Sulphur 408 Sept-Oct 2023
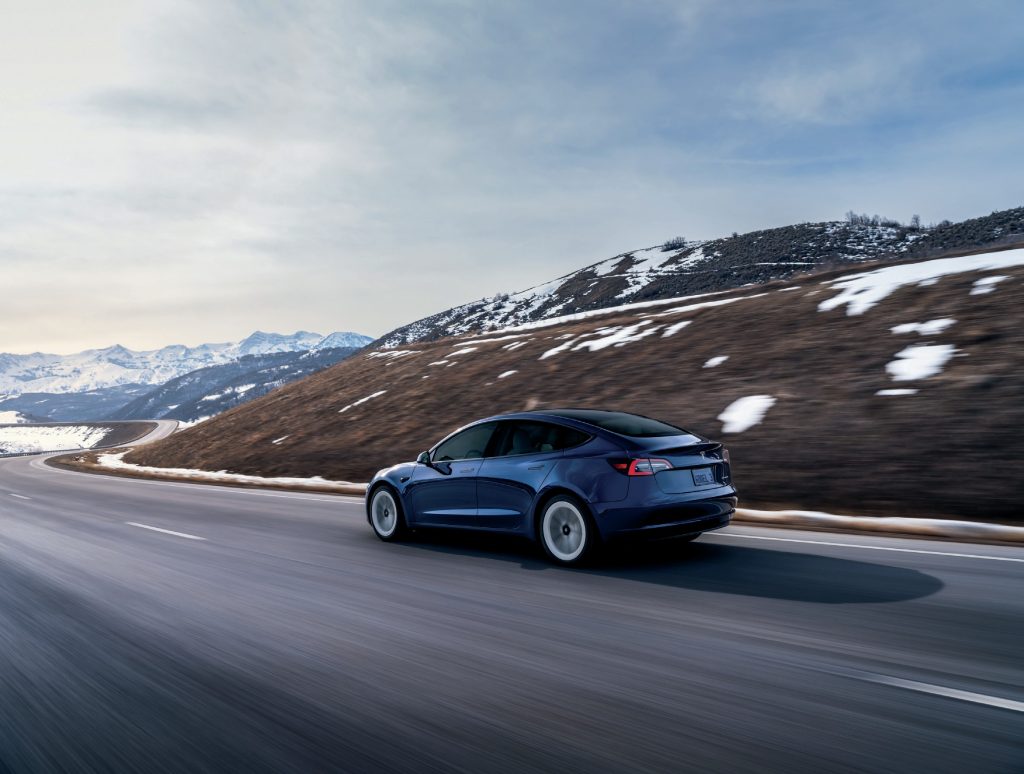
30 September 2023
Is LFP the ‘next big thing’?
BATTERIES
Is LFP the ‘next big thing’?
Lithium ion battery production is driving major expansions in nickel and cobalt extraction, but lithium iron phosphate (LFP) battery use is growing rapidly.
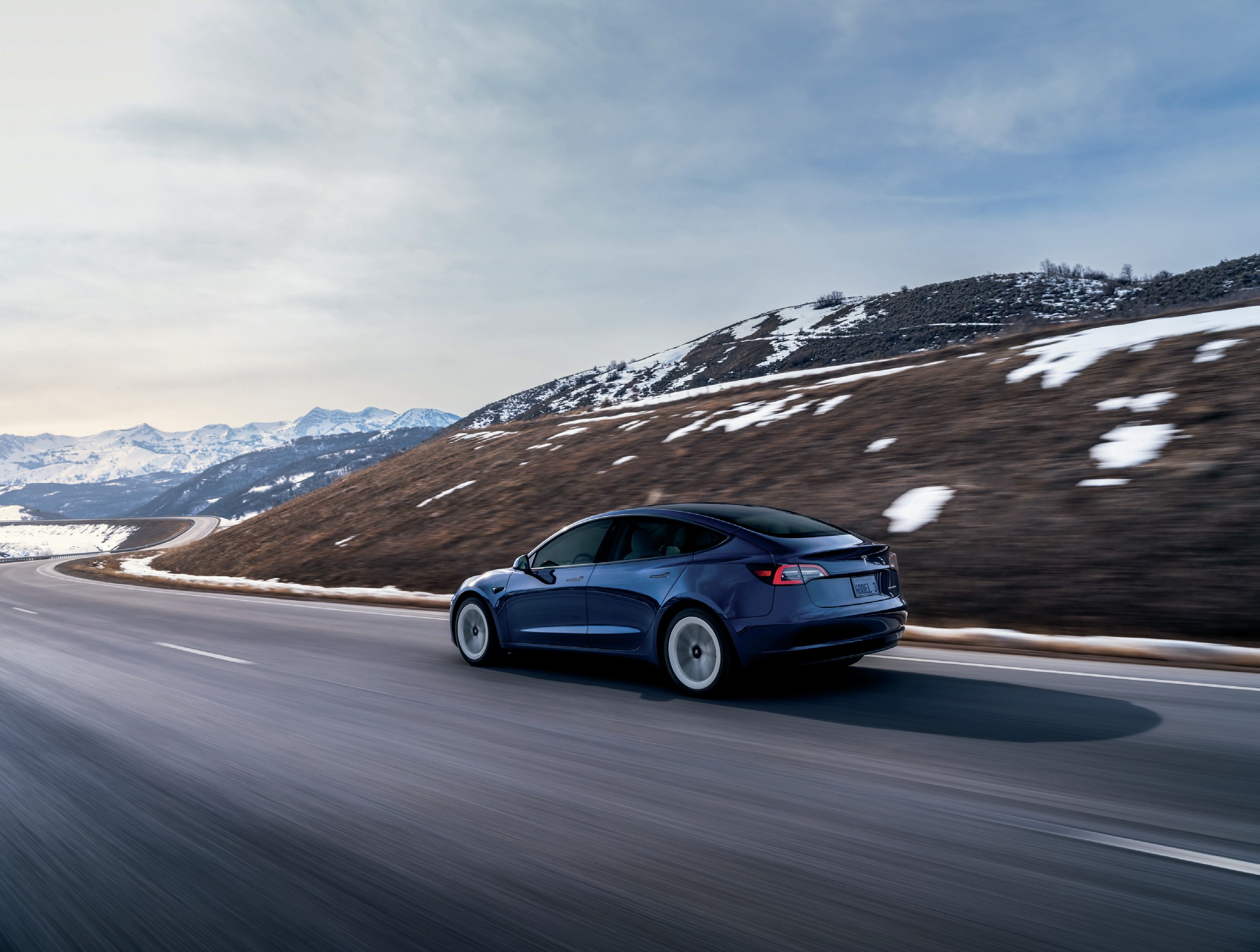
The electrification of the world has driven increasing use of a number of strategic minerals, particularly copper, and with it demand for the sulphuric acid used to extract the metals from the other components of the rock that they are bound into. As electrification spreads from power grids into automotive uses, there has been a new push for nickel, cobalt and lithium. Increased copper and cobalt mining in Africa’s copper belt, the nickel high pressure acid leaching plants springing up in Indonesia and the new lithium mines being developed in the US are just three symptoms of this.
So far, the recent wave of new capacity has been based around serving new lithium ion battery production, which has been growing at astonishing rates of up to 40% year on year. But ‘lithium ion’ actually covers a range of battery chemistries, including nickel manganese cobalt (NMC) and nickel manganese aluminium (NMA). NMC has become the dominant technology for personal electronics and some electric vehicle (EV) producers, including Volkswagen and some Tesla models, and this is leading to the increased appetite for cobalt in Africa. However, a competing technology, lithium iron/ferrous phosphate (LFP), is also becoming increasingly important.
Different chemistries
Both types of battery use graphite as an anode for lightness, but differ in their cathode composition. NMC contains a mixture of lithium manganese oxide and lithium cobalt dioxide, and produces the highest energy capacity; between 150-200 Watt hours per kg (Wh/kg). By comparison, LFP (LiFePO4 ) has an energy capacity of 90-120 Wh/kg. This is why NMC has come to be preferred for electronics that require high levels of power density like laptops, mobile phones and tablets, as well as automotive applications. However, they also have disadvantages. NMC batteries are less stable, especially in environments with higher or fluctuating temperatures. They heat up quickly and because of their oxide component have been known to experience runaway thermal reactions leading them in the worst cases to catch fire. The oxygen is released when the cell suffers an internal short circuit and heats up. Since fires require fuel, oxygen and an ignition source, robbing the fire of any of these will put it out. However, once a fire starts in a nickel-cobalt battery, it produces its own oxygen which is why these fires are so difficult to extinguish. Fire protection agencies cite lithium battery fires as the fastest growing fire risk in many countries.
LFP batteries, conversely, have excellent chemical and thermal stability. Furthermore, NMC batteries have a life cycle between 500-1,000 charging cycles, much lower than the 1,000-10,000 cycles that LFP batteries can tolerate. This makes lithium iron phosphate batteries much better for applications that need to run for long periods of time without being changed.
The weight penalty of LFP batteries means that NMC is likely to be preferred for personal electronic items, but for electric vehicles that do not require the longest ranges, some EV manufacturers have preferred the better thermal stability of LFP batteries, including Ford and Tesla’s Model 3. There is another factor as well; battery cost is the single largest component of EV cost, and LFP batteries are typically cheaper than NMC batteries. Both require lithium, but iron and phosphates are generally cheaper than cobalt, nickel and manganese, particularly following the price spikes in commodities after the Russian invasion of Ukraine.
Another issue is the potential scale-up required for battery production. Nickel sulphate demand has been rising at around 12% year on year, and in spite of the HPAL boom in southeast Asia, not enough high grade nickel production is coming on stream to meet projected demand. It is estimated that by 2030 there could be a shortfall of up to 400,000 t/a of nickel unless new projects are developed quickly. To achieve the estimated 3.1 million t/a of nickel required by 2040 would require around 70 new nickel projects, at a typical annual production capacity of 45,000 t/a. Phosphate, however, is already mined at 20 times the volume of nickel, and scaling up is likely to be less problematic.
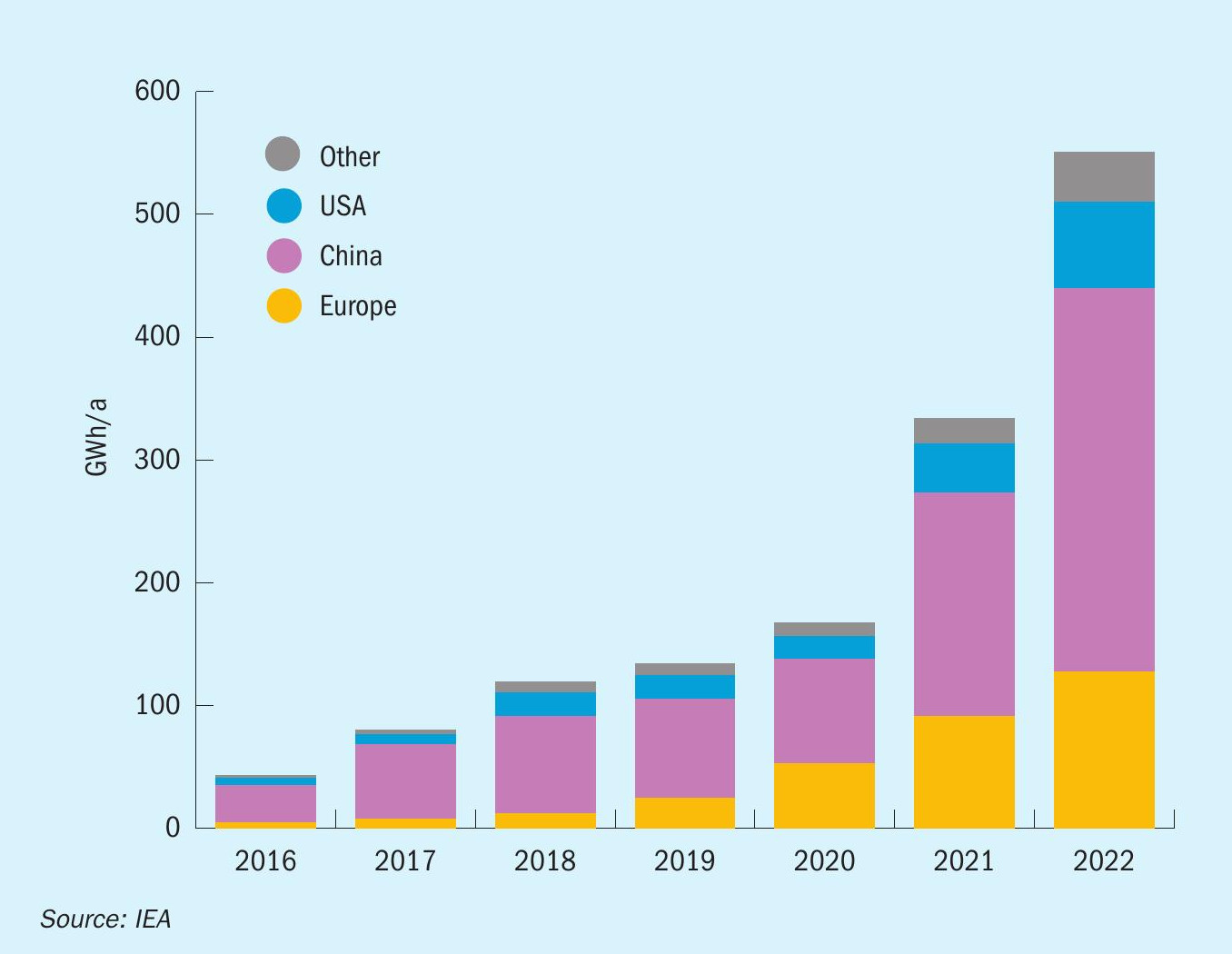
China leading demand
LPF batteries already power the majority (60%) of electric vehicles in the large and rapidly growing Chinese EV market, and they are now starting to make inroads in North America and Europe. By the end of last year, LFP batteries had already claimed one third of the global market for EV batteries, and that share seems likely to rise. While this will have a similar effect on the lithium market whether NMC or LFP batteries are produced, a preference for LFP has the potential to affect the phosphate market. To produce one tonne of LFP requires 0.73 tonnes of 85% phosphoric acid, and therefore of course a slightly higher quantity of sulphuric acid.
“China’s EV market grew by 80% in 2022 alone”
In 2021, China’s capacity for manufacturing LFP stood at 970,000 t/a. By the end of 2022, this had reached 3 million t/a, including 370,000 t/a of capacity at Hunan Yuneng, 200,000 t/a by Longbai Group; 190,000 t/a at German Nanometer; and 100,000 tons at Longpan Technology, who acquired Changzhou Liyuan. New and planned capacity additions, according to Acuity Commodities, include another 3.1 million t/a in 2023, and 2.8 million t/a in 2024. These capacity additions include battery manufacturers such as Hubei Wanrun and Hunan Yuneng; mineral suppliers such as GEM, Huayou Cobalt and Zhongwei; and chemical phosphate and titanium dioxide manufacturers like Longbai Group, Chuanfa Lomon and Jinpu Titanium. Partnerships are forming between EV manufacturers, battery companies and raw materials suppliers in order to secure sufficient supply.
LMFP
A new wrinkle to LFP development is lithium iron manganese phosphate (LMFP), by doping iron in lithium manganese phosphate to form a solution. LMFP has a higher energy capacity than conventional LMP; up to 260 Wh/kg. However, it suffers by comparison in terms of number of charging cycles, though still better than NMC. Manganese precipitation remains a niggling problem with the technology, though iron: manganese ratios can be adjusted to mitigate this, though this also lowers the energy capacity, and there is considerable research development effort being put into solving this issue, using concentration gradients or carbon coatings. Low temperature performance can also be relatively poor. Nevertheless, China’s (and indeed the world’s) largest battery maker Contemporary Amperex Technology Co Ltd (CATL) has began construction of a new LMFP battery factory in June 2022, with completion due this year.
Acid demand
While the LFP capacity additions in China are spectacular, they are also running considerably ahead of demand. However, demand is increasing rapidly and will begin to catch up over the next few years. China’s EV market grew by 80% in 2022 alone, and worldwide the EV market continues to evolve rapidly as shown in Figure 1. Wood Mackenzie estimates that total world demand for LFP will be 685,000 t/a this year, and that it will continue to rise at an average annual growth rate of 13-14% year on year for the next ten years. This would take it close to 2 million t/a by 2030, with a similar effect on phosphoric acid and sulphuric acid demand over that period, outside of the lithium required.