Fertilizer International 517 Nov-Dec 2023
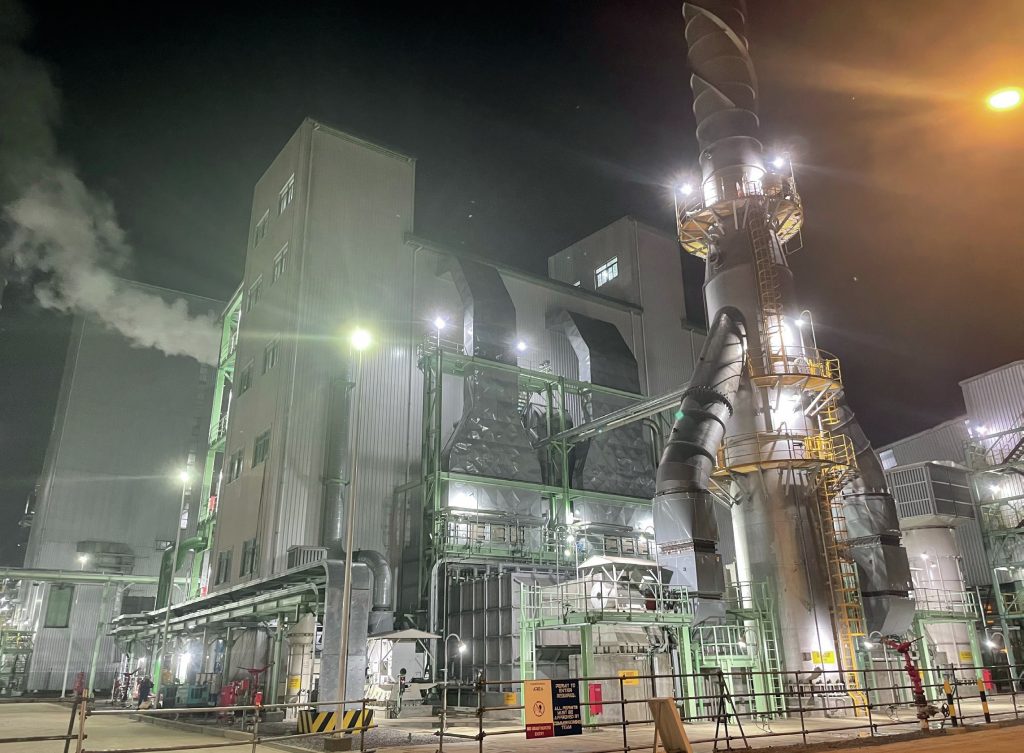
30 November 2023
Casale granulation – revolutionising finishing technology
FERTILIZER FINISHING
Casale granulation – revolutionising finishing technology
With the addition of Green Granulation technology (GGT), Casale is the only industry licensor able to provide customers with an entire nitrogen fertilizer complex. Ken Monstrey and Matteo Fumagalli of Casale outline the benefits of this technology and its revolutionary new elements.
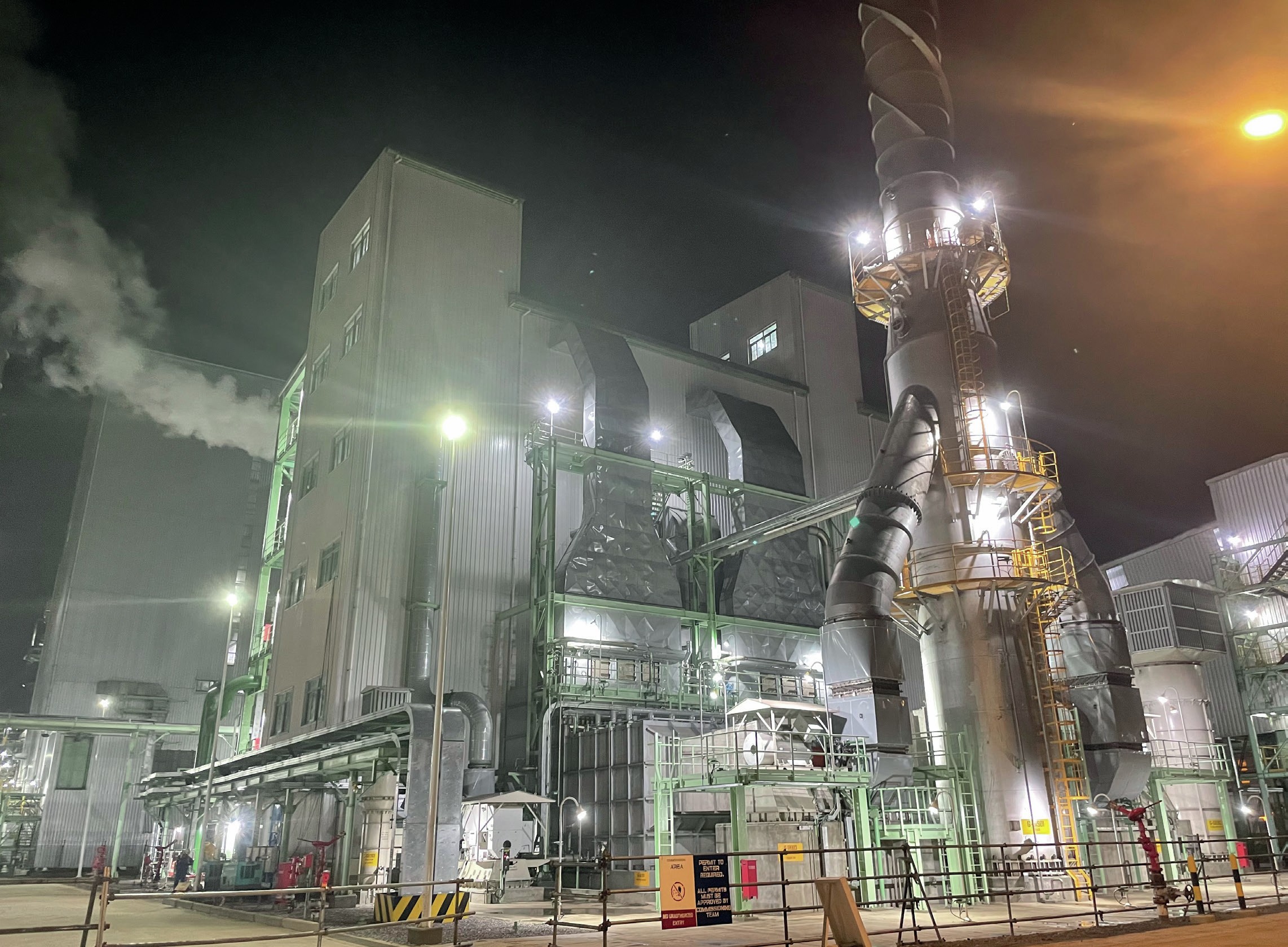
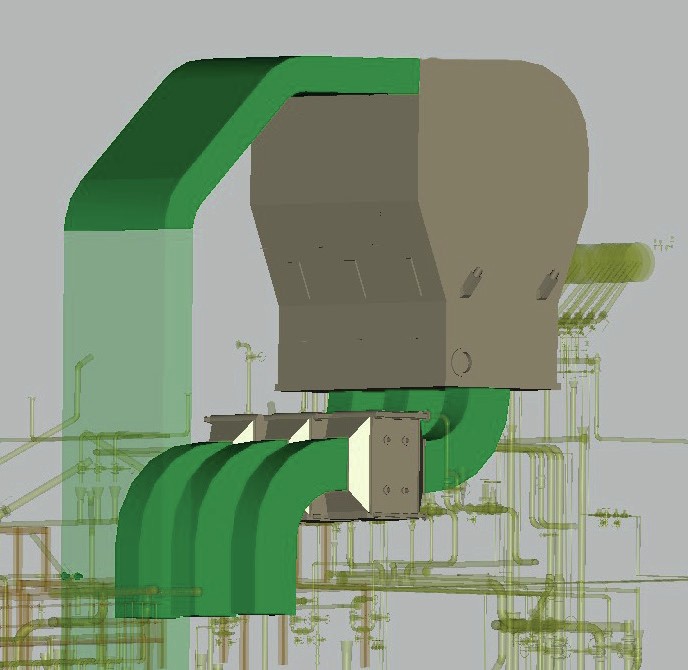
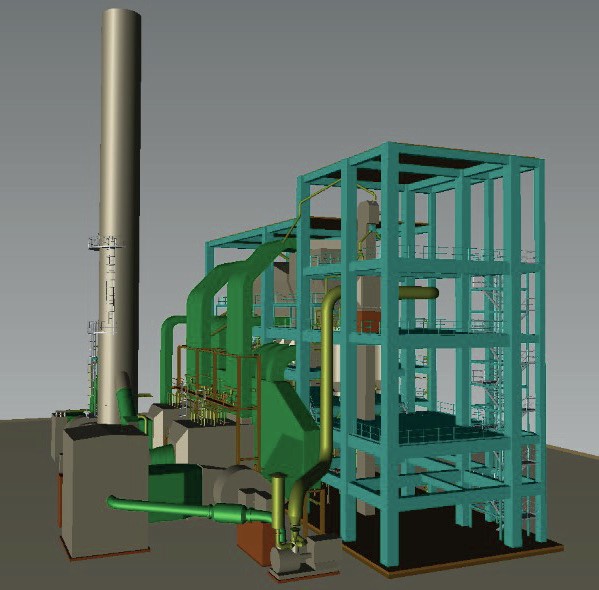
Casale’s technologies cover the entire value chain for nitrogen fertilizers – from syngas through to NPKs – including ammonia, urea, nitric acid and ammonium nitrate production. The range of services provided by the company include the revamping of existing fertilizer plants as well as the design and construction of new fertilizer complexes.
Casale successfully acquired Green Granulation Ltd in 2022 to strengthen and broaden its nitrogen technology portfolio. The newly purchased company, now part of Casale Ltd, is the licensor of granulation technology for urea, ammonium nitrate (AN), calcium ammonium nitrate (CAN) and urea ammonium sulfate (UAS) production. Historically, it has been more active in the Chinese market.
With the addition of GGT technology, Casale is the only industry licensor able to provide customers with an entire nitrogen fertilizer complex – covering every process step from gas treatment all the way through to solid finishing.
The recent award of a front-end engineering design (FEED) contract for a new 1,800 t/d capacity urea granulation complex in Uzbekistan provided the opportunity to combine the technologies of Casale’s holding and subsidiary companies for the first time. This project is scheduled to be completed in the first half of 2025.
Casale Green Granulation process
Since its establishment, Casale has developed and incorporated revolutionary new elements within the overall fluidised bed process used to produce nitrogen-based fertilizer granules. The company has embedded proprietary innovations such as Optimised Fluid Bed Dynamics and Double Temperature Scrubbing within Cold Recycle Urea Granulation (CRG) technology. These developments have provided the business with a technological edge over its competitors.
Casale offers the most advanced fluidised bed technology currently available and, thanks to its unique plant design with a horizontal layout, offers both lower construction costs and higher efficiency. Additionally, the inclusion of CRG technology provides customers with tangible operational, economic and environmental benefits, such as:
- Lower total investment costs
- Lower power consumption
- Simplified operations
- Greater operational flexibility.
The Casale Green Granulation process (Figure 1) proceeds as follows:
- The fluid bed urea granulation plant receives concentrated solution from the evaporation section of the upstream synthesis plant.
- This solution is sprayed inside the granulator where it is transformed from liquid into solid granules of the desired size and quality.
- The fluid bed process produces granules by spraying this solution onto seed particles which are kept in a fluidised state.
- The seeds grow by continuous evaporation, crystallisation and solidification.
- The spraying system, by producing a large number of very fine droplets, guarantees a highly homogeneous granule structure.
- After cooling, the end product is sent to a bulk storage and/or bagging section.
In urea production, the Casale Green Granulation plant uses a feed of melt urea solution with a concentration of 96-97 percent (urea + biuret). The ammonium nitrate (AN) process, in contrast, introduces the AN melt to the granulation section at a concentration of 97.5-98 percent.
Optimised Fluid Bed Dynamics
A crucial factor in producing superior quality granules – whether these are urea, AN, calcium ammonium nitrate (CAN) or any other fertilizer or non-fertilizer granules – is achieving adequate particle movement within the fluidised bed layer. This is needed to create a continuous stream of fresh particles and direct these towards the different spray zones within the granulator, as well as ensuring water in the melt feed is evenly distributed and can evaporate.
The Green Granulation process incorporates Optimised Fluid Bed Dynamics (OFBD) technology. By combining a low operating fluidised bed level with a rolling movement inside the bed, OFBD ensures a constant and predictable feed of seed particles to the different spray zones. This has major technical advantages.
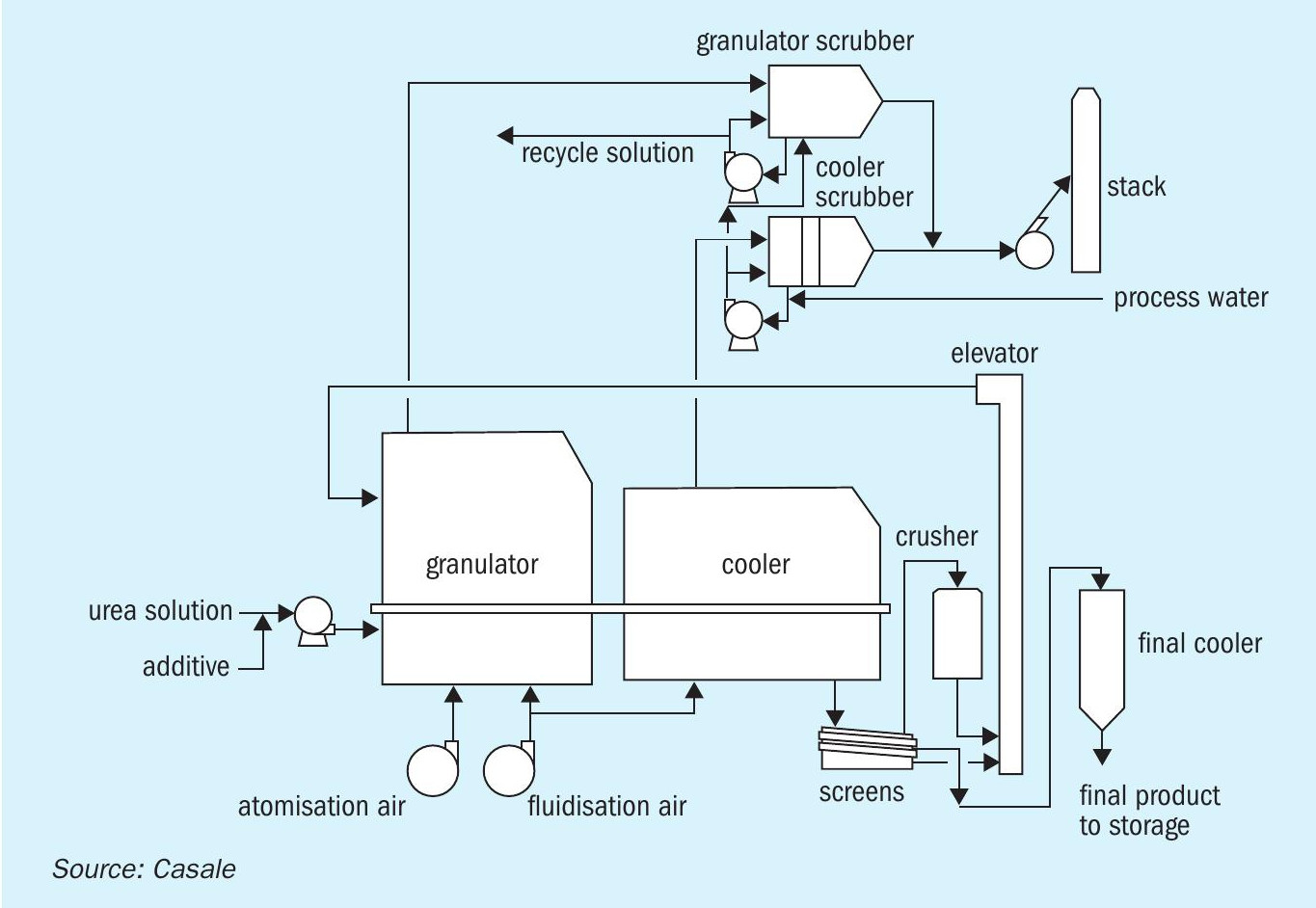
The low bed level, for example, reduces power consumption because it allows the fluidised bed to operate with a low pressure drop across the entire system. The rolling movement in between the consecutive sprayer banks also ensures a more predictable particle movement compared to a traditional ‘bubbling bed’ system.
“Casale offers the most advanced fluidised bed technology currently available and offers both lower construction costs and higher efficiency
Casale Green Granulation plants therefore benefit from the operational advantages of OFBD. These ensure sufficient particle movement occurs within the bed while avoiding the large pressure drop found in traditional high level bubbling beds. This enhanced performance contrasts with the high power consumption of traditional fluidised bed systems caused by the large pressure drop created by their high bed level.
Another crucial aspect of OFBD technology is the liquid sprayers used. These hydraulic sprayers were developed in-house and produce a homogenous spray of fine, uniform droplets in the spray zones. This spray penetrates deeply into the fluidised bed layer, assisted by a stream of atomised air, without generating too much dust.
Within fluidised beds, for every granule that leaves the system, a replacement ‘seed’ granule is required to restart the granulation process. Traditionally, these seeds are generated by crushing oversize granules (or on-size product) to feed the granulator. Crushers need to supply a constant stream of seed material – the exact amount determined by the recycle ratio – to maintain the reliability of the process and ensure that product granules have a stable size distribution.
Advantageously, the hydraulic sprayers used in the Green Granulation process can be set to generate seeds. This, in turn, makes the OFBD process much more stable and less dependent on feed from the crusher(s). This allows the granulator to function at a very low recycle ratio, while still maintaining a very stable granulation process without size distribution fluctuations.
Cold Recycle Granulation
Casale Green Granulation plants incorporate Cold Recycle Granulation. This cools granules to optimise process conditions and guarantee stable operations. In particular, the crushers and vibrating screens are kept clean thanks to the low temperature of the solid recycle.
In other processes, in contrast, the presence of warm granules, being softer than cooled granules, leads to fouling of the screen decks and roll crusher. This is deleterious as the blocking of screen decks has a huge influence on the size distribution of the end-product. Fouled crusher rolls also create excessive dust which can build up inside the granulator and overload the process.
Casale Green Granulation plants avoid these problems as they are designed to handle the solid recycle at the lowest economically feasible temperature. Their deep cooling action also helps to generate granular products with a desirable highly polished surface.
The overall reliability of the Green Granulation process is also ensured by optimising the airflow. Proper airflow through the system is beneficial as it:
- Creates movement
- Evacuates heat from the fluidised bed layer
- Removes dust particles from the spray zones
- Maximises the interval between wash stops by keeping the walls and roof sides inside the granulator and cooler(s) clean.
Double Temperature Scrubbing
The tail gases from Casale Green Granulation units are treated using Double Temperature Scrubbing. Installed scrubbers are designed to meet the strictest emissions limits and usually comprise of 2-4 consecutive wet scrubbing stages, depending on regulatory requirements and the type of end product.
The combination of horizontal wet scrubbers and irrigated vertical demister stages in this type of granulator scrubber provides a highly efficient scrubbing action at very low pressure drop. The mist formed in the double temperature stage(s) makes it possible to catch even sub-micron dust particles. As well as this, the high concentration (50-55 weight-percent) of the recovered solution – which is recycled to the synthesis unit – also keeps steam consumption in the evaporation section low.
Comprehensive capabilities
Casale Green Granulation technology can produce a wide range of granular products for agricultural and industrial markets, including:
- Urea
- ‘Urea+’ products that incorporate, for example, ammonium sulphate (U+AS), elemental sulphur (U+ES) and small quantities of plant nutrients (U+micronutrients)
- Ammonium nitrate (AN)
- Calcium ammonium nitrate (CAN)
- Compound fertilizers
- Urea for diesel exhaust fluid (DEF)
- Urea for cattle feed
- Technical grade urea.
These comprehensive capabilities are valuable, especially as the nitrogen fertilizer market is continuously looking for enhanced fertilizers, higher nitrogen efficiency, and more effective, tailor-made products for specific crops.
As outlined in this article, the state-of-the art finishing technologies in the Green Granulation portfolio open up various new market opportunities, at a time when requirements from fertilizer producers are becoming ever more challenging. Casale is consequently well positioned to meet the demands of its customers, today and tomorrow, by offering front-to-end solutions and complete key-turn projects, as well as revamping options for outdated units.