Fertilizer International 520 May-Jun 2024
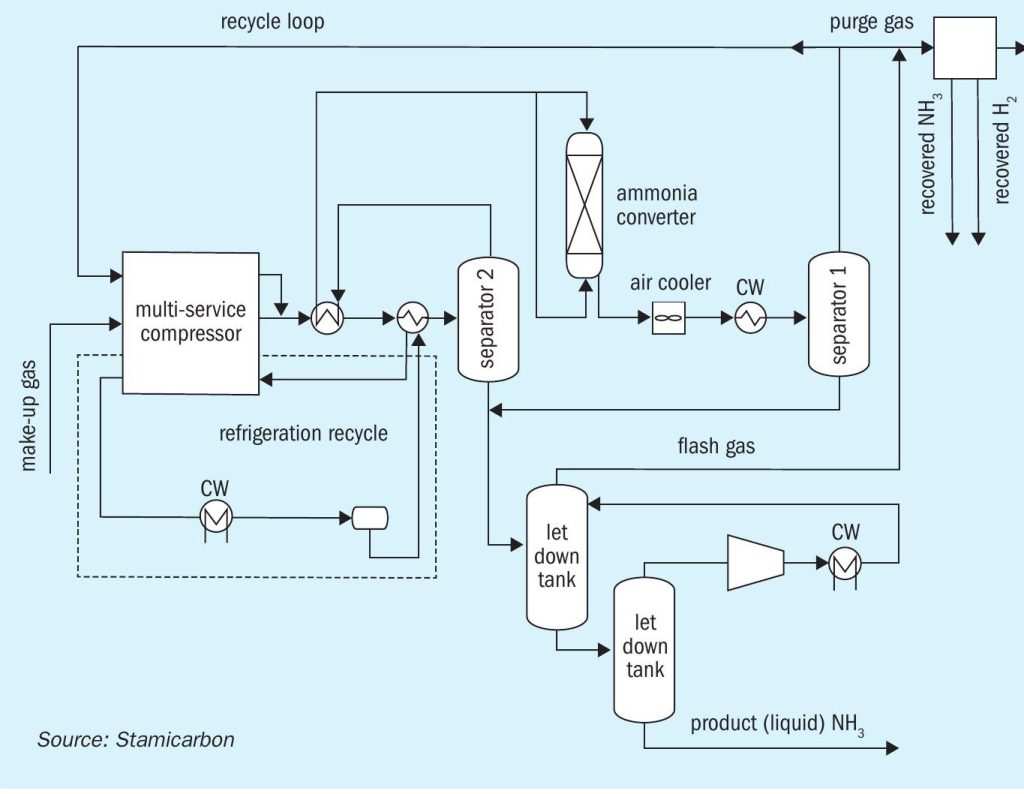
31 May 2024
One-stop shop for green fertilizer technologies
LOW-CARBON AMMONIA PROJECTS
One-stop shop for green fertilizer technologies
The need for immediate climate action and cuts in carbon emissions has never been more urgent, especially in a world where ecosystems are increasingly under threat. The production of green fertilizers offers a clear route to achieving these goals by decreasing the chemical industry’s reliance on fossil fuels. Stamicarbon’s Carmen Perez, Rolf Postma and Nikolay Ketov outline the company’s innovative and integrated approach to green fertilizer technology.
Introduction
Combining ammonia production using renewable power with the most efficient fertilizer technology is a promising green production pathway. Indeed, Stamicarbon, the nitrogen technology licensor of MAIRE engineering group, believes this approach can improve agricultural sustainability and deliver humanity’s food needs while preserving the planet for future generations. The company is actively contributing to the transition to green fertilizers by advancing a suite of technologies that can be integrated and customised to design energy-efficient, carbon-free production plants.
In this article, we will explore the innovative world of green fertilizer technology and examine its potential to revolutionise fertilizer production. We also highlight the synergies made possible when adopting a unified approach from a single technology licensor.
Green ammonia to fertilizers
Ammonia is produced on an enormous scale globally and plays a crucial role in fertilizer production. Achieving fertilizer industry climate goals will therefore depend on the sustainable synthesis of this fundamental basic chemical in future.
Currently, the reliance of ammonia production on fossil fuel feedstocks leads to large-scale greenhouse gas (GHG) emissions. Nonetheless, there is a viable route to a more sustainable ammonia industry.
The most promising pathway, in the view of many industry leaders and regulators globally, is the shift to green hydrogen and green ammonia production. The starting point for both these products is water electrolysis powered by renewable energy generated by wind, solar, geothermal or hydroelectric sources.
The electrolysis process, by splitting water into hydrogen and oxygen, provides a carbon-free feedstock for ammonia production. This production pathway, because it uses proven and readily-available technology, is increasingly being seen as one of the most practical routes for transitioning to carbon-free ammonia production.
Despite this, an immediate green ammonia transition on a global scale is not yet possible. This is primarily due to the limited availability and high cost of renewable electricity and other challenges such as a shortage of suitable electrolysers.
These factors have acted as a roadblock to change and have left pioneering green ammonia companies with many unanswered questions. This is especially true of market entrants wishing to develop ‘power-to-X’ plants – where the X refers to a range of potential final products. These can include fertilizers, fuels or an intermediate energy carrier used in transport and trading.
There are also additional technological challenges when adapting conventional ammonia production plants – originally designed to consume fossil fuels – to accommodate renewable feedstocks. Successful modification of these existing production assets will be crucial for the efficient and economically viable shift to green ammonia production. Managing the intermittent nature of renewable energy supply is another challenge, as the storage options for green electricity and green hydrogen are generally expensive.
Despite these hurdles, green ammonia technology can be a viable and practical option in certain markets and regions globally. In Stamicarbon’s view, a shift to medium-scale sustainable fertilizer production, tailored to local needs, can be a practical first step toward a carbon-free future, especially in areas rich in renewable energy resources and with a high demand for fertilizer. This strategy promotes the sustainable agricultural use of fertilizers, supports global environmental goals by eliminating fossil fuel reliance, and can reduce a country’s dependency on fertilizer imports.
Stamicarbon has introduced Stami Green Ammonia technology to address and overcome the technical challenges associated with carbon-free production. Green ammonia plants designed using this innovative technology can effectively handle the fluctuating nature of renewable energy sources while also offering lower capital expenditure (capex) and operational costs (opex).
Features of Stami Green Ammonia design
Stamicarbon has developed a new market standard – focused on medium-scale production plants – to address the growing demand for sustainable ammonia. Stami Green Ammonia is based on a modified high-pressure ammonia synthesis loop operating at approximately 300 bar (Figure 1). This optimised layout is ideal for plants that rely on green feedstocks and have capacities ranging from 50-500 t/d.
Hydrogen and nitrogen make-up gas for the ammonia synthesis unit is generated from the upstream electrolysers and nitrogen generation unit. This is then compressed to a pressure of over 300 bar by an electrically-driven, multi-service reciprocating compressor. The same compressor is also responsible for recompressing the recycle stream containing unconverted gas and managing the refrigeration loop.
The high-pressure synthesis loop enables single-stage condensation of ammonia using cooling water. Eliminating the need for a dedicated refrigerating compressor, by minimising equipment requirements, delivers a 25-30 percent capex saving – an essential cost reduction given the absence of economies of scale for a plant of this size.
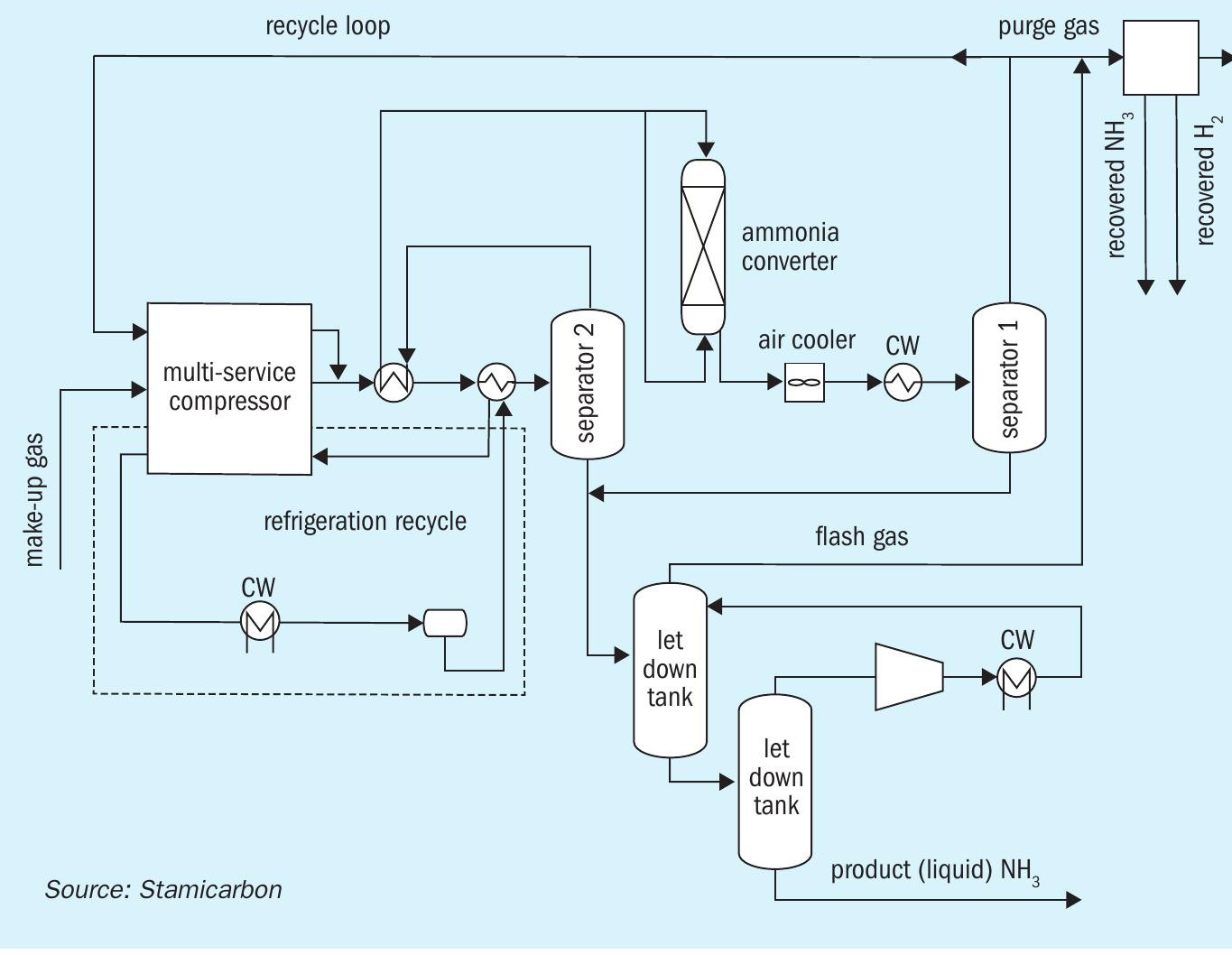
More than 70 percent of ammonia is recovered in separator 1 with the remaining 30 percent condensed in separator 2. The second separator is placed upstream of the converter to protect the catalyst by condensing out contaminants (mainly water) from the make-up gas.
High-pressure conditions within the synthesis loop enable the use of a smaller reactor and a lower catalyst volume. A single-bed axial-flow ammonia converter with a tubular design is used. The feed is pre-heated to the temperature necessary for catalytic activity by capturing heat from the exothermic ammonia synthesis reaction.
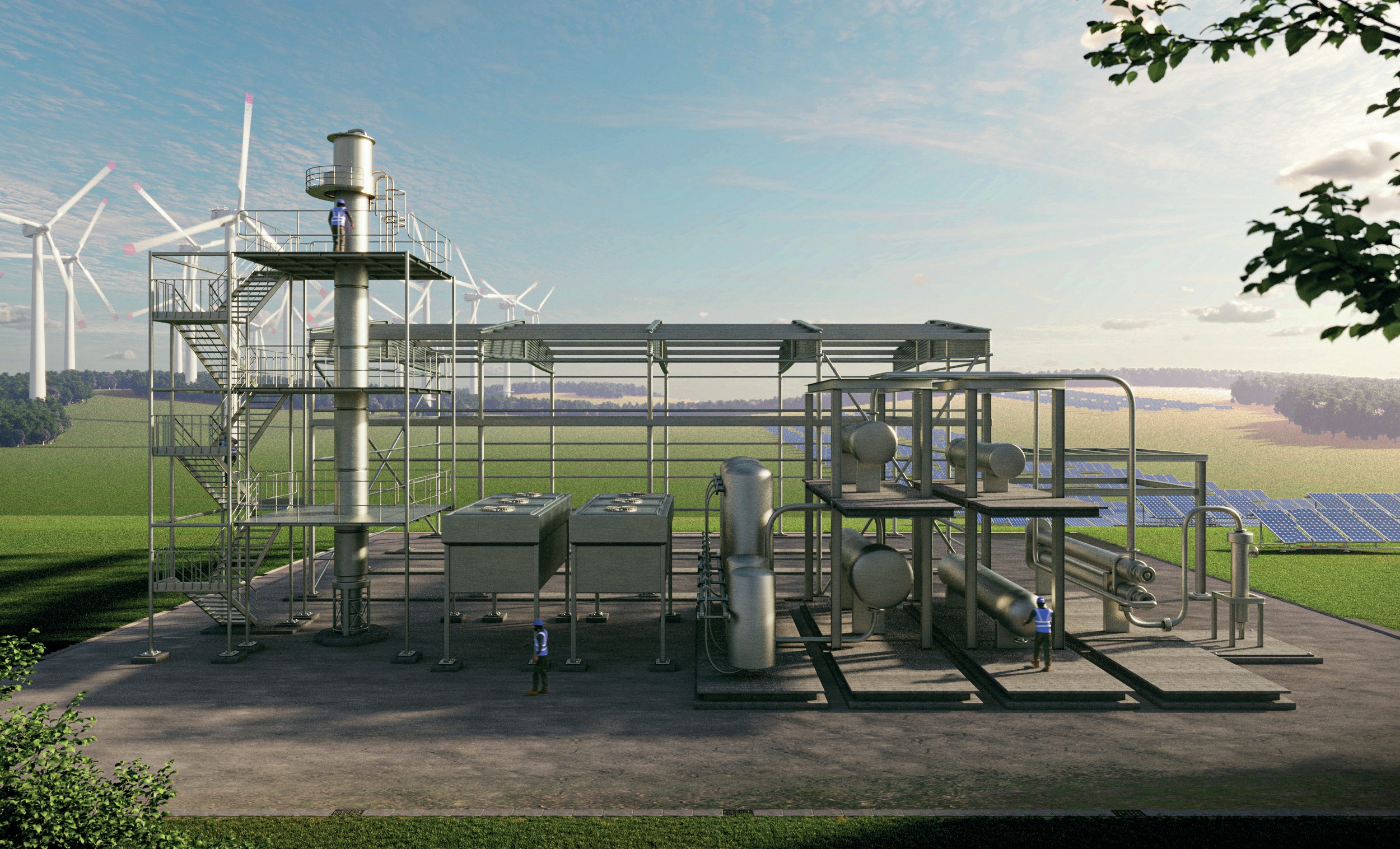
A heater integrated within the ammonia converter is also used during start-up.
The green ammonia plant (Figure 2) uses between 25-250 MW of power, depending on its capacity. Plant footprint varies, being about 15×30 metres for smaller scale units with this increasing to 50×50 metres for larger scale units.
The plant can generate green ammonia for atmospheric storage at ambient pressure and a temperature of -33°C. Alternatively, ammonia can be produced under pressurised conditions (16–18 bar) at ambient temperature for storage or direct use in a downstream production plant.
Stamicarbon’s nitic acid process
When setting up a fertilizer plant, the goal is to optimise energy recovery while keeping investment costs low.
Stamicarbon’s nitric acid technology offers high energy efficiency and reliable operation, being designed to minimise heat losses and maximise the recovery of heat from process streams. Greenhouse gas emissions are also minimal due to its tail gas treatment system.
The technology, which has either a mono- or dual-pressure design, uses the Ostwald production process to convert ammonia to nitric acid in two steps: l Step 1: The oxidation of ammonia (NH3 ) to form nitric oxide (NO), which is further oxidized to nitrogen dioxide (NO2 ) l Step 2: The absorption of the nitrogen dioxide (NO2 ) in water (H2 O) to form nitric acid (HNO3 ).
In the mono-pressure process, oxidation and absorption sections operate at the same pressure level (Figure 3). The dual-pressure process, in contrast, by using different pressure levels in the oxidation (4-6 bar) and absorption sections (8-12 bar), combines the advantages of medium-pressure combustion with the efficiency of high-pressure absorption (Figure 4).
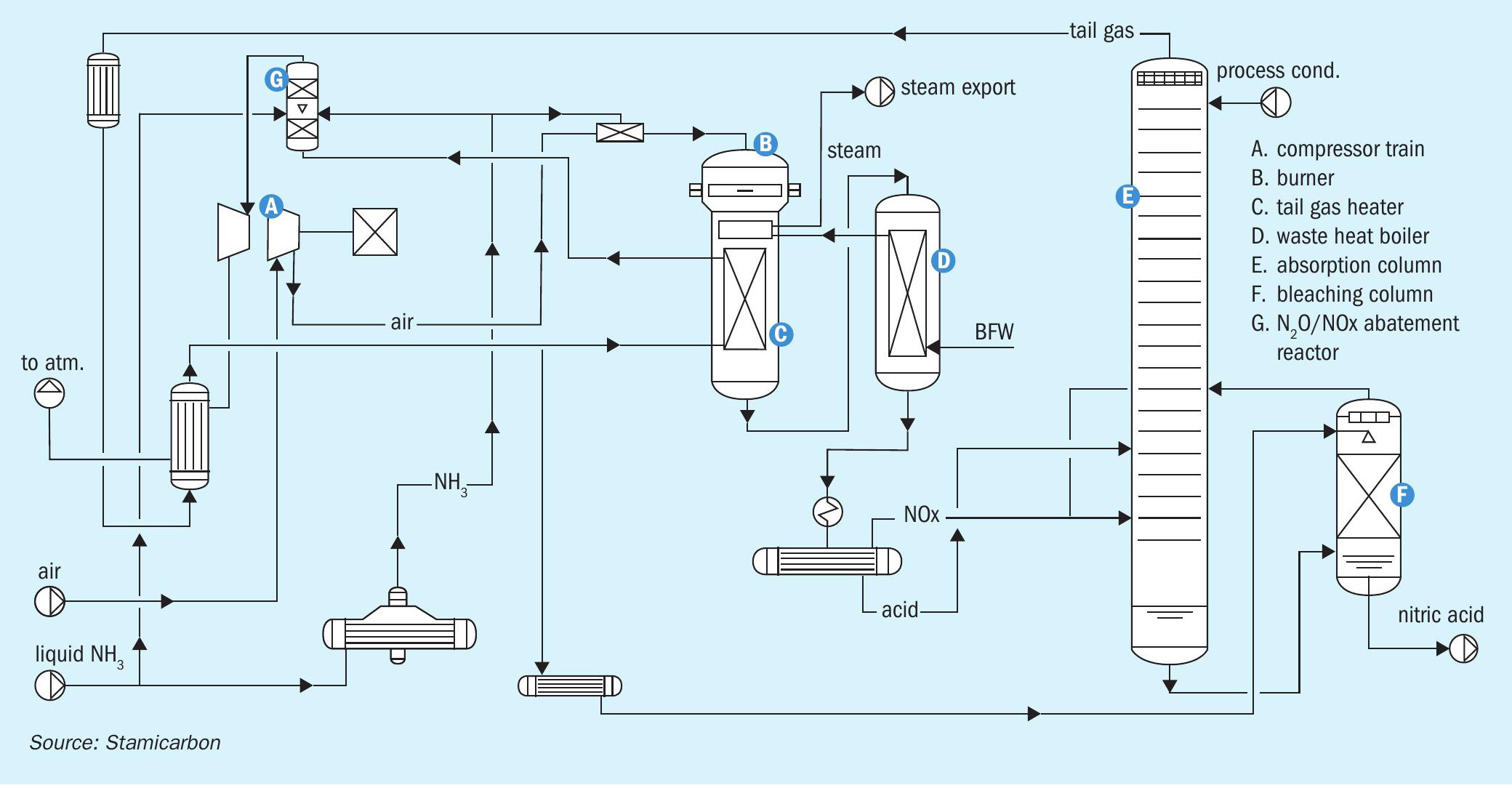
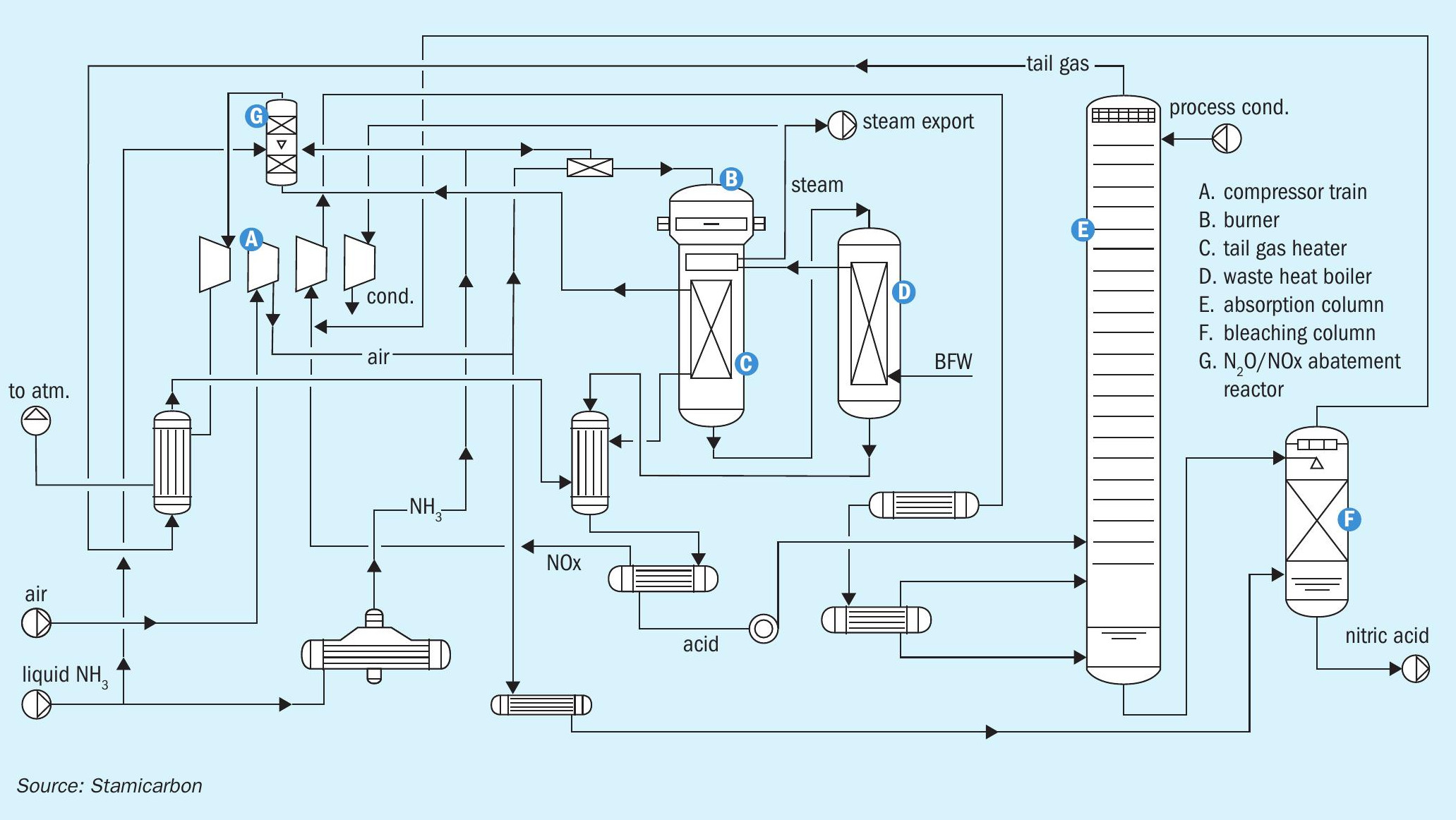
The standout feature of Stamicarbon’s nitric acid technology is its exceptional steam generation capabilities. This adds significant value particularly under favourable pressure and temperature conditions. Overall, Stamicarbon’s nitric acid plant design provides guarantees on: steam export, N2 O/NOx emissions, cooling water consumption, acid quality, and ammonia consumption.
A mono- or dual-pressure nitric acid plant can be integrated efficiently within a larger urea ammonium nitrate (UAN) production complex (Figure 5). The resulting green fertilizer complex can include a green ammonia plant, a nitric acid plant and other units such as a urea solution plant, an ammonium nitrate solution plant, and a UAN mixing plant.
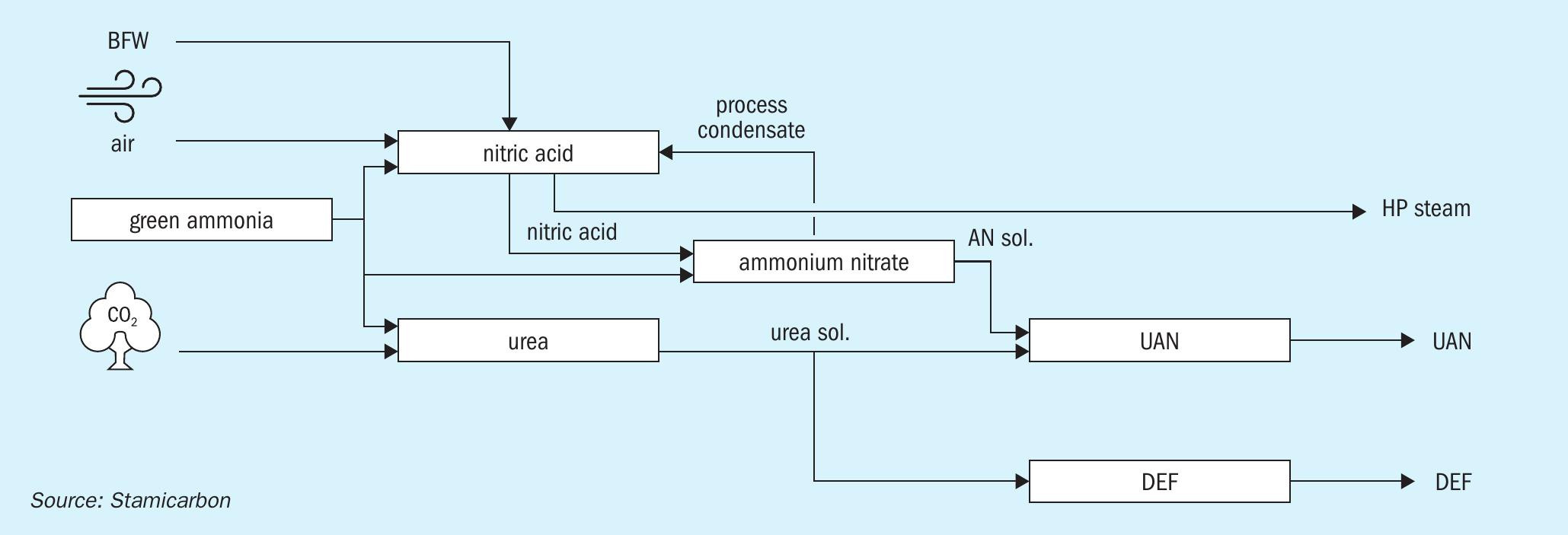
Having a portfolio of technologies for green ammonia, urea, nitric acid and ammonium nitrate allows Stamicarbon to improve the integration of individual plants and make the complex more economically attractive.
Stamicarbon is continuously evaluating options for improving the integration of green ammonia and nitric acid technologies. One promising option involves integrating oxygen generated by water electrolysis and the nitrogen generation unit (Figure 1) into the nitric acid plant.
This can be accomplished in several ways. When the ammonia feed for the nitric acid plant is sourced from a green ammonia plant, for example, oxygen from the electrolysers could replace a portion of the air-supplied oxygen in the nitric acid process. The addition of air sourced from recirculated tail gas (Figure 6) would also be necessary to ensure that the ammonia and oxygen mixture upstream of the burner remains below the explosive limit.
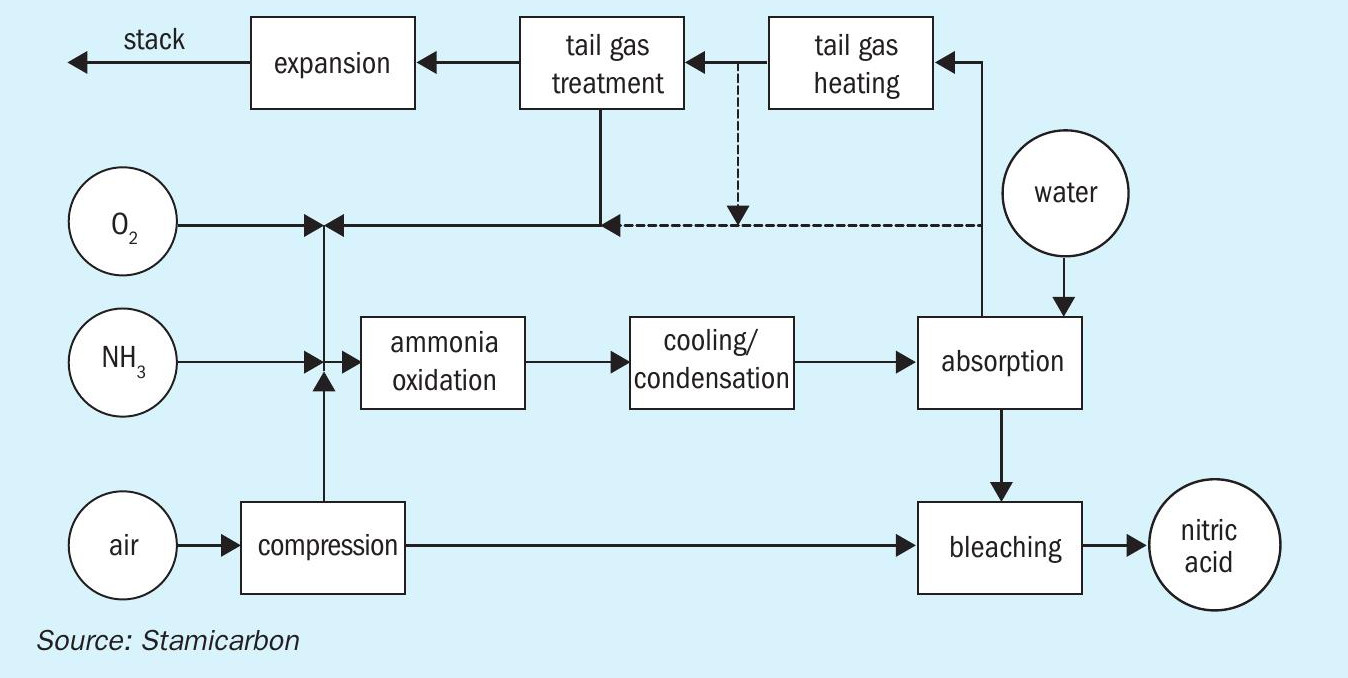
Integration offers the following key advantages versus the standard nitric acid process:
- Recirculating a portion of the tail gas reduces emissions, with the total flow of NOx and N2 O released into the environment cut by about 40 percent.
- Catalyst demand is reduced due to the lower flow rate of the abatement system.
- A smaller cross-section reduces the total catalyst volume by up to 40 percent.
- Use of a lower power compressor increases steam export by more than 30 percent.
- Capex is reduced thanks to the use of a smaller compressor unit and expander and the lower amount of catalyst used in abatement.
- The potential for increased conversion efficiency by looping NOx gases back into the reaction, via the burner, the bleacher, or both.
Capitalising on process integration
Integrating the oxygen stream into standard mono- or dual-pressure nitric acid technology can deliver capex and opex savings.
Opex benefits include the increase in steam export and lower N2 O emissions. N2 O reductions, when converted into their CO2 equivalent, can deliver operational cost savings.
Overall, process integration, based on local prices and considering only the increase in steam export, can yield a cost reduction of more than $5/t of nitric acid, compared to the standard mono-pressure nitric acid concept. This is equivalent to an annual saving of more than one million US dollars for a 450 t/d nitric acid plant.
Additionally, carbon taxes are being introduced and carbon capture is being monetised in an increasing number of countries and regions. Because of this, the integrated process – by converting cuts to atmospheric N2 O emissions into CO2 equivalents – could potentially deliver cost reductions for a 450 t/d nitric acid plant of more than one percent of total operational costs. The application of carbon taxes in more locations and at higher rates suggest operational costs could be reduced even further in future.
Overall, Stamicarbon’s complete technology package for a green fertilizer complex is a competitive option for the local production of a high-value products and has significant potential in a carbon-free economy. Having a single licensor provide all of the technology for a green fertilizer complex can also streamline process integration, reduce emissions, simplify maintenance and – ultimately – maximise operational efficiency.
Conclusion
Supplying crop nutrients to meet rising global food demand, while simultaneously reducing the environmental impacts of fertilizer production, is a critical challenge. In response, the nitrogen fertilizer industry is developing and introducing new green technologies based on fossil-free feedstocks as part of the shift to towards more productive and sustainable agricultural systems.
Case study: grassroots green fertilizer complex in Nebraska
In 2023, a prominent North American fertilizer producer awarded MAIRE group, through Stamicarbon, licensing and basic engineering design contracts for a 450 t/d capacity green ammonia plant in Gothenburg, Nebraska.
This milestone contract was secured thanks to the capabilities of two MAIRE business units: Sustainable Technology Solutions led by NEXTCHEM and Integrated Engineering & Construction Solutions through KT-Kinetics Technology. Tecnimont USA’s knowledge of the local supply chain and construction market was also a key factor that helped secure this award.
The Gothenburg fertilizer complex will be the first to use Stami Green Ammonia technology for nitrogen fertilizer production from renewable feedstocks. It is expected to start up in 2026. Additionally, the complex will be the first to integrate Stamicarbon’s technologies for urea, nitric acid and ammonium nitrate.
The design package for the fertilizer complex includes a 450 t/d capacity green ammonia plant and a 330 t/d capacity nitric acid plant. This will be integrated with a urea section, neutralisation section and UAN mixing section. The nitric acid plant will operate at a constant pressure of eight bar, combining the absorption and bleaching operations in a single piece of equipment. In addition, all the high-pressure steam generated by the nitric acid plant will be exported and used in other sections of the fertilizer complex due to the absence of a steam turbine.
Once operational, the Gothenburg complex will diversify fertilizer production in the Western Corn Belt while having a negative carbon footprint. The plant will consume CO2 waste from other production facilities in the region, combine wastewater with groundwater, and use electricity from renewable sources to produce cleaner fertilizers and chemical products.
The facility, by leveraging locally produced renewable energy, has impressive projected annual production outputs. These include 365,000 tons of urea ammonium nitrate (UAN) and 146,000 tons of ammonium thiosulphate (ATS). Additionally, the plant will produce 20 million gallons of diesel exhaust fluid (DEF) annually to supply heavy-trucks in the region.
This project case study is a practical example of how an integrated production complex can incorporate key units based on Stamicarbon technology – for green ammonia, urea, nitric acid, ammonium nitrate and DEF. This one-stop shop approach optimises plant operations and achieves the lowest possible emissions, along with a high level of integration for utilities.
Globally, major fertilizer industry players are already taking significant steps towards achieving this goal. The fertilizer industry’s adoption of green technologies and practices is a strategic response to both the changing demands of global agriculture and rising environmental concerns.
Stamicarbon, as a single licensor for a green fertilizer complex integrating ammonia, urea, nitric acid, and ammonium nitrate production, is able to maximise process synergies by reducing capex, opex and the environmental footprint of plant operations.
Stamicarbon offers a combination of proven technologies with decades of experience in engineering and delivering integrated fertilizer units worldwide. As highlighted in this article, in sustainable fertilizer production, having one technology licensor covering the whole value chain offers multiple advantages. These include better process integration between different production units and improved energy efficiency. Having a single company responsible for a green fertilizer project is also simpler and can reduce project timescales.
Overall, this integrated approach will be an essential part of the industry’s successful shift to sustainable fertilizer production and meeting the dual demands of higher agricultural productivity and environmental stewardship.