Sulphur 413 Jul-Aug 2024
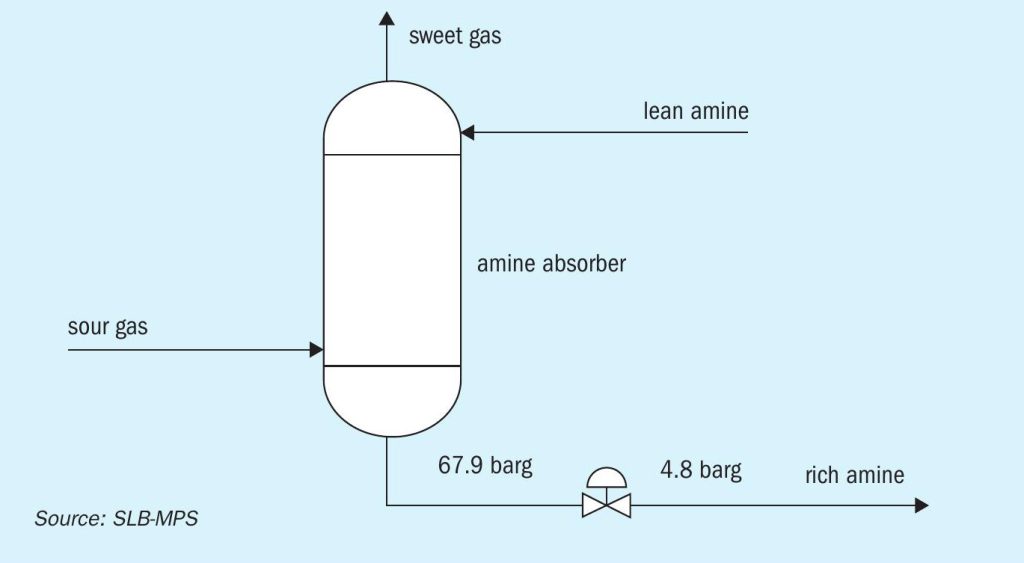
31 July 2024
Energy optimisation in amine sweetening units
GAS SWEETENING
Energy optimisation in amine sweetening units
Aparna Saiju and Nishevitha U G of SLB-MPS explore the concept of energy optimisation using power recovery turbine (PRT) technology in amine sweetening units, focusing on its potential benefits, implementation strategies, and environmental implications.
Energy optimisation is a critical concern in the oil and gas industry because it directly impacts operational efficiency, cost effectiveness, and environmental sustainability. One area in which significant energy savings can be achieved is the amine sweetening process, which is an essential step in natural gas processing for the removal of acid gases like H2S and CO2. A chemical solvent, typically monoethanolamine (MEA) or diethanolamine (DEA), is used to absorb acid gases from the sour gas stream, creating a rich amine. The rich amine is then regenerated to release the captured acid gases, and the lean amine is recycled back to the absorber.
One inherent process parameter in the amine sweetening process is the significant pressure difference between the absorber and the regenerator. The absorber operates at high pressures, often ranging from 50 to 100 barg, while the regenerator operates at much lower pressures, typically between 3 and 6 barg. This pressure differential necessitates the use of pressure reduction measures before the rich amine can be sent to the regenerator, resulting in a substantial energy loss.
Traditionally, the reduction of pressure in the amine sweetening process has been achieved through the use of control valves (Fig. 1). These valves regulate the flow of rich amine by throttling it, thereby decreasing the pressure, which dissipates the fluid’s energy. A lean amine pump is used to increase the pressure and convey the regenerated lean amine back to the absorber.
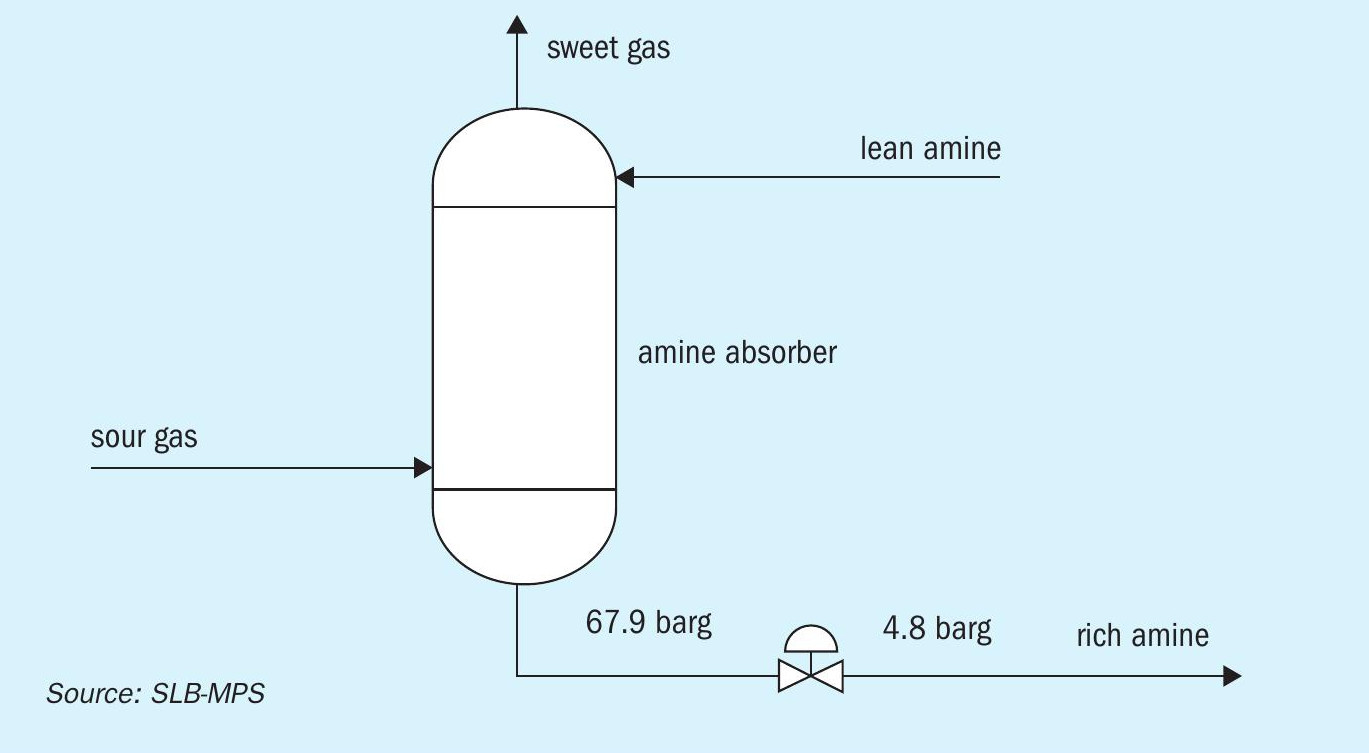
The role of power recovery turbines
To address this energy loss, the concept of using power recovery turbines has gained attention. PRT technology offers a more sustainable and economically viable solution for energy optimisation in amine sweetening units.
The PRT is designed to capture energy that would otherwise be released during pressure reductions and convert it into useful mechanical energy. This recovered energy can be used to reduce the power consumption of various equipment within the unit, such as pumps and compressors, thereby enhancing overall process efficiency.
Implementing PRTs in amine units
The application of PRTs in amine sweetening units (Fig. 2) involves several key components and operational stages:
- Rich amine inlet: The rich amine, which is saturated with absorbed CO2 and H2S, enters the PRT system from the absorber. This rich amine contains a significant amount of potential energy as a result of its high pressure.
- PRT operation: The PRT, which is a specially designed turbine, is positioned to receive the high-pressure rich amine. As the rich amine flows through the PRT, it drives the turbine blades. This enables the PRT to capture the energy that would otherwise be lost during the pressure reduction.

l Mechanical coupling: The PRT is mechanically coupled to the equipment that requires power, typically a motor driving a lean amine circulation pump. This coupling enables the energy captured by the PRT to be directly used to offset the power requirements of the equipment.
l Power generation: As the PRT spins, it generates mechanical energy that can be converted into electrical power by means of a generator. This electrical power can be used internally within the amine sweetening unit or fed back into the facility’s power grid, reducing energy consumption and operational costs.
Carbon footprint reduction
The integration of PRTs in amine sweetening units offers a multifaceted approach to sustainability. Because the energy produced using PRTs can be used to reduce the power consumption, the PRTs can be instrumental in reducing Scope 2 emissions and help contribute to the industry’s sustainability goals. The decreased use of energy generated from fossil fuels reduces the emission of greenhouse gases, including CO2 , which is a critical step toward mitigating climate change.
PRTs significantly enhance energy efficiency by recovering and reusing energy that would otherwise be lost, reducing the need for additional power generation, which often relies on fossil fuels, and thereby lowering carbon emissions. Energy optimisation achieved as a result of PRT integration results in cost savings because decreased energy consumption reduces operational expenses.
Case study quantification
The following case study, which is based on an amine sweetening unit with a capacity of 397 m3 /h for treating 60 MMscf/d of sour gas, illustrates the energy reduction potential of PRT integration. The critical parameters of the case study were:
- Circulation rate of lean amine: 397 m3 /h
- Rich amine pressure at contactor outlet: 67.9 barg
- Density of rich amine at absorber column outlet: 1,037 kg/m3
Considering there is a 4.8 barg operating pressure requirement at the rich amine flash drum, the available differential head for power generation is 622 m after considering a 10% frictional loss.
The power generated using this available head is calculated as [(397 m3 /h × 1,037 kg/m3 )/3,600 seconds per hour × 9.8 m/s2 × 622 m] = 697 kW
For this case study, considering the efficiency of PRT as 75%, the power recovered by means of the PRT – which can be integrated with the motor of the lean amine pump per the schematic shown in Fig. 2 – is 522 kW.
Assuming 0.46 kg of CO2 equivalent (CO2 e) per kilowatt-hour as the global electric emissions factor, in this case study, implementing a PRT reduces the carbon footprint of amine unit by 1,921 tonnes of CO2 e per year.
Payback analysis
A payback analysis was performed to assess the financial feasibility of a PRT installation. Table 1 presents the payback analysis for the aforementioned case study, focusing on the generation of 697 kW. The savings (in USD) were calculated on the basis of 8,000 hours of annual operation. The listed price of the PRT represents the average value that was obtained by comparing prices from various PRT vendors. The results indicate that the PRT system should recover its cost in less than 1.1 years. This relatively short payback period is generally deemed acceptable by most customers.
Modes of implementation
Revamping an existing facility
One of the key advantages of this technology is that a PRT can be installed in an existing amine sweetening unit. If there is available footprint, the motor of lean amine circulation pumps can be coupled with the PRT to recover power, although the existing motor may need to be modified or replaced. In other instances, the PRT can be used to directly drive a generator feeding the power grid.
Adding a PRT during project implementation
A detailed study of the feasibility of implementing a PRT in an amine sweetening unit for various capacities was carried out as shown in Table 2. It was observed that PRT implementation is not feasible for low flow rates.
Challenges in PRT implementation
The implementation of PRT in amine units can pose the following challenges:
- Seal quality: A seal leak in the PRT can result in H2S exposure because of the rich amine. The risk can be mitigated by providing double seal & Seal Plan 53B.
- Footprint: Implementation in offshore platform can become a major challenge considering the footprint limitation.
- Operational issues: When the flow is inadequate, the PRT can overload the motor. To prevent this, a one-way clutch is required. In addition, when the PRT is used to directly drive a generator, precautions must be taken to ensure mechanical reliability in the event of a power failure.
Conclusion
The integration of PRTs in amine sweetening units represents a pivotal step toward achieving sustainable and efficient energy use within the oil and gas sector. By transforming energy that would otherwise be wasted into a valuable resource, PRTs enhance energy efficiency, reduce operational costs, and mitigate carbon emissions. The case study quantification clearly demonstrates the substantial energy recovery potential that could be achieved through PRT integration, enhancing the sustainability and economic viability of amine sweetening units.