Sulphur 415 Nov-Dec 2024
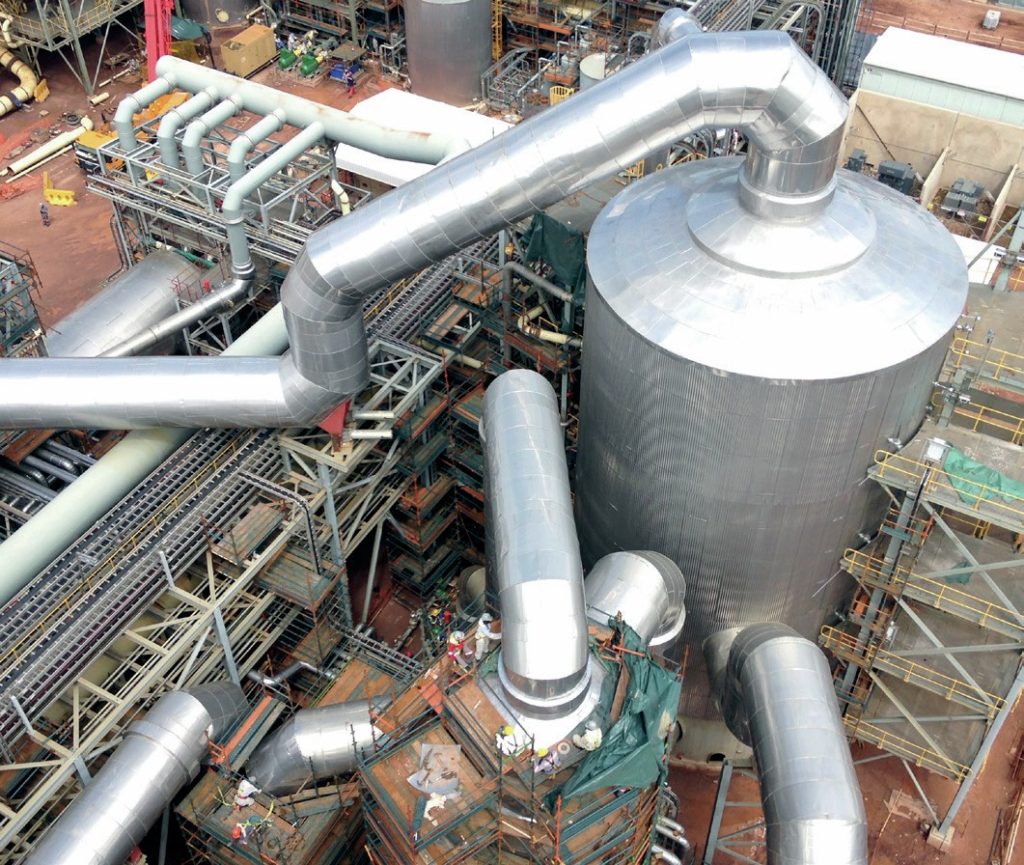
30 November 2024
60 years in the sulphuric acid industry
SULPHURIC ACID DESIGN AND EQUIPMENT
60 years in the sulphuric acid industry
For six decades, Chemetics has been a pioneering force in the sulphuric acid design and equipment industry, consistently introducing groundbreaking technologies that have revolutionised the field by optimising the methodology in which chemicals are produced. This year, Chemetics celebrates its 60-year anniversary as one of the leading designers, direct equipment suppliers and fabricators that has modernised the sulphuric acid industry of today. This article dives into Chemetics’ rich history and key innovations that have shaped and moulded the industry.
A brief history
Chemetics Inc. began its journey on 2 March 1964 as Chemtech Engineering, specialising in sodium chlorate electrolysis and in the pulp and paper industry. In 1967 CIL (Canadian Industries Limited), which was majority owned by ICI of the UK and Chemetics Ltd, banded together to form a joint venture to market the chlorate technology. During this time, the experts at CIL invented the anodically protected shell and tube heat exchanger, originally known as the “CIL cooler”, which was marketed through the joint venture and that transformed the sulphuric acid industry. In September 1970, Chemech Engineering was purchased by CIL and in 1971 changed the name to Chemetics International Company Ltd. Over the next two decades, Chemetics International Ltd introduced new lines of proprietary equipment which would set the foundation and change the way sulphuric acid plants are designed today. In 1981, the company also had the foresight to purchase the fabrication facility, Fromson Heat Transfer, that had been producing the anodically protected acid coolers for Chemetics since their inception. This marked the beginning of the close cooperation between engineering and design and the fabrication that continues until today.
In the 1980s, Chemetics marketed and sold its new technology and equipment to the sulphuric acid industry expanding its market base offerings, while taking on new and exciting projects domestically and internationally. On 1 November 1989, ICI Chemicals Plc, the UK parent of CIL, sold Chemetics to Trafalgar House Plc, a UK holding company with headquarters in London. Chemetics then became part of John Brown E&C, the engineering division of Trafalgar House.
In the 1990s, Chemetics continued to expand its technology, equipment and plant sales worldwide. In 1992, Chemetics consolidated its acid business and operation in Vancouver. In 1996, Trafalgar House was purchased by Kvaerner ASA, Norway’s largest privately held company. Chemetics, as technology supplier, maintained its independence, a common theme seen throughout the rest of the acquisitions.
Chemetics in the 2000s continued to expand its market and develop new technologies. These years proved pivotal for Chemetics as different approaches in both technology offerings and commercial offerings were explored.
In 2009, Chemetics opened a new 90,000 square foot modern fabrication shop specialising in high alloy fabrication to continue to supplement the technology and engineering supply of Chemetics Inc. This replaced the existing fabrication shop that was purchased in the 1980s.
In 2011, Jacobs Engineering group acquired Aker Solutions Canada Inc., along with the entire P&C group of Aker. Chemetics, again being the technology supplier and having already 50 years’ worth of experience in the industries it served, kept its name as a specialised entity. Jacobs Engineering subsequently sold its entire ECR business, including Chemetics, to Worley Parsons in 2019.
Within the Worley organisation, Chemetics Inc. (branded as Worley Chemetics) is currently part of Worley’s Technology Solutions group focused on technology offerings to its global clients. As part of the greater Worley Group, Chemetics has enhanced its global presence through the potential use of the local area offices, allowing for local support.
Since 2023 Chemetics has been rebranded as Worley Chemetics, but remains the same entity that has enabled it to thrive over the last 60 years. Chemetics still incorporates the innovative spirit that has led it to where it is today, supplemented by the experience gained over the course of many executed projects over its existence. Chemetics’ ability to retain its brand name and recognition over the course of 50 years of acquisition and sales speaks volumes for the quality and brand recognition in the sulphuric acid industry.
Key innovations and modern technological advancements
Chemetics has been and continues to be a pioneering force in the advancement of sulphuric acid plant technology and sodium chlorate electrolysis today. These advancements are a direct result of its customers’ needs for better emissions, higher capacities, longer campaigns, and fewer unscheduled shutdowns. Chemetics within the sulphuric acid industry has been able to service its clients whether they are producing acid via burning sulphur, capturing SO2 off-gas from a metallurgical operation, or regenerating/concentrating acid from weak acid streams. Within each industry the need for innovation has been driven by the requirement to increase value for its customers and provide maximum reliability of operation. Fig. 2 shows a snapshot of Chemetics’ key innovations over the decades.
Acid cooler
In 1967, CIL and subsequently, Chemetics Inc. revolutionised the sulphuric acid industry by the invention and installation of the anodically protected (AP) sulphuric acid cooler. This proprietary piece of equipment can be considered a founding product as it enabled Chemetics to become the company it is today. Few developments within the acid industry can claim that they changed the industry as much as the Chemetics acid cooler. The Chemetics acid cooler replaced the ductile iron serpentine coil acid coolers that were prone to failure and took up a huge footprint area of the plant. The Chemetics AP cooler reduced the size of the equipment by 80+%, increased longevity and was virtually maintenance free. These proprietary pieces of technology are manufactured to the highest standards in Chemetics’ shop to enable direct quality control over the fabrication, ensuring a consistent and reliable product every time. The AP acid cooler, while developed in 1967, has continued to adapt to client requirements over the course of the decades to become what it is today, incorporating new process design criteria, materials of construction, thermal designs, manufacturing details and improved electronics. One such key component that allows for life spans of over 30 years is the ANOTROL system designed in 1970, which is Chemetics’ electrical/electrochemical corrosion control system used to protect the acid coolers from acid corrosion. Each new generation of ANOTROL system has been custom designed based on the experience of the previous version and as such the new ANOTROL 20/20 system provides an even wider range of capabilities.
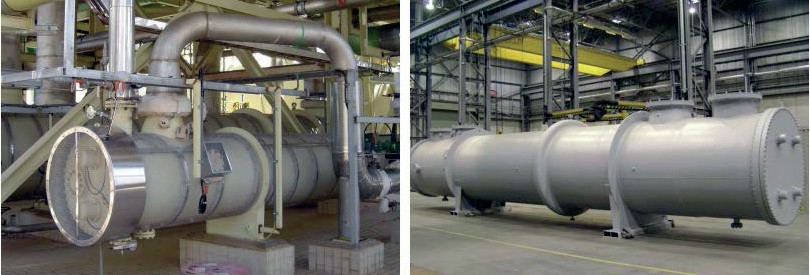
Stainless steel converters and radial flow gas exchangers
In 1980, Chemetics introduced the first iteration of the fully welded stainless steel converter, which forms the heart of the acid plant today. The converter design replaced the old grid-and-post catalyst support beds, brought a different nozzle arrangement and incorporated a design philosophy to reduce maintenance and expand converter longevity. The design philosophy was such that there would be no flat surfaces making all components round, curved, or dished to reduce overall stress. The converter incorporated a central core allowing for internal exchangers to be installed, reducing the need for an external gas exchanger and allowing for modular fabrication. The converter was fully welded and manufactured out of specific controlled stainless-steel chemistry chosen for the application. It was the first stainless steel converter in the acid industry. These design conditions have allowed the converter to last for longer than 30 years without major repairs. Over the decades, advancements have been made to the design bringing the Chemetics converter to what it is today, allowing for massive converter constructions for capacities of even 5,000 t/d. Leak free operation for decades is the norm for Chemetics radial flow converters.
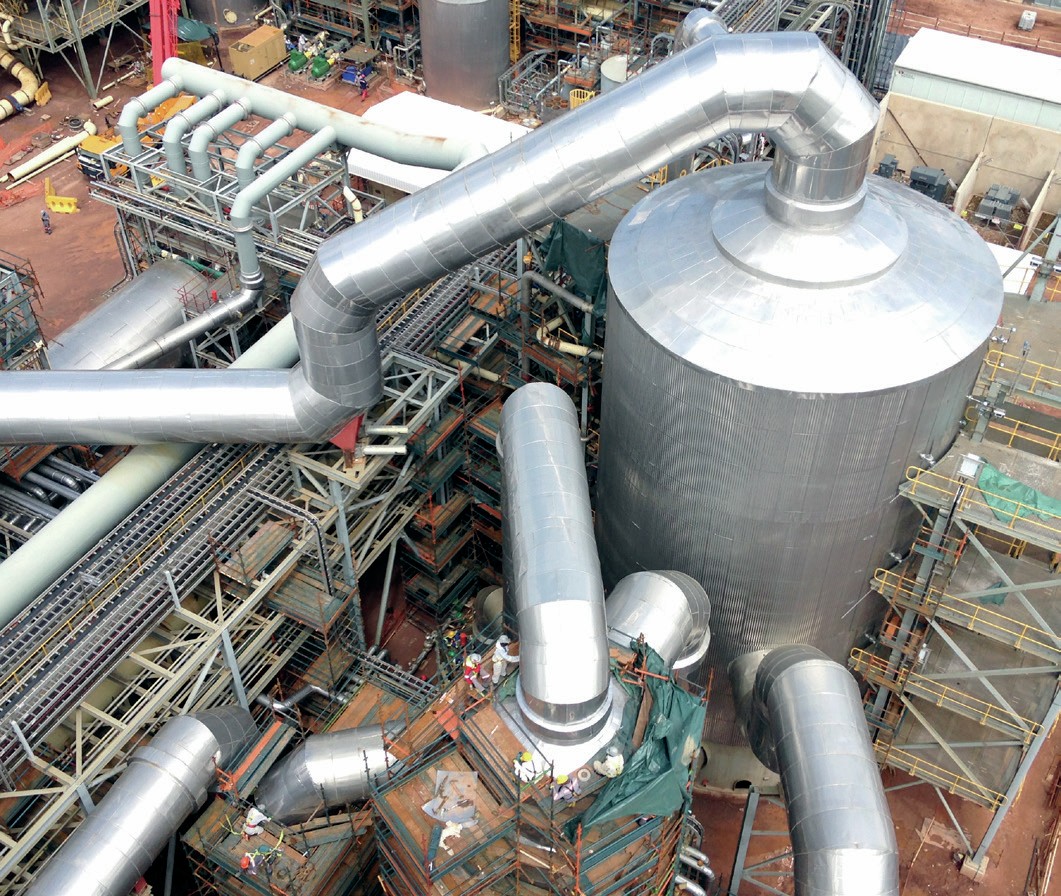
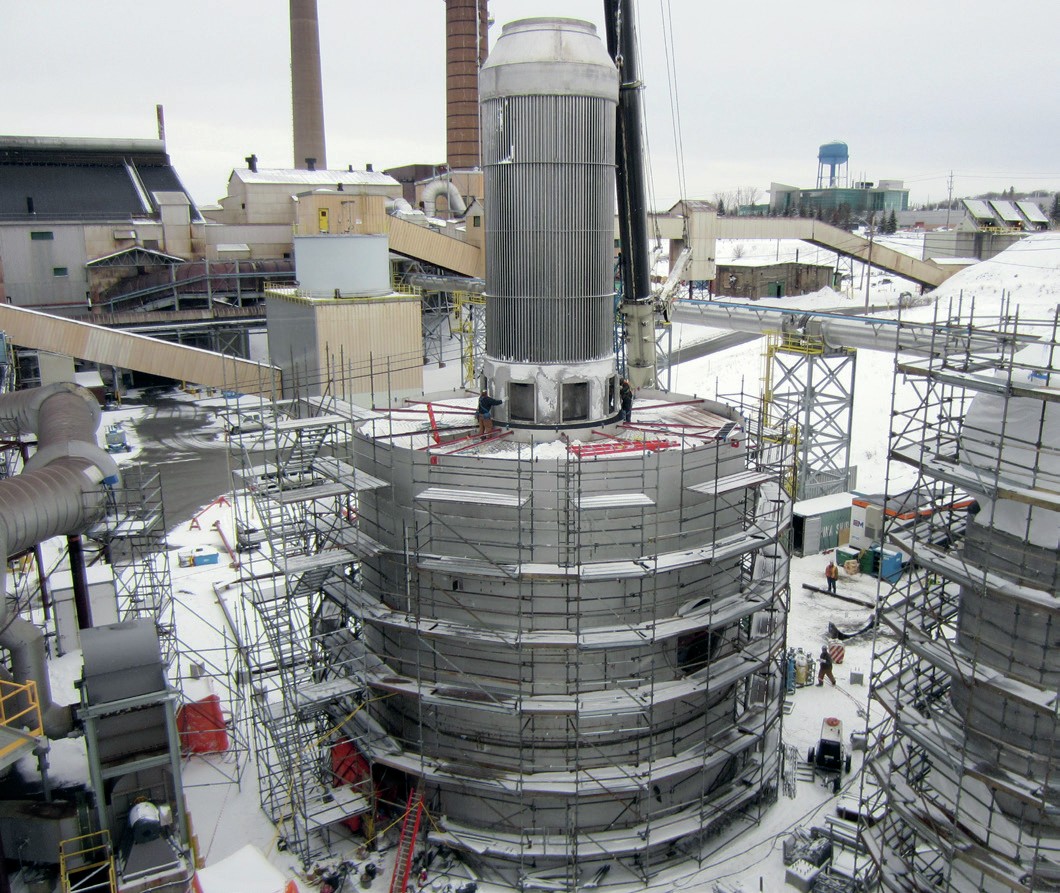
Alongside the push of stainless-steel components into the acid plant, modernising them to today’s standards, Chemetics also introduced the stainless-steel radial flow gas exchanger in 1979, installing over 400 worldwide since its inception. These patented designs followed a radial pitch tube layout allowing for a better overall thermal design with improved thermal efficiency creating a constant mass velocity between the tubes. It allows for a smaller sized exchanger saving on footprint and space. The radial gas flow pattern minimises thermal stresses across the bundle by eliminating temperature variation and differential thermal expansion, leading to longer life and virtually zero leaks. The requirement of welding the tube-to-tube sheet joints on both tube sheets also ensured leak free life for the exchangers and allowed changes in the plant flowsheets to allow greater heat recovery and lower stack emissions.
SARAMET™
The introduction of the Sulphuric Acid Resistance Alloy METal (SARAMET© ) a high silicon stainless steel material that allows for direct metal to sulphuric acid contact at any velocity was introduced and patented in 1982. The first introduction of SARAMET 23 allowed for fully welded piping systems significantly improving safety. Shortly after, full alloy related equipment including absorbing and drying towers, distributors, internals, tanks, coolers, etc. were introduced. Innovations to the metallurgy have not stopped with the addition of grades of 25 in 1990, 35 in 1998, HT in 2018, and HT+ in 2020, each specifically designed to be used in a specific range of acid concentration and operating temperature while being cost conscious.
Drying and absorbing towers
In 1982, with the introduction of SARAMET material to the market, Chemetics was able to utilise the benefit of the material to provide other key parts of the acid plant such as alloy towers starting from 1986. This edition to the family of equipment allowed for easier retrofit projects that reduced the overall construction length on site and reduced shutdown modifications ultimately lowering the total installed costs. The drying and absorbing towers brought key advancements to the industry such as how the gas nozzle inlet is fabricated and protected, how the packing support functions to reduce overall pressure drop of the tower, the self-supported distribution system that evenly irrigates the acid flow throughout the transfer bed and gets rid of unnecessary hangers, and the uniquely designed candle plate housing the candles used to filter acid mist and droplets. These design additions changed the way that alloy acid towers were designed. The attention to the design details in Chemetics towers has virtually eliminated localised corrosion issues that plague some other designs.
Chemetics also introduced some key design changes to how brick-lined towers are constructed, such as the use of a fully self-supported ceramic packing dome, multi-layered special shaped acid-resistant brick backed by a PTFE membrane insert, the dished bottom down to prevent brick heaving, and how the nozzles are packed, resulting in over 25 years of service.
Strong acid distributors
The next instance of utilising SARAMET came into effect in 1983 when Chemetics started introducing the SARAMET material to replace the common ductile iron pipe distributor. This was the first advancement made in this area and it wasn’t until 1995 that Chemetics delivered its first SARAMET© trough distributor design, which was a welcomed change compared to the original pipe distributors, simplifying the irrigation portion of the acid. The ISO-FLOW™ trough distributors featured an orifice design, which allowed uniform flow and control through each downcomer tube, allowing for better absorption and for flow imbalances, if any, to be visually seen and adjusted easily. The calming plates with integral screens filter out any packing chips or debris and eliminate the need for an acid strainer upstream. The ISO-FLOW design creates a calm liquid surface of acid within the trough ensuring even flow to each downcomer. Diagnosis of plugged or partially blocked tubes is simple with a flow test ensuring that the distribution will be optimal after every plant cold shutdown. Expanding on the notion to reduce site installation and maintenance time, Chemetics in 2016 designed the SWIFT LOCK™ , which simplifies attaching the downcomer tube banks to the main trough, making installation of the already fully fabricated (expanded and seal welded) tubes onto the distributor with preinstalled attachment brackets. This reduced the overall installation time by 90% and helps with any future plant shutdowns. The distributors can easily be disassembled and removed from the towers and later reinstalled if desired. This can greatly simplify tower maintenance. Chemetics has supplied over 150 of these ISO-FLOW™ with SWIFT-LOCK™ distributors in various different SARAMET alloys.
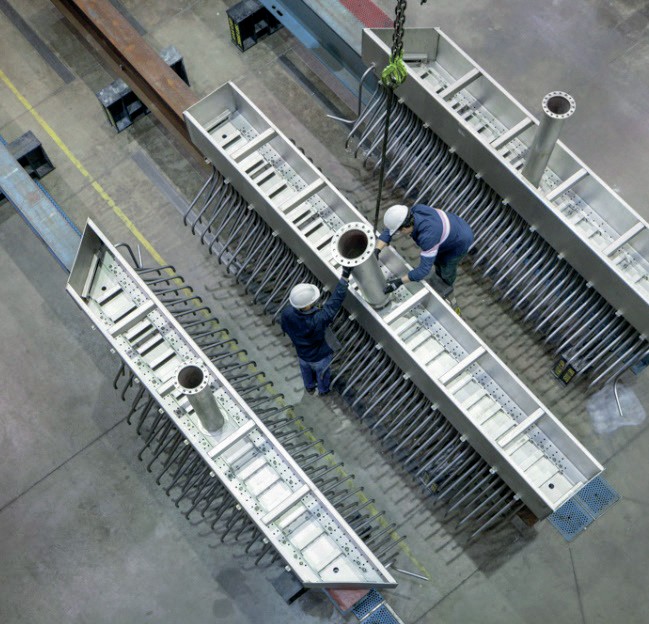
Modular equipment
Clients with their ever-expanding need for capacity were demanding larger and large pieces of equipment forcing site assembly due to transportation corridor limitations to the site. Transfer of the shop fabrication scope to field assembly became an issue due to the unpredictability of weather events, assembly at heights and consistent site construction cost overruns. Chemetics met this challenge by redesigning the large equipment into modules where the goal was to complete as much pre-fabrication, especially of the complex portions, in a controlled shop environment and then just assemble the modules together on site like a series of building blocks. This approach ensures high quality of the end product and minimises field costs. Modular gas to gas exchangers have been shipped worldwide, converters are assembled in a fraction of the time, modular acid alloy towers are constructed on site all with the assistance of Chemetics construction experts.
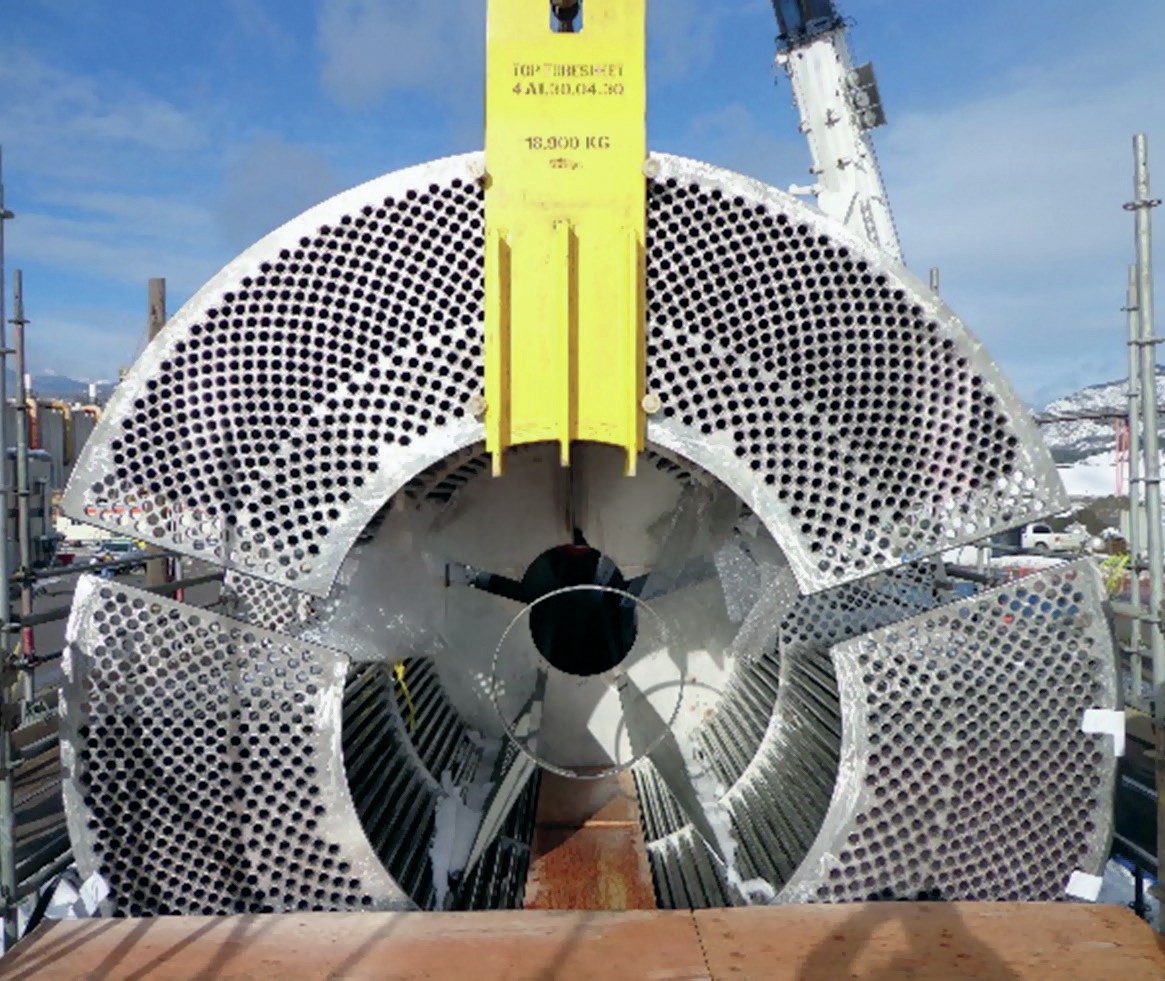
Gas cleaning
In metallurgical operations the requirement for gas cleaning prior to the contact plant is an absolute requirement as the hot and dirty gases arising from the smelting operation need to be cleaned and conditioned prior to any further processing. Traditionally equipment used in the hot, cold, or wet gas duties was fabricated out of carbon steel and then loosely lined with lead for corrosion protection followed by acid brick lining to protect the lead lining. This led to problems such as the difficulty in identifying leaks, fluoride attacks, cracks due to pressure cycling, and ultimately impossibility of repairs. Equipment used in this service must be able to withstand corrosive effects of weak acid. Chemetics’ innovation began with lining the carbon steel equipment with a fully bonded rubber lining and then providing thermal and mechanical protection by insulating with specific bricks. This prevented the fluoride attacks. FRP, often dual laminate, was introduced to prevent attacks from weak acid and wet SO2 and high alloy plate exchangers were introduced to cool the weak acid. Further to this, Chemetics also developed two key pieces of equipment, the quench venturi, and the wet gas condenser. The quench venturi is used to adiabatically quench the hot 350 °C smelter off gas and needs to be able to withstand rigorous cycling and duty. The alloy wet gas condenser is used to replace the carbon steel equipment of the plant prior to the wet ESP utilising high alloy to withstand the harsh conditions, making retrofits easier and faster. Chemetics has brought value for over 35 years in the gas cleaning industry and continues to make breakthrough strides.
Chemetics is unique in the field of sulphuric acid design and supply as it is one of the only companies to own and operate its own in-house fabrication shop. The purchase of Fromson in 1981 was pivotal to the success and supply of Chemetics designed equipment worldwide as it allowed for strict quality control during the fabrication process to ensure the equipment was going to withstand the harsh conditions of production of sulphuric acid. Today, Chemetics can state that it has over 50 years of experience in fabricating high alloy equipment for acid, chemical, oil and gas industries, and in the last few years has also obtained nuclear certification for work on heat exchangers used in the nuclear industry. The new state-of-the-art facility opened in 2009 and expanded by more than 50% in 2024 boasts some of the most technical advanced manufacturing equipment, including plasma welding, a horizontal boring mill, laser cutting, a quick mill that can produce tube sheets of over 90” in one piece, etc. This experience allows Chemetics to control the equipment fabrication, and for equipment that is too large to ship from Canada, it has the necessary experience and knowhow to properly sub contract and manage fabricators worldwide.
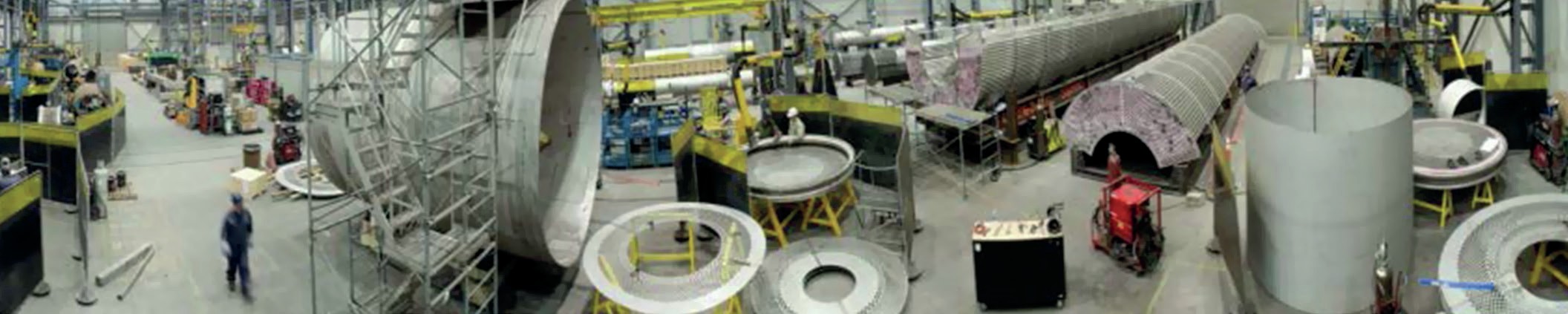
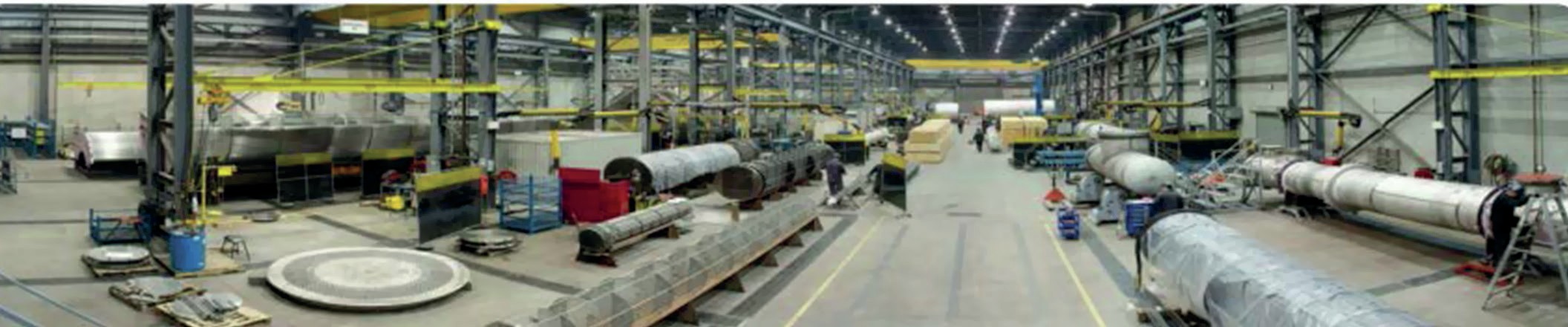
CORE™ converter
Invented in 2007, the iso-thermal one pass converter retains the ability to completely change the conversion process in the acid plant today. In the Cooled Oxidised Reactor (CORE™ ), a tubular oxidation reaction is used to convert SO2 to SO3 while avoiding the pitfalls of the adiabatic conversion process of hitting the equilibrium curve. This process removes the upper limit of SO2 concentration typically seen and allows for conversion from concentrations higher than 30% directly to SO3 . The benefit is the reduction of the footprint of the plant by up to 60% and removal of plant equipment such as the final absorbing tower, gas exchangers, and economisers, reducing capex by 25%. Further reduction in size is possible when there is source of O2 present within the plant, allowing the ability to utilise this high concentration conversion. Similarly, the CORE converter can be used for low SO2 concentration plants when paired with an amine regeneration-based scrubber. The CORE converter is either air cooled, allowing for easy retrofit capabilities for enhanced expansion, or can be cooled with a molten salt when higher capacities are required. There are currently three of these plants in existence and this new conversion process is the latest innovation brought to the table by lowering capex investment and minimising emissions.
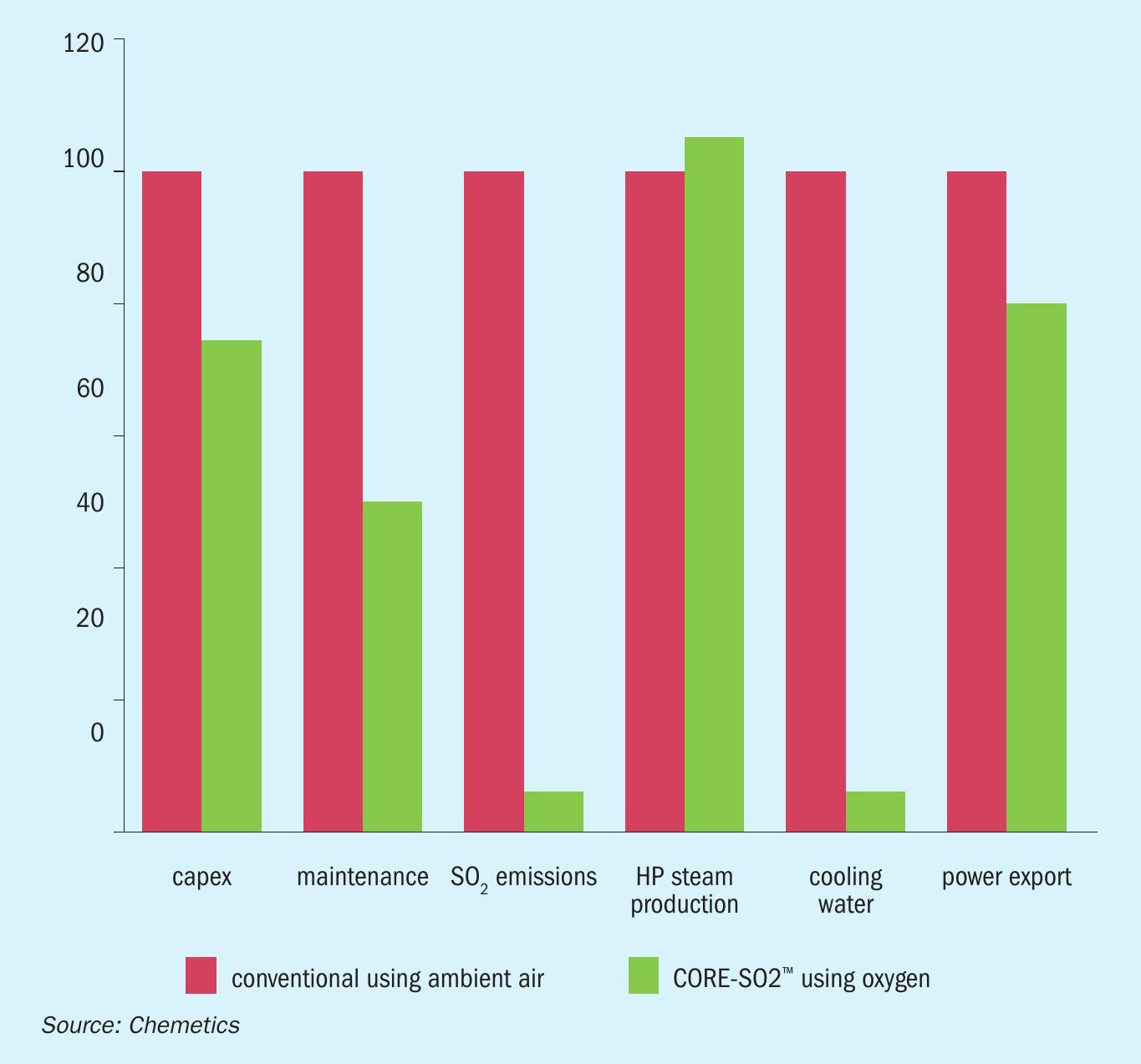
Chemetics approach
Over the course of 60 years Chemetics has provided projects in all different variations of supply from licensing packages all the way to turn key construction projects. In 2024, Chemetics has honed its scope of supply to provide the best value to its clients.
Chemetics’ preferred scope of supply is a lump sum engineering procurement and service scope. This contractual model offers ease of mind for clients as it allows a technology company to focus on the core aspects of the plant and allows for other parties to perform the auxiliary non process and non-critical components such as the civil, electrical, structural, and construction. Chemetics offers full support during the construction phase to ensure that the Chemetics supplied units and other pieces of critical equipment are installed to applicable specifications. This entire scope of work is backed by a world class guarantee that has applicable scope drive remedies if required giving clients the reassurance that they are derisked when it comes to performance of the plant.
Chemetics has been and continues to be a key innovator and technology pioneer, consistently bringing new innovations, inventions, and improvements to the sulphuric acid industry and looks forward to servicing this community for another 60 years.