Nitrogen+Syngas 390 Jul-Aug 2024
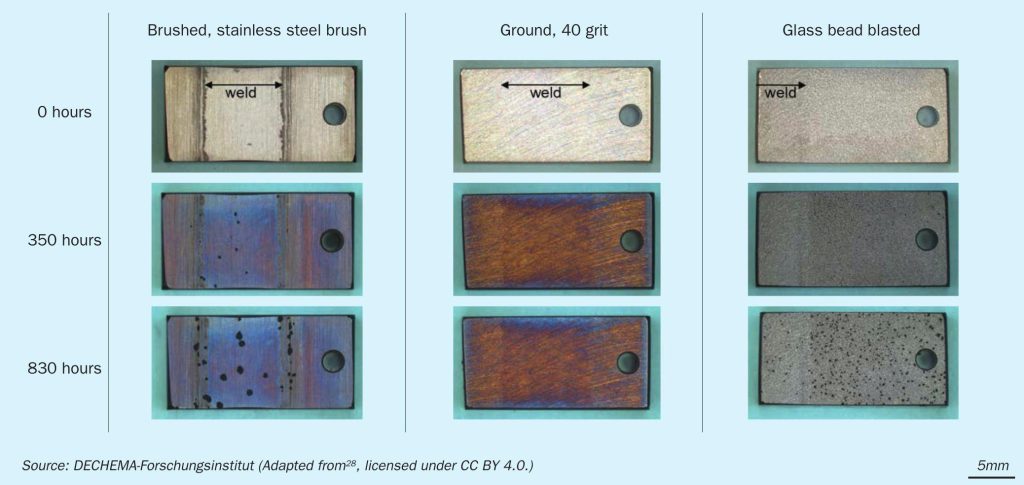
31 July 2024
Methods to mitigate metal dusting in syngas production
MATERIALS OF CONSTRUCTION
Methods to mitigate metal dusting in syngas production
Industrial plants using synthesis gas at elevated temperatures risk metal dusting attack on the equipment, which are typically made of steels or Ni-based alloys. Parameters which impact the metal dusting risk are discussed and factors affecting the material selection and processing are described. One important focus is surface preparation, showing that grinding (40 grit) improves the metal dusting resistance compared to glass bead blasting and brushing. The surface treatment outweighs the impact of welds or the manufacturing route.
Process plants handling carbon-containing gases at high temperatures often face a corrosive attack termed “metal dusting”. This occurs at 450 to 750°C in gases with a high carbon activity and is catalysed by iron, nickel and cobalt1–3. Among other industries, synthesis gas production is highly affected by metal dusting which is known to occur in the downstream sections of these plants. A common solution is cooling the gas very quickly in the critical metal dusting temperature regime. However, the losses of process heat are immense, and were estimated at $220 to 290 million per year in 2000 in US hydrogen production alone4. With the increasing demand for hydrogen and CO2 neutral syngas, optimisation of steam reformers and development of new syngas production technologies become even more important. Independent of the technology used, losses in process efficiency are less acceptable than ever, driving a strong need for effective and efficient mitigation of metal dusting.
Components prone to metal dusting are commonly made of steels or Ni-based alloys. Alloying additions of Cr, Al, and/ or Si can result in the formation of an oxide scale under process conditions. The oxide scale acts as a barrier between the process gas and metal substrate. In carbon-rich gases, carbon may deposit on the surface of the oxide by CO or CH4 dissociation. However, if the oxide scale fails to provide a protective barrier after an initiation period, the corrosive attack will start locally. Carbon accesses the metal through the oxide, dissolves and supersaturates. Cementite (Fe3C) forms in most steels. Both cementite in steels and nickel in Ni-base alloys catalyse graphite formation along grain boundaries from the supersaturated carbon. This breaks up the integrity of the material, resulting in the corrosion product “coke”. Coke is a mixture of metallic particles, graphite, amorphous carbon, and oxides1,5 .
Due to the initiation of the attack at local failures within the oxide scale, the attack grows into the material in the form of pits. Once metal dusting attack starts, it proceeds very rapidly. Therefore, most effective mitigation strategies aim to stop the attack from the beginning, that is before carbon ingress occurs in the metal.
Experimental methods
The results were obtained using quasi-isothermal laboratory exposure experiments. If not stated otherwise, samples of sheet materials were wire eroded (electro-discharge machined) and ground to P1200 grit with SiC paper. Samples were then cleaned ultrasonically with ethanol and placed in separate slitted alumina crucibles. Tests were performed in a horizontal tube furnace at elevated pressure. Details of the apparatuses are given in6. The samples were heated up in Ar, then pressurised with the test gas. After a given exposure time, the system was de-pressurised and cooled down simultaneously. The samples were cleaned after each exposure period.
Results and discussion
The following discussion is divided in two sections: 1) the process conditions, and 2) the material selection. In both sections, the main parameters are discussed first, followed by an overview of mitigation strategies.
Process conditions
Impact of the process conditions
Low or stagnant gas velocities were shown to enhance localised attack and allow transformation of the gas to a more (or less) aggressive composition7. On the other hand, a high gas flow can remove the already formed coke from the surface, which promotes access of the process gas to the damaged oxide/metal surface and results in a faster and more uniform attack7,8. In addition, hard particle erosion can enhance the corrosive attack8. Depending on the gas and metal temperature, the gas velocity can also make a difference in reaching or avoiding the critical metal dusting temperature range7,8.
Several studies showed that the incubation time of the metal dusting attack is significantly shorter at elevated pressures when compared to ambient pressure for the same gas composition and temperature4,6,9. Other parameters affecting the metal dusting attack are gas impurities10 and surface stresses from temperature and pressure gradients8.
The gas composition is decisive for the metal dusting risk. Process gases with a low driving force for carbon deposition have a low metal dusting risk as this reduces the supersaturation potential. However, the driving force for carbon deposition currently cannot be determined precisely. In the literature, various methods to estimate the driving force for carbon deposition, and thus the risk for metal dusting have been discussed. These chemical reactions for carbon deposition have been considered:
However, at 650°C methane formation is more likely than methane cracking11 . Thus, often only the syngas reaction and the Boudouard reactions are considered. One way to estimate the driving force for carbon deposition is the CO/H2 ratio in the gas12. A second option is to calculate the carbon activity in the syngas reaction:
And the Boudouard reaction:
where Ksyn and KBoud are the equilibrium constants of the reactions and pi is the partial pressure of the components. For the purpose of this calculation, carbon activities greater than one are interpreted as a high driving force for carbon deposition.
Hermse et al.7 pointed out that in addition to the carbon deposition reactions, the water gas shift reaction may also take place.
These local changes in the gas composition may occur near the surface or in areas with low gas exchange rates. Hermse et al. suggested to assume that the water gas shift reaction proceeds until thermodynamic equilibrium is reached7 . The changed gas composition can then be calculated. The carbon activity of the changed gas is labelled aC,synWGS. Hermse et al. reported a positive correlation between these parameters and the aggressivity of the attack observed in laboratory tests7.
The gas composition at equilibrium, now considering all possible reactions between the species, can be calculated with the CALPHAD approach. In order to obtain the driving force for carbon deposition similar to those above, graphite formation is suppressed in the calculation. The result gives the carbon activity in metastable equilibrium (aC,metast ). It is metastable because in full thermodynamic equilibrium, graphite may form. Comparison of all of the described parameters against experimentally observed attack have been reported in detail in13.
Further work is necessary to extend the model with kinetics and surface reactions.
Mitigation strategies through adapting process conditions
Within the design limits of the process and plant, adaptations can be implemented to lower the metal dusting risk. Mitigation strategies by changing process conditions and their drawbacks are summarised in Table 1.
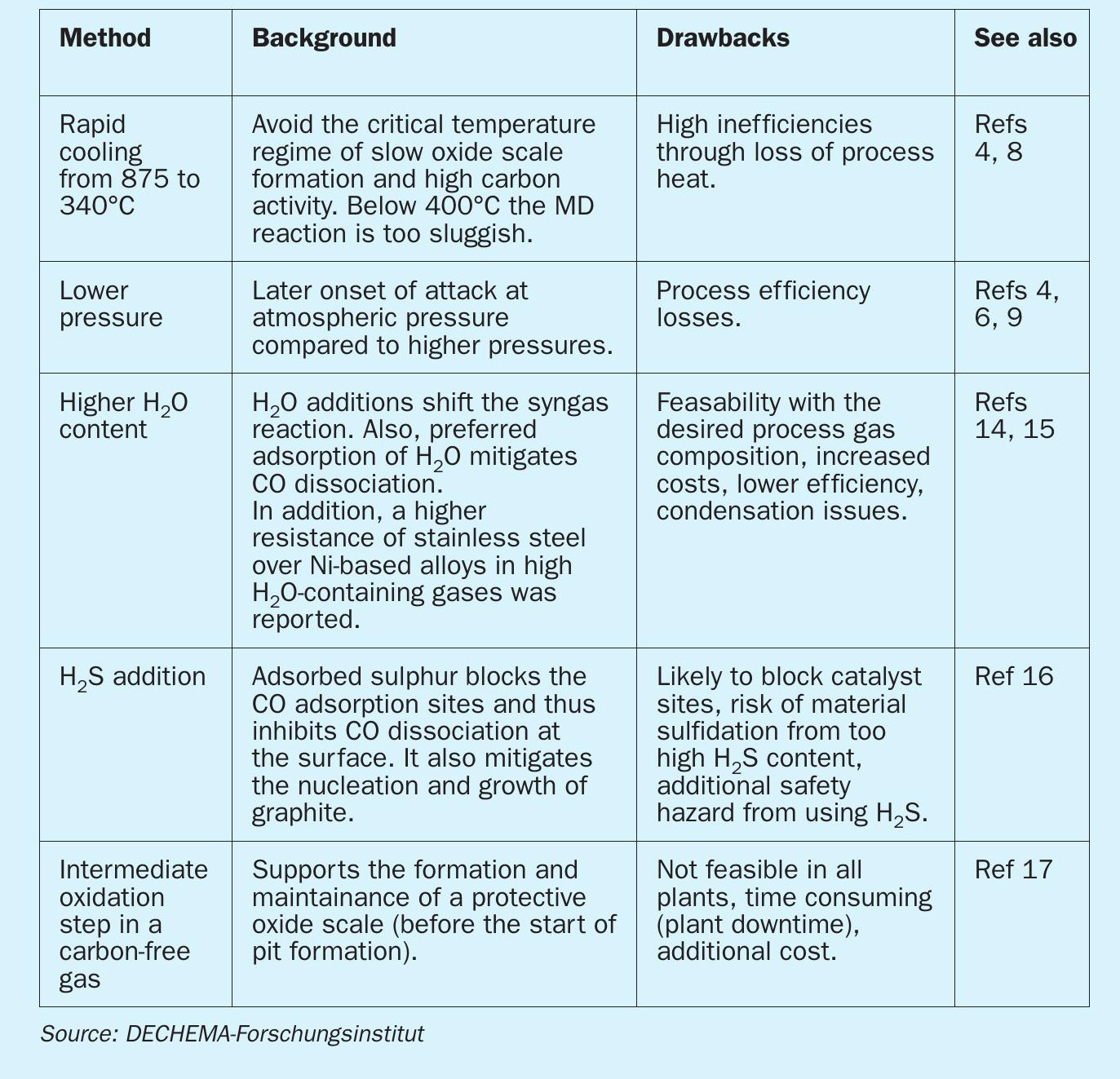
Material selection
Impact of the material and surface
Two approaches in alloy design can improve the resistance of the materials against metal dusting. One is alloying with stable oxide-forming elements such as chromium, aluminium and silicon. The other is adding elements which inhibit the catalytic dissociation of CO and formation of graphite, such as copper or tin18–20. The more recently developed alloy HR-235 and alloy 696 combine both strategies by alloying with oxide-forming elements and copper. However, the currently most used alloy systems are steels or Ni-based alloys with high additions of oxide formers. The following discussion is therefore focused on these alloys.
The oxide scale acts as a barrier between the gas and the metal. A protective barrier is expected to form under process conditions, regrow in case of damage and should, of course, be impermeable to carbon. The pure oxides chromia, alumina and silica offer excellent protection, but mixed oxide layers and spinels which grow under process conditions may be infiltrated by carbon after long times and/or in very aggressive environments21–24 . Oxide scale formation can be optimised by tailored alloying and surface preparation.
Several studies showed that a high alloying content of chromium and aluminium reduces the metal dusting attack25–27 . Thus, commercial alloys with very high chromium and relatively high aluminium contents were developed for these applications (e.g. alloy 699 XA, alloy 693). Alternatively, coatings can be used to establish a protective barrier between the process gas and metal, for example by applying a diffusion coating enriched in oxide-forming elements.
Surface treatments are often applied to remove impurities, such as oxides formed during welding. In most industrially used surface treatments, the surface roughness is generally lowered and the near-surface zone is deformed. In the deformed zone, more diffusion paths are available for the oxide forming elements like chromium, aluminium and silicon. This may be decisive in the formation and maintenance of an oxide scale during operation. Samples of weld beads on alloy 602 CA with different surface treatments, before and after metal dusting exposure experiments in a harsh laboratory environment are displayed in Fig. 1.
The surface treatments were performed industrially. After the metal dusting exposure experiment, no attack or carbon deposition was observed on the ground sample (40 grit zircon corundum paper). Some carbon deposition resulted on the glass bead blasted sample and the strongest attack occurred on the brushed sample (stainless steel brush). During brushing, iron impurities contaminate the alloy and act as nucleation sites for the metal dusting attack29 . In general, all working media used in the last step of the surface treatment should be free of any steel to prevent this effect.
Fig. 1 also shows that with a suitable surface treatment, a weld can be as resistant against metal dusting as the base alloy. Here, it is important that the filler material has a similar composition to the base material. Also, the removal of impurities from the weld, achieved in the shown example by fully flattening the weld bead while grinding, can prolong the metal dusting resistance.
Additive manufacturing (AM) enables a faster exchange of attacked parts through just-in-time on-site production of components. A study was carried out to evaluate whether the manufacturing route changes the metal dusting susceptibility. Samples of hot rolled and AM alloy 699 XA, with and without heat treatment (solution annealing), were exposed to industrially relevant process conditions.
First results showed that no metal dusting pits were observed on any of the samples. On the ground AM samples (P1200 grit SiC paper), no carbon deposition was visible independent of the heat treatment. The same is true for the hot rolled and mill ground sample. However, carbon deposition was clearly visible on the heat-treated AM sample with as-built surface. Carbon was also present on the AM as-built sample (without heat treatment) due to the higher surface roughness. In conclusion of this first study, the surface state of the samples is more decisive for the metal dusting resistance than the manufacturing route.
Mitigation by material selection and coatings
Careful choice of materials, coatings, surface treatment and equipment design are vital to reduce the risk of metal dusting attack. Table 2 summarises approaches to mitigate metal dusting from the component side.
Conclusions
Overcoming the problems resulting from metal dusting attack is a key element in reaching a low CO2 footprint in syngas production. As the gas compositions differ between old and new technologies, it is important to understand the impact of the gas composition on the metal dusting risk. If altering the gas composition or process conditions are possible, this is a powerful tool to mitigate the metal dusting attack. Alternatively, the component material and surface finish must be selected carefully. Initial results of additively manufactured parts show limited impact of the manufacturing route. The surface treatment (and surface area) has a stronger impact on the metal dusting resistance for highly alloyed Ni-based materials, such as alloy 699XA. Choice of highly alloyed materials or suitable coating strategies are recommended to mitigate metal dusting.
Acknowledgement
The authors would like to thank VDM Metals International GmbH and Digital Additive Production of RWTH Aachen for providing alloy 699 XA sample material. This project has received funding from the European Union’s Horizon 2020 Research and Innovation Programme under grant agreement No. 958192. It was also supported by German Federal Ministry for Economic Affairs and Climate Action via IGF number 20854N.
References