Sulphur 416 Jan-Feb 2025
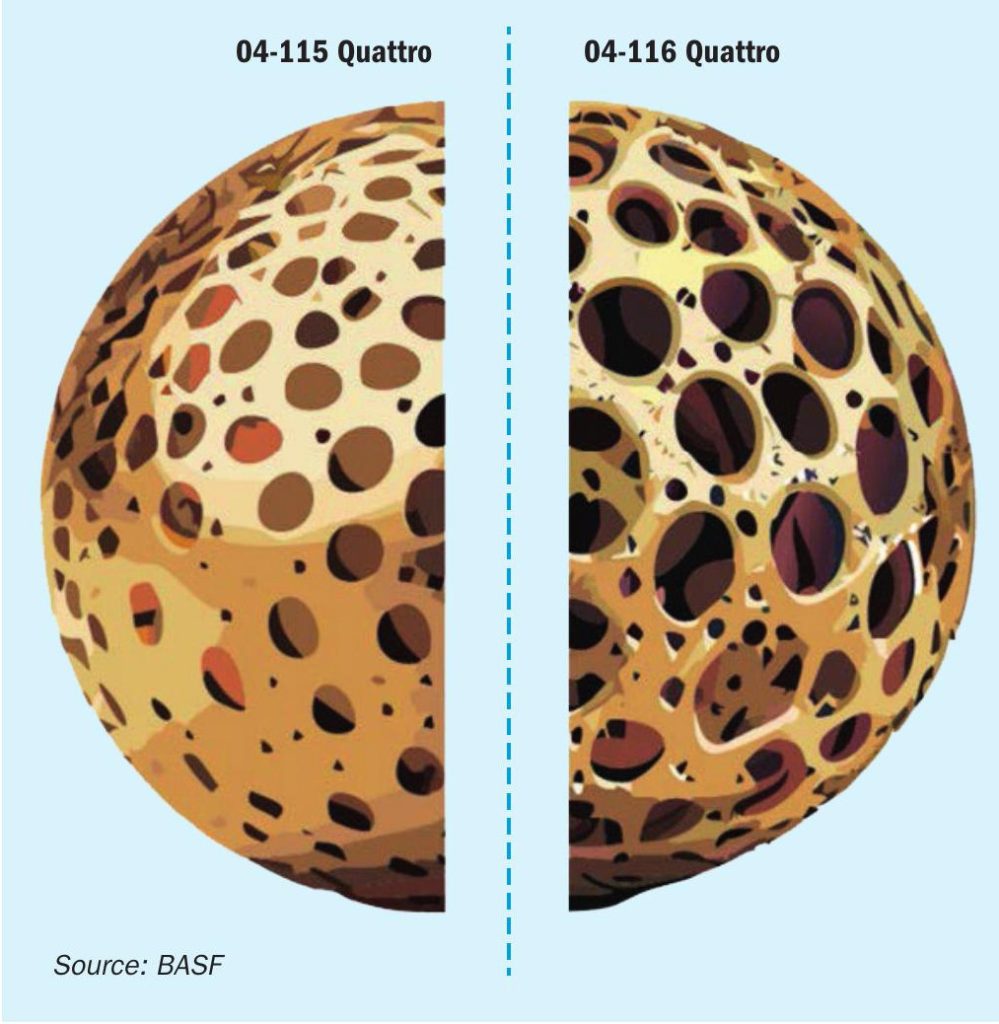
31 January 2025
Staying ahead of SO₂ emission limits
BASF has produced sulphuric acid for various industrial applications since 1866 and has been producing catalyst for the sulphuric acid process since the early 20th century. Today, BASF operates six sulphuric acid and 12 sulphonation plants with inline SO2 oxidation units worldwide, all using BASF’s in-house catalyst technology with world class plants operating at emission levels below 50 ppm SO2. The last 20 years have brought new challenges such as tighter emission regulations and cost pressure to the sulphuric acid market. This has led BASF to be at the forefront with cutting-edge research into one of the oldest catalysts of the portfolio.
BASF works directly with customers to make sure customers achieve the best performance under the specific design and operation conditions of their reactors. This is enabled through BASF’s state-of-the-art testing facility and analytics combined with more than 150 years of research and experience.
SO2 emission regulation
Nearly all chemical and industrial processes result in a certain amount of by-products or waste components, which are harmful for our environment. The impacts are plentiful and can lead to soil contamination, eutrophication, and most importantly, to global warming. In order to reduce their negative effects on the environment, the emission of these harmful components is regulated, and measures are taken by companies to reduce their emissions. Sulphur dioxide (SO2) and sulphur trioxide (SO3) also fall under these regulations. Starting from the first ratification of the Helsinki Protocol in 1985, the emission limits were further decreased, and other protocols were implemented to decrease the amount of SOx emitted through various sources (e.g. automotive, electricity generation, and industrial processes) namely the Oslo Protocol in 1994 and the Gothenburg Protocol in 1999, which was further amended in 2012. Since SO2 is not just poisonous, but also a major contributor to acid rain when it is released to the atmosphere, the emission limits for SO2 for sulphuric acid plants became ever stricter over the past decades. The graph in Fig. 1 displays the development for average SO2 emission limits for sulphuric acid producing units in Germany, which follow the regulations provided by the European Union and the German Federal Government.
As displayed in Fig. 1, there has been a significant decrease in emission limits for the most common sulphuric acid producing technologies over the past 25 years in Germany. Furthermore, a new LVIC-BREF (best available techniques reference document for the manufacture of large volume inorganic chemicals) for the European Union is under discussion which will most likely result in a further decrease in SO2 emission limits in the near future. These emission limit reductions for SO2 resulted in a lot of changes in the industry: The use of scrubbers to remove excess SO2 for single contact units, double contact units with five catalyst beds, and the implementation of caesium-promoted catalysts that are active at lower temperatures to maximise the conversion of SO2 to SO3. Among others, these changes made a major contribution to the reduction of SO2 emissions whilst also maximising the sulphuric acid output of these units. However, as stricter emission regulations are already on the horizon, more powerful tools need to be implemented in the future to be able to comply with the regulations.
New extruded shapes
An elegant way to accomplish this is with the use of even more powerful catalysts, which enable higher conversion rates. BASF’s approach to achieve this is through the improvement of catalyst shape geometry.
In 2016 BASF launched the Quattro shape geometry for its sulphuric acid catalyst family. This outstanding catalyst shape geometry combines a 30% increased surface area with significantly increased catalyst strength whilst maintaining the pressure drop of Star Ring catalysts.
Since the launch of O4-115 Quattro in 2016, many additional customers are benefiting from realised performance improvements, such as higher capacity, lower catalyst loading volume, or significant conversion increase. A major gamechanger in emission reduction is BASFs high performance catalyst O4-116 Quattro. This catalyst combines the geometrical benefits of the Quattro family with a superior active mass composition and enables significant reduction in emissions.
O4-115 versus O4-116
For caesium-promoted catalysts, there are two different application fields. The first application field is as an ignition layer for the first pass. This is mostly necessary in metallurgical plants, where the inlet temperature to the first bed can fluctuate and is in most cases around 400°C. The second field of application is for emission reduction after the intermediate absorption step as described above. As both fields have a different set of requirements, such as different upper operating temperatures, or mass transfer properties, it is not favourable to use one single catalyst to do both jobs, as a lot of potential remains unused. Hence, BASF developed two different caesium-promoted catalysts in its portfolio, namely O4-115 as the catalyst dedicated to operating in bed 1 ignition layers and in single absorption units, i.e. situations with high SO2 and SO3 concentrations where the conversion is mostly equilibrium controlled. O4-116 was developed as the high-performance low temperature catalyst for applications after the intermediate absorption, where a high mass transfer rate is key to maximise the conversion.
As displayed in the schematic in Fig. 2, the key difference between O4-115 and O4-116 is the pore structure and pore size distribution of those catalysts. The carrier material of O4-115 is specifically designed to operate under conditions where the oxidation reaction of SO2 to SO3 is equilibrium controlled meaning high temperatures and high SO2 and SO3 concentrations. Here, the stability of the catalyst is crucial, to withstand the extremes it is experiencing and an increase in porosity has no apparent benefit, as the reaction is not mass transfer limited. The opposite is the case for the intended application field of O4-116. Here mass transfer limitation is the key issue, which needs to be overcome by a superior pore size structure to enable a fast diffusion of all reactants in and out of the active phase.
Surpassing state-of-the-art performance
When applying the fundamental concepts of a change in shape geometry from Star Ring to Quattro, O4-116 displays not just the same benefits as seen with the other catalysts, such as a higher mechanical strength, lower attrition and a higher geometric surface area. The activity increase surpasses the expected boost originating from the higher geometric surface area. This is a result of a synergistic effect between the pore structure of the O-116 carrier material and the Quattro shape geometry surpassing the activity standard catalysts by far. When comparing the kinetic rates of O4-115 Quattro and O4-116 Quattro, O4-116 Quattro has a significantly higher activity between 20 and 40% at temperatures below 405°C. This is significantly higher than is the case for the Star Ring geometries and can only be explained by a synergistic effect, since the base composition of the catalyst is not changed and only a change in the shape geometry was conducted.
The superior activity and the low ignition and operating temperature of O4-116 Quattro enable sulphuric acid producers to further decrease their SO2 emissions without the need to conduct significant capex investments. The catalyst is capable to oxidise more SO2 due to its increased geometrical surface area enabling a higher conversion with the same amount of catalyst, which was employed before. O4-116 Quattro is significantly outperforming O4-115 Quattro, which displays a comparative activity and operating range to the old O4-116 Star Ring. The significantly lower ignition temperature and improved operating range enable entirely new potentials for emission reduction in sulphuric acid plants.
O4-116 Quattro reference
The target of this project for the client was to reduce the start-up SO2 emissions of the converter after hot and cold shutdowns. The client operates a zinc smelter in Europe and has an annual SO2 emission contingent. This means that there is a total amount of SO2 per year, which the client is allowed to emit.
Especially after a cold shutdown, the initial emission level during start-up is quite high until the catalyst in each converter bed reaches the operating temperature. Therefore, it is of key interest to reduce these SO2 emissions upon start-up and avoid exhausting the emission contingent.
The converter is a double absorption unit with an intermediate absorption step after the 2nd stage and a nominal capacity of 1,080 t/d with a target conversion of 99.90%. The average gas composition is as follows:
- Nominal volume flow: 129,000 Nm³/h
- Feed source: metallurgical
- SO2 : 7.8 vol-%l O2: 9.9 vol-%
- Nitrogen: balance
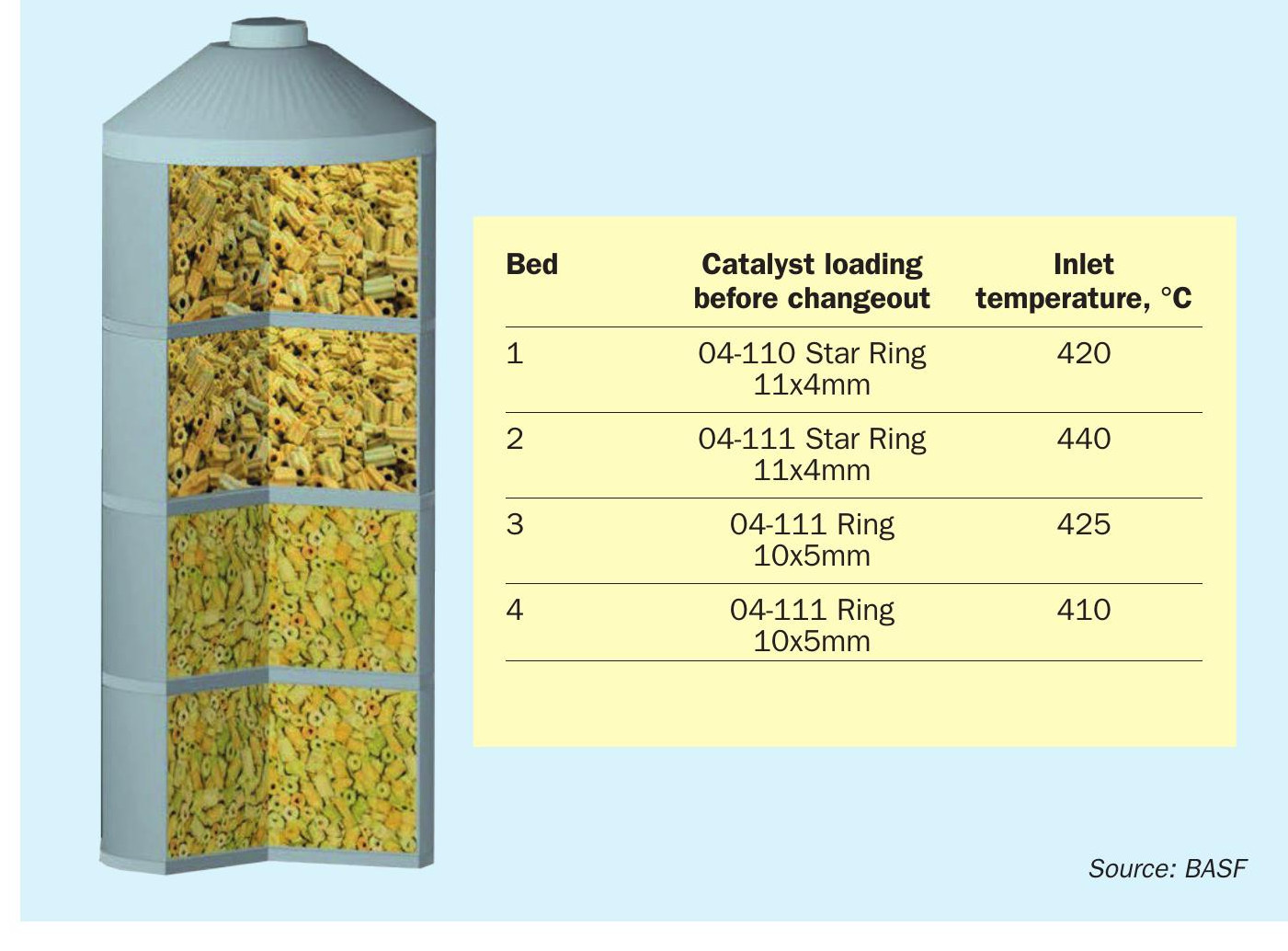
As shown in Fig. 3, the converter was loaded with Star Ring- and Ring-shaped catalyst only, with the latter being phased out in the meantime. Additionally, this converter setup was not utilising any caesium-promoted catalysts in the original setup but was solely running on pure vanadium catalysts. Since a catalyst changeout was scheduled in late-2022, BASF conducted BOSS100 measurements in early 2022 to assess the current performance of the converter and give indications about potential catalyst changeouts.
As visible from Table 2, the performance measurement on 31 January 2022 displayed that bed 1 is due for a changeout. This was expected, as the catalyst was installed more than two years prior to the measurement and the catalyst activity had decrease to the expected extent, where a changeout is required. Additionally, bed 3 performance is below average and displays signs of catalyst aging. The measured SO2 conversion of the bed was only 66%, which is below expectations. Beds 2 and 4 were still able to regain the loss of conversion of their preceding passes, but the target conversion of 99.90% was not reached during the period when the BOSS100 measurement was conducted. Therefore, it was decided to exchange the first pass as scheduled and additionally change out pass 3 to fully regain the converter performance. Due to the need of the client to reduce the SO2 emissions on start-ups, it was decided to install an ignition layer in the third stage after the intermediate absorption step. BASF proposed to employ the newly launched O4-116 Quattro catalyst to fully harness the benefit of this catalyst technology as ignition layer.
In total, 30% of the total bed volume was changed to O4-116 Quattro. This should ensure good start-up behaviour of beds 3 and 4 following the intermediate absorption stage, and thus result in a decreased SO2 emission upon start-ups. The remainder of the bed was equipped with O4-111 Star Ring catalyst. Beds 2 and 4 were not touched during the shutdown and the inlet temperatures for each bed remained the same as before.
Approximately a year after the catalyst exchange, a second BOSS100 measurement was conducted to verify the conversion increase predicted from the simulations.
As shown in Table 3, the catalyst exchange in bed 1 resulted in the expected performance increase of the respective bed. In addition, the catalyst exchange in bed 3 resulted in a significant performance increase of the bed from 66% to 96.9% of the incoming SO2 converted to SO3. This exceptional increase of 46% of conversion also strongly contributes to the total conversion increase to 99.93%, which strongly exceeds the targeted conversion of 99.90%. This result displays the power of caesium-promoted catalysts as well as the Quattro shape geometry achieving significantly higher SO2 turnovers even with only 30% of the catalyst bed being equipped with this technology. However, the main reason for the exchange was to improve the start-up behaviour of the converter and thus reduce the SO2 emissions during startup.
Start-up behaviour improvements using O4-116 Quattro
To demonstrate how an ignition layer after the intermediate absorption stage can contribute to a significant reduction in SO2 emissions, two start-up cases were investigated. The first investigated cold start-up in May 2022 from the period before the catalyst changeout was conducted. The second investigated case was in May 2023 after the new catalyst was installed (Fig. 4).
As displayed in the graph in Fig. 4a, a short emission peak of 67 ppm was detected directly after the gas flow to the converter was started. The flow then decreased for approx. 40 minutes before increasing again to 1,880 Nm³/min. During that increase, the SO2emission detected at the stack increased to around 422 ppm for an hour, before settling down to 133 ppm and stabilising. The total duration of the startup emission peak was two hours, with an emission of 91.4 kg SO2measured at the stack of the converter. The observed trend with a timeframe, where the emissions are significantly above the average, can be regarded as normal. The converter beds are not fully at operating temperature resulting in decreased activity. Only when all beds are fully thermally equilibrated do the SO2emissions drop significantly.
This outstanding result displays the high potential of O4-116 Quattro catalysts as an ignition layer. Under ideal conditions this catalyst can significantly decrease the SO2 emissions upon start-up and thus contribute to a decreased risk of exceeding the SO2 emission contingent for the client.
However, this can only be achieved when the entire converter is at least preheated close to operating conditions, before the process gas is directed to the converter. Without the preceding converter beds being operational, an ignition layer after the intermediate absorption step can reduce the stack emissions upon cold start-ups, but it cannot compensate for a significantly reduced conversion in the first passes. Therefore, standard start-up procedures, such as sufficient pre-heating of the converter still need to be followed to achieve the desired effects of an emission reduction. As always, operational excellence and diligent personnel training are key to a sustainable operation of sulphuric acid units and staying ahead of today’s and tomorrow’s SO2 limits.
Conclusion and next steps
With the launch of O4-116 Quattro, BASF has completed the Quattro product family offering the most powerful catalyst technology to date. However, the Quattro technology is not the end of what BASF can offer as new catalyst technology to supports clients in achieving their production and emission targets. BASF’s X3D® catalyst technology based on 3D-printing marks further step change in catalyst technology.
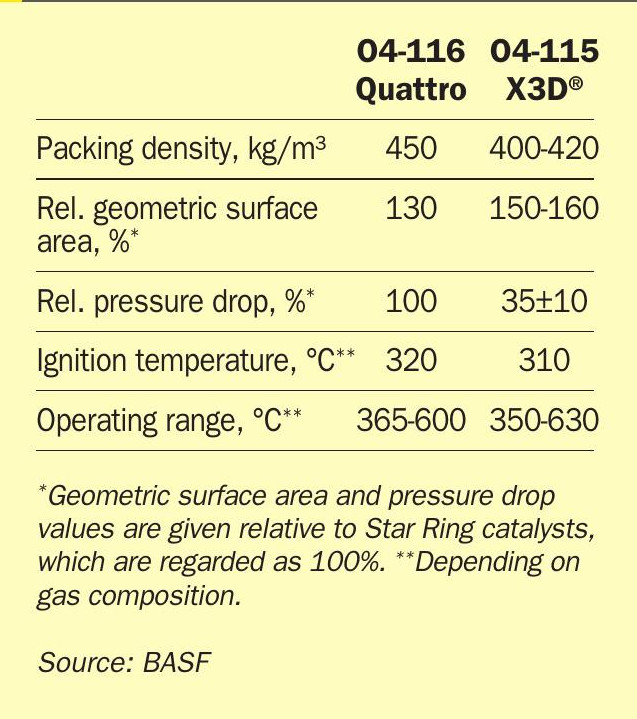
As shown in Table 5, X3D ® technology enables an even higher potential to reduce start-up emissions with the lower ignition temperature and operating range, as well as the higher surface area. Due to the low pressure drop increase, this catalyst can be added as ignition layer on top of existing beds without the threat of losing capacity due to increased pressure drop and can significantly contribute to increased conversion during continuous operations and especially during start-ups.