Fertilizer International 518 Jan-Feb 2024
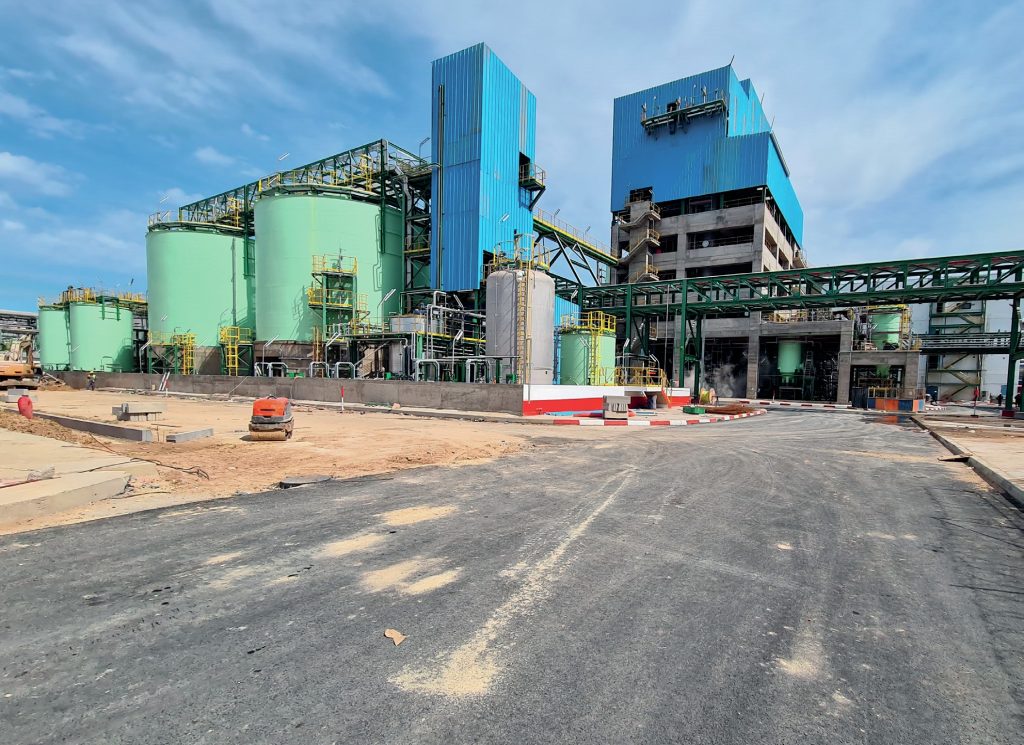
31 January 2024
Phosphates project listing 2024
PROJECT LISTING
Phosphates project listing 2024
Fertilizer International presents a global round-up of phosphate rock, phosphoric acid and finished phosphates projects.
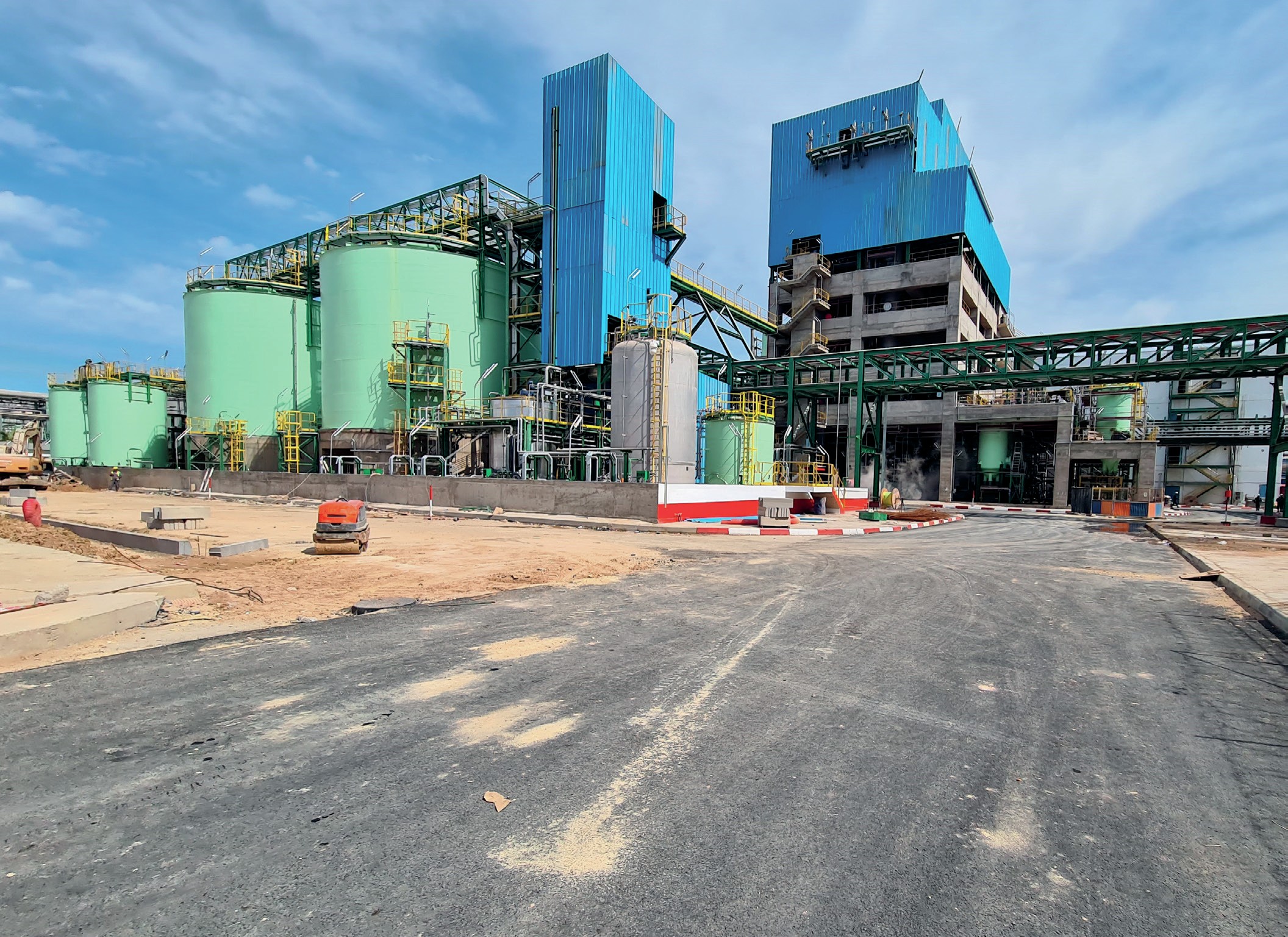
Phosphate rock*
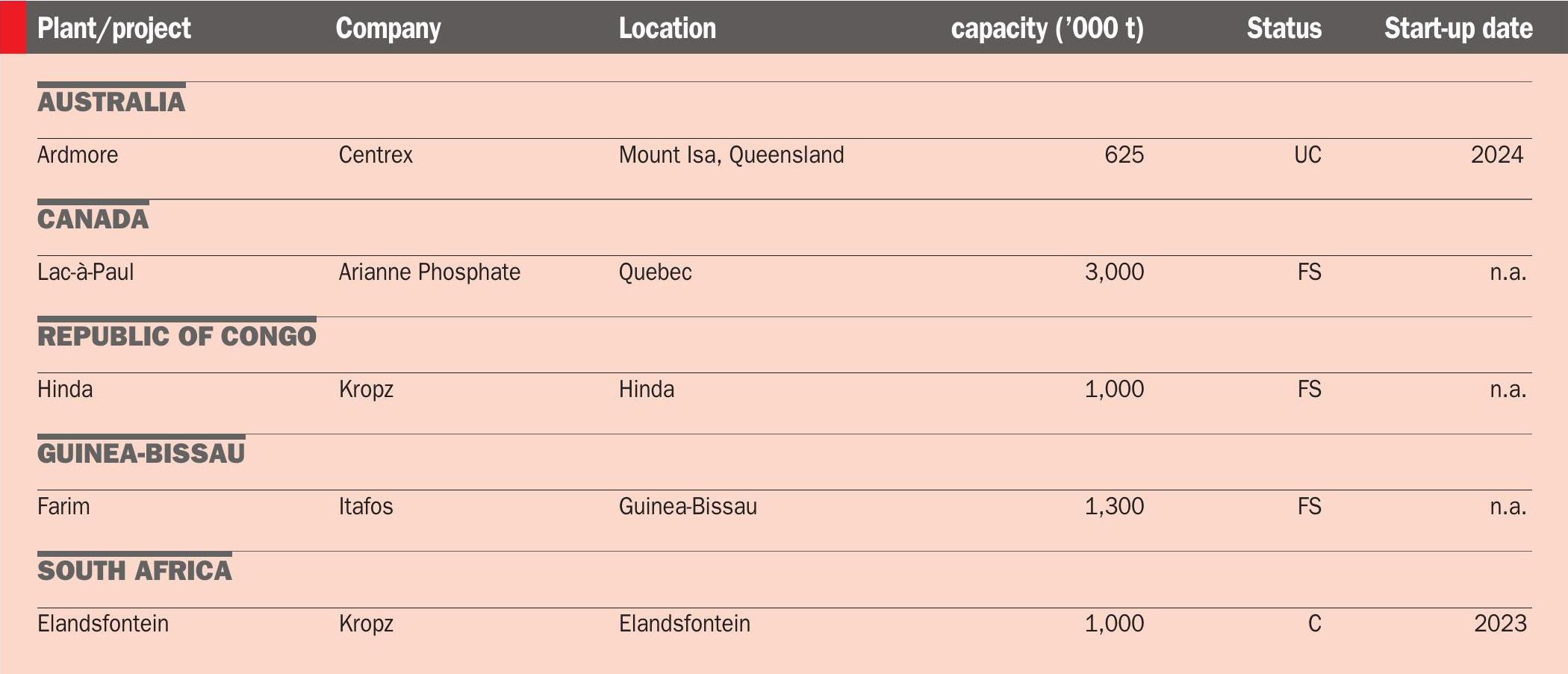
*Excluding China. Standalone, non-integrated projects only.
At present, there are tens of junior phosphate mining projects globally. However, only capacity developments with a published feasibility study are listed here. In general, these projects have yet to secure the necessary finance and, consequently, none have committed to a firm construction schedule and start-up date currently. Africa, Australia and Canada are undoubtedly the locations with the most potential for virgin phosphate rock projects – although large uncertainties over individual projects and their timescales remain. OCP Group is, however, pressing on with ambitious plans to increase phosphate rock capacity at Khouribga and Meskala in Morocco. Major expansions in phosphate rock capacity are also expected out to 2026 from established phosphate producers in Russia and Kazakhstan (Acron, EuroChem, PhosAgro), Brazil (EuroChem, Itafos) and Mexico (Fertinal). This extra supply will be largely consumed in integrated, downstream operations. Kropz’s Elandsfontein one million tonne capacity, export-oriented project in South Africa is currently in the commissioning phase. In Australia, Centrex plans to ramp up monthly phosphate rock production at its flagship Ardmore project in Queensland from 10,000 tonnes currently to 30,000 tonnes this year. EuroChem recently began shipping phosphate rock concentrate to its European production units from its Serra do Salitre project in Brazil.
Phosphate fertilizer, phosphoric acid and integrated phosphate rock projects**
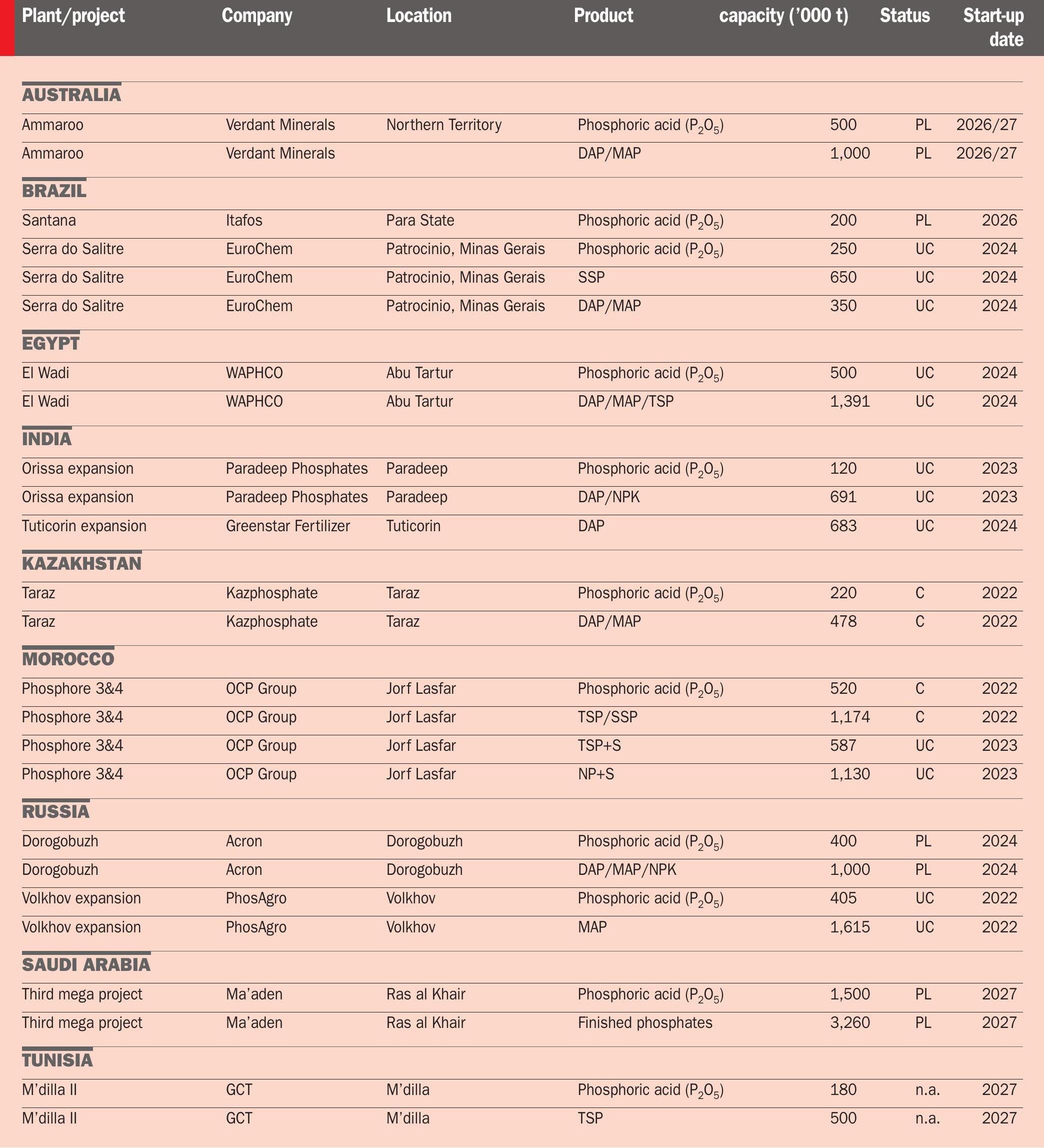
KEY FOR BOTH TABLES
FS Feasibility study complete
PL Planned
UC Under construction
C Project completed
n.a. Not available
DAP Diammonium phosphate
DCP Dicalcium phosphate
MAP Monoammonium phosphate
PPA Purified phosphoric acid
SSP Single superphosphate
TSP Triple superphosphate
**Excluding China. The International Fertilizer Association (IFA) expects investments by OCP Group to add 1.7 million t/a to Morocco’s finished phosphates capacity in 2023. In Egypt, WAPHCO is currently constructing a major phosphate production complex at Abu Tartur. EuroChem is also pressing ahead with the development of its one million tonne capacity Serra do Salitre project. The third phosphates mega project announced by Ma’aden and its partners could eventually ramp-up Saudi Arabia’s phosphates production capacity by a further 3.3 million t/a.
PHOSPHATE TECHNOLOGY AND ENGINEERING PROFILES
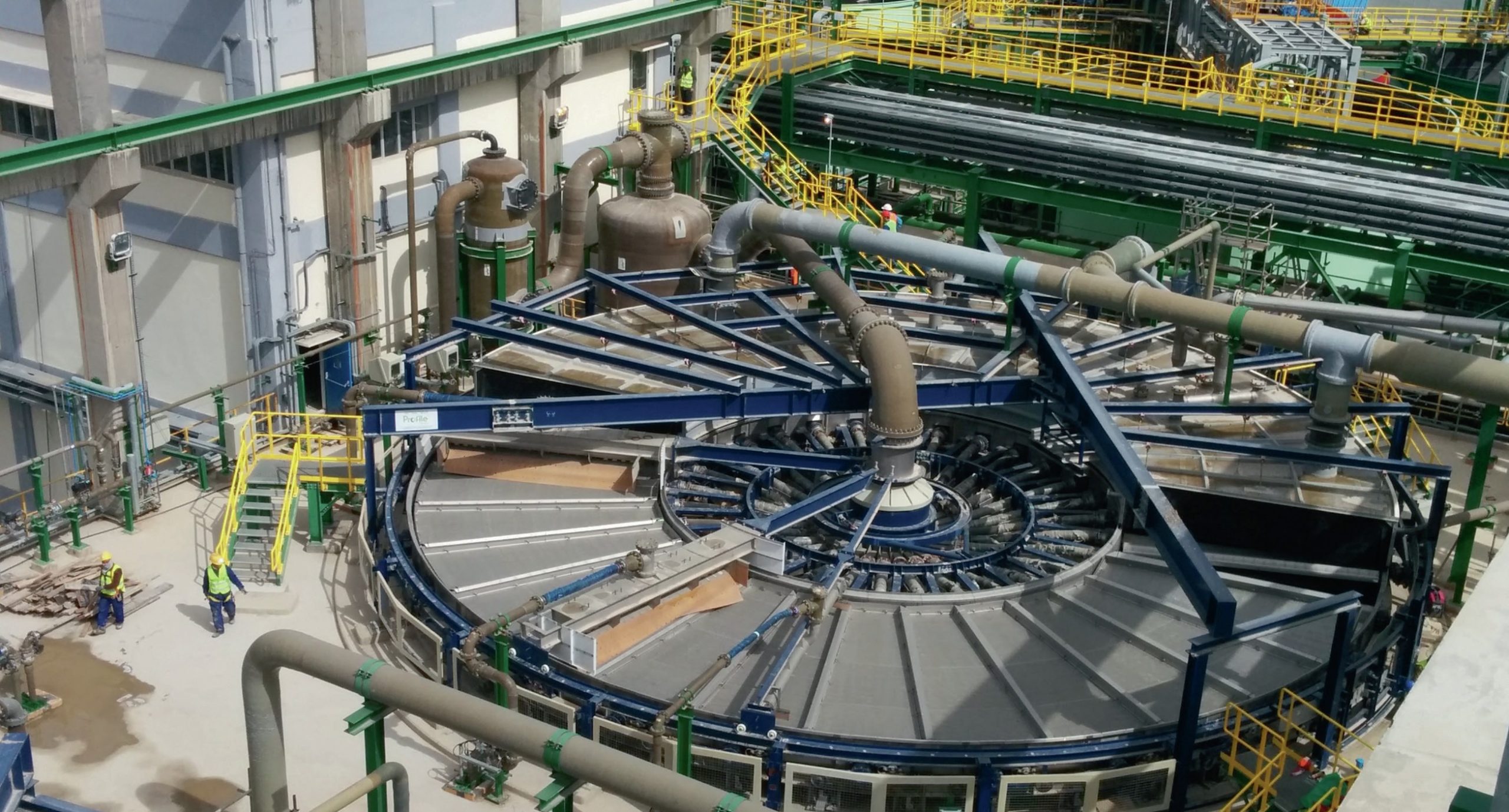
Profile
Bravely facing new challenges
Paul-Henri Legros, general manager, Profile, a division of Prayon s.a. provides a personal update on latest phosphate industry developments:
“Feeding the world is a wonderful motivation and the ultimate goal for our phosphoric acid–fertilizer industry. The world’s current trajectory is placing new obstacles in our path and – to succeed – we will need all our knowledge and experience to overcome these.
“On the one hand, you have a continuous growing global population. Yet there’s also a constant need to improve the living conditions and health of the whole population. So, as time goes on, everybody on the planet will be looking for better quality food together with more food availability worldwide.
“Currently, we are all witnessing the decrease in the area of land available and dedicated to agriculture – the main factors being urbanisation and changing climate and weather patterns across the world. In parallel, the quality of available phosphate rock resources is decreasing – while, at the same time, the necessity to think sustainability, save energy, and shift to ‘green’ production is also becoming more evident.
“Great, we have found our challenges for the next decade! So now is the time for the industry, for the chemists, for the engineers, for all men of good will, to put in place the solutions to these.
“At Prayon, we have an opportunity to strongly influence the future of the phosphate industry – a prospect that, I must admit, is very exciting. Being able to bring to the market our experience, our knowledge, our achievements in continuous process and equipment development. These skills combined will really enable us to make the difference.
“25 years ago, we were proud to introduce a Prayon Tilting Pan Filter® with a total surface of 100 m² into a 400 tonne (P2 O5 ) per day capacity production plant. Today, we are announcing the possibility of achieving a total surface of 360 m² in a single Prayon Tilting Pan Filter® .
“As well as this, in a relatively short period – by dedicating time and sinking resources into fundamental research – we have been able to reduce the power consumption of our process agitators by 50 percent. Additionally, the successful recovery of P2 O5 and fluorine droplets from the exhaust gases at installations, using Prayon’s efficient and effective PRAYSEP® separator, has allowed operators to increase their process yields by almost two percent.
“These new developments, together with the confidence shown in Prayon by the world’s great fertilizer producers – in Morocco, Saudi Arabia, Jordan and Egypt to name just a few – have allowed these leading companies to develop new production lines with a P2 O5 capacity of more than 1,200 tonnes/day – that’s despite the general decrease in phosphate rock quality already mentioned.
“Our progress in both phosphoric acid plant design and chemical process implementation holds the key to our market impact. Being able to show our customers and fellow producers that it’s possible to produce more, at better quality, while drastically reducing their energy and water consumption, and being more green, is a really satisfactory reward for all the efforts put in place by Prayon.
“Just taking into account those projects which Prayon participates in, we anticipate the addition of more than 20,000 tonnes/ day of extra P2 O5 production capacity before 2030. This expansion in production, combined with fertilizer industry decarbonisation and resources savings, will allow us to say that we have faced up to global challenges and responded positively. Yes, we know how to feed the world and, yes, we have the capabilities to change the world into a better place for upcoming generations.”
Prayon Technologies (PRT)
Prayon Technologies (PRT), the licensing division of Prayon, is internationally renowned for its phosphate production technologies. Currently, plants fitted with Prayon technology are responsible for one third of worldwide phosphoric acid production. Prayon’s notable achievements include more than:
- 130 references in over 30 countries
- 20 production processes
- 65 validated phosphate rock types.
Experts at PRT dedicate themselves to designing easily operable and highly reliable phosphoric acid plants. This expertise comes from the company’s know-how and its track record with production plants gained during more than 70 years of experience. Prayon incorporates the very latest process developments into its plant designs to benefit all of the phosphoric acid producers the company works with.
PRT offers the widest range of technologies for phosphoric acid production. Each of the company’s five processes has its own characteristics. This allows Prayon to offer its partners successful tailor-made production options. The ability to deliver operationally successful phosphoric acid plants is reinforced by incorporating premium-quality equipment specifically designed by Profile, the process filtration and liquid equipment division of Prayon.
Alongside the traditional route for producing feed phosphates from high-grade phosphoric acid, Prayon now offers two cutting-edge technologies that can use low-grade phosphate rock as a starting material. These innovative processes can significantly reduce production costs while generating feed phosphates of the same grade.
Prayon is aware that technological innovation will be vital for improving production processes to meet the needs of future generations. This includes developing technologies that are able to capture and use recycled raw materials. These will allow the phosphate industry to convert waste into valuable products while at the same time increasing the size of available phosphate resources.
PRT works closely with phosphoric acid producers to ensure they meet local environmental regulations. Reliable Profile-designed equipment, such as gas scrubbers and towers, enable businesses to reach high performance levels with close to zero emissions. The liquid bleed from these systems is either cleverly recycled into the process or concentrated to generate valuable co-products. Technologies are available to selectively remove deleterious and unwanted impurities (As, Cd, F, SO4 , Mg. etc.). Prayon has also developed a new Mg leaching technology – a chemical beneficiation process – which can be added as a stage between the existing mechanical beneficiation and the phosphoric acid plant. This beneficiation innovation will enable phosphate rocks with high MgO content to be used in the production of high grade fertilizers such as DAP.
Our in-depth process knowledge and understanding is the key to getting the best from a phosphoric acid plant. Prayon, through its wide range of services, always accompanies the owner at each and every stage of their project – starting by providing a tailor-made plant design all the way through to offering consultancy services during plant operations.
The company’s expertise encompasses:
- Lab to semi-industrial scale testing and validation
- Plant simulation training
- Technical surveys
- Achieving operational excellence through data management and plant optimisation.
Ballestra
Milan-headquartered Ballestra SpA has extensive experience in the design and supply of chemical plants.
For the fertilizer industry, the engineering company offers production plants for sulphuric acid, merchant-grade phosphoric acid (MGA), single superphosphate (SSP), triple superphosphate (TSP), potassium sulphate, granulated NPK compound fertilizers, ammonium nitrate (AN), ammonium sulpho nitrate (ASN), calcium nitrate (CN), calcium ammonium nitrate (CAN), urea ammonium nitrate, urea ammonium sulphate (UAS), and slow/ controlled release fertilizers
From initial design through to plant start-up, Ballestra offers support to clients during all of the following project phases:
- Feasibility studies
- Material supply
- Process design
- Project implementation
- Detailed engineering
- Plant start-up the phases
- Follow up services along the entire plant life cycle.
Ballestra phosphoric acid plants are highly flexible. The design of each plant is bespoke, being specifically tailored to individual client needs. To maximise process efficiency, plants are customised to accommodate different types of phosphate rock.
Uniquely globally, Ballestra is the permanent licensee of the major technology providers Elessent MECS for sulphuric acid and Prayon Technologies for phosphoric acid.
Ballestra offers phosphoric acid plants based on the following processes:
- DH: Di-Hydrate (single crystallization)
- HH: Hemi-Hydrate (single crystallization)
- CPP: Central Prayon Process (double crystallization DH-HH)
- HDH: Hemi-hydrate to Di-Hydrate (double crystallization HH-DH)
- DA-HF: Di-hydrate attack, Hemi-Hydrate filtration (double crystallization DH-HH).
These versatile, well-proven and market-leading processes are widely employed in many phosphoric acid projects around the globe. The most suitable process is selected based on a range of factors, such as rock quality, performance parameters and production economics. All the above processes enable the production of 52-54 percent concentration phosphoric acid, an intermediate in the manufacture of phosphate fertilizers.
Plants can also be configured to allow the recovery of fluosilicic acid (FSA). This is obtained as a process by-product – in concentrations up to 18 percent – and can be sold to market, or converted into valuable anhydrous hydrofluoric acid (AHF) or AlF3 under a technology collaboration with Ballestra’s fully owned subsidiary Buss ChemTech. Alternatively, it can be neutralised for disposal.
Ballestra is also an established supplier of potassium sulphate (SOP) plants delivered via a greatly improved Mannheim process or through its innovative and proprietary WET SOP technology. Finishing plants for all the fertilizer technologies are also available.
De Smet Agro
De Smet Agro (DSAG) has been providing project management, engineering, procurement and construction management services to the fertilizer industry for more than 65 years. The company, a division of De Smet Engineers & Contractors, is based near Brussels, Belgium, with satellite offices in France, Morocco, Argentina and India.
DSAG has strong and globally recognised expertise in the engineering and construction of fertilizer complexes, working in collaboration with multiple partners and different technology licensors. This has enabled the company to deliver more than 250 industrial plants in 35 countries since 1957 – including numerous sulphuric, phosphoric acid and fertilizer granulation plants.
The multi-disciplinary team at DSAG offers engineering services for new ‘greenfield’ plants. The company also offers revamping and capacity improvement projects at existing production sites.
DSAG is recognised worldwide as the most experienced and wide-ranging licensee for Prayon Technologies (PRT), offering all of the company’s industry-leading phosphoric acid production routes, and its processes for phosphoric acid derivatives and by-products. This longstanding cooperation with PRT, which dates from 1960, has delivered many notable project achievements globally.
DSAG has full in-house expertise for all the engineering, procurement and construction supervision needed to deliver phosphoric acid projects. (Prayon’s process design package being the starting point for these activities.) The company’s project capabilities cover the complete production process, from raw materials to the handling and storage of the final product. DSAG possesses in-depth expertise for:
- Single and double crystallisation phosphoric acid processes
- Phosphoric acid purification technologies (solvent and membranes)
- Phosphate salt technologies, including those for food phosphates, and new processes such as those for soluble fertilizers
- Dicalcium phosphate (DCP) processes (HClor H2 SO4 -based) including a phosphoric acid production process based on DCP
- Fluorine gas scrubbing
- Phosphoric acid concentration and fluosilicic acid recovery
- Phosphate rock solids or slurry handling and storage
- Acidic cooling tower design
- Gypsum transfer as solids or slurry, storage and valorisation.
Additionally, DSAG offers fully proven inhouse technologies for nitrogen fertilizer production. The company’s nitrogen process design expertise covers synthesis, evaporation, crystallisation, prilling and granulation units for clients all over the world. Specific areas of expertise include:
- In-house fluidised drum granulation technology for ammonium nitrate products (AN/CAN/ASN) and calcium nitrate (CN)
- Prilling of low density ammonium nitrate (LDAN)
- Ammonium Sulphate (AS).
DSAG also offers a comprehensive range of construction services for fertilizer granulation. These services cover the construction of granulation units for:
- Monoammonium phosphate (MAP)
- Diammonium phosphate (DAP l NPKs.
The company’s granulation expertise also includes the design of gaseous effluent cleaning systems.
To meet client or project needs, DSAG has the capability to team up with other recognised fertilizer technology providers/ contractors, thanks to strong relationships built over decades. This provides industry customers with a single point of contact with complete responsibility for the delivery of their fertilizer projects.
DSAG provides a complete range of services to the fertilizer industry all around the world. These range from technical audits to the full delivery of EP and EPCM contracts and typically include:
- Technical audits
- Prefeasibility, feasibility studies, capex and opex estimates, including all onsite and off-site facilities
- Financial studies
- Overall project management
- Front-end engineering design (FEED), basic and detailed engineering design
- Procurement
- Construction management and site supervision
- Training of client personnel
- Pre-commissioning and commissioning services
- Start-up assistance and performance guarantee tests.
Client: Emaphos
Location: Jorf Lasfar, Morocco
Project: Emaphos 2 purified phosphoric acid plant
This plant was commissioned in 2023 and consists of a pretreatment unit and a solvent extraction purification section. De Smet Engineers & Contractors and its subsidiary DSAG completed the project’s EPCM mandate.
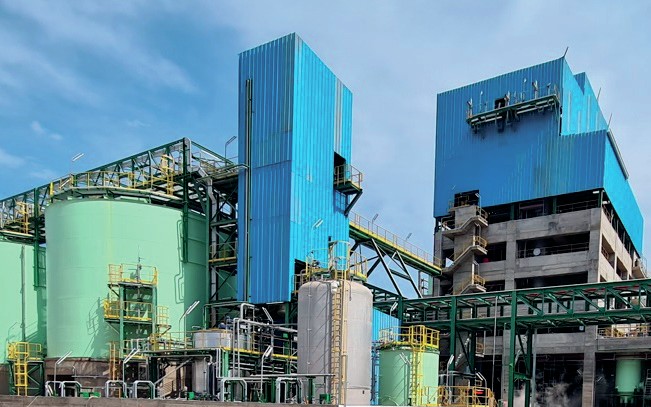
JESA Technologies
JESA Technologies (JT), based in Lakeland, Florida, has proudly served the global phosphate industry for over a half century. The company, backed by two global powerhouses, OCP and Worley, offers licensed technology to the phosphates industry covering the whole production process, from mine to market. The company is a leading licensor for three process steps in particular: phosphate rock beneficiation, phosphoric acid production and granular fertilizer manufacture.
Additionally, JT offers on-site pilot plants, for both beneficiation and phosphoric acid, supported by a fully equipped analytical laboratory. The ability to combine in-house technical and engineering design know-how – from mined rock all the way through to the finished product – with on-site pilot plants makes JT unique as a licensor.
Since its establishment in 1974, JT has been responsible for the design of over 150 process facilities for the phosphate fertilizer industry in 29 countries. The plants designed by JT include the largest single-train phosphate operations in the world. Notably, these include a phosphoric acid plant with a demonstrated capacity above 3,000 tonnes per day – plus numerous examples of DAP/NPK plants with capacities in excess of one million tonnes per year.
In addition to designing new plants, JT has an extensive track record in revamping operational plants. These revamps have successfully delivered a range of desired outcomes for customers – including increased production capacity, product quality improvements, energy savings and improved environmental performance.
JT’s extensive test facilities in Lakeland, Florida, include:
- A comprehensively equipped analytical laboratory
- A bench-scale metallurgical laboratory, capable of testing ore samples obtained from core drilling or pits
- A fully-equipped pilot plant capable of batch or continuous operation
- A continuous phosphoric acid pilot plant.
These test facilities make a vital contribution to feasibility studies. By developing process design data, they enable JT to offer its customers process guarantees. They are also engaged in contract research for clients.
Two case studies of phosphate industry projects recently awarded to JT are provided below:
Client: Itafos Conda Phosphate Operations
Location: Soda Springs, Idaho, USA
Project: Beneficiation improvement project – detail engineering
Itafos Conda Phosphate Operations (CPO) operates a phosphate fertilizer production complex in Soda Springs, Idaho. Prospecting activities indicate that in the coming years, the magnesium content of the ore recovered from mining operations will be elevated to the point that the current processing plant may not be able to produce fertilizer products with acceptable levels of magnesium impurity. Improvements to the ore beneficiation process are therefore needed.
Commencing in the fall of 2021, JT has assisted Itafos with the development of a new processing flowsheet which incorporates froth flotation to improve the beneficiation plant concentrate product quality. Laboratory and pilot plant test results indicated that additional processing steps would be necessary to optimise phosphate recovery and improve the operability of the plant. A subsequent basic engineering and design stage was used to define the exact beneficiation requirements and estimate the budget for this brownfield project.
Itafos and JT, based on this revised concept and a value engineering study, then proceeded to the detailed engineering and procurement phase of the project in January 2024.
Client: Ma’aden
Location: Ras Al Khair, Saudi Arabia
Project: Front-end engineering design (FEED) for two large-scale granular fertilizer plants
JT has been selected as the licensor for a major granular fertilizer project as part of Phase 1 of Ma’aden’s ‘Phosphate 3’ mega project. Two large-scale granulation plants, with a total annual production capacity of two million tonnes, will be designed to produce over 25 different fertilizer grades.
As licensor, JT will be involved throughout the life of the project – all the way through from technology and design to staff training and then plant commissioning and start-up, supporting the engineering, procurement and construction (EPC) contractor.
JTs’ mission is to provide the client with reliable, efficient designs that demonstrate the excellence of its expertise and unrivalled leadership in the phosphate industry.
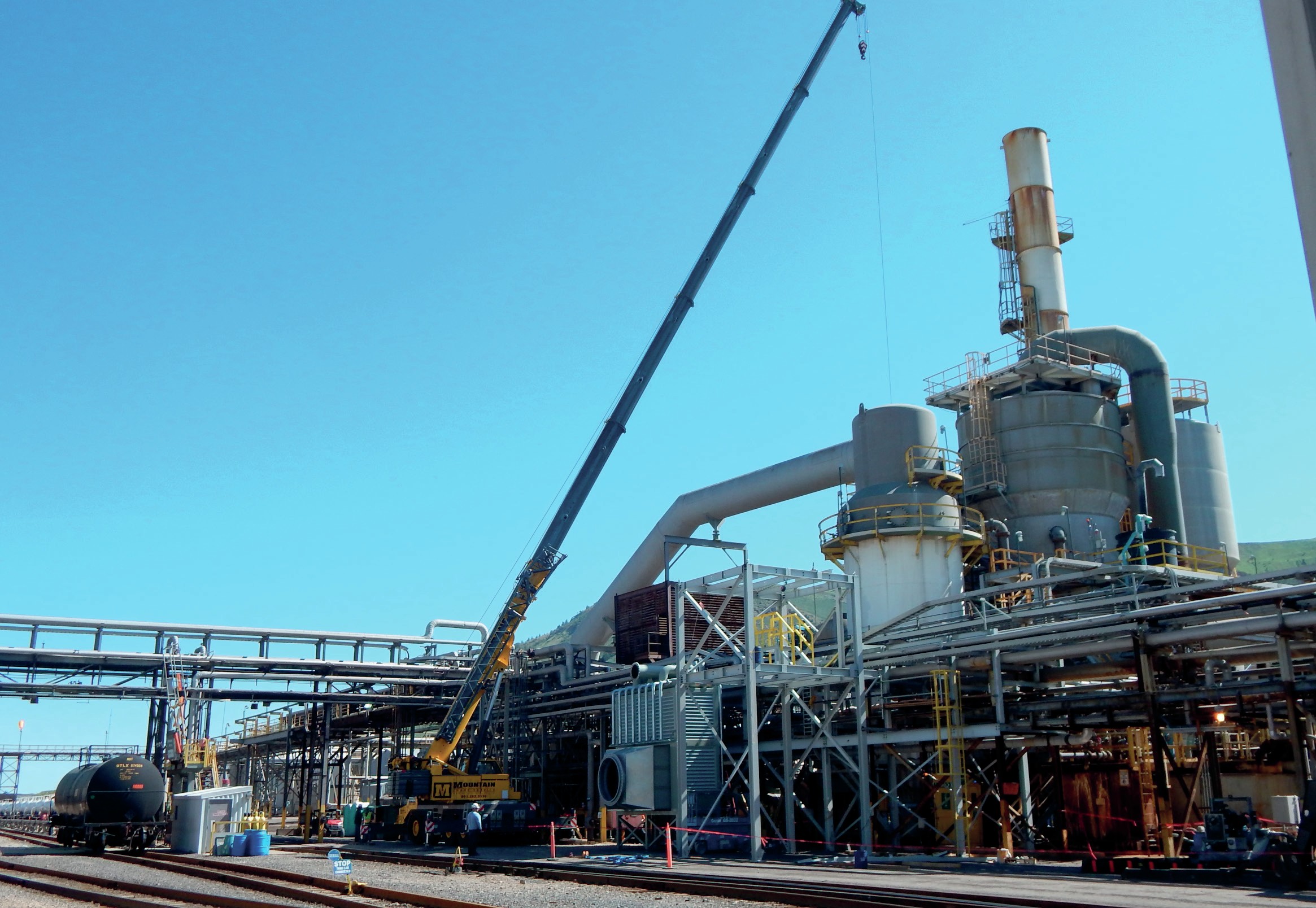
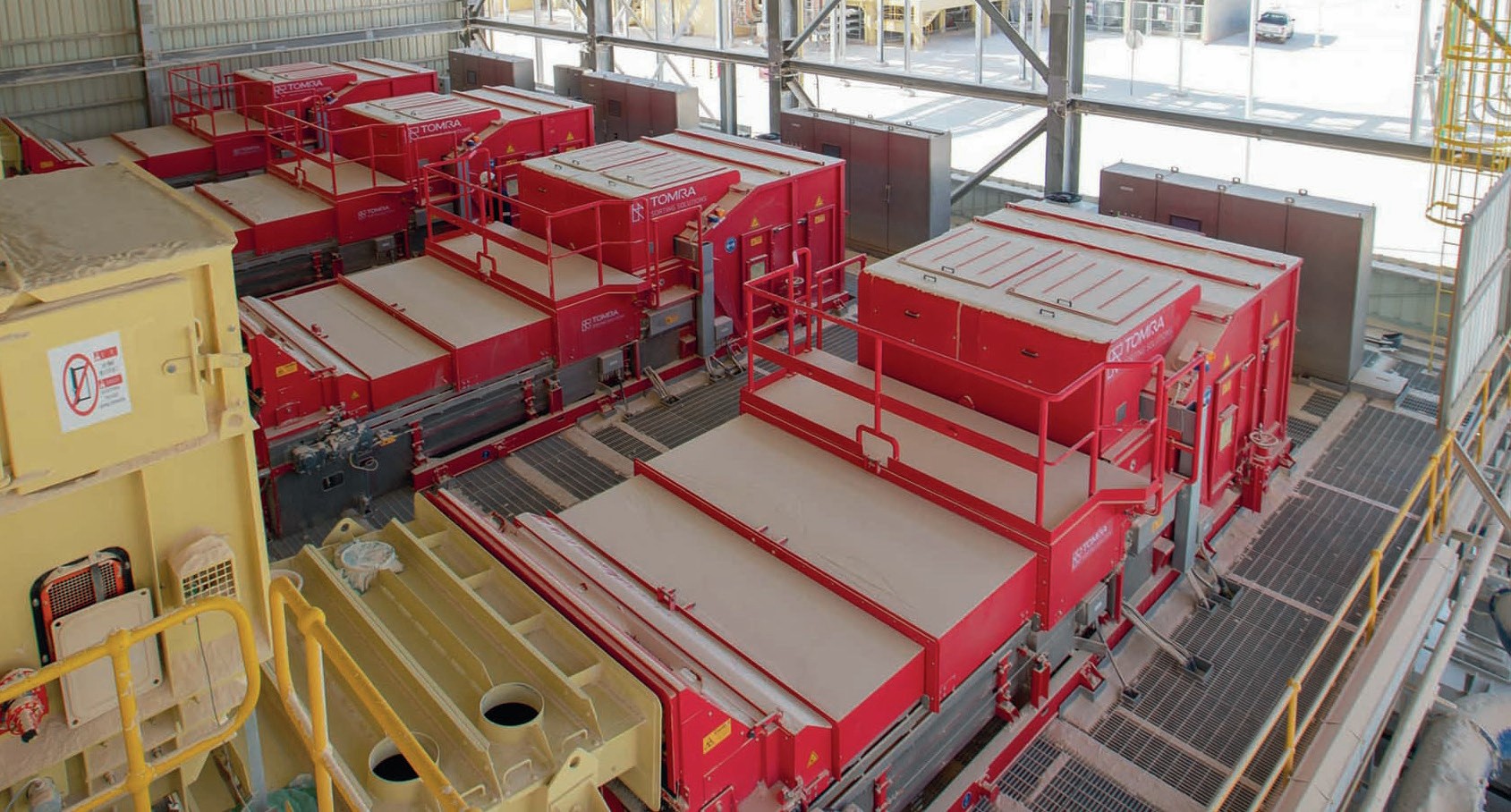
TOMRA
The use of TOMRA sorting machines at a major new phosphate mining and processing operation is showing how phosphorus can be extracted from ore with greater environmental and economic efficiency.
Transforming phosphate rock into a high-quality and commercially-usable concentrate can be costly, logistically complex and technically-demanding. Fortunately, the introduction of innovative and pioneering sorting technology is now helping to improve the efficiency of phosphate fertilizer production.
Indeed, the installation of TOMRA sorting machines at a new large-scale phosphates mining and processing complex in Saudi Arabia has shown how it is possible to cut production costs – while at the same time turning traditionally discarded waste into usable phosphate.
The massive complex, located in the remote north of the Kingdom, is run by the Ma’aden Wa’ad al Shamal Phosphate Company (MWSPC), an $8 billion joint venture between Saudi mining giant Ma’aden, Saudi Basic Industries Corporation (SABIC) and US-based Mosaic, a leading international fertilizer producer. The successful completion of the MWSPC project in 2018 has turned Saudi Arabia into the second-largest phosphate producer in the Middle East.
The biggest challenge at the MWSPC plant – in common with many other phosphate operations around the world – is removing significant amounts of unwanted silica, also known as flintstone or chert. This needs to be eliminated from run-of-mine material to improve its quality and ensure that phosphate rock concentrates are suitable for downstream chemical processing.
This challenge is even tougher for MWSPC. That’s because contaminants are traditionally removed from phosphate ore using large quantities of water (and chemicals). Yet this is not possible at the company’s arid inland desert location due to the lack of a natural rain-fed water supply.
TOMRA therefore collaborated closely with the designers of the MWSPC plant to find a way of reducing water (and electricity) consumption in downstream production processes. The installation of high-capacity TOMRA sorting machines emerged as the most viable and practical option. These machines are capable of efficiently identifying and ejecting unwanted silica from large volumes of phosphate feed materials.
Following their installation, TOMRA’s XRT (X-Ray Transmission) machines are now preprocessing more than half of the total 13.5 million tonnes of phosphate ore handled by the MWSPC plant every year. Running at a rate of 1,800-2,000 tonnes per hour, the XRT machines recognise and separate materials according to their specific atomic density. Advantageously, this process is completely dry and avoids the need for wet, water-based cleaning of materials.
The sorting machines have performed remarkably well at the MWSPC plant, delivering large efficiency gains and cost savings. “Now that this plant has been running for years, the effectiveness of XRT sorting is clear,” comments Jens-Michael
Bergmann, TOMRA’s area sales manager for Europe, MENA and India. “By making it possible to remove 98 percent or more of liberated silica contaminants, XRT has reduced the workload and costs of crushing by about 75 percent, reduced the costs of milling by 45 percent, and reduced water consumption by 45 percent.”
He adds: “What’s more, the ability to reduce the size of the flotation plant has saved millions of dollars in construction costs, and continues to save about $10 million per year in the cost of flotation reagents alone.”
XRT sorting technology can perform equally well at improving the phosphate-processing efficiencies of many other operations globally. That’s the main lesson from the successful installation of TOMRA sorting machines at the MWSPC plant – in some of the most hostile working conditions on earth.