Sulphur 412 May-Jun 2024
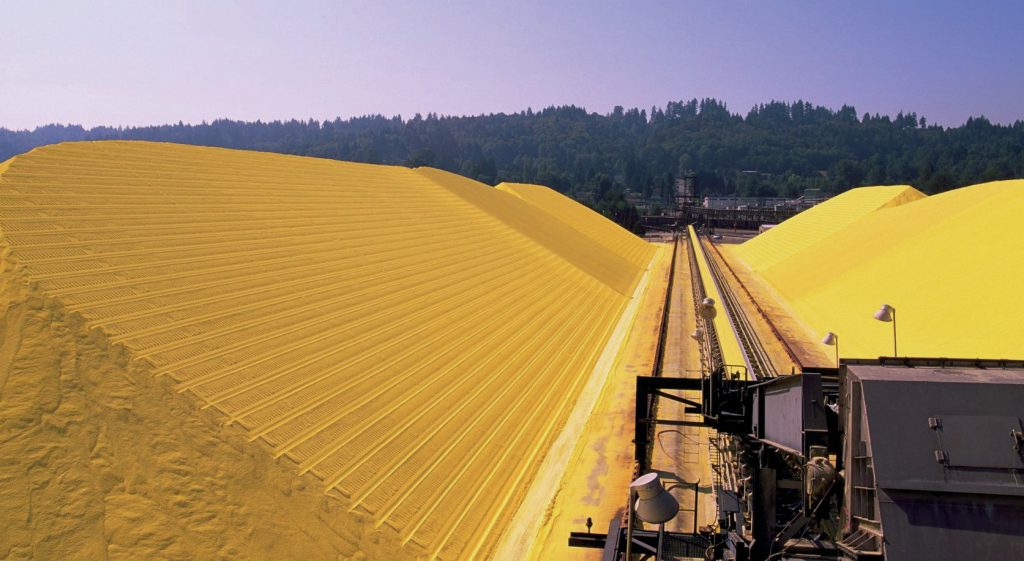
31 May 2024
Canada’s sulphur exports
CANADA
Canada’s sulphur exports
Though production, particularly from sour gas in Alberta, has declined, Canada remains the world’s second largest exporter of sulphur.
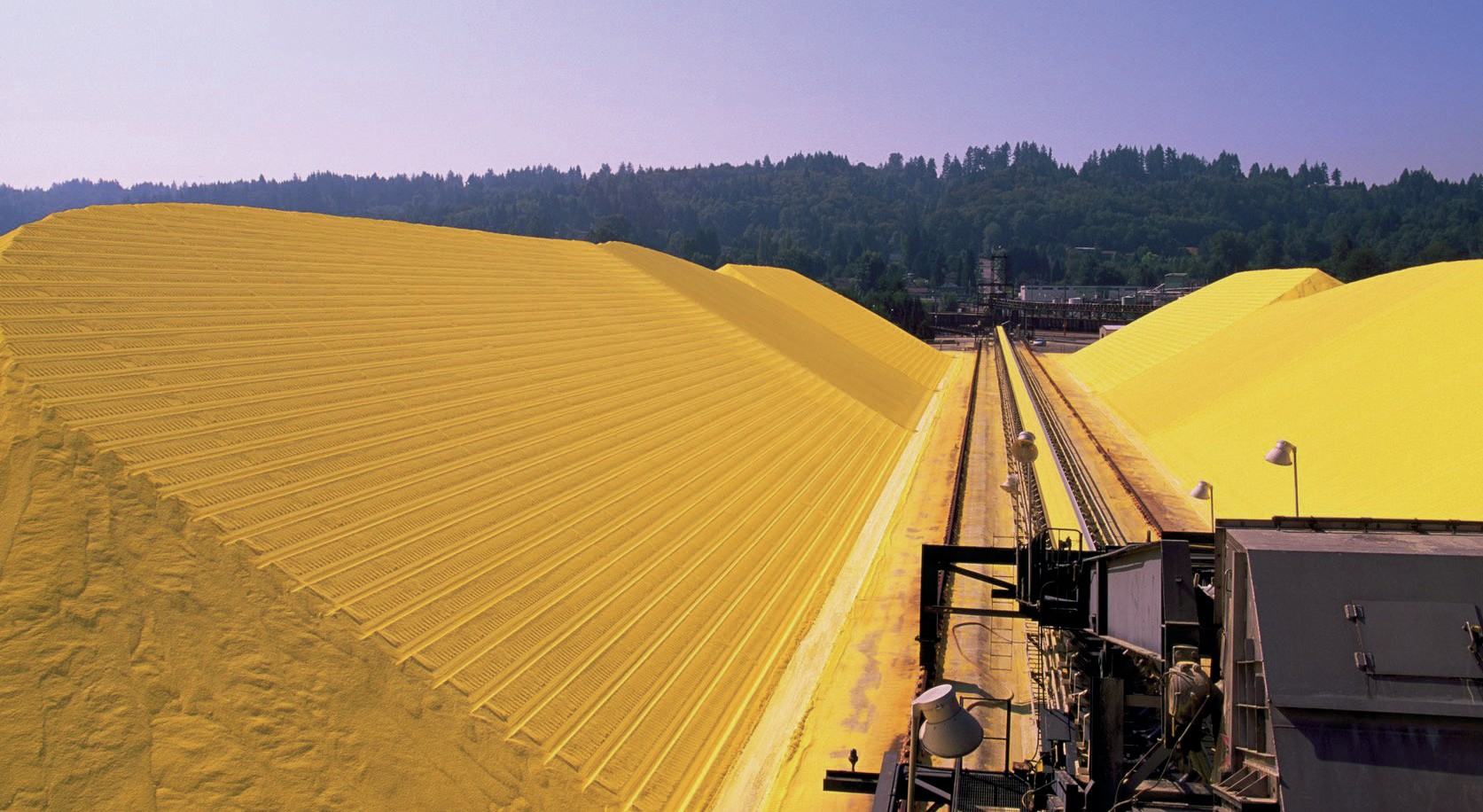
Canada was the world’s fifth largest producer of sulphur in 2023, at 4.52 million t/a. More importantly, it was the second largest exporter, behind only the UAE, with a total of 4.01 million t/a of sulphur exported. While it is not the dominant player that it once was, its exports are comparable to those of Saudi Arabia or Kazakhstan. In spite of falling volumes being recovered from declining sour gas fields, increased recovery from oil sands production have so far by and large balanced this, but falling recovery from oil production may see it slip into third or fourth place in export terms in the next few years. Canada’s reservoir of long term sulphur stocks remains a potential wild card for the market however.
Canada’s elemental sulphur production has three main components; refining, mainly in the east of the country; sour gas processing, mainly in the provinces of Alberta and British Columbia in western Canada; and production from processing and upgrading of oil sands bitumen, almost exclusively in northern Alberta, as well as some production in British Columbia.
Oil refining
Canada is the world’s fourth largest oil producer after the US, Russia and Saudi Arabia, averaging 5.5 million barrels per day in 2022, representing 5.9 % of global oil production, and its reserves, at least if the oil sands patch is included (representing as it does 97% of Canada’s oil/oil equivalent reserves), are the third largest in the world at 170 billion barrels, representing 10% of the world’s oil reserves. Canadian oil production has been on a steadily rising trend for many years, climbing from 2.1 million bbl/d of production in 2000 to its present figure. Production has risen by 60% since 2010. The country’s oil/oil equivalent production is split into two main areas – conventional oil production and oil sands mining and processing. Conventional oil production, including gas condensates, has remained relatively steady over the past two decades at around 1.5 million bbl/d. All of the growth during that time has come from oil sands production, which now represents 65% of Canadian oil production, and most of its exports.
Canadian domestic demand for oil is about 2.4 million bbl/d, mostly (around 1.7 million bbl/d) to feed its refining sector, which provides most of Canada’s demand for refined products (the rest is imported from the US, though some product also goes the other way). Consequently, as domestic oil production outstrips demand by over 3 million bbl/d, most of the oil, especially from the oil sands patch, is exported, mainly across the border south to the United States. A total of 4.0 million bbl/d of oil was exported in 2022, but a further 0.5 million bbl/d was imported, mainly into eastern Canada from the northeastern US, for a net 3.5 million bbl/d of exports. Most of this was diluted bitumen (‘dilbit’) from the oil sands.
Downstream, Canada’s domestic refining capacity is relatively small; there are 16 refineries operational in Canada (including two bitumen refineries), with a total capacity of 1.9 million barrels per day, and an average utilisation of 89% in 2022. Refineries in eastern Canada and Quebec are dependent on imported crudes and tend to process a more diverse crude slate than their counterparts in western Canada and Ontario. Eastern refineries’ input is split roughly evenly between conventional, light sweet crude, is medium sulphur, heavy crude oil, and sour and/or heavy crude oil. In western Canada and Ontario, it is around 50% conventional light, sweet crude and 25% synthetic crude oil from bitumen.
Oil sands processing
Increasingly, Canada relies upon oil sands bitumen for its oil production. Most of the oil sands mines are in northern Alberta. Mining was originally by open cast recovery of deposits close to the surface, but increasingly extraction relies upon so-called in situ recovery. This involves pumping steam down into underground deposits to soften and melt the bitumen and draw it back out. This method, steam assisted gravity drainage (SAGD), now represents just over 50% of all extraction, and it is likely to become increasingly used, as 80% of all deposits are too deep to be recovered using open pit mining. This causes some controversy, as the energy required to melt and recover in situ deposits, most of that energy coming from burning natural gas, makes oil sands bitumen one of the most carbon intensive forms of oil, roughly 30% more so than US production. This has led to increasing pressure on the industry to reduce its carbon footprint, and carbon capture and storage (CCS) and even nuclear power to generate steam have been suggested as alternatives, and the Federal government is looking at an emissions cap on the industry. There are also carbon taxes within Canada, but as in industry subject to ‘carbon leakage’ (ie moving to less regulated locations), around 80% of this cost is refunded by the government at present. Nevertheless, it has spurred efficiency improvements from producers.
The largest carbon capture project is a joint venture between the major oil sands producers; Canadian Natural Resources, Cenovus Energy, Imperial Oil, Suncor Energy, ConocoPhillips Canada and MEG Energy. It aims to develop a capture and storage network to carry an estimated 1.1 billion liquid tonnes of CO2 from more than 20 oil sands facilities to an underground storage hub in northeast Alberta. However, this has faced cost hurdles even with government tax credits modelled on the US Inflation Reduction Act, and while front end engineering and design work is said to be complete, its planned start-up date of 2026 looks very optimistic to say the least.
After mining, the bitumen is either ‘upgraded’ to produce synthetic crude oil (‘syncrude’), or diluted with lighter fractions such as naphtha to produce a ‘dilbit’ (dilute bitumen) or with syncrude to create a ‘synbit’. These are light enough to be pumped, and so can be exported by pipeline or rail. Around 15% is upgraded at present. Oil sands oil production has been rising slowly but steadily, aside from a covid-related dip in 2020. Production is up 10% since 2018, reaching 3.5 million bbl/d in 2023.
As oil sands are sulphur rich (about 4-5% by weight), where this production is processed is of vital importance to the sulphur industry. Most Canadian oil sands production is exported directly to the US, by rail or pipeline, without being upgraded. Bottlenecks in cross-border transit capacity have been exacerbated by long-running disputes over export pipelines like Keystone XL. But these constraints continue to ease. Meanwhile the new Trans-Mountain Pipeline will begin operations on May 1st this year, adding an extra 600,000 bbl/d of export capacity via west coast ports. All of this should see more oil sands bitumen exported over the next few years. In spite of this, domestic sulphur production has been rising as new upgraders come on stream. Oil sands processing in Alberta generated about 2.6 million t/a of sulphur in 2023.
Sour gas
North American sour gas production is mainly concentrated in western Canada, in particular the Western Canadian Sedimentary Basin (WCSB), which extends from Saskatchewan across northern Alberta and British Columbia and up into the Northwest Territories. Sour gas exploitation was pioneered in Western Canada, and sulphur production began at Jumping Pound, Alberta in 1951.
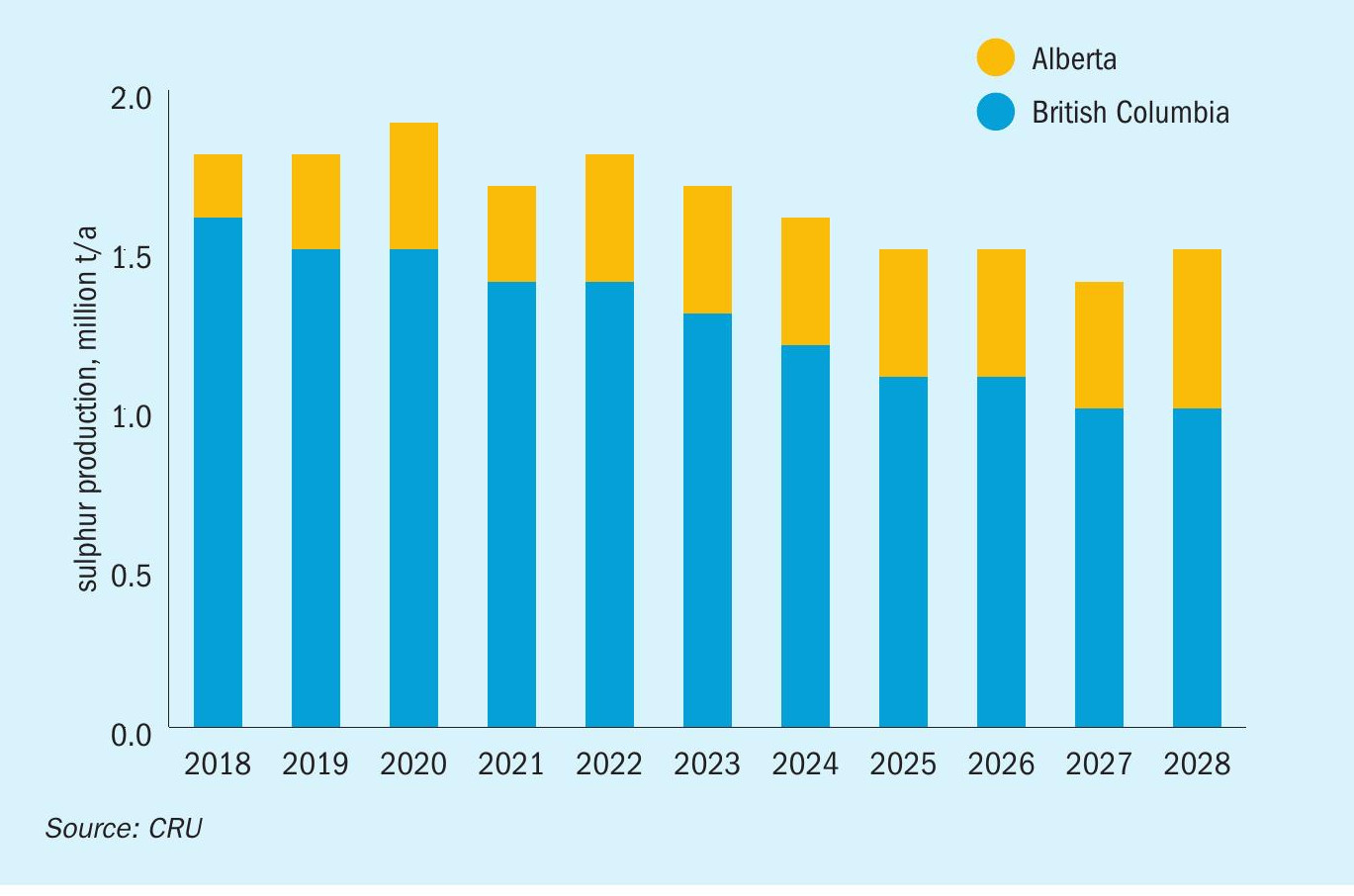
Most of Canada’s sour gas boom is well and truly over now, with sour gas wells in Alberta declining and most new production coming from unconventional (shale gas) production. However, there is some new production coming from British Columbia. Overall, sulphur recovery from sour gas processing was 1.3 million t/a in Alberta in 2023, and 0.4 million t/a from British Columbia. Over the next few years, output from Alberta is expected to continue to decline to around 1.0 million t/a by 2028, with output from British Columbia increasing slightly to just under 0.5 million t/a.
Sulphur markets
Domestic demand for sulphur in Canada is relatively low, totalling about 630,000 t/a. While the country is a major producer of potash, it has never really developed the phosphate mining industry that its larger neighbour to the south has, and the last phosphoric acid plant closed down in 2019. Sulphur consumption is mainly for industrial uses and some ammonium sulphate production.
Ariane Phosphates has for some years been developing a phosphate mine and beneficiation complex at Lac a Paul in Quebec, which would produce 3 million t/a of phosphate concentrate at capacity. It has also been looking at downstream phosphoric acid production at Belledune in New Brunswick, using sulphuric acid from Glencore’s Brunswick lead smelter to process 1.4 million t/a of the phosphate concentrate from the mine. Most recently it has begun a feasibility study into a purified phosphoric acid plant to feed lithium iron phosphate battery production. However, there is as yet no on-stream date for these project.
Exports
Canadian sulphur production was about 4.5 million t/a in 2023, with about 1.7 million t/a coming from sour gas processing and 2.6 million t/a from oil sands upgrading, plus 0.2 million t/a from conventional refining. Canadian domestic consumption runs at about 0.6 million t/a, leading to a surplus of 3.9 million t/a, most of which is exported. In 2023, 4.1 million t/a of sulphur was exported, around 1.3 million t/a was exported south to the US, mainly as molten sulphur, while 2.8 million t/a was exported via Vancouver port. Around 0.2 million t/a of this export was from stock drawdowns, at both oil sands and sour gas producers.
Generally Canada has exported molten sulphur south to the US market for phosphate production, but demand continues to fall, as the US phosphate industry shrinks and new import options like the New Wales sulphur melter put pressure on Canadian supplies. This in turn has pushed Canada towards more sulphur forming projects, allowing for greater flexibility in export. Over the medium term, CRU expects that exports will continue to be in the range 3.8-4.2 million t/a, depending on pricing, stock build and stock draw down.