Nitrogen+Syngas 392 Nov-Dec 2024
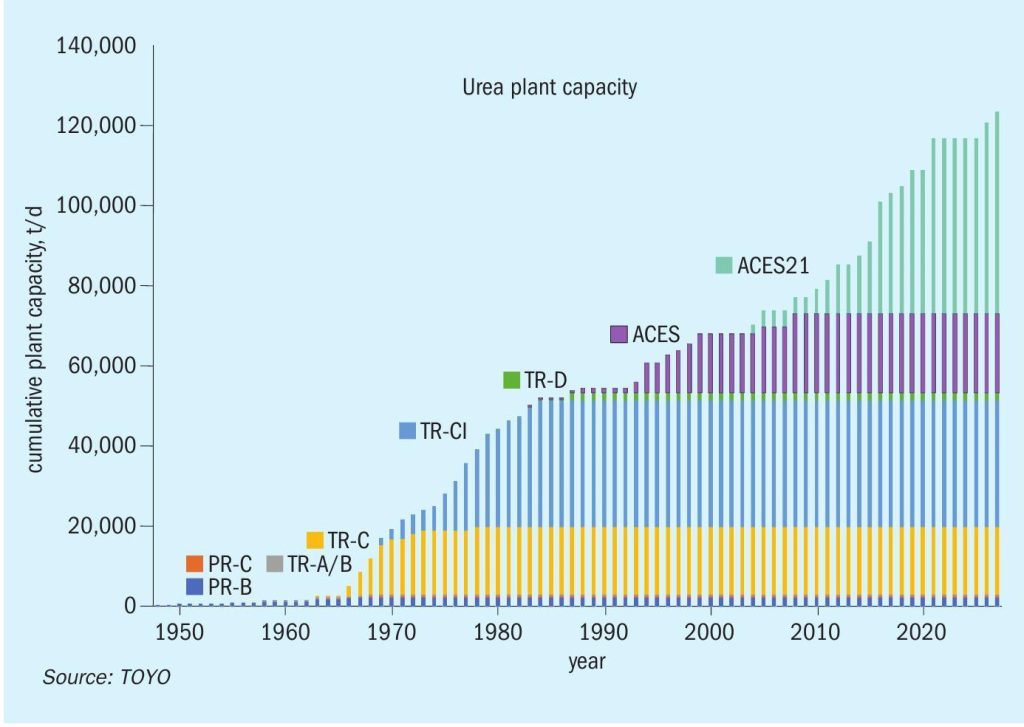
30 November 2024
Revamping to optimise performance and sustainability
UREA REVAMPING
Revamping to optimise performance and sustainability
Revamping aging urea plants with the latest urea technology brings many benefits. Not only can greenhouse gas emissions be reduced, but the overall performance and sustainability of these facilities can also be optimised. Hiroo Kunii of Toyo Engineering Corporation discusses TOYO’s approach to urea plant revamping.
Toyo Engineering Corporation (TOYO), a global leading engineering contractor and urea process licensor, has developed its proprietary urea processes since the development of the partial recycle process in the 1950s. Using its expertise, advanced technology and novel thinking, TOYO established ACES21™ in the late 1990s and has since been awarded 18 ACES21™ projects, including three 4,000 t/d urea projects in Nigeria which are the world’s largest single-train urea plant. Fig. 1 shows the cumulative capacity of urea plants using TOYO’s urea technology which has now reached approximately 120,000 t/d, corresponding to 40 million t/a and representing around 20% of the current global urea production. The revamping and upgrading of existing, aging urea plants is one of TOYO’s key strategies. This article provides a detailed account of TOYO’s approach to urea plant revamping.
TOYO’s revamping experiences
TOYO possesses a diverse array of stateof-the-art technologies for revamping existing urea plants. For example, TOYO has upgraded outdated urea synthesis technologies to its latest processes, converted the final product from prilled to granulated urea, added process condensate treatment facilities, etc. utilising its latest technology. These initiatives are aimed at enhancing energy efficiency (reducing CO2 emissions), lowering operational costs, increasing the added value of products, and contributing to environmental sustainability. Each project has been carefully planned, effectively implemented, and successfully completed, meeting all objectives and deadlines. Table 1 lists the revamping projects undertaken by TOYO, showcasing the remarkable achievements made worldwide through the application of these diverse technologies.
This section explains the methods of upgrading outdated urea synthesis technologies to TOYO’s latest processes, ACES21™ or ACES21-LP™ 1 as part of the revamping approaches discussed above.
Urea plants employing conventional processes, such as self-stripping and total recycle processes, are widespread globally, with approximately 200 to 300 plants in operation (TOYO estimate). The cumulative capacity of these plants has reached an impressive total of more than 100 million tons per year (TOYO estimate).
Fig. 2 shows the modification scheme for the synthesis section of the conventional total recycle process to convert it to ACES21™ or ACES21-LP™ . The equipment illustrated in pink, the stripper/ carbamate condenser and HP ejector, is added in the synthesis section; however, the existing reactor can be reutilised as it is. By virtue of this modification, a capacity increase of 50% can be achieved with energy savings of more than 30%, keeping the existing ammonia feed pump and carbamate feed pump without any modification. Replacement or modification of the CO2 compressor to increase its capacity is an option depending on the revamping concept. In case the purpose is to increase the production capacity or to improve the maintenance frequency of the existing reciprocating compressor, replacement with a new centrifugal type is one solution.
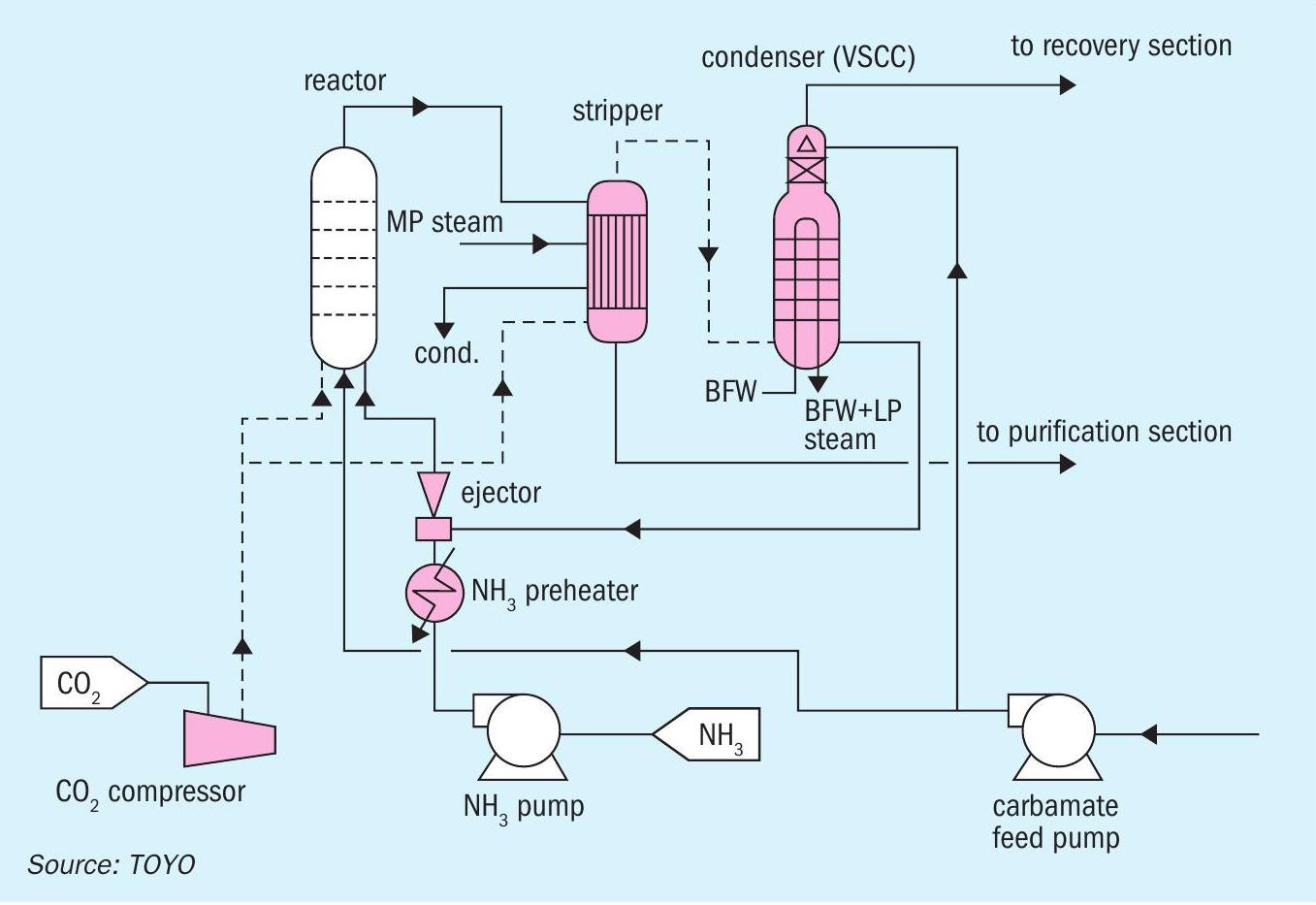
Strategies for reducing GHG emissions
In this section, the reduction in greenhouse gas (GHG) emissions achieved by applying the latest technologies to enhance the capacity of aged existing urea plants is discussed. TOYO believes that renovating old plants is a crucial pillar of environmental measures in the fertilizer industry. For example, for this study, an existing urea plant with a capacity of 1,620 t/d, one of the standard production capacities in the past, was examined to increase its capacity by 50% (to 2,460 t/d) by implementing advanced technologies and optimising processes. Table 2 shows the typical calculation results of energy savings and CO2 emissions when upgrading from a total recycle process to ACES21™ . It is obvious that a significantly lower carbon footprint is achieved after the revamp. Despite a 50% increase in production capacity, the annual CO2 emissions for urea production have only increased by 9%, thanks to the latest synthesis technology. Specifically, CO2 emissions can be reduced by 0.111 t CO2 / t urea, dropping from 0.393 to 0.282 t CO2 / t urea.
Revamping old urea plants using the total recycle process with the latest technology, as modelled above, could lead to significant reductions in greenhouse gas emissions. Assuming there are 200 such existing plants worldwide and applying this upgrade to 30% (i.e., 60 plants), and if these 60 plants could maintain a daily production of 1,620 tons without increasing capacity while reducing specific CO2 emissions from 0.393 to 0.282 t CO2 /t urea, it could result in an annual reduction of approximately 4 million tons of CO2 emissions. This significant decrease in emissions shows the environmental benefits of modernising outdated facilities and the contributions to global sustainability from these upgrades. It underscores the importance of using advanced technologies to reduce the environmental impact of industrial activities.
In this context, the evaluation aims to determine whether revamping an existing, aged urea plant offers advantages compared to a grassroots project, specifically from the perspective of CO2 emissions during construction. Two scenarios are considered: one where a new urea plant with a daily production capacity of 840 t is constructed, and another where the daily production capacity of an existing urea plant is increased from 1,620 t to 2,460 t using the latest technology (an increase of 840 t/d). As shown in Table 3, the CO2 emissions associated with the manufacturing and transportation of equipment and materials are reduced by 34% in the revamping scenario. While there may be constraints in the revamping scenario due to the restriction of the plot area and the condition of existing equipment and materials, the revamping case offers clear advantages over new construction from the perspective of CO2 emissions during construction alone.
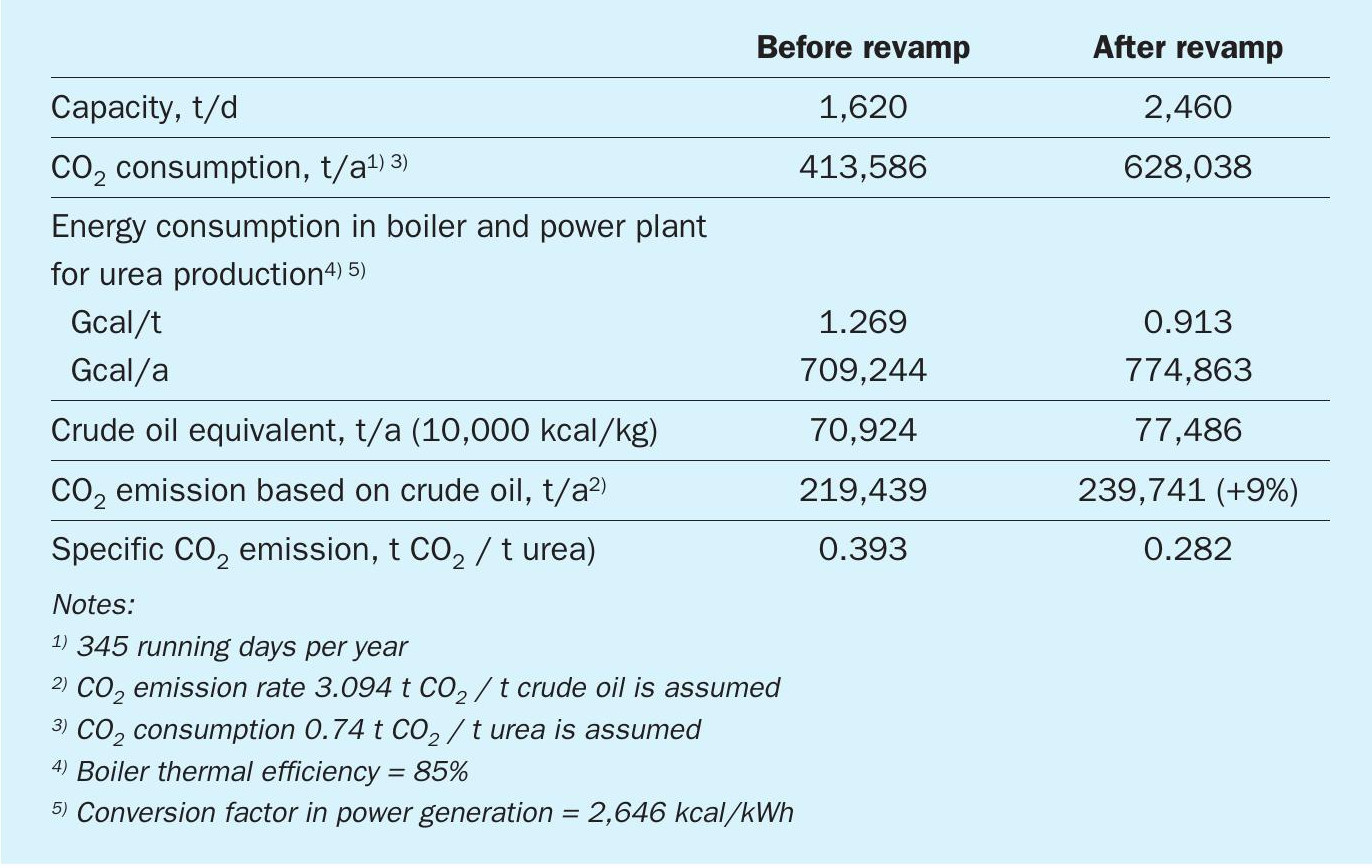
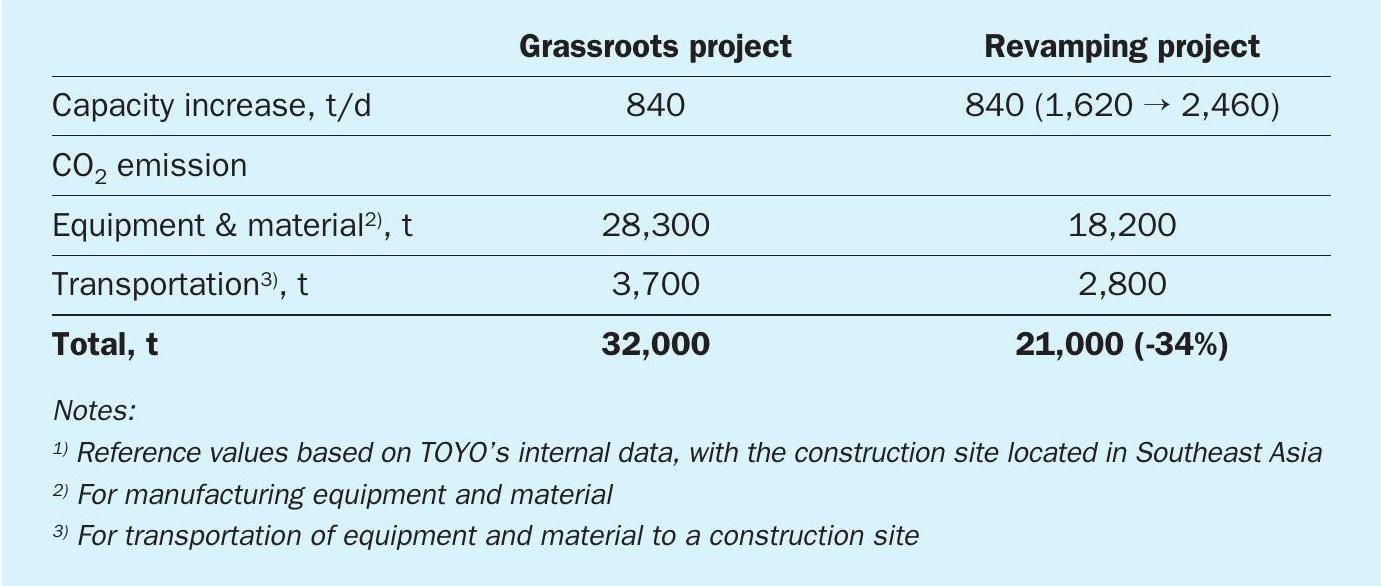
Next, a comprehensive evaluation of the CO2 emissions in the revamping scenario has been conducted, considering not only the construction phase but also the 20-year operational period of the plant. The analysis compares two scenarios: one where two old urea plants with daily capacities of 1,620 t and 840 t continue to operate, and another where the older urea plant with a daily capacity of 1,620 tons is revamped using the latest technology to achieve a daily capacity of 2,460 t. As indicated in Table 4, the CO2 emissions in the revamping scenario are reduced by 28% compared to the scenario where the old plants continue to operate. This revamping scenario focuses on an increase of 840 t/d, allowing the cessation of operations of an older unit with equivalent capacity, which is a high GHG emitter, thereby significantly contributing to the mitigation of global warming.
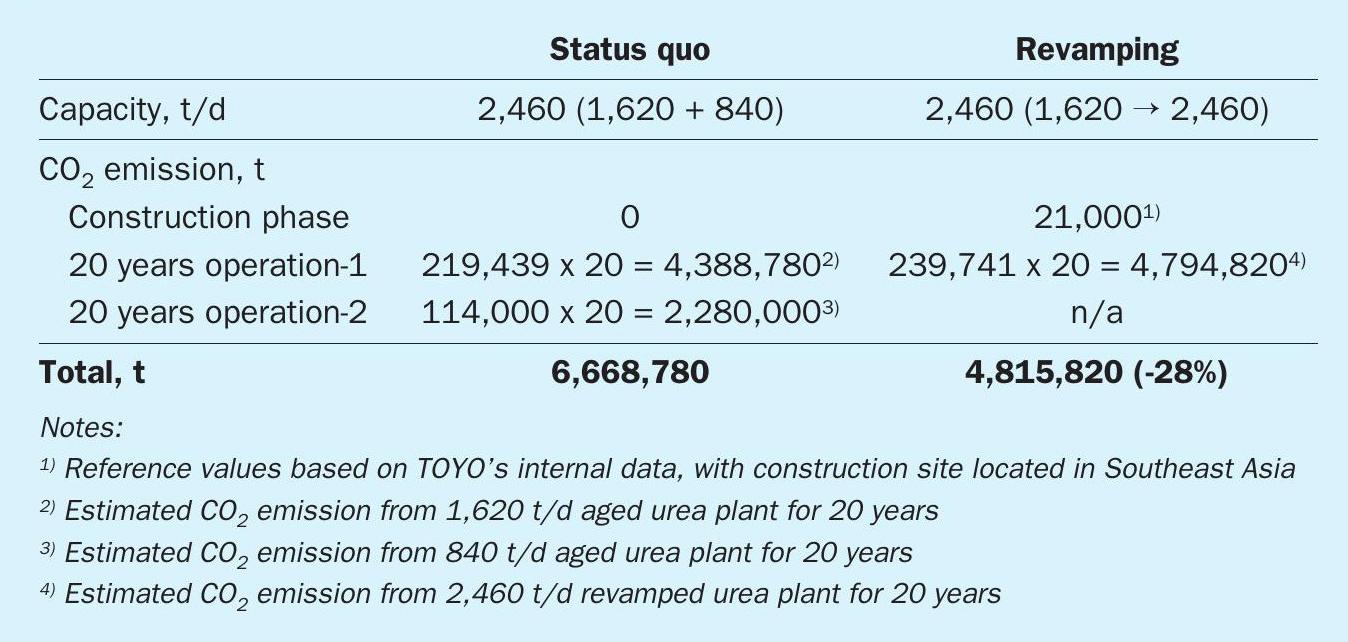
Thus, as a future trend, it is crucial to enhance the production and energy efficiency of old plants using the latest technologies such as ACES21™ /ACES21-LP™ , while simultaneously shutting down less energy-efficient plants corresponding to the increased production. Moreover, it is also necessary to increase the upstream ammonia plant’s production to match the increased urea production. Given that ammonia plants consume more energy than urea plants, it is imperative to focus on energy efficiency improvements and the transition to blue and green ammonia on the ammonia plant side. This transition involves adopting more environmentally friendly production methods and utilising renewable energy sources, which can significantly reduce the carbon footprint of ammonia production. By integrating these advanced technologies and strategies, the fertilizer industry can achieve a balance between increased production capacity and environmental sustainability. This comprehensive approach highlights the importance of continuous innovation and adaptation in industrial processes to meet the growing demands while minimising environmental impact.
It emphasises the need for a concerted effort to modernise outdated facilities and adopt more sustainable technologies, paving the way for a more sustainable future.
Replacement of urea synthesis equipment
It is worth mentioning simpler revamping projects undertaken by TOYO, which involved the replacement of existing synthesis equipment in urea plants, rather than the extensive modifications mentioned earlier. Synthesis equipment in urea plants that has been in operation for over 20-30 years inevitably deteriorates and requires replacement according to the circumstances. Table 5 shows recent records of synthesis equipment renewals. There have been some instances of replacing or refurbishing equipment for both older and latest technologies, including the total recycle process. In these cases, state-of-the-art technology, including the latest equipment models, corrosion-resistant material DP28W™ , and the latest high-efficiency baffle plates, have been applied to enhance the reliability and performance of the equipment. These equipment renewal projects often include the dispatch of specialists for on-site installation of internal parts and start-up support as part of the scope of work.
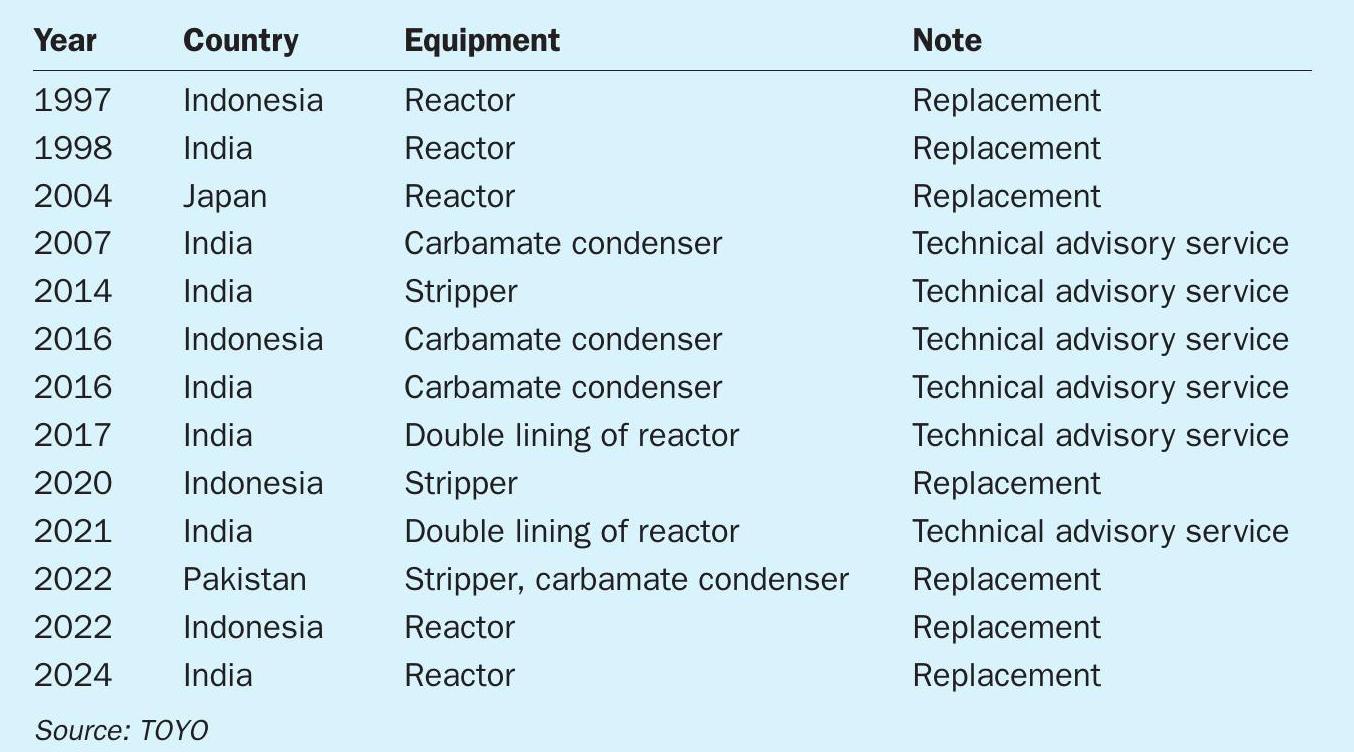
Conclusion
As discussed in this article, TOYO’s latest urea technology can be leveraged to enhance and improve the energy efficiency of existing, aging plants, significantly contributing to global GHG reduction. By implementing these advanced technologies, not only can greenhouse gas emissions be reduced, but the overall performance and sustainability of these facilities can also be optimised. As a leading licensor of urea technology, TOYO remains committed to contributing to a sustainable society worldwide, continuously innovating and providing solutions that support environmental sustainability and energy efficiency.
Reference