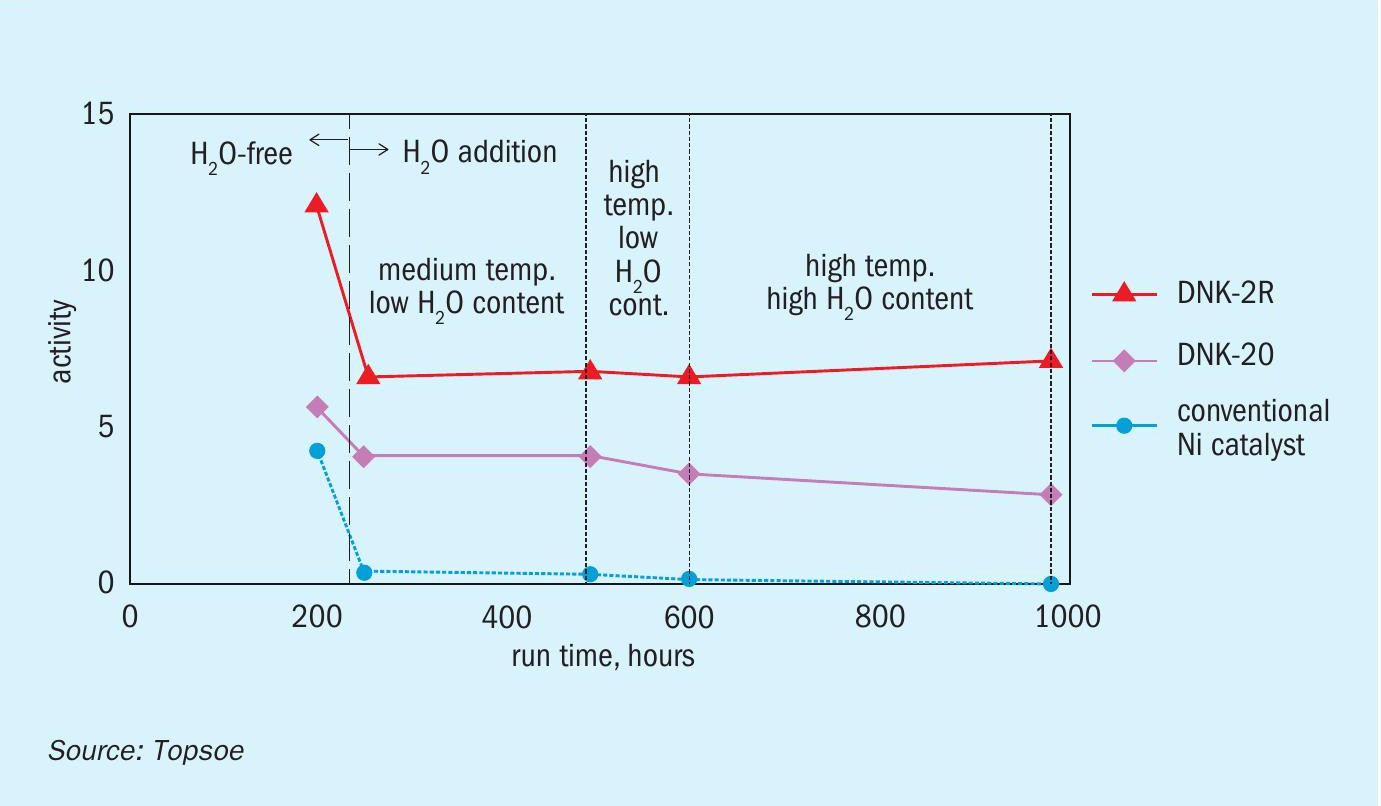
Key technology features allowing this performance are:
- Very active, non-noble metal catalysts allow operation down to 400°C. Direct heat integration between the process streams eliminates the need for a steam system. Water tolerant ammonia cracking catalyst capable of operating with the water levels present in commercial-grade ammonia, eliminating the need for distillation.
- No usage of cooling water minimises energy losses.
Replacement of the cracked gas in the fuel mixture with an alternative fuel allows larger recovery of hydrogen from the ammonia feed but can result in CO2 emissions. The hydrogen recovery can be further maximised by implementing a two-stage PSA separation. However, this reduces the energy efficiency slightly due to a requirement of an interstage compressor. Table 2 compares the efficiencies of different process configurations for an 800 t/d H2 plant.
Conclusion
Ammonia as the energy carrier and storage medium of the future is becoming a reality, and the market is currently experiencing a significant interest in large-scale ammonia cracking. Large-scale ammonia cracking technology from Topsoe is fully proven, with several industrial references and high-performance catalysts. Furthermore, with Topsoe’s newly released H2Retake technology, improvements are available to realise an energy-efficient process and high hydrogen efficiencies. An energy-efficiency of up to 96% can be achieved, dependent on supplementation of any external fuel for process heat.