Sulphur 410 Jan-Feb 2024
31 January 2024
New low-density titania catalyst for improved sulphur recovery
TITANIA CLAUS CATALYSTS
New low-density titania catalyst for improved sulphur recovery
Axens has developed a new titania-based catalyst named CRS 41, which has a much larger porosity than its renowned predecessor, CRS 31 catalyst. Thanks to an improved catalyst manufacturing process and a new recipe, the porosity of CRS 41 has been increased while preserving the mechanical resistance for loading, allowing customers to optimise their capex by either reducing the Claus reactor size or loading volume of TiO2 catalyst.
Increasingly stringent environmental legislation requires maximising sulphur recovery yields. That explains the growing role of titania (TiO2 ) catalysts in SRUs, which is accompanied by the arrival of high-activity tail gas treatment catalysts on the market. Titania-based catalysts are used because they can efficiently convert all sulphur species to elemental sulphur, even under conditions that deactivate conventional alumina catalysts. Furthermore, the use of titania facilitates the conversion of COS and CS2 at low temperature, which is essential if hydrocarbons are present in the acid gas feed. Axens’ titania-based catalyst, CRS 31, has extensive commercial experience with thousands of tonnes loaded worldwide, and is considered to be the benchmark titania catalyst. It contains high amounts of TiO2 , which is very active towards hydrolysis of sulphided species. However, not all the titanium dioxide of CRS 31 contributes to the catalytic activity, since not all of it is accessible to the gaseous reagents.
From the standard 3.6 mm diameter extrudates of CRS 31 to smaller diameter extrudates and low diameter granules, performance can be critically improved. As gases move slowly toward the inner areas of the extrudates, the catalyst’s core sees a low amount of gas. Inner parts of the catalyst thus contribute poorly to the overall performance. The accessibility of these parts can be strongly favoured by shortening the pathway of gases towards the catalyst’s core, i.e. by reducing the particles size. In addition, the minimum contact time required to reach a minimum of 95% conversion can be drastically reduced (less catalyst in the reactor) with smaller particles, as illustrated in Fig. 1. Further size reduction has little impact once all the material in the catalyst is fully active. Compared with 0.5-2 mm granules considered 100% active, CRS 31 needs a sixfold longer contact time to reach the same performance. These results suggest that about only one sixth (≈17%) of the CRS 31 catalyst is actually performing at maximum activity.
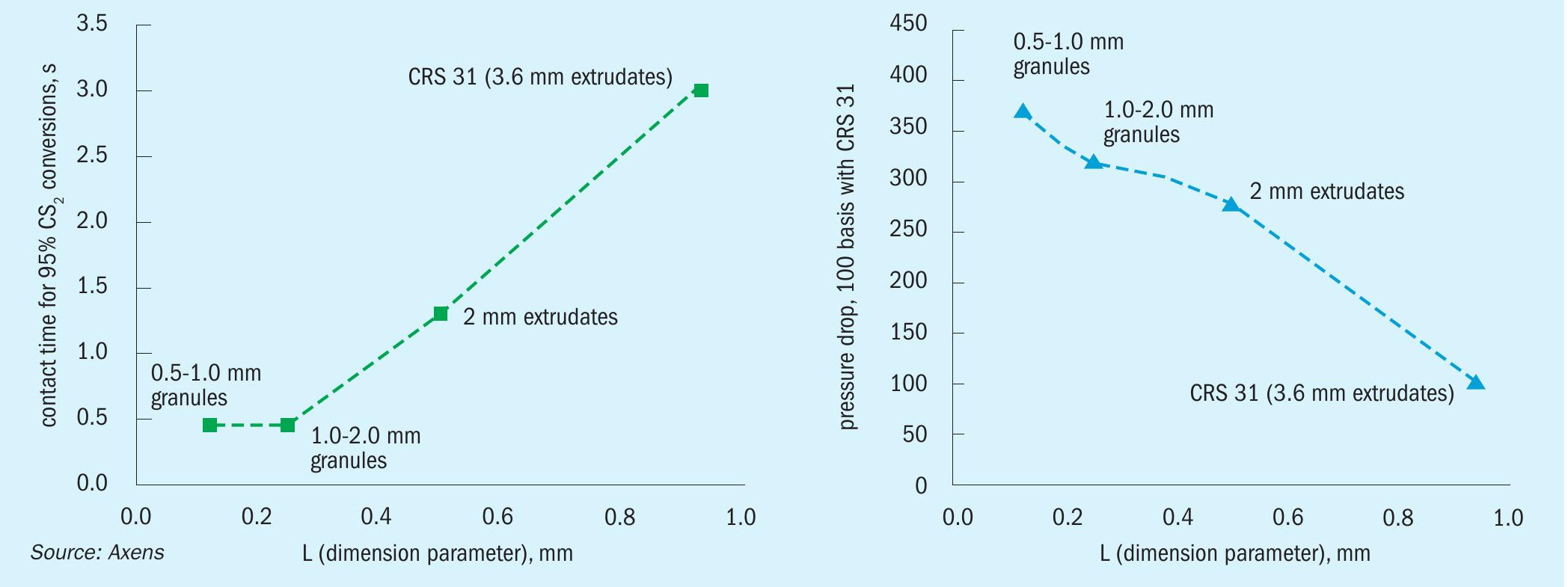
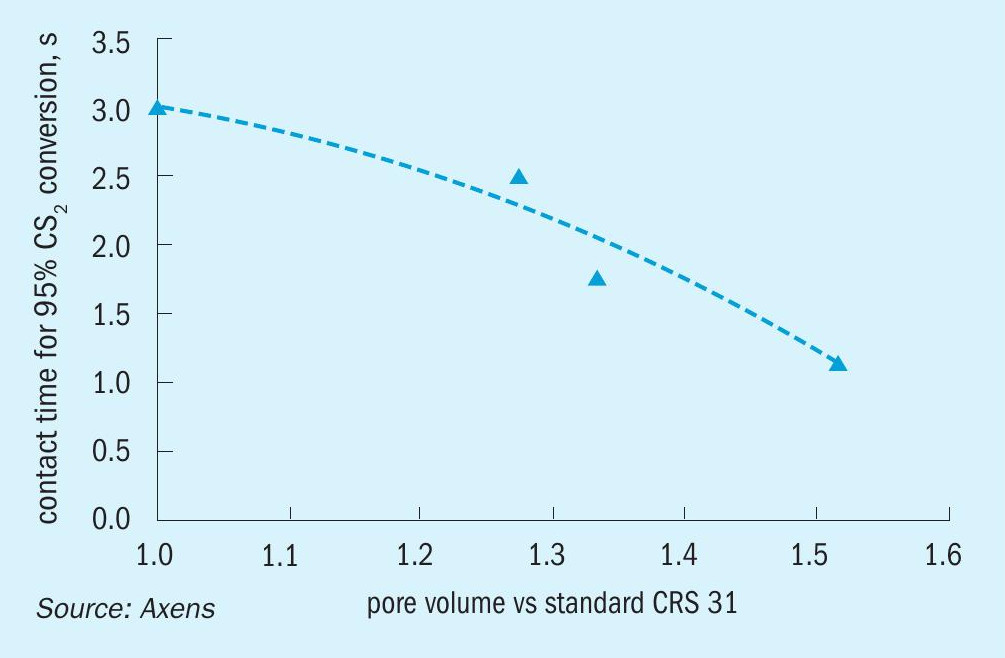
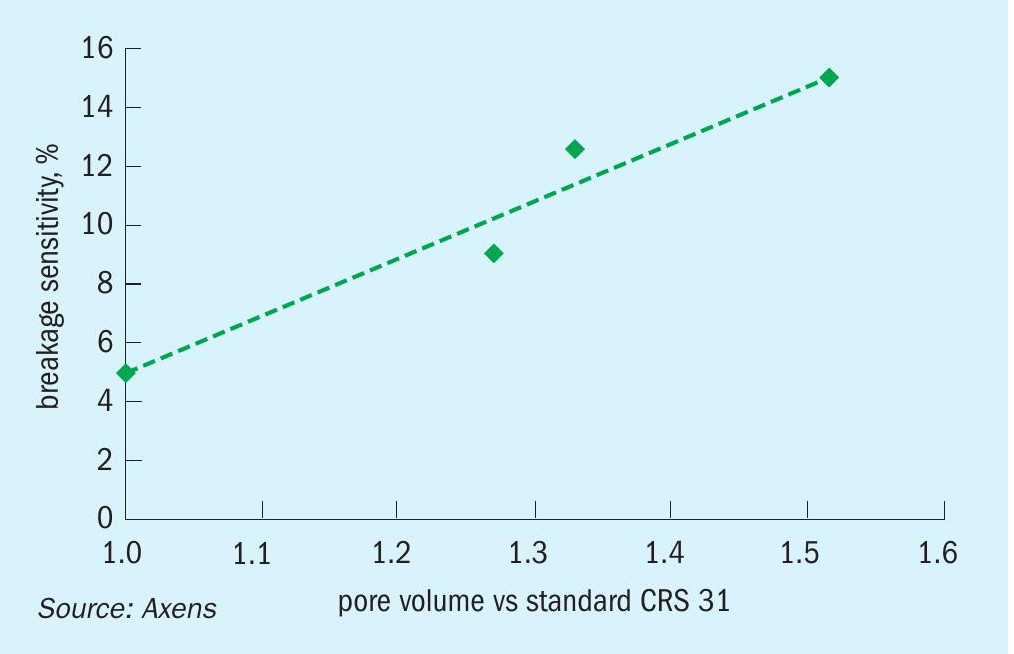
However, catalyst size reduction has a huge drawback in terms of pressure drop. Indeed, reducing the diameter of the extrudates by a factor close to two triples the pressure drop generated by the catalyst bed, which would lead to hydraulic issues.
Another possibility to achieve better performance when catalyst activity is limited by gas diffusion is to increase the accessibility to the active sites by increasing the catalyst porosity and/or its outer surface area (with more complex shapes). The increase of porosity results in larger “roads” inside the catalyst which help gases access the active sites1. A 95% CS2 conversion could be achieved with half the amount of titania in the converter when the pore volume is increased by 50%. From results shown in Fig. 2, such catalyst achieving 95% CS2 conversion at a contact time of 1.25 seconds would see at least 40% (2.5 times less active than 0.5-2 mm granules) of its titania working at maximum activity. It should also be noted that increasing the titanium dioxide content will have no significant impact on performance since only a low content of TiO2 operates at full activity.
However, Axens’ experience has shown that major drawbacks can come from the increase of porosity e.g., the catalysts show critical brittleness.
Claus catalysts are sock-loaded in SRU converters and may fall from a height of several metres (from the hopper outlet to the flexible loading sleeve outlet). When extrudates hit hard surfaces (like ceramic beads, steel or catalysts), the shock generates shards. Even if these shards are highly active, they will also generate pressure drop.
Axens developed a test to check the resistance of Claus catalysts to free falls, where extrudates are projected on a steel plate using compressed air. The method is derived from ASTM 8353, where catalysts are dropped from a height of 7.6 m through a pipe on a steel plate. In this protocol, the use of compressed air enables to the size of the setup to be reduced while mimicking the shock undergone by the extrudates falling freely from a height of 5 m, which is a typical fall height during actual sock loading. The sensitivity of catalysts to breakage is then calculated as the volume of extrudates broken from the shock (excluding shards and fines). In the case of catalysts with higher pore volumes than CRS 31, the brittleness monitored with the breakage sensitivity becomes critical. As shown in Fig. 3, the breakage sensitivity is tripled when the pore volume is 50% higher than that of CRS 31. The breakage of extrudates generates several shards per extrudate and the pressure drop rises accordingly.
An increase of porosity favours an increase in the breakage sensitivity of extrudates. Observation of the inner parts of extrudates via scanning electron microscopy (SEM) reveals that cracks are already present inside the extrudates with high porosity before the breakage test. Such cracks on the extrudates microstructure are totally absent in CRS 31 (see Fig. 4).
Any shock from a free fall leads to the propagation of these cracks and favours the generation of shards.
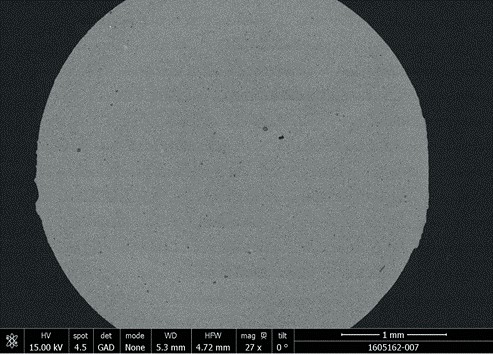
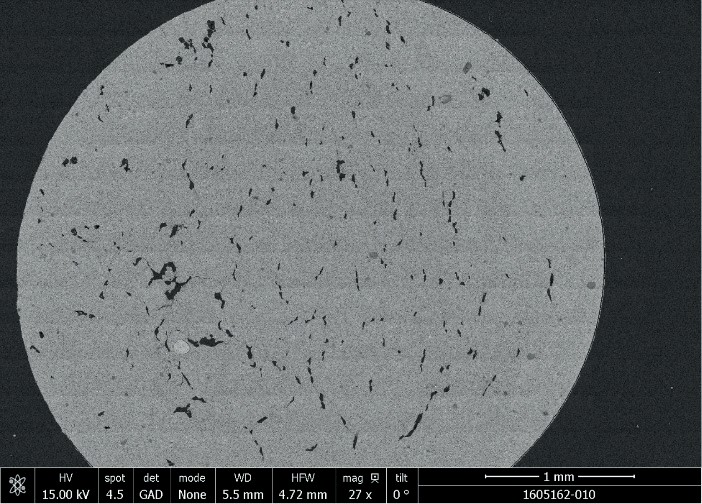
Several parameters can be optimised to improve the performance of titania Claus catalysts. This study shows that reducing the catalyst dimensions or increasing its porosity highly benefits the product performance. However, major drawbacks result from these parameter changes since pressure drop will rise dramatically with the reduction of catalyst dimensions and/ or with the shards generated during the loading operation of too porous catalysts. The development of Axens’ in-house testing methodology to measure breakage sensitivity of Claus catalysts has helped to target catalyst improvement pathways while keeping critical mechanical properties under surveillance.
Development of new low-density titania-based Claus catalyst
When making titania extrudates, scale-up is critical because the mechanical and textural properties can only be assessed at an industrial level. Several operating conditions validated at pilot scale cannot be fully transferred at industrial level. Since the launch of CRS 31 in 1981, Axens has accumulated significant experience on scale-up issues. As a matter of fact, Axens is able to shape some titania supports at the pilot scale with exceptional textural properties associated with good mechanical resistance. However, when applying the pilot recipe on the production line, those outstanding titania extrudates cannot be fully reproduced because of loading densities that are too high or due to insufficient mechanical properties.
The use of calcium sulphate as a binder in Claus titania catalyst has been previously reported to be beneficial on crush strength and catalyst stability under operation2 . This binder improves the mechanical strength of titanium oxide extrudate, which would be too brittle without it. As reported above, the beneficial effect of this binder is limited when high performance catalysts are targeted.
Consequently, Axens decided to develop a new generation Claus titania catalyst – CRS 41 – to run an extensive study directly at its production line. It is the first time Axens has followed such a method for an extrudated catalyst. The workshop was devoted to the new CRS 41 for a couple of months. Manufacturing operating conditions were studied thoroughly by a versatile team of manufacturing and development engineers and data scientists. New additives selected by molecular modelling by Axens’ R&D teams were used.
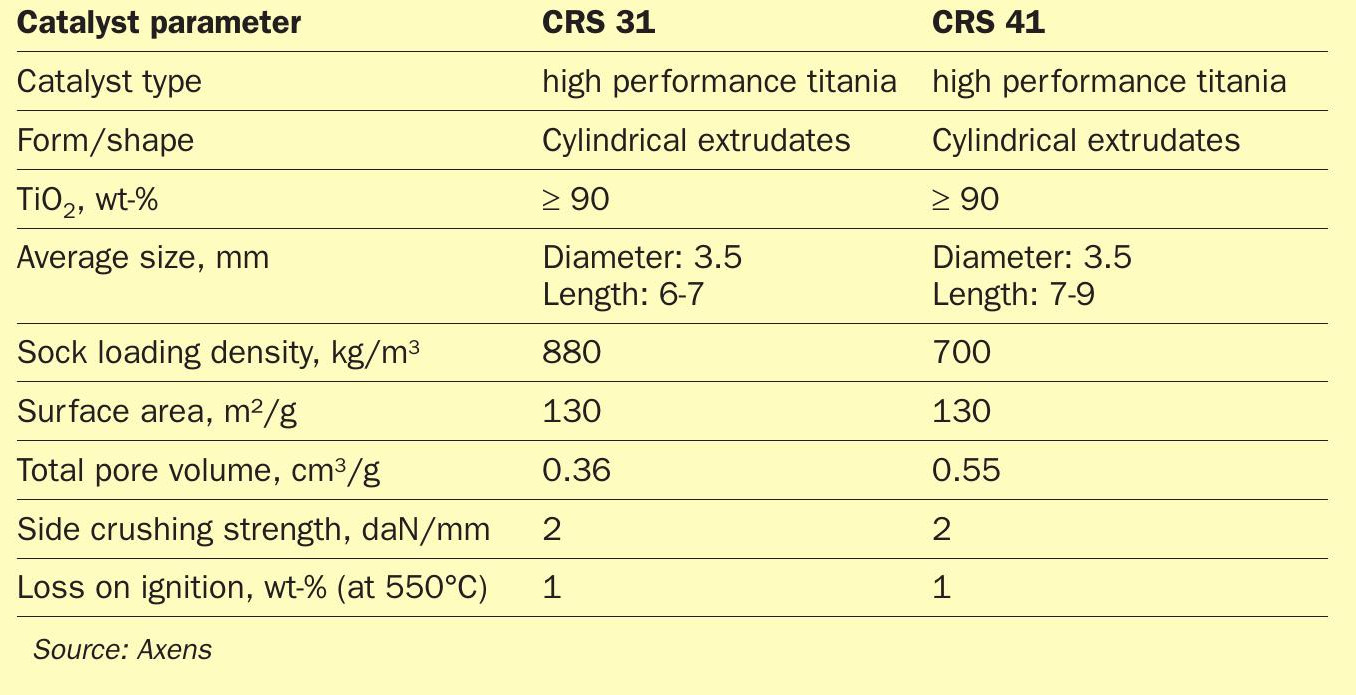
The use of Axens’ production line was mandatory to find the optimal textural properties in association with satisfying mechanical properties. A new set of operating conditions and a new recipe were identified to manufacture this new titania catalyst, CRS 41.
Table 1 compares the key specifications of CRS 31 and CRS 41.
Porosity
CRS 41 is a highly porous TiO2 catalyst. CRS 41 has a total pore volume of 0.55 cm3 /g compared to 0.36 cm3 /g for CRS 31. It is worth noting that the macroporous volume of CRS 41 (pores of larger than 0.1 µm) is four times higher than CRS 31, as shown in Fig. 5.
The benefits of increased macroprous volumes on the Claus activity of alumina has been previously reported2,3 . The proposed explanation to this phenomenon is that larger pores tend to ease the diffusion of the product of the Claus reaction (S6 and S8 molecules) out of the porous structure of the catalyst. It is anticipated therefore that the performance of CRS 41 will be better than CRS 31 on a weight basis.
Surface area
In heterogeneous catalysis, the chemical reaction takes place at the interface between the gaseous reagents and the solid catalyst at the catalyst surface. Hence, the specific surface area is a critical parameter. CRS 31 and CRS 41 exhibit comparable high surface areas of typically 130 m²/g.
Density
CRS 41 is produced with a sock loading density of 700 kg/m3 , much lower than that of CRS 31 (880 kg/m3 ). The reduction in density allows a given reactor volume to be filled with a lower weight of catalyst, allowing cost savings. Importantly, this reduction in density does not have a negative impact on the performances of the catalyst on a volume basis. The performance of CRS 41 is actually higher than that of the same volume of CRS 31.
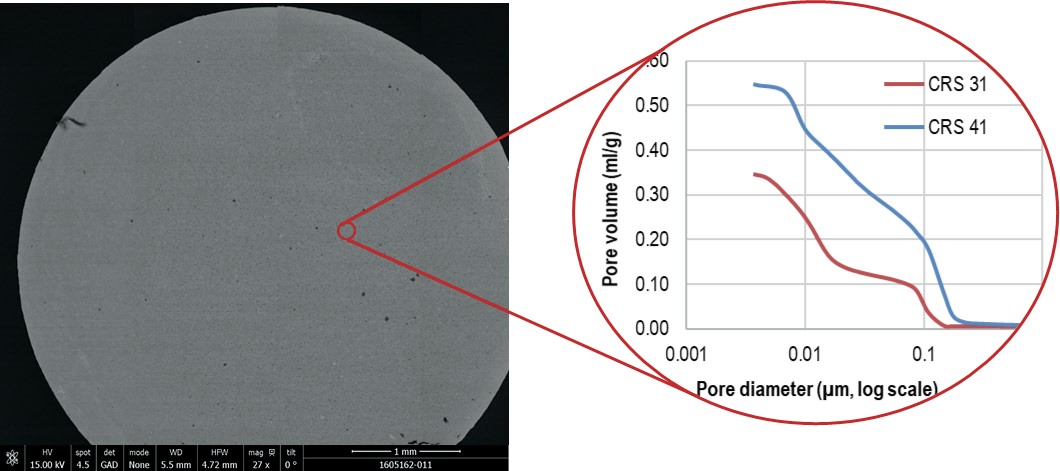
Catalytic conversion performance evaluation
Claus conversion
A pilot test was carried out to compare the performance of CRS 31 and CRS 41 in terms of H2 S conversion. This experiment was conducted under specific conditions at a temperature of 320°C (simulating first Claus reactor operations) and of 240°C (simulating second Claus reactor operations). The test utilised a mixture comprising H2 S, SO2 , and H2 O with concentrations of 2, 1, and 30 mol-% respectively. The results of the test revealed that both catalysts exhibited comparable performance in their ability to convert H2 S. The result of the test is provided in the Fig. 6.
COS and CS2 hydrolysis
The pilot test was conducted under specific conditions, at a temperature of 310°C, using a mixture of H2 S, SO2 , H2 O, and CS2 at concentrations of 8, 4.5, 30, and 0.5 mol-%, respectively. These conditions were selected to simulate real-world operating conditions and provide accurate results.
The performance of the catalysts was measured through the conversion of CS2 . The pilot test results in Fig. 7 show that CRS 41 requires less contact time to reach a desired conversion of CS2 .
Cost effectiveness
Utilisation of the new catalyst CRS 41 featuring a lower density, has the potential to bring a significant benefit: an improved cost-effectiveness. Indeed, for a given volume of catalyst, CRS 41 allows customers to reduce their expenses on titanium dioxide catalysts at every turnaround.
With CRS 41, customers can also optimise their capex by either reducing their Claus reactor size or the loading volume of TiO2 catalyst, without compromising the overall performance.
Conclusion
Axens has developed a new titania-based catalyst named CRS 41, which has a much larger porosity opening than the renowned CRS 31. Thanks to improved catalyst manufacturing and the new recipe, the porosity of CRS 41 has been increased while the required mechanical resistance for loading is preserved.
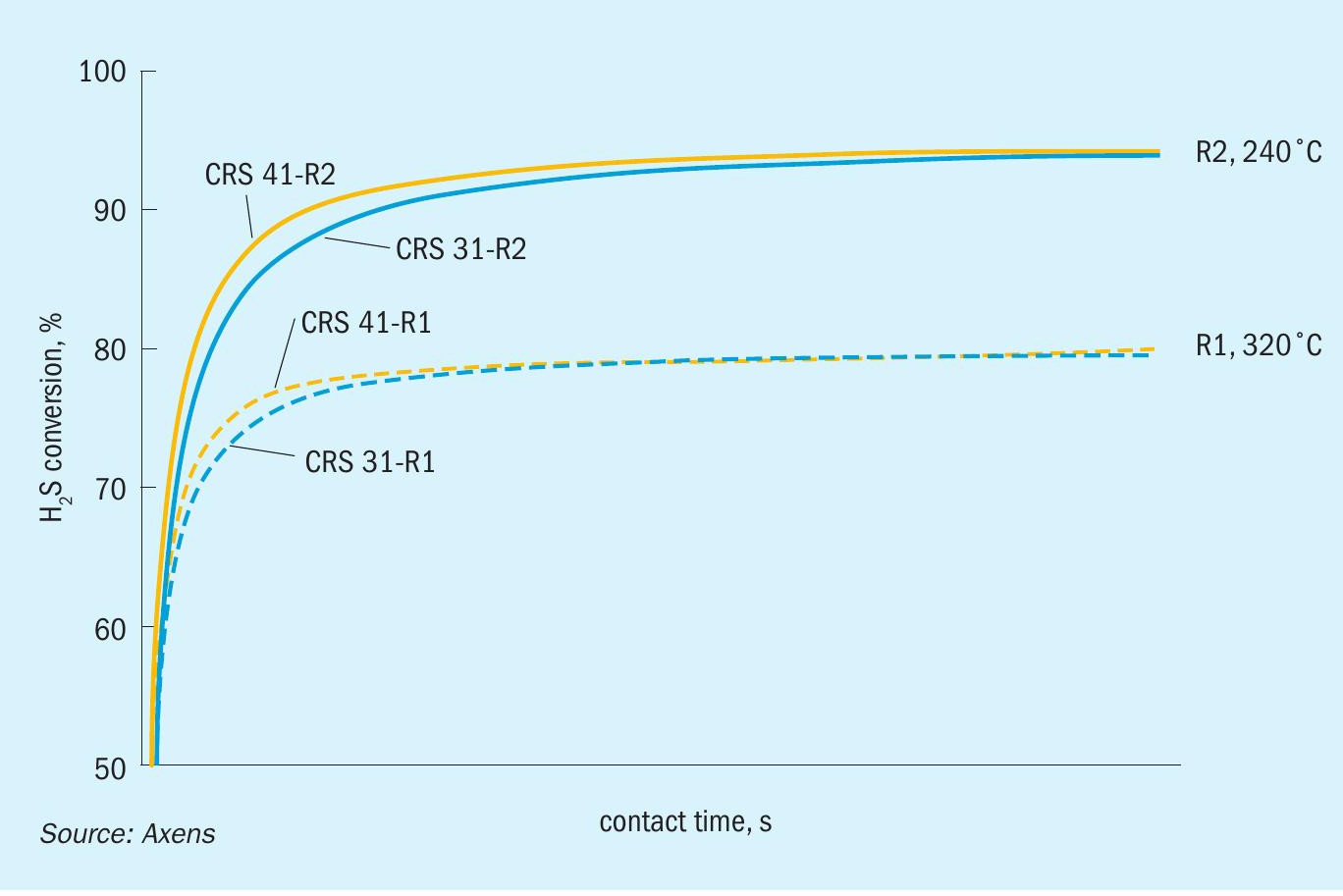

The large porosity of CRS 41 results in a significant improvement in product performance, allowing customers to achieve higher COS/CS2 conversions by reducing the reactor size or the titania requirement by 10%. The new CRS 41 features a reduced sock loading density of 700 kg/m3 , which makes it around 20% lighter than CRS 31, for a more sustainable use of the TiO2 resources. Thus, the cost-to-fill with CRS 41 is more attractive without compromising the pressure drop and the performance.
Acknowledgement
Thanks to Aurore Higon, Adrien Goigoux, Jérémy Thome and all manufacturing staff of Axens’ Salindres plant.
References