Sulphur 411 Mar-Apr 2024
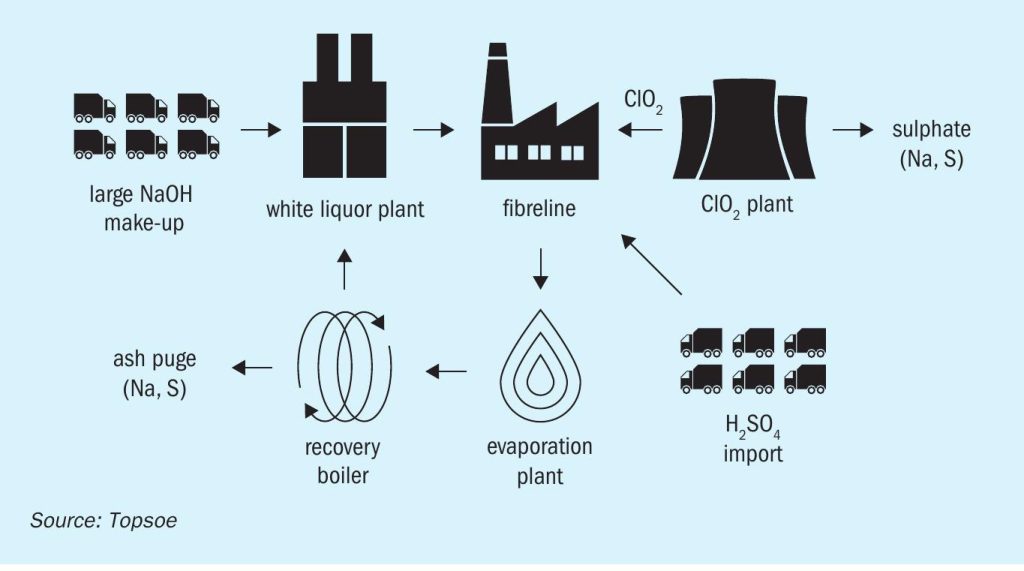
31 March 2024
A smarter way to treat lean sulphurous off-gases
WET GAS SULPHURIC ACID TECHNOLOGY
A smarter way to treat lean sulphurous off-gases
The implementation of WSA technology to recover sulphur as sulphuric acid from lean sulphurous off-gases offers significant environmental benefits. These include waste reduction, resource efficiency and reduced overall CO2 e footprint, while also producing profitable sulphuric acid. By embracing such practices, industries can ensure improved or better consumption and production patterns and foster a more sustainable and responsible future. J. Feddersen and S. S. Johansson of Topsoe illustrate these benefits using three distinct industrial applications where WSA technology provides a smarter way to treat sulphurous off-gases. It is not only waste stream management in the three cases, but also reduced transportation of chemicals, reduced opex and reduced CO2 e footprint.
Taking a people- and environment-first approach to business can have multiple benefits across sustainability, efficiency, and cost effectiveness. For instance, reducing waste, using resources more efficiently, and implementing practices that help mitigate negative environmental impact allows companies to save on operating costs while improving reputation and image.
A more sustainability-focused brand profile is hard to put a price on, but it can increase customer loyalty, attract and retain qualified employees, and help secure access to investment. Embracing sustainability also helps businesses to align with the United Nations’ Sustainable Development Goals like the goal on “Responsible consumption and production”.
In a multitude of industries, lean sulphurous off-gases, characterised by SO2 concentrations in the range of 0.1 to 6.0 vol-%, will often go untreated or be treated using scrubbing technologies that generate waste streams. Wet gas Sulphuric Acid (WSA) technology can be utilised to responsibly recover sulphur as sulphuric acid from such lean waste streams. This is illustrated here by three distinct industrial applications where WSA technology provides a smarter solution for waste stream management.
The metallurgical industry, like many industries, generates lean SO2 gases that are left untreated or treated using scrubbers. Similarly, the pulp and paper industry experiences substantial losses of sodium and sulphur as waste streams throughout the pulp mill, necessitating additional purchases of NaOH and H2 SO4 . Refineries also face the challenge of treating lean off-gases such as the Claus tail gases, often resorting to amine absorption and fuel gas incineration, which leads to increased overall CO2 emissions. By adopting WSA technology, these industries (and many others) can efficiently recover sulphur as profitable sulphuric acid from lean sulphurous off-gases, mitigating waste generation, reducing the loss of valuable chemicals, and minimising greenhouse gas emissions.
Metallurgical industry
The metallurgical industry is a vital part of the manufacturing sector and the green energy transition, responsible for producing various metals, including nickel, zinc, copper, molybdenum, platinum group metals. It is a highly energy-intensive industry that relies on a range of processes to extract and refine metals from ores. During extraction, several metal processing plants generate SO2 off-gases from the roasting or smelting of non-ferrous metal ore. From some of the metallurgical processing plants these gases are relatively lean up to 6 mol-% of SO2 , requiring further treatment. Traditionally, these gases have been treated in scrubbers, generating waste products, or they have not been treated at all and simply released through the stack. However, the latter is becoming more infrequent due to environmental restrictions.
WSA technology is a good alternative to scrubbers as the operating cost and waste management are significantly reduced, while the SO2 off-gases can be converted into profitable sulphuric acid.
Case story – Molybdenum plant in Asia
With increasing demand for molybdenum products, several companies around the world are considering increasing production. A new molybdenum roasting site in Asia required a solution for treating the off-gas with SO2 concentration around 2 mol-%. After comparing a scrubber using Mg(OH)2 with Topsoe’s WSA technology, it became clear that WSA technology was the best match due to several reasons including:
- Scrubbers require continuous chemical consumption and waste management of sludge and water; WSA technology significantly reduces these parameters. This reduction leads to lower operating expenses for WSA technology, making it the cheapest solution after only a few years of operation, despite a higher initial capital expenditure.
- WSA technology produces valuable sulphuric acid, particularly beneficial in a country that needs to import sulphuric acid.
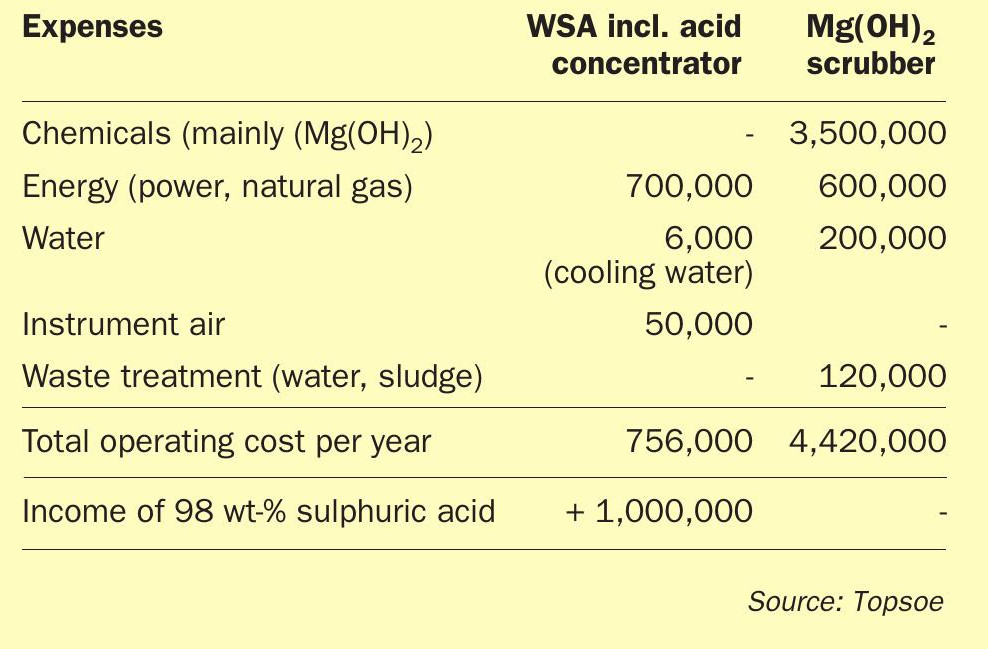
The above benefits are clear when comparing the main expenses for the two technologies in Table 1. WSA technology is proved to be the cheapest option after just a few years of operation (Fig. 1). A WSA unit requires additional equipment, piping and design, hence the investment will typically be higher than a scrubber. Even though the total investment cost is higher, soon the high expense for scrubbing consumables is felt, making WSA more cost efficient in the long run. The profit on 98 wt-% sulphuric acid makes the WSA unit more and more favourable year by year.
The annual operating expenses are compared in Table 1. The list of expenses is a simplified version and does not include expenses for labour, potentially transport cost for chemicals, waste or products, maintenance or operating availability. This is because these factors will be highly dependent on operational excellence and plant location.
The WSA unit includes an integrated sulphuric acid concentrator (in short called an ISAC) to ensure a high purity sulphuric acid of 98 wt-%.
The ISAC uses hot, dry air to drive some of the water content out of the sulphuric acid. Depending on what and where the sulphuric acid will be used, lower concentrated sulphuric acid can be sufficient, and the ISAC is not required. This will reduce the power consumption by approximately 30%.
This example is based on the following parameters:
- off-gas flow up to 35,000 Nm3 /hr;
- SO2 flucating between 1-2 mol-%;
- off-gas temperature around 45-55°C;
- location in low-cost country;
- maximum allowed SO2 emission of 450 mg/Nm3;
- expenses for labour, maintenance, operating availability, cost of transportation have been excluded for simplification;
- the income of 98 wt-% sulphuric acid is based on a price of $50/t;
- MgSO4 is sent directly to wastewater treatment, hence it generates no income in this case.
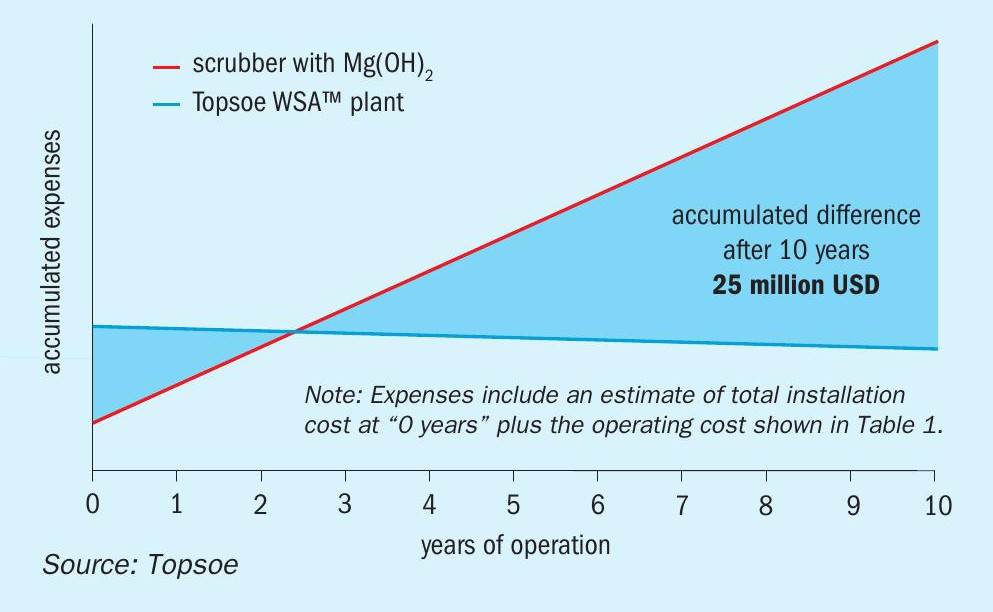
Despite the business case not being favourable if only the total installation cost is considered, WSA technology will be the most cost-effective solution over time, while reducing waste management significantly. Hence, the WSA technology was selected for the new molybdenum roaster planned to be commissioned in 2025.
A similar but more extensive assessment was made by Anglo American Platinum to comply with new dust and SO2 emission standards at Polokwane Metallurgical complex in South Africa. Close to 40 different abatement technologies were evaluated, and the final selection went to WSA technology as it was the best operational match as well as economically. The WSA unit was commissioned in 2021 and is operating very well.
Pulp and paper industry
The pulp and paper industry produces paper products from wood, via pulp. Pulp production is a highly energy-intensive process that relies on a range of chemical technologies utilising sodium hydroxide and sulphuric acid. During production, a pulp mill generates concentrated non-condensable gases (CNCG) containing relatively low levels of sulphurous compounds, including mercaptans and H2 S, as well as other hydrocarbons. These gases are traditionally removed in recovery boilers or special CNCG boilers with NaOH scrubbers to collect the waste sulphur and provide the only means of removing sulphur from the recovery cycle. However, this sulphur is recovered as Na2 SO4 , resulting in the loss of sodium in the mill, which then needs to be imported and replenished to the plant. Recovering the sulphur as sulphuric acid for reuse within the site increased circularity of the production process. This can help minimise chemical import to the plant and reduce waste, and reduce waste management, contributing to a lower carbon footprint with less transportation to/from the plant.
Case story – Pulp mill in Brazil
Klabin, a Brazilian pulp and paper producer, is committed to optimising the use of by-products generated in its mills and to significantly reducing greenhouse gas emissions. As part of achieving these goals, the company has implemented the Topsoe WSA solution, which enables the production of sulphuric acid from gases formed in the mill itself. This represents an important step towards a circular economy, which aims to close material and energy loops completely and reduce energy input, emissions, and waste to a minimum.
The WSA technology has been tailored to Klabin’s specific pulp and paper facility, resulting in a reduced environmental impact and improved economics for the plant. The very high sulphur recovery achieved by the WSA technology leads to a reduced import of both sulphuric acid and sodium hydroxide.

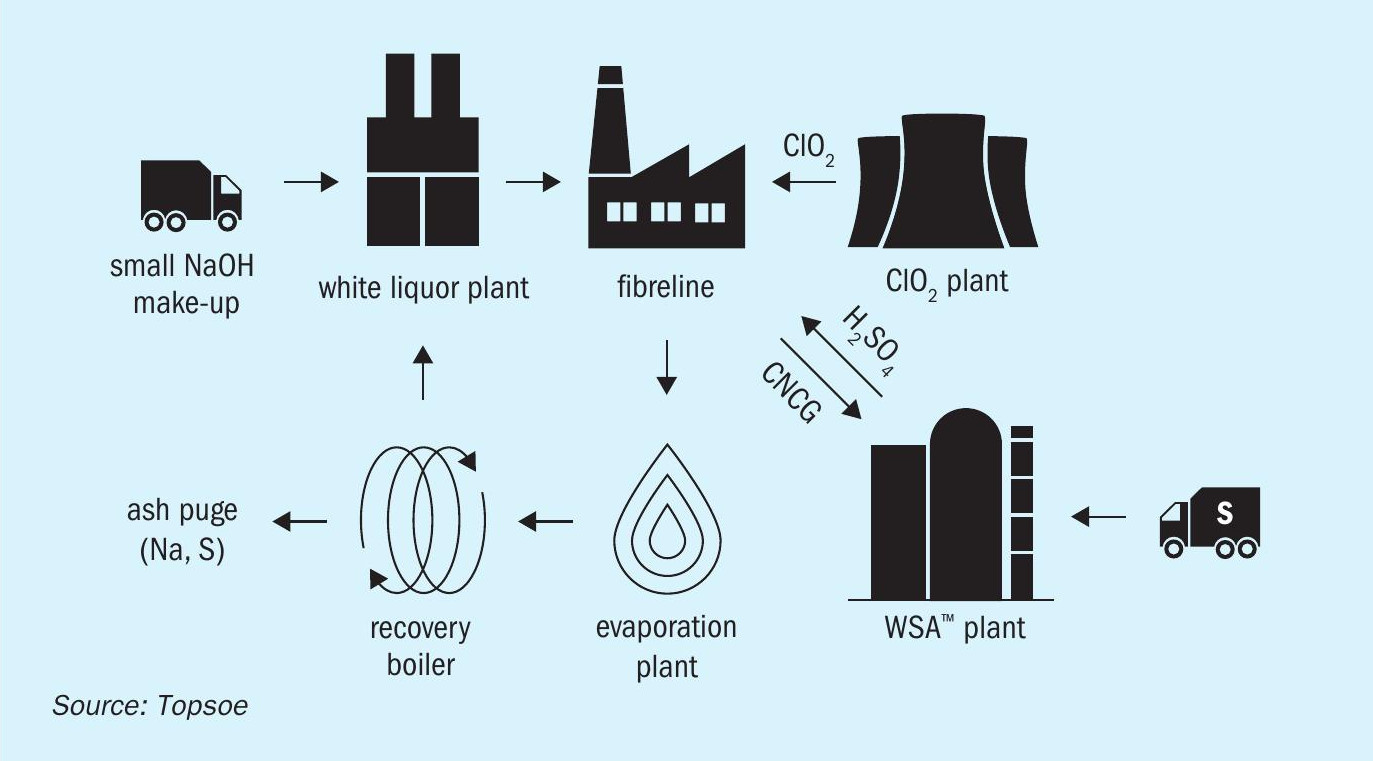
At the Ortigueira mill, operated by Klabin in southern Brazil, commercial grade sulphuric acid is produced from concentrated non-condensable gases generated on-site, as the first plant in the pulp industry worldwide.
The sulphuric acid production is based on the WSA technology and is designed to produce 150 t/d of high-purity (98 wt-%) sulphuric acid. The plant will supply all the sulphuric acid consumed in the pulp production process in “Puma I” and “Puma II” processing lines at the Ortigueira mill, as well as for the pulp production line at Klabin’s Telemaco Borba mill, 25 km away. Other resources are also used more efficiently as the sodium losses in the plant are cut by the introduction of the WSA unit; before producing their own sulphuric acid from waste gases the pulp mill had to remove sulphur from the recovery cycle of the pulp mill by means of taking out NaSO4 which leads to loss of Na in the recovery cycle (see Fig. 2). This sodium is typically replaced by adding NaOH to the mill, which must be transported to site in large quantities. By removing sulphur as sulphuric acid, Klabin could greatly cut down on the import of sodium hydroxide, which further reduced the transportation of chemicals to the site (see Fig. 3).
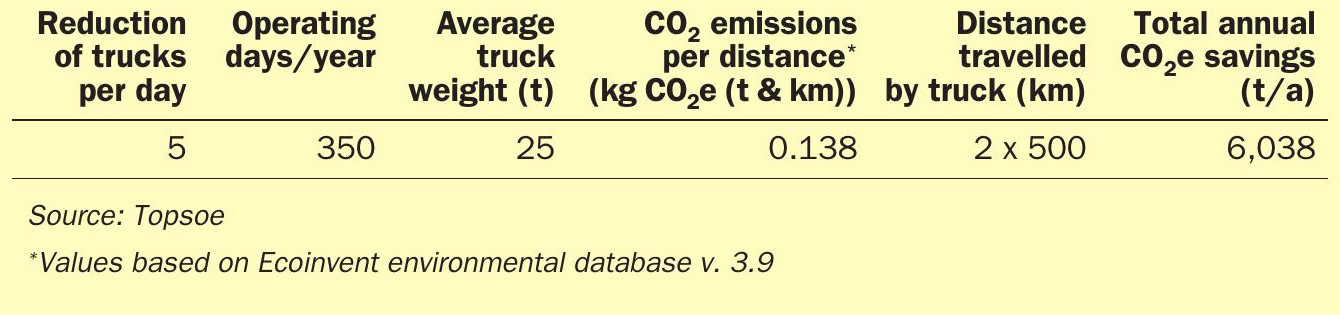
Previously, sulphuric acid and caustic required in the two mills had to be trucked 500 km from the port, with high labour input and greenhouse gas emissions. The WSA unit has enabled the reduction of trucks covering these 500 km from 6 per day to only 1, with a saving on fuel and CO2 emissions of 6,000 tonnes per year as per calculations in Table 2. According to Klabin’s Projects Director, João Braga, the sulphuric acid plant is an excellent example of how the company is closing its material loops with the aid of technology. Recovering sulphurous gases is particularly important among the by-products generated in Klabin’s mills, and the WSA technology represents a significant step towards a circular economy.
Oil refineries
The oil refining industry is a critical part of the energy and transportation sector, responsible for processing crude oil into various products, including gasoline, diesel, and jet fuel. It relies on a range of processes to refine crude oil into high-quality fuels that meet strict regulatory requirements. During the refining process, the H2 S gases are generated from hydro-treaters, via amine units, and SWS gases from sour water strippers. These gases are typically treated in Claus plants to recover the sulphur. The Claus plants generate a tail gas that traditionally did not require further treatment; however, due to updates in most national legislation the lean tail gases will require further treatment to bring down the sulphur emissions. The treatment of such Claus tail gases can be done in many ways; two of the most common ones are H2 S recovery in an amine unit followed by incineration, or incineration followed by SO2 removal in a caustic scrubber. Both options have drawbacks; a scrubber solution comes with chemical consumption and waste generation, while the amine unit option has higher CO2 emissions associated with it due to the high energy consumption and low efficiency.
Case story – An oil refinery in Eastern Europe
A refinery in Eastern Europe faced the challenge of finding a reliable and effective solution for the treatment of its Claus tail gases to meet sulphur emission compliance regulations. The target was to reach a sulphur dioxide emission of maximum 90 ppmv in the stack, corresponding to a total sulphur removal efficiency of 99.93%.
After evaluating different technologies for the treatment of Claus tail gas, the refinery narrowed down their options to two: Topsoe’s WSA technology and an amine-based tail gas treating unit.
To highlight the differences between a traditional amine-based Claus tail gas treatment, and Topsoe’s WSA technology, a comparison on CO2 equivalent (CO2 e) savings generated by the two options has been made. The comparison is made on a standard refinery sulphur recovery unit, recovering 270 t/d sulphur.
The main CO2 equivalent sources for each Claus tail gas treatment option are shown in Fig. 4 and Fig. 5 and can be summarised as:
- actual stack CO2 emissions stemming from the combustion of fuel gas within the tail gas unit;
- CO2 equivalents from the electricity consumed by the unit (electricity consumed comes from the refinery fuel gas fired boiler with associated CO2 emissions);
- CO2 equivalents saved from the production of high-pressure steam (produced HP steam replaces steam produced in the refinery fuel gas fired boiler with associated CO2 emissions).
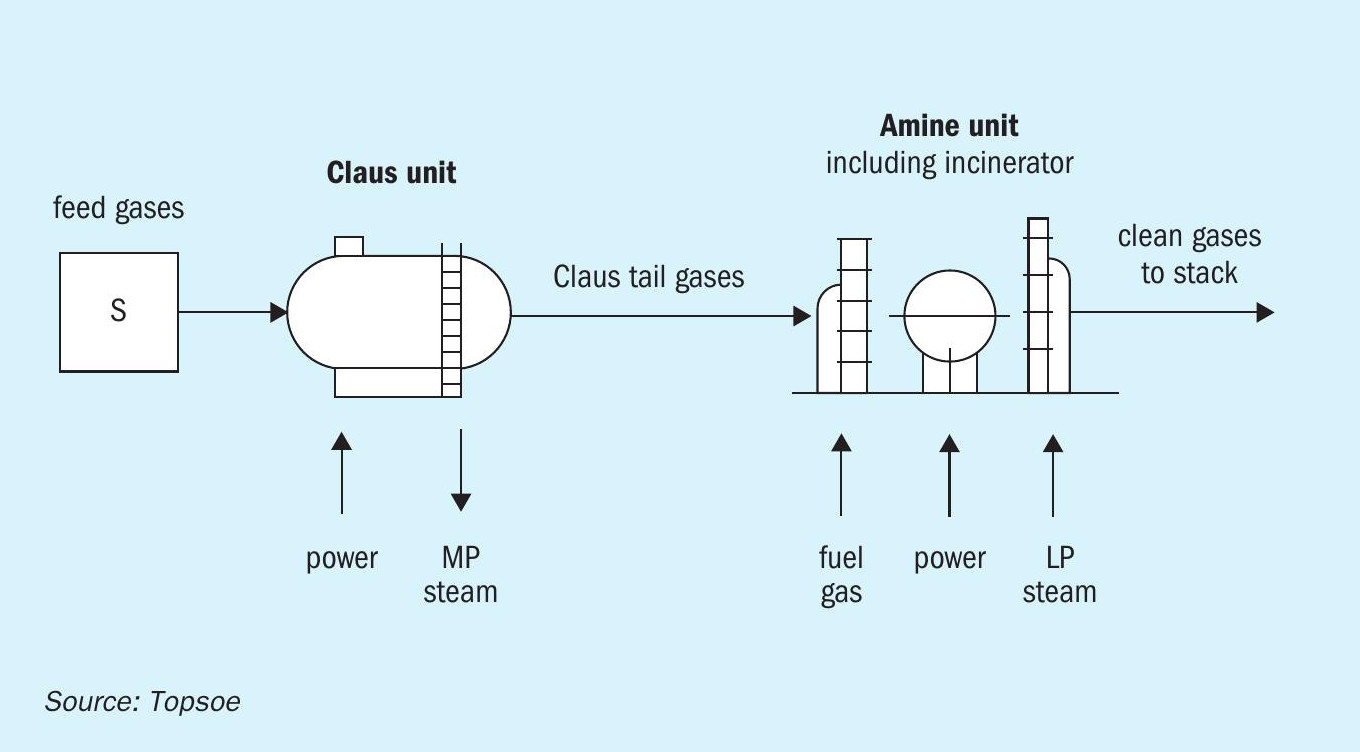
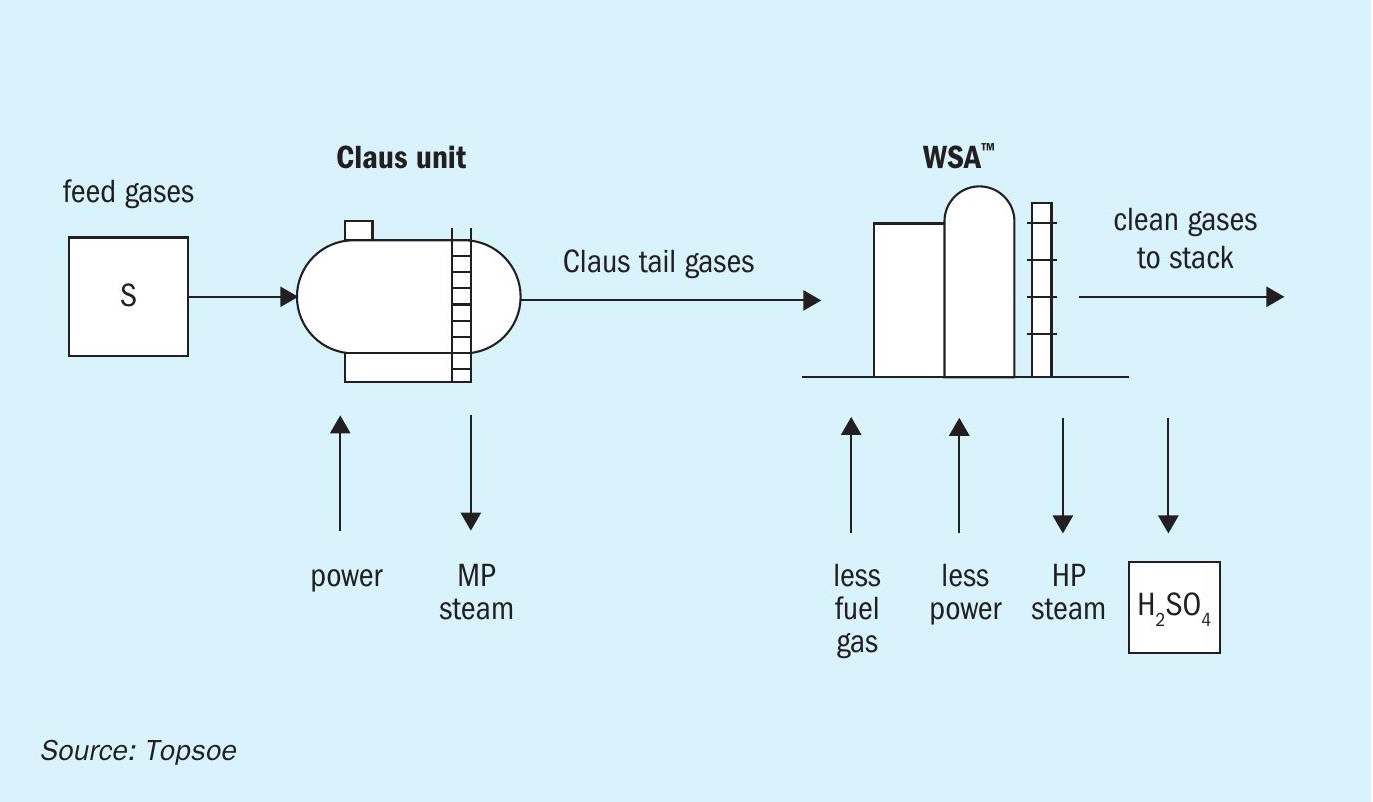
The results of the technology comparison are presented in Table 3. The comparison showed that the WSA process contributes significantly to high-pressure steam production, this steam production can replace fossil fuel-based steam production in the refinery’s power plant, resulting in a significant reduction in overall CO2 emissions from the unit. Also, the WSA allows for replacing some fuel gas with acid gas in the tail gas system, resulting in improved operating figures not possible with an amine-based unit. Overall, the comparison demonstrates that the WSA process is a smarter solution for treating the lean sulphurous tail gases coming from sulphur recovery units in the crude oil refining industry.
After comparing both options, the refinery chose Topsoe’s WSA technology. The WSA technology proved to be the optimal solution for several reasons:
- It can operate with Claus process off-gas of variable flow and composition, including low sulphur content. This flexibility allows for efficient and effective treatment of lean sulphurous off-gases. Additionally, the WSA process is highly reliable and flexible, providing consistent and stable performance.
- It is a more energy-efficient solution compared to the alternatives. By recovering most of the heat generated in the complete oxidation of sulphur from H2 S to H2 SO4 it utilises less fuel gas and produces more high-pressure steam, resulting in a reduction of total CO2 emissions.
- It can produce high-quality concentrated sulphuric acid, which can be used for a variety of industrial applications. This adds value and economic benefits to the refinery operation.
- It has lower investment and operation costs compared to alternative processes. This makes it an attractive and cost-effective solution for tail gas treatment in the refining industry.
Thanks to the higher amount of heat recovery in a WSA unit compared to an amine based TGTU the WSA has a lower fuel gas consumption and a higher HP steam production. In addition, the power consumption is slightly lower in the WSA option.
For this project, Topsoe provided technology, design, equipment, and catalyst to the refinery. The WSA unit has been in operation since 2011. Since the successful commissioning and operation of this plant, the WSA for Claus tail gas treatment has been further developed in cooperation with Comprimo; the new development is called TopClaus™ and it is now possible to recycle the produced sulphuric acid back to the reaction furnace in the main Claus plant. In this way, the sulphur collected in the tail gas treatment can be recovered as elemental sulphur in the Claus unit, ensuring the SRU is only exporting one type of sulphur product (molten or solid sulphur) instead of co-producing sulphuric acid. When sulphuric acid is injected into a Claus furnace the sulphuric acid it decomposes into sulphur dioxide, water, and oxygen, this addition of oxygen to the Claus process gas means that the total process gas flow of the Claus unit can be decreased, leading to a capacity increase in the Claus unit of typically around 10%, further increasing the benefits of utilising Topsoe WSA as the technology for treating Claus tail gases.
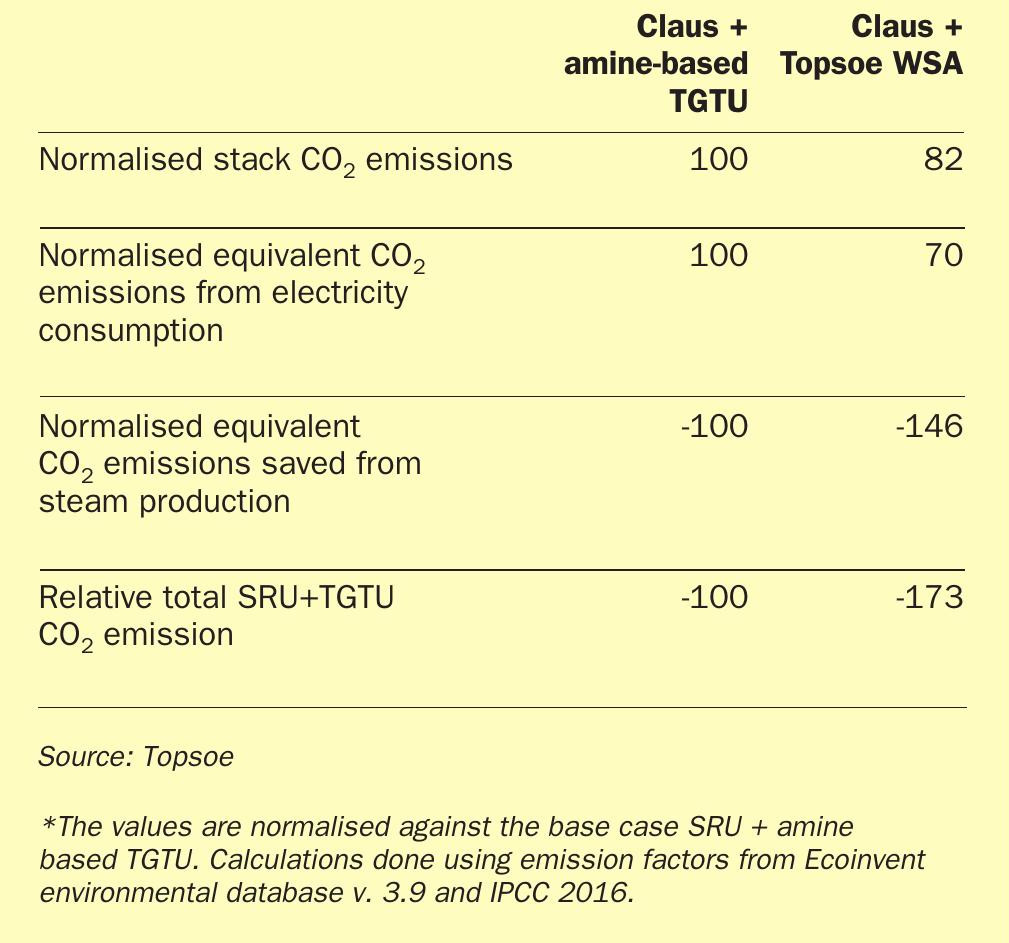
Summary
The WSA process is a flexible technology that effectively can treat sulphurous off-gases in many different industries.
This article highlights three industries where the WSA technology has been successfully implemented to illustrate many of the benefits:
- In the metallurgical industry, the WSA technology can reduce waste and waste management significantly.
- In the pulp and paper industry, the WSA technology increases the circular use of chemicals, avoiding replenishment of chemicals such as sodium and sulphuric acid.
- In a refinery, the WSA technology leads to a saving in CO2 equivialents of the SRU and tail gas unit as a result of higher HP steam production and less fuel/power consumption.