Sulphur 410 Jan-Feb 2024
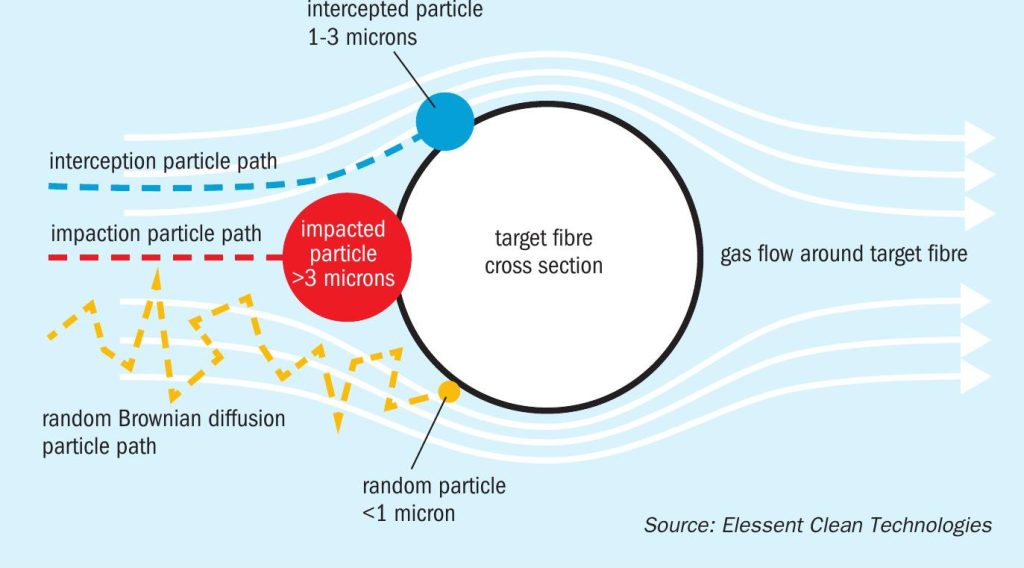
31 January 2024
New impaction technology for acid plant towers
FIBRE BED MIST ELIMINATORS
New impaction technology for acid plant towers
MECS, Inc. (MECS) has developed a new impaction-based mist eliminator called Brink® Prime Impact™ , which offers equivalent or improved efficiency at higher throughput and the same pressure drop as traditional impaction beds, resulting in the ability to debottleneck existing inter-pass absorption towers and final absorption towers in sulphuric acid plants or design new or replacement towers with smaller diameters, thus reducing investment cost.
Fibre bed mist eliminators have a long history of use in industrial applications and are utilised in a wide variety of processes. Originally invented and developed by Joe Brink in the 1950s, the use of the products that comprise this technology has become ubiquitous with removal of liquid mist and soluble solids from a gas stream throughout industry.
The devices employ micron-sized fibres to remove entrained droplets and particles from gas streams via three principal mechanisms: direct impaction, interception and Brownian diffusion. Fig. 1 shows a graphical representation of the three collection mechanisms.
Impaction mechanism: The impaction mechanism (typically effective for particles larger than 3 microns) collects a mist particle in a gas stream when it directly impacts onto a fibre. The larger the particle, the more mass it contains and therefore at a set velocity the more inertia it has that works to continue propelling the particle forward in flight when the gas flow changes direction due to an obstruction, which is in this instance a fibre in our discussion. If the gas velocity is sufficiently fast, the mass of the particle moving within the gas will have adequate momentum to cause it to impact on a fibre and adhere by weak Van der Waals forces rather than continue following the gas streamline around the fibre. Therefore, the larger the particle diameter, the more mass and thus momentum the particle has, and the easier it is for capture by the impaction mechanism.
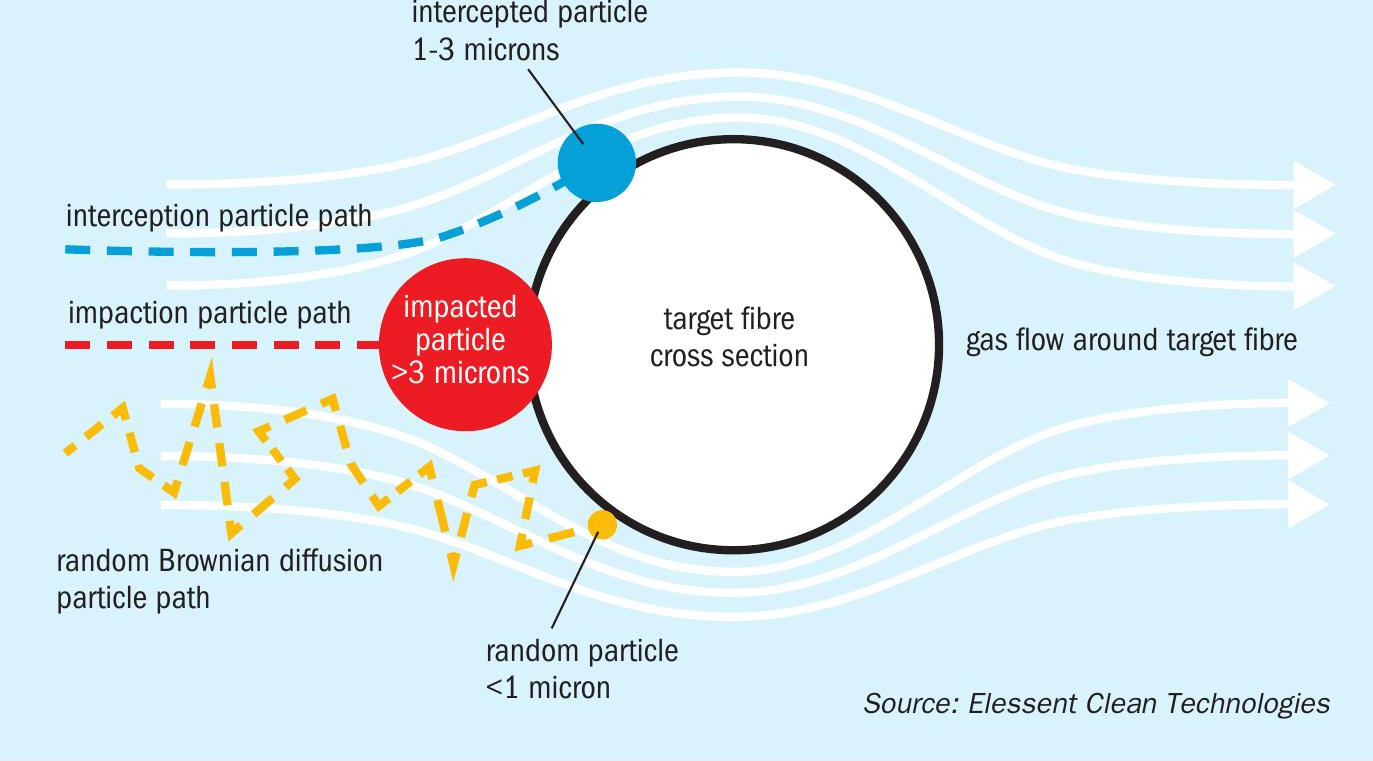
Interception mechanism: The second mist collection mechanism is direct interception. Mist particles collected via this mechanism are intercepted from the gas stream if they cannot ride the streamline between two fibres (or if the particle touches the tangent of a fibre as it passes within the barrier zone between the freely moving gas and the fibre surface, adhering to the fibre by means of weak Van der Waals forces). Consider a particle 1.0 micron in diameter which follows a gas streamline passing within 0.5 micron of a fibre. As the particle attempts to pass the fibre, its tangential fringe will make contact with the fibre, whereupon adhesion as governed by Van der Waals forces will cause the particle to stick to the surface of the fibre and therefore be collected by interception. This mechanism is similar to the action of a mesh filter or sieve. Interception efficiency is largely independent of fibre bed velocity but is most effective for particle sizes greater than 0.5 micron and less than approximately 3 microns.
Brownian diffusion: Impaction and interception are the primary collection methods employed by devices which are designed for removal of larger mists from a gas stream. In order to remove sub-micron mist particles out of a gas stream however, a third mist capture mechanism called “Brownian motion” or “Brownian diffusion” must be utilised. All molecules in a gas stream are in constant, random, thermally induced motion. This molecular motion causes collisions between gas molecules and suspended mist particles. As mist particles are bombarded by surrounding molecules of gas, the momentum exchange causes a randomly oriented “zigzag” effect on mist particle motion. Since these collisions have little energy, this mechanism is only effective for very small particles (typically less than 1 micron) and decreases in intensity as the particle size increases. Therefore, the smaller the particle, the greater its random motion (also known as particle diffusivity) and the more likely an incident particle will collide with a fibre and stick (collect) by weak Van der Waals forces during transit through the fibre bed. This of course assumes that there is enough residence time (low enough velocity) for the random motion to walk the particle into the collecting fibre.
The flow of process gas through a fibre bed is complex and the path the process gas takes through a fibre bed is torturous. Many other factors contribute to determining mist capture including the amount of collected mist retained within the fibre bed at steady state, mist residence time as it passes through collecting fibres, mist properties, fibre bed uniformity, and general fibre bed properties to name a few. Brownian diffusion requires large residence time of a droplet within a fibre bed to allow time for capture, so operation of an impaction fibre bed at high velocities largely diminishes the effectiveness of the Brownian capture mechanism for these devices.
For all types of fibre beds which rely upon these mechanisms, technology provider experience, based on development of semi-empirical models supported by rigorous piloting and field measurements, is critical to accurately predict diffusion fibre bed collection efficiency and operating pressure drop. The MECS field-collected mist sampling data base has over 50 years of mist measurements in support of Brink® fibre bed products and designs.
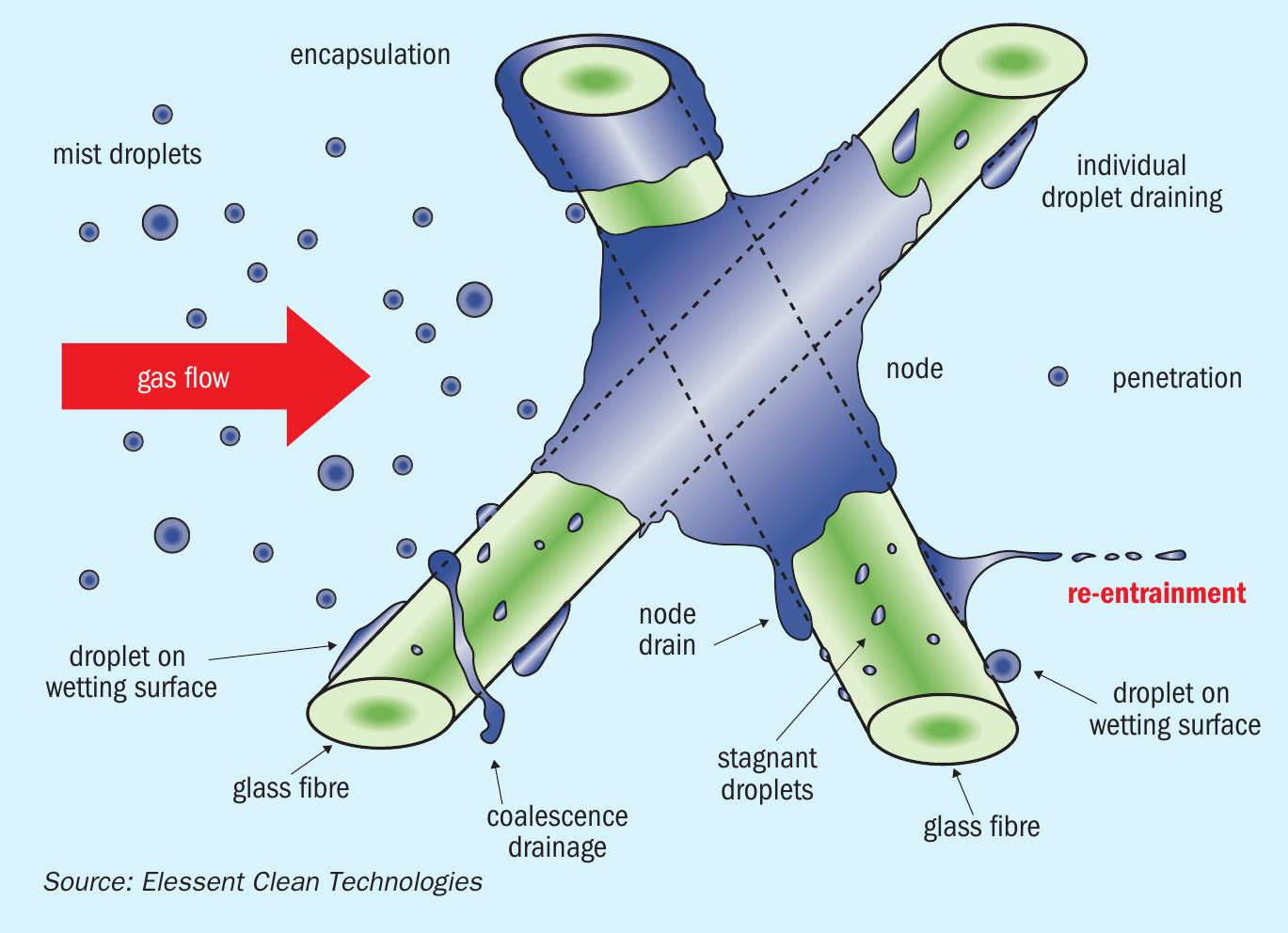
Re-entrainment: It is important to take into account the effect of the gas flow through the fibre beds and the resulting disturbance on liquid contained within the matrix of the fibres within the device. As the gas flows around and past the liquid the drag force and Van der Waals attraction of the liquid to the surface of the fibre establish an equilibrium. If the gas velocity is high enough, the Van der Waals attraction is overcome and at least a portion of the liquid can be sheared by the gas back into the downstream gas flow. Any fibre bed has the ability of this mechanism to degrade performance of the device and if significant enough the resulting overall efficiency of the fibre bed is degraded. This is why it is imperative to use re-entrainment control devices or methods to prevent this mechanism from significantly degrading performance.
Fig. 2 demonstrates liquid appearance and interaction with media in a fibre bed to include representation of reentrainment.
Proper use of impaction technology in acid plants
Mist capture devices frequently found in operating sulphuric acid plants are mesh pads, impaction fibre beds and diffusion fibre beds. Mesh pads and low velocity impaction fibre beds (350 ft/min devices such as the MECS® CS-IP model) are typically found in drying towers (DTs). These devices rely upon the impaction mechanism for capture of larger diameter sulphuric acid droplets emanating from the sulphuric acid saturated tower packing below them in the tower. Fig. 3 shows a typical mesh pad and impaction (CS) fibre bed.
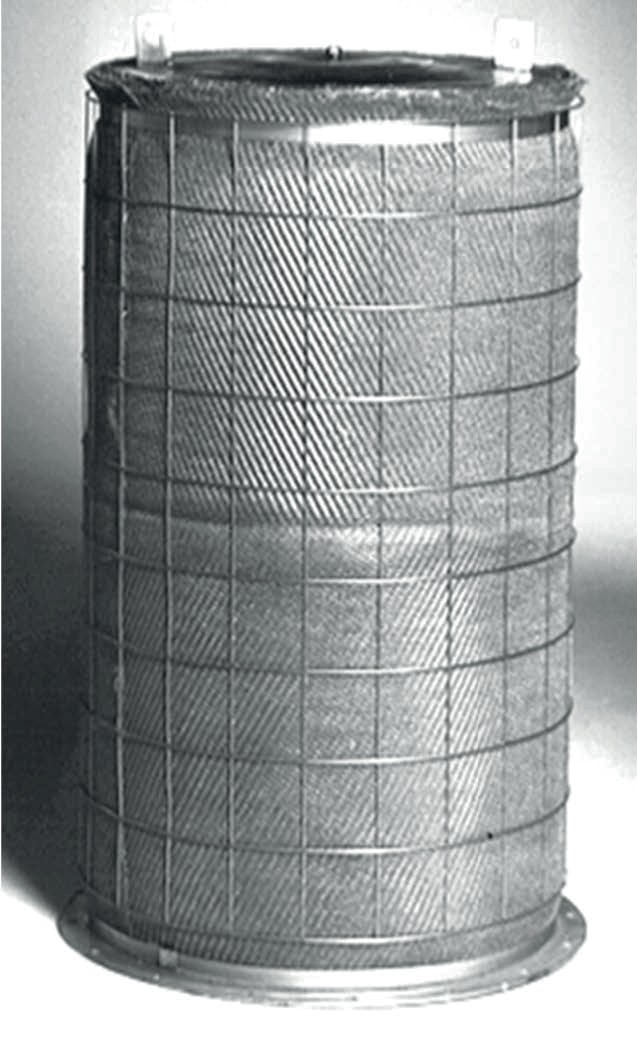
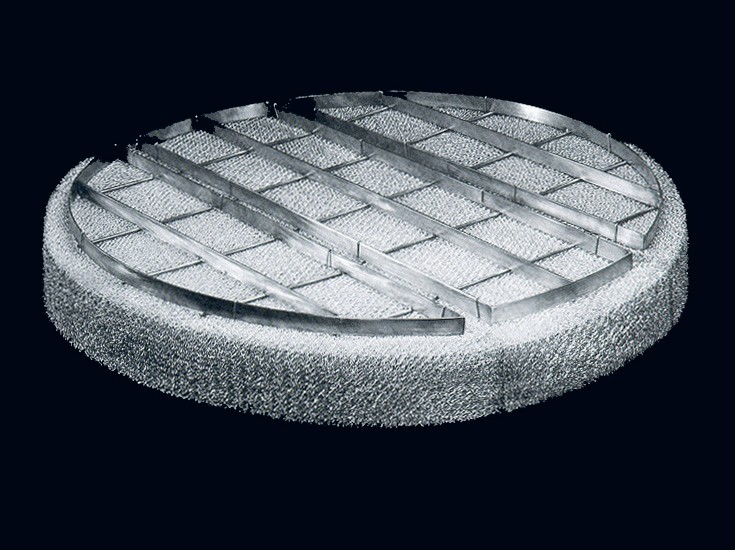
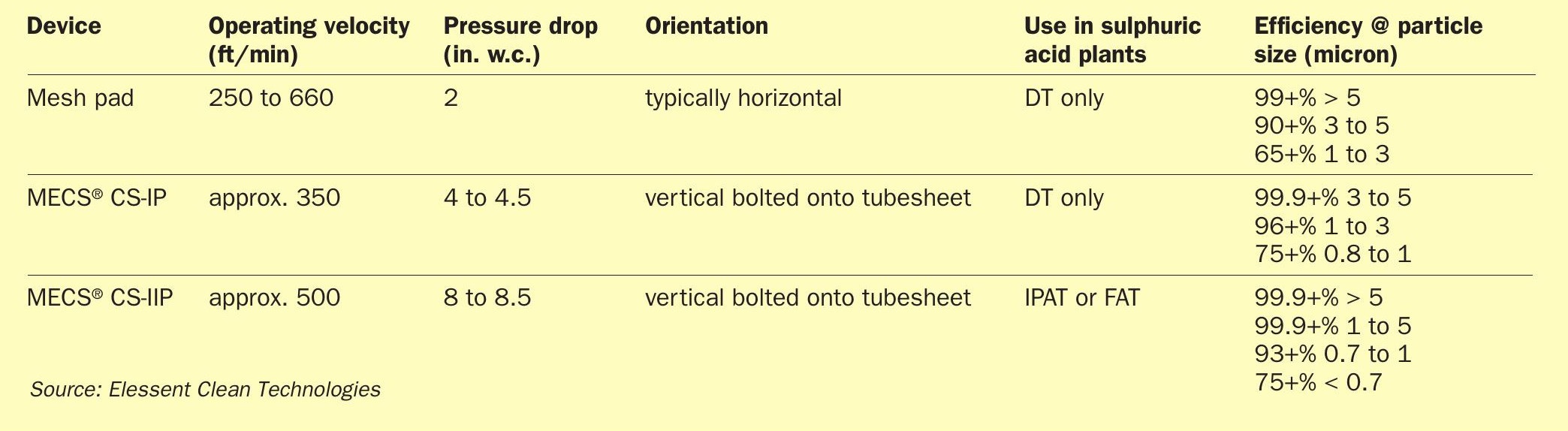
There are other applications for impaction fibre beds in sulphuric acid. Enhancement of MECS’s original impaction technology led to the development of the MECS® CS-IIP product which is used in the final absorption tower (FAT) and operates closer to 500 ft/min. The MECS® CS-IIP product offers some enhancement in the collection of 1-micron sized droplets and is appropriate for superior overall mist control in select applications. For instance, some US and Canadian based sulphuric acid plants use MECS® CS-IIP impaction fibre beds in their interpass (IPAT) towers and many ex-US plants use impaction fibre beds in both their IPAT and FAT towers. A word of caution however is that impaction driven devices are not used in areas where the local or regional emissions regulations have opacity requirements since impaction-driven device efficiency is lower on less than 1-micron sized droplets (which is also the most optically active and thus opacity sensitive region of droplet size). Also, since impaction fibre beds rely upon velocity to achieve adequate capture, pressure drop is device specific and cannot be tailored. At less than 80% production rate (gas velocity), collection efficiency will plummet and there is risk from an emissions standpoint, thus turndown rate with impaction device use is severely limited.
In the case of impaction-based devices, the higher velocity used to drive collection efficiency has a potential drawback: re-entrainment. Thankfully, re-entrainment can be overcome by creative use of materials and with differing composition and density within the fibre bed to allow vertical drainage paths for liquid removal while the gas freely passes through the device horizontally. This is an advantage of MECS impaction fibre bed technology compared to mesh pads used in sulphuric acid service, as the fibre beds operate under a drier state since gas flow through and liquid flow down the fibre bed are not along the same orientation with respect to the collection media.
It is important that these material combinations are thoroughly vetted, as improper design can actually induce worse re-entrainment than a design lacking re-entrainment suppression media. However, even the creative use of these materials has an ultimate limit necessitating additional means to enable pushing impaction bed technology further.
Brink® Prime Impact™
While considering improvement to its existing technology, MECS reviewed the original development data for its MECS® CS-IIP product originally conducted during the 1970s. The data demonstrated higher theoretical efficiency when using impaction fibre beds at higher velocity. However, this came at a trade-off as the developers at the time noted that the amount of re-entrainment was significantly higher than with lower velocity designs. Thus, there was an optimisation struck between the velocity through the bed and degree of re-entrainment generated giving way to the overall collection efficiency measured. Based on this understanding, MECS was able to consider packing alteration using materials in different forms and/or new materials of construction to realise re-entrainment reduction improvements to reduce exit emissions at higher bed velocity without the negative side effects of re-entrainment. These improvements culminated in the development of a new impaction fibre bed product offering – Brink® Prime Impact™ (Brink® PI).
PI impaction elements use a proprietary combination of fibres and re-entrainment prevention techniques to enable operation of these beds with a higher velocity limit without suffering additional pressure drop or suffering from poorer collection efficiency overall. One of the interesting aspects of this product given the mix of layers contained within the device, the pressure drop is consistent with operation of the MECS® CS-IIP even though it is designed to operate at 20% higher bed velocity. Effectively this means that fewer fibre beds can be used for the same pressure drop at overall improved droplet removal from the gas stream as compared to the previous high velocity impaction products. A mechanical review revealed that when using 20% fewer Brink® PI in an IPAT or FAT as compared to MECS® CS-IIP elements, the cost savings for a new tower can be in excess of 5% from reduction of the number of beds alone. Alternatively, these Brink® PI devices can be used in existing impaction installations that have undergone rate expansion and there is insufficient space for additional elements.
Field trial results of Prime Impact™
After some internal prototyping to determine fabrication details, in 2020 MECS moved forward with production of field prototypes to enable real-world operational comparison to MECS® CS-IIP impaction fibre beds in a client site. Fig. 4 shows a picture of the new Brink® Prime Impact™ bed.
J. R. Simplot (Pocatello, Idaho, U.S.A.) had an existing installation of MECS® CS-IIP fibre beds in their IPAT tower and were looking to replace their old fibre beds with a new set due to high pressure drop buildup following years of service. After some initial discussions concerning the new product and its capabilities, Simplot agreed to replace the older MECS® CS-IIP elements with a new set of Brink® PI impaction fibre beds and allow MECS to perform on-site testing using a modified version of US EPA Method 8 complete with Andersen (cascade-style) Impactors for determination of inlet and outlet mist loading and particle size distribution
The Brink ® PI fibre beds were installed during a routine maintenance shutdown at J. R. Simplot in the fall of 2020 and testing was conducted in early summer 2023. During the run from 2020 to 2023, the client experienced excellent stick test results (Fig. 5), reduction in overall acid carryover to downstream ductwork and pressure drop consistent with previously installed MECS ® CS-IIP elements at around 8-inches w.c.
The MECS modified version of US EPA Method 8 enables measurement of acid mist, acid vapor and sulphur trioxide. The modification entails the use of an Andersen cascade impactor that provides a mist particle size distribution as opposed to a single mass loading. In this way, it is possible to assess the performance of a mist removal device for particles ranging in size from 0.1to beyond 10-micron in diameter. It is critical to know the performance capabilities of emission control equipment to meet design criteria for different chemical processes and applications. Such information can also be useful for troubleshooting events. Analysis of the data revealed a few interesting facts:
l J. R. Simplot’s IPAT gas to the inlet of the mist eliminators had a lower mist load than expected – only around 16.4 mg/ACF. MECS normally expects up to 50 mg/ACF as the inlet mist loading to fibre beds in IPAT installations based on 60 years of sampling in this service. The value measured at Simplot is reflective of excellent maintenance and operation protocols.
l The performance on submicron droplets was excellent as compared to impaction fibre beds, including the MECS ® CS-IIP, and surpassed the theoretically expected performance (Fig. 6).
l Pressure drop of the Brink ® PI fibre beds was consistent with expectation at 7-inches w.c., even after nearly three years of operation where an increase in pressure drop would be expected due to the buildup of sulphates and any remaining dust and dirt which makes it through upstream catalyst passes.
Fig. 6 shows a logarithmic plot of the efficiency versus particle size and the resulting efficiency achieved at the J. R. Simplot facility as recorded during sampling work performed in June 2023.
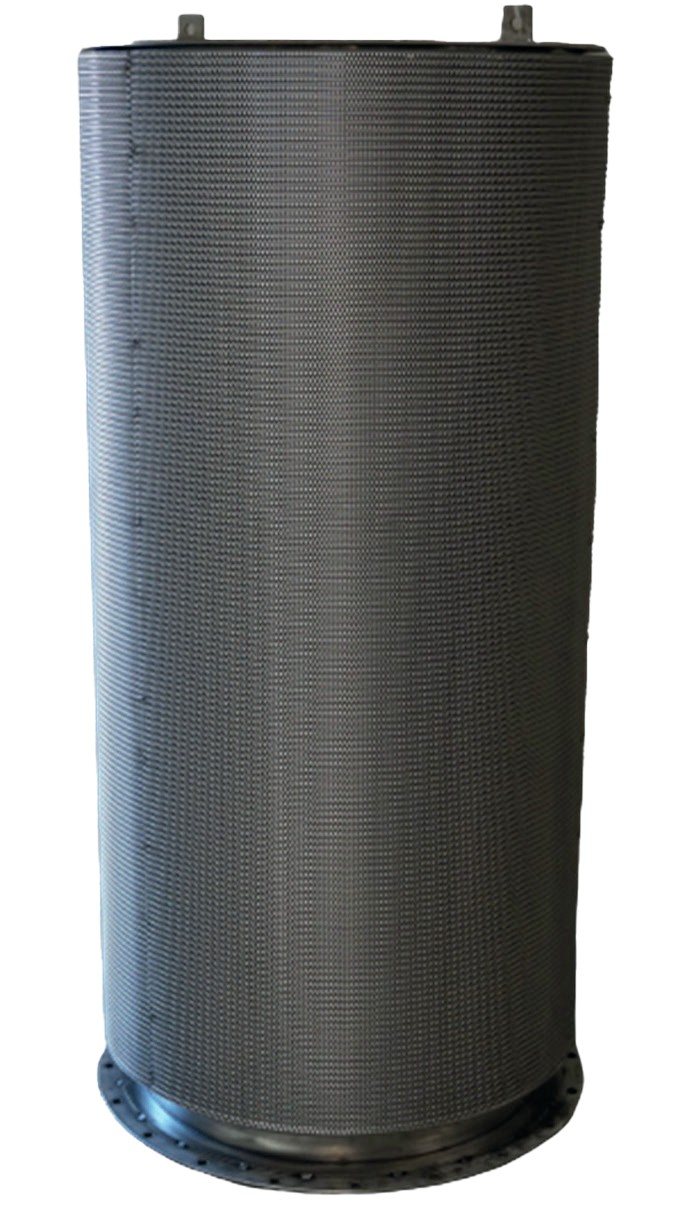
Design options and case studies
Whenever a new technology is introduced to the market, it is imperative to consider the implications of using the advancement in either new equipment or existing operations. Table 2 demonstrates design options which are available to provide a perspective on the new Brink ® PI impaction beds and their capabilities. For this example, MECS first considered the implications on replacement of MECS ® CS-IIP fibre beds in an existing installation where equipment limits are pushed and then what these new Brink ® PI beds can enable for the design of a new tower. The data is based on an IPAT in an average sized 2,500 s. t/d sulphur burning sulphuric acid plant at sea level. The gas flow is 111,471 ACFM (189,389 Am 3 /hr) at a temperature of 176°F (80°C) and 75” w.c. (1905 mm w.c.) static pressure at the inlet to the impaction beds.
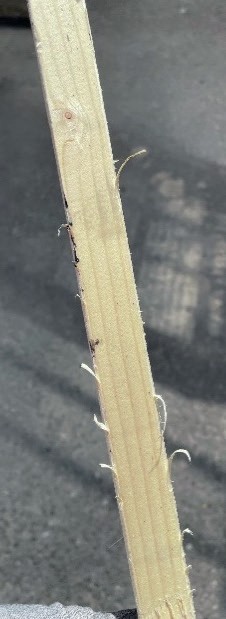
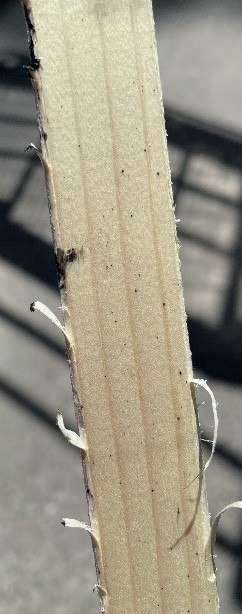
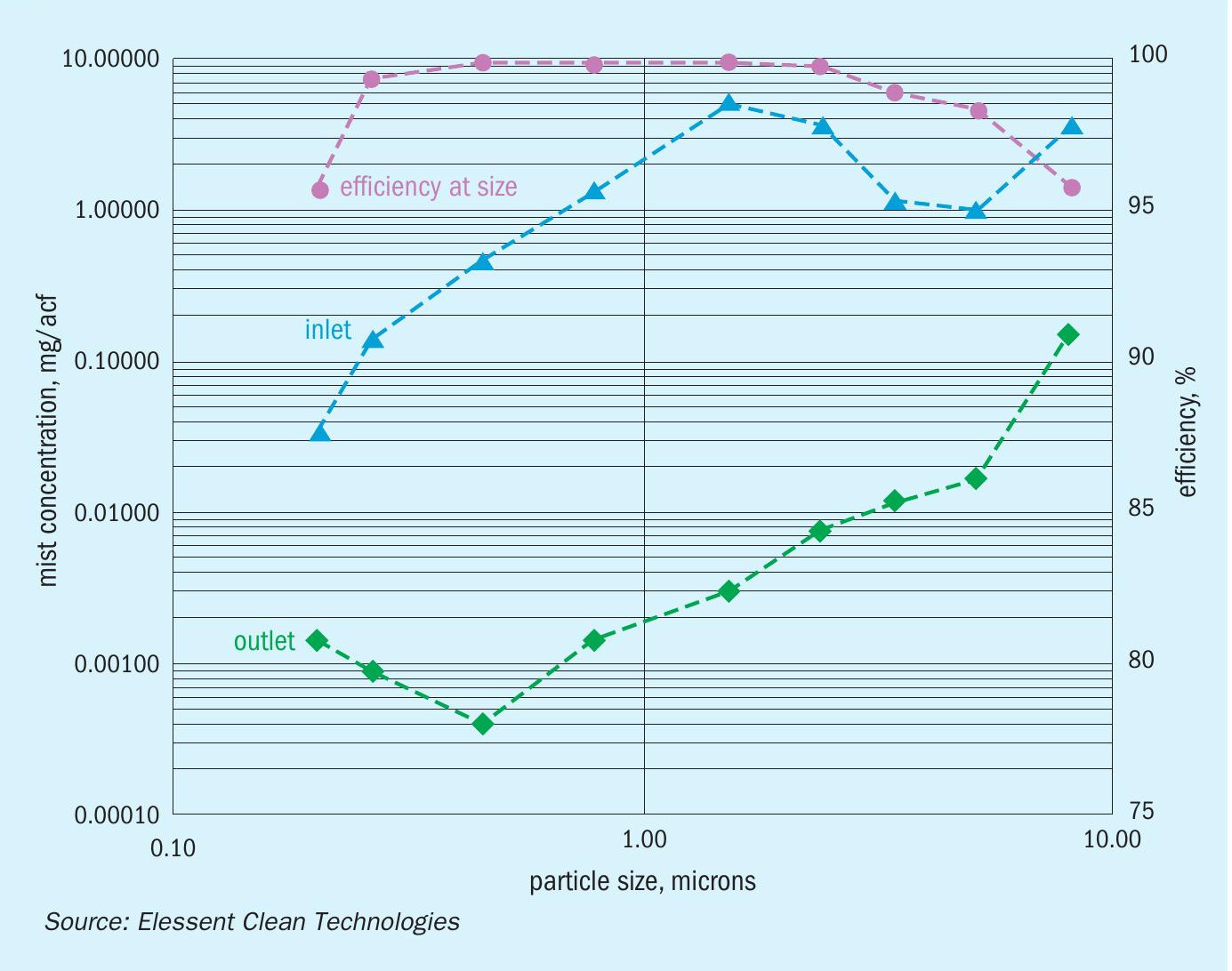
As presented in Table 2, the use of Brink® Prime Impact™ fibre beds offers a wide array of advantages for both existing plants looking to expand production capability and for new plants which are attempting to minimise tower cost. The Brink® PI fibre beds offer a lower pressure drop at the same gas flow rate as their MECS® CS-IIP predecessors, so there is no operational drawback from an energy consumption standpoint when considering pressure margin required to push the gas through the plant. Since overall efficiency and re-entrainment of the Brink® PI fibre beds is superior to MECS® CS-IIP fibre beds (see Fig. 7), there are no operational issues to consider. When considering the possibility of replacement of existing MECS® CS-IIP fibre beds with Brink® PI there is a great advantage to Brink® PI use if the client is considering a plant expansion in the future as well. For new plants, the smaller diameter tower when using Brink® PI beds (since fewer beds are required) enables savings in tower cost. Overall, the Brink® PI product offers a significant advantage in the sulphuric acid market.
The following cases highlight the advantages of Brink® PI fibre beds.
Case 1 – existing plant
A client has pushed their production over the years beyond their original boilerplate and as a result the 9 MECS® CS-IIP elements installed in their IPAT operate at 11 inches w.c. (271 mm w.c.) upon installation. The bed velocity is beyond what MECS recommends and there are plans for modification to their IPAT to add additional elements to rectify. While they have been running at higher rate, they have noticed increased downstream ductwork corrosion, heat exchanger vestibule drainage and corrosion, and fourth pass catalyst destruction. MECS evaluates the process data and determines that the existing MECS® CS-IIP elements can be replaced with 9 Brink® PI impaction beds and operate with much reduced acid mist carryover and lower pressure drop at 8 inches w.c. (203 mm w.c.). Not only does this save money in reduction of downstream catalyst, ductwork and heat exchanger repairs but the 3 inches w.c. (76 mm w.c.) savings directly translates to around $40,000 – $60,000 per year in energy savings for plant blower operation.

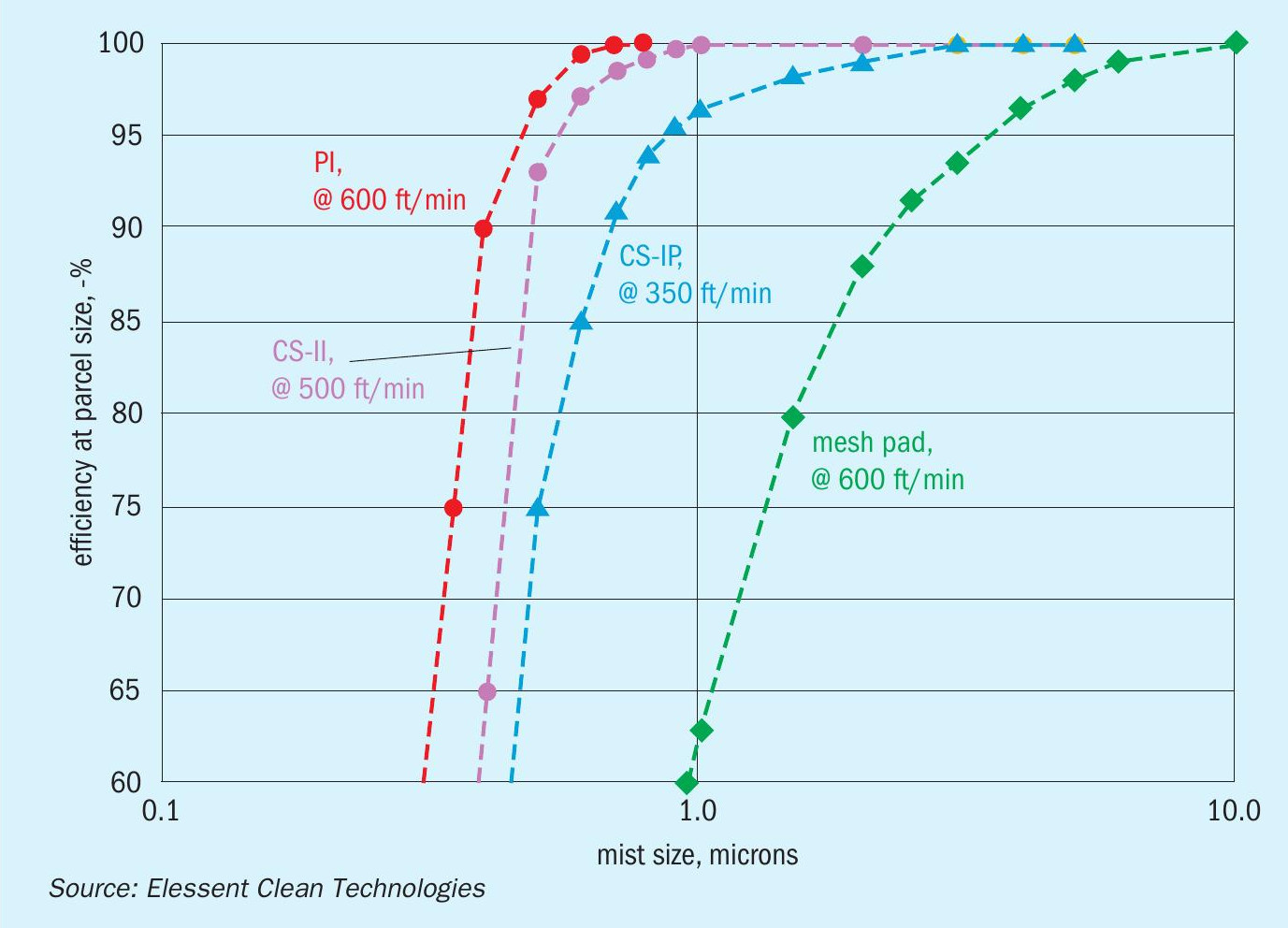
Case 2 – new tower
This case features a client who is considering a tower replacement. They have used MECS® CS-IIP elements in prior towers with good success. While evaluating options they are intrigued by the possibility that Brink® PI offers better efficiency at the same pressure drop as MECS® CS-IIP elements with up to 25% fewer beds. Additionally, the option of making the tower doghouse smaller with the 5+% savings in capital expenditure is appealing. They also consider the fact that fewer elements mean fewer bolts securing the elements to the tubesheet, fewer gaskets and an easier installation for better downstream ductwork, heat exchanger and catalyst protection from the effects of carry-over sulphuric acid droplets coming from the IPAT.
Conclusions
Impaction elements are commonly used in inter-pass absorption towers and final absorption towers to remove entrained sulphuric acid, especially when stack opacity is not regulated or operators are satisfied with the droplet removal efficiency. MECS has developed a new impaction-based mist eliminator called Brink® Prime Impact™ , which offers equivalent or improved efficiency at higher throughput and the same pressure drop as traditional impaction beds, resulting in the ability to debottleneck existing towers or design new or replacement towers with smaller diameters, thus reducing investment cost. Brink® Prime Impact™ elements have performed well in industrial service for over 3 years, showing clean stick tests and excellent mist removal at the initial installation, an inter-pass absorption tower in the United States.