Nitrogen+Syngas 385 Sept-Oct 2023
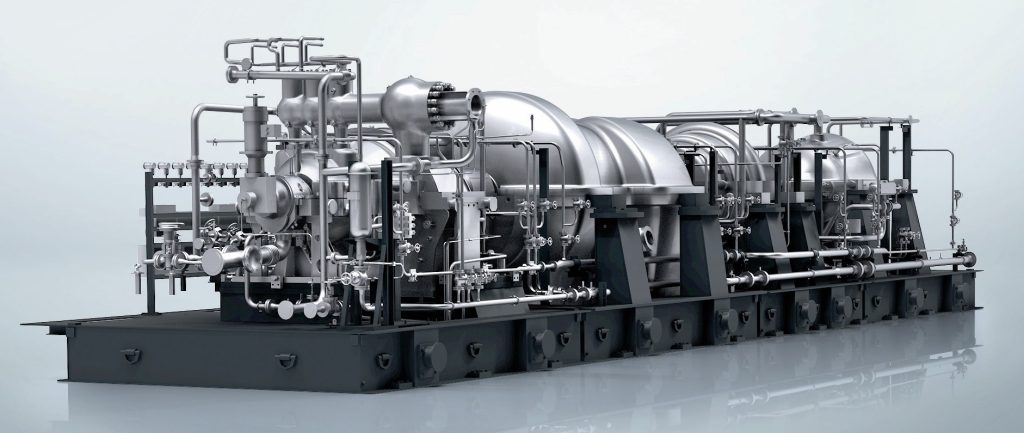
30 September 2023
Optimise fertilizer production by plant digitalisation
DIGITALISATION
Optimise fertilizer production by plant digitalisation
Plant digitalisation can contribute to increase the profitability of chemical plants by optimising performance of operation as well as maintenance. Available digital products range from visualisation of plant data for increased transparency to closed-loop AI controllers based on digital twins.
Digitalisation is a large field of unlimited possibilities. It is not surprising that it can mean different things to different people. Commercial experts look at accounting, order management, warehouse management and other elements, mostly covered by modern ERP systems. Engineers are interested in operating data and their optimisation or are developing new ways for designing plants. Others may be looking from different perspectives. However, all areas of digitalisation have one thing in common: new applications, more powerful computers, and better network connections, even in remote locations, offer ever increasing possibilities of digitalisation.
McKinsey expects that chemical companies can improve their end-to-end EBITDA by 8.5 to 16% by applying digital technologies1 .
However, there are also some critical issues which must be mentioned. Of course, data security is an important topic to be discussed as cybercrime is increasing every year. In addition, digitalisation can be disappointing for customers, especially when it comes without domain expertise. The simple use of algorithms does not solve customer problems in most cases. It usually needs domain experts to interpret data and consult customers on how to optimise their operation, which is not surprising in a very complex environment in which typically several hundred signals must be processed. thyssenkrupp Uhde has been active in plant digitalisation for more than 15 years and in chemical process technologies as well as engineering and construction for more than 100 years.
Today, thyssenkrupp Uhde offers a wide range of digital products which help its customers to maximise production, reduce raw material and energy consumption as well as effectively lower emissions. In addition, digitalisation can significantly improve plant availability and safety.
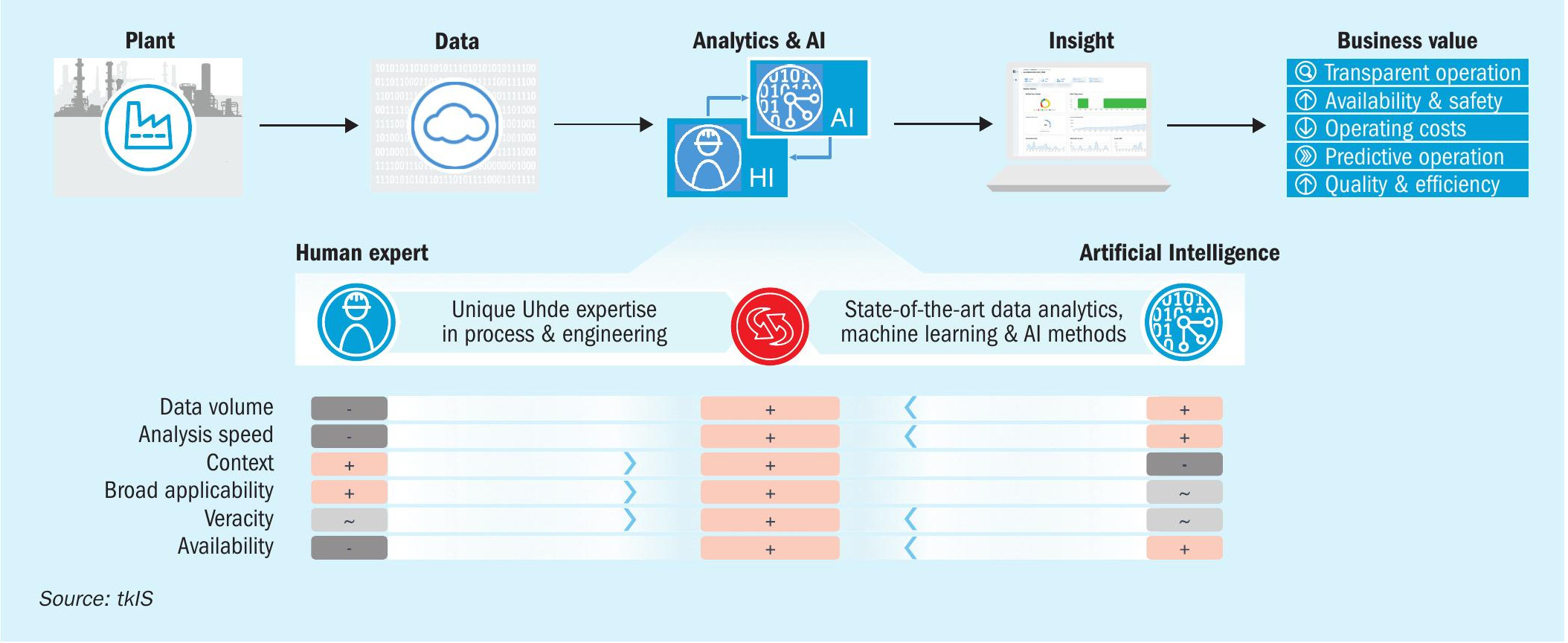
Digital products can be divided into four categories (Fig. 1):
1. Data analytics and consultancy: This includes service products like remote condition monitoring of the plant, regular reporting with thyssenkrupp Uhde expert advice and root cause analysis of issues.
2. Digitalised maintenance: This covers methods to detect wear, predict failures and the remaining lifetime.
3. Predictive operation: These products support personnel to operate the plant to increase production rate, availability and product quality, while lowering consumption figures.
4. Performance optimisation: While digital products from category 3 are still “openloop”, leaving the final decision whether to follow the suggestions with the operators, products within this cluster automatically optimise plant performance without involvement of operators.
Many of the products from categories 2 to 4 are based on a “digital twin”. However, what is a digital twin and how can it help customers?
By definition, a digital twin is a virtual representation of a physical object that should describe this object in a precise manner. Digital twins can be found in the fields of science, medicine, engineering, pharmaceuticals, sports, and many more.
A digital twin of a chemical plant may cover the following elements (refer also to Fig. 2):
- Process model: This model describes the process behaviour of the plant and is typically either based on a process simulation (white box) or an empirical, mathematical (black box) model. Such models help to optimise plant performance.
- 3D model: Typically developed during the engineering phase, this model represents the exact geometrical representation of the plant and can be used for planning of maintenance and revamp activities.
- Maintenance management model: Typically, this is available in all modern CMMS applications and contains equipment information like data sheets, spare parts, equipment history, planned maintenance tasks, etc.
thyssenkrupp Uhde is able to provide all of the above-described models and combine them to generate one common digital twin of a chemical plant. Alternatively, it is also possible to focus on single elements only, e.g., the process model.
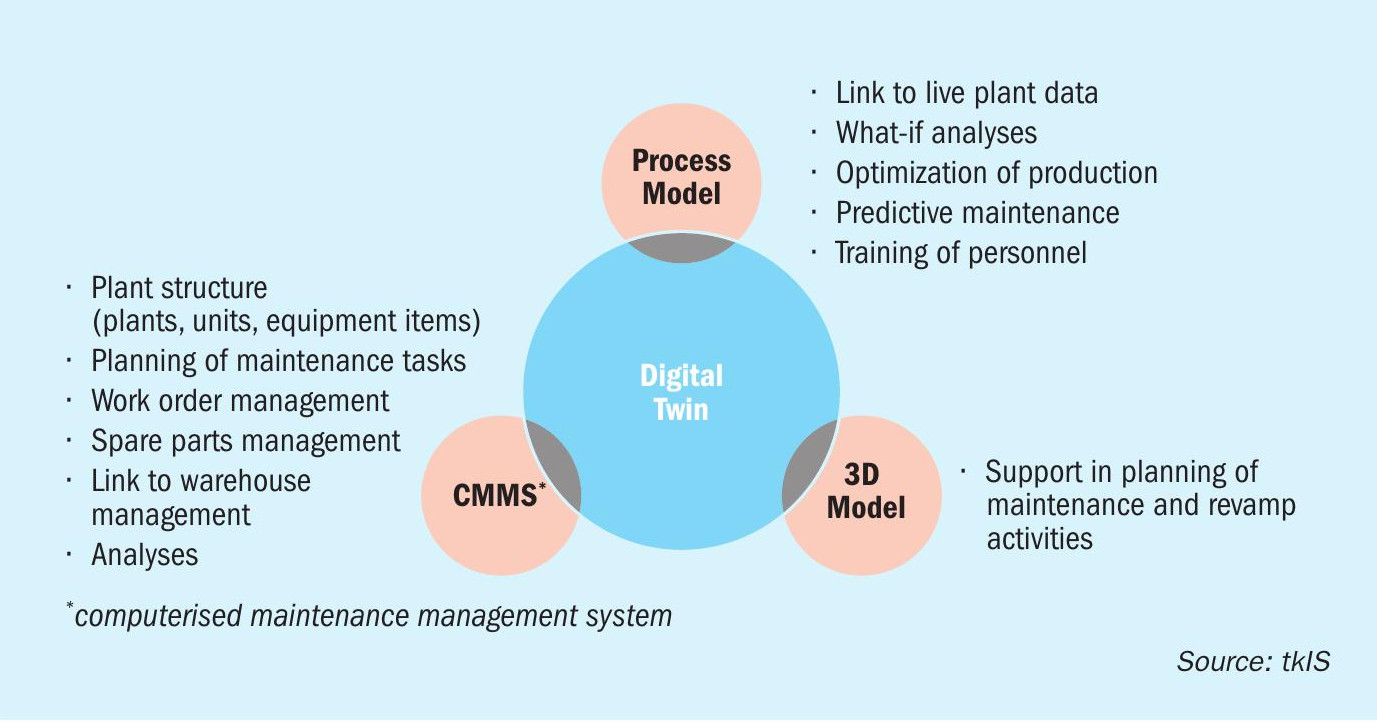
In the following sections, some examples of digital products applied in customer projects are described.
Product quality prediction in CAN granulation
tk Uhde and Tech Center Control Technology (TCCT), thyssenkrupp’s competence centre for data analytics and AI, have jointly developed a method for quality prediction in CAN granulation to solve the problem of the accumulation of off-spec material in this complex process with a large recycling loop during the time-consuming laboratory analysis. State-of-the-art machine learning algorithms like neural network models were used to develop the AI (Artificial Intelligence) tool. The neural network was trained with historical data to predict the main quality parameters of the solid nitrate fertilizer: nitrogen content, humidity and hardness.
After initial training, the tool was rolled out and implemented together with a fertilizer producer in a tk Uhde pugmill granulation plant. It predicts the main quality parameters almost instantaneously, based on live process data coming from the DCS, and thus works as an online AI soft sensor. If recent laboratory data are available, the AI tool is even capable of providing a forecast for the main product quality data for the upcoming two hours if the process conditions remain unchanged. Comparisons with laboratory test results show a high accuracy of the model in continuous operation of the plant. The offered insights regarding the expected product quality enable the operator to take measures to avoid off-spec material immediately without the delay of laboratory tests, thus maximising the yield of the production facilities.
All AI soft sensor data as well as the process data are visualised in web dashboards which are full customisable and can be adapted to the customer needs. They allow the process data and predictions to be queried and analysed at any point of time.
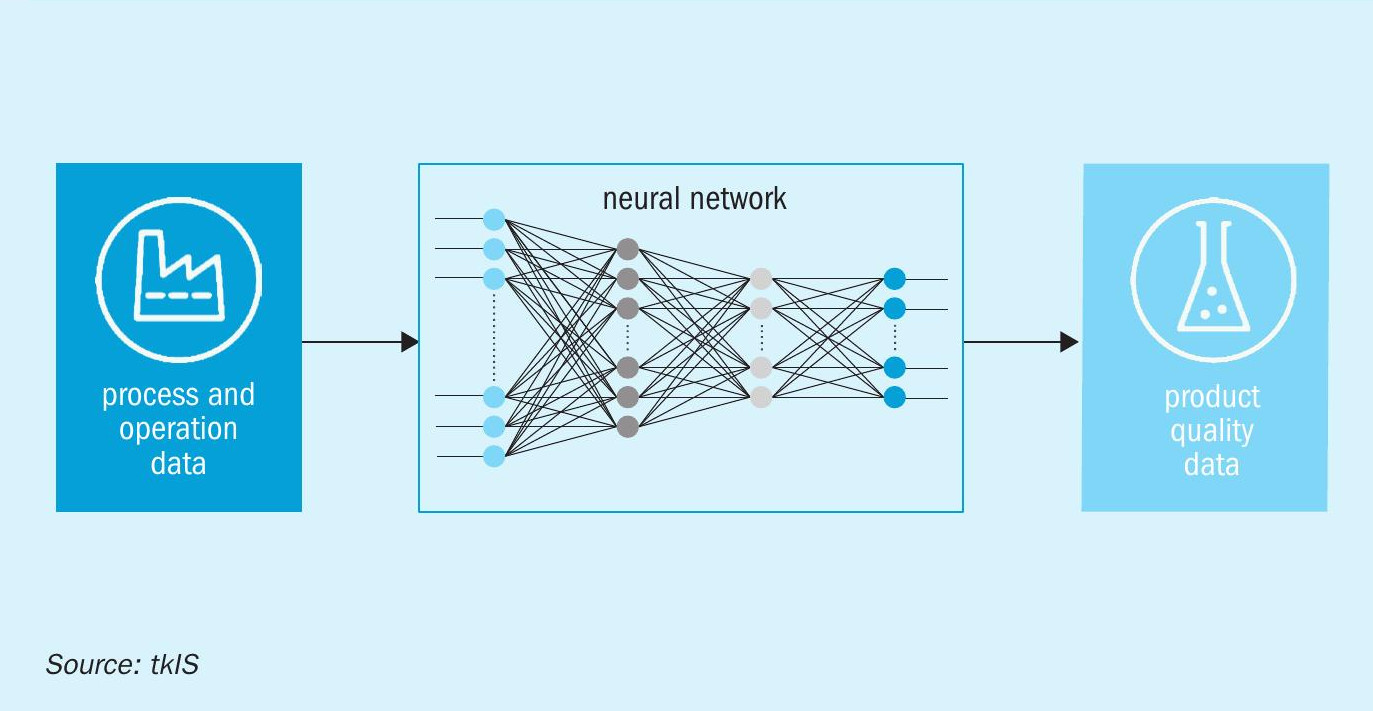
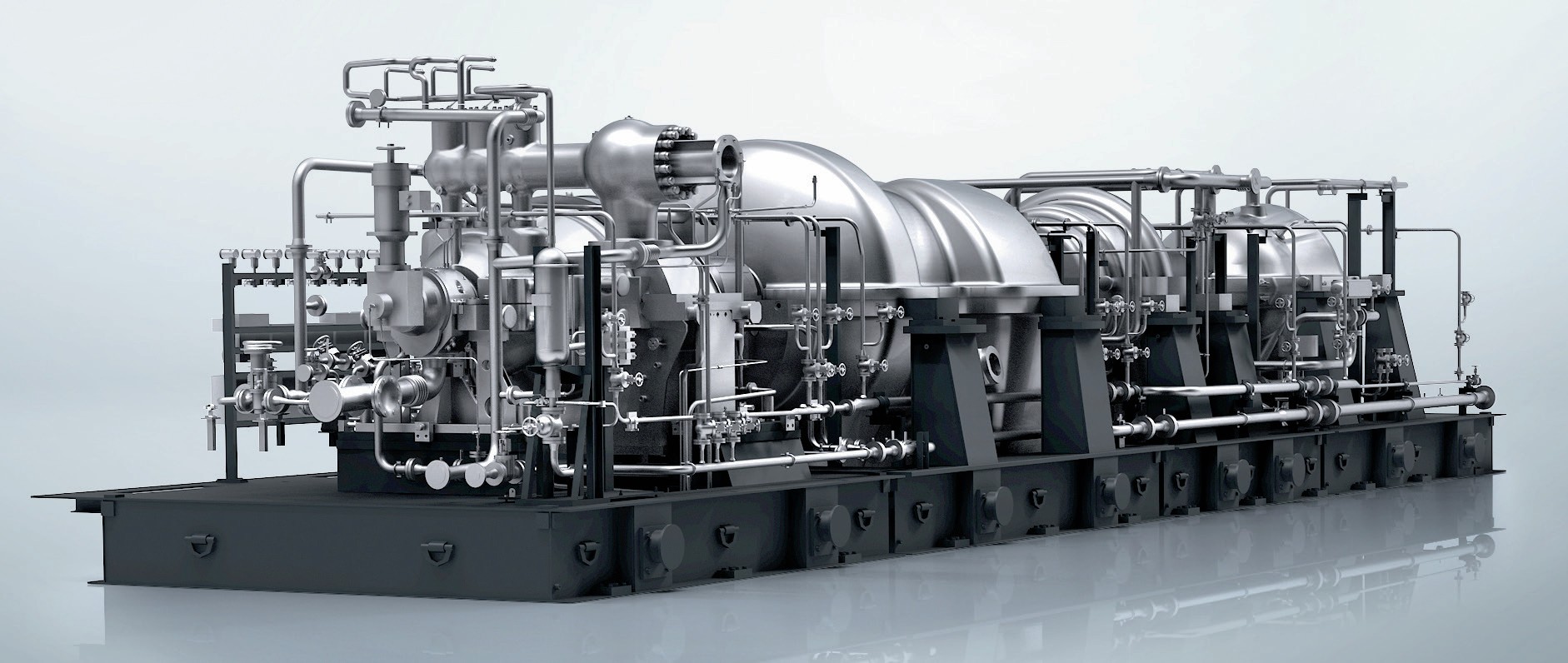
Co-operation with MAN Energy Solutions regarding nitric acid plants
In nitric acid plants, the compressor train is not only an exceptionally complex piece of equipment, it is also deeply integrated into the nitric acid process. Therefore, aiming at a higher degree of autonomy and optimised operating points of nitric acid plants, it is advantageous to optimise the compressor train controls and plant controls together.
Uhde has constructed nitric acid plants for almost a century, now. Today, Uhde is a global market leader in nitric acid technology, offering capacities of up to 2,000 t/d of nitric acid (100%). Since the 1950s, Uhde has built and commissioned more than 130 plants. MAN ES is a global market leader for nitric acid compressor trains (Fig. 4) equipping the majority of new-built nitric acid plants. MAN ES has proven its expertise in autonomous operation in the field of unmanned sub-sea turbocompressors. Moreover, during the pandemic, MAN ES has gained experience in remote commissioning. For these reasons, MAN ES and Uhde are perfect partners for the development of autonomy solutions for nitric acid compressors trains and plants.
A joint task force has been set up, which is currently combining rigorous physical relations and real-life data with AI methods and digital controllers. The task force consists of process and machinery experts as well as process simulation professionals and data scientists. thyssenkrupp Uhde and MAN Energy Solutions (MAN ES) have joined forces to use artificial intelligence to support plant operation, considering product price and resource costs, energy efficiency, maintenance aspects as well as process stability. The focus of the development is a higher degree of autonomous operation considering the above-mentioned goals for efficiency and stability.
Digital products for new fertilizer complex
tk Uhde provided various digital products to support the operation and maintenance of a new fertilizer complex just recently started up in the Middle East, i.e., an operator training simulator, remote performance monitoring including online dashboards and regular reports (Fig. 5) as well as digital twins for the various plants.
The digital twins are based on process models which are either based on a process simulation (white box digital twin) or on artificial neural networks (black box) which first must be trained and verified based on plant data.
Typically, white box digital twins are applied for Uhde’s proprietary technologies for which process simulations have already been used to design the plants. These process simulations will then be further enhanced by adding design parameters from the engineering phase like equipment and piping dimensions, pump and valve curves, etc.
Black box digital twins can also be applied for very complex systems in which not all relations are exactly known, e.g., for prediction of product parameters when producing solid particles (refer to quality prediction in CAN granulation).
The digital twins will be applied for testing of new process parameters to run “what if” analyses. They also offer anomaly detection to make the operators aware of any potential problems.
AI controller for aromatics extraction
In the following example one of the newest developments in plant digitalisation is described. Although it has been applied in aromatics extraction, an important petrochemical process, similar systems may also be used for fertilizer applications.
tk Uhde’s Morphylane technology is one of the leading aromatics extraction technologies in the world which can be used to produce high purity benzene and toluene from feedstocks like reformate, pyrolysis gasoline or coke-oven light oil.
To further enhance its performance, tk Uhde, TCCT and German refinery Holborn have jointly developed a digital twin which can be used to adjust relevant process parameters like the solvent flow rate and temperatures depending on the feed to this very complex system. The digital twin is based on an artificial neural network which has been trained and verified based on process data from the real production plant. Its machine learning algorithms continuously improve the model with time.
In a first phase, the digital twin has been operated in an open-loop arrangement for some time, offering guidance to the operators who still needed to adjust the set-points in the control system manually. Now, it is even possible to close the loop, i.e., the AI controller may automatically adjust the mentioned process parameters in the control system to optimise production. Manual operation is only required under very special circumstances, making this digital product a very powerful tool to increase profitability and help operators in their daily work.
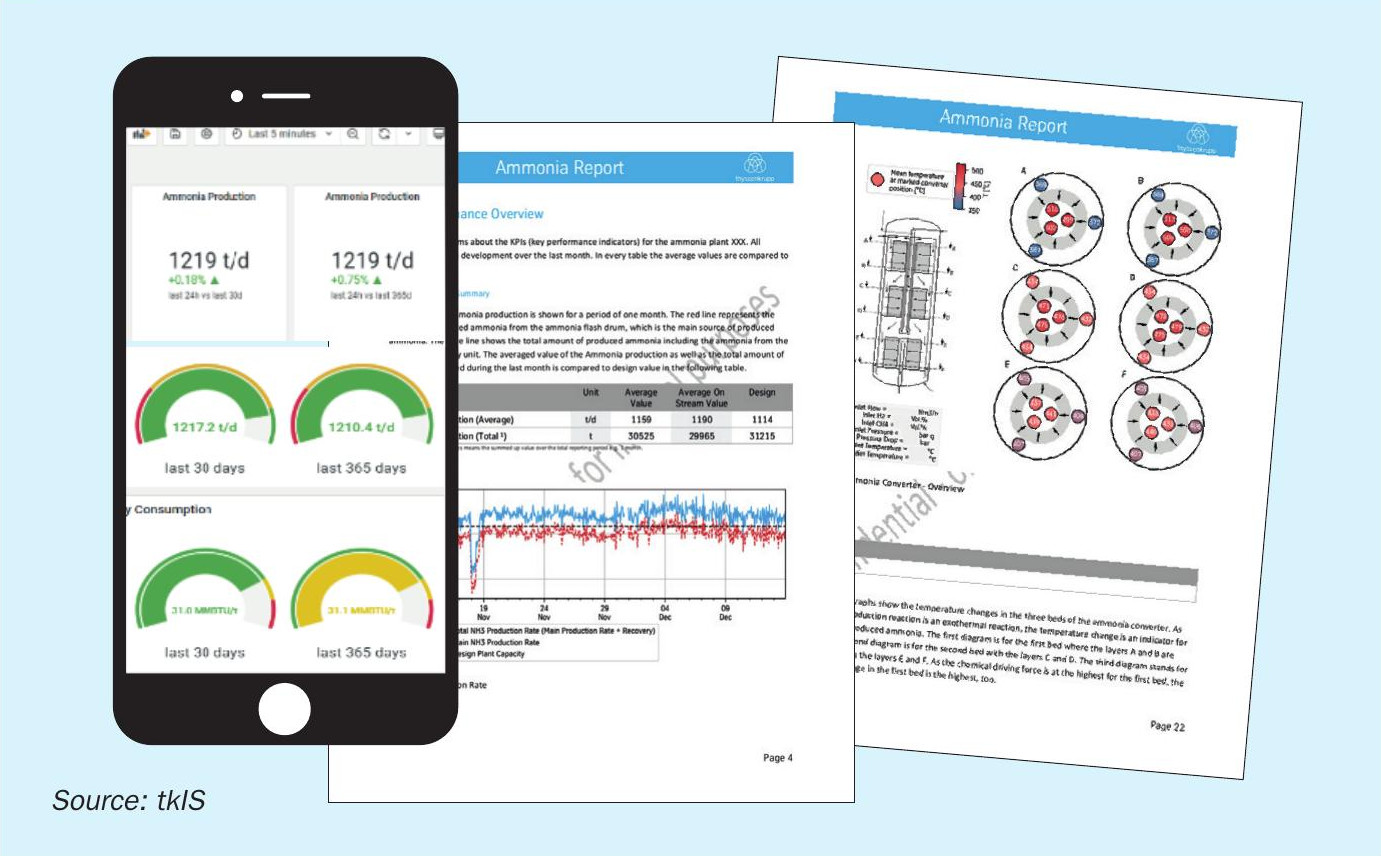
Conclusion
A wide range of digital products are available to maximise production, reduce raw material and energy consumption, and to effectively lower emissions. Digitalisation can also significantly improve plant availability and safety.
The level of digitalisation depends on the complexity of the process technology applied. Often, it is sufficient to focus on the most complex systems within a plant. However, due to the increased speed of modern computers and software, it is already possible to model complete plants as well.
Finally, the combination of state-of-theart simulation software often supported by machine learning techniques and domain expertise avoids frustration during the execution of digitalisation projects. With the help of process technology experts, the development and application of digital products becomes much more efficient. n
Reference