Sulphur 410 Jan-Feb 2024
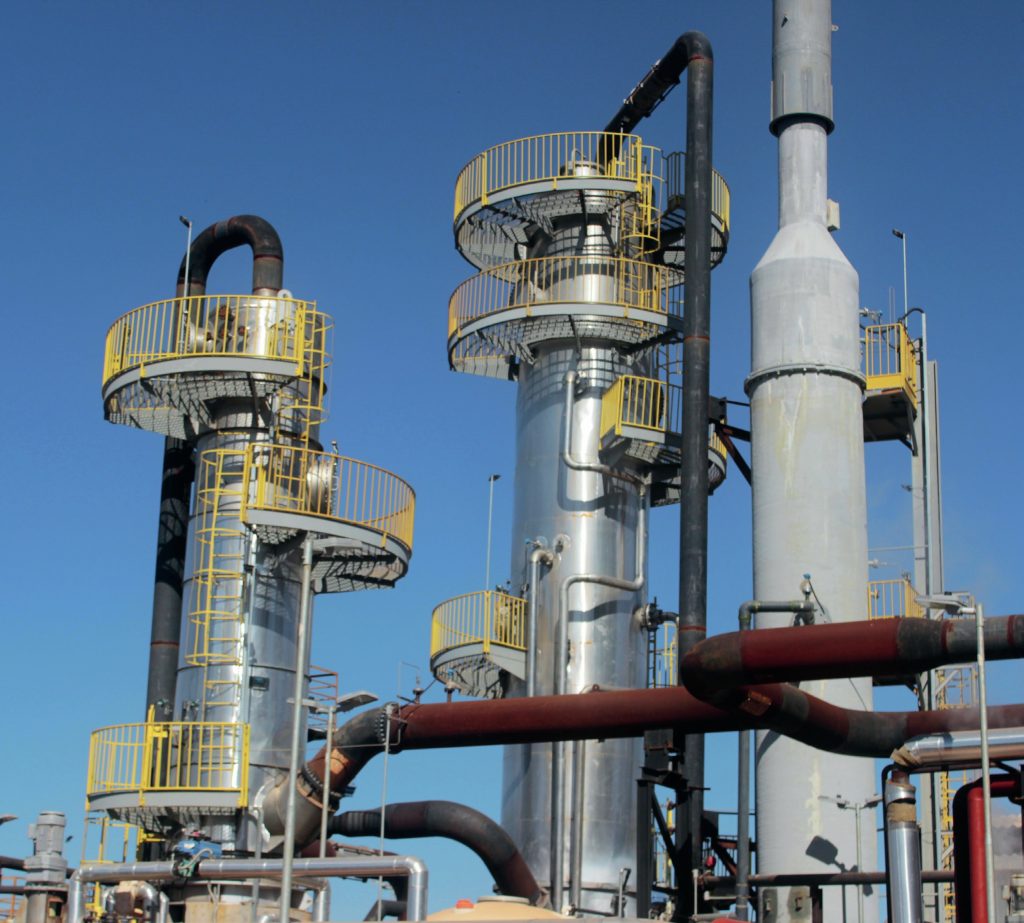
31 January 2024
Back to the roots: single versus double absorption
SULPHURIC ACID PLANTS
Back to the roots: single versus double absorption
With increased demands to reduce SO2 emissions and lower energy consumption, Eduardo Almeida and Nelson Clark of Clark Solutions highlight the advantages of single absorption sulphuric acid plants compared to double absorption plants.
In the 1950s, led by environmentalist pressure following events such as the Great Smog of London in 1952, industries emitting sulphur dioxide (SO2 ) began searching for alternatives. Specifically in the sulphuric acid industry, the solution was to increase the conversion of SO2 to SO3 from 96 – 97% to 99.6 – 99.7%, favouring thermodynamics by the intermediate removal of oxidised SO3 . This transformation changed single absorption plants into double absorption, reducing emissions by both increasing energy consumption and decreasing specific steam generation.
This situation was not a problem until the end of the 20th century and the beginning of the 21st century when energy costs and environmental restrictions became more relevant. This made single absorption plants with tail gas treatment more economically and environmentally viable.
Current scenario
As a result of a more than 60-year hiatus, single absorption (SA) plants have been set aside in most countries, and double absorption (DA) plants have become the global standard. As environmental legislation advances and becomes stricter, SO2 emission limits for sulphuric acid plants will gradually decrease. The typical 2 kg SO2 /tonne produced H2 SO4 is being reduced worldwide, with a new standard in development that requires emissions below 0.5 kg SO2 /t H2 SO4 .
SO2 emission control in DA plants is not straightforward. As the campaign progresses, the efficiency of catalyst conversion decreases, and the usual method of control involves reducing plant capacity, which has a significant economic impact. Some double absorption plants address this issue by adding a 5th catalytic bed and using more sophisticated and efficient catalysts. However, this solution results in a substantial increase in energy consumption for the plant.
Additionally, plant start-ups and shutdowns in DA plants typically lead to emission levels above regulations. This is increasingly deemed unacceptable by public administration and nearby communities
On the other hand, with advancements in flue gas desulphurisation (FGD) technologies, the versatility of single absorption plants becomes more attractive. SA energy consumption is considerably lower, specific steam production is higher, and there is the possibility of a co-product generated from gas washing at the end of the process.
Sume current DA plants are adding a tail gas treatment system downstream from the final absorption tower. However, a more attractive alternative is transforming a double absorption plant into a single absorption plant.
Converting from double to single absorption
The core of a double absorption plant lies in the intermediate circuit, where oxidised SO3 in two or three catalytic beds is absorbed in an intermediate absorption tower before returning to the reactor. This flow proceeds towards one or two catalytic reactors where the absence of SO3 significantly favours the course of the oxidation reaction and overall conversion.
The intermediate circuit is complex, generally consisting of a SO3 absorption tower and its internals and appendices (liquid distributors, mist eliminators, packing, pump, tank, acid cooler), gas-gas heat exchangers, pipelines, valves, instrumentation, and, last but not least, footprint/ civil basis.
From the perspective of conversion efficiency, the intermediate circuit allows the possibility of raising conversion up to 99.9%, although the trade-off is higher energy consumption and a loss of plant operational flexibility.
Inside the gas-gas heat exchangers, the process gas cools down the gas heading towards absorption and reheats the stream exiting the tower that returns to the reactor. This process becomes extremely restricted at low capacity when limited heat exchange area prevents or hinders ideal temperature conditions. In such instances, the plant experiences lower conversion and acid condensation on cold heat exchanger locations.
To transform a double absorption plant into a single absorption plant, two aspects must be considered: Removal of intermediate absorption circuit and tail gas (TG) system addition.
Intermediate circuit elimination
In SA plants, the gas passing through the reactor, containing three or four beds, does not undergo an intermediate removal of SO3 . This eliminates the need for gas-gas heat exchangers. Instead, heat removal equipment can be installed to recover the heat generated from oxidation.
This configuration may include boilers, economisers, and superheaters to achieve virtually any desired steam specification. Of course, the intermediate absorption tower must be disabled or transformed into a final absorption tower, and the choice of tower characteristics will determine the best course of action. Acid coolers can be repurposed, and depending on their configuration, circulation tanks may be reused or reallocated.
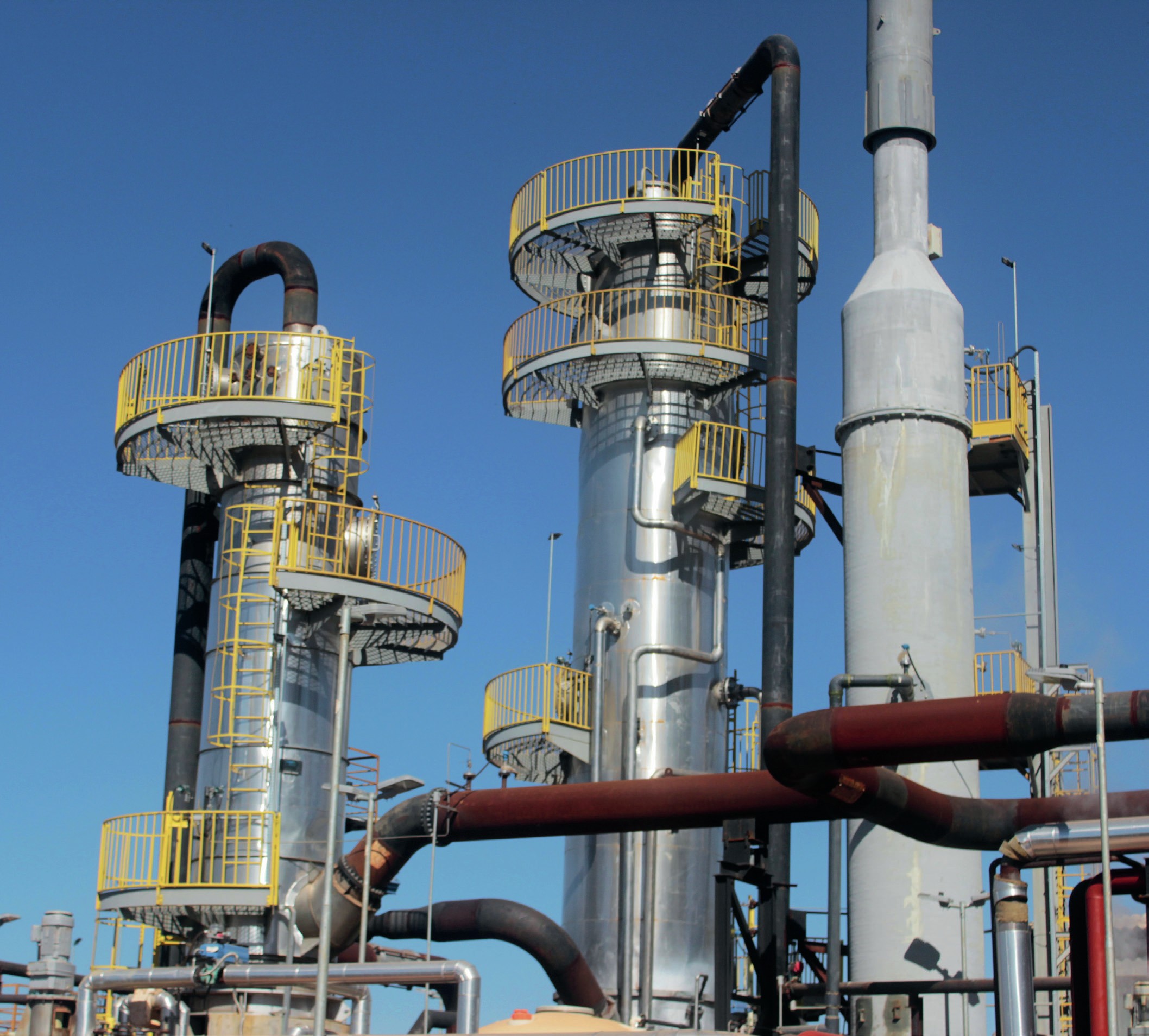
After these modifications, the single absorption plant can benefit from maximum recovery of heat generated in the catalytic reactor. This energy can increase steam generation by more than 25% compared to DA plants.
Additionally, by eliminating the intermediate circuit, the plant’s total pressure drop is reduced by roughly 30 to 40%, significantly decreasing the energy consumption of main blowers and increasing the time between shutdowns.
Tail gas scrubber system addition
The removal of the intermediate circuit reduces the SO2 content after the catalytic reactor to pre-double absorption levels, ranging from 6 to 20 kg SO2 /t H2 SO4 . Utilising cutting-edge catalysts enables conversions of 98.5%-99.0% to be achieved in reactors with three or four beds in an SA plant. In addition to eliminating the intermediate acid circuit, a catalytic bed can be removed, still achieving SO2 conversions up to 98.5% using modern catalysts and adjusting gas inlet concentrations.
To address residual non-converted SO2 , a tail gas treatment is added between the absorption tower and the stack. This treatment can be approached in two different strategies: coproduct generation or SO2 regeneration. The former generates a solution that could either be sold or used in other applications when the sulphuric acid plant is part of an industrial complex. The latter consumes negligible washing solution with the associated costs of steam consumption.
In the coproduct generation approach, a plastic or metallic scrubber is installed. SO2 reacts with a selected solution, generating the coproduct. The choice of coproduct should ideally align with a strategic destination, considering factors such as high added value and logistical advantages in its use. Numerous options exist, as SO2 is an acid gas with properties favourable to acid-base reactions.
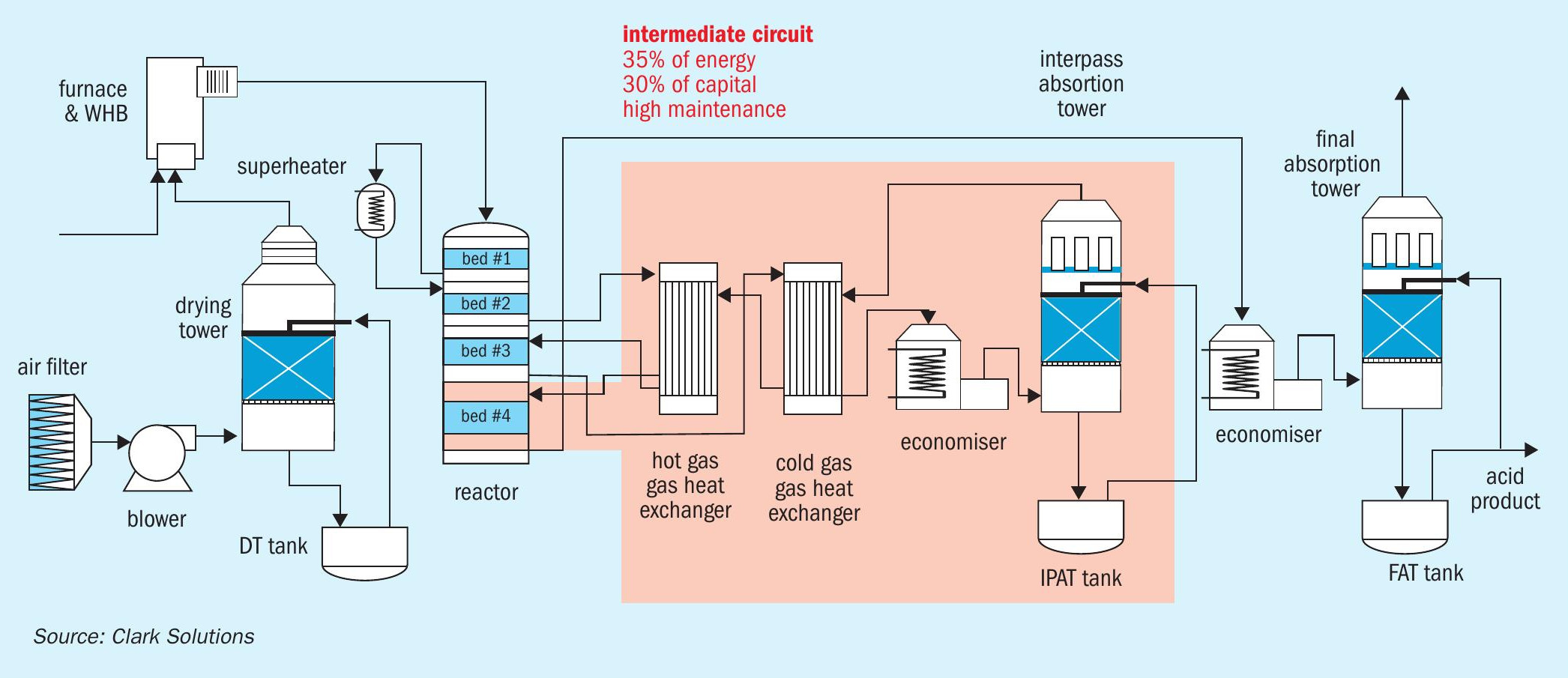
Washing solution: ammonia
Due to issues related to vapour pressure between coproducts, ammonia scrubbers should utilise two packed beds operating with different concentrations of ammonia solutions. The following reactions take place on the packed beds:
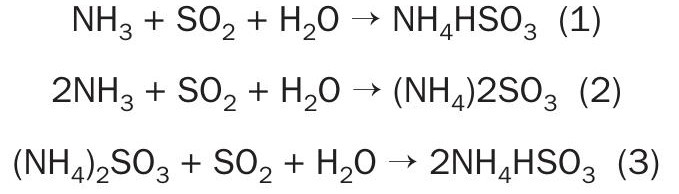
Ammonia reacts with SO2 , producing ammonium sulphite and bisulphite. This solution circulates towards an acidulator, where sulphuric acid is added, releasing SO2 from sulphite and bisulphite and yielding ammonium sulphate, a high-value product.
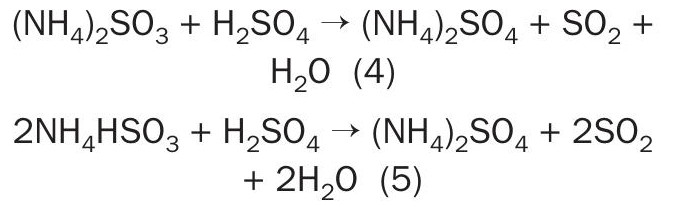
In addition to ammonium sulphate, a portion of the recovered SO2 can be recycled back to the plant’s drying tower.
Washing solution: hydrogen peroxide
Unlike the other standard washing methods, using peroxide will produce diluted sulphuric acid that can be directed to the process either as dilution water or used for leaching processes. The reaction strongly depends on both sulphuric acid and hydrogen peroxide concentration in the washer recirculating solution. As a general rule, the optimal concentration of acid in this solution is about 35-40%. Higher concentrations will require a double-deck solution, marginally increasing system investment.

Washing solution: caustic soda
Using caustic soda is the most traditional method of absorbing SO2 in atmospheric emission treatment systems. The caustic soda solution reacts immediately with SO2 inside the scrubber:
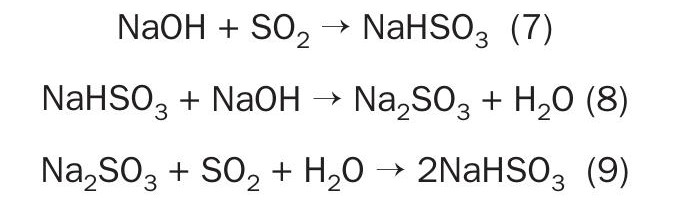
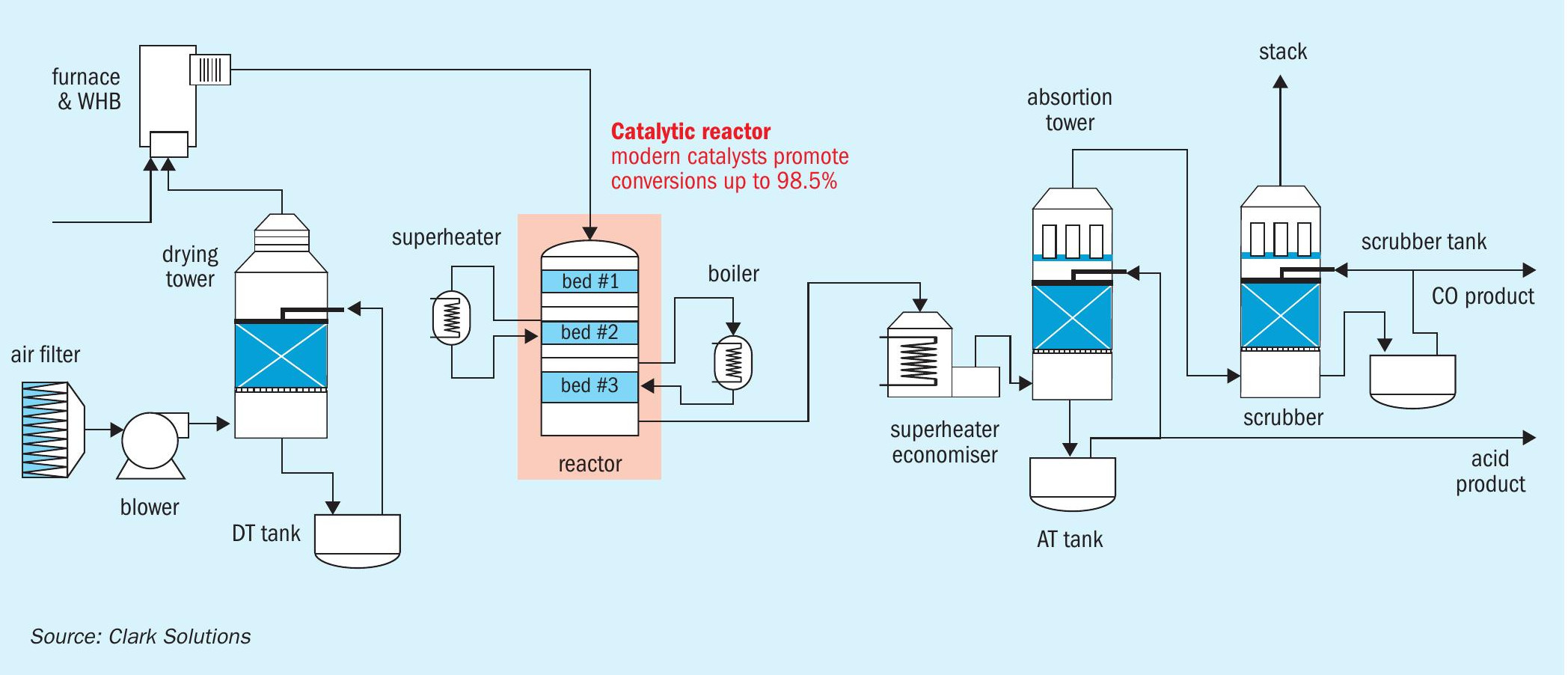
Caustic soda reacts with SO2 , yielding sodium sulphite and bisulphite. pH control of the solution allows for the preferred coproduct to be produced. The sulphite or bisulphite can then be removed as a valuable commercial product. The SO2 can be regenerated by introducing the solution into an evaporator, where SO2 is recovered and can be sent back to the plant drying tower.

In this case, the sulphite and bisulphite production can be adjusted, both to minimise and maximise production. This situation involves reducing acid plant conversion to increase coproduct yield.
Other methods of eliminating SO2 with alkaline solutions are viable. Lime or calcium hydroxide can be used to produce calcium carbonate. In this scenario, scrubbers with large nozzles without a packed bed, e.g., Clark Solutions MaxiJet, are necessary to minimise fouling. Other chemicals, such as magnesium hydroxide, zinc hydroxide, among others, can also be employed.
Regenerative approach
A different approach involves regenerating all SO2 absorbed by the washing solution. In this case, the objective is to capture almost all SO2 , leaving the stack free of this component. Subsequently, the recovered SO2 can be regenerated by treating the scrubbing solution. This generates a SO2 stream that can be returned to the acid plant and/or utilised for some specific purpose as a pure stream.
The most common regenerative systems utilise either amines, sodium sulphite/bisulphite (as mentioned before), or sodium bisulphite/phosphate. All of them operate with reversible reactions, each with its benefits and disadvantages. Clark Solutions recommends the sodium bisulphite/phosphate approach using the SOPHOS technology, which ensures a decrease in the washing solution oxidation, and consequently, losses.
All cited regenerative approaches consist of two towers and auxiliary equipment. The absorption tower is where the lean washing solution reduces the SO2 content from the gas to meet environmental restrictions standards. The washing solution will be rich at the absorber bottom; therefore, it is fed to an evaporator or stripper. The increase in temperature reverses the reaction, releasing the SO2 , which is then conditioned and returned to the sulphuric acid plant drying tower and/or dried for compression and other uses.
Advantages of single absorption over double absorption
A single absorption plant can offer numerous advantages compared to a double absorption plant, both in the case of a transformation and the construction of a new facility. Advantages include:
- Smaller capex:
– Fewer equipment requirement by eliminating the intermediate acid circuit.
– Lower blower and engine costs due to reduced pressure drop.
– Lesser catalyst volume with tail-gas treatment leading to lower SO2 emissions.
- Lower opex:
– Reduced blower pressure discharge and energy consumption.
– Tail gas system opex:
- Compensated with coproduct added value.
- Very low for regenerative configurations.
- Less maintenance cost:
– Lower catalyst usage in single absorption plants, reducing maintenance expenses.
– Single-stage blowers with reduced maintenance costs.
– No intermediate acid circuit, lowering equipment maintenance costs.
- Higher reliability:
– Fewer equipment and valves.
– Single-stage blowers in single absorption plants typically experience fewer issues than those in double absorption plants.
– Elimination of gas-gas heat exchangers, prone to acid condensation and failures.
- Higher turndown:
– Single absorption plants can operate at lower capacities, limited only by blower capacity, whereas double absorption plants face limitations due to reheating difficulties in the intermediate circuit.
- Higher steam generation:
– Improved heat utilisation without the intermediate circuit leads to surplus steam generation, around 0.3 t/t H2 SO4 more compared to double absorption.
l Lower emissions:
m Emissions easily controlled by the tail-gas treatment system, achieving levels lower than 0.1 kg SO2 /t H2 SO4 if needed.
- Cleaner start-ups and shutdowns:
– Continuous control by the tail-gas treatment system in single absorption plants, ensuring emissions are managed during all operational phases.
- Faster and cheaper start-ups:
– Smaller plant size, fewer catalysts, and equipment result in about 30% less fuel and time required to start a single absorption plant compared to a double absorption plant.
- Safer:
– Lower risk of hydrogen accidents in single absorption plants compared to double absorption plants, with fewer reported incidents due to hydrogen exposure.
- Sustainability:
– Currently, companies are reinventing themselves to achieve greater efficiency with fewer resources. This involves producing more acid and energy while minimising capital, operational, and maintenance costs. This embodies the essence of sustainability.
Conclusions
Advantages of a single absorption plant compared to a double absorption plant have been listed, highlighting that in the current scenario, single absorption presents more economic and versatile appeal compared to double absorption. Single absorption plants should capture the attention of investors, both for constructing new facilities and for remodelling existing double absorption plants, aiming to eliminate the environmental and economic weaknesses associated with double absorption.
Clark Solutions offers an extensive range of options for evaluating, building and converting sulphuric acid plants to single absorption, including tail gas treatment systems.