Sulphur 415 Nov-Dec 2024
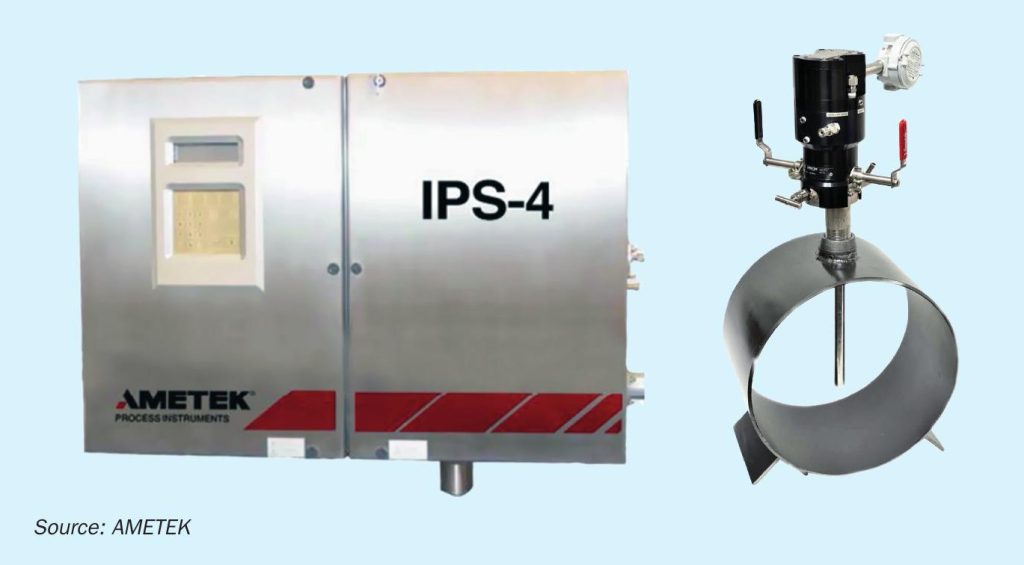
30 November 2024
Advanced feed gas control by detecting BTEX in SRU feed gas
PROCESS CONTROL
Advanced feed gas control by detecting BTEX in SRU feed gas
The development and implementation of modern process instruments and control systems in sulphur recovery units has increased significantly over the last decade. In this article, the impact of BTEX on sulphur plant operations and how the BTEX concentrations can be measured are discussed.
In some hydrocarbon processing plants and refineries, benzene, toluene, ethylbenzene and xylene (BTEX), can be present in the feed gas to the Claus thermal reactor. Unlike the lighter hydrocarbons, the complete destruction of BTEX requires the reactor to operate at over 1,100°C. If BTEX destruction is not complete, soot is likely to form on the catalytic beds. For refineries this is not usually a concern as most modified Claus process units are designed to handle sour water stripper gas (SWS), which contains a percentage of ammonia (NH3 ). In such cases the reaction furnace temperature is kept above 1,200°C, but for natural gas processing plants it is a real concern, as the normal reactor operating temperature is below 1,000°C, making co-firing mandatory.
Several recent papers and presentations regarding operational improvements using advanced process control strategies for modified Claus plant operations have been published. The basis of this approach is the measurement of the most critical components – hydrogen sulphide (H2S), total hydrocarbons (THC), carbon dioxide (CO2), ammonia (NH3), if present and water (H2O) “not standard” – in the feed gas to the thermal reactor, to better manage the combustion air:oxygen use. Optimising this acid gas (feed gas) to air flow ratio is the key target. In addition to process efficiency gains, through higher recovery efficiency and SRU throughput, and cost savings through the use of less air or oxygen, better combustion management can also reduce CO2 emissions, which are increasingly being measured, reported and regulated. With tighter control of the entire modified Claus unit, upset conditions can also be mitigated resulting in reduced emission violations and greater sulphur recovery efficiency.
Another area for improvement in sulphur recovery operations is the better management of co-firing. When incoming acid gas is lean in terms of hydrocarbon content, the introduction of additional “fuel” to the thermal reactor (co-firing) is required. Ideal co-firing properly manages the introduction and use of natural gas in order to maintain a thermal reactor temperature that is high enough to destroy any BTEX present. But the use of natural gas is not desired, as it represents a reduction in sellable gas, i.e. a financial loss for the gas producers. Improper co-firing can also result in inefficient combustion, with increased CO2 generation as a negative outcome.
Looking for answers
With a solid installed base of Claus feed gas analyser systems built up over multiple decades, a lot of historical data is available. This data includes operational experiences and learnings. The first instruments installed were aimed at looking into H2 S and NH3 , and really only served to provide insights into what was entering the SRU. Later, when more advanced analysers, capable of incorporating multiple measurement technologies became available, measurements for THC, CO2 and H2O were added. The additional measurement of THC has been extremely valuable, as plant operators are able to adjust the amount of air or oxygen they are delivering when the THC concentrations are varying. When present, THC “steals” oxygen from the H2S to SO2 conversion process. And when the THC suddenly goes away, there is surplus O2 present, which leads to excess SO2 production in the modified Claus plant.
With near complete understanding of the concentrations of the gas compounds entering the SRU, plant operations can operate more efficiently, more safely and with fewer emission incidents. For those that are not completely certain how to incorporate this analytical data into their control systems and recognise plant improvements, a company like Worley Comprimo with its Analyser Air Control Technology, “2ACT™ solution (see Fig. 1), can assist. Some plants are already benefitting from the 2ACT solution and there is a growing interest in it from design engineers and plant operation managers.
It is important to acknowledge that because the measured components (specifically H2S) are highly dangerous to humans, an area of concern when performing measurement of this feed gas is the safety of the maintenance team.
To minimise some of the risks associated with both performing this measurement and maintaining the analyser without compromising the reliability of the measurement, it is important to use an appropriate sample probe. The probe should be heated, have a means of filtering out liquids and particulates, and be designed with multiple shut off valves for both the sample inlet and outlet paths. One such probe is shown in Fig. 2 – the AMETEK Heated Acid Gas or HAG probe.
The analyser operation and maintenance should also be easy to understand and perform. The use of analysers that include several consumable items that need to be frequently replaced should be avoided. An analyser should be selected that can be serviced by the local maintenance team, so there is no need to wait for an expert to come to the plant.
However, because of the location of the measurement, individuals assigned to work on this analyser system should be experienced and clearly understand that the sampled gas stream will almost always be dangerous to personnel safety. The impact of “human error” should never be ignored and detailed work instructions should be present and followed.
The benefit of feed gas measurement
As experience with performing feed gas measurement has increased, additional points of process improvement are being evaluated, for example, the potential measurement of BTEX, but can this measurement be achieved?
From an analytical standpoint, we need to understand that the process analyser used for this kind of measurement is a combined ultraviolet / infrared instrument. Both spectral regions are required to perform this combination of measurements. For example, most of the hydrocarbons and water (H2O) are fully transparent (not detectable) in the ultraviolet (UV) regime. On the other hand, the component of main interest, hydrogen sulphide, is very challenging to make in the infrared (IR) absorbance spectra. The simple reason for this effect is that water IR absorbance is present at similar wavelengths as H2S. This poses a risk to the H2S IR absorbance measurement, as the absorbance would not be true to H2S alone. This effect is called interference /cross-sensitivity.
BTEX aromatic components exhibit both electronic and vibrational absorbances when adequately stimulated, meaning they have a detectable absorbance in both the UV-Vis and IR wavelength regimes. The AMETEK IPS-4 includes both UV and IR optical benches, making it a unique analytical tool for this measurement application.
The IR bench uses several narrow bandpass filters with pre-selected central wavelengths to isolate the absorbances from IR species of interest. Careful selection of bandpass filters aids in the reduction of interference, as it blocks the transmission of light from wavelengths not allowed to pass through the filter. The efficacy of the IR bench isn’t without its limitations. For example, total BTEX measurement in the IR is not suitable due to the overlapping spectra of components, as illustrated in Fig. 3. These aromatic compounds have similar carbon ring bond behaviour, meaning their absorbance spectra is likely to superimpose when given sufficient concentrations.
In contrast, the xenon flashlamp and diode array structure of the IPS-4’s UV bench provides selective and speciation capabilities that the IR bench lacks. This bench benefits heavily from the use of a diode array, which can collect the absorbance from multiple wavelengths. Collecting multiple wavelengths enables the use of more complex regression techniques for improved speciation, such as principal component analysis (PCA). Additionally, BTEX components in the UV regime exhibit enough distinguishing absorbance characteristics that further improves the efficacy of a PCA approach. For these reasons, a speciated BTEX measurement is most likely to see success when analysis is performed within the IPS-4 UV-optical bench. Fig. 4 showcases an example of BTEX absorbance cross-section spectra in the UV regime.
With the IPS-4 UV bench as the starting point for BTEX measurement, the next focus turns to what reasonable concentration limits can be made across all components. There are multiple factors at play here that can affect the instrument’s capacity for a successful measurement:
- What is the end-user’s typical concentration range for each BTEX component?
- At what process pressures and temperatures do we expect the sample gas to be supplied at?
- If H2S is present, what can we anticipate as the typical and maximum concentration levels?
- Are other contaminants present in the supplied sample (such as other sulphur-based species, amines, moisture, etc.)?
These are only a handful of questions specific to the application, but acquiring information for each subject is important.
These factors play a role in the minimum detectable concentration value that the IPS-4 can measure. As this BTEX will be in the gas phase, pressure and temperature will also influence the absorbance results due to pressure broadening effects and temperature related effects on the electron transition states of each BTEX component. A major limiting factor in BTEX measurement, however, will likely be H2S. This sulphur component exhibits a strong absorbance at wavelengths of <230 nm, but this absorbance can extend several wavelengths further depending on the pathlength chosen to compensate for BTEX measurement.
The significance of H2S on the efficacy of a BTEX measurement cannot be understated, as it will be the primary limiter on the minimum concentrations needed for each BTEX component. As an example, an IPS-4 analyser shipped to a gas processing unit was intended to measure BTEX in the presence of H2S. During calibration, the following concentrations of each BTEX component was used:
- benzene: 2,000 ppmv;
- toluene: 1,500 ppmv;
- ethylbenzene: 1,000 ppmv;
- m-xylene: 800 ppmv.
Because this sample process was also in the presence of H2S, typically 10 vol-%, but with a max. of 70 vol-%, the total wavelength band that is usable for BTEX calibration is significantly reduced. This is primarily due to H2 S absorbance saturation of the BTEX absorbances, creating what amounts to statistical noise. Fig. 5 illustrates this behaviour for reference. Given this behaviour, there’s a give-and-take relationship between minimum BTEX concentrations, acceptable H2S concentration levels, and the pathlength used in maximising BTEX absorbance.
Through analysis and testing, AMETEK found that adding a total BTEX measurement in addition to the measurement of the “classic” feed gas components is possible. Similar to the measurement of total hydrocarbons (THC) there is no differentiation between benzene, toluene, ethylbenzene, and xylene. The output is presenting the total BTEX.
How to use the information
It is well understood, and previously mentioned, that the presence of BTEX can lead to major issues with the Claus catalysts. But what can be done? Permanent co-firing under the premise “let’s be on the safe side” will lead to higher CO2 emissions. Permanent co-firing is also a direct loss of money as the gas which is co-fired cannot be sold. So, the best case would be that BTEX would be prevented from entering the Claus thermal reactor. And in some cases, BTEX removal systems are used. But can these systems consistently remove all of the BTEX? AMETEK experiences indicate that they do not. So, preventing BTEX from ever entering the SRU is not realistic, making it a good idea to measure for it and know when it is entering and at what concentrations. BTEX will not be permanently present in the feed gas and will vary in concentration when it enters the SRU.
Because the amount of co-firing gas used depends on how much BTEX is present, considerations similar to those made for the presence of THCs are required and must be made quickly. Any BTEX concentration increase should immediately increase the amount of co-firing gas to ensure it is properly thermally destroyed while any BTEX concentration decrease should result in a reduction in co-firing gas. After the BTEX goes away, the continued introduction of co-firing gas will result in wasted sellable gas and increased CO2 production, both negative outcomes.
Although speciation of the BTEX components is analytically possible with process gas chromatography (PGC) technology, the GC’s cycle time is too long to properly report changes in feed gas BTEX levels, thus significantly reducing any real improvements of co-firing gas management in the thermal reactor. However, these speciated measurements can be beneficial to a process specialist that is trying to better understand the root cause of the presence and varying concentrations of BTEX at the thermal reactor. Something to keep in mind.
Summary and conclusion
The initial investment in a feed gas measurement analyser and burner control system is not negligible and the application challenges are high with regards to measurement reliability and safety aspects (the SRU has the most toxic gas mixtures of the entire refinery). Successful examples exist of users that are benefitting from these analyser + control system configurations. But these installations work because of the cooperation of different functional teams. In order to achieve the goals of improving and optimising the overall unit performance, different technical disciplines have to work together, starting at the design phase of the processing unit and continuing through use of the analytical measurements during operation and proper predictive and reactive maintenance of the analytical devices. Choosing a “basic” instrument may result in not achieving the best possible process performance.
By adding BTEX measurement to the feed gas control system, plant operators can better adjust and control co-firing. This will lead to less natural gas use, optimal oxygen introduction, lower CO2 emissions, and longer catalyst life. Depending on current operational measurements and practices, significant money savings can be achieved.