Sulphur 408 Sept-Oct 2023
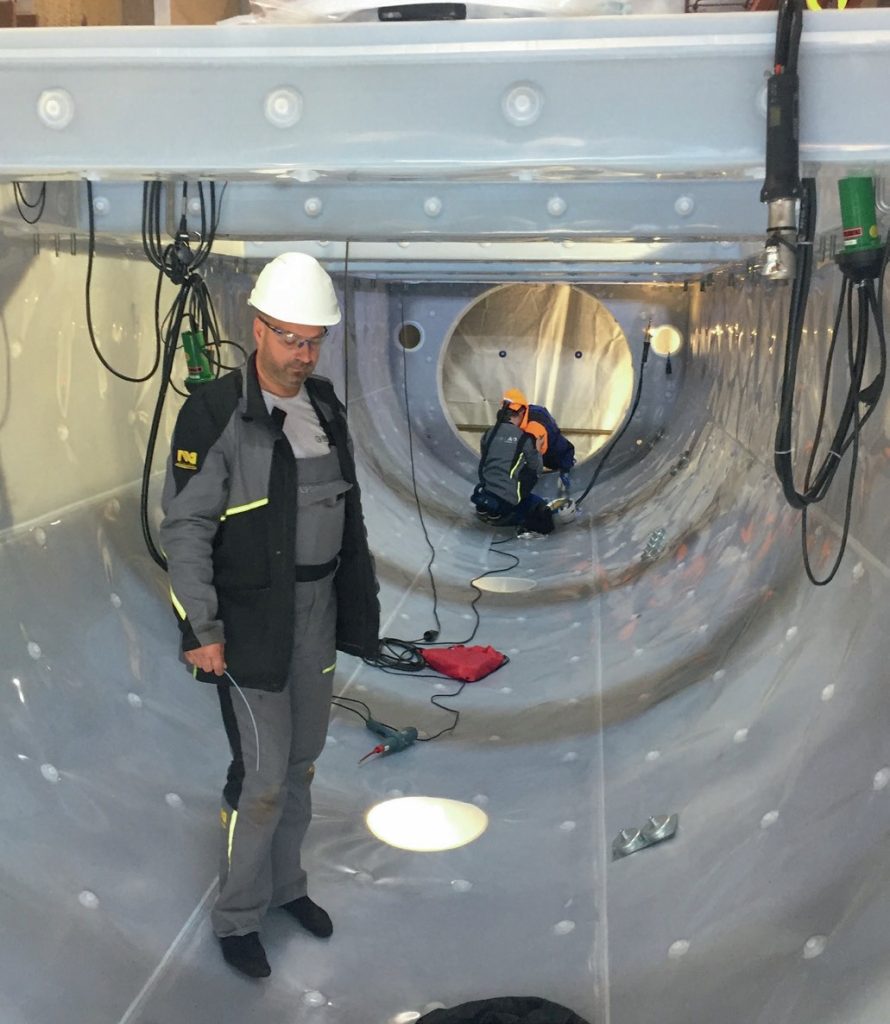
30 September 2023
Protecting your assets with PFA
SULPHURIC ACID PRODUCTION
Protecting your assets with PFA
In this case study Johannes Derfler of AGRU Kunststofftechnik reports on how a new condenser design, engineered by OMV and INWA AG using PFA sheets from AGRU, was implemented at OMV refinery in Austria to address maintenance problems due to corrosion of the wet sulphuric acid (WSA) condensers and the follow-up units. As a result of the renovation, maintenance costs have been cut in half, while both maintenance intervals and overall operational safety has increased.
OMV, the largest industrial company in Austria refines fuel products and petrochemicals at its site in Schwechat Austria. In the refining process, crude oil and natural gas are processed into high-quality fuels, oils and other special products such as paraffin, heating oil, bitumen, sulphur and sulphuric acid.
The aim of all these processing steps is to achieve a high added value product from the raw material, to work economically as a company, all while operating to sustainably protect dwindling resources and the environment. In the end, all the residual products from the processes are fed into a combined heat power plant to produce steam, electricity, district heating and other products through combustion energy. A downstream flue gas cleaning system (SNOx) cleans the flue gases and allows the burning of high-sulphur fuels in the power plant. Due to the high sulphur content in the fuels, SO2 is produced during combustion which is then used for the production of concentrated sulphuric acid. Sulphuric acid is the most commonly used acid in the world, and there is a global interest in this product as it is essential for a variety of applications. As a result, a contaminated flue gas is turned into clean exhaust air and a saleable industrial product.
In the first step of the flue gas cleaning system, dust is filtered via electrostatic precipitators. Afterwards the NOx is removed in a catalytic process in a second step. The remaining SO2 gases are then oxidised via converters to SO3 . In the last step of the converters, the majority of the SO3 reacts with H2 O to form H2 SO4 vapour. The vapour is transported to the heat exchanger, in which the gaseous sulphuric acid is condensed to liquid H2 SO4 with a concentration >94%. The condensing droplets of sulphuric acid are formed on the surfaces of the heat exchangers (acid condenser) and the surrounding equipment.
The dew point of the flue gases depends on its composition and is typically reached if the gas temperature drops below approximately 250°C. The condensation of acid droplets on metal surfaces leads to so-called “dew point” corrosion, in which regular steels and stainless steels are rapidly destroyed. In order to achieve sufficient resistance to the highly aggressive application conditions, a multilayer structure is often used, consisting of the following materials: a chemical stone lining, a foam glass layer, non-welded PTFE plates, a chemical protection layer and a carbon steel tank.
This lining system was also used at OMV. However, due to the significant increase of maintenance work over the years, the associated operational downtimes and repair costs that occurred, the economic efficiency of the SNOx plant decreased considerably over time. It was apparent that the multilayer structure did not create a long-term leak-proof lining system. This resulted in corrosion of the carbon steel tank by the condensing sulphuric acid. To ensure safe operation it was necessary to remove the lining system, which was already soaked with acid, and to refurbish the steel structure before applying a new corrosion protection lining system.
Due to the apparent downtimes and the increasing repair costs OMV decided to fundamentally redesign the condenser area. The design objectives were defined as follows:
- production capacity and product quality at least equal to the current system;
- increased reliability, availability and safety;
- extension of maintenance intervals;
- lower maintenance costs due to easier repair.
In the course of the design work, detailed solutions were worked out, that made it possible to shut off certain parts of the SNOx plant, so that the plant could be operated under partial load during its maintenance. In addition, a two-layer structure already patented by OMV was developed, to allow the process to be permanently checked for leaks via a monitoring system. However, the focus of the development was the selection of a lining system that would withstand the harsh operating conditions and meet the specified project objectives. In the selection process, eight different lining systems were evaluated and analysed. Due to experience in the field of PFA linings for sulphuric acid condensers INWA AG was able to provide long-term references demonstrating the functionality of this lining system in similar applications. In addition, AGRU placed an order with a Swedish testing institute to expose AGRU PFA sheets for one year at temperatures and concentrations that exceeded the operation conditions. The results clearly showed that no significant changes to the product properties occurred at 260°C and 98% sulphuric acid after one year. Based on the available long-term references and the investigation carried out, the PFA fixed point lining system was specified as the optimal lining system by OMV. INWA AG was awarded the contract to start with the refurbishment of the first of four plant sections in 2018. Fig. 1 shows the new tank design, which consists of a double layered steel tank, both layers lined with PFA.
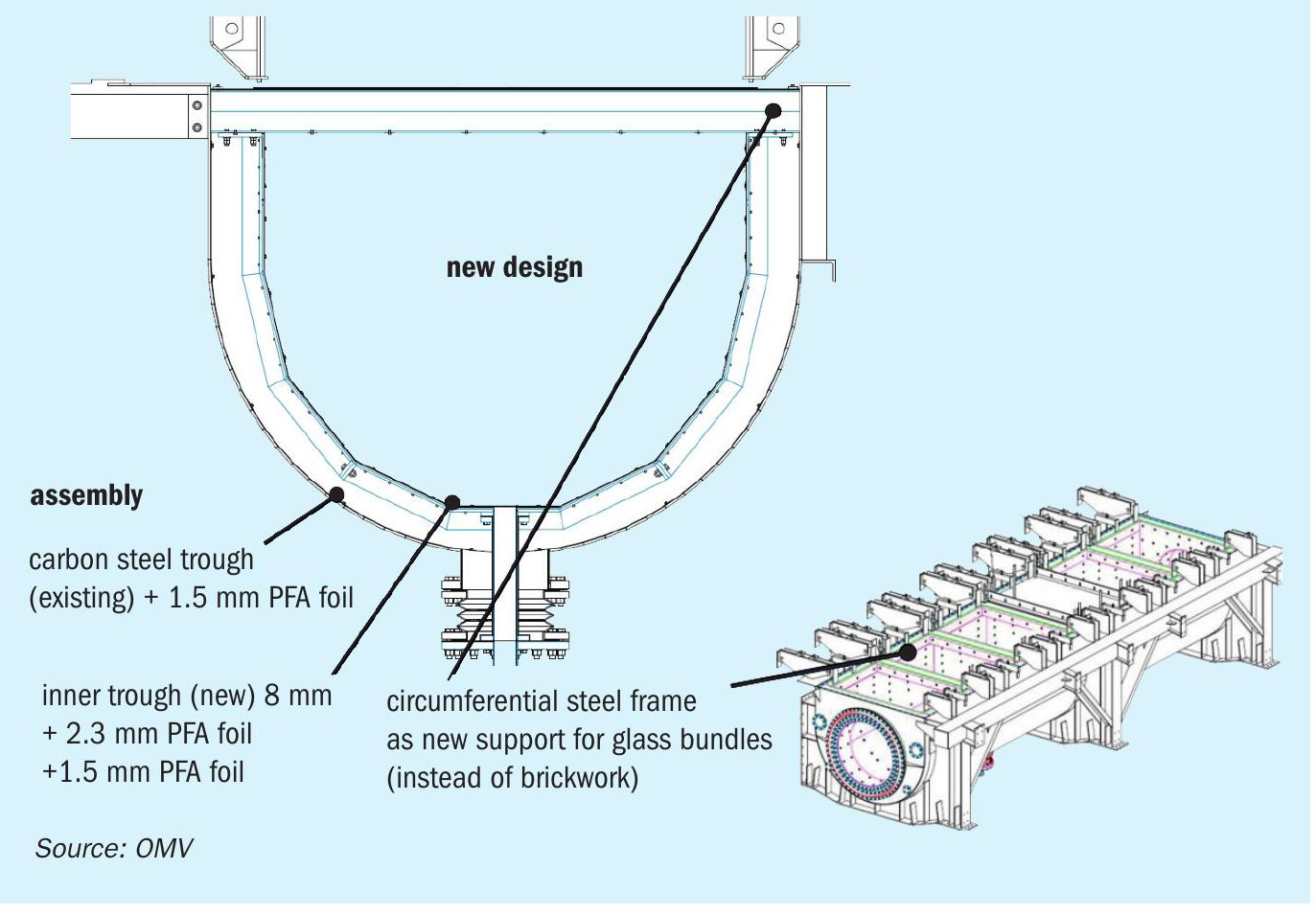
Compared to the old design, the chemical protection layer now consists of two PFA sheets located on top of each other, whereby the PFA sheet at the bottom was simply installed for additional operational safety. The steel tank at the bottom, which is not in contact with the medium during normal operation, was also lined with a PFA sheet in order to provide comprehensive corrosion protection even in the event of leakages.
PFA fixed point lining
With the PFA fixed point lining, a PFA sheet is fixed to a steel structure by a mechanical fastening using bolts or screws. This system is mainly used in flue gas applications and desulphurisation plants up to 260°C (see Fig. 2).
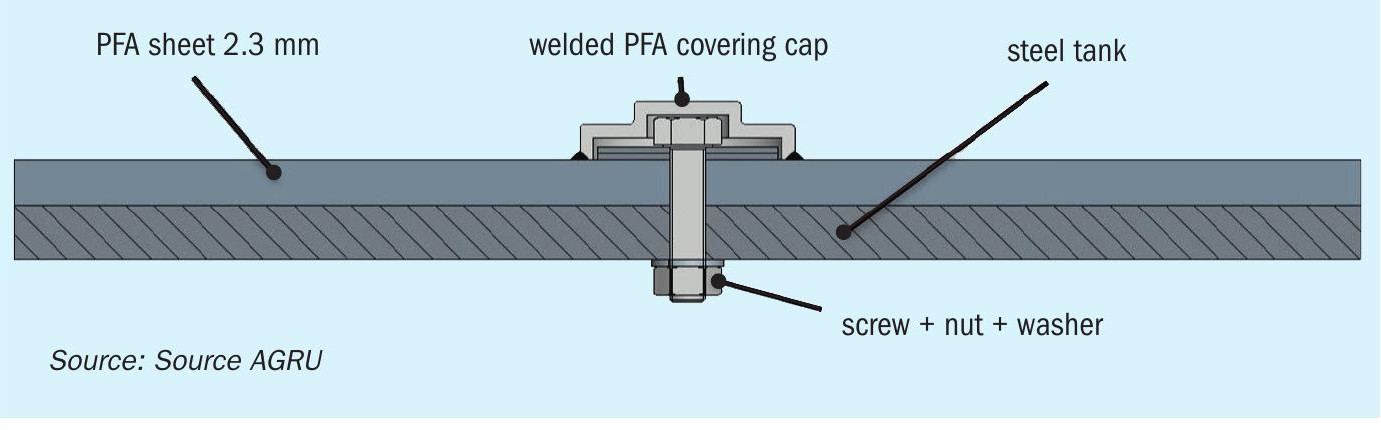
Between 2018 and 2022 all four condensers were relined using this patented lining concept. Since the PFA products are used under very aggressive operation conditions, the PFA production was inspected and controlled by INWA AG and OMV through regular audits. As a system supplier, AGRU was able to produce all the required PFA products, thus making an important contribution to the realisation of this project.
Fig. 3 shows the installation and welding work of the AGRU PFA sheets in the sump area and Fig. 4 shows the final lined condenser, before being placed into operation.
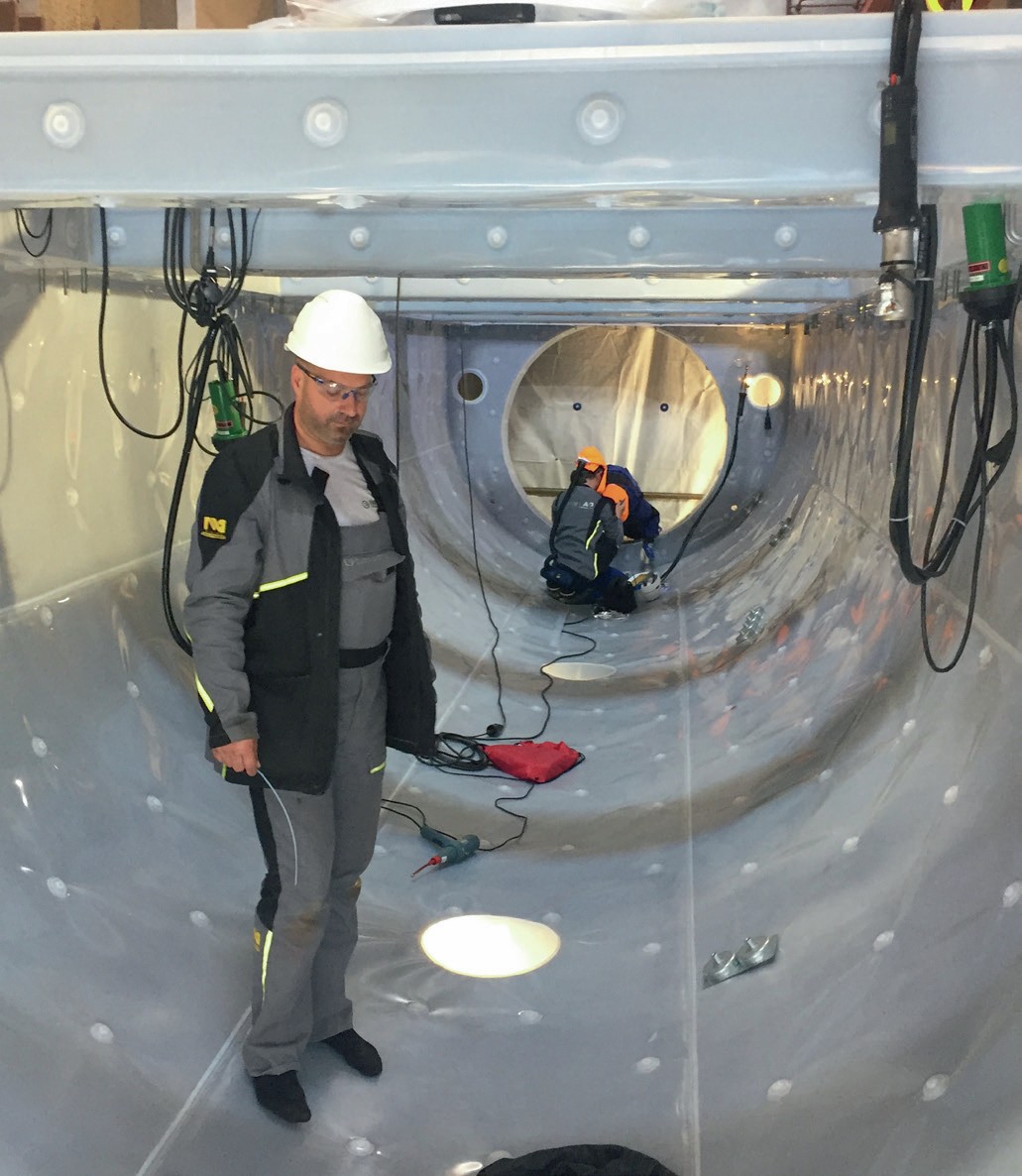
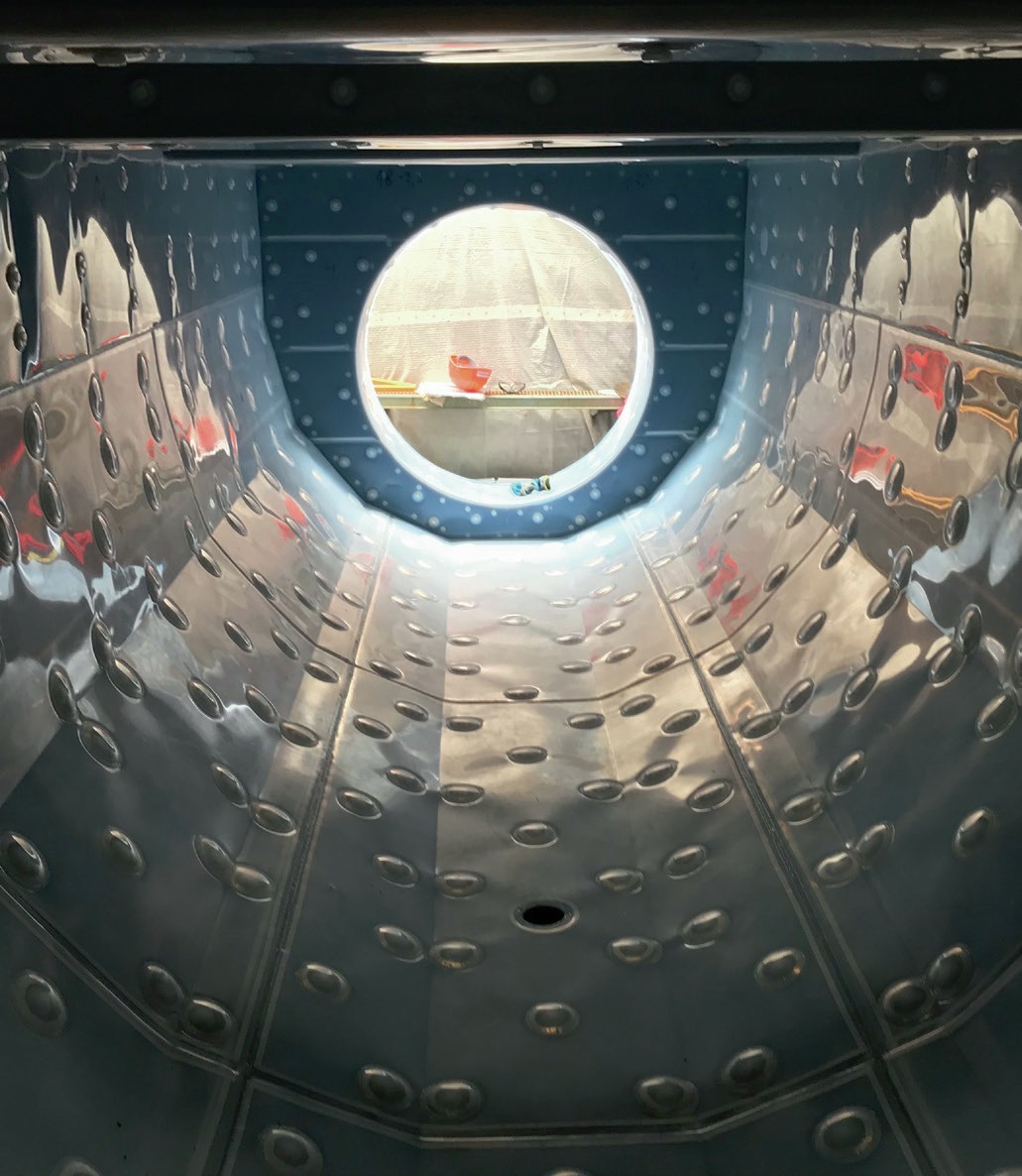
Flue gas ducts
The flue gases cleaned by the condensers are then collected in the clean gas ducts so that they can leave the plant via the chimney system, see Fig. 5. In the old design, the clean gas ducts were made from steel components with a thin polymeric coating for chemical resistance. Due to the low thickness and the large number of flange joints required for this type of installation, many corrosion problems and leaks were present, see Fig. 6. As a result, it was decided to completely replace the pipes using a combination of PFA FRP dual-laminate pipes and a PFA fixed point lining.
FRP dual-laminate construction
By using the FRP dual-laminate construction the chemical resistance of the PFA material is combined with the mechanical strength of the FRP reinforced plastic. A fabric backing system in the polymer lining is used to provide a bonding between both materials, see Fig. 7. The refurbishment of the clean gas ducts was conducted in 2022. An overview of the new plant components and linings is shown in Fig. 8.
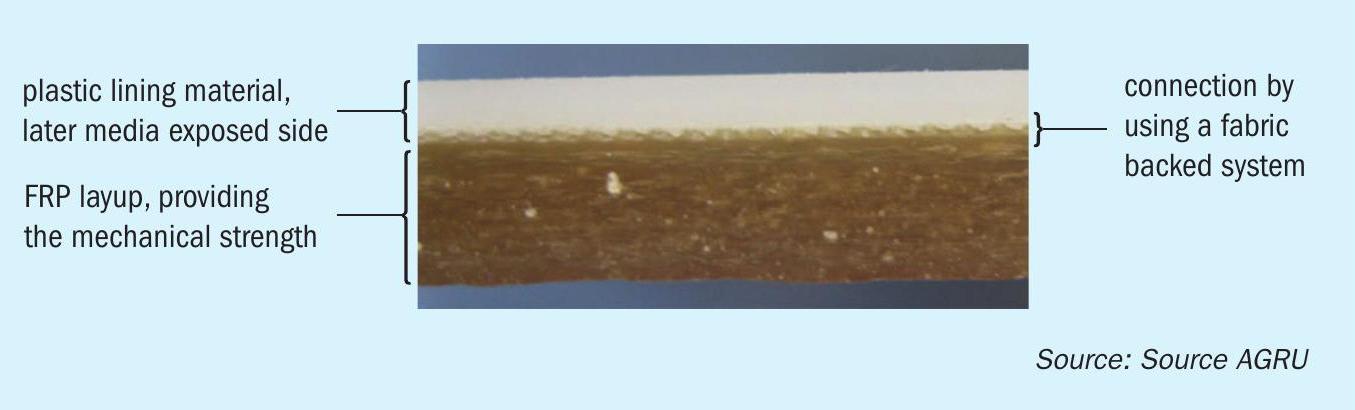
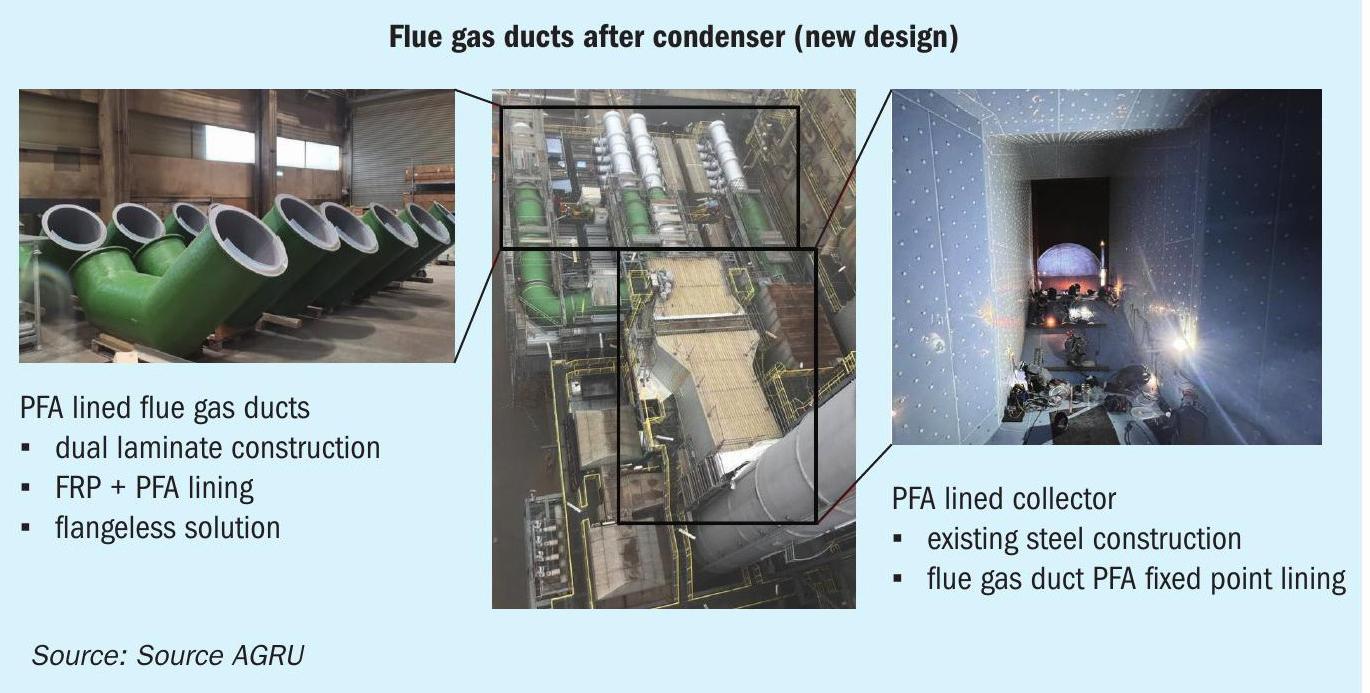
Conclusion
In the course of a routine inspection carried out in 2022 no damage or abnormalities were detected on the PFA condenser lining installed in 2018. Mr Ronald Hoffer, the person responsible for this project for OMV concluded after inspection of the plant area: “Despite the highly aggressive application conditions, the PFA lining shows no noteworthy damage or changes after an operating period of three years. It seems that sheets have just been installed”.
Thanks to the successful development and the completed reconstruction, OMV and INWA AG were able to apply for a patent for this double layer lining system. In addition, the specified project goals were achieved:
- increase in reliability, availability and safety;
- 50% reduction in maintenance costs;
- 75% reduction of downtimes;
- patented leakage monitoring system enables permanent control of the plant components;
- increased operational safety due to installation of an additional tight lining system.