Fertilizer International 517 Nov-Dec 2023
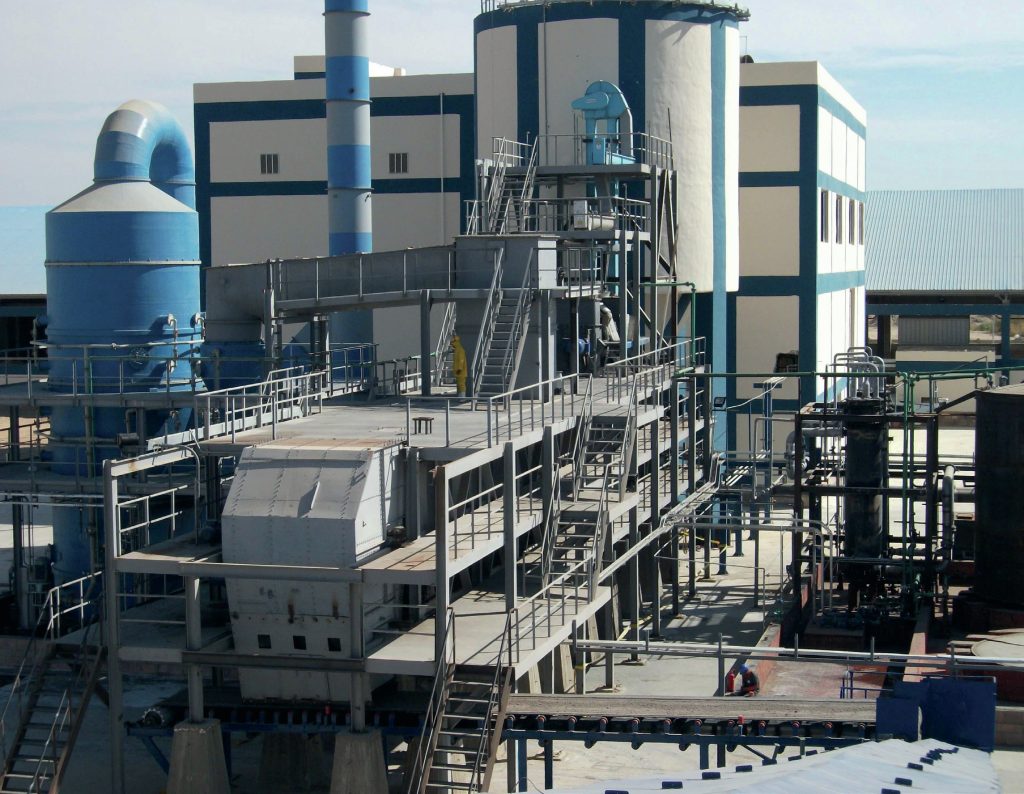
30 November 2023
Minimising heavy metals in superphosphate manufacturing
PHOSPHATE FERTILIZER PRODUCTION
Minimising heavy metals in superphosphate manufacturing
The cadmium and heavy metal content of sedimentary phosphates are of great concern. This has seen industry raw material consumption shift towards igneous phosphates or the blending of phosphate rocks from different sources. While rock blending can successfully reduce the heavy metal content of superphosphates, it needs to be accompanied by careful process adjustments, as Ian Hancock, Bradley Pulverizer’s vice president sales & operations, explains.
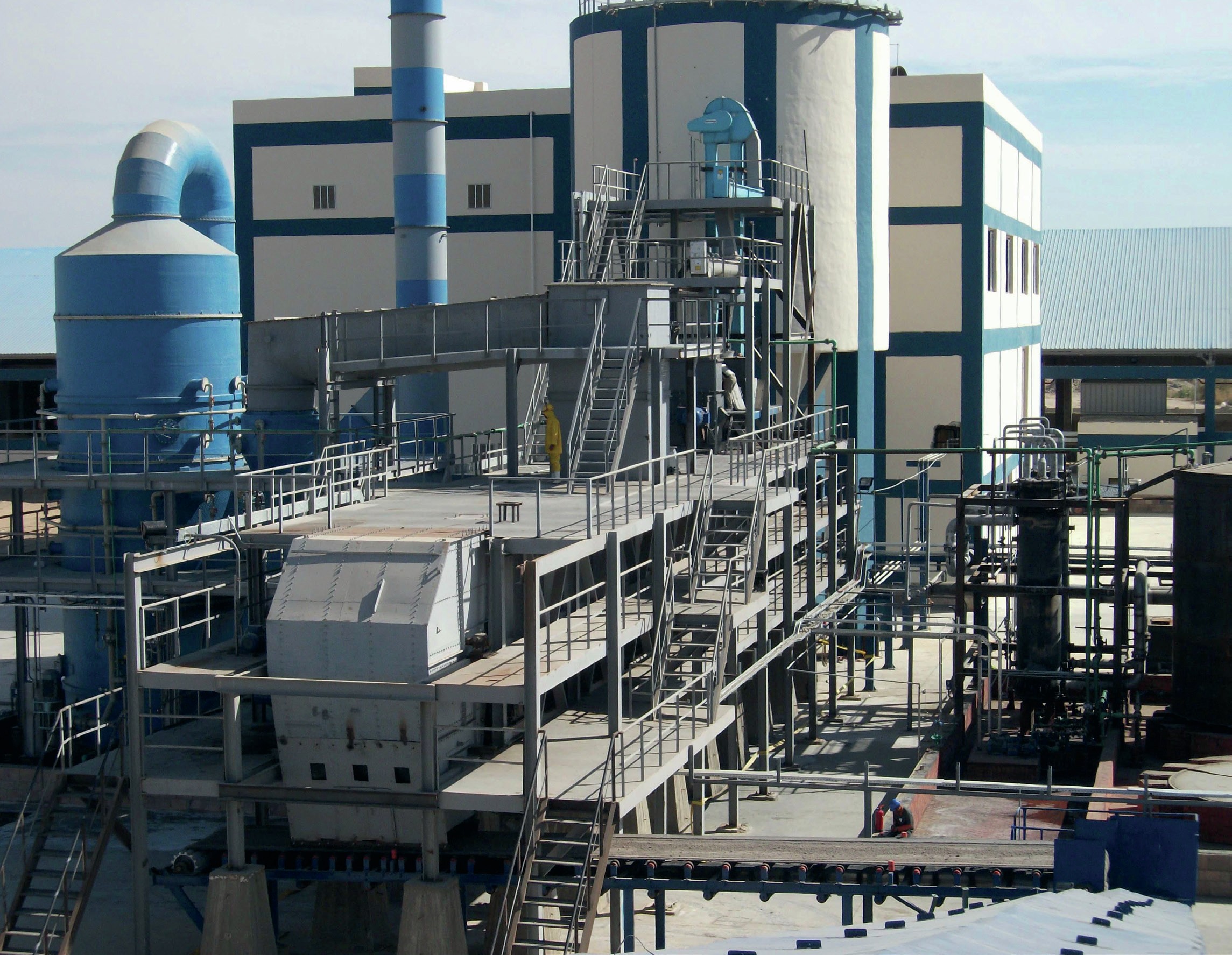
Introduction
The manufacture of single superphosphate (SSP) and triple superphosphate (TSP) fertilizers, through acidulation of fluorapatite rock, continues to evolve. Process adaptations have been necessary, for example, in response to the consumption and depletion of known phosphate rock resources worldwide.
In addition to the more obvious economic consequences, the environmental impacts of declining phosphate rock quality also demand attention and must be compensated for by the production process. Avoiding the presence of unacceptable levels of cadmium and other heavy metals in phosphate fertilizers is a particular concern and priority – as this can eventually lead to soil contamination.
Farmers first began applying phosphorus-rich materials to soils over 200 years ago by adding ground animal bones to provide crops with beneficial nutrients. The subsequent development of NPK fertilizers eventually paved the way for the large-scale fertilization of crops that is commonplace today.
The development of the Broadfield ® process by the Bradley Pulverizer Company in 1936 boosted the worldwide production of commercial fertilizers to new levels. This made the mass production of superphosphate fertilizers possible for the first time. The process produces single superphosphate (SSP) by acidulation of phosphate rock with sulphuric acid, while the addition of phosphoric acid produces triple superphosphate (TSP) and other enriched superphosphates.
Single superphosphate production
SSP production (see Fertilizer International 510, p61 for full process description) begins with the grinding of crushed phosphate rock (mainly fluorapatite, Ca3 (PO4)2 CaF2 ) in an airswept Bradley mill (Figure 1) to generate particles of the specified size (commonly 53–150µm). The resulting powder is then continuously fed into a Broadfield mixer along with sulphuric acid produced on-site. The mixer agitates the rock/acid mixture and, by coating the rock particles with the acid, kicks off the following chemical reaction:

After an average reaction time of 3-4 minutes (Figure 2), the mixture is discharged as a cake into a rugged, sealed den (Figure 1). Exothermic reactions continue within the den for approximately 20-40 minutes as the material is slowly conveyed towards the exit. On leaving the Broadfield den, the material is extruded through a cutter to break the cake into granules. It is then stored for an average of 7-10 days to allow the complete conversion of insoluble phosphate rock into water-soluble SSP fertilizer.
The acidulation process is something of a balancing act. While the number of mechanical process variables is kept to a minimum, the few that are available are designed for production flexibility, regularly allowing machines to operate at between 60-110 percent of their rated capacity.
The sulphuric acid required by the process is often generated on-site and is relatively inexpensive in comparison to overall operating costs. This means that the economics of continuous superphosphate production, at consistent yields, is primarily determined by the quality/chemistry of the phosphate rock feed. In fact, it is fair to say that superphosphate production economics are totally dependent on the phosphate rock source.
The relatively long operating life of Broadfield equipment – and the need to accommodate increasingly frequent changes to the price, quality and specifications of raw materials – means superphosphate plants have to be installed with both foresight and flexibility. To minimise costs, new installations need to combine sensible process design and operational flexibility with the latest process controls and materials technology.
Equipment upgrades generally remain an economic option even for long-lived plant operations. In fact, some Broadfield dens have continuously operated for more than 50 years. Over this period, they have experienced a marked decline in the average phosphate feedstock grade (P2O5), down from 36 percent originally to a level of 27 percent or less currently.
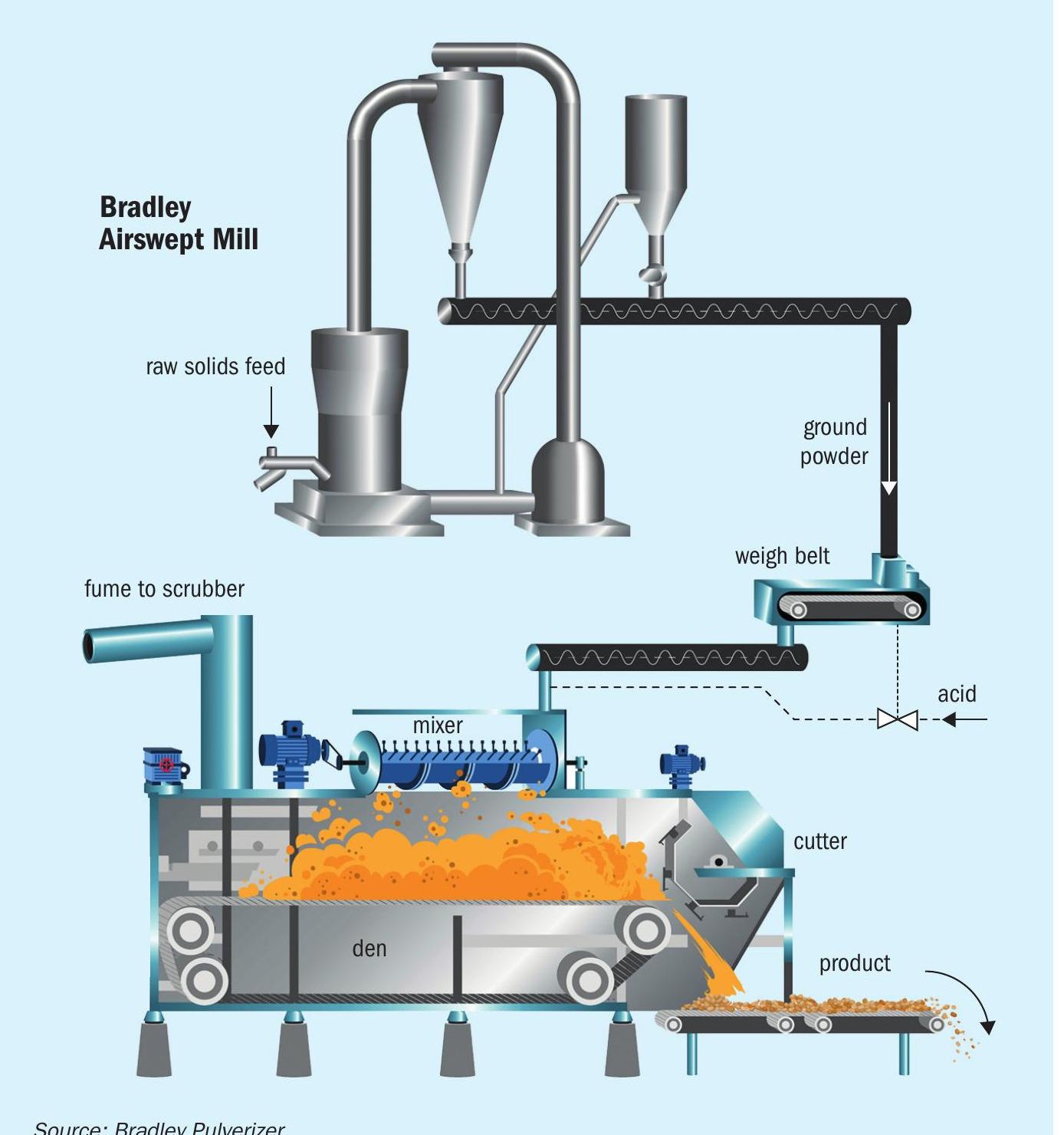
Environmental considerations
Most phosphate rock sources used in superphosphate production worldwide contain concentrations of heavy metals (cadmium, uranium, radium, lead, mercury, etc.). Such elements are known to be toxic to both livestock and humans and injurious to health if ingested at high levels.
High cadmium (Cd) levels tend to be most prevalent, making this element the heavy metal of most concern. Care is therefore taken to minimise its concentration in superphosphate fertilizers. Cd levels are typically kept to below a threshold of 280 ppm, although regulations do vary from country to country.
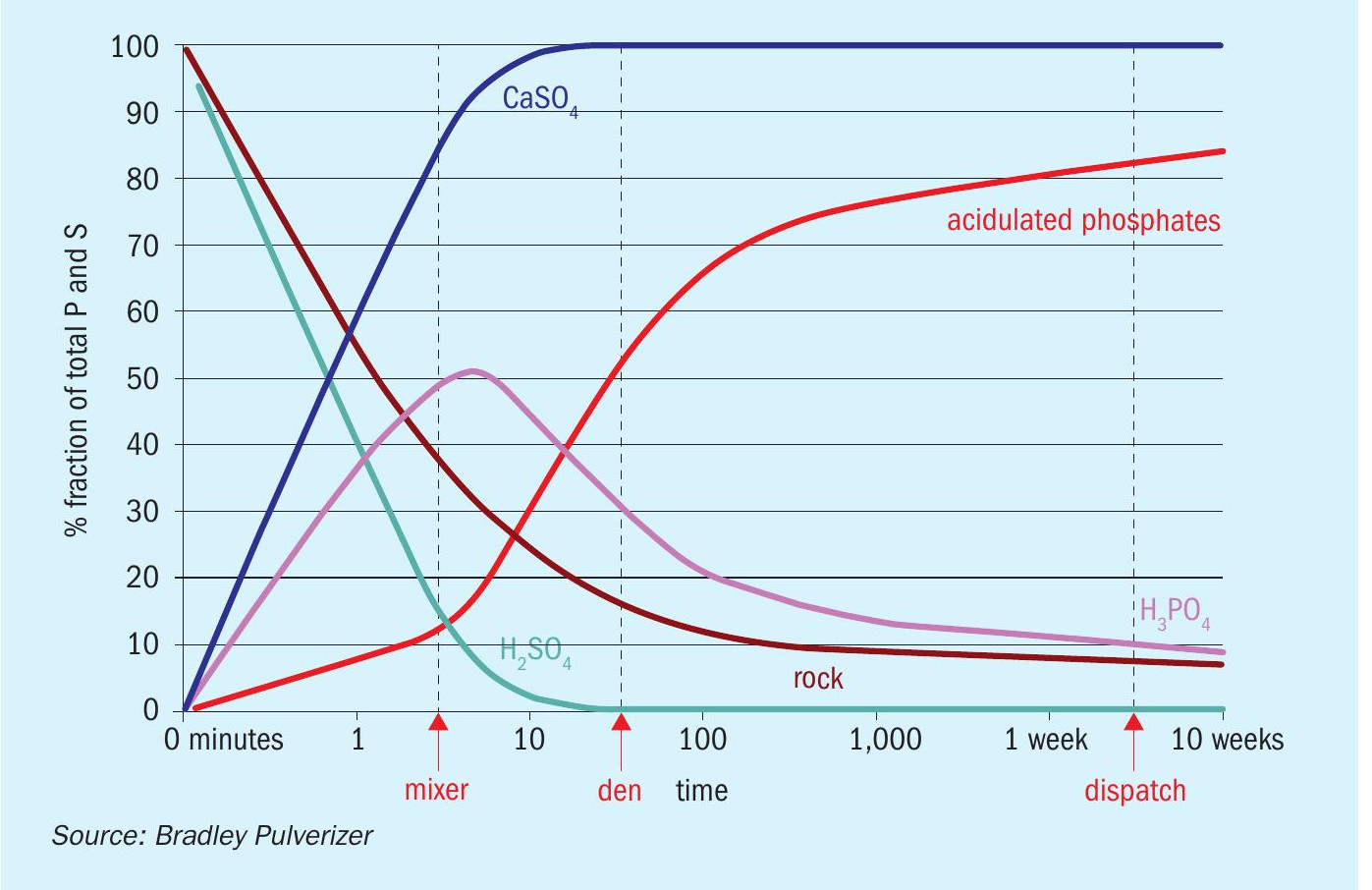
In superphosphate production, there is no simple or economically feasible way to remove heavy metals from the phosphate rock feed prior to the acidulation process, as these potentially toxic elements are locked within the crystalline structure of minerals. Fortunately, blending feed rock from multiple sources, as described in this article, can ensure that maximum Cd levels are not exceeded. Blending is a successful approach that can help prevent cadmium from accumulating in soils, crops, livestock and ultimately humans – this being the desirable long-term goal.
As well as potentially toxic elements, careful attention is also paid to the iron (Fe2O3) and aluminium (Al2O3 ) content of the phosphate rock feed. These two minor elements – collectively known as ‘R2O3 compounds’ – directly affect overall reactivity during the acidulation process and together are responsible for relatively high sulphuric acid consumption.
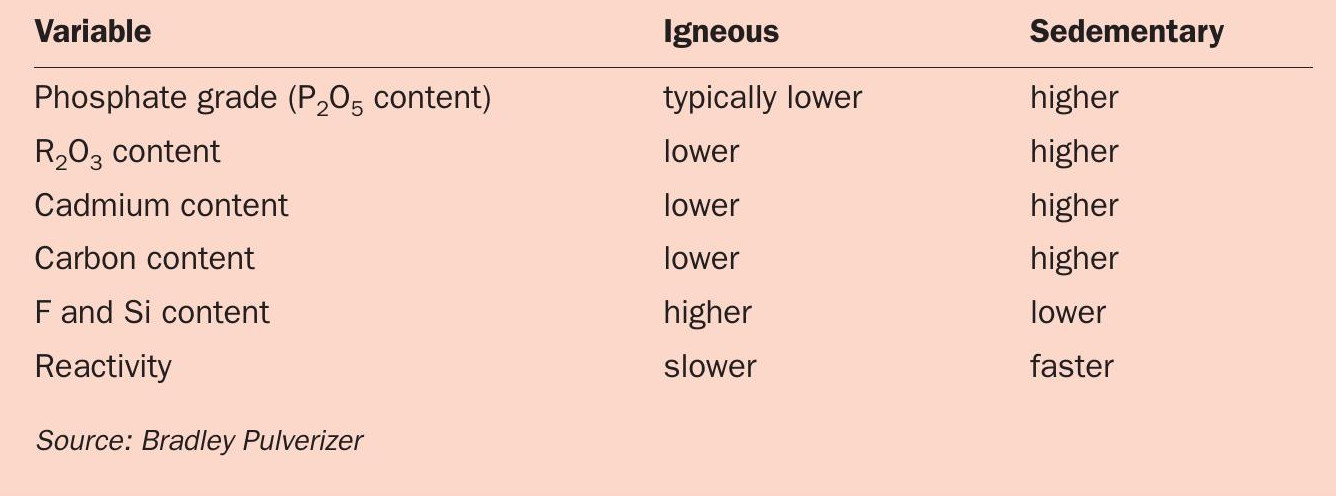
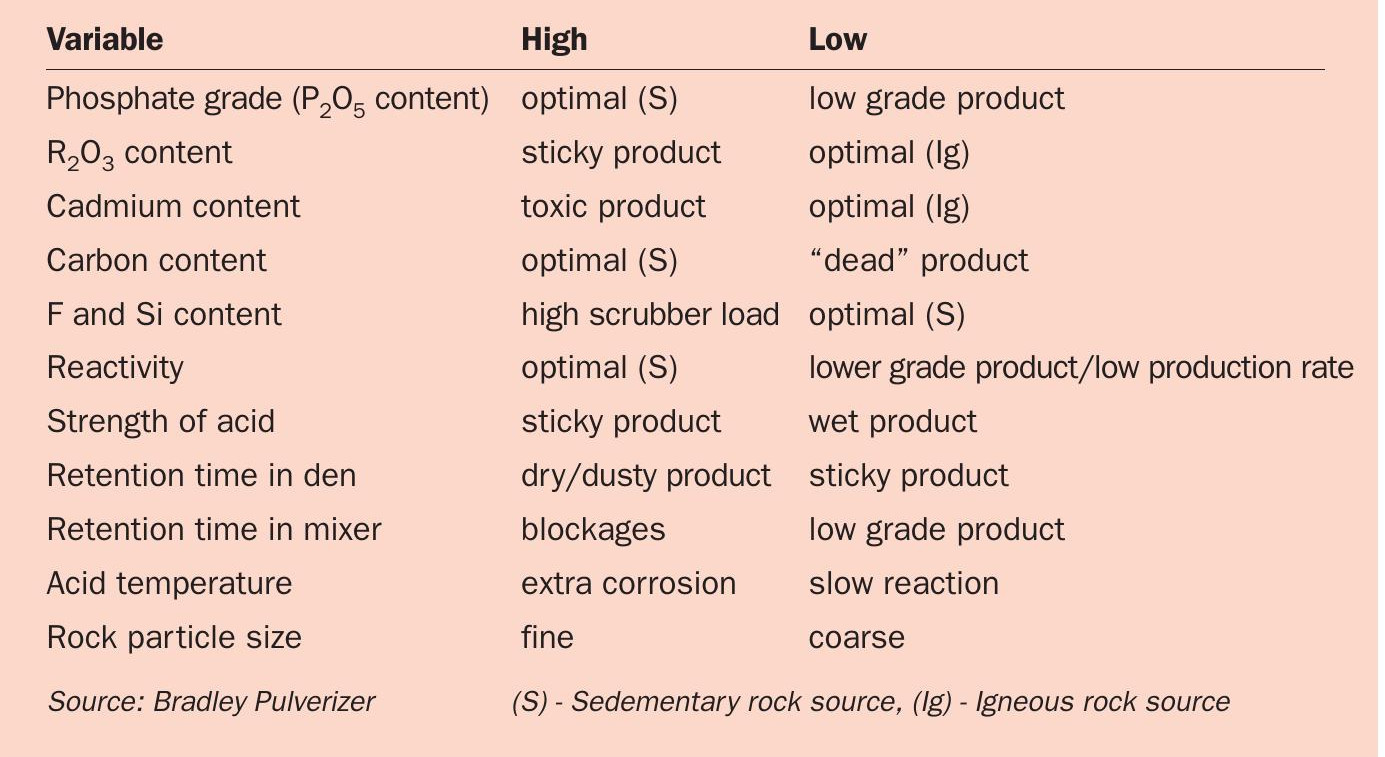
Iron and aluminium also have a strong influence on ‘retrogradation’, a phenomenon that occurs when unreacted acid is present due to a lowering of the reaction rate. This increases the liquid content of the mix and, together with iron and aluminium dissolution, causes processing difficulties and production headaches at superphosphate plants.
A phosphate rock feed with an iron and aluminium content of 1.5-2.5 percent is generally considered ideal, as it produces the best granules when processing with sulphuric and phosphoric acids. Levels above three percent, in contrast, will result in a sticky and difficult to granulate product, while, conversely, granules will degrade during storage if levels are below one percent. Running operations outside of this range is suboptimal and undesirable as, to offset inefficiencies in the acidulation process, it requires higher acid demand and energy consumption at the production plant. This result in both higher environmental impacts and lower production profitability.
Regulating heavy metals through blending
As already stated, the typical target limit for cadmium in superphosphate fertilizers is <280 ppm. It might be concluded, therefore, that the answer is to simply source phosphate rock with cadmium levels (in fluorapatite) below this limit as a production feedstock. However, this apparently simple answer is not generally practical due to the different processing characteristics of low cadmium (igneous) and high cadmium (sedimentary) phosphate sources (Table 1).
In practice, igneous phosphate ores, typically sourced from South Africa, Brazil, and Russia, while providing safe cadmium levels (typically 30 mg/kg P), come with operational downsides. Hard, crystalline igneous phosphates, because they are less reactive during the acidulation process, can unfortunately deliver suboptimal end-products. Softer sedimentary rocks, meanwhile, from major suppliers such as Morocco are unsatisfactory for different reasons. Although their reactivity rate during the acidulation process is more optimal, they can contain prohibitive levels of cadmium (200-600 mg/kg P average).
The most practical and effective solution, therefore, is to blend together phosphate rock from multiple sources to achieve the desired cadmium target limit (<280ppm) while also ensuring the acidulation process and overall operation of the superphosphate plant remains optimal.
New Zealand leads the way
New Zealand has led the way and successfully reduced Cd levels in soils that have been treated with superphosphate for decades. The country sources both igneous and sedimentary phosphate rock from worldwide suppliers – chemically analysing each shipment to establish its composition. Individual phosphate rock sources and shipments imported by New Zealand have distinctly different physical and chemical characteristics (Table 2). These include:
- Total phosphorus content
- Reactivity rate
- Amounts of impurities (i.e. Cd, Fe, Al)
- Fluorine content and volatilisation levels
- Quantities of odorous compounds.
All of the above properties need to be evaluated before the feedstock can enter the Broadfield process. The optimal rock blend is calculated, based on these operational considerations and the results of chemistry analyses.
The amount of cadmium present in the end-product is directly controlled by the levels introduced into the process. This can therefore be regulated by precise blending of different feedstock sources to provide the required rate of dilution. Typically, this is achieved by storing each phosphate rock shipment in its own feed hopper. This allows the independent control of feed volumes from different sources, to match the established blend proportion, while also allowing for adjustments during continuous operation and in-between shipments.
Blending rocks from different sources is necessary to keep superphosphate production within an ‘optimal window’. Operating within this window is desirable as, by maintaining optimal process conditions, it ensures that the end-product generated will meet all of the required specifications.
To help achieve these production objectives, Broadfield superphosphate units are designed and engineered to
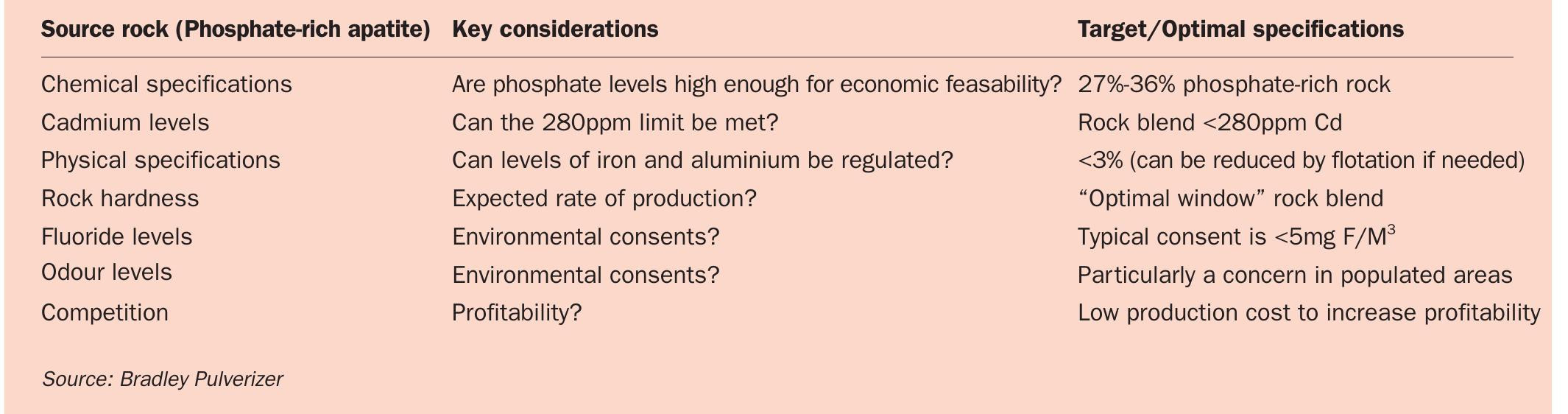
provide operators with the ability to make necessary process adjustments – for milling fineness, acid concentrations, mixer speeds, den time, etc. This allows the unit to operate efficiently, at between 60-110 percent of rated capacity, while consuming most low- and high-grade phosphate rock types.
Notably, the ability to make in-line adjustments (see below) is critical to the success of superphosphate manufacturing – given that the chemistry of the blend can change at any time due to the arrival of a new phosphate rock source, or even a new shipment from the same source. Some key manufacturing considerations are summarised in Table 3.
Determining the ideal rock blend
A stepwise approach for determining the optimal rock blend in superphosphate manufacturing is outlined below. Once the optimal blend is established, the production process tends to be straightforward and can run unimpeded with only relatively minor mechanical adjustments. However, any significant change in chemistry – due to a new phosphate rock source and/ or sourcing from a new face in an existing quarry, for example – will potentially require a change to the blend.
1. Chemical analysis. This is used to determine elemental concentrations in each phosphate rock source. At a minimum, chemical analyses should be performed by the manufacturer every time a new rock source is introduced into the process, including potential source changes at existing mines and quarries.
“Once the optimal blend is established, the production process tends to be straightforward and can run unimpeded with only relatively minor mechanical adjustments
In continuous processing, analysis of the source rock(s) at regular intervals is also recommended to determine what process or mechanical adjustments might be required to maintain the highest end-product yields. Particular attention is placed on phosphorus, iron, aluminium, calcium, and fluoride concentrations, as these elements have the greatest influence on the reaction process and the specifications of end-products. Levels of heavy metals such as cadmium are also verified at this point as, although having a minimal effect on the acidulation process, these are of primary importance to the commercial viability of the end-product.
2. Determine ideal acid:rock (A:R) ratio. The information collected in step 1 is run through stoichiometric calculations to establish a theoretically ideal rock blend that will meet end-product specifications. This assumes ‘perfect-world’ conditions such as constant process conditions and uniform rock chemistry. A further quantitative analysis is then applied to establish the volume of acid required for optimal process conditions. This is known as the A:R ratio and, for the purposes of calculation, assumes 100 percent acid strength.
3. Pilot-scale testing to confirm actual A:R ratio. Laboratory testing of phosphate rock sources only requires around 100 grams of material. The nearly instantaneous results obtained make this the ideal step for establishing the ’real world’ rock blend necessary for commercial-scale superphosphate production. The data gathered is used to determine the optimal phosphate rock blend and A:R ratio at production-scale needed to meet the target end-product specifications.
4. Production testing. During production, the actual acidulation reaction conditions (e.g., time and volume) taking place in the exothermic conversion of rock to fertilizer cannot be replicated in laboratory batch tests. Production testing is therefore necessary. Conveniently, there is an opportunity to test both the physical and chemical properties of partially reacted superphosphate when this exits the den and enters the storage silos. Target values – for optimal maturation time and high-quality superphosphate – typically include 7-8 percent free acid and 11-12 percent water content. The target cadmium levels (<280 ppm) in the end-product are also confirmed at this stage. Further blending and testing, to keep within cadmium limits and achieve commercial acceptance, will be necessary if product Cd levels exceed this target value.
In-line process optimisation
Actual process conditions within the Broadfield superphosphate unit are only fully measurable during full scale production. In-line process sampling and testing is non-disruptive and the ideal way to maximise plant profitability by ensuring continuous production with minimal shutdowns.
As this article makes clear, superphosphate fertilizer production is always subject to unexpected changes in process conditions (temperature, rock chemistry, reaction times, etc.). Increases in iron, aluminium and magnesium levels, for example, introduce undesirable effects by:
- Preventing the A:R ratio being reached
- Consuming more acid
- Making the ex-den product sticky.
Fortunately, the Broadfield unit can be mechanically adjusted to compensate for these changes by increasing:
- The fineness of the rock
- The residence time in the mixer or den
- The reaction temperature within process restraints.
In fact, the Broadfield mixer, with its horizontal trough design, is specifically engineered to compensate for many of the variations frequently encountered during the acidulation process, as described in this article, such as changes in phosphate rock composition. In particular, the mixer’s low speed means it can hold materials for longer and therefore slow down processing times if necessary. Indeed, the ability of the Broadfield mixer to alter residence time, and the operational flexibility this provides, is a valuable characteristic that enables superphosphate producers to make process improvements that increase product quality worldwide.
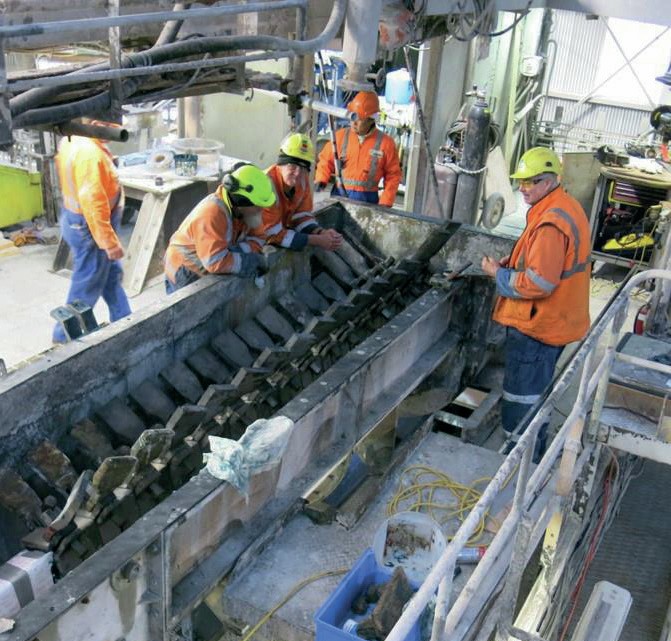