Nitrogen+Syngas 363 Jan-Feb 2020
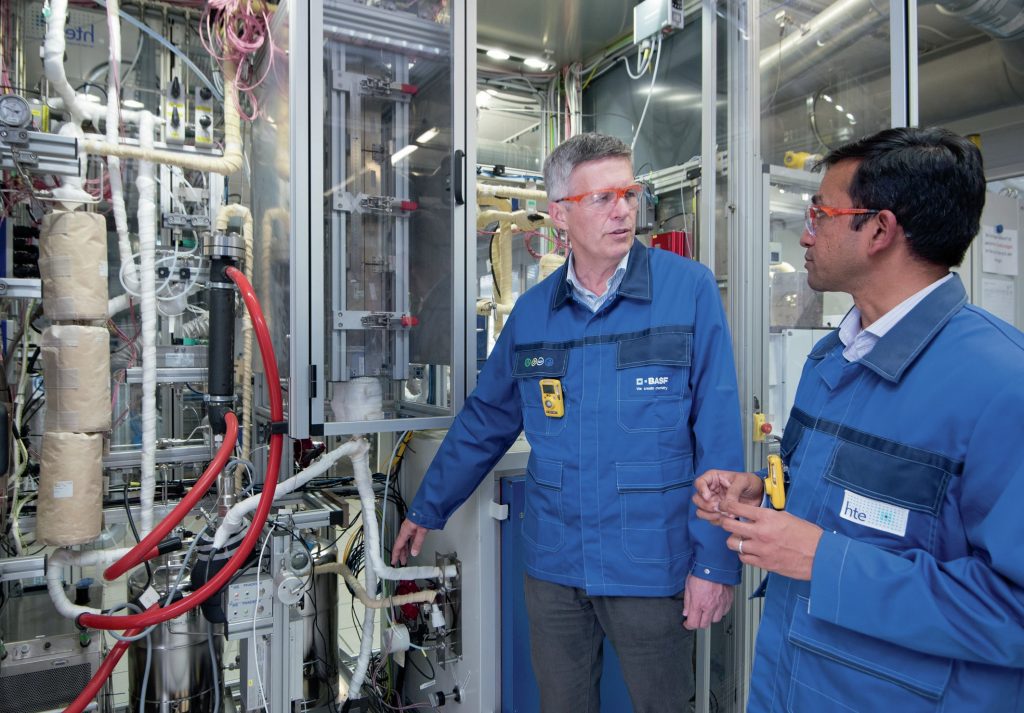
31 January 2020
Emission-free methanol
CARBON MANAGEMENT
Emission-free methanol
BASF has filed a patent application for a greenhouse gas-free method for producing methanol. If successful on a large-scale, the process could eliminate carbon dioxide emissions throughout the entire production process from synthesis gas generation to pure methanol.
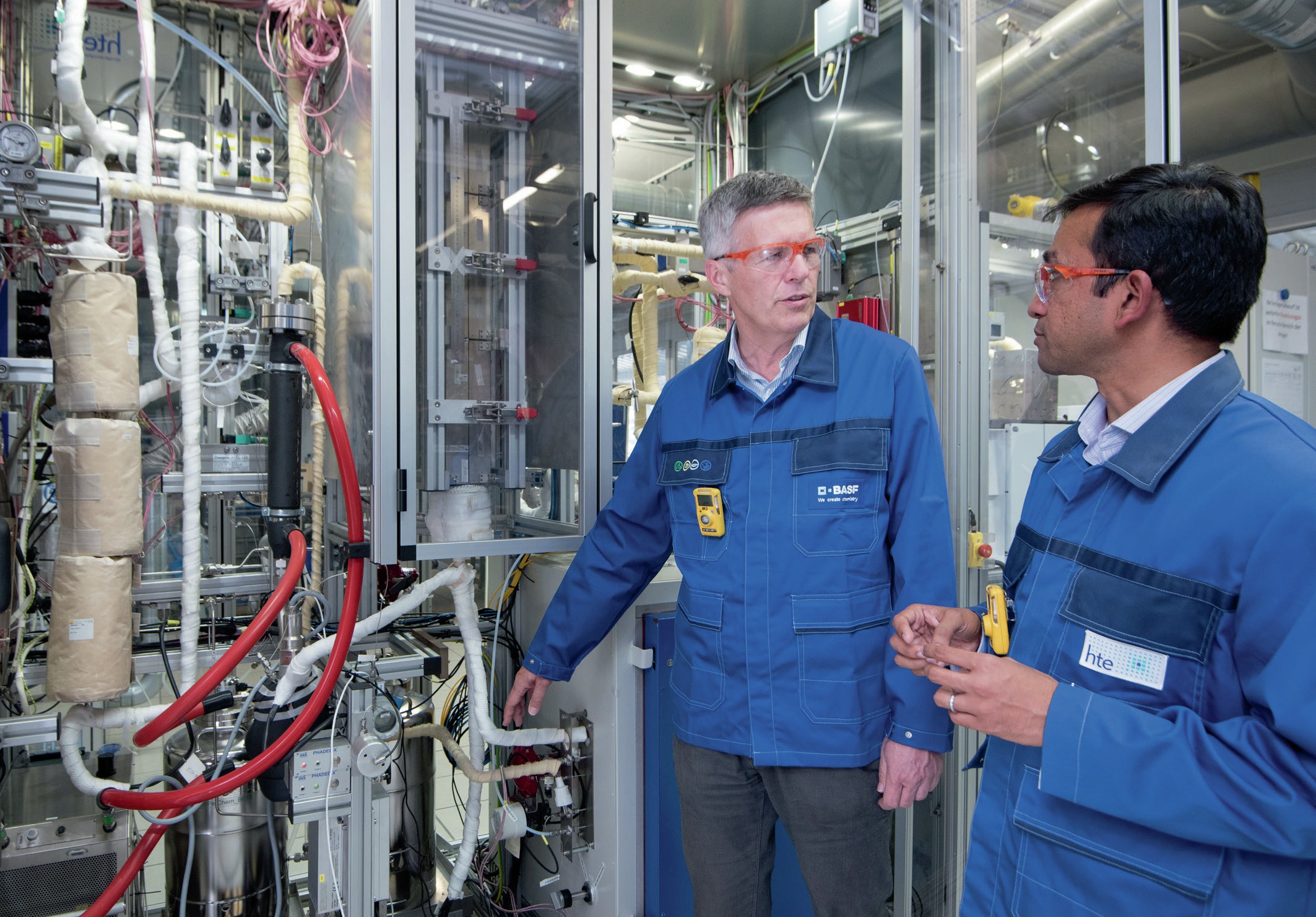
Above: Aspects of the new CO2 emission-free methanol synthesis process were tested in a pilot plant at BASF’s subsidiary hte GmbH, the high throughput experimentation company, in Heidelberg, Germany. Project manager Dr Maximilian Vicari and hte expert Dr Nakul Thakar are pleased to have solved challenges that arose during catalyst activation and operation of the plant.
BASF has set itself the target of carbon-neutral growth by 2030. Since 1990, the company has already halved its emissions from 40 million to 22 million tonnes despite doubling its production volume during the same period. The amount of CO 2 per tonne of product has fallen from 2.2 to 0.6 tonnes. “Completely new technologies are needed in order to further substantially decrease CO 2 emissions. That’s why we have initiated an ambitious research program,” explained Dr. Martin Brudermüller, Chairman of the Board of Executive Directors at BASF.
The aim is to identify technologies and processes that significantly reduce CO 2 emissions and that can be implemented on an industrial scale. A research and development team led by Dr Maximilian Vicari, Director Global Technology Operating Division Intermediates at BASF, recently made great progress in this respect: The “Emission-free Methanol” project within the Carbon Management program has been developed and refined to the extent that a patent application has been filed for the process. “The objective of our project is not just to reduce CO 2 emissions, but to prevent any CO 2 emissions in the entire production process, from natural gas to pure methanol. By doing this, we hope to achieve a 100% carbon yield from synthesis gas generation to the end product methanol,” said Vicari.
New emission-free methanol process
The new process begins by producing the synthesis gas through partial oxidation of natural gas, with no carbon dioxide emissions at all. The methanol synthesis and distillation steps of the process can be applied with almost no changes. The partial oxidation process was tested in a joint study with Linde Engineering and proved to be beneficial. “It is the only process we are currently aware of that generates a synthesis gas without any CO 2 emissions and that does not exhibit any serious technical problems. The study we compiled together with Linde clearly confirmed that this procedure harbors the fewest technical risks,” Vicari explained.
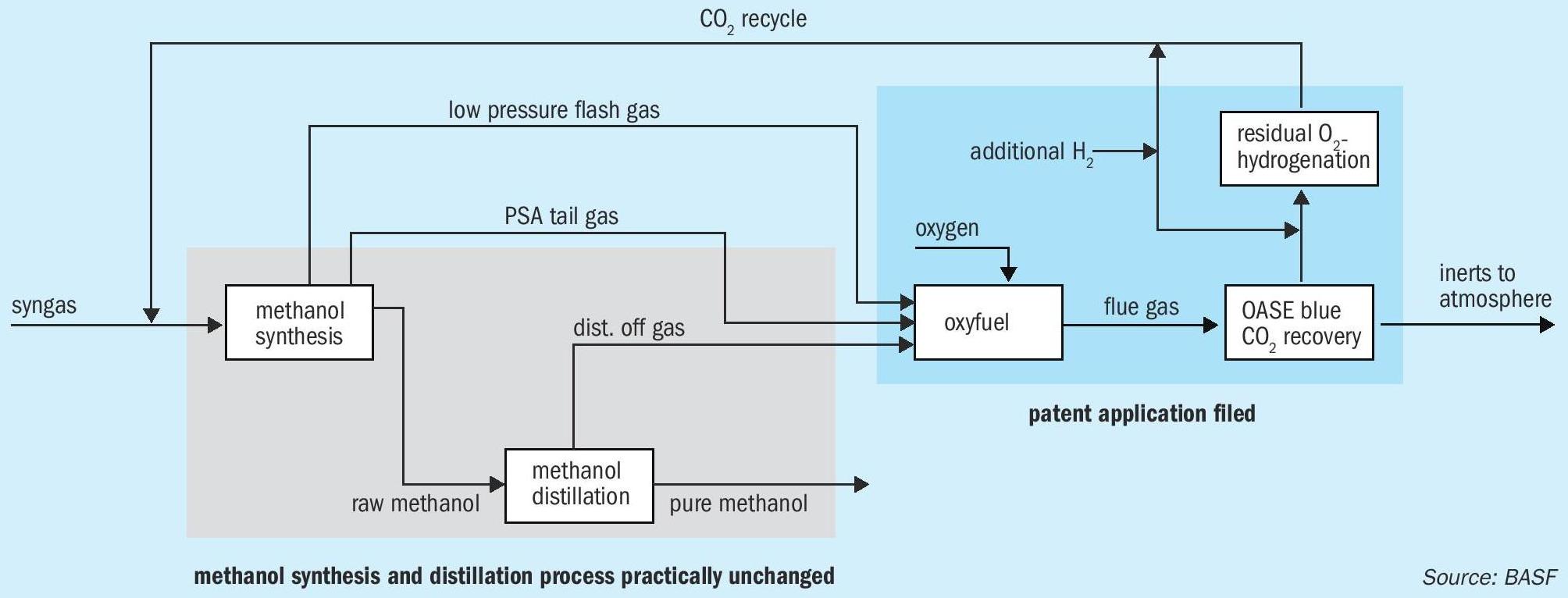
A waste gas stream is ejected from the methanol synthesis cycle in order to prevent the accumulation of components that cannot be converted to methanol, e.g. methane or nitrogen. Hydrogen is recovered from this waste gas stream by means of pressure swing absorption. The raw methanol product is also produced as a liquid stream. The pressure of this stream is reduced to 6 bar (absolute), during the course of which a CO 2 and methane component is produced in what is known as the low-pressure flash gas. Low-boiling components such as CO 2 and dimethyl ether are then separated from the raw methanol stream in a distillation column. Methanol, water and several higher-boiling substances remain in the sump. The pure methanol distillation then takes place. The methanol synthesis and distillation process thus produces three waste gas streams, which are unavoidable even when the process is run in an optimal manner. The waste gases from distillation and pressure swing absorption and the low-pressure flash gas are collected and subsequently combusted in an oxy-fuel process with pure oxygen. “As a result, there is a minimal amount of flue gas with a maximum CO 2 content, which has a very advantageous effect on the next stage – OASE gas scrubbing,” commented Vicari.
This flue gas is then subjected to gas scrubbing in the tried-and-tested BASF OASE ® process, in order to completely wash out the CO 2 . OASE blue is an optimised post-combustion capture technology (PCC) for use after combustion. With low energy consumption, low solvent losses and an exceptionally flexible operating range, OASE blue is an important technology for use in the separation of carbon dioxide in waste gases or other gases containing oxygen from sources including fossil fuel power plants or combustion turbines. The technology is based on the separation of carbon dioxide using aqueous amine solutions. OASE blue plays a special role due to the ease of retrofitting this system compared to other separation procedures and the ability to adapt it to the gas streams to be treated. The corresponding CO 2 scrubbing is characterised by a low energy requirement, low washing agent consumption, low emissions, low investment and maintenance costs and a high level of plant availability.
The goal – no carbon loss
Thanks to the recovery of CO 2 , the contained carbon is not lost, but is again available for methanol synthesis and is fed into the synthesis gas or into the process for producing synthesis gas. Hydrogen from renewable sources is also added following the gas scrubbing in order to ensure the correct stoichiometry during the methanol synthesis. Small quantities of residual oxygen from the oxy-fuel combustion can then be catalytically hydrogenated. Fixed-bed catalysts containing copper and precious metals can be considered as suitable catalysts. As such, it is possible to reduce the oxygen content to values below one ppm by volume. Inert gases in the process, such as nitrogen and argon, are discharged following the gas scrubbing to avoid accumulation of these components.
The new process from BASF enables methanol to be generated from synthesis gas with a high yield and with the required purity. As no significant procedural changes are necessary in the actual methanol synthesis and distillation, the concept also allows existing plants to be retrofitted. The key feature is the virtually complete material use of components containing carbon for methanol synthesis and the avoidance of any CO 2 emissions. The CO 2 is not only fed back into the system, but also increases the yield of methanol. BASF expects the new process to be implemented on an industrial scale in a first plant within the next ten years.
Methanol from renewable sources
Another approach for reducing greenhouse gases is the generation of methanol based on renewable raw materials. Since November 2018, BASF has been producing methanol based on renewable raw materials in accordance with the principle of biomass balance under the name “EU-REDcert Methanol.” Instead of fossil sources such as natural gas, second-generation renewable raw materials are used as well as waste and residual materials. In doing so, BASF is reducing the emissions of greenhouse gases by at least 50% compared to conventionally produced methanol. The biomass-certified methanol is identical to the conventionally produced compound in terms of its chemical and physical properties. BASF is marketing EU-REDcert methanol to customers and also uses it itself as an intermediate for other biomass-balanced products. Both of these new approaches – the innovative CO 2 -free production process and the increasing use of renewable raw materials – are significantly reducing greenhouse gas emissions.