Sulphur 412 May-Jun 2024
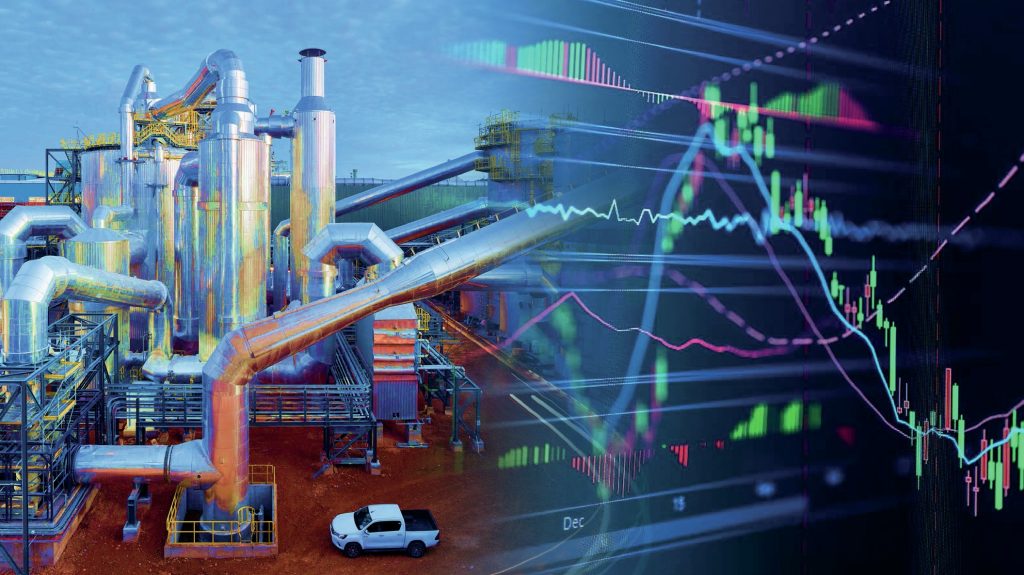
31 May 2024
Taking digitalisation to the next level
DIGITALISATION
Taking digitalisation to the next level
Digitalisation is making a strong impact in the process industry and is providing an opportunity to have a positive impact on the production KPIs. Metso’s Metals & Chemical Processing Business reviews the impact of digitalisation in the sulphuric acid industry today and discusses the concept of a future pit-to-port system within a digital eco-structure.
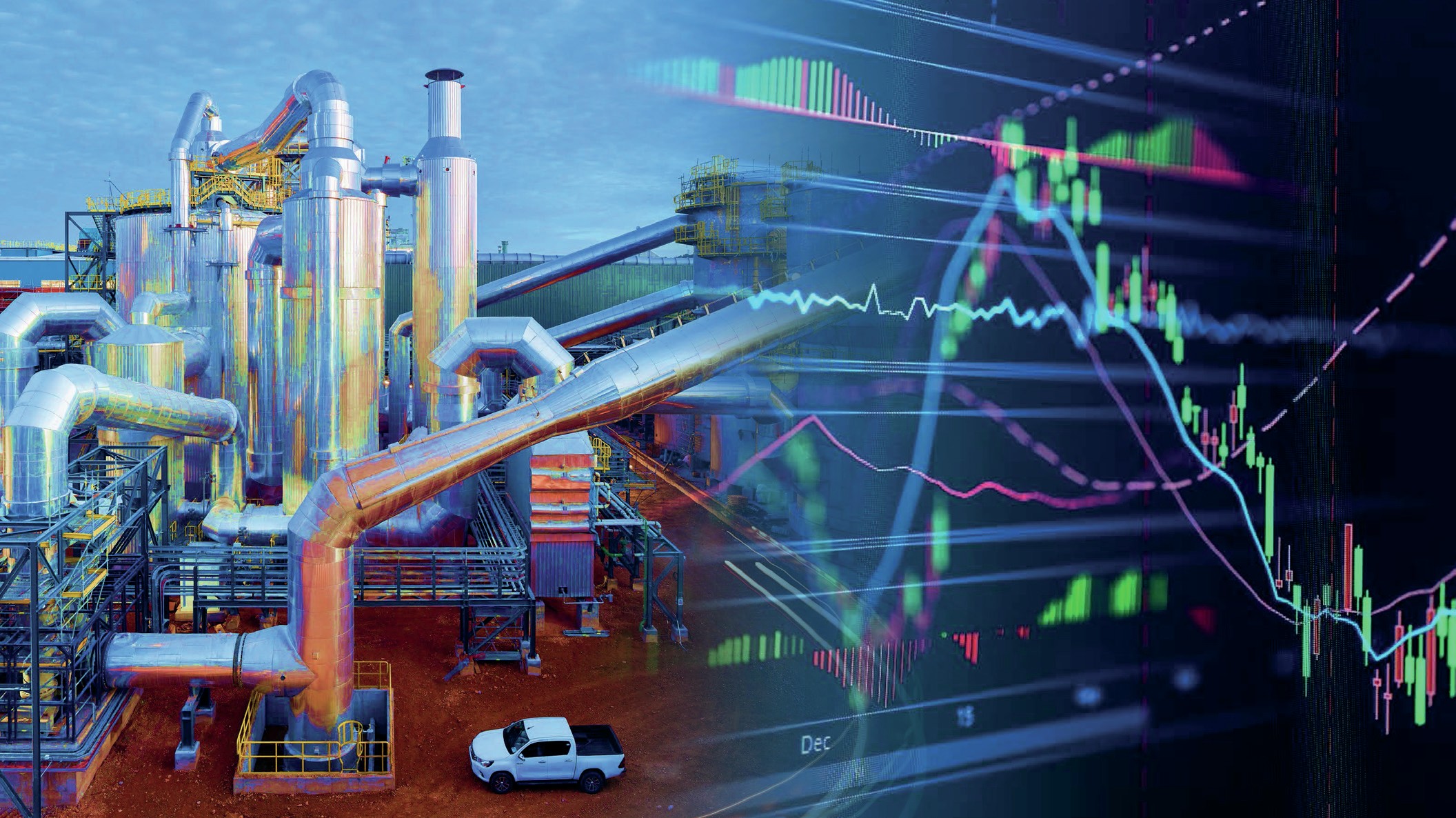
The sulphuric acid industry has been driven by almost a century of improvements in process technology and equipment design. It is expected that this trend will continue, although not at the same rate as in earlier decades and with potential change in focus to consider the challenges associated with the mega-trends such as energy transition, circularity, etc.
One key area for future development will be digitalisation. As in other industries, digitalisation has made an entry into the sulphuric acid space in recent years and today plays an entirely different role compared to classical process technology and equipment modernisations/upgrades. By utilising digital tools based on first principle process simulations, there is also the potential to harness artificial intelligence (AI).
Even though this trend is still in its infancy, it is expected to have an ever-stronger impact on the industry in the future. Current demand for transparency in Environmental, Social and Governance (ESG) topics is expected to take place and existing technologies and emerging technical advancements may well require digitalisation to meet these needs.
A further aspect is consideration of the entire ‘pit-to-port’ operation within a digital eco-structure, meaning that digitalisation will not stop at the battery limits of any one plant section or industrial function (refer to Fig. 1).
Impact of digitalisation in the process industry
Looking back at the last 20 years in digitalisation in the sulphuric acid production process, a few key milestones can be identified regarding Metso’s own digital development in the field of sulphuric acid and fluid bed technologies, and these are shown in Fig. 2.
The development of Metso’s digital tools was from the beginning focussed on first principles solutions and on translating Metso’s unique process and equipment know-how into a digital offering. As high-resolution process data upload is today a secure and safe way to allow remote support for customers, regardless of the location of site and supporting experts, the functionality has improved considerably.
The development milestones shown in Fig. 2 are only a few to exemplify the progress in the digital solutions available today. It can also be seen that the field of digitalisation covers a wide range of different operational aspects. While solutions such as process optimisers aim to increase operational efficiency (for example, of a roasting plant), remote data access targets a closer and seamless collaboration between experts from the equipment manufacturer and the operating company. Troubleshooting is thus simplified, timely, and support is provided more specifically and with a higher efficiency. In short, digital technologies play a key role to connect process industry experts around the globe.
Digitalisation is used to integrate process know-how and technology understanding into the daily operation of a process plant. Expert systems, optimisers, etc., are one way to digitalise knowhow, making the know-how immediately available when required during on-site operations. Another opportunity, followed up very recently within Metso, is to review the process instrumentation or digital readiness of a plant with the dedicated target to allow for more advanced digital solutions to be considered.
Embracing modern digitalisation solutions as described above, it becomes clear that today the road to key performance indicator (KPI) optimisation is driven by two main topics:
l First, and historically the strongest, the process and equipment technology steps were the first choice to enhance process KPIs. It must be noted, however, the huge process developments as in earlier decades cannot be expected in the future.
l Secondly, emerging in recent years and continuing with an even increasing impact, digital solutions and remote connectivity of equipment has entered the process industry. Digital solutions are starting to pay off for operating companies and are a measurable impact on production KPIs in a defined time scale. Today, further growth in demand of digital solutions driving operational KPIs can be expected and may also encompass future legislation on ESG reporting. Such solutions, targeting the production KPIs of equipment and plants, are an immediate solution now to drive the operation to higher KPIs.
Considering the ‘central processing facility’ in the pit-to-port graphic detailed in Fig. 1, there is a need to drill down into detail of the differing needs of the process value chain, plant or relevant process equipment within the facility. A simplified example is shown in Fig. 3.
It should first be noted that the graphic considers a process value chain sub system associated with an overall pyrometallurgical process but could just as well be a stand-alone sulphur-burning sulphuric acid plant feeding a fertilizer complex.
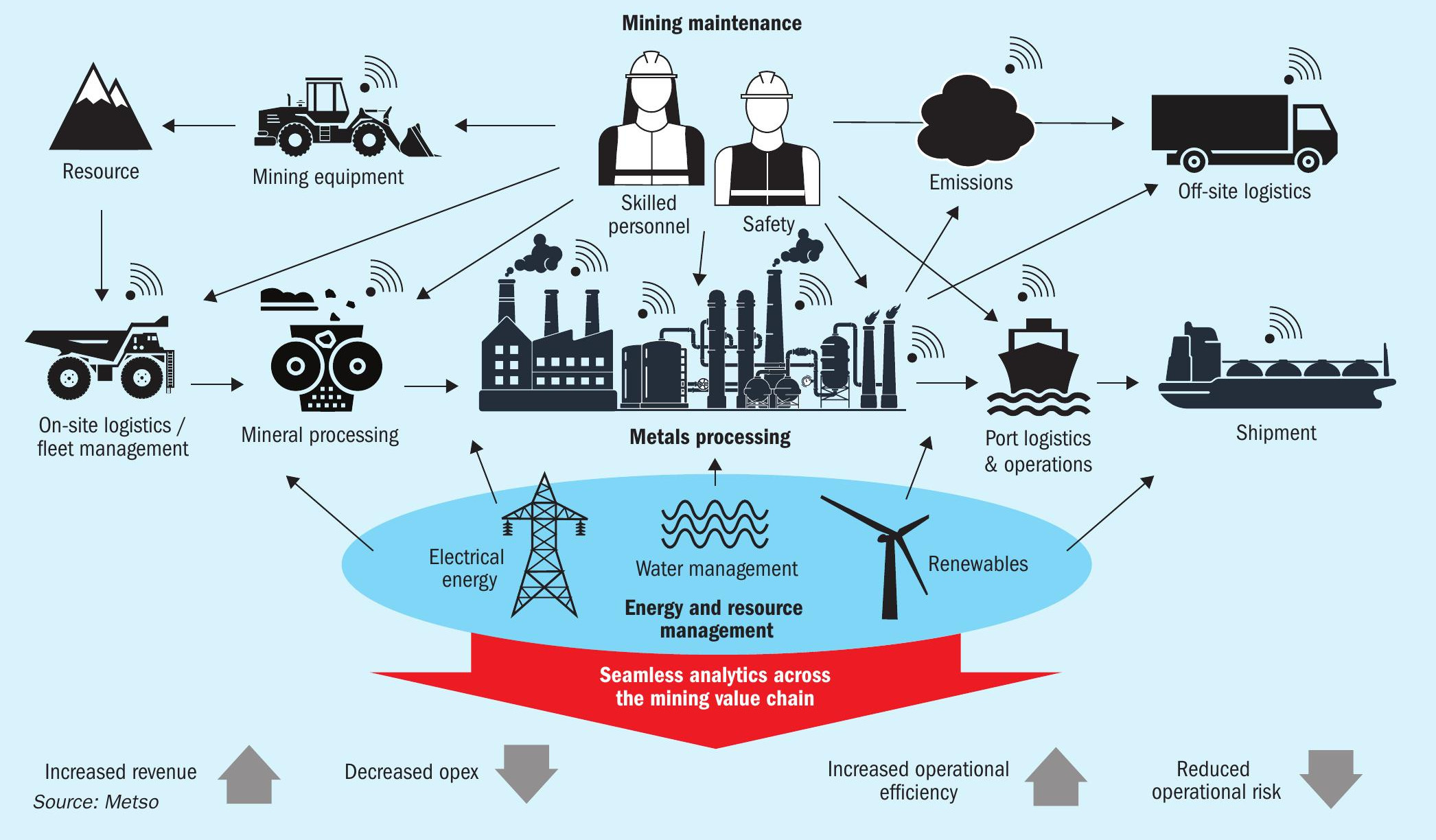
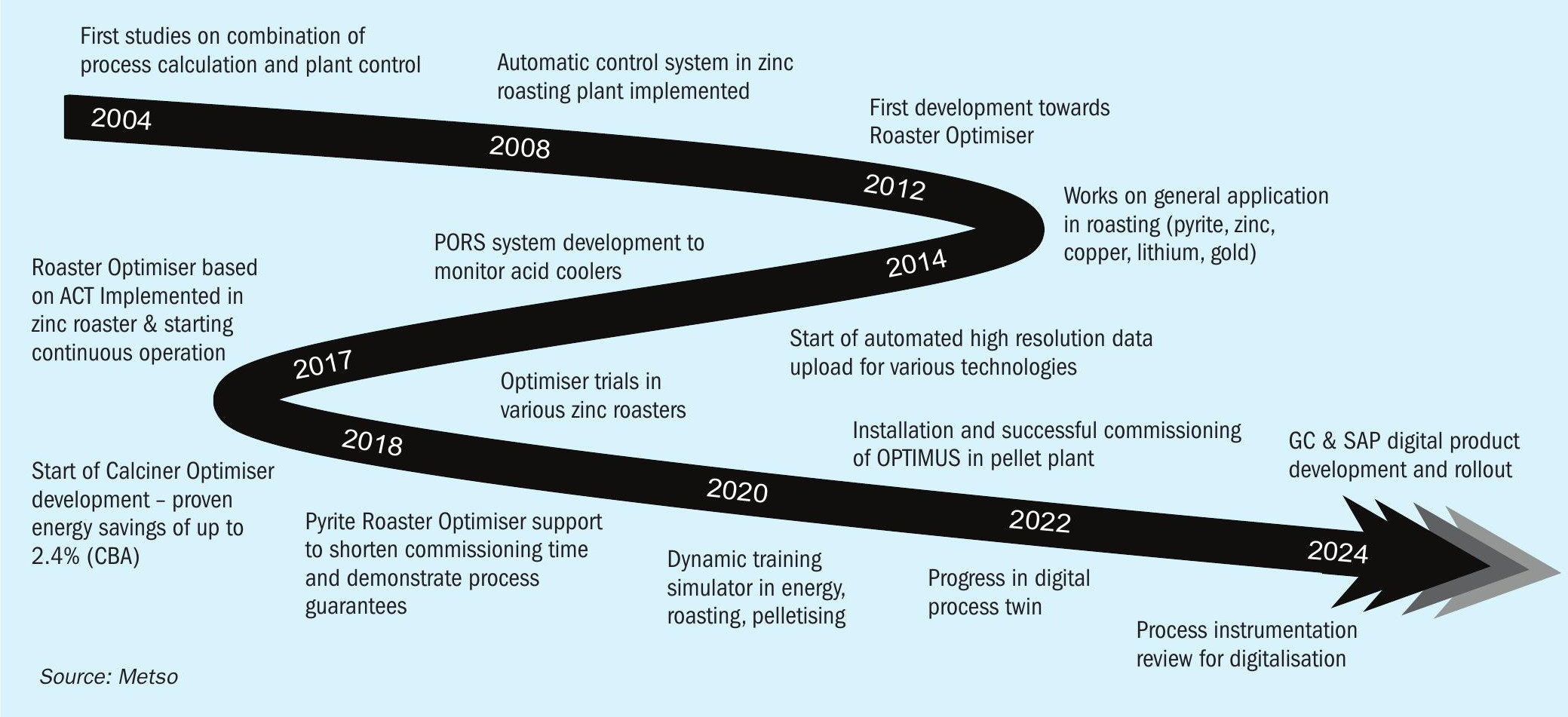
To completely enable pit-to-port digital connectivity and the associated operational and performance KPIs it is critical to drive transparency from all key individual process equipment of the plant and/or sub system.
Irrespective of the way data will be used, by way of AI or first principles tools, the greatest challenge for the current installed base of industrial plant is the understanding of the quality of data and the complexity of retrofitting the appropriate degree of instrumentation and associated data capture. This is particularly the case for older installations with limited instrumentation and control, whereas facilities built in say the past ten years may well require significantly less capital investment to attain the required degree transparency. It should also be noted that Metso’s sulphuric acid plant offerings today take into consideration the needs of digital readiness from initial flowsheet development to equipment/ plant supply. Development of new digital solutions will inevitably emanate from the execution of new greenfield projects and that these concepts in time will cascade back into the installed base.
The transition from historical upgrades of process and equipment to investments in digitalisation can also be observed in the focus of Research and Development (R&D) teams. As process development steps were dominant until a few years ago, many aspects of new developments have a focus on digitalisation today. In summary, digitalisation is making a strong impact in the process industry and is providing an opportunity to have a positive impact on the production KPIs with a surprisingly short return on investment.
As a process plant builder Metso’s digital solutions are based on process understanding, expertise and experience that has been gained over decades of plant design, construction, commissioning, and troubleshooting. This knowledge, together with remote access digital tools, can now form the basis for analysis of on-site challenges in existing facilities. Metso know-how is today digitalised in the form of process models and not only used for process plant design, but to support operations in real-time. That said this is the full extent of Metso expertise and capability and the digital eco-structure associated with a pit-to-port system requires the involvement of other capable parties.
The digital eco system of a pit-toport system
It is acknowledged that a process plant builder will not impact the digitalisation on an enterprise level. Making an impact on both the equipment/plant scale and on the wider site level will demand all stakeholders to consider partnerships and collaboration considering a ‘sharing not owning approach’. It is expected that a key for successful digital transition will require effort from providers of a digital enterprise level eco-structures. These are in use in other industry sectors today, however utilisation of digital eco-structures in the process industry cannot yet be observed. Furthermore, the ability of an end-user to accept change management for a site-wide digitalisation journey, will be an essential success factor.
The challenges of pit-to-port digitalisation in the industry is multifaceted and require careful consideration. Key hurdles include:
- Many operations still rely on outdated legacy systems and infrastructure and integrating new digital technologies can be complex and costly. Upgrading existing systems whilst ensuring minimal disruption to ongoing operations is a significant challenge.
- The industry generates vast amounts of data from sensors, equipment, geological surveys, and other sources. Managing, storing, and analysing this data efficiently is crucial. At the same time, ensuring data accuracy, consistency, and quality is challenging, especially when dealing with remote/multiple sites and diverse data formats.
- As the industry becomes more connected, the risk of cyber threats increases and protecting critical infrastructure, intellectual property, and sensitive data is essential. Implementing robust cybersecurity measures and training staff to recognise and prevent cyberattacks are ongoing challenges.
- Transitioning to digital processes requires buy-in from all levels of the organisation and resistance to change can hinder successful implementation. Training the workforce to use new tools effectively and fostering a digital culture is a high priority for success.
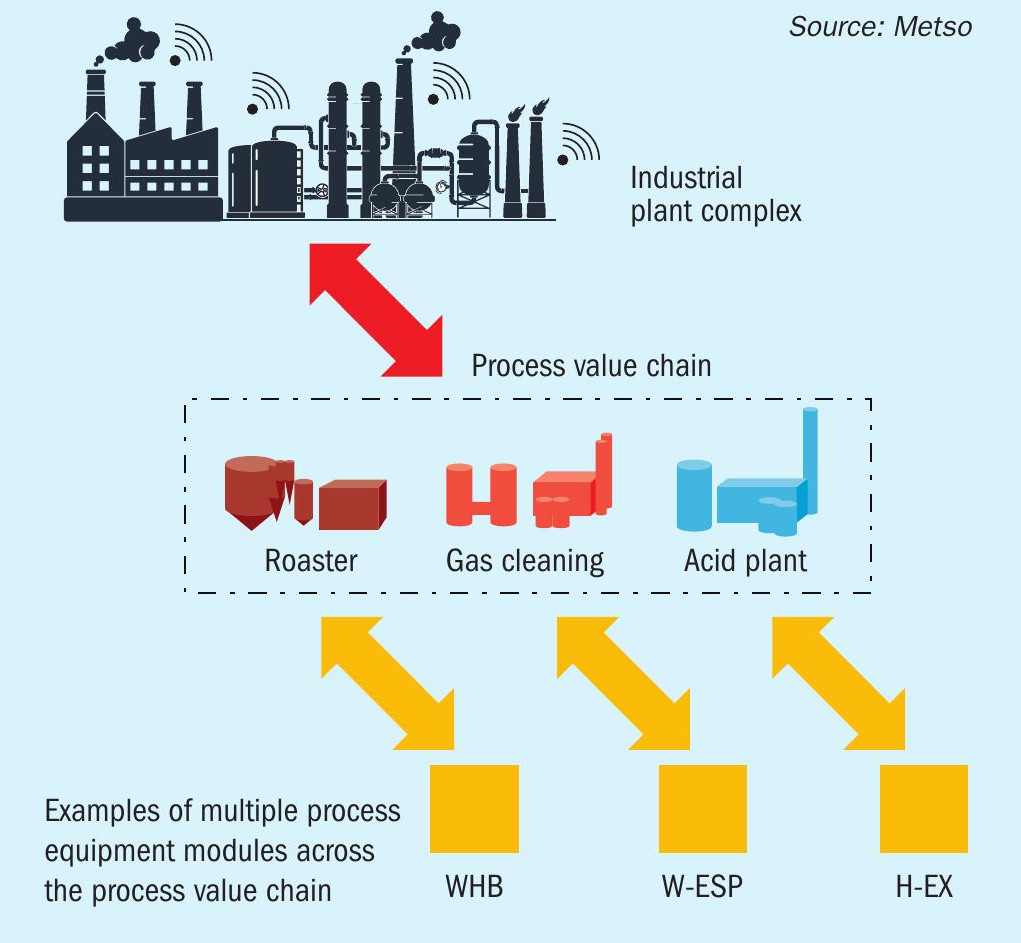
- Different enterprise software, hardware, and communication protocols often lack interoperability and integrating such diverse systems seamlessly is a challenge. Establishing enterprise standards for data exchange, communication, and interoperability is essential for efficient digitalisation.
- Investing in digital technologies can be expensive and the industry must weigh the costs against the potential benefits. Demonstrating transparent ROI and long-term value is essential to justify digitalisation investments.
- The industry must comply with various regulations related to safety, environmental impact, and the associated reporting – ensuring that digital solutions align with regulatory requirements.
- Digital solutions should be scalable to accommodate growth and changing operational needs and defining solutions that can adapt to different scenarios is essential.
- Balancing digitalisation with sustainability objectives (such as reducing energy consumption and minimising environmental impact) is critical. Ensuring that digital initiatives align with broader sustainability strategies is a challenge that needs to be met.
This extensive list of hurdles may lead some to conclude that the pit-to-port concept will never gain a foothold, however the emerging disruptor to the status quo may end up being artificial intelligence (AI) and its ability to process the massive amounts of data from multiple sources, formats and platforms (see Fig. 4). Some advanced industries are already harnessing this phenomenon and it is not beyond reality to expect that as further AI development takes place and such costs have been amortised, our industry may succumb to such tools.
Many recent consultancy reports (Accenture, McKinsey, etc.) indicate that the cost savings from such eco-structure optimisation could be significant – globally in excess of 400 billion USD in just the pit alone, and value chain logistics potentially reduced by a further 20%. These are potential savings are certainly worth considering for the blue chip leaders in our industry, allowing a digital momentum to commence for the industry as a whole.
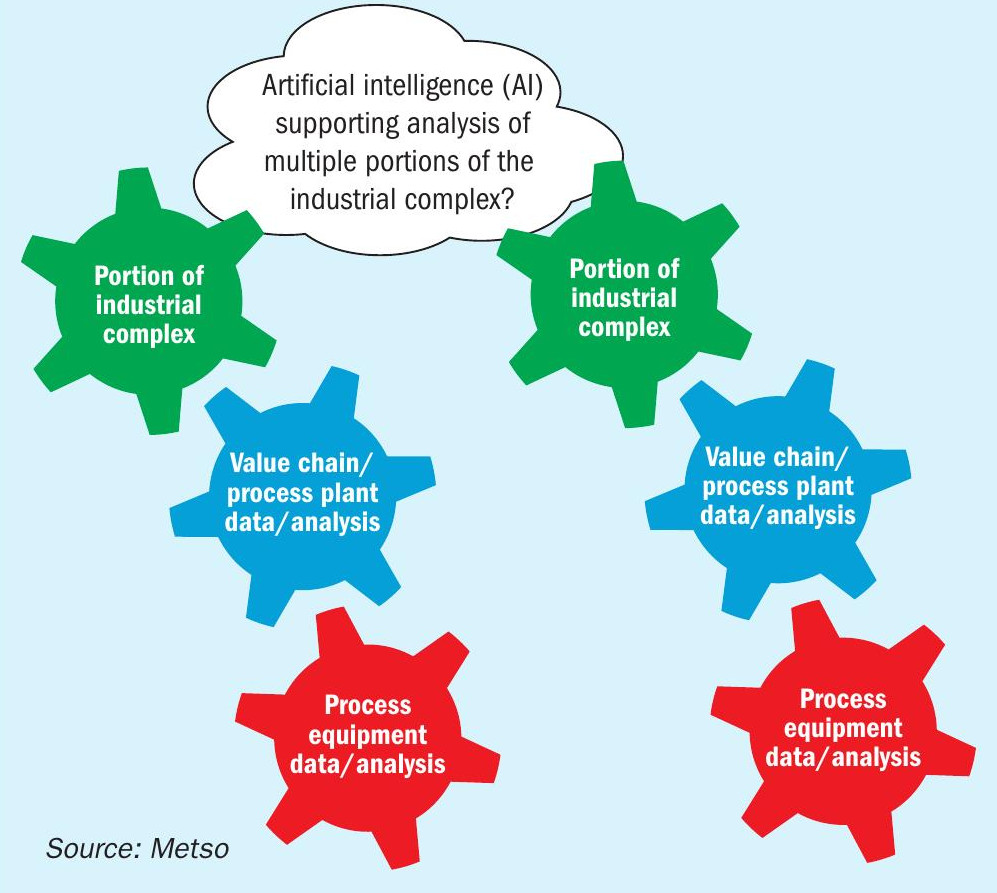
Summary
Metso is committed to further digitalisation of its portfolio of equipment and process plant offerings that is required to ensure that it is ‘digitally ready’ as momentum grows for a comprehensive digital eco-structure in the industry. Metso believes that this digital development will inevitably emanate from the execution of new greenfield projects, and that the concepts in time will cascade back into the installed base.
Process plant builders’ roots are in the field of process design and equipment design and technology. Not surprisingly, digital solutions will focus on equipment or process plants within their capability and expertise – each supplier must consider if this is strategically important enough for the future.
It is acknowledged, that a process plant builder with deep technical expertise on specific technologies cannot supply an operating company with a comprehensive pit-to-port digital solution. Such an eco-structure must enable connectivity and data security as well as data integrity for multiple plants on many production sites and it must connect both equipment and applications from multiple suppliers. This transformational journey involving site operations, enterprise digital integrators, together with multiple tiers of suppliers has only just begun and there is a significant road to travel.
References