Nitrogen+Syngas 387 Jan-Feb 2024
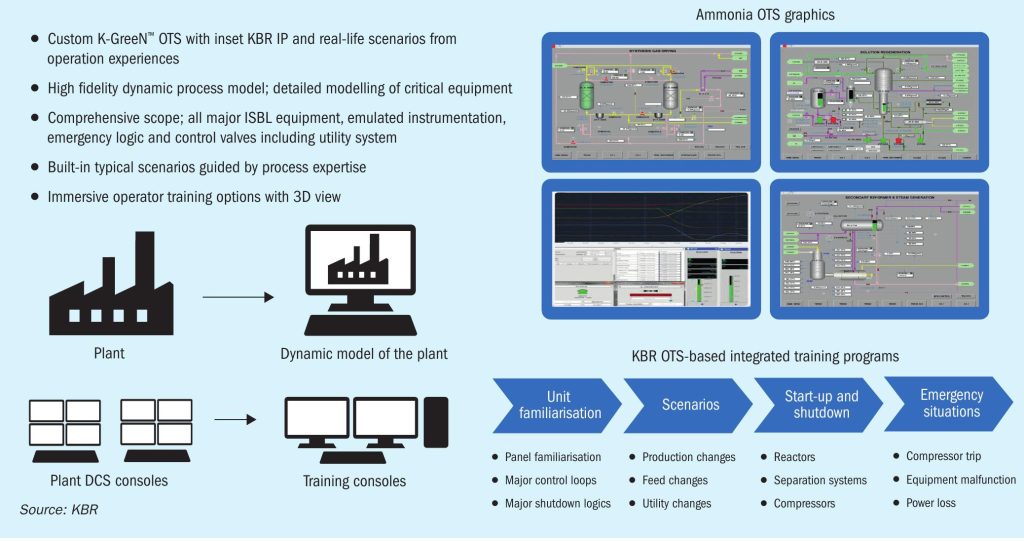
31 January 2024
End-to-end digitalisation
GREEN AMMONIA PLANTS
End-to-end digitalisation
KBR offers an end-to-end digitalisation solution specifically designed for green ammonia plants to balance the available renewable resources and consistently deliver the lowest levelised cost of green ammonia (LCOA). This article outlines some of the key modules of the KBR end-toend digitalisation solution developed to overcome the challenges in green ammonia operation and achieve best in class, safe and reliable plant operation.
KBR’s K-GreeN® Technology
KBR has developed the K-GreeN® technology, which consists of a fully integrated solution for the synthesis of green ammonia via electrolysis of water to produce green hydrogen, separation of air to produce nitrogen and the KBR’s proprietary Haber-Bosch process to produce ammonia. The KBR design can accommodate different electrolysis technologies such as alkaline, PEM and SOE electrolysis, the latter bringing attractive integration opportunities and significant overall efficiency improvements.
The KBR ammonia synthesis section is a proprietary design with proven unmatched reliability and lower energy consumption at lower capital cost (due to lower equipment count). In developing its K-GreeN® concept, KBR has leveraged on its past 75+ years of experience in designing ammonia plants, from very small capacity (4 t/d) to the largest single train capacity (6,000 t/d). Flexibility is paramount to most of the green ammonia facilities, KBR has extensive experience in flexible design and operation and has already designed and operated loops between 20% and 100% without changing the process, and with some alterations 10% turn-down is possible. Fig. 1 exemplifies a typical block flow diagram for generic green ammonia plants.
The advantages of the K-GreeN® process scheme are:
- well-proven design;
- reduced number of optimised and modularised design of the high-pressure equipment, in particular the converter and the chilling system, reducing capex and construction time;
- KBR’s horizontal converter, design well-proven since 1971;
- unitised chiller combining the feed/ effluent exchanger, several chillers, and the compressor knock-out drums into one piece of equipment;
- steam generation, superheated steam generation making loop energy efficient;
- no start-up boiler required;
- reduced opex due to lower loop pressure drop;
- reduced maintenance cost associated with fewer equipment pieces;
- robust, reliable steam generation and superheating with process gas.
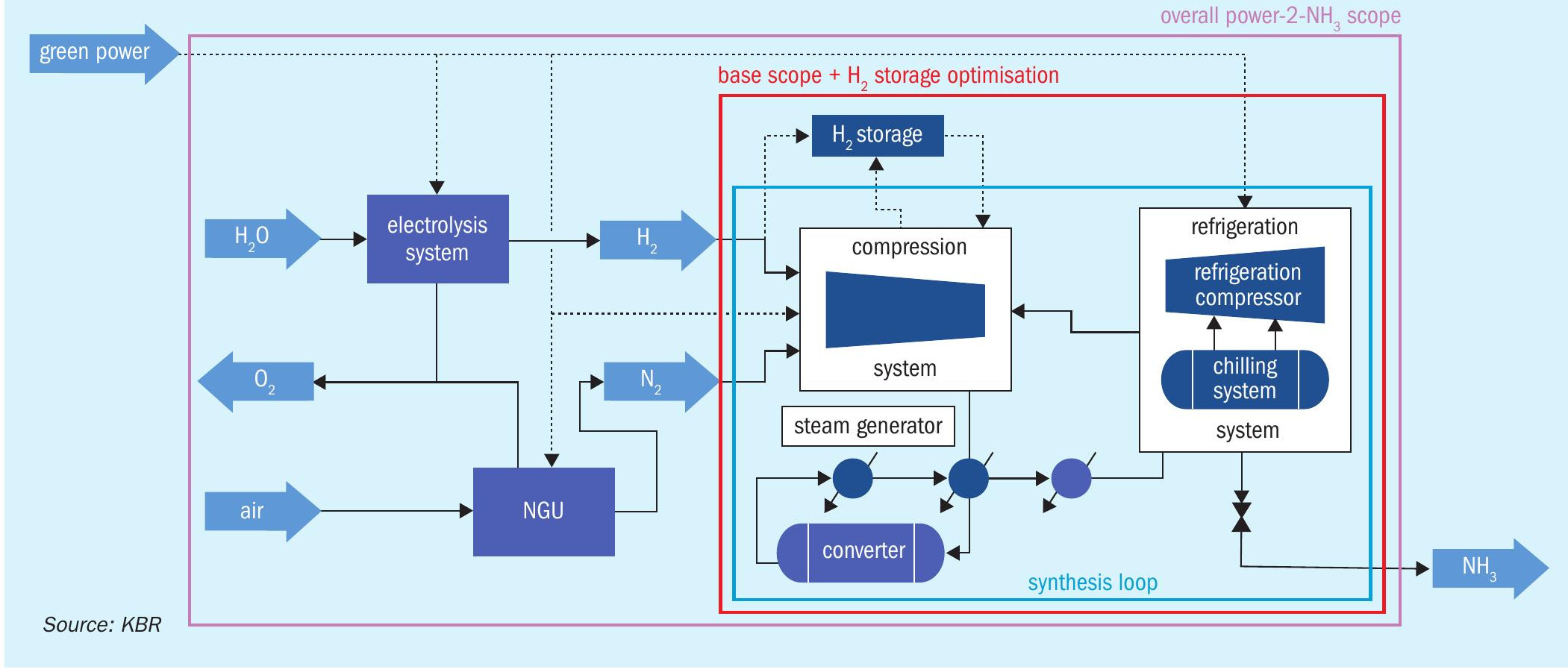
KBR solution for green ammonia plants
The availability of renewable energy, unstable by nature, causes significant fluctuations in hydrogen production, hence the synthesis loop operation may not receive a stable supply of hydrogen as required for reliable, efficient operation of the green ammonia plant. Moreover, the front end (electrolysis plant) and the back end (ammonia synthesis loop) have different dynamic responses to variations in the availability of renewable energy and different times for reaching steady state. Specifically, the ammonia synthesis loop needs longer time, several minutes or even hours, to respond to hydrogen availability variations and reach new steady state operating conditions. Therefore, it is desirable to proactively and dynamically compensate for continuous and rapid energy availability changes to ensure stable and reliable operation of the ammonia synthesis loop.
KBR offers an end-to-end digitalisation solution specifically designed and developed for green ammonia plants, which enables reliable and stable operation, while minimising the levelised cost of green ammonia (LCOA). The solution is made up of modules which can stand alone but are also appropriately interconnected and synergetic.
This article outlines some of the key modules of the KBR end-to-end digitalisation solution for green ammonia plants.
KBR Investment Optimizer
KBR offers conceptual design services, aiming at optimising LCOA for the overall plant, including the electrolysis system. The KBR Investment Optimizer is a tool which identifies the optimum size of each section for given plant location conditions and given renewable energy or hydrogen profile. The Investment Optimizer has embedded actual operating parameters which ensure realistic unit sizing and comprehensive LCOA calculations. The user can view the sizing and economic results of the design scenarios graphically on a graphical user interface.
KBR Operational Digital Twin
The KBR green ammonia plant digital twin covers the entire green ammonia plant. It receives a power generation profile as input and simulates the plant operations, including the electrolyser front end and the ammonia synthesis loop back end.
The integrated dynamic simulation model is the means to evaluate the response of ammonia production to the periodic fluctuations of renewable energy sources. Based on the analysis of different steady state and transient scenarios, the operation envelop of each equipment unit is established, and the overall control strategy is optimised to achieve robust response.
The KBR green ammonia plant digital twin is used as a design assurance tool to:
- identify the best type and configuration of the electrolysis unit;
- size the hydrogen storage;
- verify control strategies for the ammonia plant and the interconnecting systems;
- identify additional instrumentation required;
- establish operation boundaries for critical equipment.
Moreover, it is used to mimic start-up and shutdown sequences for the entire production chain and turndown and ramp-up rate of synthesis loop and critical utility systems. Through what-if analysis, it can also be used to minimise the risk of cascade trip during minor process disturbances.
KBR Advanced Process Control (APC)
The KBR APC solution covers the entire green ammonia plant, including the production of hydrogen and nitrogen in the front end and the production of ammonia in the back end synthesis loop, and achieves an optimised operation with respect to production and energy usage, while considering variations in the renewable energy availability and hydrogen storage capacity. It calculates the control setpoints to minimise process fluctuations and operate the plant closer to its equipment and process constraints in a stable and reliable manner.
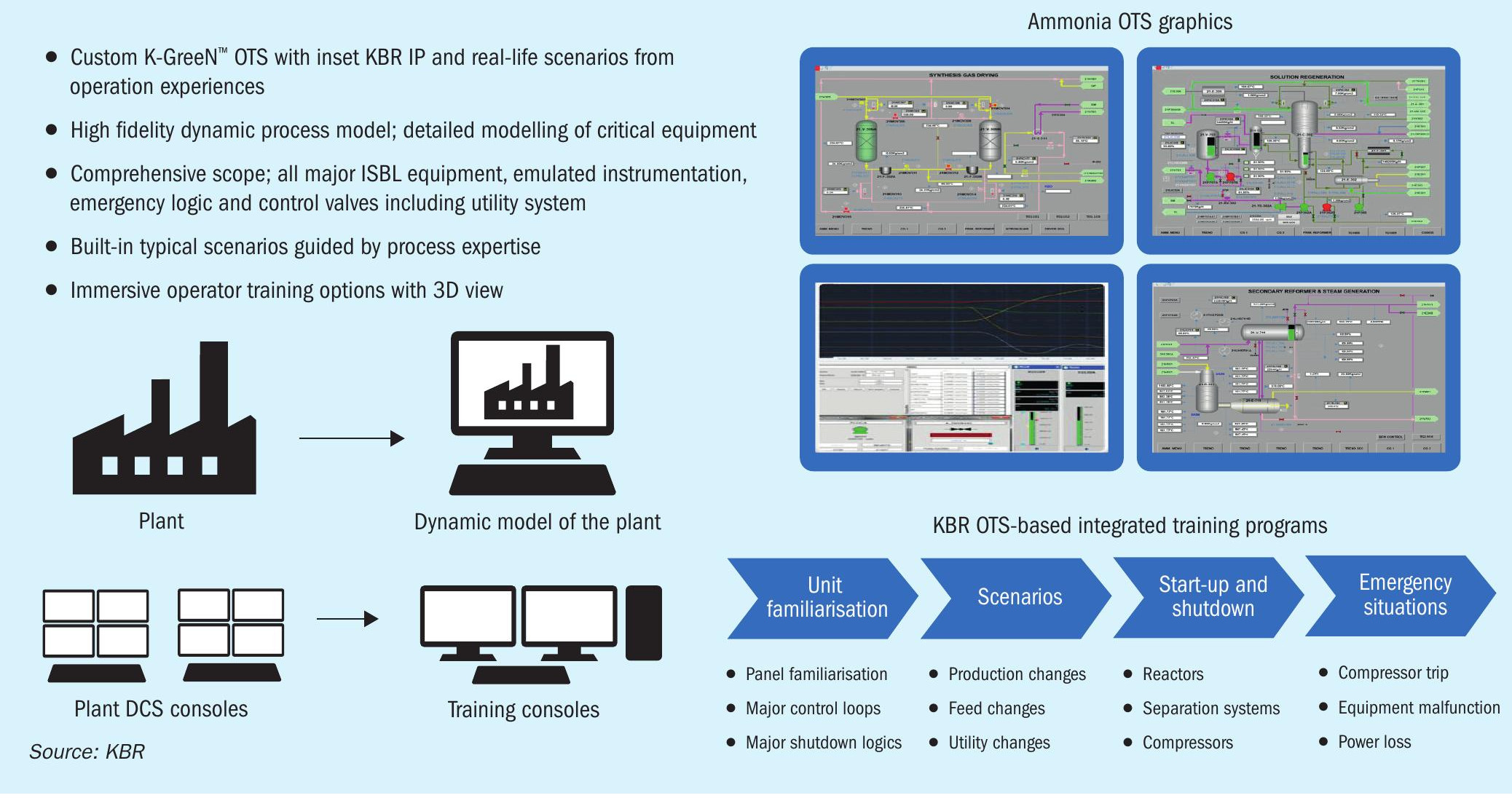
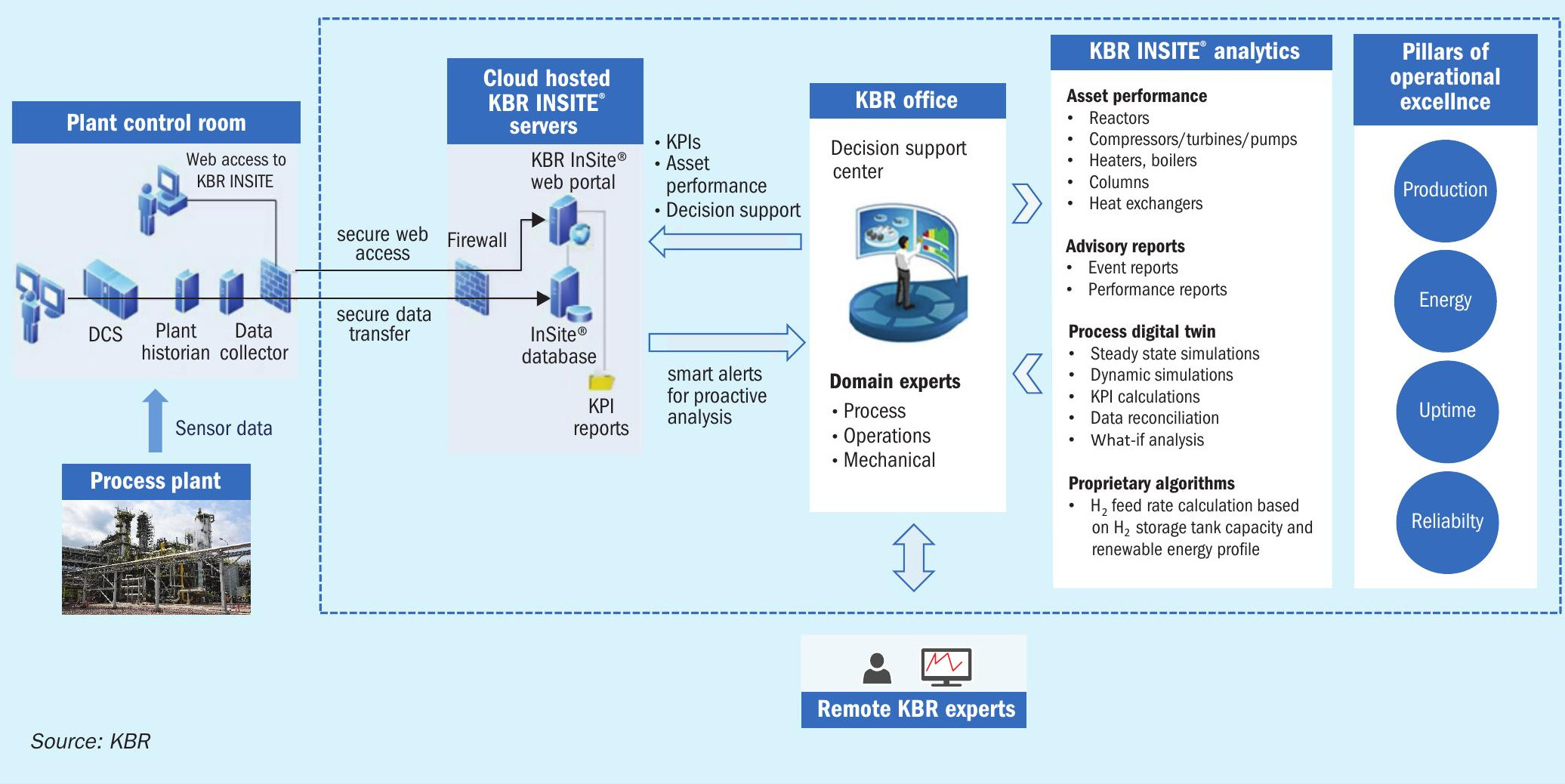
The main KBR APC objectives are:
- satisfy offtake contracts;
- optimise hydrogen production while balancing the forecasted renewable energy supply with the hydrogen storage availability;
- minimise the fluctuation in the ammonia plant production due to fluctuations in the hydrogen supply ;
- minimise energy consumption.
Additional benefits of the APC include:
- standardisation of operation;
- increase in plant reliability and safety;
- allowing operators to focus more on process monitoring than on the minuteby-minute control of the plant.
KBR operator competency development program
KBR offers operator training simulators (OTS) as well as full operator competency programs for green ammonia plants. The KBR OTS for green ammonia plants (Fig. 2) embeds KBR’s deep domain knowledge as a leading ammonia technology licensor.
The KBR OTS covers the entire plant and offers the following benefits:
- promotes faster and more efficient process unit start-ups by enabling operations staff to repeatedly practice the complete start-up procedure from empty and ambient conditions to full production;
- develops a deep understanding of the process unit operations and interactions between interconnected sections of the unit;
- tests operating procedures before they are used on the actual plant and thus identifies and eradicates any deficiencies;
- evaluates, standardises, and monitors operator performance within and across shifts;
- trains the operations team on the identification, diagnosis and management of abnormal situations that may occur during plant operations and may impact production;
- builds strong cooperation between shift supervisors, panel operators and field operators;
- greatly reduces the time required to train a new operator to a board-certified level – reduction from 2-3 years to 6-12 months may be expected.
The green ammonia plant is required to maintain smooth operation of the synthesis section considering the variation in hydrogen generation, based on renewable power availability, hydrogen storage capacity etc.
In addition to the high-fidelity OTS solutions, KBR also offers an integrated training service (ITS) program specifically for green ammonia plants, designed to maximise the value that its clients derive from the OTS. The KBR ITS includes an OTS-based integrated training guide and customised training modules for the green ammonia process, as well as training scenarios focusing on the dynamic nature of the process.
KBR INSITE® for green ammonia plants
KBR INSITE® is a market-leading, cross-industry digital platform that enables cloud-based real-time monitoring and diagnostics services aiming to optimise the performance of green ammonia plants (Fig. 3). It uses a combination of web-enabled visualisation dashboards and innovative tools based on first-principles, artificial intelligence (AI), and machine learning (ML) to unlock the value of near real-time sensor data and create an accurate digital representation of the process plant. Backed by KBR’s deep process domain knowledge, KBR INSITE® offers a uniquely differentiated service that leverages in-house or remotely located subject matter experts to provide proactive and timely guidance and decision support to plant operators.
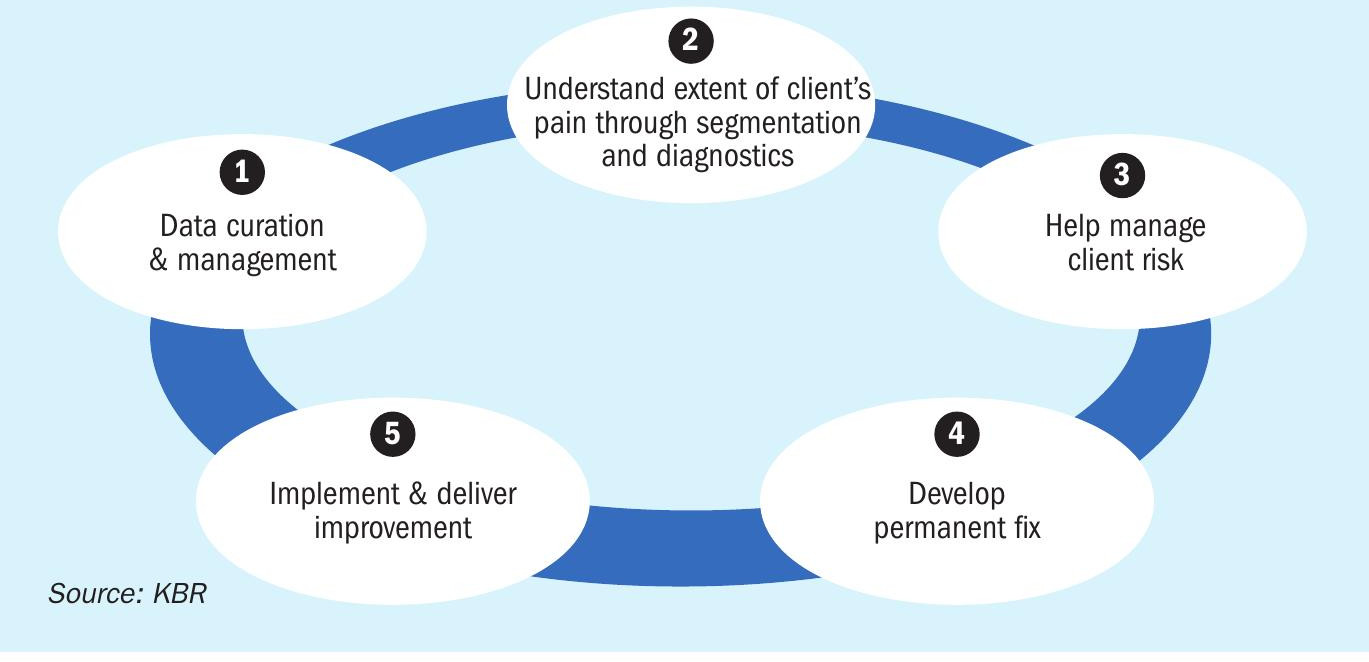
Physics-based models are utilised to estimate inherent asset health and performance parameters such as heat exchanger fouling, catalyst activity, compressor and pump efficiency, and turbine power. AI/ML based anomaly alerts are triggered from within KBR INSITE® to provide advance notification to operators of impending abnormal or sub-optimal deviations in process or equipment behaviour. In addition, these AI/ML modules are also leveraged to make aheadof-time forecasts of process behaviour and mean-time-to-failure of critical rotating equipment. Process experts analyse these alerts and predictions to rapidly identify the root cause of active or evolving operational problems, and then proactively recommend mitigating actions to minimise and even eliminate unplanned disruptions to plant operations.
Moreover, KBR INSITE® utilises smart alerts based on proprietary statistical algorithms for tracking deviations from normal equipment behaviour that can cause metal fatigue and impact the mechanical integrity of equipment.
The ability to capture and reuse past lessons and best practices, and effectively combine expert knowledge within a blend of digital solutions provides plant operators the opportunity to achieve operational excellence across all phases of the plant life cycle and for safely driving their plant operations closer to optimum targets for longer periods, while maintaining critical equipment at peak levels of efficiency, availability, and reliability.
KBR INSITE® dashboards offer:
- process schematic view of the plant with real-time access to operations data;
- KPI dashboards for visualising real-time data as well as aggregated data;
- plant hierarchy tree-structure for drilldown, navigation, content search, and alarm propagation;
- advanced trending capability to study interactions between key variables;
- secure, cross-platform, role-based access including from mobile devices;
- intelligent alerts to flag current or predicted excursions of KPIs from targeted values;
- built-in, real-time calculation engine and analytical tools for real-time KPI evaluation and overall equipment effectiveness;
- direct access to all stored content and documentation such as operation manuals, user manuals, data sheets, and best practice manuals.
KBR Intelligent Asset Management
KBR’s INSITE® Intelligent Asset Management (IAM) can accurately predict and maintain appropriate inventory levels of spare parts and ensure operational, maintenance and insurance requirements without overstocking. It can reduce inventory levels, release significant working capital, and enable better decision-making during maintenance and operations. The business objective is to maintain maintenance, repair and operations (MRO) materials and spare parts using a risk-based approach MRO, which aligns business risk with holding cost to optimise inventory levels to reduce or eliminate stockouts whilst at the same time achieving the lowest cost of ownership.

Fig. 4 provides a function overview of KBR Intelligent Asset Management.
IAM leverages cutting edge AI/ML technology on a scalable cloud platform to:
- intelligently extract and curate material and bill of materials (BOM) data at scale and pace from tag data, materials and BOM rich drawings, un-intelligent drawings and documents not available in searchable and analysable electronic format, which is frequent in older, mature plants;
- manage vast data sets in a single hierarchical plane on the cutting-edge AI/ ML platform;
- harmonise material master descriptions through the ability to learn and recognise attributes in text strings and split into reconcilable data using a standard class model;
- identify excess, obsolete and duplicate materials and bills of materials, produce clean and enriched lists with optimised min/max levels and quantifies gaps and risks;
- minimise the number of discrete suppliers, by converting original equipment manufacturers to original component manufacturers;
- identify accurately interchangeability and minimise the number of suppliers and associated contractual burden;
- identify maintenance plans and work orders which are not fully resourced with materials;
- identify critical high-risk areas and recommend solutions along with hidden/ latent insurance spares.
Use case – optimising green ammonia plant production
A case study for green ammonia production using renewable power is presented here, to demonstrate the value of the KBR digital twin and the KBR APC in optimising the production of a green ammonia plant with an assumed nameplate capacity of 1,500 t/d.
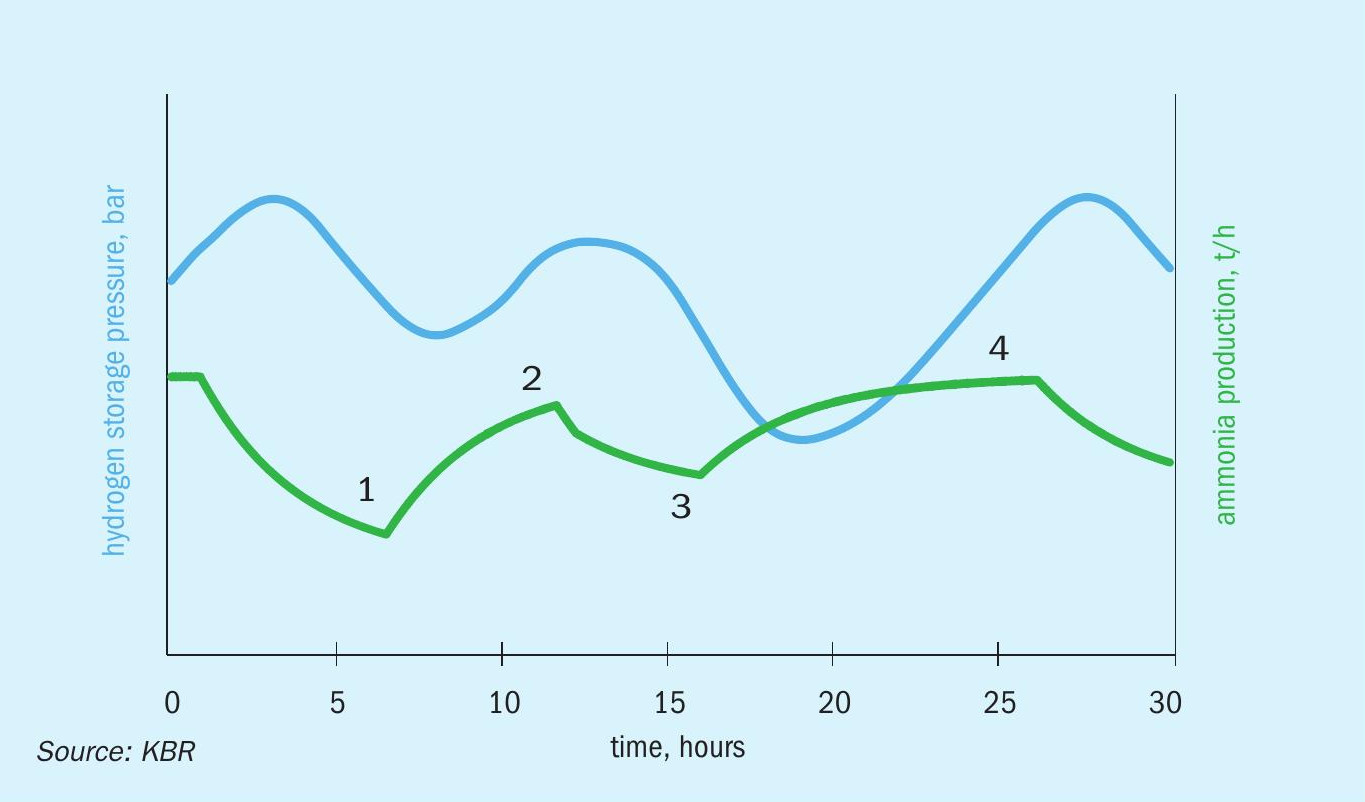
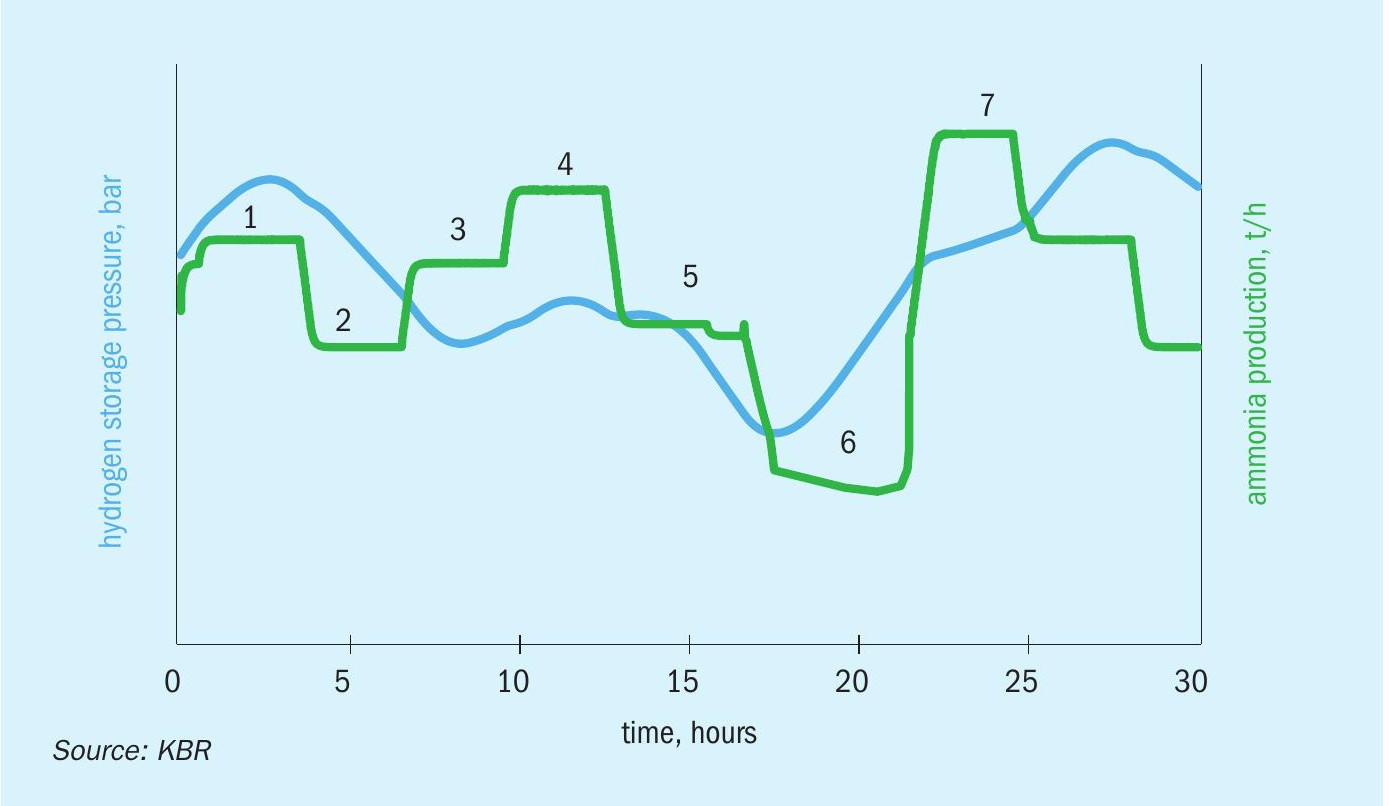
A sample power generation profile having a high degree of variability is shown in Fig. 5.
This power availability profile is fed into the KBR digital twin and the KBR APC. The APC processes the profile input and decides at each point the optimum actions to be taken across the plant.
The graph in Fig. 6 shows the expected ammonia production based on operator action to adjust plant setpoints, so as to maintain continuous ammonia production given the power availability profile.
Points 1, 2, 3 and 4 on the green curve in Fig. 6 represent changes in the flow controller setpoint enforced by the operator. With operator action, the plant runs within design parameters avoiding undesired shut down situations due to low or lack of availability of renewables. The total ammonia produced during the 30 hours period is about 89% of the nameplate production over the same period. The plant runs continuously, but not necessarily at the optimum production efficiency levels.
Fig. 7 demonstrates the capability of the KBR digital twin as part of the KBR OTS to train the operators through various scenarios, such as high variability in renewable power generation, modification of constraint limits as well as adapting to unforeseen events during operation, to evaluate operator actions and to forecast the plant’s response to those actions.
The next scenario shows how through proactive action deployed by the KBR APC, ammonia production can be improved beyond what could be achieved by an operator.
Compared to Fig. 6, Fig. 7 shows how the APC made more proactive moves to the plant operation over the first 15 hour period, resulting in higher average ammonia production. At around 17 hours (point 6) the hydrogen storage pressure is below the requirements for the forecasted period, here the APC reacts by directing hydrogen to the storage to fulfill that foreseen consumption. In total, during the 30 hours of operation under APC, ammonia production is about 4% higher than what was achieved by the operator intervention alone, as seen in Fig. 6.
Conclusion
In this article KBR describes its end-to-end integrated digitalisation solution developed to overcome the challenges in green ammonia operation and achieve best in class, safe and reliable plant operation.
Adaptability and predictability are key features to successfully design, build, commission and operate green ammonia facilities. KBR’s end-to-end digitalisation solution considers key issues such as capex and opex optimisation, increased reliability during operations, maintaining well trained, fully skilled operators, optimising the maintenance function and costs and proactively monitor and adjust plant performance based on expert advisory. KBR’s solution covers the entire lifecycle of the plant, from the feasibility study stage to conceptual and detailed design, EPC, commissioning and handover, operations and maintenance up to the end of the plant’s lifecycle. The aim is to balance the available renewable resources and to consistently deliver the lowest LCOA. n