Sulphur 417 Mar-Apr 2025
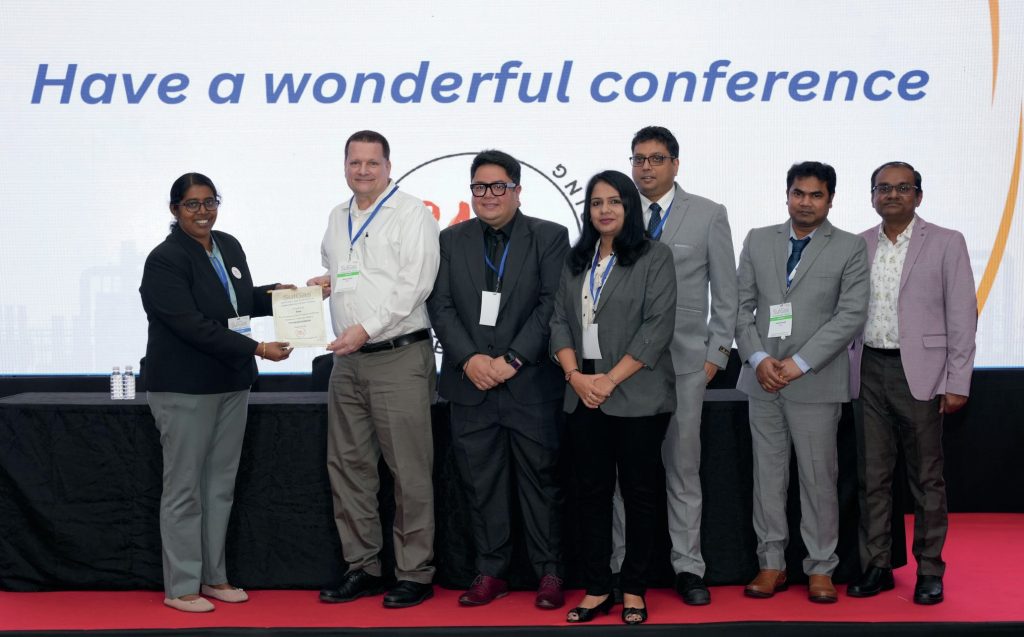
19 March 2025
Sulgas Mumbai 2025
CONFERENCE REPORT
Sulgas Mumbai 2025
Building on the success of its previous conferences, SulGas Mumbai 2025 brought together 154 sulphur and gas treating stakeholders, representing 68 companies for its 7th technical forum in the Indian subcontinent. We report on some of the key topics on the agenda.
The 7th SulGas® Conference, organised by Three Ten Initiative Technologies LLP, took place from 5-7 February 2025, at the Holiday Inn, Mumbai. The conference featured 25 speakers in interactive technical sessions, fostering maximum technical exchanges among participants. Alongside the conference a dedicated exhibition area provided full-day access for all delegates. The conference agenda featured ten sessions. Each session concluded with a detailed panel discussion, sparking valuable dialogue between the audience and speakers.
The key themes of the conference were:
• Foundations masterclass – foundation training in the fundamentals of process instrumentation for sulphur recovery units, presented by Anatha Kukkuvada of Ametek Process Instruments.
• Gas processing and troubleshooting – providing field insights into process reliability, best practices for SO2 breakthroughs, case studies on iron sulphide contamination in gas treating and issues of a liquid treater.
• From biofeeds to beyond Claus – including decarbonisation, biogas catalyst, and green refining guidelines.
• SRU process automation and instrumentation – case studies providing field insights, technology advancement, optimisation with AI and gas analysis using process analytics.
• Gas processing: Challenges and innovations – simulation of trace component handling, solvent technology for selective treating and technology advancement in automation.
• Integrated approach to SRU optimisation – real time monitoring for decarbonisation, field insights on preventative maintenance and technology advancement in simulation.
• Minimising risks in SRU start-up and shutdown – operations and analyser best practices for safe transitions.
Some of the topics discussed at the conference are highlighted below.
Amine absorber fouling
A frequent problem in Indian refineries is amine absorber fouling. When this happens, the amine and gas supply must be temporarily stopped so the vessel can be cleaned. Usually there is not enough time to thoroughly clean the tower and the equipment remains partially fouled, shortening the interval before cleaning will be needed again. This problem is costly and time consuming. Ben Spooner of SGS Amine Experts described how to predict when the risk of absorber fouling increases and how to prevent, or at least delay, the adverse effects. By using a combination of good amine analysis, appropriate operation methods and an understanding of the equipment design, engineers and operators can take control of the amine plant.
SO2 breakthrough in the SRU TGT
The tail gas from the Claus section of a sulphur recovery unit (SRU) contains small amounts of unconverted H2S, SO2, COS and CS2 and traces of sulphur as mist or vapour. In a typical tail gas treating (TGT) unit based on the reduction-absorption-regeneration process, the TGT design includes a quench column downstream of the hydrogenation reactor, mainly to cool the reactor effluent gases before it enters the amine solvent in the absorber column. The quench column also serves as a guard against possible SO2 slippage from the upstream hydrogenation reactor into the amine solution, which has the potential to result in major plant upsets and be the cause of permanent damages and losses in the SRU.
Typically, the first response to tackle SO2 breakthrough is to address the “symptom”, the drop in pH in the quench water circuit. Neutralising agents (ammonia or caustic) are injected or dosed to bring the pH back to normal values, but in many cases, due to the delayed action from the operator, there can be significant damage to the downstream amine system. Fluor provides a design which provides sufficient time for the operator to prevent SO2 reaching the downstream amine system. However, this does not address the real cause and does not provide a “cure” to this condition. Debopam Chaudhuri of Fluor explained how continuous monitoring of key operating parameters has the potential to reduce and even eliminate the chance of any SO2 breakthrough, thus providing longer run lengths and longer operating lives for the SRU.
Closing the cycle by spent acid regeneration
In downstream operations, H2S is generated in processes where sulphur-containing hydrocarbons are treated to remove sulphur and meet stringent environmental standards for fuel emissions. Typically, H2S is first converted to sulphur in a sulphur recovery unit, then transported to an acid plant to produce sulphuric acid, requiring two separate facilities. Paul Zorn of P&P Industries explained how P&P’s Sulphur Oxidation Process (SOP) provides a more efficient alternative by converting H2S directly into sulphuric acid in a single plant. This eliminates the need for sulphur production, transport, storage and operation of two plants. The SOP technology is established and has been successfully implemented in operational plants, including those incorporating spent acid treatment. High acid concentration (>98.5%) or oleum production can be achieved with add-on units.
COS and mercaptans removal
Gas and liquid hydrocarbon streams from refineries and gas plants must be well cleaned of sulphur compounds such as H2S, COS and mercaptans, dictated mainly by environmental constraints. Although a copper strip test may indicated acceptable sulphur content today, COS slowly reverts to H2S and CO2 in the presence of water so the same test administered tomorrow may fail. Users of legacy simulators have complained for years that predicted COS removal has been far removed from observations. That deviancy has now been rectified, Jeff Weinfeld of Optimized Gas Treating introduced a new model for COS absorption into alkaline solvents based on mass transfer rates enhanced by reaction kinetics, the first time that commercial software has had the ability to simulate this aspect of COS absorption accurately.
SRU Energy and cost optimisation
Most operating companies consider the SRU as a license to operate and therefore, if the SRU is working reliably and the emission targets are met, little attention is paid to optimise the unit. However, with modern monitoring algorithms, historical data availability and active support of the unit engineer and technology specialist, both financial as well as sustainability improvement can be achieved.
Together with Slovnaft, Worley Comprimo has developed a near real-time monitoring system dashboard using data sharing via the Cloud. Proprietary KPIs have been developed and tested for their relevance. Using a two-year data set containing minute average data, trends and insights were used to optimise performance. Claudia Guarino of Worley Comprimo described the main learnings and improvements with respect to energy optimisation which supports sustainability targets for Slovnaft.
Tubesheet protection system inspections
Tubesheet protection systems (ceramic ferrules) are one of the most vulnerable refractory systems in a sulphur plant. Failure analysis is a very complicated systematic process, requiring extensive knowledge and experience in order to reach the proper conclusions. Ceramic ferrule and tubesheet lining problems are often the first symptom of a problem, regardless of origin (plant design, installation, operation and/or maintenance). One broken ferrule, undetected, can cascade into an unplanned shutdown, equipment damage, premature corrosion of tube welds and metallurgy and eventual leaks. Domenic Misale of Industrial Ceramics presented a blueprint that has proven to be a useful tool for methodical visual tubesheet production system inspection.
Continuous BTEX emission monitoring from SRU furnace
Dr Abhijeet Raj of IIT Delhi discussed how by using a previously created precise reaction mechanism for Claus furnace simulations, a simplified reaction model for the degradation of aromatics in the furnace was constructed to create a BTEX soft sensor. The generated kinetic model was incorporated into the Aspen HYSYS software to perform Claus furnace simulations. For a sufficiently broad range of acid gas flow rates, air flow rates, fuel gas flow rates and the concentrations of H2S, CO2 and BTEX in the acid gas feed, the model was able to predict the furnace temperature withing a 5% error margin and the BTEX concentration within a 5 pm error margin based on comparison with plant data. The great accuracy of the plant data predictions made by the BTEX sort sensor suggests that it can be used in SRUs to continuously measure the amount of BTEX that leaves the reaction furnace.
Mid-IR tunable laser analysers for SRU applications
Tunable laser gas analysers have been successfully proven in many demanding process control applications. Dr Pawel Lluczynski of Airoptic reported on the successful installation and operation of a tunable laser based air demand analyser for an SRU process.
It was put into operation at one of Sweden’s refineries, where it has been operating continuously in a closed loop for process control since 2023. The laser air demand analyser offers several advantages over UV analysers such as: high sensitivity, excellent selectivity, facilitates real-time data acquisition, suitable for varying conditions and non-destructive measurements. In addition the laser analyser does not require extensive sample conditioning, simplifying deployment and reducing maintenance needs.
Pioneering practices in green refining
In a green refinery, the concentration of acid gas from the amine regeneration unit has an extremely low H2S content, which originates entirely from the addition of dimethyl sulphide (DMDS) as there is no sulphur in the feed to the HDO unit. Separating and recycling the H2S reduces the need for continuous DMDS addition, helping both the environment and economic efficiency by decreasing chemical consumption. Ayan Dasgupta of Fluor introduced an innovative system that eliminates the need for an SRU by employing a two-unit approach that combines a conventional amine recovery unit with a specialised unit unique to green refineries, termed the H2S Enrichment Unit (H2SEU). The H2SEU unit effectively increases the H2S concentration from the very low levels in the feed gas to the required to allow it to be recycled back into the process.
Registrations are now open for SulGas® ’s first sulphur recovery and gas treating conference in Kuala Lumpur, 2-3July at Impiana KLCC.
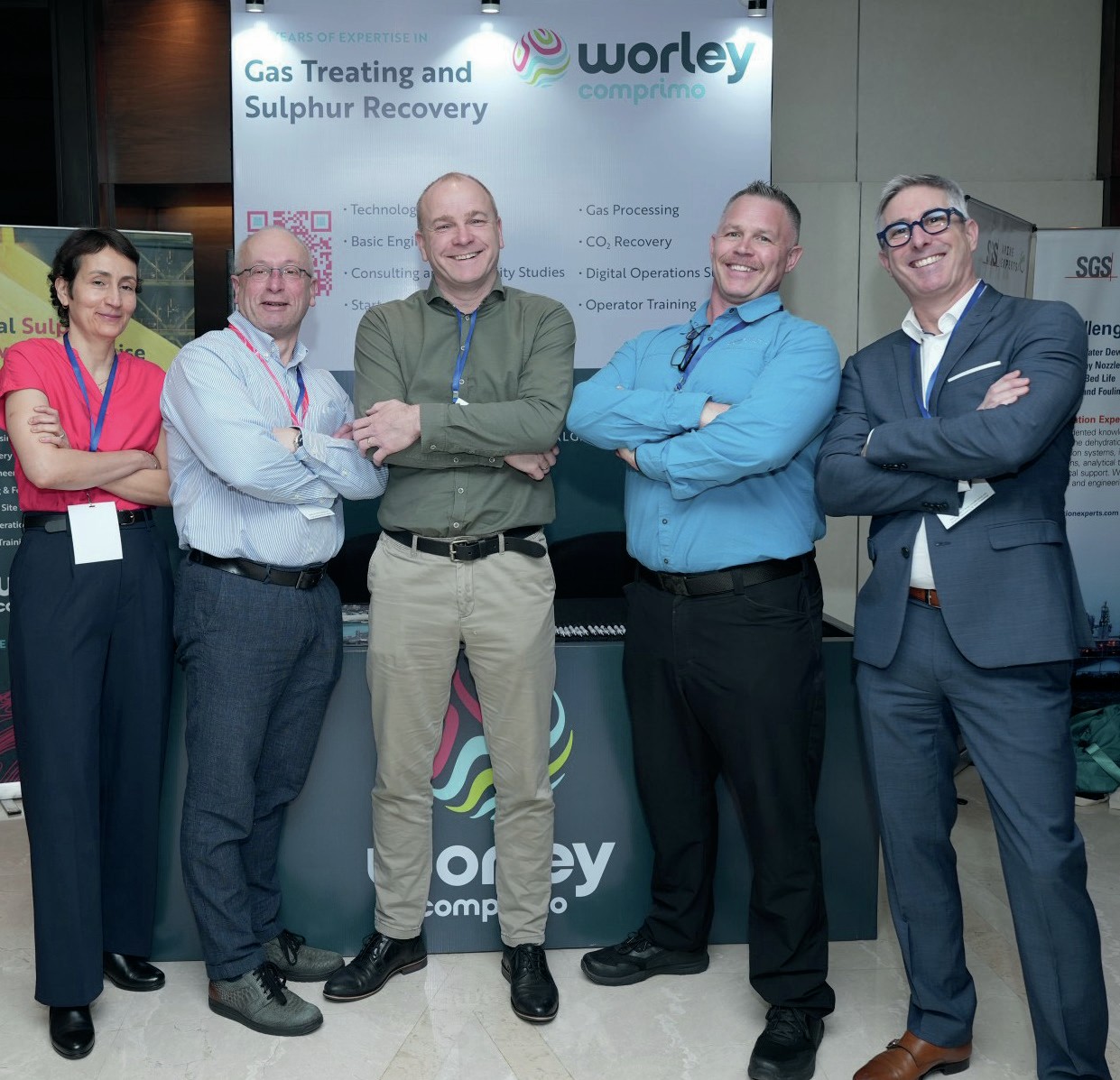