Sulphur 408 Sept-Oct 2023
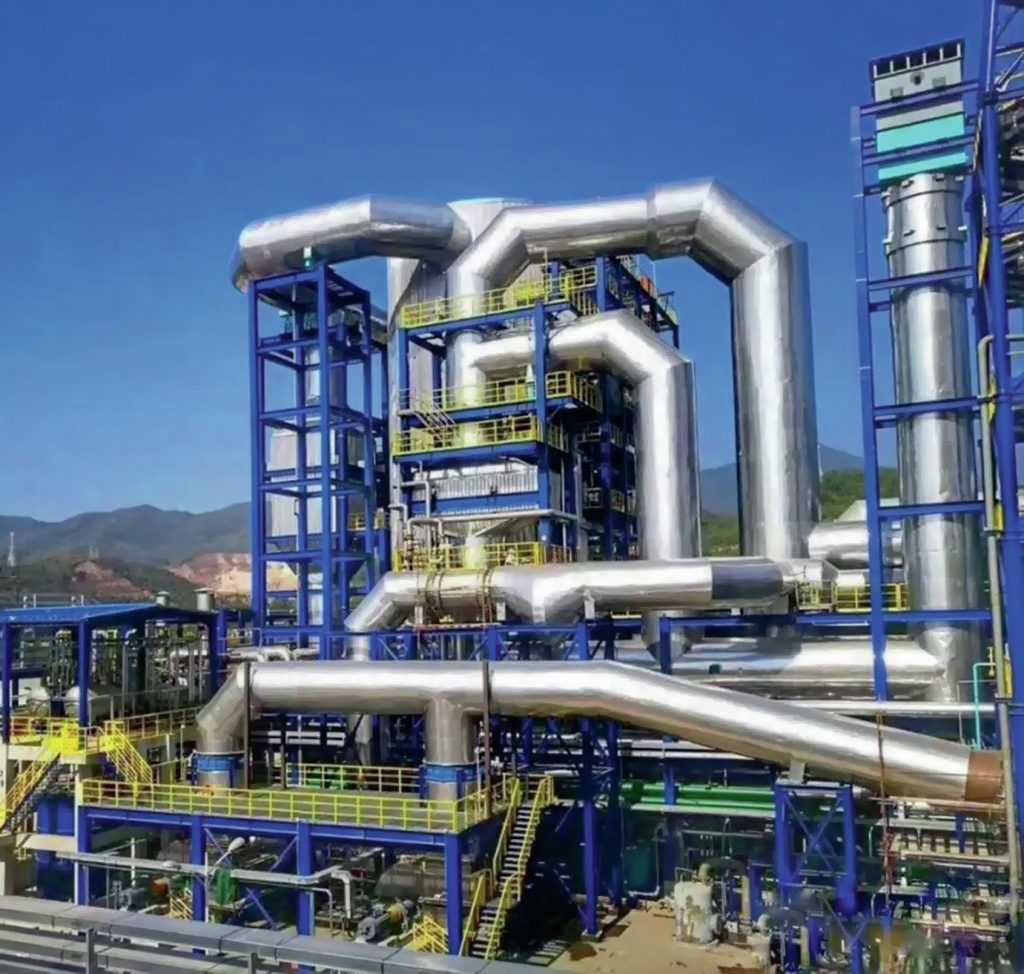
30 September 2023
Sulphuric acid recycling
SULPHURIC ACID
Sulphuric acid recycling
As producers and regulators become increasingly concerned about the ‘circular economy’, there is increasing focus on regenerating waste sulphuric acid for re-use.
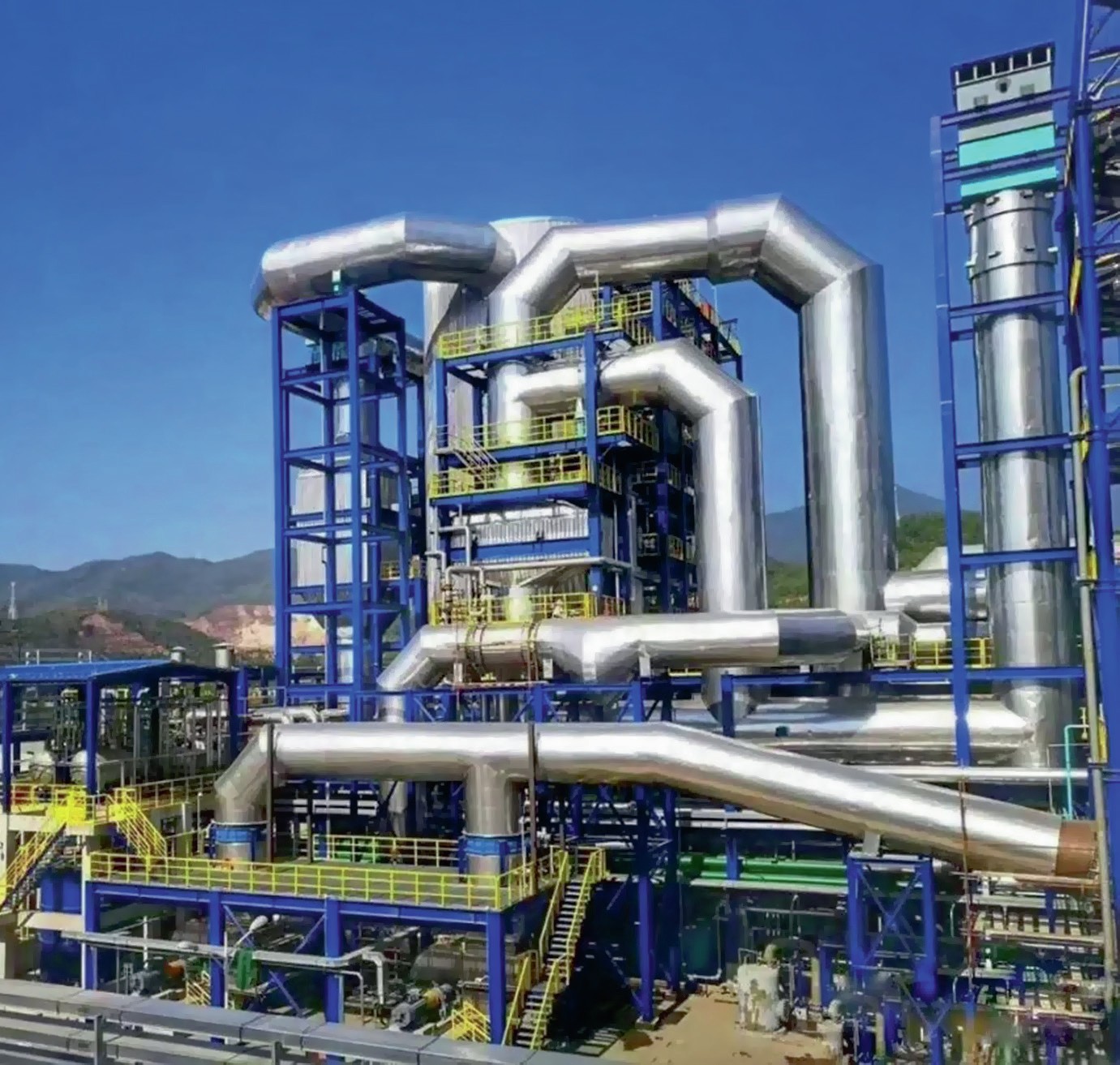
Environmental concerns are driving attempts to recycle and reduce consumption of raw materials, leading to the concept of the ‘circular’ economy, where materials are recycled and reused in a continuous loop. For sulphuric acid, this takes the form of regeneration or recycling of acid or acid-containing waste streams which have already been used in an industrial process.
Alkylation
One of the major sources of spent acid is refinery alkylation units. Alkylation converts light olefins into a high-quality gasoline blendstock by reacting them with isobutane. The most common is C4 alkylate, made by alkylating butylene with isobutane. However, alkylate can also be made from propylene and isobutane, or pentene and isobutane. It is particularly desirable because of its combination of properties; zero sulphur content, no aromatic content, low vapour pressure and high octane number, and is used as a blendstock in the manufacture of cleaner burning, premium quality gasoline.
It has been a mainstay of US refineries for some time, particularly since alternative octane improvers like MTBE have been significantly restricted since the 1990s, the increasing mandate of ethanol from corn has required alkylate as a balancing component, and higher-octane gasolines have been required to meet Corporate Average Fuel Economy (CAFE) standards. In the US 90% of refiners operate alkylate units, and alkylate now represents around 15% of the US gasoline pool. But while US alkylate capacity has been relatively stable over the past decade, use of alkylate as a blendstock has slowly but steadily continued to spread elsewhere around the world, particularly in Asia.
Acid is used to catalyse the alkylation reaction, and the two main ones used are sulphuric and hydrofluoric (HF) acid. Installation and operating costs are similar for sulphuric and hydrofluoric acid alkylation. Sulphuric acid is cheaper than HF but is more complex to regenerate and has higher usage rates. In the early days of the processes sulphuric acid was preferred, but during the 1980s and 90s, HF gained predominance, and by the turn of the century there was roughly a 50-50 split between their installations. However, sulphuric acid has gradually gained prominent due to concerns over the use of hydrofluoric acid. In particular, an explosion and fire at the Philadelphia Energy Solutions (PES) refinery in Philadelphia in 2019 led the US Chemical Safety Board (CSB) to call upon the Environmental Protection Agency (EPA) to review its regulation of HF in alkylation and other applications and look for substitutes. As yet no formal rulemaking has emerged on the subject, but there have been several conversions from HF to sulphuric acid or other systems, and the split between sulphuric acid and hydrofluoric acid alkylation systems is currently about 60-40.
One of the factors that favours sulphuric acid is ready access to sulphur or sulphur-containing off-gases at refineries from the sulphur recovery section. Various sulphuric acid technologies are available for dealing with SO2 from Claus plants, such as Topsoe’s Wet gas Sulphuric Acid (WSA) process.
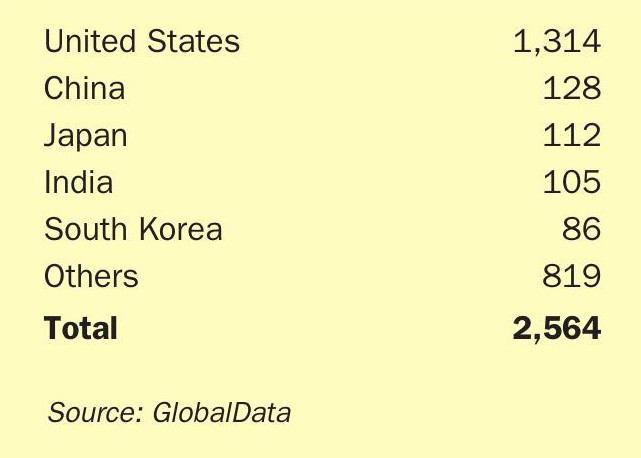
Capacity
Total US alkylate capacity is just over 1.3 million bbl/d, according to the Energy Information Association, just over half of it in the PADD 3 region (US Gulf Coast). This has been relatively stable over the past five years, but over the same period capacity outside the US has risen to almost the same amount; 1.3 million bbl/d (see Table 1), with installations at, e.g. Reliance’s refinery in Jamnagar where an 83,000 bbl/d unit – one of the largest in the world – now operates. Chinese capacity now represents about 128,000 bbl/d of this, with a number of alkylation sections added to refineries over the past decade to help meet China-VI (<10ppm sulphur content) gasoline standards. Elessent alone says that it has completed seven installations of its STRATCO technology at Chinese refineries.
Between 2022 and 2026 another 39 refineries have started up or are expected to start up alkylation units, including at Vadinar in India, with 32,000 bbl/d of capacity, Al Zour in Kuwait, as well as refineries in Mexico, Brunei and Nigeria, for a total of 200,000 bbl/d of capacity. About 70% of this will be in China and India, much of it expansions at existing refineries, taking global alkylation capacity to 2.8 million bbl/d, or about 120 million t/a of capacity.
Looking to the longer term, OPEC forecasts a steady (ca 2% year on year) increase in global alkylation capacity out to 2035 to deal with ever more stringent fuel quality standards.
Spent acid
While HF functions almost as a ‘pure’ catalyst, for the sulphuric acid alkylation route there is a fractional conversion of acid, and hence ‘consumption’ is relatively high; around 10-12 kg of acid per barrel of alkylate produced at best, and potentially as high as 15-25 kg/ bbl alkylate if the cracker is being run at high severity. Not all of this is pure consumption; acid concentrations must be kept high (>90%) in order to prevent acid ‘runaway’, where catalytic activity rapidly declines and polymerisation is enhanced, and so the acid must be continually topped up with fresh acid and spent acid removed from the system. Spent acid often has a lower concentration than a clean project and so cannot be reused until it is cleaned and concentrated again.
Dealing with this acid can be done either on-site or off-site, by a contractor. The latter is typically used for refineries that have moderate to low alkylation capacity, and the benefits are primarily reliability and an economically viable solution for SAR that helps reduce a company’s environmental footprint. To achieve scale, such merchant facilities typically handle acid from a number of customers, and may also handle chemical spent acid from an electronics plant etc.
With the onsite model, a refiner can either build its own facility, or engage a third party to design, build, own and operate the facility for them. In this case, the third party can provide key sulphur management services for the refinery by processing all of its spent acid, along with all or some of its sulphur-bearing gases. This is a good option for large scale consumers of acid and can dovetail neatly with an on-site acid plant handling Claus plant gases as described above, offering more certainty about availability as well as a reduced environmental footprint, transportation and loading/unloading costs. An onsite plant can also deliver high-pressure steam back to the refinery for its use in production.
Regeneration
The regeneration process is essentially an oxidation reaction. Feed acid coming into the regeneration plant is concentrated to remove any water. This reduces the total volume of the spent stream before it enters the regeneration furnace where it undergoes thermal cracking. Spent acid is atomised and sprayed into a large furnace heated to around 1000-1200°C, where it decomposes into SO2 , water and oxygen. The fuel/air mix is controlled to maximise the yield of SO2 , with the fuel feed either natural gas or, at a refinery, potentially off-gases from refinery process streams or fuel oil. The hot combustion gases are then cooled in a high-pressure boiler or radiant heat exchanger, which recovers heat for the conversion section of the plant. The gas stream then passes to a gas cleaning section to remove any ash or solid impurities such as metals or organics from the gas, and reduce the water vapour content to the desired acid concentration. The SO2 bearing gas is then dried by contact with weak (93-96%) sulphuric acid in a packed bed acid tower or drying tower, and passes to a contact vessel, where it reacts with a catalyst, typically vanadium pentoxide, to form SO3 . The SO3 is dissolved in 100% sulphuric acid and added to water to produce pure sulphuric acid at the desired concentration, from 93-99%.
“Between 2022 and 2026 another 39 refineries have started up or are expected to start up alkylation units, including at Vadinar in India with 32,000 bbl/d of capacity
Other sources
As well as refinery alkylation, many chemical processes generate spent sulphuric acid, including electronics manufacture, pigments and dyestuffs, old car batteries and many more. Historically these have sometimes been merely diluted and discharged into water courses, leading to environmental pollution, and regulations continue to tighten on the disposal of sulphuric acid. For small scale producers, neutralisation with calcium carbonate or the like is a possibility, though this generates tailings that must also be disposed of. But for sites generating more than 2,000 t/a, regeneration becomes an option. As demand for sulphuric acid continues to increase, coupled with increasingly strict SOx emissions regulations and a growing corporate and regulatory focus on reducing environmental footprint, the use of spent acid regeneration is likely to continue to increase.